What is a wood splitting wedge?
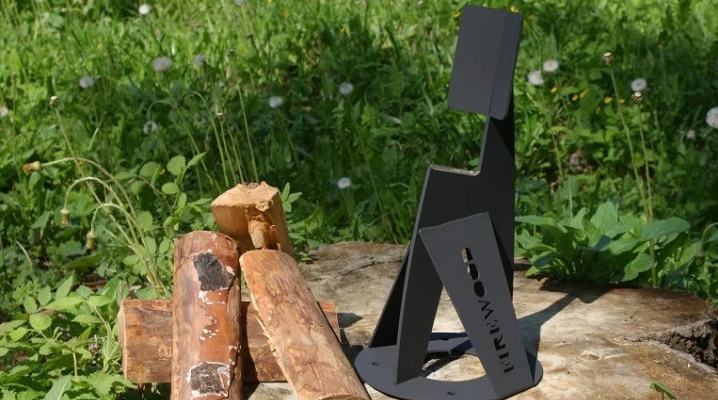
A wedge for splitting firewood is chosen by people who, due to their age, are too tedious to use significant force to split a log into small chops. Industrial wedges are convenient, but they have disadvantages: high cost and possible savings for the manufacturer on the quality of steel.
Varieties
Compared to simple axes, cleavers have a larger handle length - about 70-80 cm. This is due to the need to create a large amplitude of splitting movements so that large logs can be chopped into small segments without bending the ax blade into a wave.
The simplest analogue of an ax is a wood splitter, made in order to protect a person from accidental injury: slips with an ax in the old days could deprive a person of his fingers, or even the whole hand. The length of the handle for splitting knotty chocks in special cases reaches 90-95, and not 50 cm, as in a simple ax.
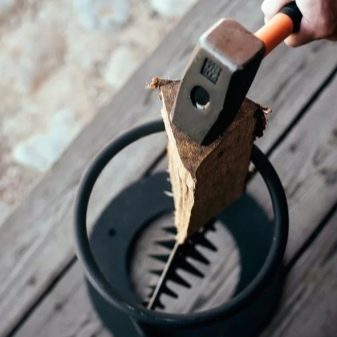

The spring wood splitter consists of a fixed part, which is a channel T-shaped base with reinforcing struts. A log is placed under the wedge, and the person presses the handle, moving it down. The weighting agent helps to break the log into two parts. The spring returns the wedge to its original position.
"Carrot" or cone wood splitter is arranged as follows. The working part is 20 cm long and 5-6 cm wide at the wide part has an approximately 30-degree conical angle. The flaw of this design is the impossibility of blooming the bark due to the looseness of the latter.

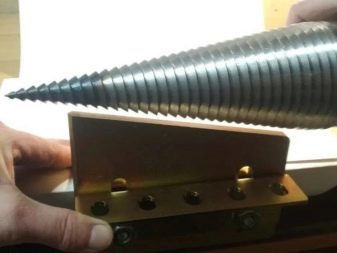
Inertial wood splitters do not need a sledgehammer. In fact, they are several powerful blades fixed on one base. The top of the blade holder is made in the likeness of an anvil, which is struck with a hammer, as a result of which the chock is dissolved into small firewood.
A forged wood splitter is made in the form of a cruciform or flat wedge. But if everything is clear with the first (it is an ordinary flat blade that divides the chock in two), then with the cruciform, everything is somewhat more complicated. It is not easy to forge such a product; most often it is made in an industrial environment. The cruciform wedge breaks the core along the core, splitting the wood in four.
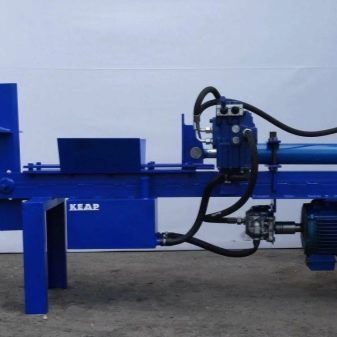
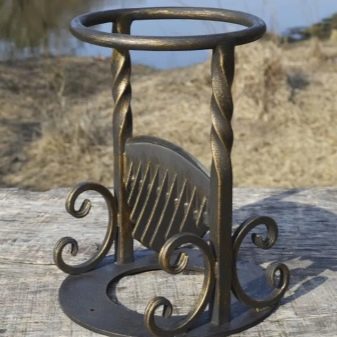
How to use?
A manual wood splitter is used in most cases as follows. A piece of wood is inserted into it, then the wedge itself is activated. Adjustment of the device for the dimensions of the chopped chocks is carried out by setting the spring to the desired level. The shorter the free travel distance of the spring, the shorter the lumps can be split without fear of damage to the wedge tip.
An electric wood splitter works in a similar way: before starting it, you need to put a piece of wood in advance. The motor will drive the drive, the kinetic force from which is transmitted through a gear (reducer) or mechanical transmission.
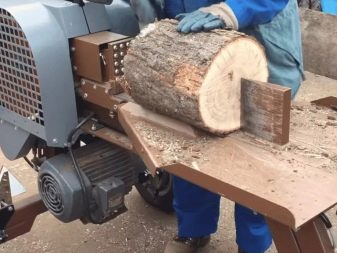
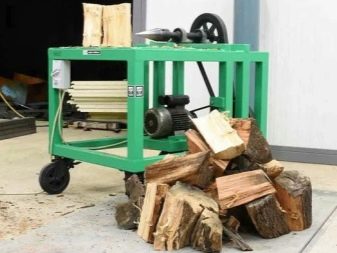
In hydraulic drives, the force is transmitted by pressing the pedal, which conducts mechanical force from the foot through the liquid (most often it is oil, which is 99.9% incompressible under normal conditions). It circulates in a system consisting of one or two vessels with oil outlets. The advantage of hydraulics is that 95% of the force is transmitted from the human leg.
When working with a conventional cleaver with no mechanics or hydraulics, stay away from the log to be chopped. To chop up large logs, you need a massive tool - up to 4 kg. In practice, a weighting agent is welded to homemade cleavers with insufficient mass.
Cutting with a cleaver with a weighting compound without annular guides is doubly dangerous.
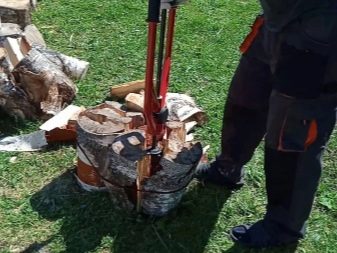
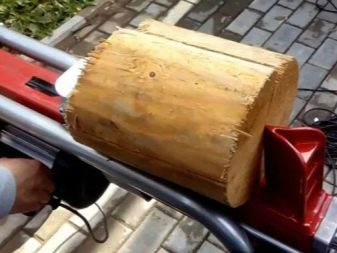
How to do it yourself?
To make the simplest cleaver with your own hands, do the following (this tool is made from a steel frame with a diameter of 25 cm):
- holes for fastening are drilled on a steel base fixed inside;
- an iron ring with a diameter of 25 cm is installed in the upper part;
- an upwardly aimed blade is fixed between the supports and welded to the base.
- a chock is installed in the ring, attached to the blade;
- then they hit the cleaver from above with a sledgehammer.
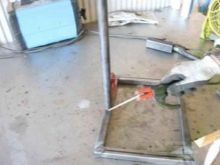
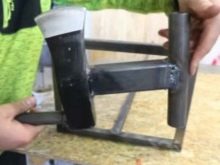
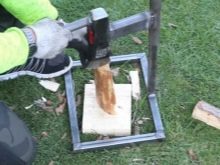
To make a spring log splitter, resort to the following steps.
- According to the drawing, a plate with a pipe welded to it is welded to the lower part of the T-base, welded from a professional pipe, at the place of fixing the spacers. The angle between the base and the plate is straight.
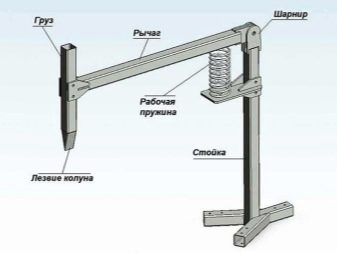
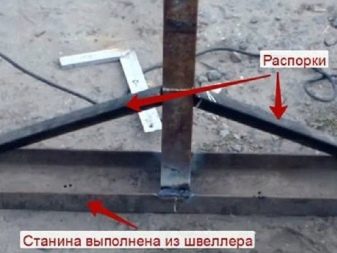
- The moving part of the wood splitter is assembled as follows. A movable steel bar is fixed at the top of the base with a hinge. A branch pipe is located at one end of this crossbeam. Both connections must be on the same axis.
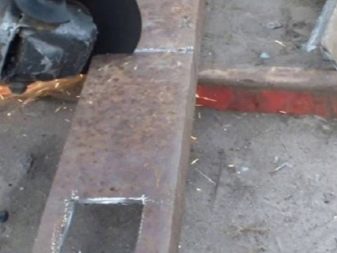
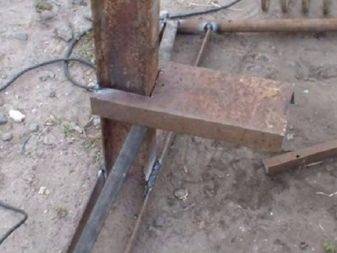
- An auto-spring is placed between the nozzles, held in the correct position by these nozzles. On the other side of the crossbeam, a pointed steel wedge is welded, aimed downward, as well as a horizontally aimed handle.
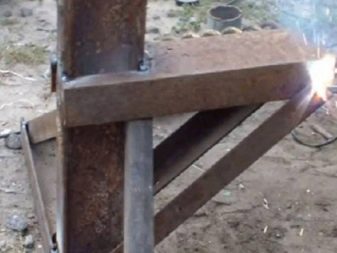
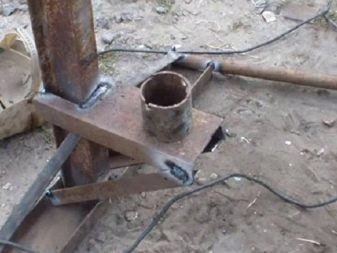
- An appendage is welded over the wedge, for example, a fragment or a piece of a rail or a dumbbell. Having completed the manufacture of a spring wood splitter, they test it in practice.
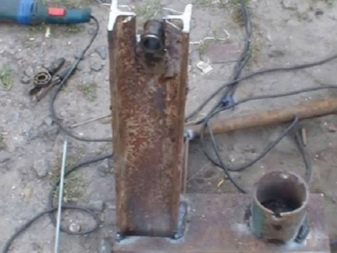
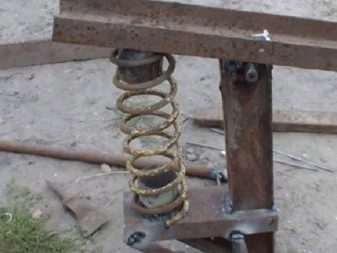
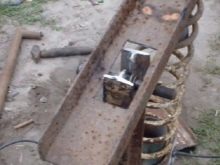
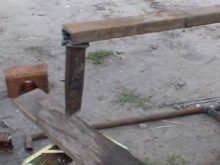
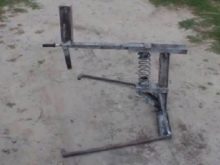
For the manufacture of an electric cone, the following instructions are followed.
- The tapered element is tapped with a groove depth of 2 mm and a thread spacing of 7 mm. A well-recessed void is cut out inside the cone-shaped element.
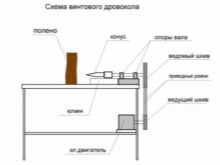
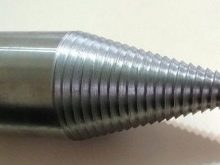
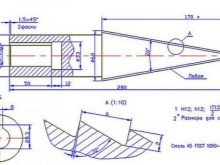
- On the part of the workpiece where there is no thread, up to three holes are drilled. A screw thread is cut into them with a tap. Then the bearings are placed in the cardan supports and welded. The cardan is installed in the ball bearing of one of the supports. A sleeve is mounted on it, which protects the cardan from the ingress of foreign solid particles.
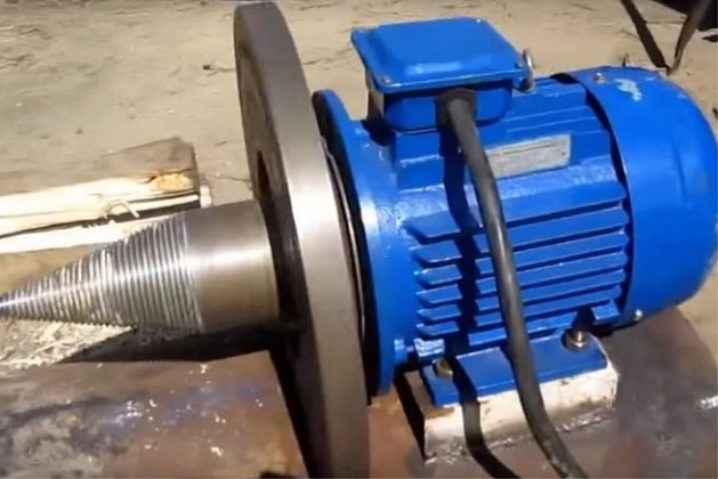
- A second support with a bearing is pushed onto the cardan until it rests against the bushing. A cone is inserted from one end of the cardan. It is fixed through the slotted holes with bolts. The other end of the cardan is firmly put on the pulley, which is secured by means of a nut. Bearing supports are fixed on a frame, under which an electric motor is attached, connected to the wood splitter through belts.
The device is ready. In work, in order to slow down the speed of the wood splitter, a reduction gear is used.
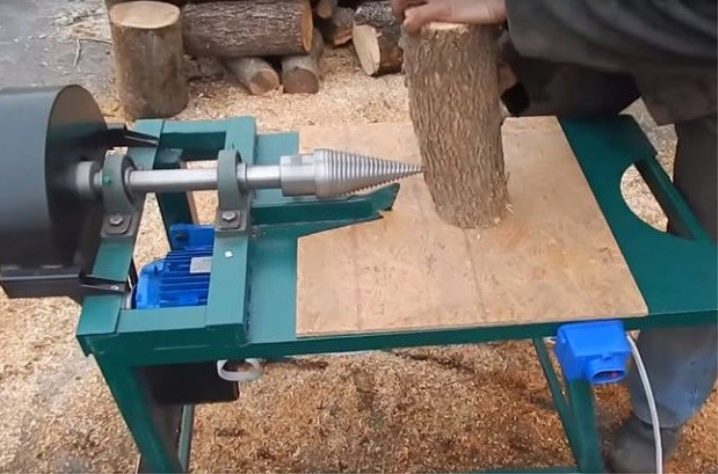
The handle of the manual cleavers is made of medium-sized wood (in terms of hardness). Oak and other particularly dense types of wood cannot be used: they do not dampen vibrations, after work the hand becomes excessively tired. When making cleavers, the blades are sharpened to a maximum of 60 degrees: this is enough to cut the hardest types of wood. Rounded sharpening is designed for raw and wet wood, straight - for thoroughly dried wood.
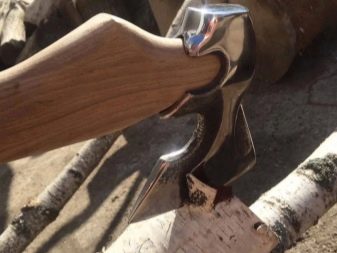
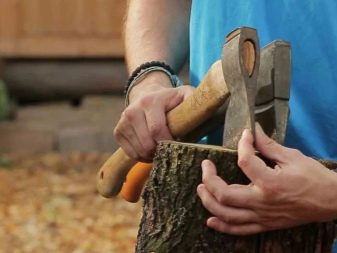
For an overview of the Zigzag EL 452 F wood splitter, see the video.
The comment was sent successfully.