Bath floor: types and features of installation
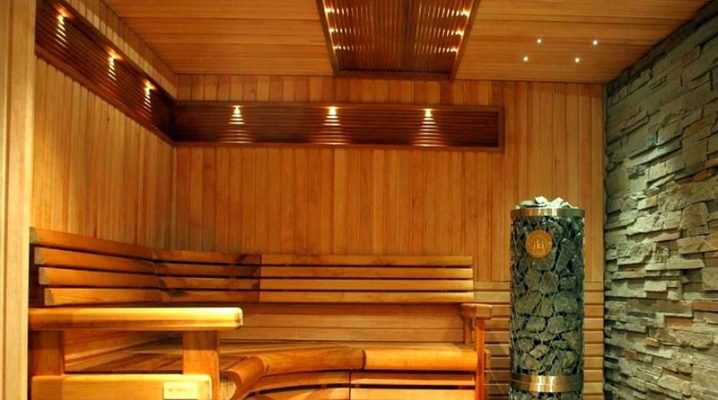
The floor in the bath has a number of functions that distinguish it from the floor in living rooms. It not only provides free movement with constant moisture, but is also part of the sewer system. Therefore, before installing such a floor, you must familiarize yourself with the features of its installation.
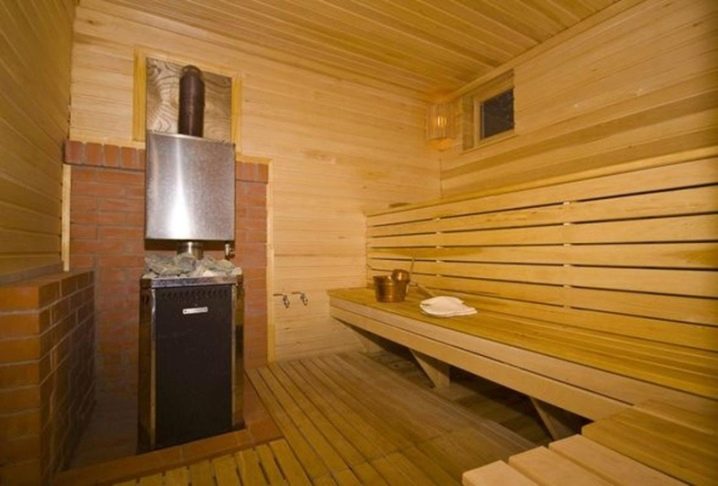
Peculiarities
Before choosing a floor for a bath, you need to take into account some of the nuances. The first thing to consider is in what season the premises will be used. If the bath will be used all year round, then showers, a dressing room, an additional steam room and rest rooms are usually placed in it. In such a bath, a capital floor is installed: an insulated coating with ventilation and drainage. It is enough to make the floor in the summer sauna leaky.
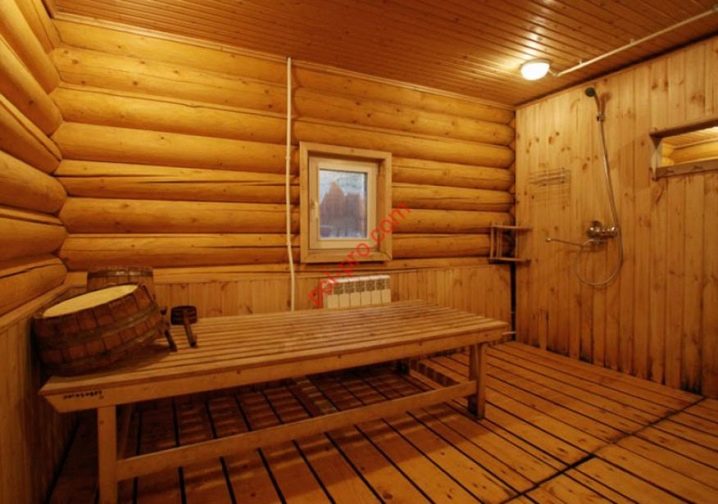
The installation of the leaking floor is carried out by laying boards measuring 1.5 meters by 50 millimeters. Boards are stacked on top of logs - beams with a diameter of about 150 mm. When installing a lag, it is necessary to take into account the type of base. For example, for a columnar foundation, the logs must be supported on a foundation beam. The logs are laid sequentially, starting from the shortest wall, the beams are placed at a distance of about 60 cm. The contact points of the log with the foundation are treated with bitumen mastic or roofing material to ensure insulation.
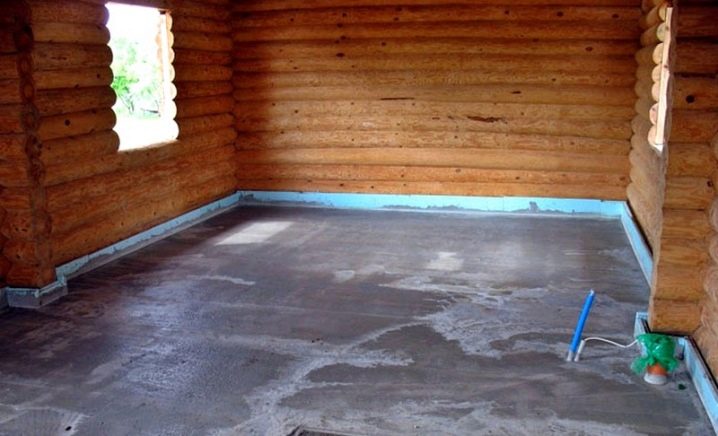
Next, the subfloor is arranged - a layer of soil is laid on top of the boards. The material and its amount are selected based on the type of base soil. If the soil absorbs water well, then the subfloor is covered with a layer of rubble about 25 centimeters thick. Clay soils, which swell when wet and do not conduct moisture well, must be covered with a material that ensures water drainage. After that, floor boards are laid, leaving a distance of 2 cm around the entire perimeter.
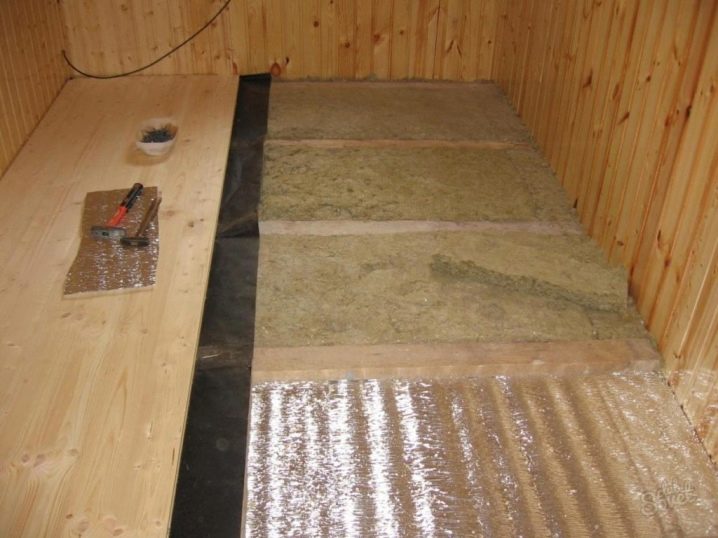
There should also be a small gap between the floorboards. Planks are fixed on beams with nails. To provide protection from dampness and prevent the development of fungus, the coating is treated with linseed oil.
A leaking floor is also called "cold" because its temperature is always low. The disadvantages of such a coating - it is recommended to install it only in regions with a mild warm climate. Premises with such a floor are almost impossible to use in the cold season, because it cannot be insulated. However, there is an option to install the stove below floor level. This design allows the boards to warm up and better protect them from decay.
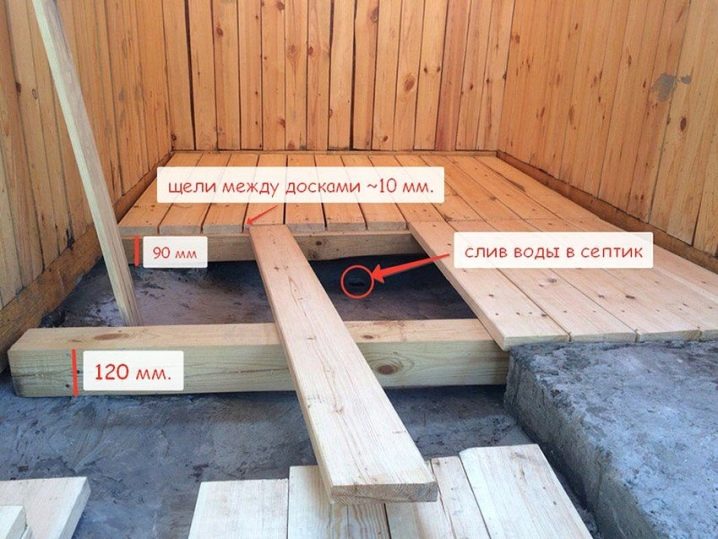
The process of creating a non-leaking floor is technologically more complex and resource-intensive. Before laying the logs, the installation of the subfloor is necessary. Next, the wooden flooring is covered with layers of waterproofing coating. To reduce heat leakage from the premises, the floor must be protected with mineral wool or fiberglass insulation boards. So that natural insulation materials do not lose their properties under the influence of water, a moisture-resistant coating is laid on top.
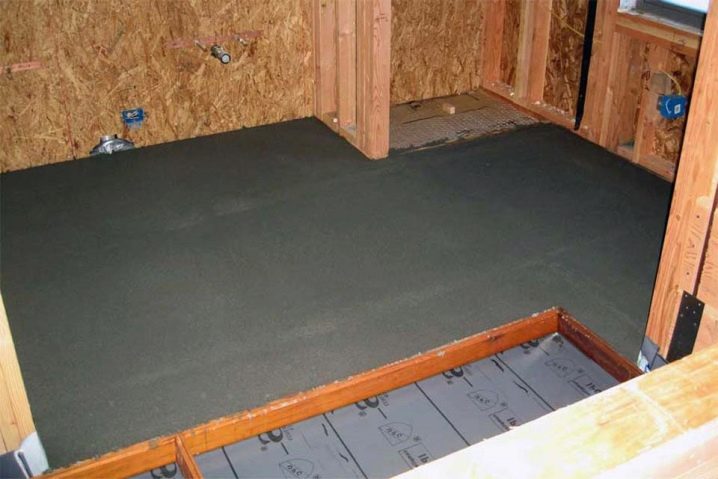
The subfloor is poured with a layer of bitumen and prepared for the installation of the floorboards. The technology of laying the boards depends on the purpose of the room. The floorboards in the steam room should face the direction of the incident light beam. In the dressing room, the flooring is laid in the direction of travel. It is important not to forget to leave a space of at least one centimeter along the contour of the room.This distance provides ventilation.
A Russian bath with a warm floor resembles a pie in terms of the drainage device. The boards are placed at a slight slope, which ensures the drainage of the liquid into the built-in collector. Further, moisture flows out through the pipes and is removed outside the extension. The advantages of underfloor heating are that the coating is additionally protected from the cold, the moisture removal system allows you to increase the shelf life of the boards.
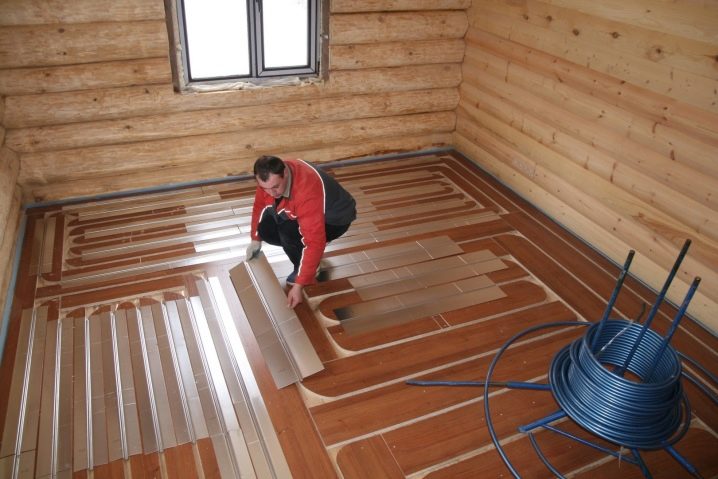
Which coverage should you choose?
The room of a classic Russian bath has high humidity, and the temperature can reach 65 degrees. Under such conditions, there is a high probability of floor rot, especially wood flooring. It is important to understand that each room of the bath has different operating conditions and the coating material and operating technology can differ significantly in each room. In addition to individual characteristics, the floor must have some general physical and mechanical characteristics.
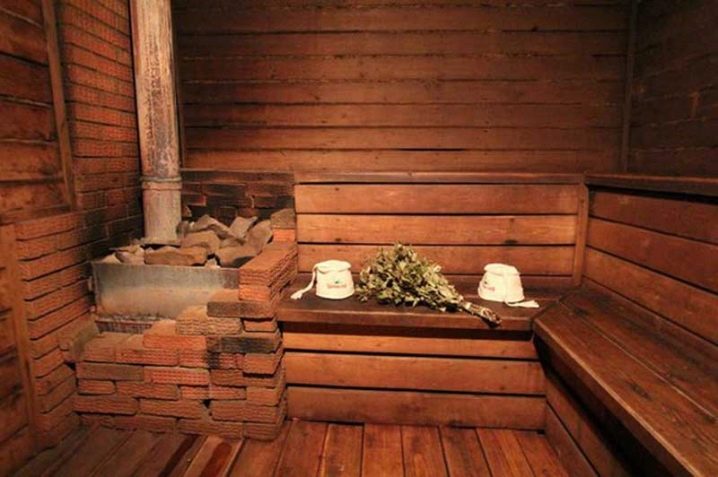
The coating must be resistant to a critical temperature drop: from above, the floor interacts with hot water, and from below, cold soil acts on it. Also, the flooring must withstand both mechanical stress and contact with chemical reagents of detergents. An obligatory characteristic of the coating is resistance to constant interaction with moisture and saturated water vapor. It is important to remember that the floorboards must be non-slip and require little maintenance. In addition to the above mechanical properties, the floor in the bath should look aesthetically pleasing.
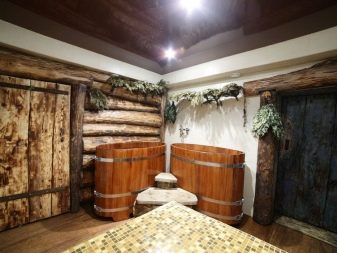
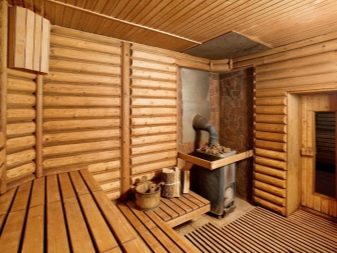
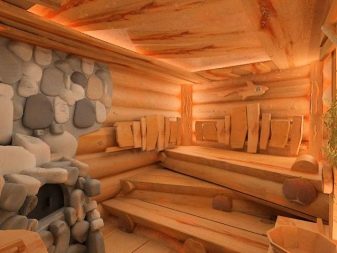
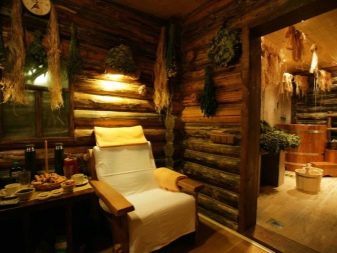
The classic flooring is wood flooring. This method of laying the floor in the bath is still used today. This is not only a tribute to tradition - wood has a high heat capacity and a beautiful appearance. A significant disadvantage of the boards is low moisture resistance: the coating is prone to decay and requires additional protection. Before deciding to install a wooden floor, it is necessary to familiarize yourself with the characteristics of each tree species. For example, oak becomes too slippery when exposed to moisture.
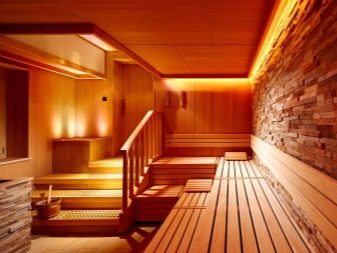
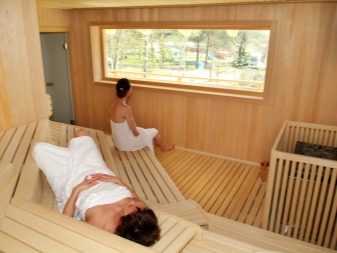
Concrete flooring is no less popular than its wooden counterpart. The cement screed has a high mechanical strength, which ensures a long service life. It is important to understand that a topcoat must be laid on the concrete base. Craftsmen advise using tiled masonry. Ceramics are easy to install and operate. A significant disadvantage of a concrete floor is the need for thermal insulation. Also, such a floor must be laid with a slope to ensure drainage of water.
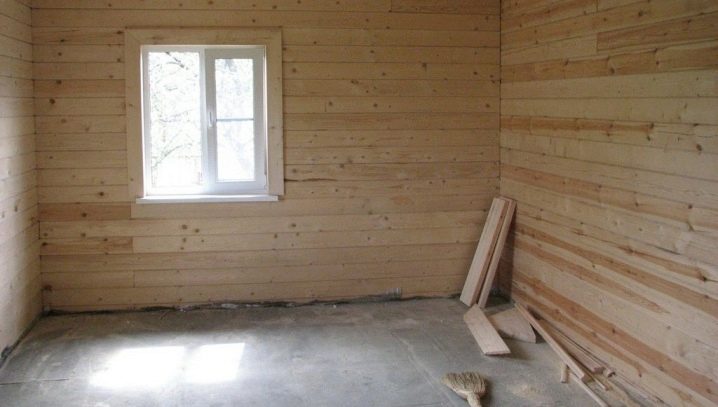
During the construction of baths, more and more preference is given to laying stone and tiled floors. Ceramics perfectly imitate natural stone and have a relatively low cost. In addition, such a coating is durable and waterproof. An important point is that the joints between ceramic fragments require additional processing to protect against moisture and prevent the formation of fungus.
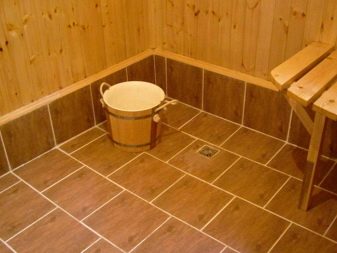
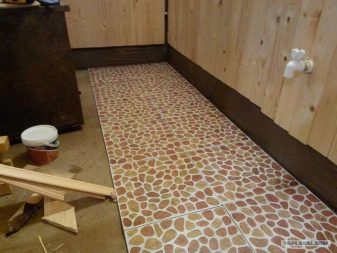
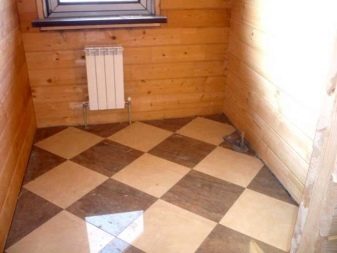
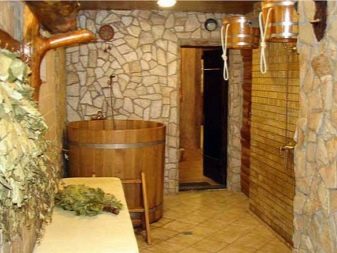
For the correct choice of flooring, you need to take into account all the operational features of the selected room. The steam room can be fitted with concrete, stone or ceramic floors - these materials can withstand extreme conditions. It is unacceptable to use coatings containing formaldehyde. When exposed to water and high temperatures, such materials release toxic substances.
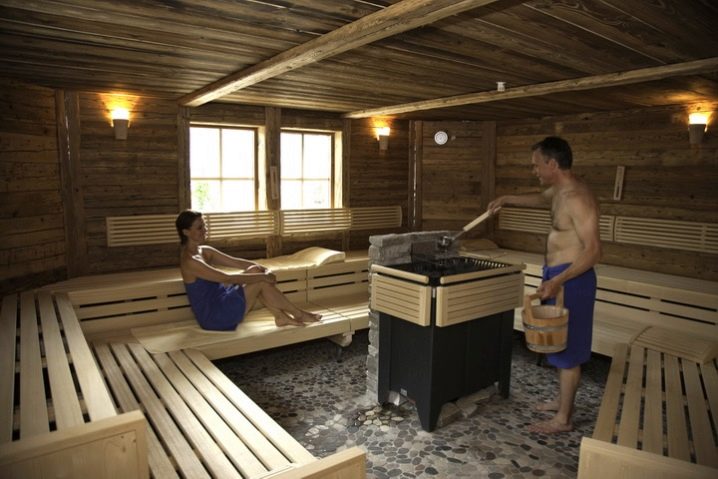
If there is a desire to decorate the floor with paint or varnish, then some restrictions must be taken into account. The safest way to decorate wood flooring is to use water-based or dispersion acrylic paint. The use of oil paint or alkyd composition is strictly prohibited in the steam room.
The requirements for the floor in the washing room are not as high as for the floor in the steam room. However, the spill coating must withstand prolonged contact with water and detergents.Floors must also withstand extreme temperature fluctuations. These requirements are fully met by ceramics. Wood is also actively used in the washing room, but it must be treated with a special impregnation or varnished.
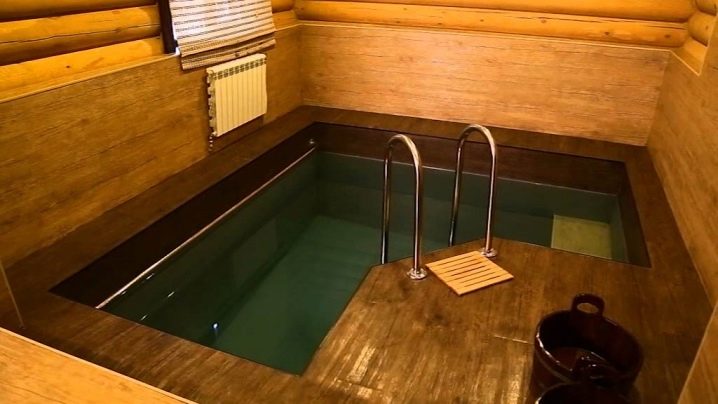
The floor in the dressing room practically does not come into contact with water and steam, so there is no need to increase its water resistance. There is a firebox in the dressing room, so the floor covering must be protected from fire and overheating. As a rule, boards are laid here. A metal plate 60 by 90 centimeters in size is mounted in front of the firebox. This device is necessary to protect the floor from falling sparks and fire.
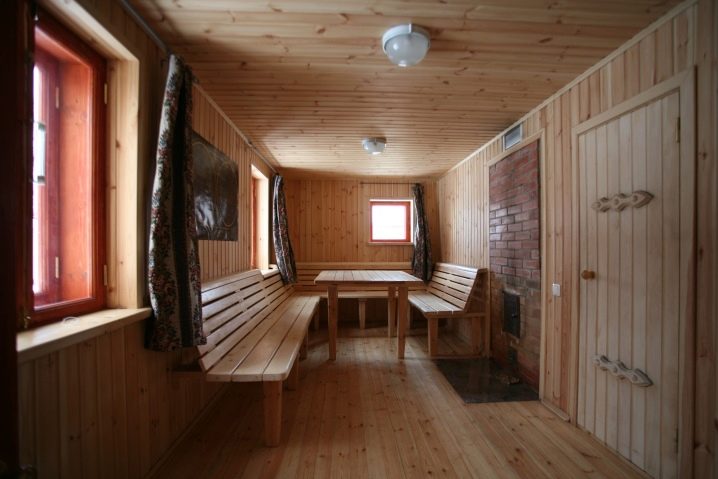
In the rest room, you can lay carpet or linoleum. The floors in this room should be comfortable and cozy. The main requirement for such a coating is that it retains heat well. Since the rest rooms do not come into contact with moisture and do not withstand temperature extremes, they do not require additional protection. Also, they can be placed on the floor or shelves to accommodate the legs, which will add comfort.
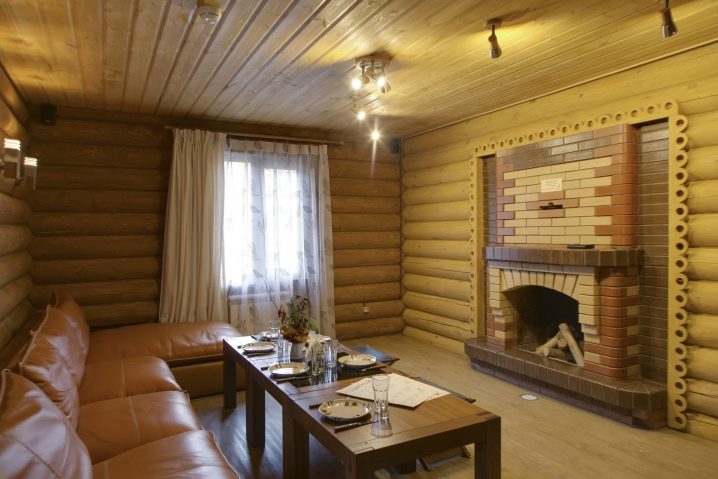
Required tools and accessories
In order to obtain a high-quality floor with a long service life, it is necessary to follow the laying technique and the technology for preparing the materials. The success of the installation largely depends on the correct choice of instrumentation. The floor can be installed under the guidance of a specialist or by yourself.
Some of the tools needed to build a concrete floor in a bath:
- The correct screed cannot be laid without the use of a special rake. These devices are used to level the concrete mass during the laying process. It is important to understand that the coating should be as even as possible: violations in technology can lead to serious consequences.
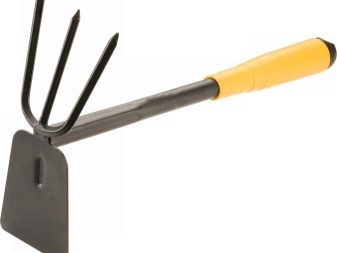
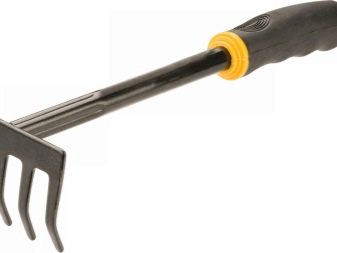
- A laser or water level will help you get the surface of the required flatness. It also allows you to vary the angle of inclination of the boards. The grooves for water drainage must be smooth: no level difference is allowed along the flow of the liquid. Such moments must be corrected both at the initial stages of installation and during the laying of the slabs.
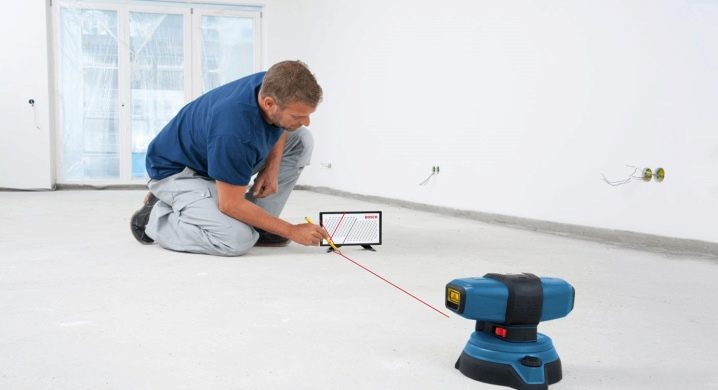
- Trowels are necessary to spread the cement over the entire surface from the far corner of the room to the edges. With the help of trowels, impregnation or varnish is also applied when finishing the surface. Trowels come in both pointed and semicircular edges. The rounded edges of the tool do not leave visible marks on the screed.
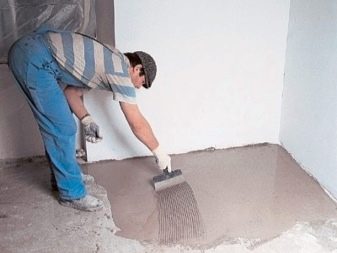
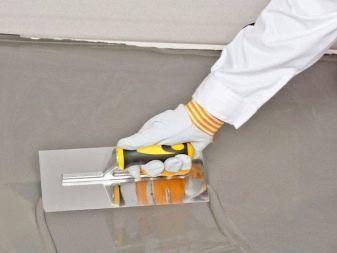
- Cement grater. This device is necessary to obtain a flat surface. It is necessary to make circular movements on the surface of the laid mass. With their help, excess material is also removed and an even coating is obtained.
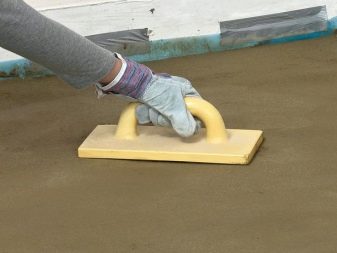
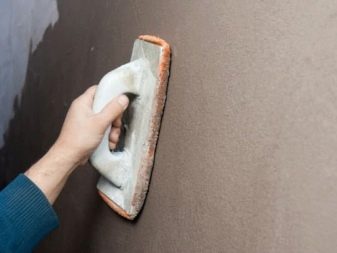
- Trowels are also needed to get a flat surface. Thanks to their design, they are able to cover and smooth a larger area than floats or trowels. The trowels are used for the global work of rolling cement over the entire surface. Among such tools, one can distinguish angle-type trowels - they are used to obtain a smooth coating at the junction of the floor with the wall.
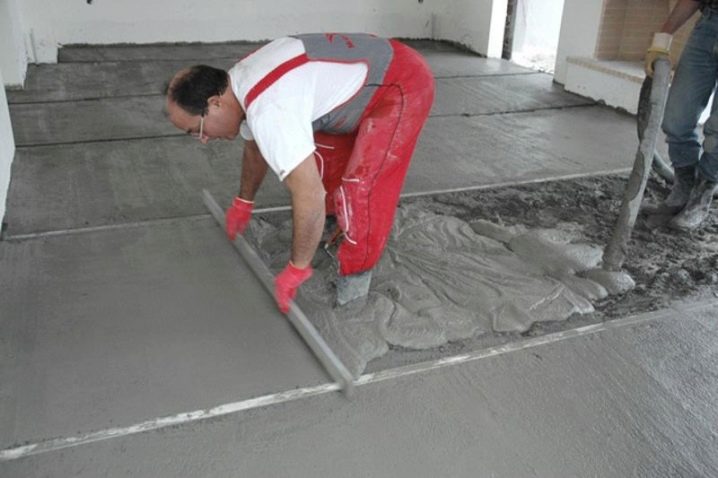
- In order to qualitatively mix expanded clay or expanded clay concrete, you need a concrete mixer and a container for mortar. The mixing technology depends on its composition and installation method. Before working directly with cement, it is necessary to familiarize yourself with the technology and mode of preparation of the mixture. This process can be done manually, but there is a risk of getting a non-uniform mass. An incorrectly mixed composition will not provide the required performance properties of the floor.
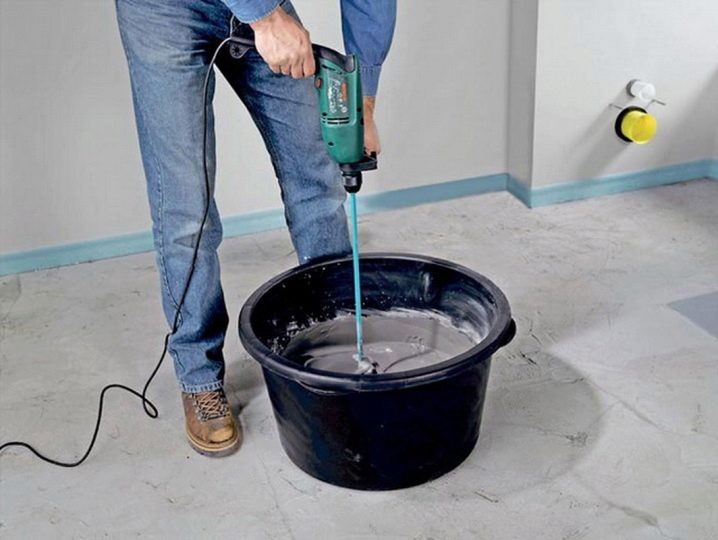
- Also, don't forget about simple tools. The shovel will greatly facilitate the process of spreading the concrete mass over the surface. A velcro towel or any other rag material is essential for cleaning the tools during use. A smooth screed will only work when working with cleaned equipment.You also need to have a container of water on hand.
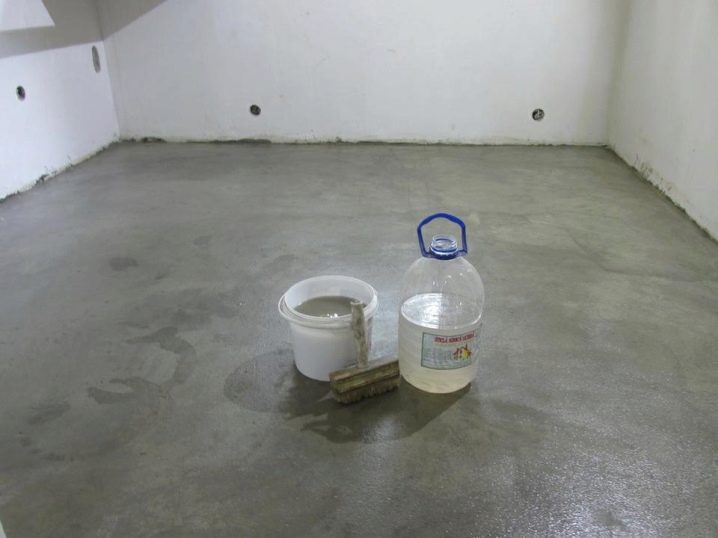
A different set of tools is required to install a wooden floor.
- Metal profile for laying boards. A special grid is mounted from small steel gutters, on which the boards are laid. Such a frame is necessary for the sauna floor to be laid flat and firmly in place. Profiles are sold complete with special fasteners.
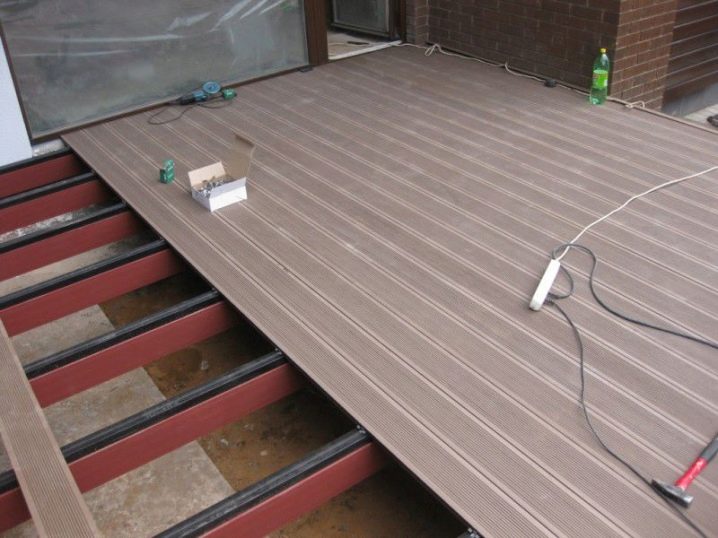
- An electric screwdriver and drill are required to secure the boards. They can be replaced with a metal hammer, but this will take a lot of time and effort. In addition to the usual screws, staples are used to fix the planks.
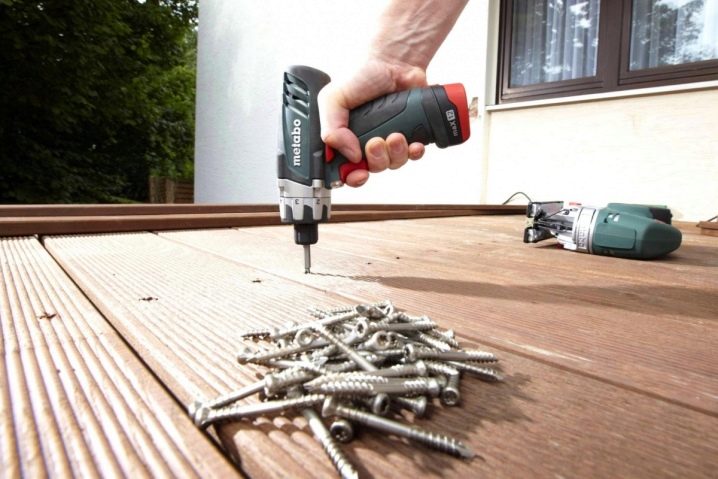
- To obtain the required size beams, use an electric plane and a hacksaw for wood. Sawing wood is quite dusty, so craftsmen recommend laying a rug or newspaper sheets on the floor of the working area. This will significantly reduce the time for subsequent cleaning.
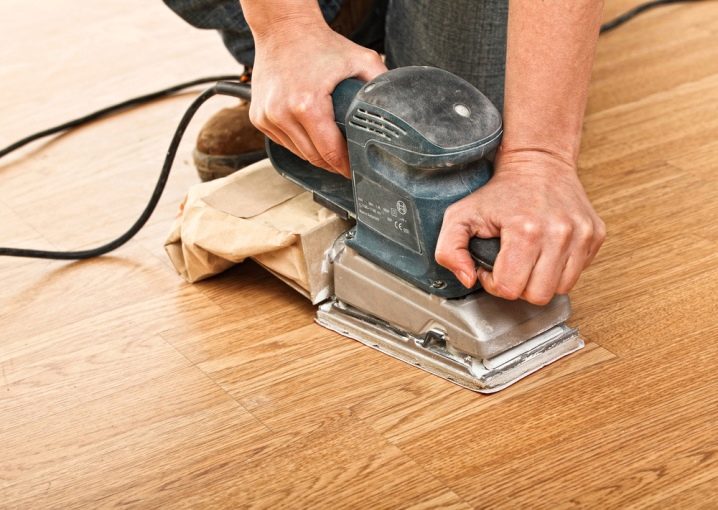
- In any work on laying the floor, you cannot do without a level. The laser device is much easier to use and helps to achieve an even coverage or the desired slope.
- The finish wood layer often needs to be varnished or painted. To do this, you need to stock up on rollers and brushes. Also, many materials are sticky and toxic, so all work must be carried out with gloves.
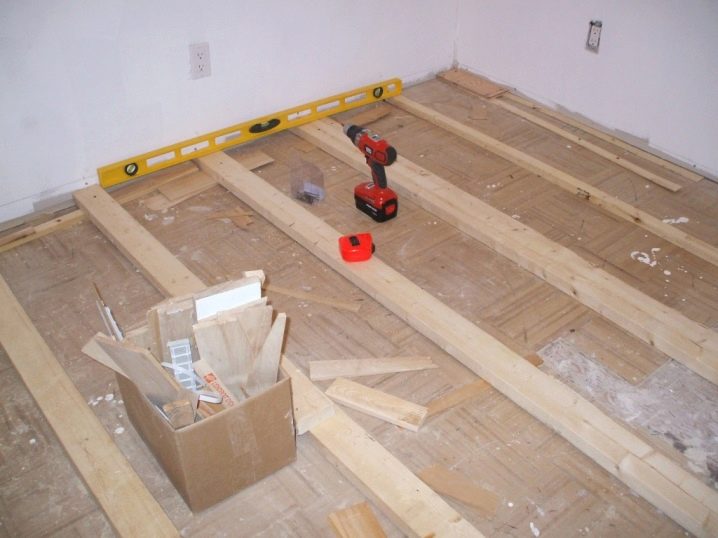
How to do it yourself?
The device of a leaking floor begins with the installation of lags. These can be wooden beams or metal beams. Before installing, the logs must be treated with a special antiseptic that increases their corrosion resistance. The choice of antiseptics is great, but some people prefer to use waste engine oil as an analogue. If wood beams are chosen for the lag device, then they must be dried. To do this, the wood is left for some time in a room with a humidity of 10 to 12 percent. To save time, you can buy ready-made wood after drying in a chamber.
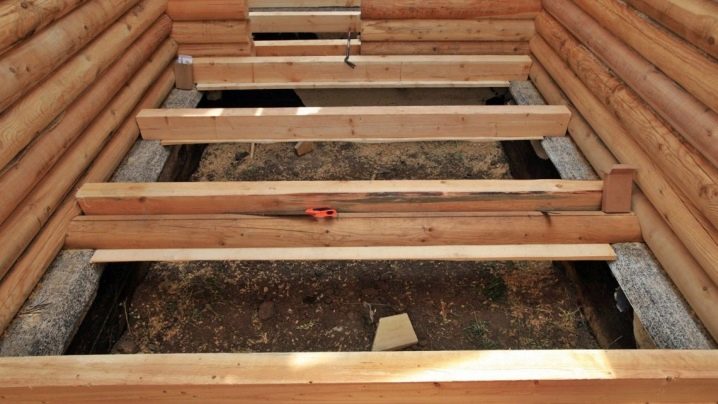
The logs are laid parallel from the smallest wall. If the room in the bath is large enough, it is recommended to create a stiffening frame. For this, reinforced concrete piles are installed under the logs with a step of no more than one meter.
There is a step-by-step guide for proper lag laying:
- The top layer of soil must be removed from the installation site. Next, lay out a layer of sand or crushed stone with a thickness of 10 to 15 centimeters and reinforce the system with a mesh.
- Piles are laid from bricks or fragments of a reinforced concrete slab. This design will provide the base with the necessary bearing capacity.
- The system must be treated with bitumen mastic to protect it from water.

The anchored piles are covered with two layers of waterproofing. Sheets should not be stacked too close to walls. It is necessary to leave a gap of at least 4 cm around the entire perimeter. This will ensure ventilation of the resulting structure.
Next, the device of the water drainage system is carried out. Moisture must be drained away from the foundation. In order to correctly equip the drainage system, it is necessary to familiarize yourself with the characteristics of the base soil. If the soil absorbs moisture well, then it is necessary to remove a layer of earth from the entire area of the bath and cover the surface with rubble. On soils with a low cultivation capacity, you need to dig a hole about 40 cm deep and conduct a moisture removal system into it. A special clay backfill ensures an even flow of water. With this method, floors must be laid at a slope of 10 degrees towards the water intake.
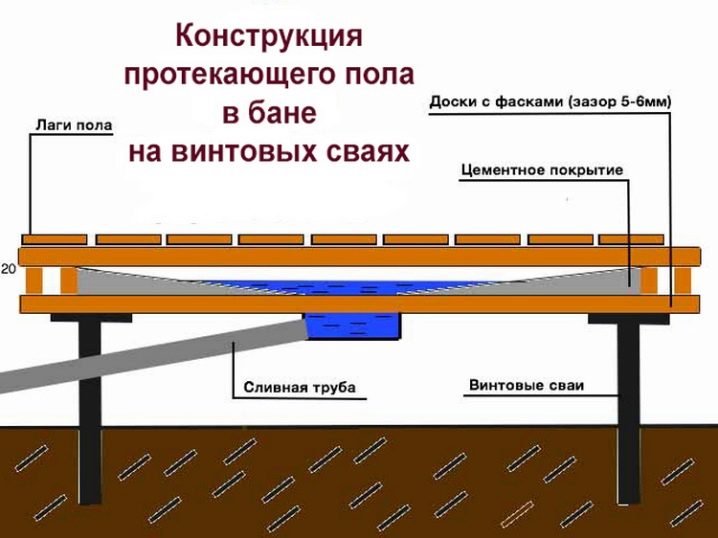
Underfloor heating boards are processed - cut from the front side and leveled. A gap of two centimeters is left between the masonry and the wall for natural ventilation. Boards are laid at right angles from the location of the lag. This technology provides the necessary strength of the future floor. It is necessary to maintain the same distance between the planks: masters advise using fragments of plywood for these purposes.
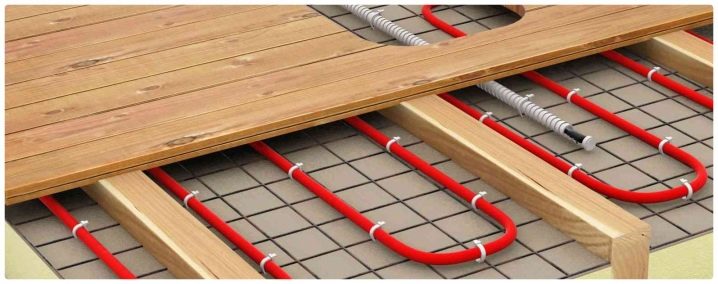
Warm floors can also be laid on logs. By the previously described step-by-step actions, beams or steel pipes are laid. To obtain a slope of the surface in the logs, cuts are made of four millimeters. It is not allowed to cut logs adjacent to the walls. The underfloor heating drainage system is excellent. A hole is dug between the two supports with a depth of at least 300 millimeters and with dimensions of 400 by 400 millimeters.
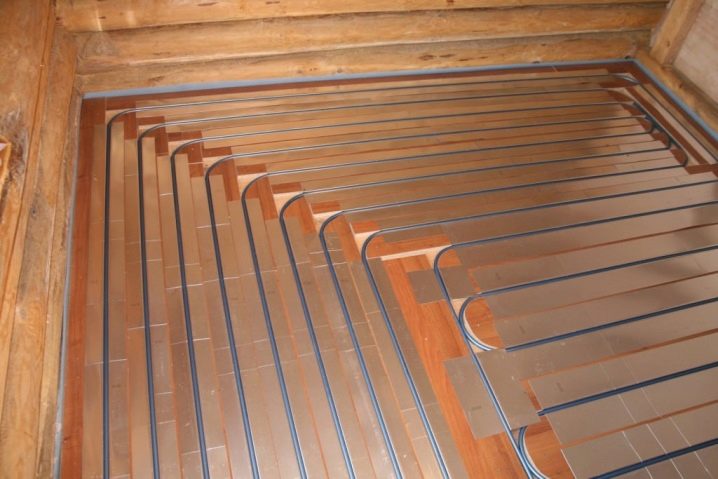
The walls of the resulting pit must be reinforced with concrete and coated with bitumen. The installation of the drain pipe is carried out at the bottom of the pit with an indent of two centimeters. The drainage pipe must be at least 15 centimeters in diameter. PVC is perfect for these purposes.
The boards are laid starting from the draft layer. This is followed by an overlapping waterproofing coating. The joints are coated with a small amount of bituminous mastic or glued with tape. After fixing the waterproofing, a layer of insulation is laid. In this case, the craftsmen are advised to pay attention to mineral or ecological wool, expanded clay slabs. A more ecological type of insulation is a mixture of sawdust with PVA.
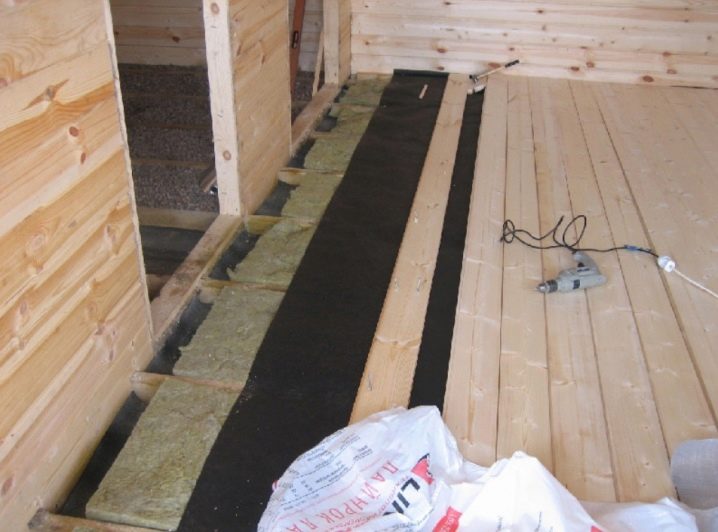
A vapor barrier must be placed between the finishing coating and the insulation. It is also important to leave a gap of at least fifteen millimeters between the layers: an exhaust pipe is drawn through the hole. The boards of the final layer should not have crevices in the joints, therefore builders prefer a tongue and groove board. It is necessary not to forget about the installation of the drain system.
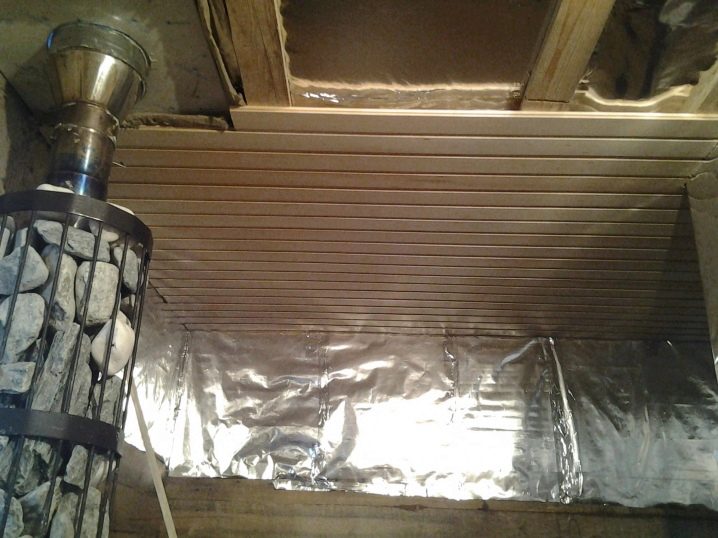
The concrete screed is laid in several stages. The first concrete layer is poured no more than six centimeters high and left not to dry completely. Thermal insulation of standard thickness is placed on a slightly damp layer. To provide the coating with the necessary rigidity, the insulation is covered with a reinforced mesh. The last layer of filling is laid at an angle of 10 to 15 degrees to ensure drainage.

The finishing layer, as a rule, does not exceed nine centimeters in thickness. Further, the surface can be decorated with ceramics or plank masonry. It is important not to forget that the coating must be resistant to temperature extremes and have a given strength. After installing the floor, the walls are polished.
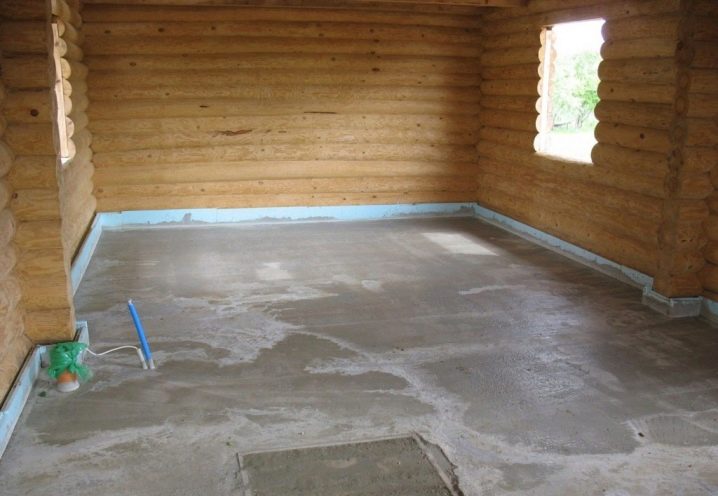
Wood
The plank flooring is perfect for leaking floors in the steam room. Wood has good technical characteristics and requires relatively little labor. Masters advise completely newcomers to focus on the device of a cold floor. There is no need to create an insulated "pie" of the foundation and the laying of utilities. A leaking floor in a steam room requires only simple drainage.
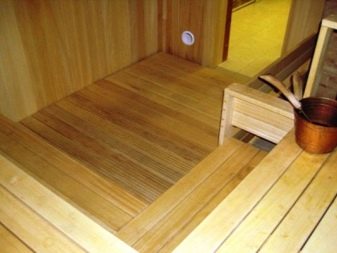
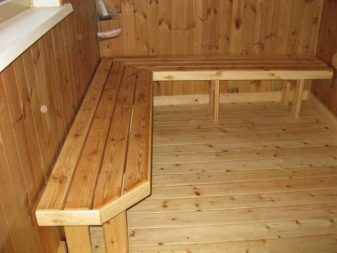
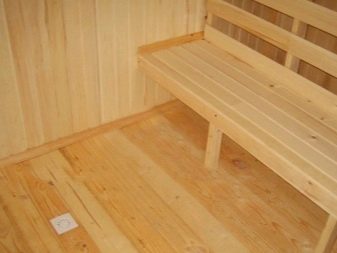
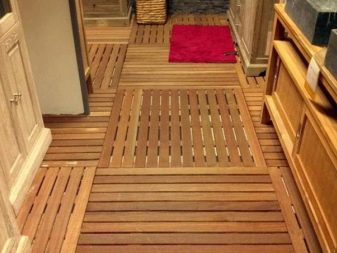
The flooring does not need to be fixed to the joists, as the flooring needs to be regularly detached and dried in the open air. This design helps to keep the material in proper condition, even with frequent contact of the floor with hot water. The board requires replacement 4-6 years after commissioning. If, nevertheless, there is a desire to fix the coating on the logs, then the boards must be carefully treated with an antiseptic. A cold floor made of larch or pine is considered the most optimal in terms of price-quality ratio. The oak flooring is not rough enough and can cause injury.
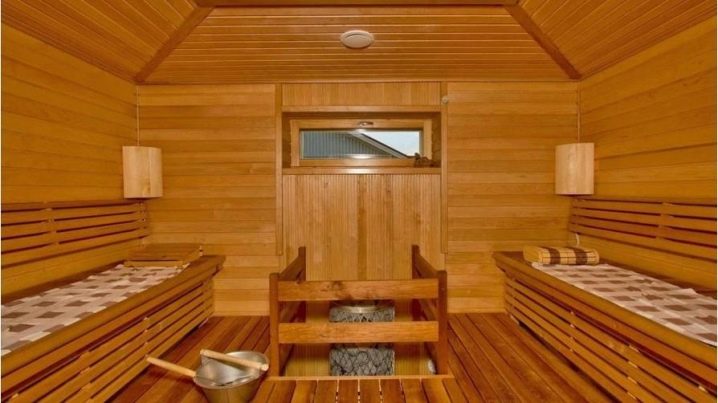
The non-leaking wood floor is suitable for year-round use. In the washing department and the steam room, such a coating will last up to 10 years, if you correctly perform the arrangement of the draft layer and do not neglect the installation of insulating materials. It is not recommended to paint the boards. The chemical composition can clog the pores of the wood, giving the coating a long-lasting chemical scent.
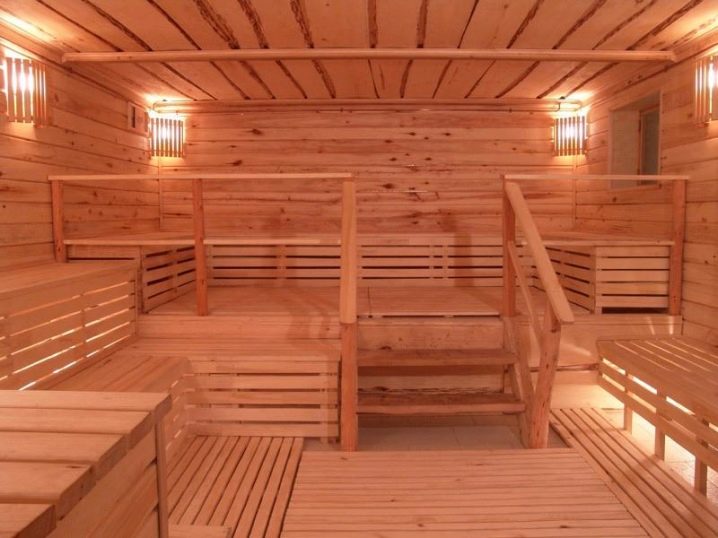
Also, the paint does not help to protect the boards from decay. Craftsmen advise to leave the surface clean, but sand well. Natural wood has a pleasant smell, and the aroma of pine needles is considered beneficial to health.In order to protect the coating from decay, special compounds are used. But an important point is the drainage device.
Concrete
Concrete has a long service life, which makes it the leader among materials for floor installation in a bath. A properly laid coating can last up to 50 years, does not require special operating conditions. The concrete screed is not prone to rotting, because microorganisms cannot develop in concrete. Caring for such a floor does not require special measures or the purchase of expensive products.
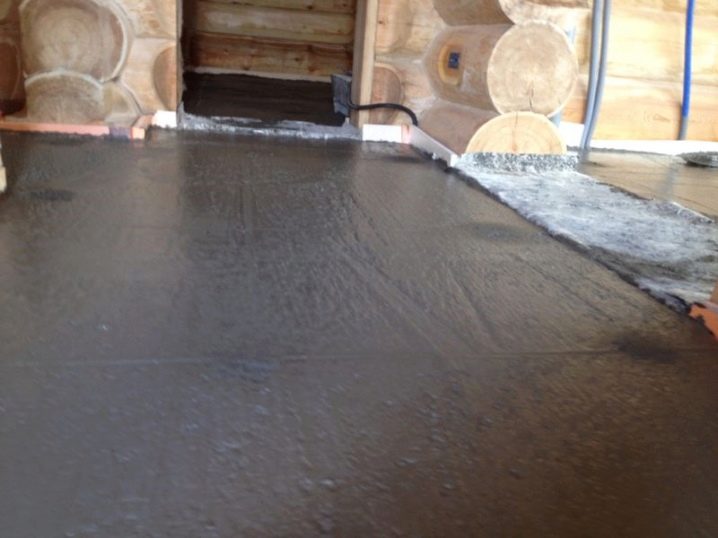
The screed can be poured and used as a finished floor covering or tiled on top. It is laid on the ground or logs. To strengthen the foundation for underfloor heating, screw piles are often used. An insulating “pie” is already being installed on these piles and a screed is being poured. Concrete flooring is time-consuming and resource-intensive because it is a complex multi-layer structure.
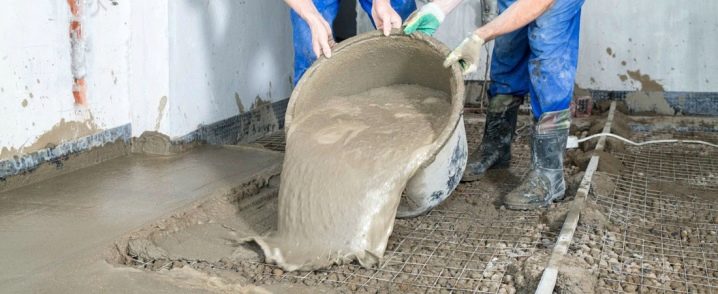
Before purchasing, you must familiarize yourself with the composition of the product. Some species contain crushed stone or gravel, so they can be difficult to mix. A homogeneous mass will be obtained only with the use of a concrete mixer or perforator. If there are no such devices, then the masters recommend purchasing a solution on a cement-sand base. This material is much easier to mix and pour.
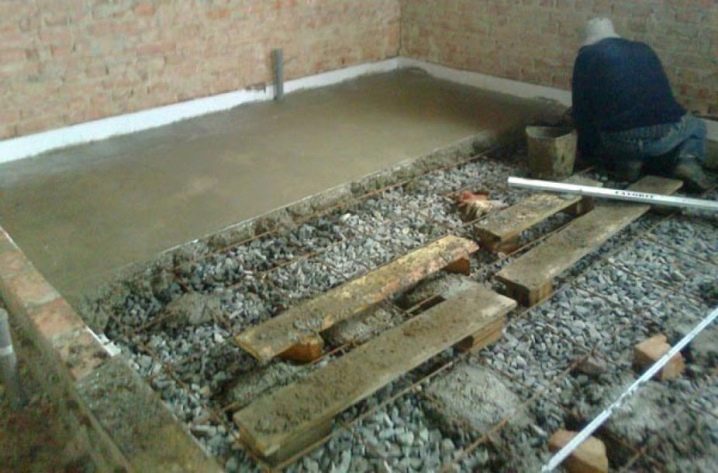
The consistency and composition of the solution largely depend on the conditions for the further operation of the cement screed. If concrete acts as a subfloor for laying boards, then the mixture does not require special additives. If you wish to lay ceramic tiles on the screed, it is necessary to add gypsum mixed with anhydrate to the mortar. It is not recommended to use a concrete floor as a rough floor for the installation of a synthetic covering. When interacting with critical temperatures, synthetics release complex chemical reagents that can be hazardous to health.
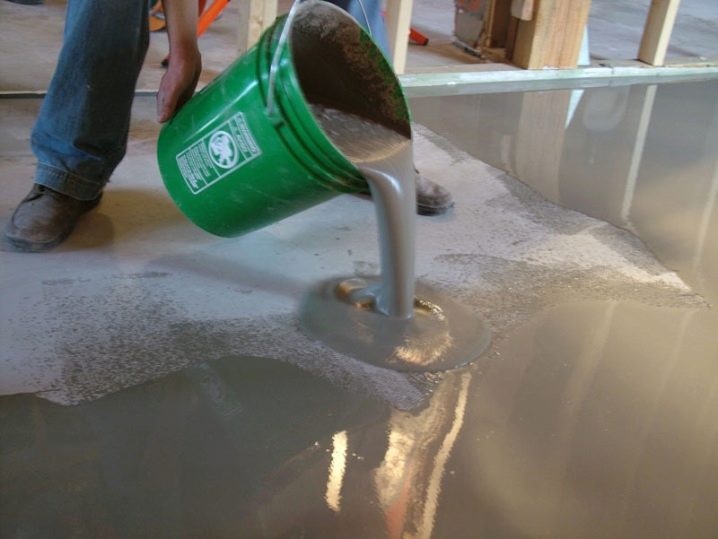
When installing a concrete cover, proper waterproofing is important. The floor is located under a slight slope, and a special pit with a drain is mounted under the base of the foundation. Water moves along the gutter and the ground and is removed outside the bath. A technologically competent installation of this system will protect the foundation from corrosion and allow the cement screed to serve for a long time.
Tiled
Ceramics are widely used for cold flooring. This material is not subject to decomposition by microorganisms and does not require special operating conditions. The tile is resistant to extreme temperature changes. The cover is also resistant to moisture, which allows it to be laid everywhere in the bath.
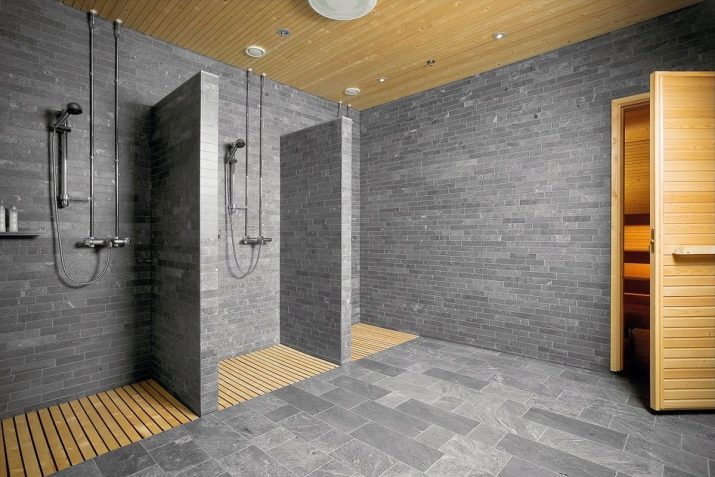
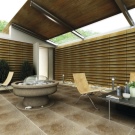
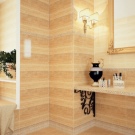
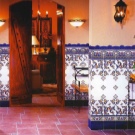
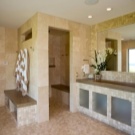
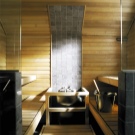
Designers note the wide color palette of this material, so they often use it to create decor in the rest room. The tile is environmentally friendly, does not emit harmful substances and does not have a chemical odor. The ceramics are placed directly on the poured concrete floor.
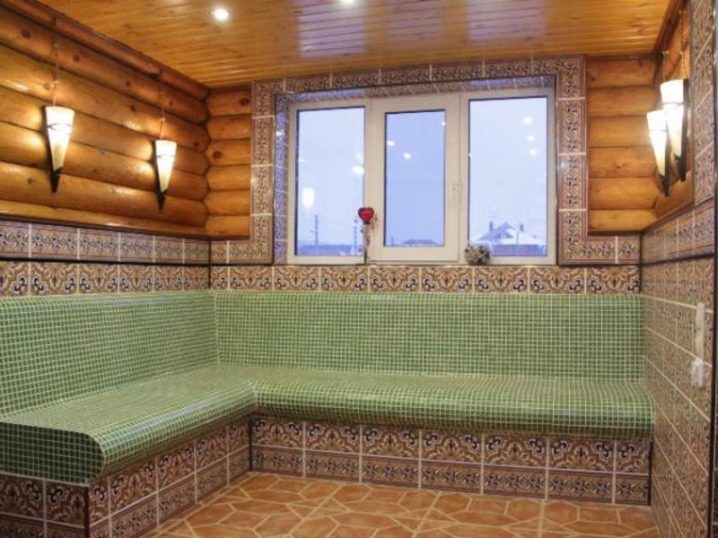
The screed does not always provide a smooth coating and requires additional measures. The roughness of the surface must be minimized, since this work requires an investment of time and effort. A tile laid on a screed with irregularities will not last long. Water can enter the voids, which will lead to the appearance of fungus between the joints of the mosaic. The gaps between the fragments must be treated with a special agent both during installation and during operation.
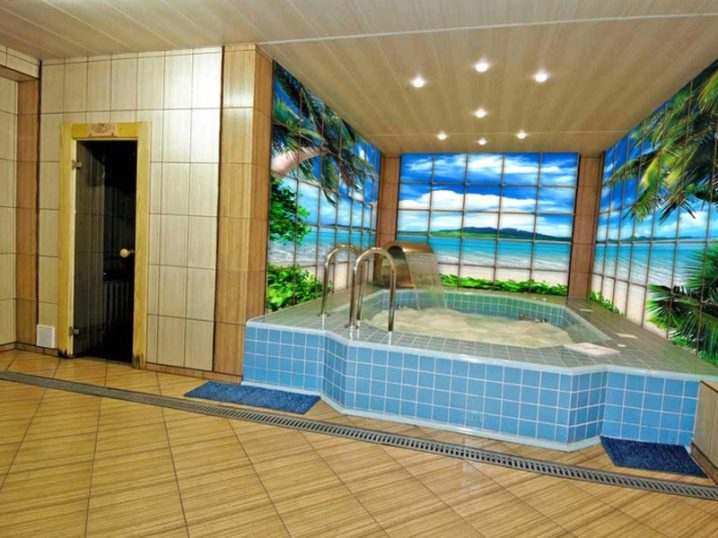
A significant disadvantage of the tile is its high thermal conductivity. To prevent the temperature in the steam room from dropping, proper thermal insulation is required. Another significant drawback is the risk of injury to the varnish coating. It is necessary to purchase tiles with a rough surface so that it does not become slippery when in contact with water. Today there are many ceramic tiles that imitate stone flooring.
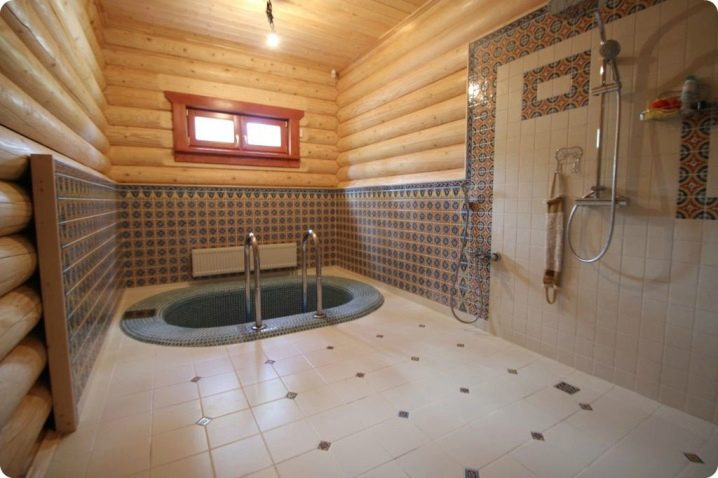
Designers highlight the pebble-style mosaic.In addition to aesthetics and beauty, this coating has a massage effect. Such tiles will be an excellent solution for decorating a restroom in a nautical style. Small stone particles are complemented with cut glass inserts. Glittering inserts have a beautiful shine and reflect light in an interesting way.
To increase the service life of the ceramic coating, it is glazed and fired several times. In addition, the craftsmen are advised to give preference to thick tiles. Such material is resistant to temperature fluctuations. You should not buy tiles with a lot of pores - they are less durable. Preference should be given to clinker mosaics or porcelain stoneware cladding. Pay close attention to the surface texture: glossy shine must be avoided.
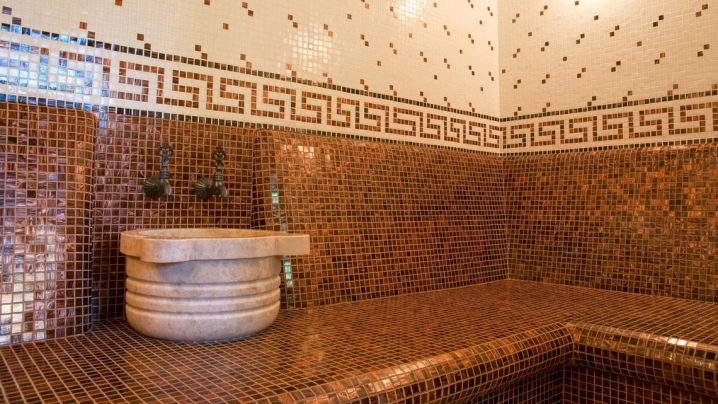
Heated
The heated concrete floor creates a comfortable microclimate. This option is necessary when installing a cold floor, especially in a cool climate zone. Also, the underfloor heating system heats the surface from the inside, drying the material. This system allows you to get rid of dampness and increase the life of the flooring. It is important to understand that such a heated floor is quite difficult for a beginner to install. Requires a wizard's instruction and control of the installation process.
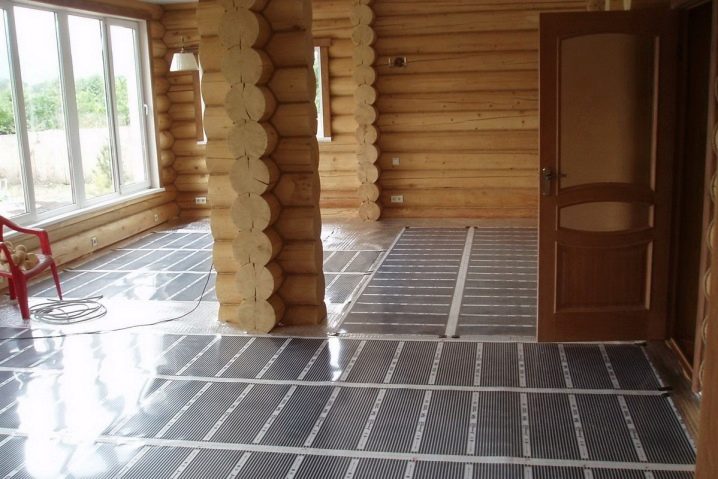
Underfloor heating - a system of pipes or cables through which a warm liquid moves. Convection provides uniform heating of the floor around the entire perimeter of the room, regardless of the location of the heating device. The pipes are under strong internal pressure, so the surface must be additionally reinforced. The contours themselves are easy to lay, but require reliable attachment to the rough surface. For the device of such heating, pipes without seams and joints should be purchased.
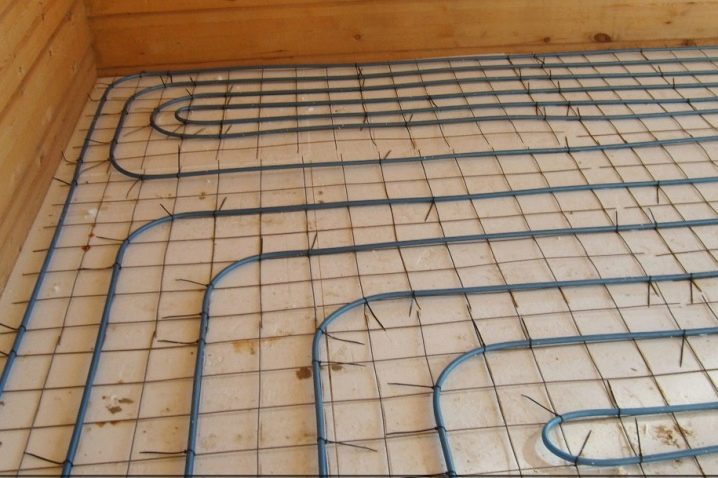
The distance between the contours is called the masonry step. It must be maintained during installation. Violation of the step leads to uneven heating of the floor. A similar gradient is felt on contact with the floor. You should also carefully choose the floor covering in the case of underfloor heating. Ceramics have the property of quickly heating up, so craftsmen do not recommend using tiles as a finishing layer. Preference should be given to wood panels.
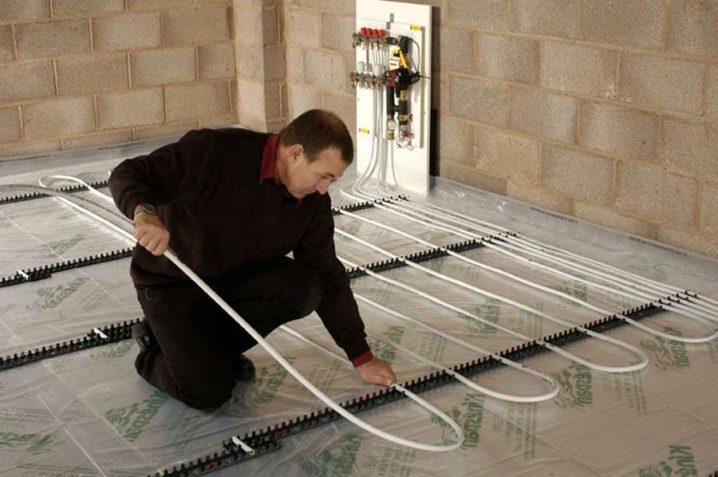
Today, there are two ways to install a warm floor. The water system is carried out by the circulation of the heating liquid from the pump through the pipes. The coolant in such a design can be either plain water or special non-freezing compounds. The water system consists of a boiler, manifold and pipes. It is difficult to install and expensive. However, such a system can reduce heating costs. Water underfloor heating is often used as additional heating in apartments and houses.
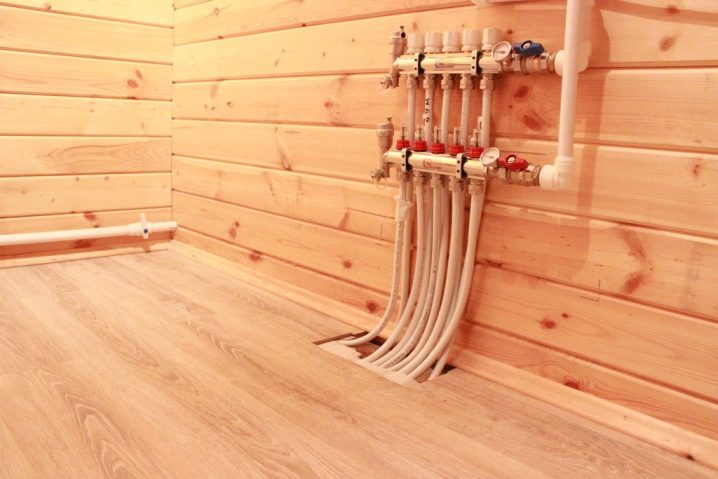
Another way to install a heated floor is an electrical system. These "cable" floors are easy to install, but their price depends entirely on energy tariffs. The cable converts electricity into heat and heats the surface evenly. To control the heating, temperature sensors are installed in the floor. It is important to remember that such a system should not be combined with wooden materials, since there is a high probability of overheating of the wood and a fire.
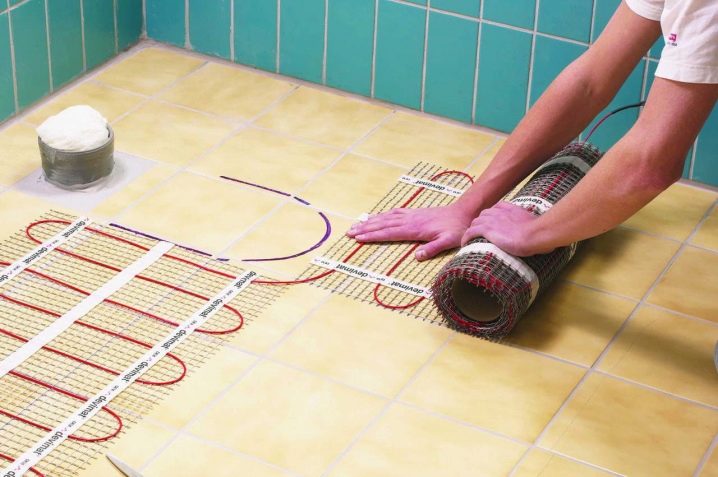
Installation of each type of heated floor requires the supervision of a master. The floor is laid on a heat-insulating material. Vapor barrier is an equally important layer when installing a warm floor. After laying the contours, the surface is poured with a cement screed.
All pipe joints must be additionally fixed. It is important to remember that it will not be possible to make adjustments once the cement layer has been laid. Otherwise, it will be necessary to completely remove the masonry, re-clean the surface and eliminate violations in the installation of the contours. It is important to lay the pipes on a perfectly cleaned surface. After making adjustments, the surface is poured with a new layer of cement mortar.
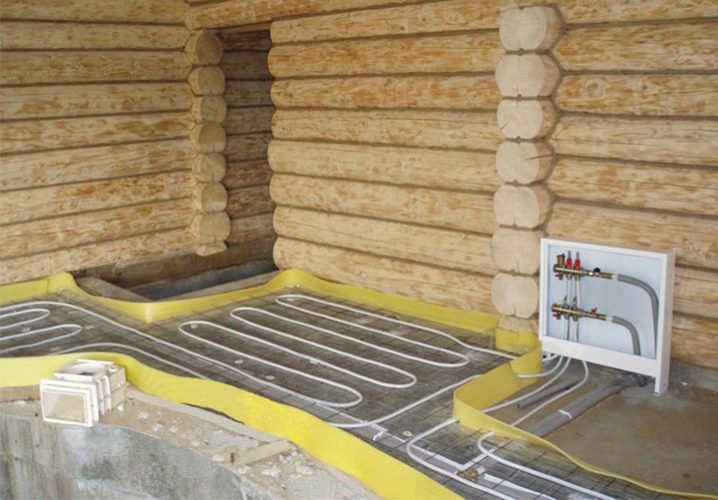
Before use, the floors are pre-tested and heated in accordance with the instructions. The problem is corrected and the system is checked again. The cycle must be resumed until the required temperature is reached. Only after the final tests, the cement screed is leveled and the installation of the finishing flooring is started. It is important to understand that every joint of the material requires careful processing. A water-heated floor will last a long time if all its features are taken into account during the installation process, for example, floor waterproofing.
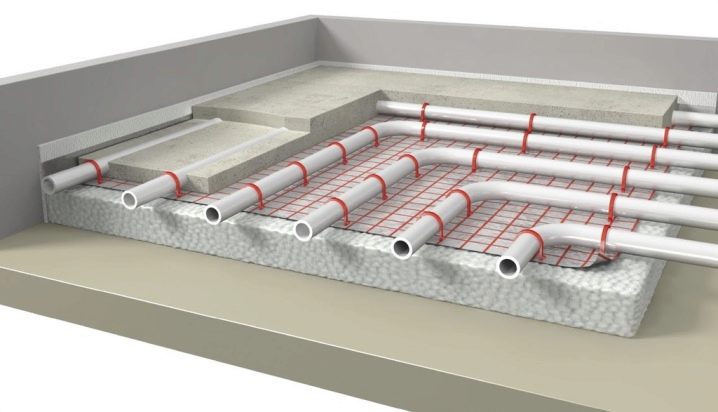
Professional advice
For the manufacture of high-quality coating, masters are advised to listen to some recommendations. The reasons for the destruction of floors can be different, but many can be prevented if the technology of laying the coating is not violated. The choice of quality material also plays an important role.
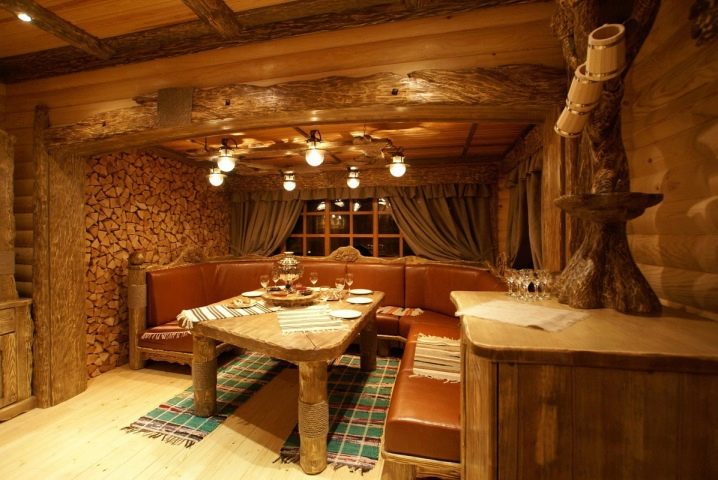
When installing lags, it is important to install waterproofing between the posts. Such a coating will protect the frame from rot and rapid destruction. Otherwise, the foundation will quickly collapse on contact with water. The posts should also be made of materials with high frost resistance and water resistance. Water can accumulate in the soil, which will corrode the concrete and cause the structure to sink.
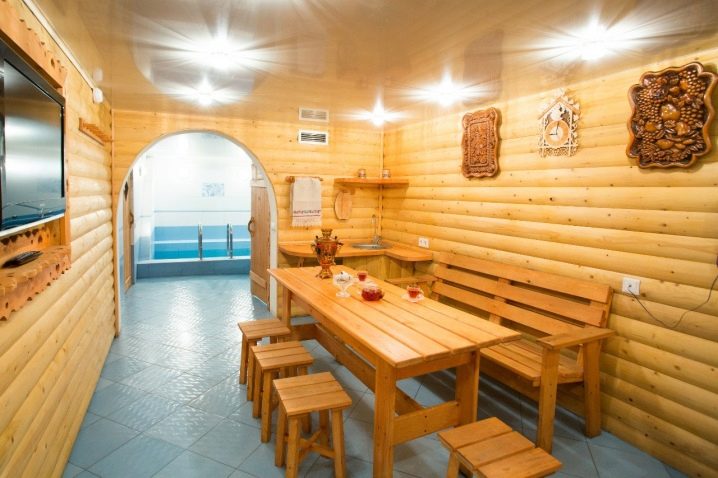
A wooden floor must not be installed without ventilation. Its scheme provides for gaps along the entire perimeter, all depending on the type of layer to be laid. It is not always possible to correct the violation after laying the topcoat, therefore it is necessary not to violate the technology at every stage of the work.
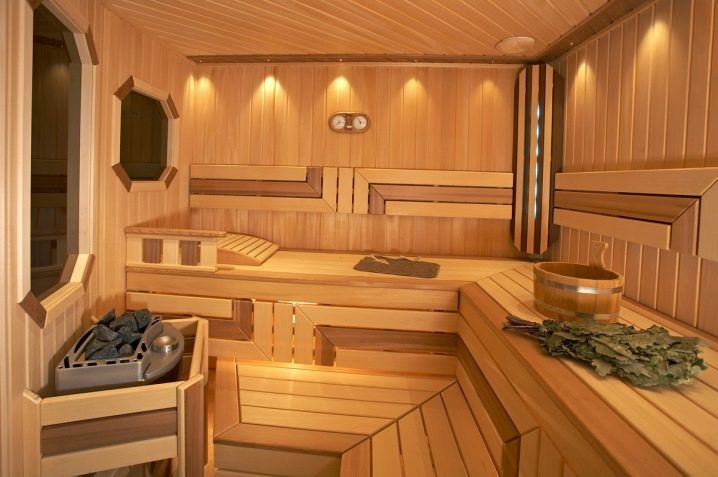
Floorboards should not be less than 35 millimeters thick. Such a plank will withstand a critical load and will last a long time, unlike an analog of a smaller thickness. All floor boards must be cut to the same size. This will not only simplify installation, but also provide the necessary evenness and slope of the surface. In cold periods, such a coating will retain heat longer.
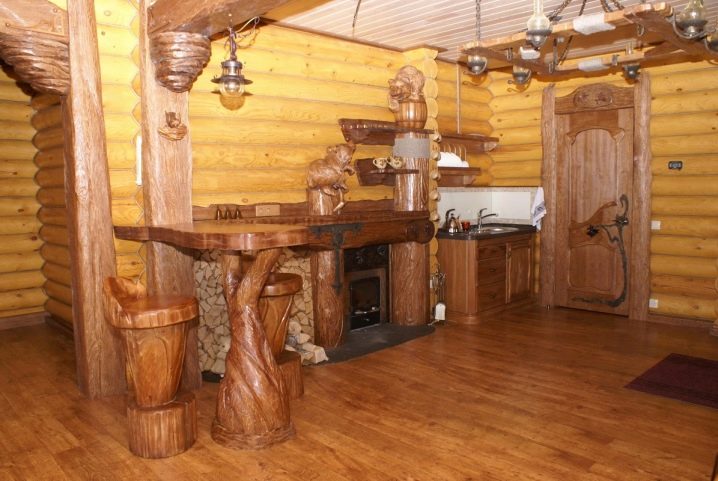
The installation of a wooden floor should only be carried out using stainless steel fasteners. Metal structures can be additionally treated to protect them from rust. Since the coating is regularly exposed to interaction with water, it is necessary to pay increased attention to the choice of metal structures and fasteners.
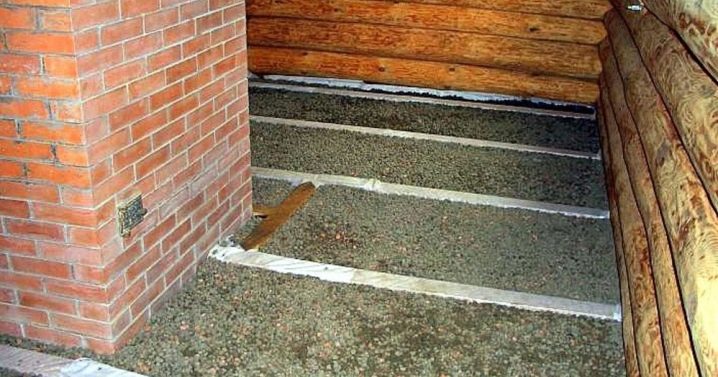
The floor level of the washroom is always slightly below the level of other rooms. The steam room and relaxation room should rise by a few millimeters.
Before you start laying the boards, the coating must be processed. The material is impregnated not only with a mixture to protect against moisture, but also with a substance that protects against fire. The latter is especially important when installing a warm electric floor. All floor components must be protected against fire. These indicators are spelled out in regulatory documents and must be confirmed by material certificates.
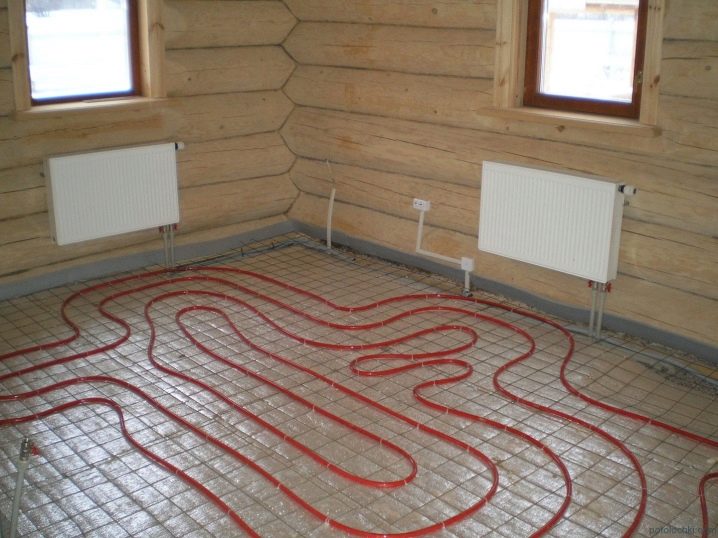
Craftsmen advise to give preference to a tiled floor. This combination reliably protects against natural phenomena and the negative effects of the bathhouse. The cover is easy to install and use and will save on hiring workers.
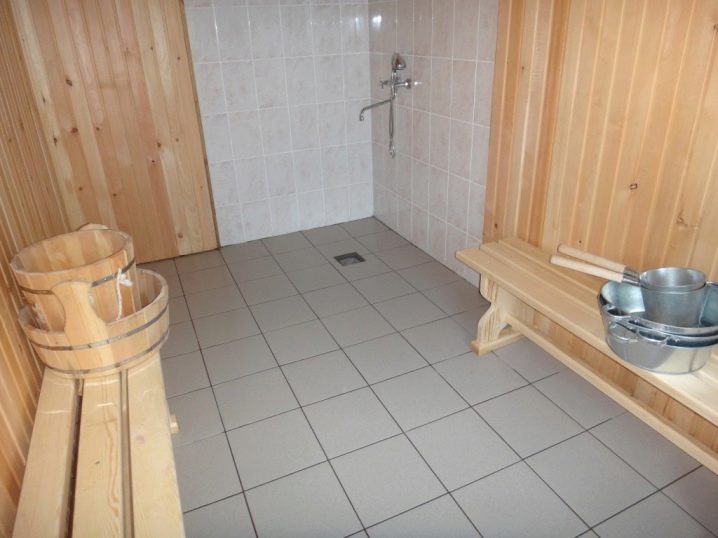
When arranging a steam room, it is necessary to correctly arrange a ventilation system. Otherwise, water vapor will accumulate and destroy the ceiling and walls. Rooms with poor ventilation require constant ventilation after use. Only in this case the bathhouse will last a long time. To bring ventilation outside in the attic, it is necessary to lay a pipe through which water vapor and smoke will be removed from the room. With a monolithic foundation, craftsmen are advised to make holes from the ventilation pipe to the outside.
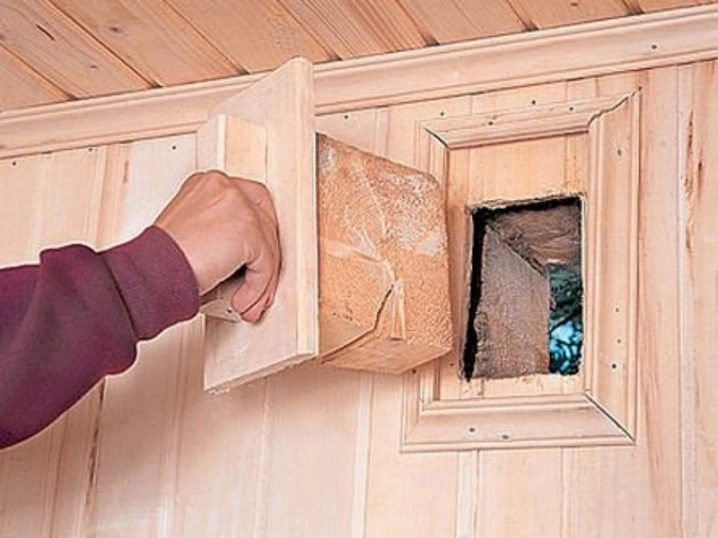
To reduce the audibility when moving around the bath, it is necessary to lay a layer of fiberglass under the finishing floor covering on the waterproofing layer. Fiberglass can be purchased on a roll, as the material is produced in the form of a wide ribbon.The joints of the coating can be connected with tape.
For information on how to make a floor in a bath with your own hands, see the next video.
The comment was sent successfully.