How to make attachments for a mini-tractor and attachment to them with your own hands?
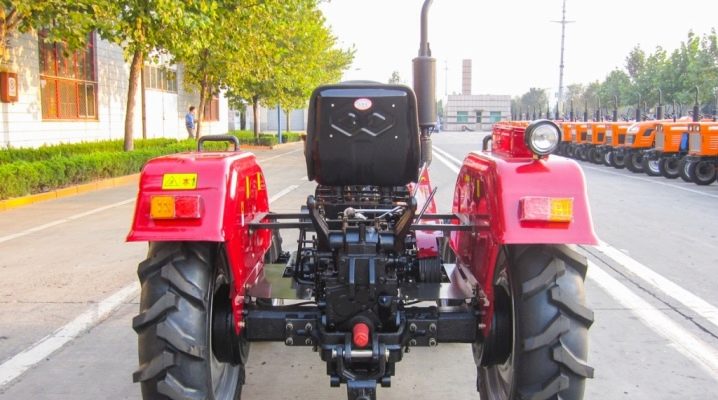
On the farms of many farmers and summer residents, you can see equipment made with your own hands. Similar units were made according to the drawings drawn up by them, because they know everything about the peculiarities of the soil, as well as what requirements need to be taken into account for the units themselves. Such equipment, if done correctly, can last a long time, performing all the necessary work.
Pros and cons of homemade designs
From the advantages of self-assembled technology, the following positions can be noted:
- even a person with low qualifications can make attachments;
- any attachment made in artisanal conditions costs quite inexpensively;
- to create equipment and repair it, you will need a standard set of tools;
- it is possible to enhance certain features of the device;
- from a safety point of view, attachments can be created at a very high level.
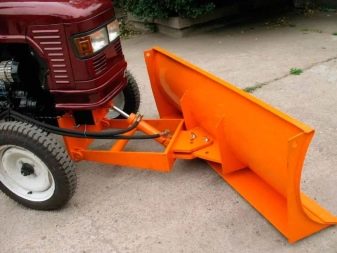
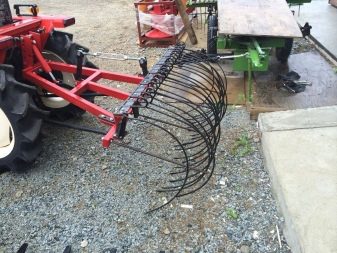
Among the shortcomings, the following criteria stand out:
- setting up and maintaining homemade equipment is a painstaking laborious process that requires skill and proper qualifications from the owner;
- during the entire service life, it is required to monitor the operation of the unit with special attention.
Attachment manufacturing
Attachments are divided into the following types:
- to prepare the soil for planting crops;
- for harvesting and processing.
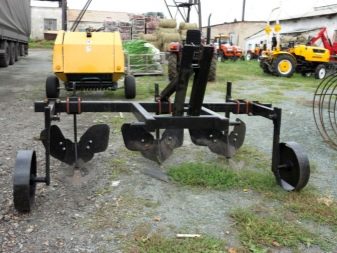
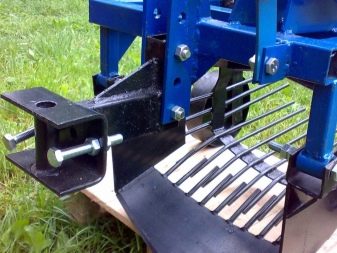
Before installing equipment on a mini-tractor, drawing up drawings, determining dimensions, you should understand:
- type of construction;
- features of the technology (advantages and disadvantages);
- cash and energy costs.
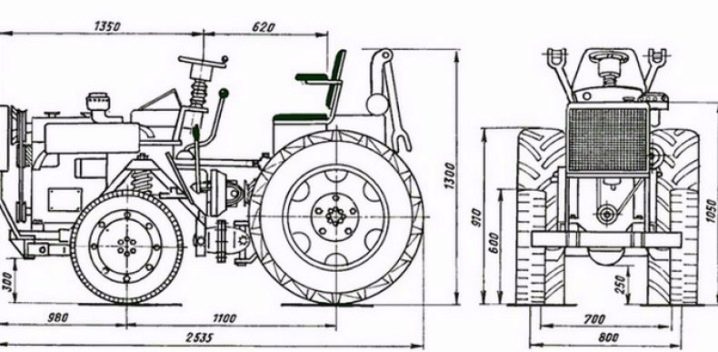
The most popular attachments for farmers, which are assembled by hand, can be distinguished:
- plow - designed to prepare the soil for sowing (usually it is connected to the rear suspension);
- harrows - provide soil preparation;
- potato planter - works with engines that have a capacity of more than 23 liters. with.;
- rake - an effective tool for cultivating the land, has a size of 1.2 to 3.2 meters, the engine power must be more than 14 liters. with.;
- cultivator - provides proper care for plants during the growing season;
- sprayer - a device for processing agricultural areas with mineral fertilizers;
- potato digger, conveyor digger - designed for harvesting root crops (rear suspension is required to work with this technique);
- trailed equipment, automatic coupler - equipment is necessary for the transportation of various goods;
- snow rotor, rotary snow blower, auger snow blower - the units are used for clearing snow drifts in the cold season;
- scythe, knife, cutter - tools for working with the ground;
- manipulator - a mini-unit with a dozer blade, which can be equipped with a mounted excavator or a loader.
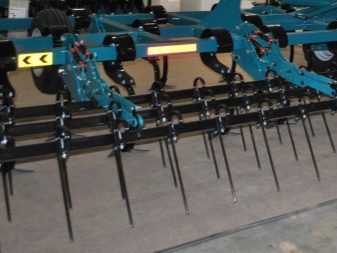
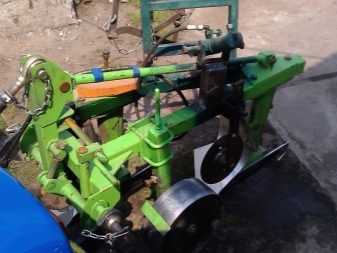
Ladle
Especially in demand such devices:
- buckets:
- KUHNs;
- snow shovels.
KUHNs are very often made in artisanal conditions, and in terms of quality they are in no way inferior to factory products. When making a KUHN for a front-end unit or as an attachment, diagrams and drawings are required. You should also carefully calculate the performance characteristics of the equipment, its carrying capacity.
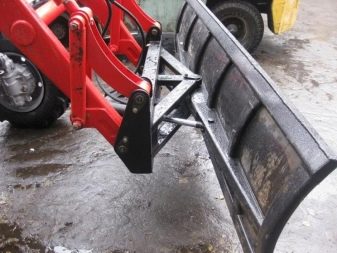
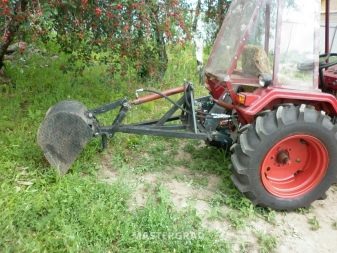
Typically, such attachments are made of 5 mm steel sheet. To create a KUHN, as well as a bucket or snow shovel, you will need the following tools:
- nippers;
- welding machine;
- clamps;
- Workbench;
- pliers;
- hammer;
- impeller.
You will also need guides and supports, which are made from tubes with a diameter of 45 and 80 mm. Additionally, it is necessary to install a hydraulic booster - its diameter should be about 25 mm. Another tube is welded to the front to secure the perpendicular elements.
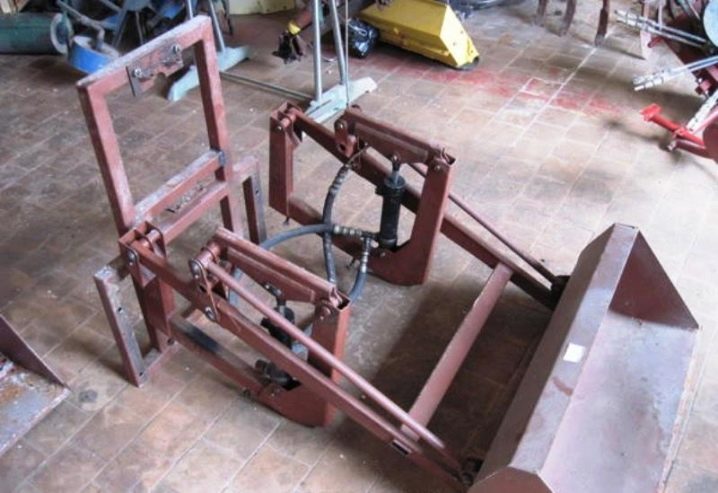
Creation of a hinged unit. To cut the pipe, an impeller with a circle "10" is used. To do this, it is necessary to implement a deviation from the edge in order to ensure the correct bend of the bucket. A profile is welded from the bottom of the pipe. Often there is a need to weld cross members, which will create an additional stiffness factor.
The bucket is fastened with an A-piece. Additionally, the unit is fixed with longitudinal beams. A particularly important component is the hydraulic lifting device.
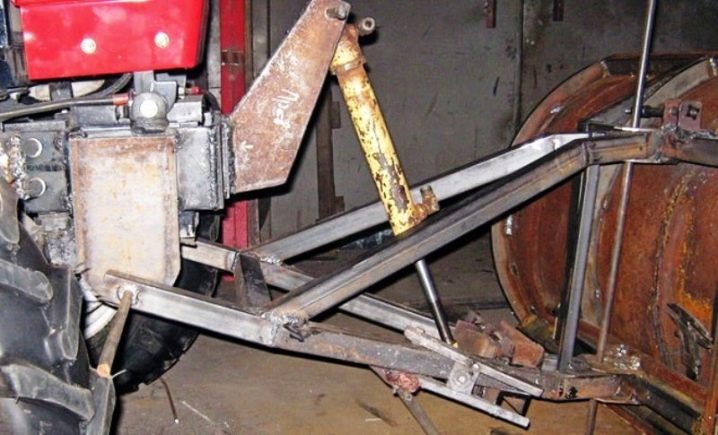
In order for it to work smoothly, all elements must be carefully adjusted. Only a highly skilled craftsman can make a hydraulic lift on his own, so it is much easier to borrow a block from a semitrailer 2 PTS-6. To fix the bucket, a front-mounted suspension is required.
Planter
Potato diggers are installed on a mini-tractor, which can heap up to 35 acres of land. This configuration requires only one conveyor and a container for 100 kg of potatoes. Also, sometimes double-row units are used - they are suitable in format for powerful tractors. The planter (seeder) is made of a sturdy frame on which various blocks are mounted:
- axle with grouser (several pieces);
- gears (2 pcs.);
- conveyor;
- tubes for feeding.
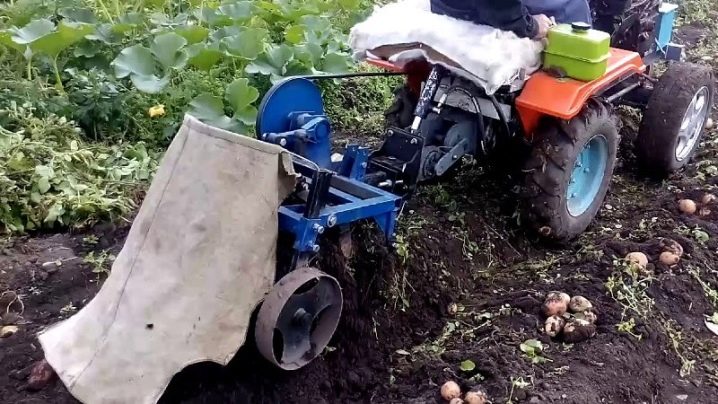
Often, an additional plow clings to the frame in order to make a furrow in which the tubers are planted. Also, a disc hiller is attached to the rear of the frame to sprinkle potatoes. If everything is put together correctly, then the process of work will take place in automatic mode. To create a planter with your own hands, you will need the following elements:
- corner "4", a rectangular pipe is also suitable, the wall thickness of which should be at least 3 mm;
- axle with fixed bearings;
- two gears and a chain;
- conical container (PVC material can be used);
- steel wire;
- lugs (they can be made from gas cylinders).
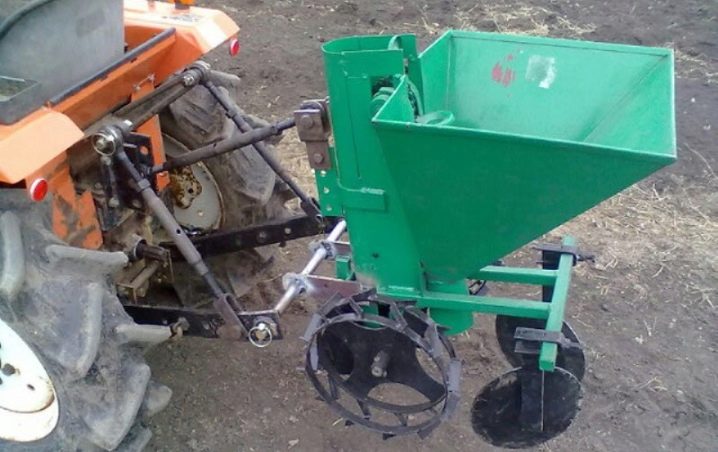
Of the tools you will need:
- Bulgarian;
- disks;
- welding machine;
- drill;
- drill;
- screwdrivers.
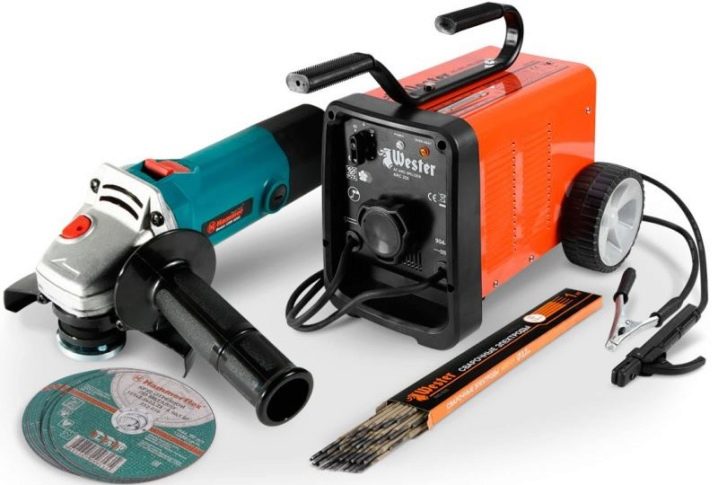
First, a 65x35 cm frame is created. For this, a 45 mm thick pipe is suitable. An axle with an "asterisk" is placed on it, which will become the main drive.
The lugs are cut from gas cylinders (the cut goes in a circle) - thus, rings 7-12 cm wide are obtained. Hubs are welded onto them, which are attached using studs.
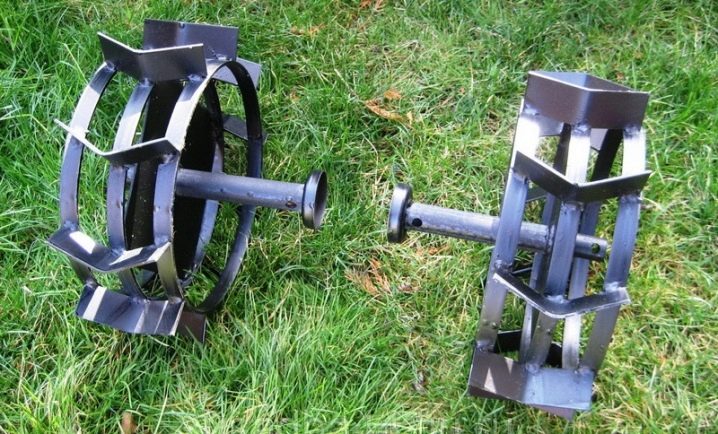
The wheels are removable. Then a container is built - it can be made of PVC sheets or tin. One container can hold approximately a bag of potatoes (50 kg).
Then the conveyor is assembled. Here it is necessary to put a chain with cells no more than 6.5 cm.
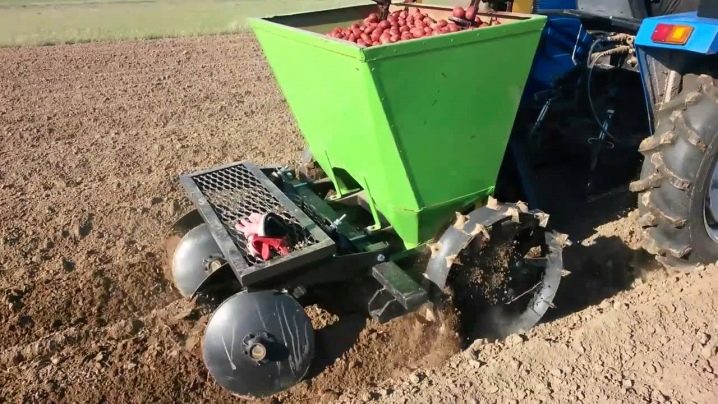
Lift
Lifting various weights (up to 800 kg at a height of 3.5 meters) can be realized using a mechanical device. In this case, you can use the "hydraulics" of the suspension.
The design is not laborious, but it is not always convenient to use it. Another lifting mechanism can be made.
To make a lift, you will need the following components:
- corner "8";
- sheet steel (6 mm);
- corner jumpers "4";
- two kerchiefs and eyelets.
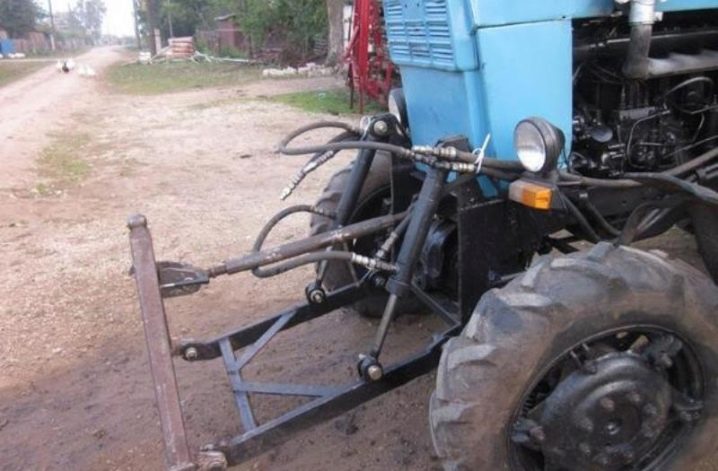
A groove is made in the rear jumper - it is needed for fixing (it is equipped with a "triangle").
All elements are fastened, holes with a diameter of 24 mm are drilled for engagement.The boom is anchored at the top of the tip - this creates a lever that provides lift height.
The boom is made from the corner "8". A channel is welded along the entire length as an attachment. All joints are reinforced with welded plates. The upper part is equipped with a hook that bends at an angle of 45 degrees. A ball joint is attached to the other end.
An additional guide is made (65 mm). Holes are drilled along the length (4-6 pcs.) So that you can fix the equipment under different operating modes.
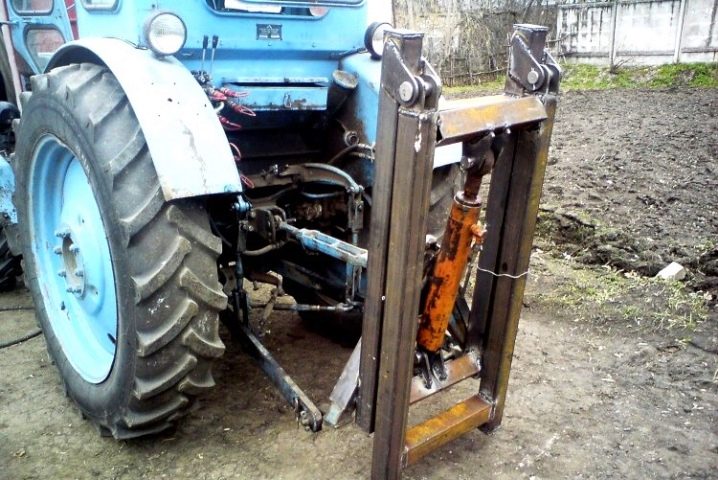
Hiller
The triple hiller is one of the most demanded agricultural tools, which is practically not inferior in purpose to a plow or a winch. It allows you to create furrows in which various crops are planted. The hiller moves along the beds, while his "wings" promptly pour soil into the holes, which already contain potato seedlings.
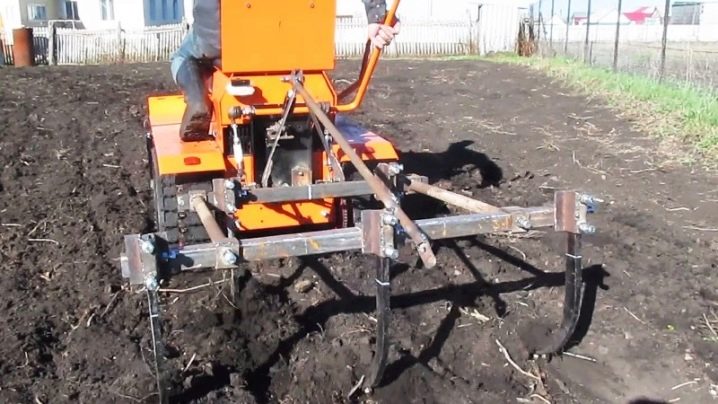
The hiller is the simplest tool in design, which has a single working width, while it looks like two wings fastened and spread apart.
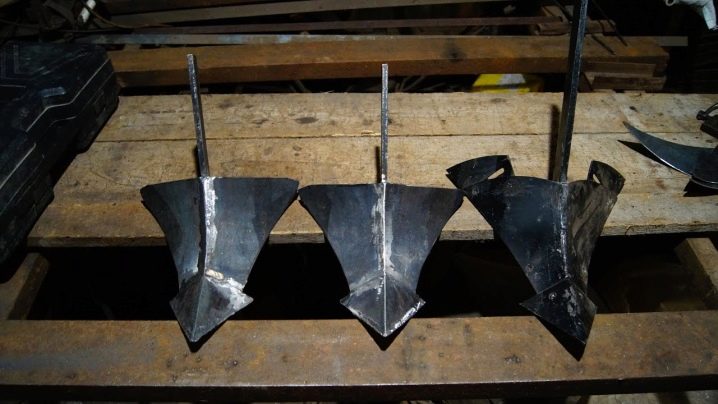
When working with a hiller, the width of the beds is adjusted for a specific tool, but not vice versa. Manufacturers make devices with a working width of 24-32 cm, which does not always meet the needs of private farms.
Hillers are divided into several types. The simplest and most popular of them is a hiller for a small area. This unit is of the propeller type. It is put on a mini-tractor, which has forward and reverse gears.
The principle of operation is as follows: special propellers loosen the soil, weed weeds, then the beds are covered with thinned soil. Work takes place in second gear with a torque of up to 190 rpm.
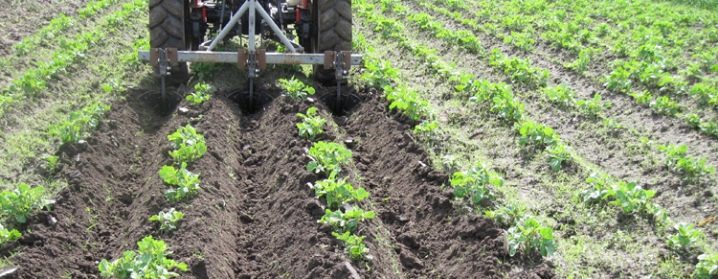
To make the simplest hiller, you will need to use 3 mm metal. Fragments of the product are bent until the radii coincide. Then you should weld them 2-3 times. Seams are processed and protected so that the surface is smooth. The "wings" are made using the same method.
Harrow
Manufacturer prices for harrows vary from 15 to 65 thousand rubles. For this reason, such a device is easier to make on your own, because it will cost several times cheaper, and it will perform the work no worse than the original version.
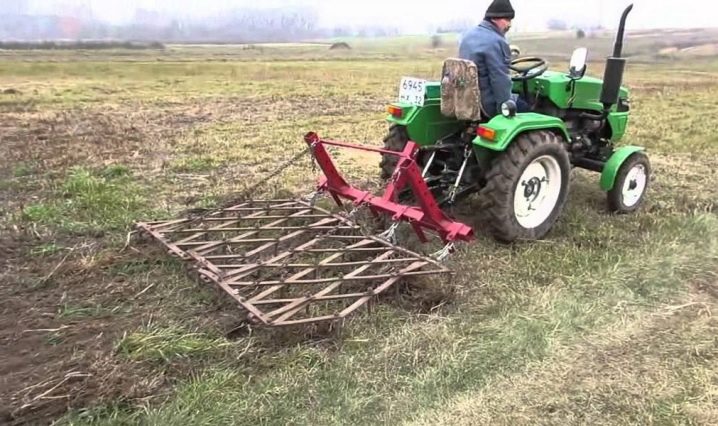
Before the land is plowed, it must be properly prepared. A disc harrow is best suited for this. The weight of the product ranges from 190 to 700 kg, the grip can be from 1 to 3 m. Several discs can be put on the model, the tillage depth will be about 20 cm.
Harrows are divided into the following types:
- rotor-powered;
- disk;
- dental.
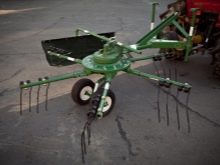
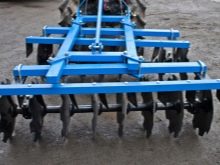
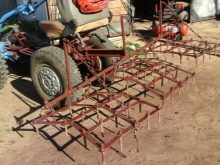
The first type removes soil in layers, the thickness of the cut can vary from 3 to 9 cm. This indicator can be controlled. It is also important to take into account the area of the allotment on which you will have to work when designing the harrow. Strip widths vary from 750 to 1450 mm.
When properly designed, the blade has a sharp angle, which allows it to penetrate the ground with maximum momentum, dissecting it and destroying weed roots at the same time. The disc harrow is used on dry soils, and a special disc in the form of an asterisk loosens the soil in such an aggregate. On one shaft there can be up to 5-7 such disks - it all depends on the power of the engine.
The tine harrow is used to create evenly weeded soil. Here, the protruding parts can be of very different configurations. Most often used:
- teeth;
- knives;
- squares.
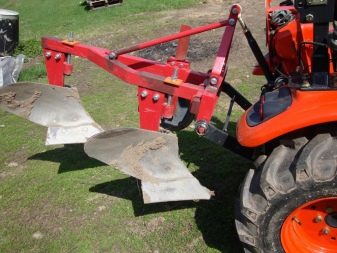
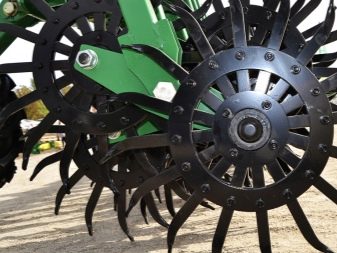
Sizes range from 20 to 40 mm. With the chassis, hitching takes place either by means of a spring strut or by means of hinges.
The simplest harrow by design is a tooth harrow. It may be enough for soil processing. In appearance, it resembles a lattice with teeth.A good grip can be an ordinary bar with holes that fit into the tube of the trailed unit, while the rod is fixed.
After the unit is assembled, dynamic chains are welded between the hook and the chassis.
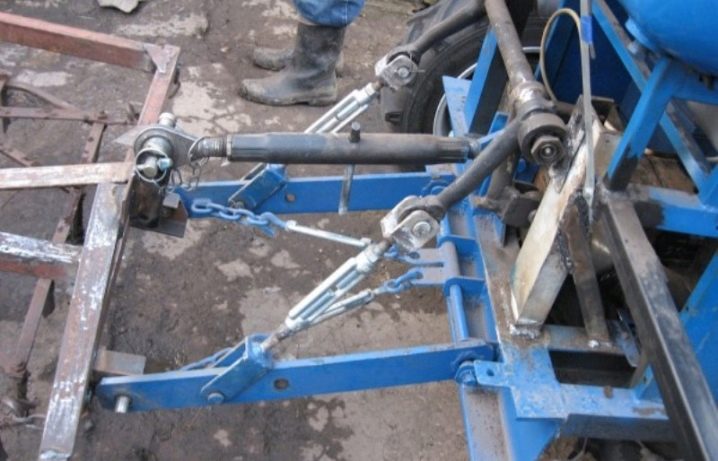
The grate is cooked from blocks or fittings. Sometimes pipes with a perpendicular section are used, while the walls must be at least 3.5 mm thick.
The angle of inclination of the "teeth" should be about 47 degrees. It should also be borne in mind that the created unit must fit seamlessly into the turning radius.
The "teeth" themselves are made up to 22 cm high, using steel, which is used for reinforcement. The longer the “tooth”, the thicker the reinforcement should be. Sometimes "teeth" are subjected to additional hardening and turning. Between themselves, they are located with an interval of 10.6 cm.
The arrangement of "teeth" should be mated with the thrust shaft, otherwise the harrow will crawl on the ground. Additional vibration will inevitably occur.

Sprayer
The sprayer is usually made of two wheels. A container with fuel and a pump are placed on the unit. Water is poured into the canister. You will also need nozzles and a hose. Sprayer differentiation:
- dispersed spraying - droplets in the form of fog cover the soil and agricultural crops with an even thin layer;
- spray spraying - usually used for the root system.
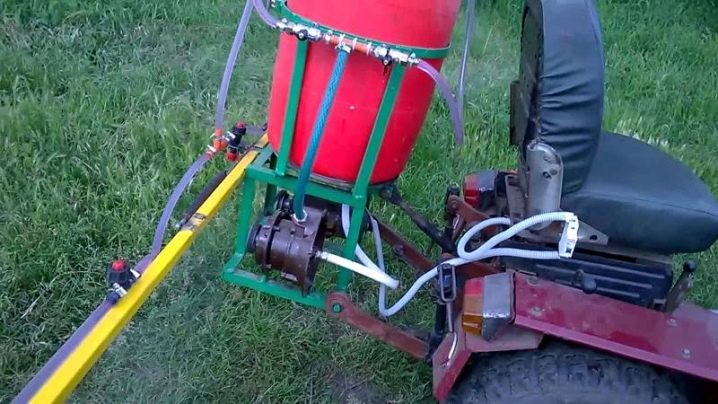
How to make simple samples?
The three-point suspension is the most popular attachment for attachments. It can be either back or front. This unit is distinguished by its versatility - only for a broken frame or a tracked tractor, the attachment points are of a different configuration.
The three-point hanger consists of a "triangle" which is welded from steel. The main screw provides dynamic fastening to the unit. It is not particularly difficult to make a hitch with a manual drive (with a mechanical lift).
Such a structure works by means of a "triangle" - thanks to it, the connection between the vehicle and attachments is realized.
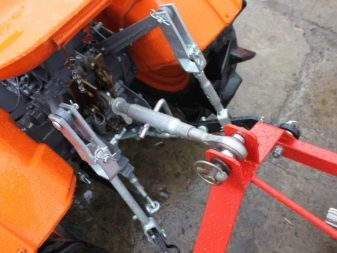
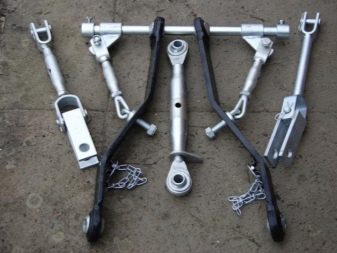
The connection takes place within two minutes: the tractor approaches the machine in reverse, the "triangle" is brought in by means of a hydraulic device under the fastening groove. The suspension rises and snaps into place.
How to make attachments for a mini-tractor with your own hands, see the next video.
The comment was sent successfully.