Bath from foam blocks: design features
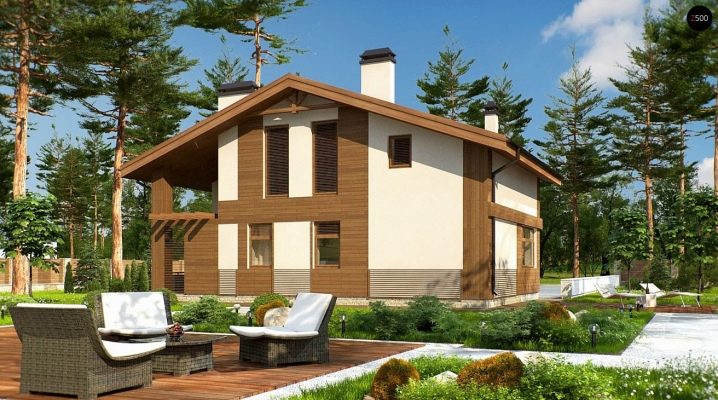
No one can deny the benefits of a bath for the physical and emotional health of a person. Baths have been popular with different peoples for many centuries. And now she enjoys well-deserved popularity. Many people want to have a bath complex for their personal use, on their site. Unfortunately, due to the rather high cost of wood, not everyone can afford the construction of a classic bathhouse. In this case, an option from modern material - foam blocks will help.
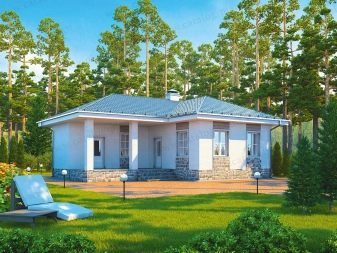
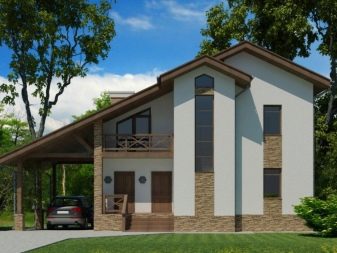
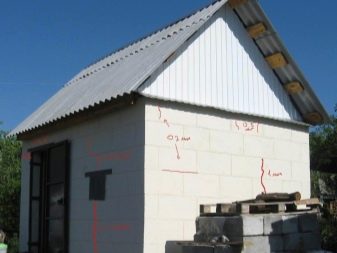
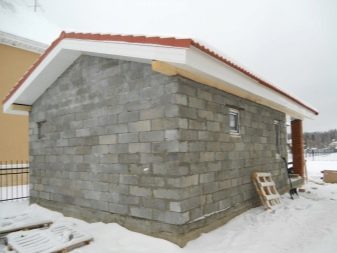
Peculiarities
Almost anyone can build a small sauna from foam blocks. Due to its light weight, at the same time, it will not take much time to lay out walls from foam blocks. Observing all the construction technology, the time that will be spent on it will take about a crescent, while the structure will be of high quality and have durability.
Foam blocks are a building material made from a mixture of a certain proportion of cement and sand with the addition of an air-forming substance mixed with water.
Cavities in the body of foam blocks serve as an additional source of high heat capacity.
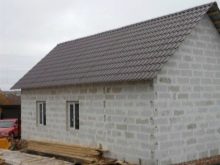
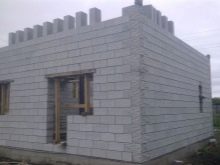
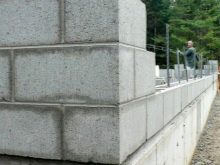
It should be borne in mind that the bath is an object where high temperature and humidity are used. Taking these factors into account, foam blocks need to be purchased of the M25 brand, while it is desirable that their density be D700. Their cost is somewhat more expensive, but this is offset by the durability and strength of the bath being built. To minimize the destructive effect of water on the building material, the walls of it must be very well waterproofed from the inside and outside.
The positive features of the use of foam blocks in the construction of a bath include, as already mentioned, the cost of building materials. For comparison: the cost of a log house made of wood is twice as high as the cost of a structure built from foam blocks.
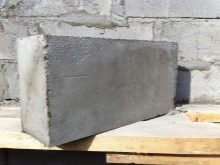
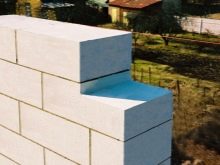
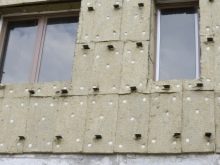
The strength of this building material differs in a positive way. Baths can be built from it in two, or even three floors. The thermal conductivity of foam blocks can be compared with the thermal conductivity of wood, in contrast to bricks, whose performance is three times worse.
Due to the lightness of the foam blocks due to the air cavities in the concrete, construction can be carried out without the involvement of outside help and special equipment - with your own hands and relatively quickly.
A significant plus is also the environmental friendliness of the material used.
Compared to most types of wood, foam blocks are non-radioactive, do not have hazardous or toxic impurities.
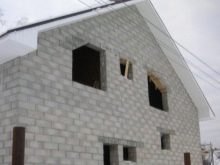
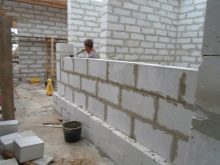
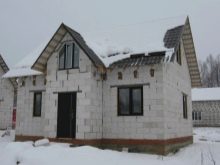
Wooden baths are distinguished by an increased fire hazard, while a foam concrete bath, on the contrary, does not burn, cannot sustain combustion and ignite. It also does not rot, rodents and insects do not breed in foam concrete buildings, foam concrete is not susceptible to fungal attack.
Due to the ease of processing, the foam blocks are perfectly cut with a simple saw, installation is practically not difficult. Any building elements are easy to cut out of any shape and size, after which they are glued together with a suitable special mixture.
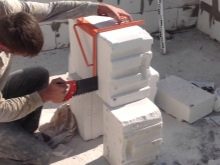
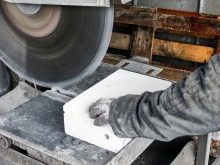
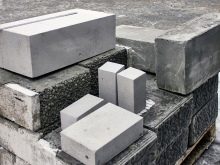
A distinctive feature is the material's resistance to deformation, blocks do not warp or crack, do not swell under the influence of temperature fluctuations and high humidity.
Unfortunately, the pores of the material absorb moisture, in this regard, it is necessary to purchase blocks for such structures, which are treated with a special composition in the form of a water-repellent soil. The cost of such a material will be more expensive, but it will pay off due to the durability of the building.
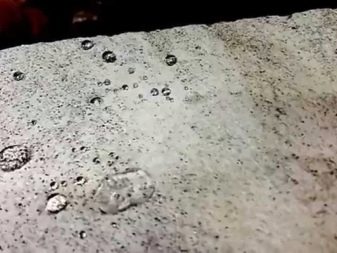
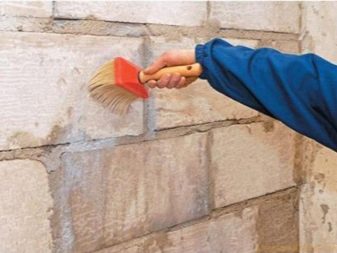
There are also some disadvantages. These include low strength in case of bending of the material, inhomogeneity of the pore structure, which creates certain problems of retention of fasteners. In such cases, it is desirable to use hardware (dowels, anchors) intended specifically for fastening in porous structures.
Deviations in the density of the material are possible due to the various technologies used for their manufacture and violations of the proportions, as well as insufficient mixing of the mixture.
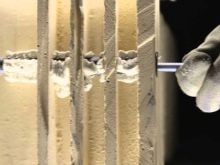
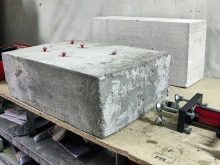
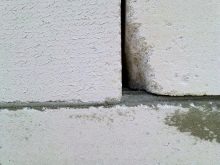
Construction is recommended to be carried out at positive temperatures. due to the fact that the properties of the adhesive are significantly weakened or completely lost under frosty conditions. If you adhere to all the recommendations, then even after 10 years the structure will look like new, and the disadvantages will be invisible.
Since, due to their porous structure, the blocks absorb moisture, it is necessary to additionally waterproof the walls and partitions being erected, and also apply the appropriate finishing of the structure.
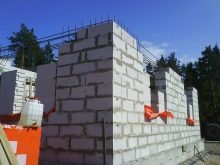
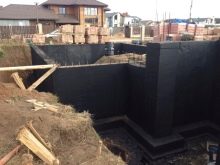
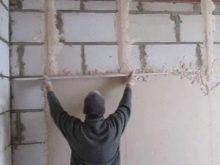
Project
Just like for any construction, before starting the construction of a bath, you need to choose a place, carefully plan, select and calculate the necessary material. Also find out what the roof will be, for example, a pitched roof.
It is advisable to immediately imagine what you want to see in the layout of your bath. In the classical version, in the drawings of almost all baths there is a steam room and a sink, a relaxation room is also desirable. Spaces in different cases are distributed according to the emerging requests. There may be options with a large steam room and a small sink, also with reverse distribution, a large relaxation room is possible and many other options.
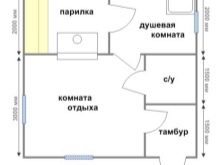
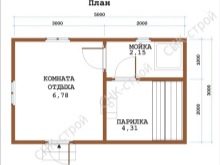
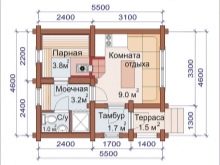
Choosing a suitable option will not be difficult. Each person has his own idea of the functionality, correct use and organization of the premises of the building being erected.
Particular attention should be paid to the construction of the vestibuleif you plan to use the bath for its intended purpose in the winter. Also, the location of the doors is of no small importance, they must be planned so that they do not take up too much space.
The stove must be selected taking into account the volume of the steam room, not forgetting that it is usually heated from the dressing room, therefore, part of the heat goes to heating it. Based on these parameters, the power of the furnace is selected.
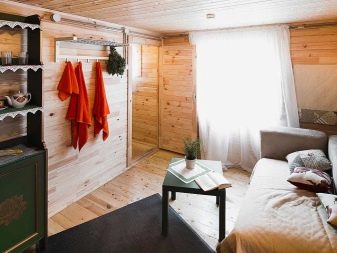
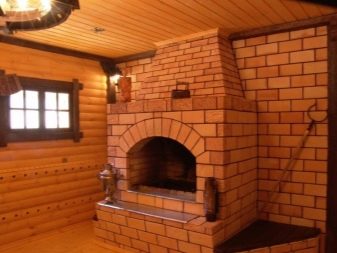
Currently, the bath is not only used for washing, it is often used for emotional and psychological relief. Based on the requirements, a construction project is selected and implemented.
It may include not only the classic set: steam room, washing room, changing room, but this may include the premises of the rest room, terrace, attic, pool.
The most economical option would be to implement a project to build a bathhouse with three rooms.
The size of such a bath is approximately 400x400 cm.
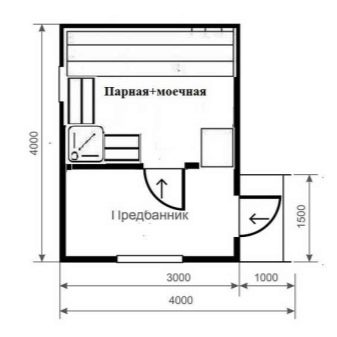
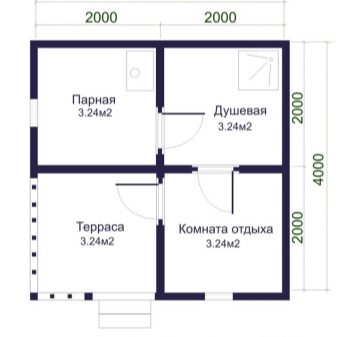
There are a great many bath projects, among them the most common are those where the rest room is combined with the dressing room. At the same time, it is advisable to make it larger than other rooms, in connection with the placement of the necessary furniture in it.
Bath plans with terraces are very common. Terraces are equipped with the necessary furniture in the form of chairs and tables, barbecues and barbecue ovens are installed. The building is carried out under a single roof and corresponding design. Instead of a terrace, you can add, for example, a garage or other annex. The original idea is a country house, combined with a sauna building.
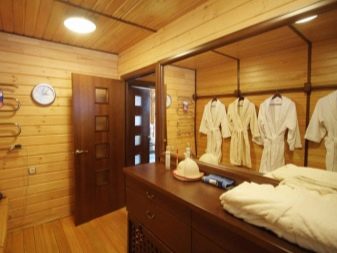
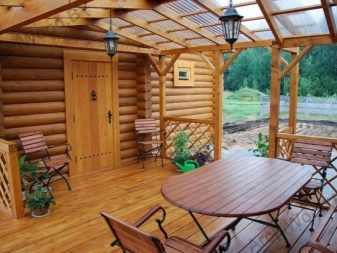
Quite often, an attic is built as a second or third floor. This two-storey building can be used as living or guest rooms, or for relaxation after procedures. Such structures can also be one-story. The most commonly used sizes are 6 by 4, 3 by 5, and 6x6 meters.
With all responsibility you need to approach the choice of a site for construction. The site must comply with all fire safety rules and the requirements of SNiP 30-02-97.
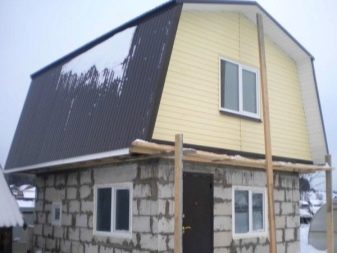
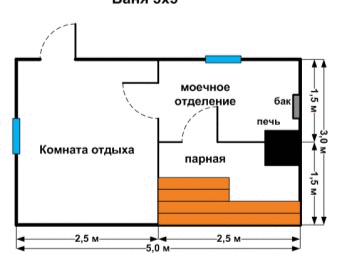
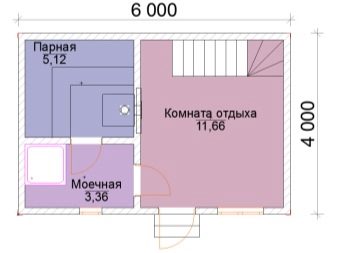
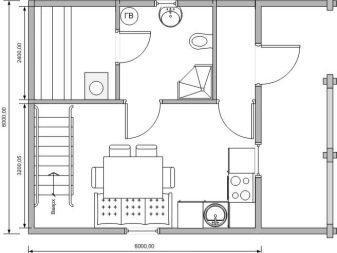
Based on these requirements, the building must be located at a distance of one meter from the fence, while the neighboring house must be at least eight meters, including five meters to the border of the site.
The site should be chosen on a dry, preferably flat, place due to the fact that the foam blocks are hygroscopic.
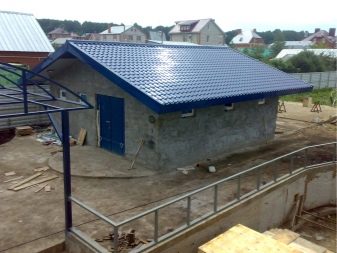
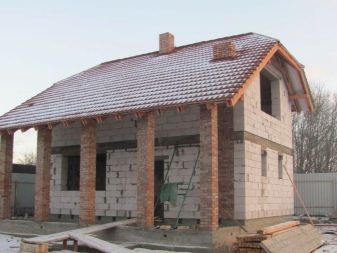
Materials (edit)
Depending on what material was used in the construction, it depends on how functional and durable it will be. You should pay close attention to the time when the blocks were manufactured. The required strength of foam blocks is established after 28 days from the time of their manufacture. Accordingly, it is not recommended to use blocks that have not passed the hardening period.
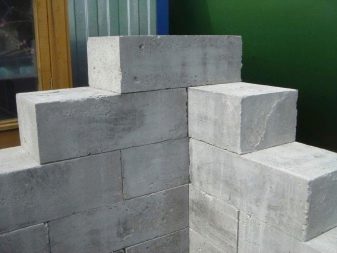
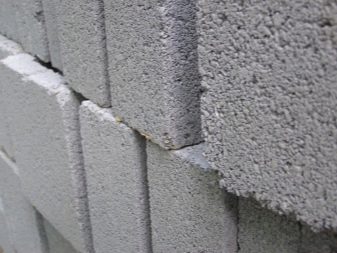
There are several factors to consider.
- It is advisable to purchase products from trusted enterprises that value their authority. These enterprises conduct laboratory tests of their products and subsequently sell them accompanied by appropriate quality certificates.
- The cost of purchased materials should not differ significantly from the market average. Otherwise, you should find out the reason for the discount so as not to purchase low-quality material.
- Pay attention to the tightness of the packaging and storage conditions in a dry place.
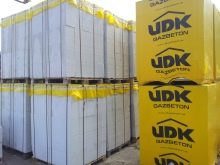
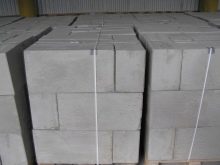
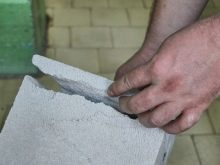
It is also desirable to conduct a visual inspection of the purchased material, while it is necessary to determine what is the pore structure of the blocks, this is clearly visible on the split block. In a high-quality material, the inner and outer surfaces are the same, while the pores are isolated and small in size. If the pores are connected, then the foam blocks are hygroscopic, with a large pore size, the strength of the product is reduced.
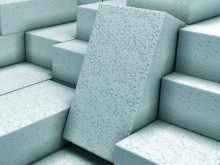
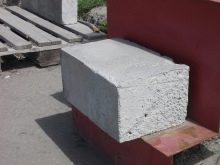
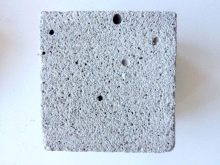
You need to buy the material in gray, which corresponds to GOST 25485-89if the color is light, this can signal a violation of proportions and a decrease in quality. It is also necessary to check how correct the purchased products are. To do this, two or three sides are joined and the presence of gaps between them is checked. If there are gaps, then an increased consumption of adhesive mass will be required.
You can calculate the required amount of material for construction yourself. This will require data on the dimensions of the future bath and the dimensions of the unit of the applicable material.
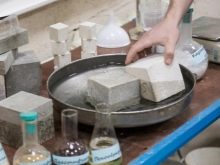
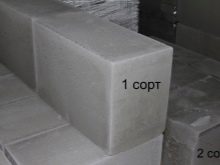
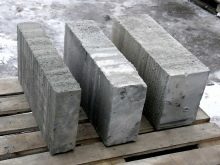
To calculate the total number of foam blocks, the number of blocks in the wall is first calculated. The width of the wall is divided by the size of the block length, the height of the bath is divided by the size of the height of the foam block, then both results are multiplied. Based on the result obtained, the perimeter is calculated. Accordingly, the number of foam blocks in the partitions is calculated. Next, you need to calculate how many foam blocks contain window and door openings and openings for the oven, subtract them from the total result, all walls and partitions. This is how the exact amount of material required for the construction of a bath is found out.
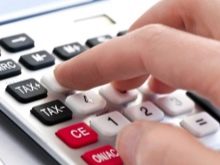
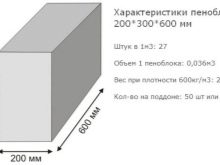
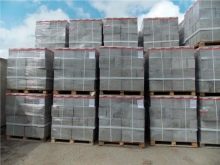
Separately, the calculation of the required number of beams for rafters and floors, plywood, Mauerlat, fasteners, necessary insulation and finishing materials is carried out.
The foam block can always be replaced with a gas block, as evidenced by the reviews of the builders. The main thing is that the thickness of the material is chosen correctly. Also, do not forget to insulate the building.
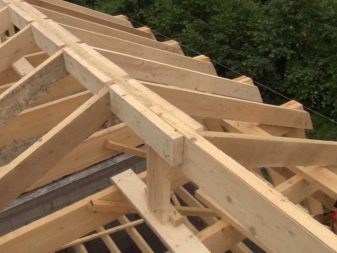
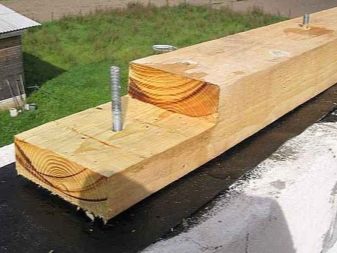
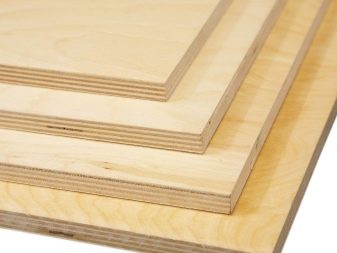
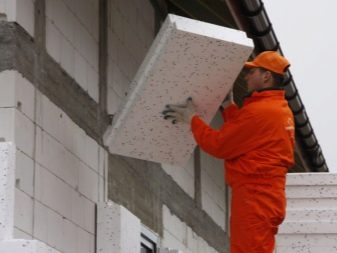
How to build with your own hands?
After you have decided on the amount of the required material and the necessary tools, we proceed to the construction. This requires step-by-step instructions. You can make such a building yourself, even if you do not have any special skills.
Due to the fact that foam blocks are a light material, it is possible to make a not very expensive strip foundation, and this will be enough.
First of all, we determine the density of the soil at the construction site, depending on this, we count on the depth of the foundation: the looser the soil, the deeper the foundation.
The durability and functionality of the bath depends on the strength of the foundation.
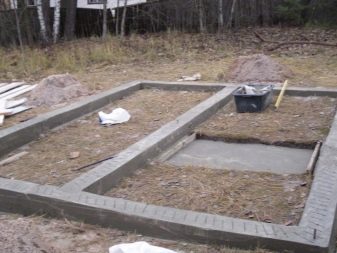
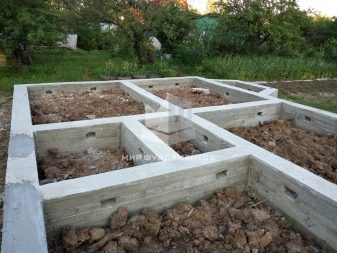
The width is laid a little more than the width of the foam block. At depth, a sand and gravel cushion is taken into account, which is laid directly under the concrete.
When you have decided what depth the foundation should be, it is necessary to mark the future bath with twine and stakes. Next, a trench is dug, depending on the soil: up to a meter deep and about 40 cm wide. The poured sand cushion is tamped and gravel is poured on top, laid with welded fittings.
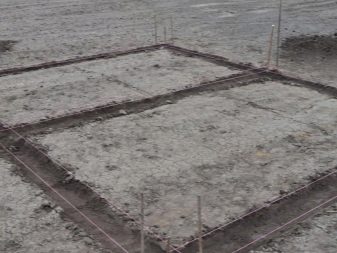
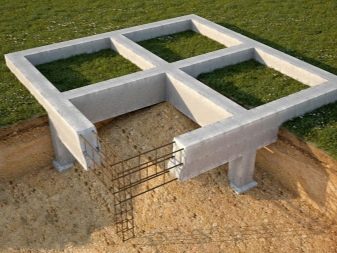
The formwork is knocked off from scrap materials, not forgetting about the ventilation holes. The prepared concrete is poured, preferably using a grade of at least M200. It is necessary to wait until the concrete hardens completely. If possible, waterproofing in the form of roofing felt or roofing material is pre-laid on the bottom of the dug trench, which will prevent the foundation tape from getting wet from the ground.
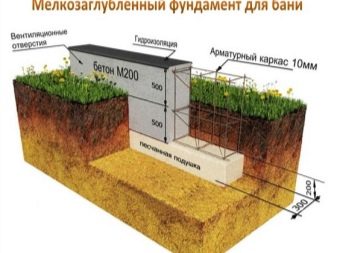
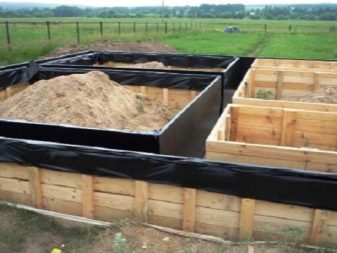
For a high-quality foundation, concrete is poured at once, interrupting during operation for no more than three hours. During the first two days, the concrete is wetted with water up to three times a day to avoid cracking, and it should also be protected from sunlight.
The formwork is removed after three days.
Complete hardening of concrete can take up to six weeks in adverse weather conditions.
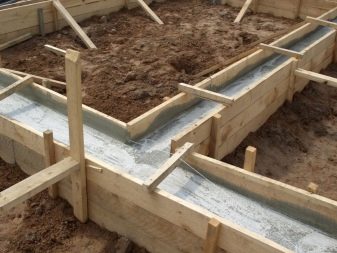
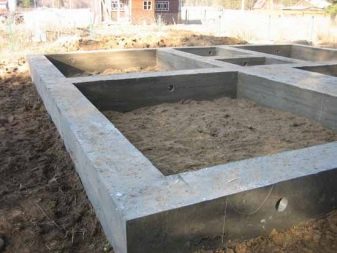
Next, it is necessary to fill the base for installing the furnace and wiring the engineering networks in order to organize the drainage of the used water. To do this, prepare a drain or equip a special pit, if possible, the sewer outlet is connected to the central sewerage system. In any case, a special channel with a slight slope is created inside the area fenced off by the foundation. When the floor is being built, a special hole will be built into it to drain the used water from the premises. Do not forget that a pit or other device for the outflow of water is equipped outside the contours of the bathhouse being erected.
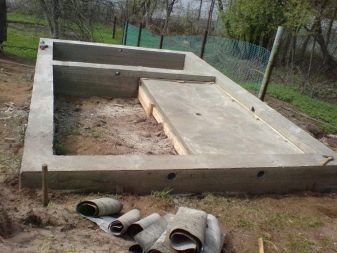
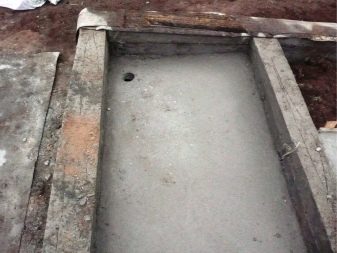
Before erecting walls, you need to insulate the foundation with polyethylene, roofing roofing or roofing material. You can also coat with bitumen mastic.
To lay out the first row, you need to pull the fishing line or twine along the level, then start laying out the foam blocks using cement mortar, a similar one used for brickwork. It is important to lay out the first row correctly, the quality of the entire structure depends on it. In order to avoid irregularities and differences in the height of the blocks, a rubber mallet is used, with the help of which they are knocked out to the required height.
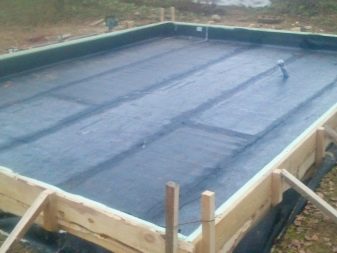
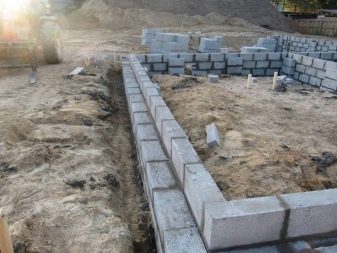
Starting the second row will make it easier to work. This is where the application of the special glue begins. The preparation of the glue is not difficult; for this, the mixture simply needs to be combined with water and stirred. The glue is applied in an even thin layer, about 0.5 cm.
To make the walls more durable, reinforcement or reinforced mesh is laid every few rows. If the height and size of the bath is quite large, then metal reinforcement is used, laid in special recesses in the blocks, when strengthening the corners and partitions, the reinforcement is rounded off without cutting. When removing window and door openings, special mortgages are used, implemented with foam blocks.
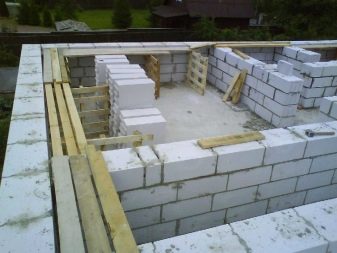
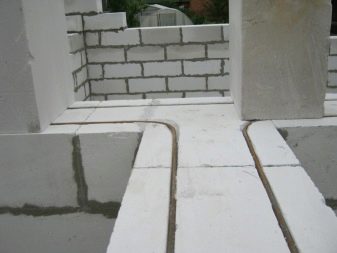
Upon completion of the construction of the wall, it is necessary to withstand up to five days so that they are completely dry, having previously covered the entire structure with a special film.During this time, the strength of the box increases, and you can start making the roof.
For buildings that are built from foam blocks, an ordinary gable roof is usually made. When choosing rafter legs, you need to take into account the width of the bath, the intended slope of the slopes. The legs in the skate are joined by a thorn-groove connection. In this case, it is advisable to arrange the roofing overhang above the walls about 50 cm.
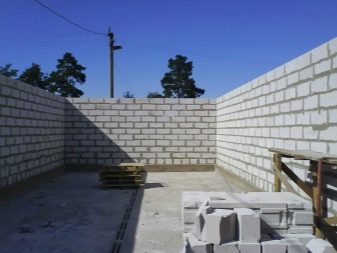
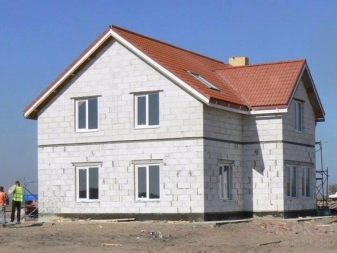
The roof is built from wooden elements and covered with corrugated board. The ends are sewn up with roofing felt or roofing material. The overlap between the ceiling and the directly under-roof space is insulated from the inside using foam plastic due to its lightness and non-hygroscopicity. To remove excess steam, holes are made in the ceilings, so that there is good ventilation, it is necessary to install vents and grilles. For the owners of the data, the structure should not forget about all these nuances.
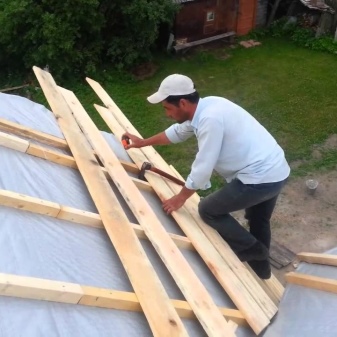
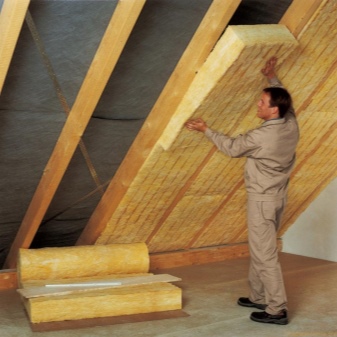
Interior decoration
Due to the moisture content of the foam blocks, it is necessary to pay special attention to the decoration of the walls of the bath. To do this, you need to do steam. The insulation of the inner surface of the foam blocks is carried out in order to avoid condensation of warm steam. For insulation, aluminum foil is used in the form of a reflective screen for heat or a special vapor-permeable membrane. Beforehand, the blocks must be impregnated with a moisture-repellent agent and dried.
It is necessary to carry out a competent insulation of the bath. Thermal insulation is carried out in several stages. The foundation and the entire area of the underground are pre-insulated. The foundation is insulated with mineral wool, while the subfloor is insulated with expanded clay and slag.
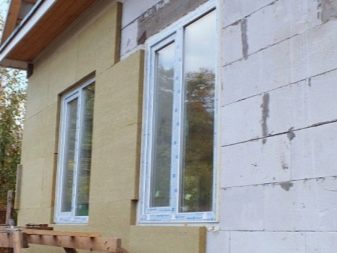
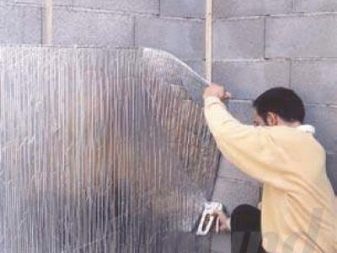
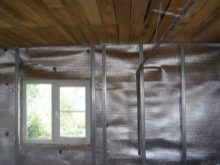
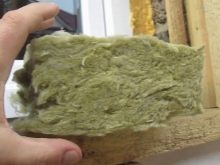
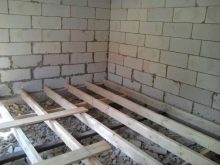
Wooden material is used to decorate the walls in the baths, it can be a board, lining and other types of lumber. The wooden sheathing is attached to the installed frame, while the distance from the sheathing to the wall should be at least five cm. For finishing, ceramic tiles or plaster are also used, which are subsequently painted.
For flooring, they mainly use sanded boards, as well as special non-smooth tiles for safety in order to avoid injury. In the case of using boards, they are stacked on logs. The tile is laid on a concrete screed, then a moisture-resistant grout is necessarily applied, otherwise the screed is destroyed in the area of the seams, and the tile will move away from the base.
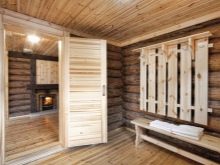
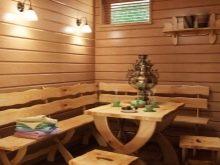
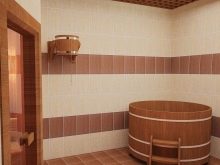
To maintain hot steam in the steam room, the floor level in it is made higher than in the rest of the bath, by about 20 cm.
It is recommended to use only wood for decorating the walls of the steam room., and preferably hardwoods. Such types of wood are resistant to decay in conditions of high-temperature humidity, if possible, you can use wood of exotic species, many of which, when heated, form specific aromas, they can also be used to make floors or shelves in a steam room.
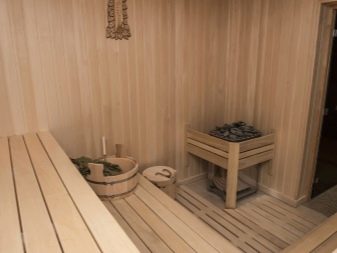
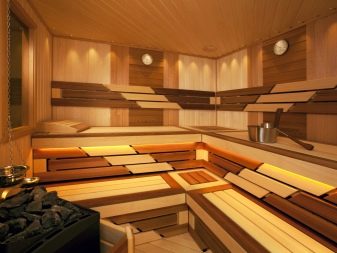
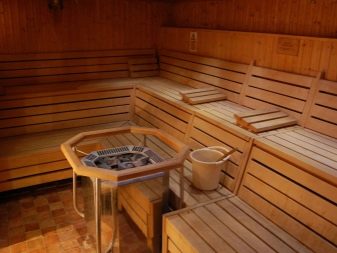
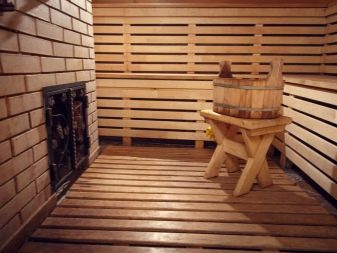
Exterior design
The external walls are preliminarily prepared by leveling and filling chips, dents and irregularities with a mortar, which is used for laying blocks, and rubbed with a float.
Dust on the walls is removed and an initial layer of plaster is applied. Reinforcement mesh is applied and pressed into the fresh plaster using a metal trowel.
A priming layer is applied to the pressed mesh, after waiting for drying, it is completed with a thin decorative layer of plaster. If desired, a certain texture is given to it using a scraper.
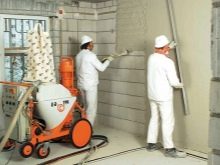
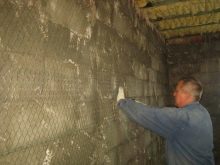
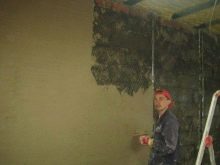
The external decoration of the bath is equipped with the use of hinged ventilated decorative facades. The use of such a finish helps to remove excess moisture, this will help to reliably protect the walls of the steam room from adverse external conditions.
The bathhouse has been built. It remains to install windows and doors outside, make benches, shelves. Put on the oven. Carry out the first test and enjoy the result.
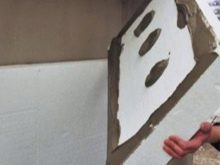
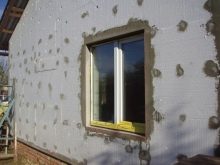
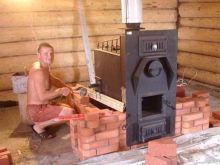
Beautiful examples
- A foam block bath can be small. Such a structure will not take up much space, but it will bring maximum pleasure.
- Such a structure may consist of the bath itself, as well as a beautiful veranda. On the terrace you can have tea and cool off a little.
- If space permits, then you can create a whole bath complex from foam blocks.
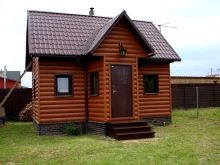
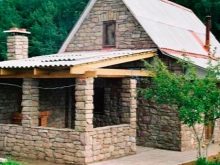
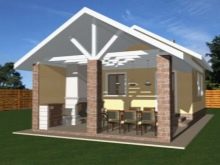
For the pros and cons of the foam block, see the next video.
The comment was sent successfully.