DIY garage construction
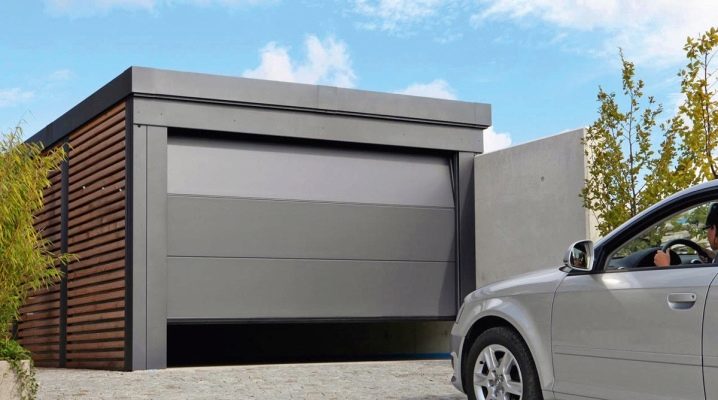
Every car owner dreams of a small, cozy garage. It is easy to turn this dream into reality with your own hands by building a garage yourself.
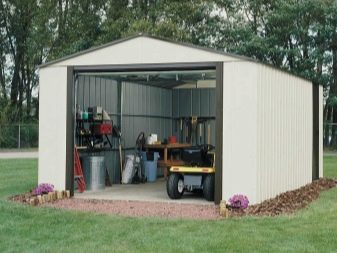
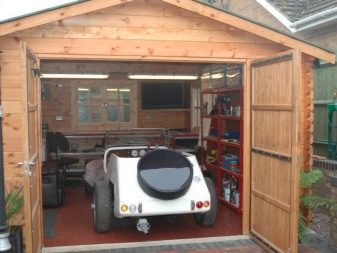
Construction features
Before you start making a garage, you need to carefully think over and disassemble the construction plan. First of all, you need to obtain a building permit.
You need to pay special attention to the following documents:
- SNiP 2.07.01-89 “Urban planning. Planning and development of urban and rural settlements ";
- SNiP 21.01.97 "Fire safety of buildings and structures."
If the fire regulations are not met, then the building can be declared illegal and demolished.
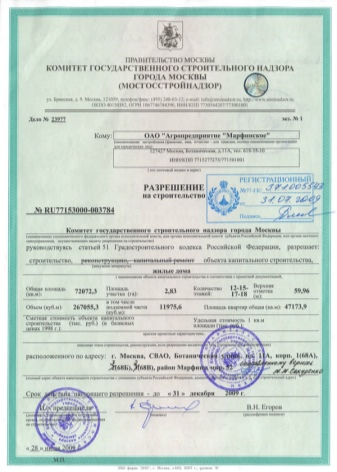
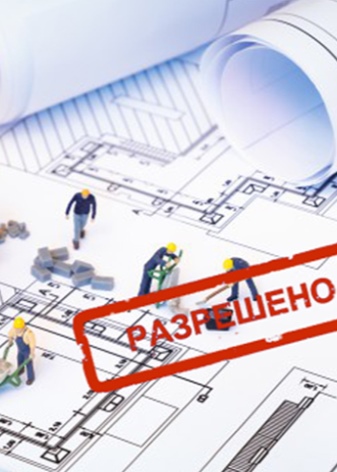
You also need to decide what the building will be. It is divided into several types:
- temporary - has a short service life;
- mobile - requires a frame structure;
- combined - suitable for subsiding soils;
- capital - has a long service life, but it will not be cheap.
It is necessary to consider protection from intruders. It is better to spend money on alarms than to later calculate losses due to stolen property and a stolen car.
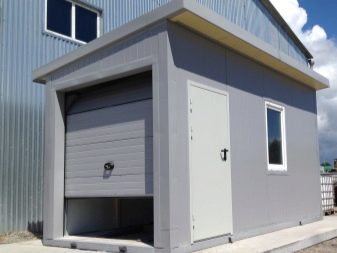
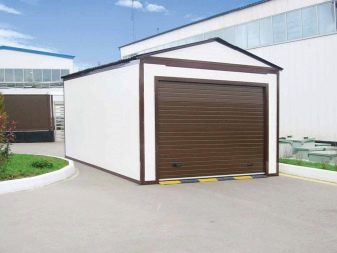
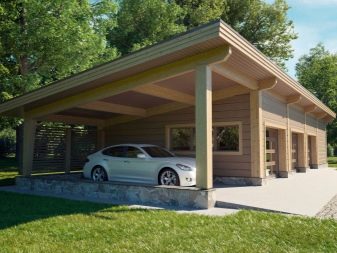
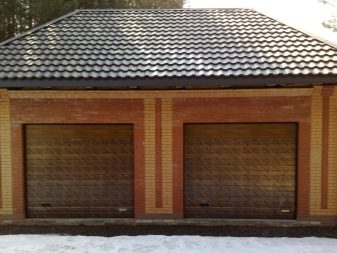
Dimensions (edit)
In order to calculate the required dimensions, you should decide on the number and size of machines that will "live" in the building. You should also understand whether any other things will be stored in the garage. It is necessary to consider whether an oversized car will be bought in the near future. For example, if in the near future the owner is going to purchase a large truck, then building for a passenger car is meaningless, it is better to immediately consider the option of building a large garage.
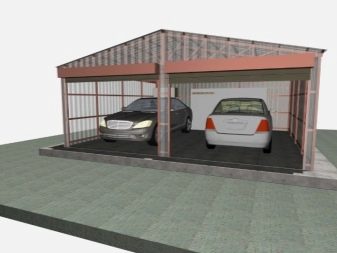
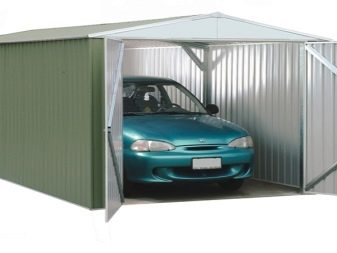
For one car, the size will be calculated based on its dimensions. To this value you need to add half a meter on each side. This is necessary for a comfortable exit from the car and free movement around the garage. It should be remembered that with such a small size there will be no room for tires and various devices. Therefore, it is worth increasing the length by 3 meters and adding a few more meters to the width. The height of the building should be more than half a meter from the height of the car.
All measurements are best done with the trunk open.
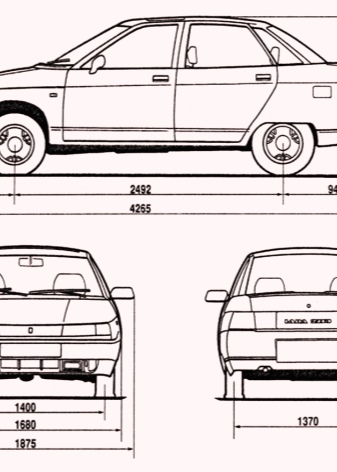
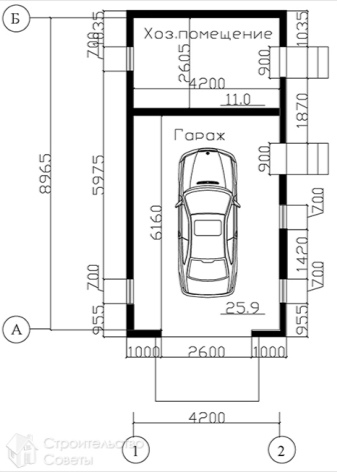
For multiple vehicles, it will be more difficult to calculate the size. Between them, you need to create a distance of a fully open door, you can add 30-40 cm for comfortable parking. The distance between the wall and the door should be more than half a meter. The front and rear of the vehicle should be positioned so that a person can freely pass. The distance should be left at about one meter.
As for the gate, here you need to take the width of the car and add 60 cm on both sides. If there are two cars, then it is better to take the width of the gate from 2.5 meters and 20 cm in reserve on each side. The height of the building is calculated in the same way as in the case of a single machine.
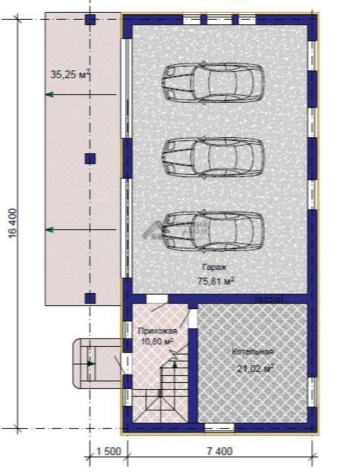
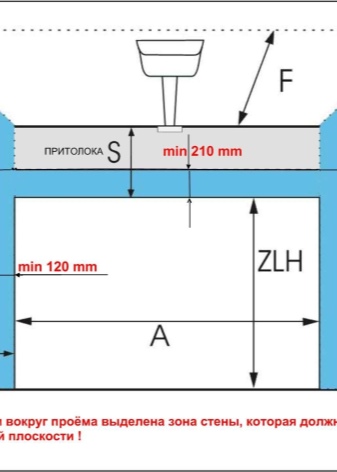
These were examples of the simplest small boxes. If the owner wants to use the garage space not only for storing his "iron horse", but also for other purposes, it will be enough to calculate the dimensions of the objects and take into account the space for free access to them. Then add the obtained data to the already available garage dimensions, which were calculated above.
Drawing will help determine the dimensions, it is performed on paper or in a special program.For advice, you can turn to the professionals, they will help and advise how best to implement this or that idea. You can take a ready-made scheme. The main thing is its presence. The drawing is very important for the subsequent work.
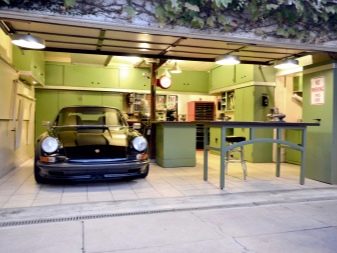
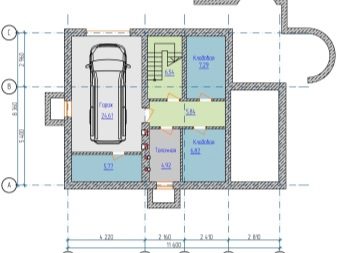
Seat selection
If the garage is located in a summer cottage, you can consider the option of adding a structure to the house. There is no need to obtain a permit, construction does not require special conditions, because such a building is considered part of the house. Here there is an opportunity to make an exit as close to the gate as possible or directly to the street.

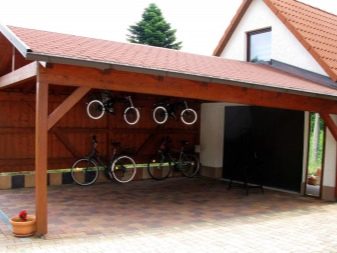
You will have to tinker with a free-standing type of garage. The SNiP states that there must be a distance of at least one meter between the garage and the border of the plot, if there are no buildings on the neighboring land plots. If they are, the distance should be at least 6 meters. When erecting a building, make sure that there are no sewer pipes, heating, water supply and power lines nearby. Erection in low areas should be avoided as this can lead to flooding. The best option would be a small hill.
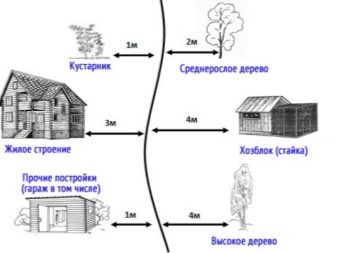
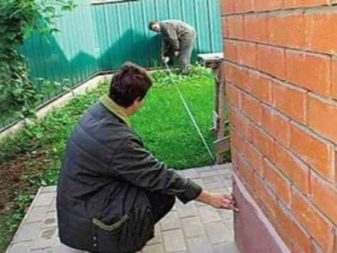
If there is not enough space on the site, then the way out of the situation is to build a garage underground. Check out the street. It is impossible to place a garage directly under the house itself; it would be more rational to make an extension to the strip foundation. The territory under which the building is located should not be used for the installation of structures with a foundation depth of more than 55 cm.But if there are underground keys or wetlands at the site of the future construction, then it is better to abandon construction, for such soil you will need an extremely expensive drainage system.
The room should be located as close to the exit and the motorway as possible, but without sharp turns.
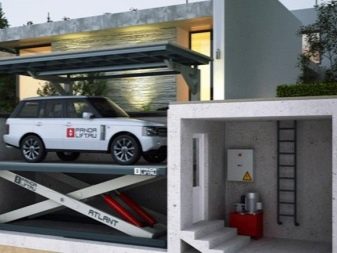
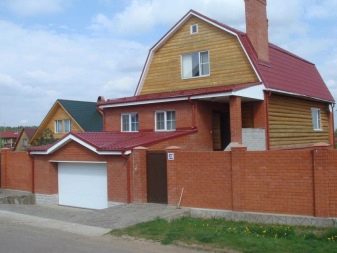
If you don't have a summer residence, but you need a garage, you can buy a privatized piece of land in the city. After that, having received permission, start construction. This procedure is very time consuming, so be patient. You should choose a place as close to home as possible, but you need to be prepared for the fact that there may not be free land for building within the city limits, but only on the outskirts or outside the city. Such a garage needs careful protection from intruders.
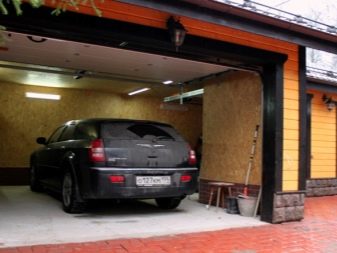
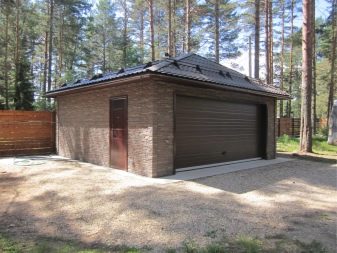
Design options
There are many types of garages to suit every taste and budget. The simplest and cheapest options are "shell" and "pencil case". They can be easily made by hand, and the "shell" can even be moved. But they do not differ in durability.
The next type is one-story, it can be made with a pit or utility block. In the city, a monolithic version is most often built, and although it looks not very attractive, it is very durable. No thief can get into it. If the garage is located in a summer cottage, then a panel frame garage can be an inexpensive option. It is being built many times faster than a monolithic and brick one.
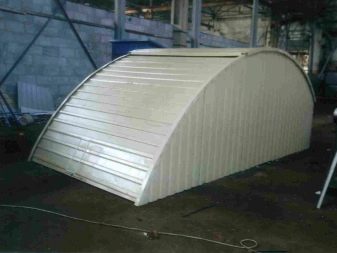
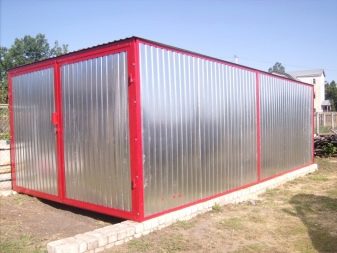
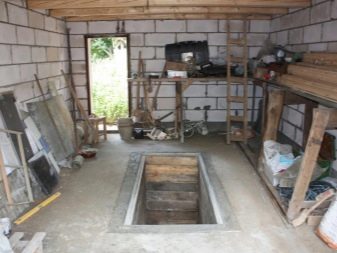
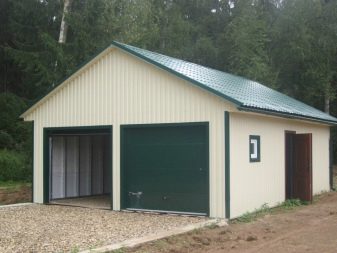
The two-story building can serve not only for storing cars, but also suitable for living in the summer. The residential floor should be warm, equipped with light, toilet and kitchen. And the second floor with a gable roof can turn into a cozy attic.
The garage can also be an extension to the main house. The advantages of such a building are that you do not need to think additionally about heating and other communications, the entrance to the extension can be done directly from the house. But a significant disadvantage is that exhaust gases penetrate into the house when the car drives in and out. This option is suitable for those owners who have not completed the main house, because an extension to an already finished building requires large investments and thorough preparation.
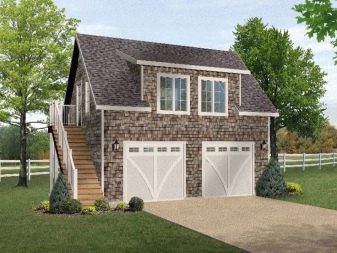
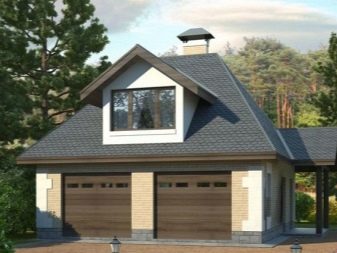
To build an underground room, several conditions must be met:
- When building a deep garage, waterproofing is considered the biggest problem. This will require the arrangement of the drainage system of the garage roof and reinforced waterproofing of all supporting structures.
- The garage roof frame must be made using concrete slabs with a mandatory support system.
- The room should have an emergency exit in case of a house collapse or fire.
- After choosing a garage design, you should decide on the material and find good suppliers of all the necessary attributes for the construction site.
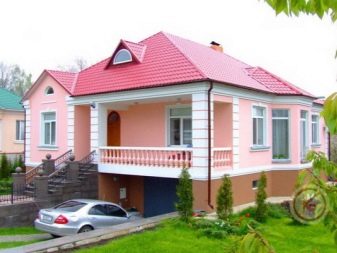
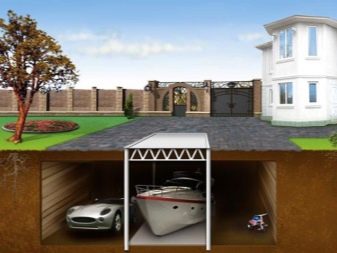
Materials (edit)
The market offers a huge range of quality materials that will last a long time. Each has its own pros and cons, you should remember this and choose an option that will be comfortable to work with.
Polycarbonate is lightweight and cheap, but should only be used in a small garage. For example, for a seashell.
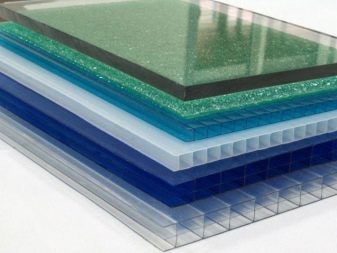
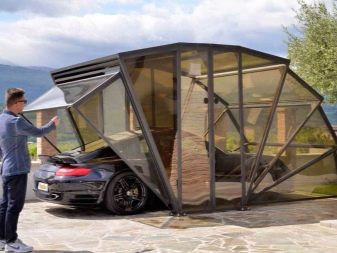
If the owner prefers metal, then you can opt for sandwich panels or corrugated board. The cross-section of the sandwich panels resembles a sandwich: there is a heater between two metal sheets. Construction is carried out in a very short time, and the structure is lightweight and lends itself to any modernization. Their price is very low, and installation can be carried out at any time of the year. But such a material is short-lived, the metal frame requires processing from rust, and the wooden base must be treated with antiseptic agents.
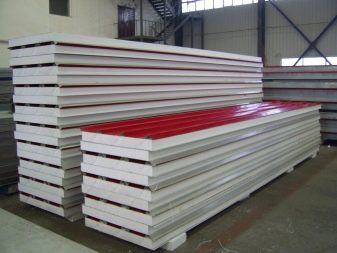
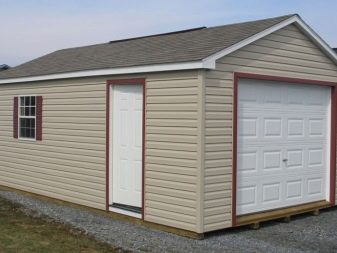
Decking is a cheap, high-quality and beautiful material. Corrugated garages are built pretty quickly. You should pay attention to the brand: it is better to choose S-20 or PS with a thickness of 0.5 mm. In no case should you take grade -8, these sheets will not last long due to poor wind resistance and low frost resistance.
A red brick structure will be much more reliable than metal. Such material has high frost resistance, low thermal conductivity. In terms of aesthetics, brickwork looks pretty decent, but the material is expensive.
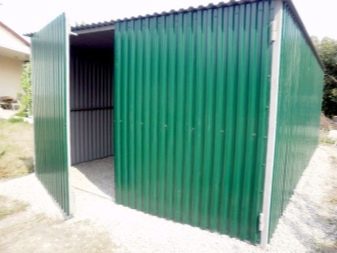
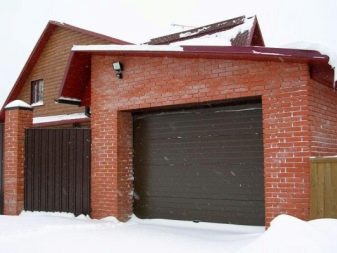
The foam block is cheap and lightweight, so one person can build from it. The only catch is that the gray blocks are not very attractive in appearance. This problem can be solved with finishing materials.
Gas silicate blocks are gaining popularity. Despite their low weight, they have high strength and are easy to process. Also, the blocks have low thermal conductivity, do not require additional treatment with antiseptics. With such a material, you can not be afraid of the appearance of mold, bacteria and fungus.
In terms of environmental characteristics, gas silicate blocks are on a par with natural materials.
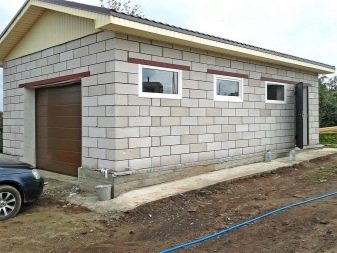
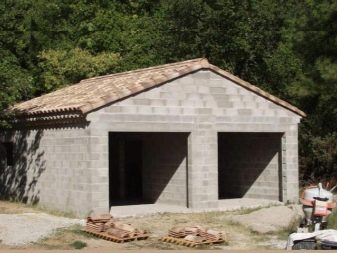
The disadvantage of gas silicate blocks is high water absorption. Plaster on walls can crack and flake off. This problem can be solved by treating the walls with penetrating primers. Since blocks are a weak basis for fasteners, it will be problematic to secure massive objects. They are not highly frost-resistant. The material has high indicators of free lime, which makes it possible to activate the corrosion processes of metal inclusions: reinforcement, pipeline, frame and others.

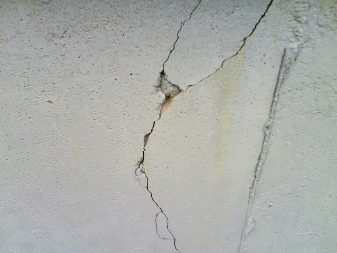
Another artificial, but environmentally friendly material is cinder block. You can buy it or make it yourself. For the second, a vibrating machine is required. When buying, you should pay attention to the filler. It is better to choose crushed stone, sawdust, shell rock, expanded clay. A garage made of cinder blocks is not afraid of natural disasters, it has a high fire safety, and is easily repaired. With this material, you can vary the thickness of the walls. In addition, it does not lend itself to biological destruction, its price is quite low, and its service life is about 100 years. Reduces the dignity of the cinder block unpresentable appearance, complex laying of pipes and cables, high thermal conductivity.
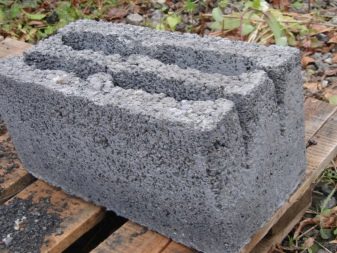
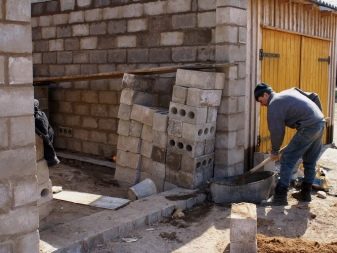
Arbolite has been known since the times of the USSR. It is lightweight and has low thermal conductivity. It is a flame-retardant material, resistant to stretching.He is not afraid of cracks and deformations during the movement of the foundation. It is immune to rot and mildew. The material is distinguished by high frost resistance. It is also easy to fix various structures on it. Such a garage will have good sound absorption. Of the minuses - a high coefficient of water absorption - from 40 to 85%, and a rather high price.
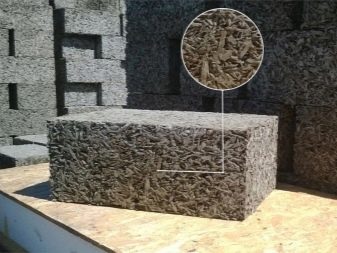
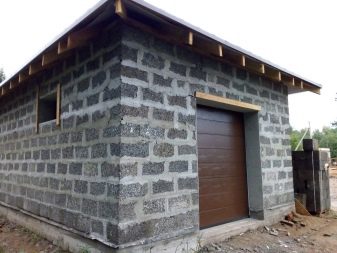
An expanded clay block will be an assistant in the embodiment of bold design and architectural ideas. Almost all types of finishes, both internal and external, are suitable for it. The material has low thermal conductivity, it is strong and durable, with high sound insulation. The vapor permeability of the blocks creates a favorable microclimate inside the room. The garage construction process will progress quickly due to the large block size. And simple production contributes to an affordable price.
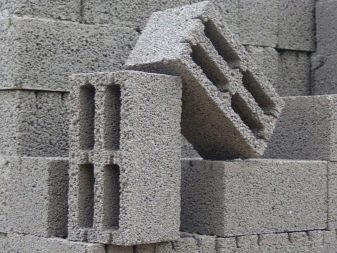
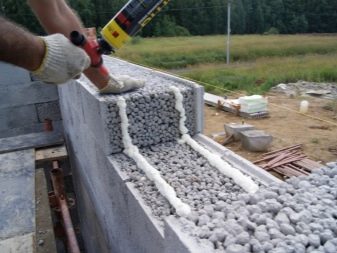
The disadvantage of expanded clay blocks is the formation of cold bridges, but with the help of cladding and additional thermal insulation, the problem can be solved. The material has low water resistance, is quite heavy and requires a strong foundation, but this building material cannot be used as a foundation.
A more natural material is wood. The material is inexpensive, beautiful and allows for bold design decisions. With the help of various impregnations, fire resistance can be achieved. Minus - short service life and high thermal conductivity.
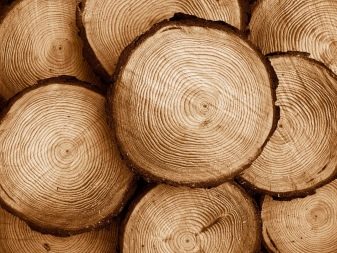
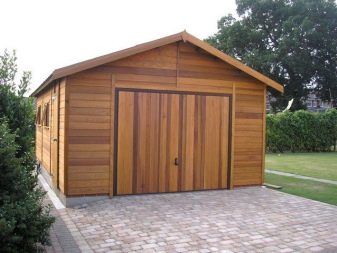
Railroad ties are wooden beams. A special blend that works as an antiseptic helps protect your garage from rot, bacteria, sun, moisture and small rodents. You can buy sleepers at the nearest railway branch, where track repairs are carried out. A garage made from this material will turn out to be dry and warm, capable of withstanding even an earthquake. But you should never build a garage with new sleepers. The smell of creosote is very dangerous, it can cause chemical burns and poisoning. The period of their use in air should be 12-30 years, during this period the mixture is washed off and loses an unpleasant odor.
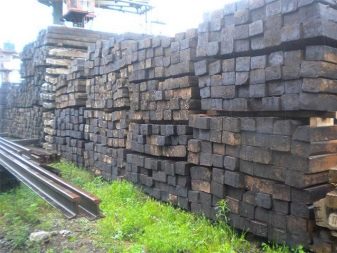
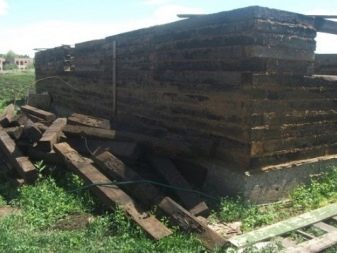
The methods of making and processing sleepers are different, some products are soaked through and through, while others by 2.75 centimeters. Better to use the latter option. Such a construction requires careful processing inside, which reduces the risk of contact with creosote residues. Outside, a well-ventilated facade must be made.
Many building materials do not have high frost resistance, therefore, the garage must be insulated. The cheapest insulation is polystyrene. It is very easy to install. But you need to remember that this is a fragile material that wears out quickly.
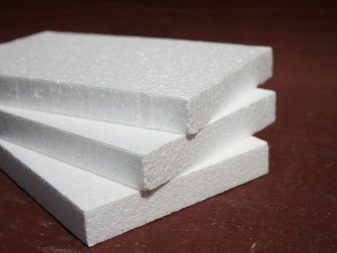
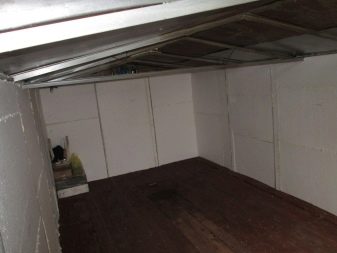
Another cheap insulation is mineral wool. It is safe for health, has high thermal insulation and a high level of sound absorption. Such material must be covered with an additional layer of vapor barrier.
More serious insulation is reflective insulation. The material consists of a layer of heat insulator, covered with a metallized film on top. Among the advantages are low thermal conductivity, excellent sound insulation, low weight, and resistance to moisture. Such material is easy to install. The disadvantage is that the material is used not so long ago and all its properties have not been studied. It is only known that this insulation is susceptible to corrosion.
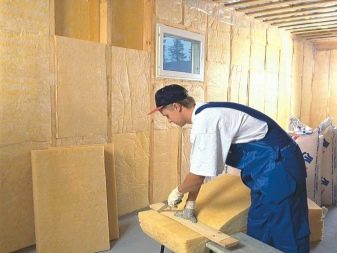
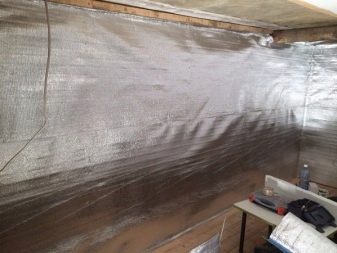
Basalt cardboard is a durable material that is distinguished by a high degree of resistance to temperature extremes, deformation and moisture. The material has low heat capacity and good sound absorption, is not afraid of fire. It is not cheap, but it is very high quality and will last for many years.
In addition, heat-insulating paint and "warm" plaster will help to insulate the garage.
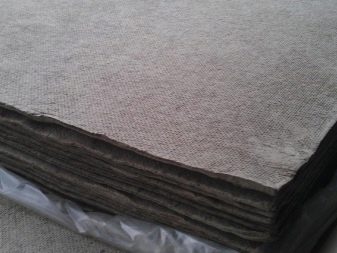
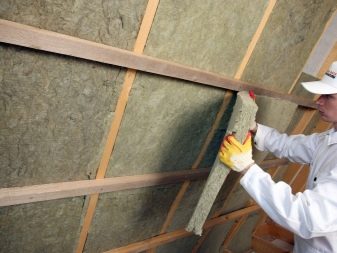
Finishing outside the building must combine resistance to external environmental influences and have a presentable appearance. The modern market offers a wide range of options that meet these conditions. The simplest and cheapest ways are joining, plastering, siding.More expensive methods are wooden lining, natural or artificial stones.
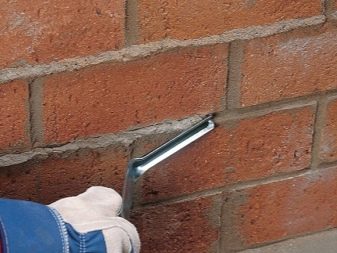

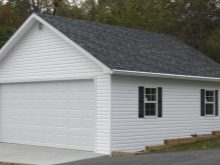
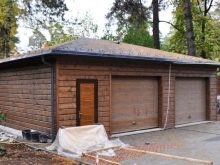
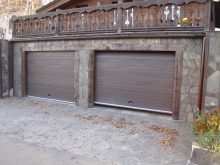
If the garage is two-story, the space between the first and second floors is covered with a precast concrete slab. It is advisable to do this with a hollow core slab, because it is easier to install and low in price.
Roof covering materials can be divided into two groups: soft and hard. The former are suitable for a flat roof, and the latter for a gable roof.
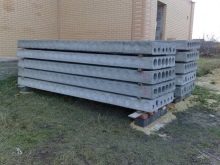
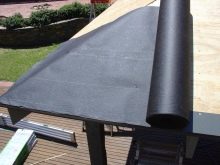
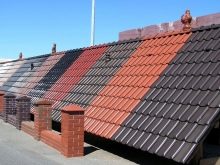
Soft include:
- Flexible shingles. The material lasts up to 55 years, is resistant to corrosion and decay and can be of any color. It is better not to use the material in the northern regions - under the influence of frost it becomes brittle.
- Roofing material. Service life is about 15 years. The material is cheap, frost and sun resistant.
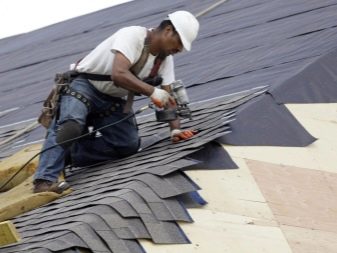
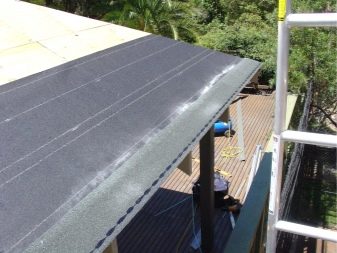
- The self-leveling roof serves for 22 years, is easily and quickly installed, and can be repaired. The application surface must be perfectly smooth.
- The welded roll roofing (waterproofing, glassy insulation) has been in operation for about 50 years. The material is durable, does not burn, it has good sound insulation, and is immune to temperature extremes. The only negative is the high price.
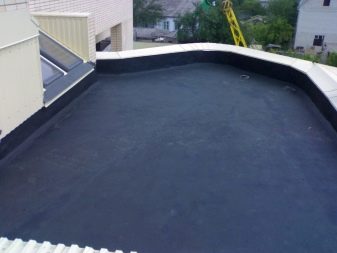
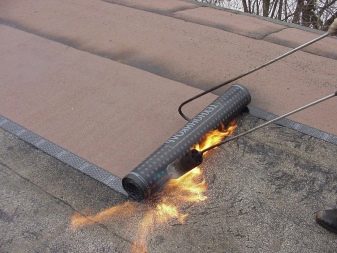
The tough ones include:
- Reinforced concrete slab - has a long service life, is also suitable for flat roofs, withstands a lot of weight. You can even set up a garden on such a roof.
- Flat slate - easy to install, inexpensive, does not lose its qualities in any climatic conditions. It is very easy to fix it.
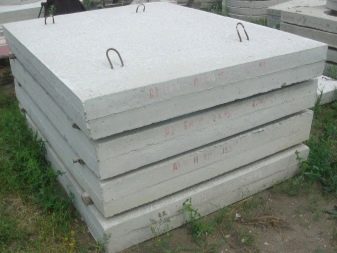
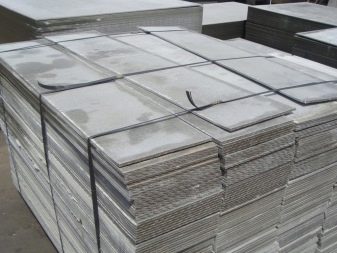
- Polycarbonate - lasts about 25 years, does not burn and does not react with solvents, is low in price. Such material is easy to install, resistant to temperature extremes, but under their influence it can slightly change its shape.
- Seam roofing - does not require a strong frame, is durable, resistant to mechanical damage and temperature extremes. Cons of the material - high price, difficult installation, low sound absorption.
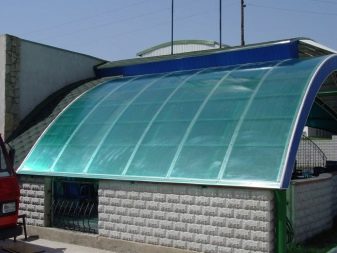
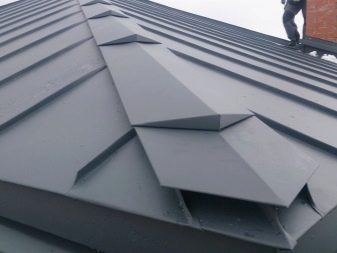
The garage needs electricity. Here you can use a self-supporting insulated wire (SIP).
There are several brands of SIP and they all have different properties:
- SIP-1, SIP-1A are resistant to ultraviolet rays;
- SIP-2 is used in the installation of power lines with voltage up to 1000 V;
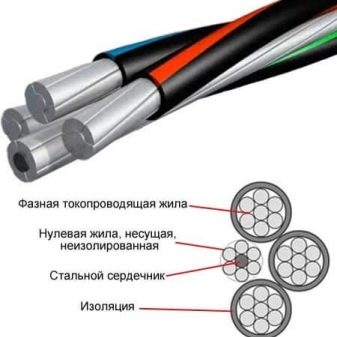
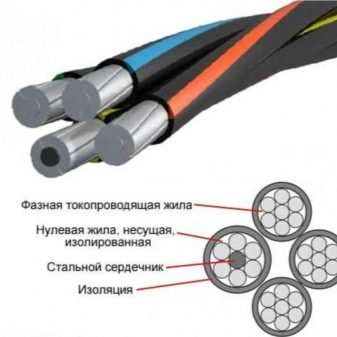
- SIP-3 is used for overhead power lines;
- SIP-4 is resistant to ultraviolet rays;
- SIP-5 is suitable for temperate and cold climates, resistant to high temperatures.
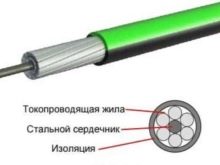
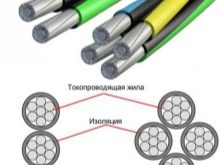
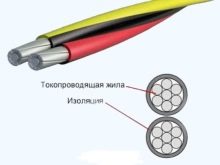
For storage and safe movement of building materials, wooden pallets are required. A white acacia, birch or boxwood pallet is a good choice.
To save money, you can buy a used pallet, the main thing is good quality.
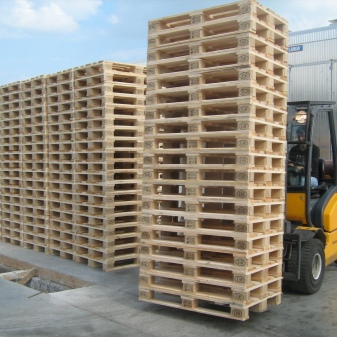
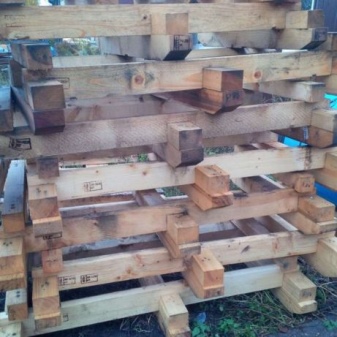
Construction process: main stages
After creating a drawing, choosing building materials and drawing up step-by-step instructions, you can start building.
"Pencil case" and "shell" do not require a solid foundation. First you need to make several separate sections and then assemble them.
Assembly steps:
- you need to drill technological holes in the structure;
- cover the finished elements with an anti-corrosion agent and paint them;
- assemble the segments into a common structure and fix;
- protect and paint all welding defects.
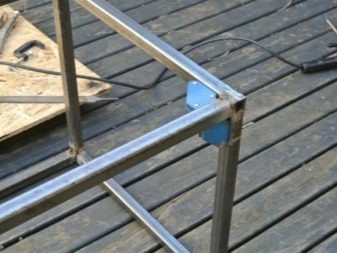
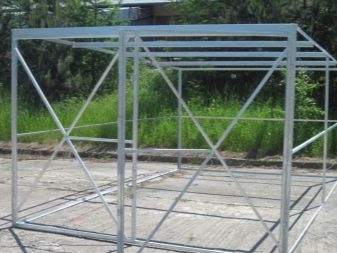
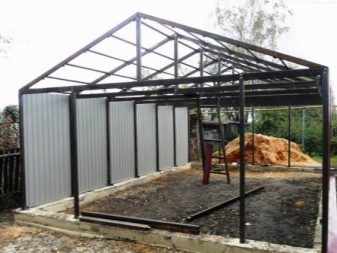
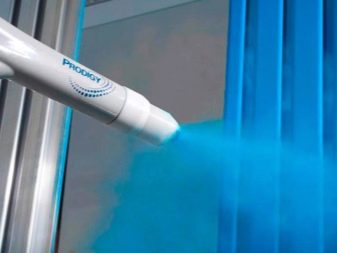
Electricity can be supplied to the garage. For this, a lamp and two sockets are installed, then the wires are passed through the corrugation. For work, double-insulated copper wires are taken.
Building a more complex structure begins with a solid foundation. For a garage, options such as a monolithic slab, pile material, tape shallow or buried foundation are suitable. If a pit or cellar is planned, then the best choice is a recessed tape. A garage with a high-quality foundation will last a long time and will not cause problems, so more attention should be paid to this stage.
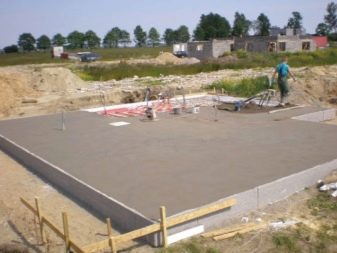
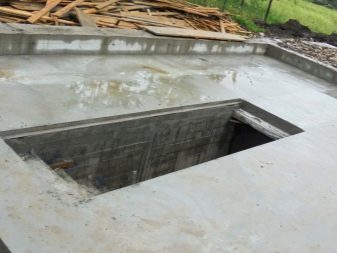
Separately, it is worth considering the construction of the pit. The size depends on the vehicle itself. For a passenger car, a width of about 70 cm is suitable, for a truck you need to add 20-25 cm to the standard size.The height depends on the height of the owner of the garage, but, in any case, it is better to make the garage a little deeper.
An important element is the plinth, its height ranges from 0.5 to 2 meters. There are two types of base: protruding and sinking. The first option is more elegant, but it will require the construction of an additional ebb along the protruding upper edge - this prevents moisture from entering. The second option is more practical and the building receives maximum protection from moisture.
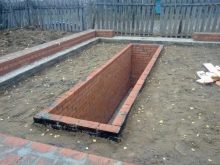
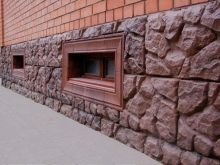
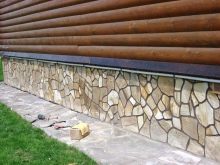
When erecting walls, two methods are used, it all depends on the chosen material. The first way is building in blocks. With it, the garage will not need to be heavily insulated, but additional finishing on the outside will be needed. The second way is wireframe. The frame is made of a metal profile pipe or a wooden bar. The advantage of this method is the rapid construction of the premises.
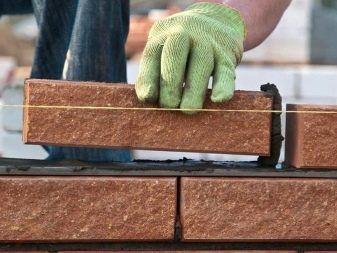
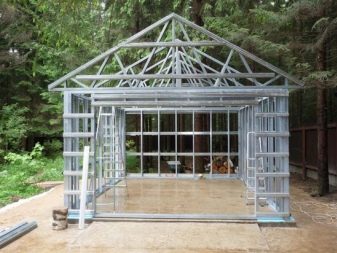
The next step is to prepare the gate for installation. First you need to make measurements. You need to measure the opening, paying attention to the distance from the right edge to the left. It is also necessary to measure the height of the lintel.
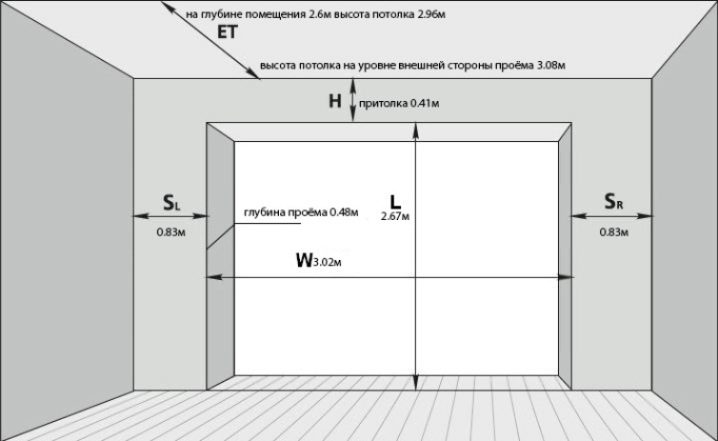
There are different types of garage doors: simple swing, sectional, automatic or manual. Most car owners prefer sectional ones. Such products are very comfortable, take up less space, are sealed and strong. But they are expensive and complex.
Before equipping the gate, you need to carefully read the instructions and properly prepare the opening. If the material is light, the opening is reinforced with a special metal frame. For a brick garage, such a frame is not required.
The room needs to be emptied, this will help to cope with the assembly and installation of the gate much faster and easier.
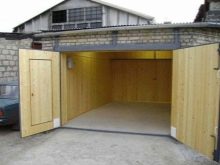
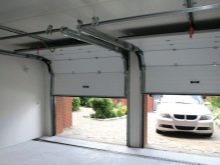
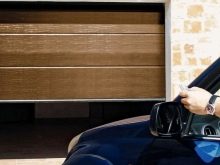
The next stage depends on the number of floors: if the garage is two-story, then it is necessary to overlap between the first and second floors with a reinforced concrete slab and re-erect the walls.
When building a roof, you need to be careful and follow safety precautions. The easiest way is to have a flat roof with a slight slope, about 15 cm. This way it will be better for precipitation to come down and drain. The only drawback of such a roof is the lack of an attic.
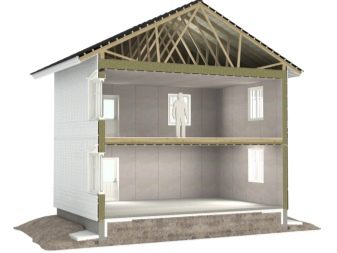
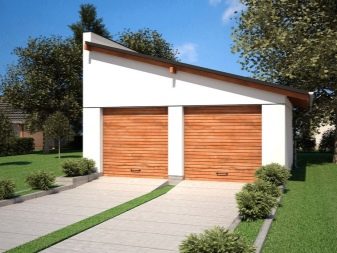
A gable roof will be more difficult to implement and it will take more roofing. But on such a roof it will be possible to make an attic with a recreation room. Such a roof also needs a heating system. Additionally, a canopy should be made, under it you can park oversized vehicles and protect the car from the sun and precipitation without corral inside.
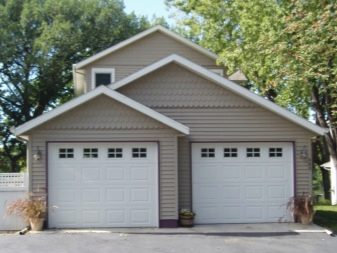
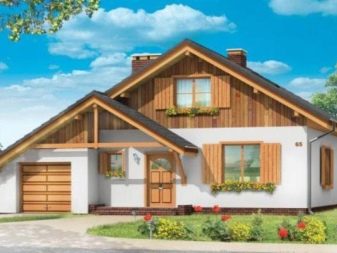
Ventilation should not be neglected. It is needed to remove moisture, remove harmful fumes. This is protection against rust of metal products and surfaces, creating a microclimate. The cheapest way is natural ventilation: air flows out through the supply and exhaust openings. But in hot weather, this ventilation does not work. Expensive installation methods are forced and combined ventilation. They ensure correct air circulation at any time of the year, and in winter they are even able to heat it up. In addition, they are easy to do-it-yourself installation.
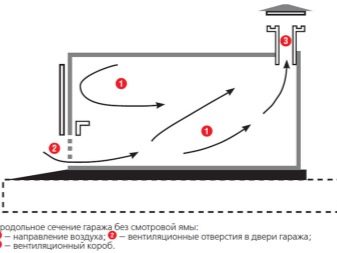
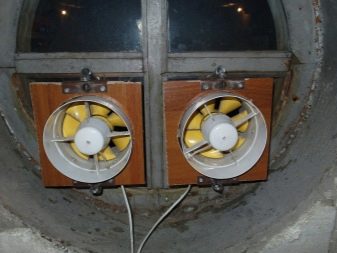
Then you can move on to interior and exterior decoration. It is necessary to take care of waterproofing, treat the floor and walls of the garage with special mixtures. For walls, Penetron will be an excellent tool, and the floor can be covered with polymer varnish or bitumen.
Before starting to coat the surface, it must be thoroughly cleaned and sanded.
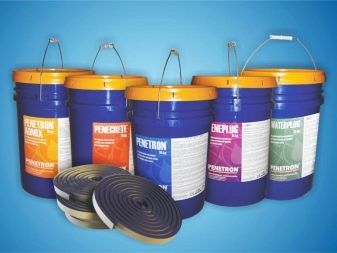
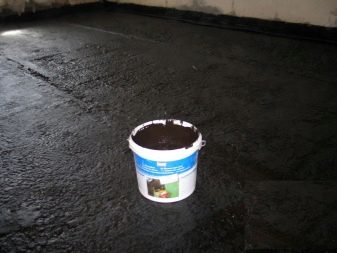
For the floor, materials such as paint, self-leveling compounds, ceramic tiles, wood or rubber are used. Walls can be clad with the same materials as the floor, or plastic panels can be used. The material must withstand temperature extremes and direct impacts. And the ceiling must be resistant to fumes.
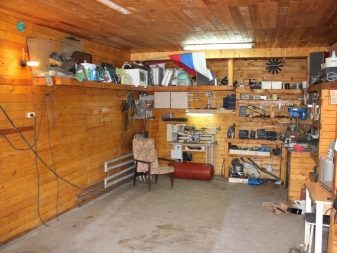
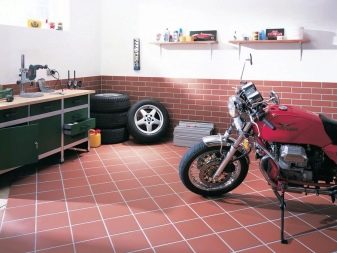
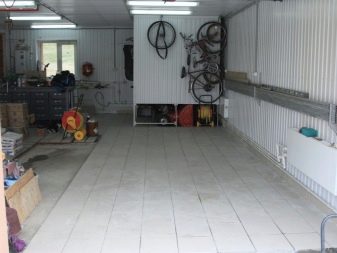
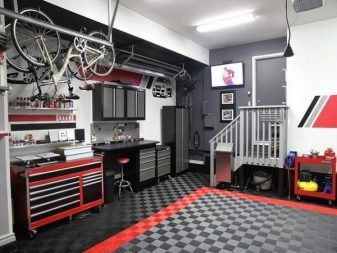
Exterior decoration should not be afraid of bad weather. The quality of the material should be carefully monitored and the cladding should be reliably performed.And you can decorate the look with decorative elements.
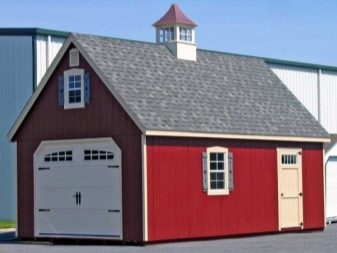
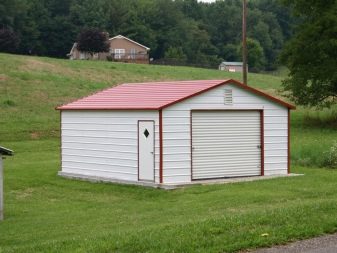
The workflow for an underground garage is very different. At the planning stage, you need to decide whether the building will be fully or partially in the ground. Next, you need to dig a pit of the required size and place the slabs on the bottom or fill with reinforcement. It is important to take high quality concrete. With the help of reinforced concrete slabs, the foundation of the walls is formed, then the overlap is installed on the side slabs.
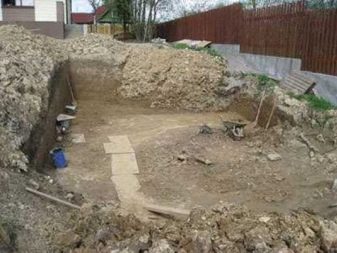
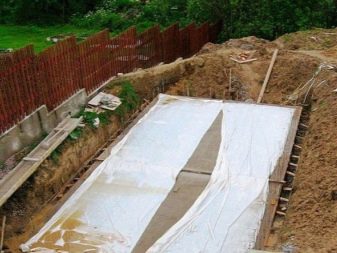
Ceilings and walls are covered with waterproofing, reinforcement mesh is installed on them and plaster is laid. Additionally, the surfaces are treated with antifungal agents and primed.
After that, you can proceed to the installation of garage doors and the formation of the driveway.
It is important to take into account several conditions:
- the slope of the entrance should be 140-150 degrees;
- there should be retaining walls on the sides, they prevent soil collapse;
- the length of the driveway depends on the length of the garage - the longer it is, the longer the driveway;
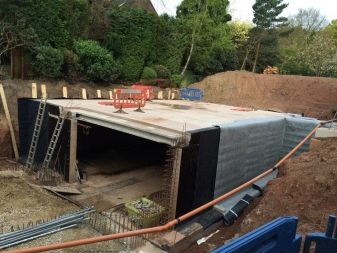
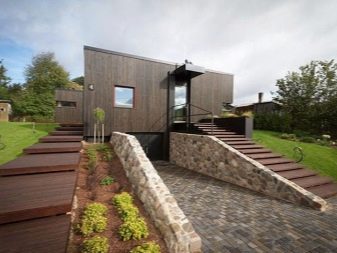
- for a safe exit and descent into the garage, a path with a handrail should be made;
- you cannot use sliding materials for the track, but in addition you need to make braking serifs, they will come in handy during rain and ice;
- near the gate, you need to make a storm drain with heating to prevent water from solidifying;
- after the completion of construction, heating, electricity is carried out, ventilation and additional waterproofing are installed.
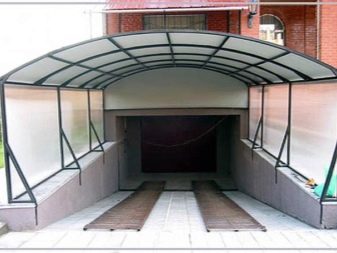
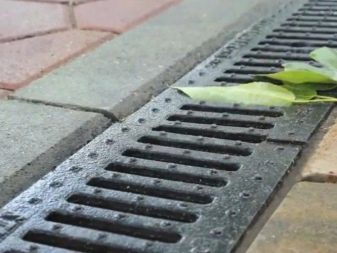
Waterproofing is carried out in several stages:
- a drainage system is installed on the outside of the garage, and the surface is once again covered with waterproofing material;
- a filter cushion is formed on the sides and under the floor;
- the final stage is interior decoration. It is better to use a material that is waterproof and warm.
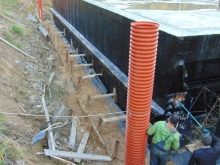
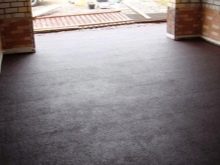
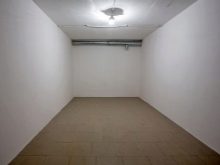
Helpful hints
Here are some more tips for creating a cozy garage:
- the house and garage will look more harmonious and more beautiful if they are designed in the same styles and colors;
- if there is an inspection pit in the garage, then a small service can be organized there, having previously received official permission for it;
- from the garage you can make a small workshop and do what you love or hobby;
- a basketball hoop can be equipped outside;
- the garage can be rented out and receive a good monthly income;
- you can organize the space using various shelves, holders and stands;
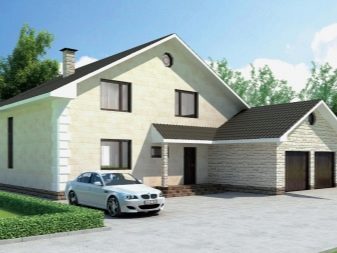
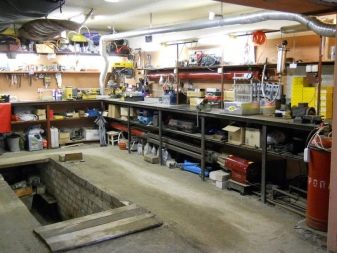
- curtains on the shelves will add extra coziness to the interior;
- a folding chair and chairs will allow you to gather here with friends, they will also be useful for a snack during a long stay in the garage;
- shelves and racks should be done at a distance of 20 cm, so it will be easier to clean the floor;
- a single-slope screed at an angle and drains for water leaving the premises will make it possible to wash the car without driving it out into the street;
- signed boxes make it much easier to find the right part;
- for additional insulation in winter, you can use an electric heater or a stove-stove.
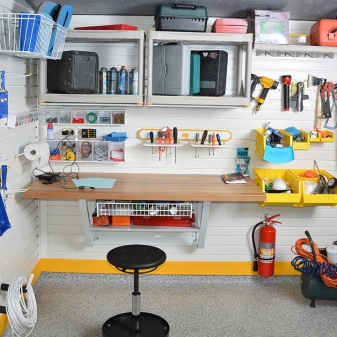
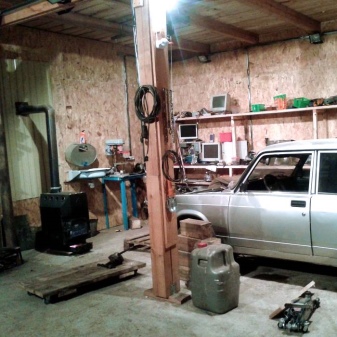
Considering all the recommendations, advice and choosing high-quality material, you can build a strong and reliable garage from any material with your own hands. Such a garage will serve for many years.
You can learn how to build a garage with your own hands from sandwich panels from the video below.
I like it. But capital construction is expensive. They are offered from fences and frames (including concrete) - cheap, reliable enough. But the choice of location? It would be interesting.
The comment was sent successfully.