All About the Drill Bit
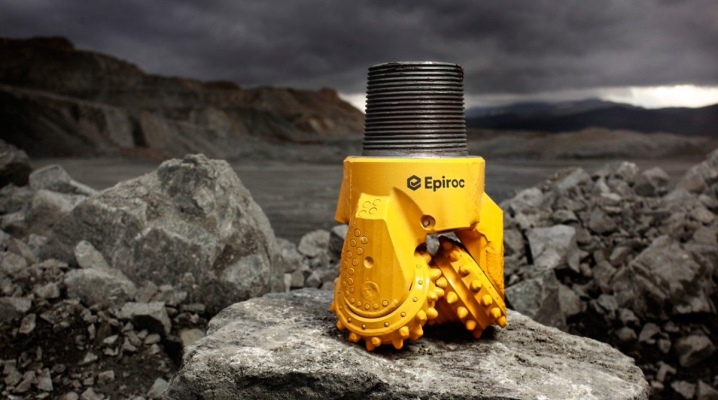
The drilling method is in demand in various industrial sectors. For the extraction of oil and gas, special installations are used. One of the elements of such equipment is a drill bit. The article will discuss the features and types of this tool, its popular manufacturers and selection criteria.
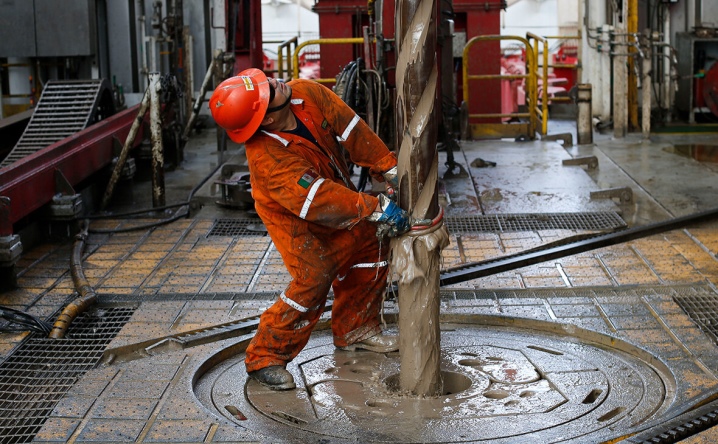
What it is?
A drill bit is a specialized tool for drilling wells. The equipment creates a crushing or cutting effect by forming a hole of the desired diameter. The design has a complex structure. The main element of the body is a rotor with a special attachment, which ensures the operation of the mechanism. Chisels are produced on industrial machines; high-quality steel is used as raw material.
The housing contains bearings. These are small elements for crushing purposes in the form of a cone with teeth. For the manufacture of rifled teeth, machine tools are used, and the bearing itself is smelted in a furnace. The bearing is located on the bit leg.
The number of elements is determined based on the purpose of the drilling equipment.

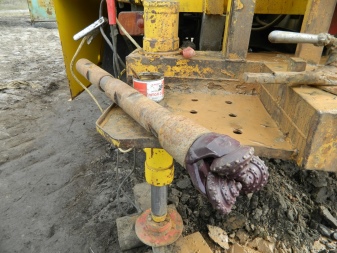
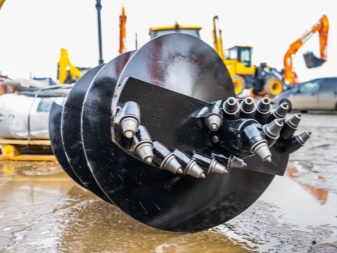
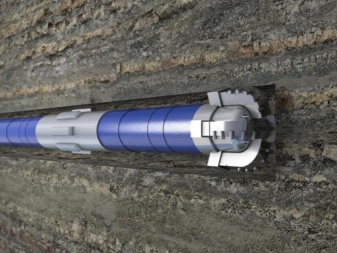
The tool speed depends on the depth of the hole and the plasticity of the soil. The deeper the depth, the lower the speed... This is due to the increase in compression pressure on all sides. This requires greater destruction of the rock and prolonged contact of the teeth with the soil. Therefore, the speed decreases with increasing depth.
A drill bit is used to drill a water, oil or gas well. The tool is indispensable for collecting information about the state of the soil. The chisel is used for drilling the soil, for example, if it is necessary to make a well.
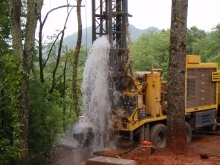
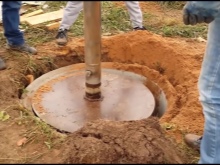
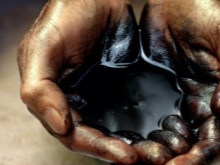
Some types of tools are treated with a special compound, or they use a reinforcement method. This reduces the impact of rocks on the equipment and increases the chance of creating even and smooth walls.
The main features of the equipment:
- creation of a deep passage;
- destruction of the soil;
- alignment of the walls of the well;
- high power;
- efficient work when creating large tunnels;
- reliability and efficiency.
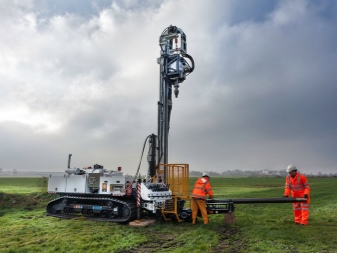
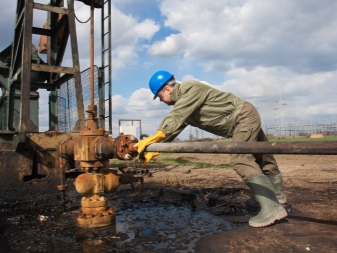
Classification
Drill bits can be classified according to several criteria.
By appointment
There are several types of equipment depending on the purpose.
- For solid drilling... The tool is used to work in a single plane.
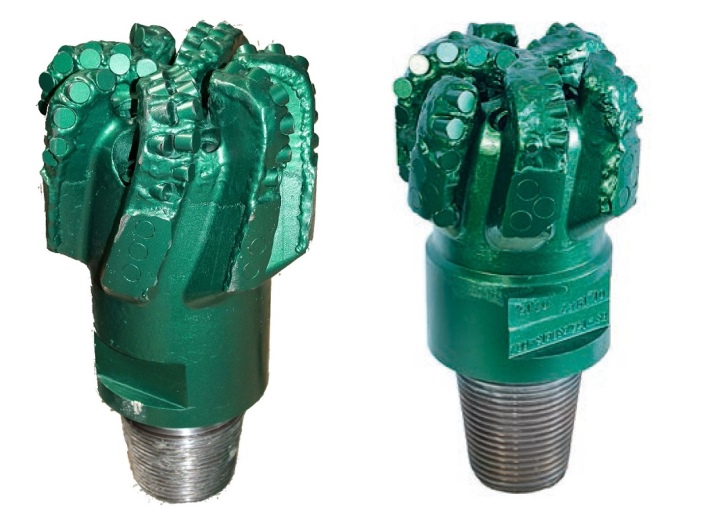
- For core drilling the equipment is used for peripheral destruction.
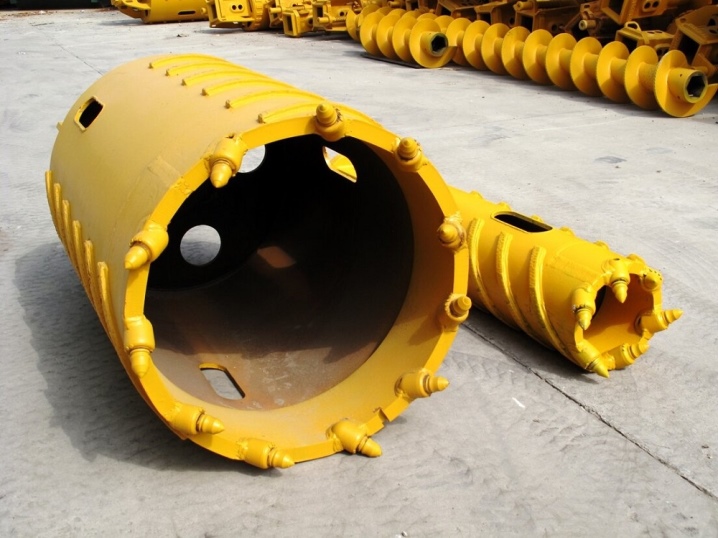
- Specialized tool... Special equipment levels the walls of an already created tunnel or well, destroys cement stone plugs.
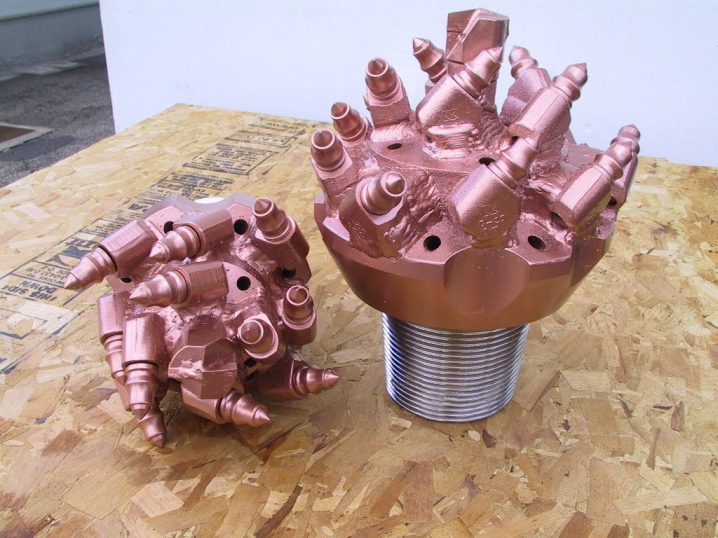
- For percussion wireline drilling the equipment is designed to gradually deform the soil by impacting heavy tools. In turn, the bits can be: flat, I-beam, cross, rounding. All types of tools are designed for work with different degrees of soil hardness. The diameter of the equipment neck is 112, 140, 165, 188, 220 mm.
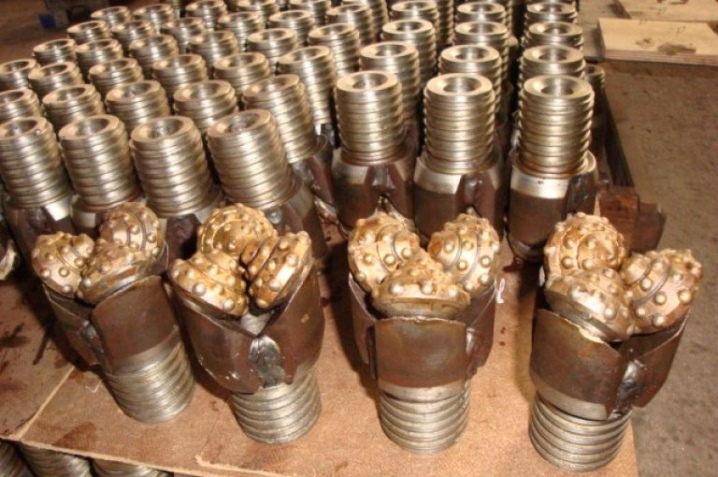
- For rotary drilling the tools work on the rotation of the drilling mechanism. The deformation of the soil occurs due to the rotor rotating around its axis, located on the column. The mechanism is used when drilling water wells.
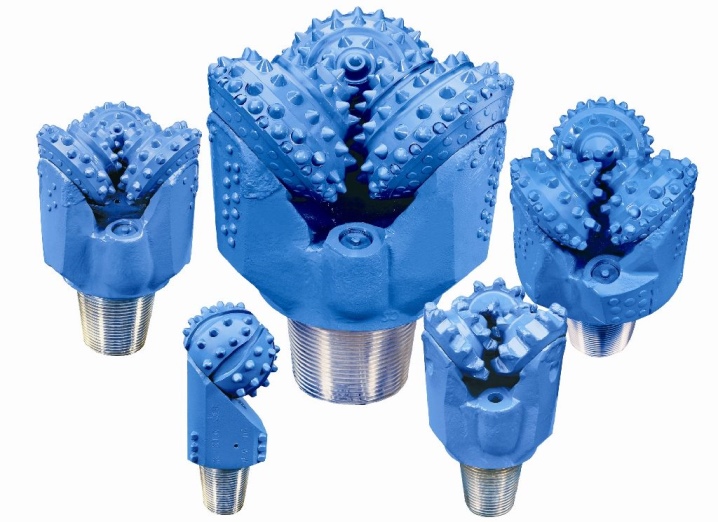
Continuous and coring machines are also suitable for deepening the face.
By the type of the working part
Depending on the type of the working part, the bits are divided into several types.
Diamond
The tool is used for drilling medium hard rocks. However, there is a soil with alternating soft and hard rocks. Therefore, the mechanism is optimal for working with medium hard soil.
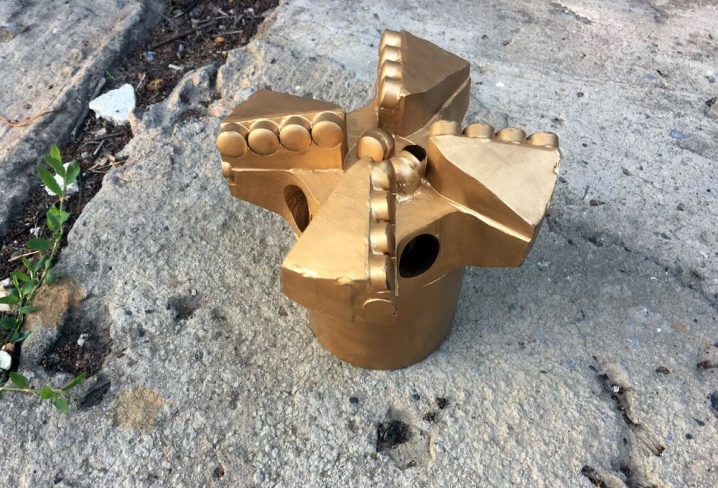
Abrasion of the soil leads to its destruction. A diamond chisel consists of cutters that have a cutting and shearing effect on the rock. The effectiveness of the work depends on the size of the diamonds that are used. According to the location of the diamonds, the tool is divided into two subspecies: single-layer and multi-layer. There is a division of tools according to the location of the mechanism: radial, spiral and stepped chisels.
The equipment has impressive characteristics, but it is considered a rather demanding mechanism. If too hard a piece of soil gets on the element during operation, the equipment will stop working. The diamond element will break or fall out.
The diamond bit needs good flushing. Otherwise, the equipment will stop functioning or give poor performance.
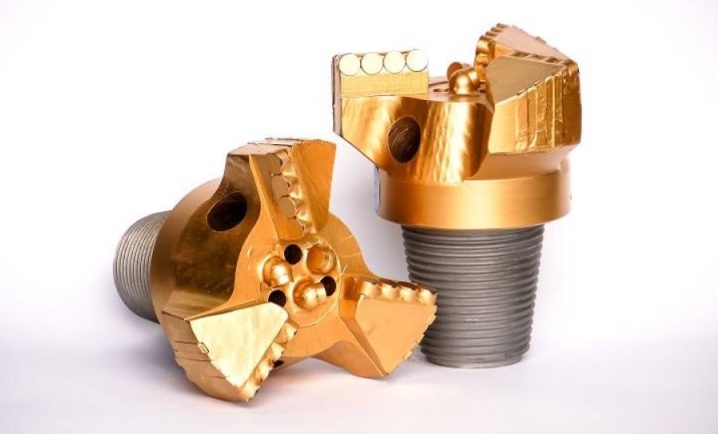
Sharoshechnoe
The design has roller cutter bearings. These are elements in the form of a cone or cylinder, thanks to their work, an impact or shock-shearing effect is created. The latter method of drilling is more efficient. Bearing slippage occurs and additional soil destruction can be carried out. Roller-cone bits are classified according to the nature of rock destruction: single-cone bits are used for deep drilling, two-cone - for geological research, three-cone - for creating oil and gas wells, four-cone - for more difficult conditions.
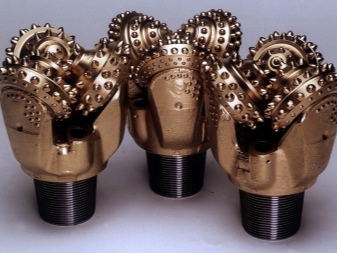
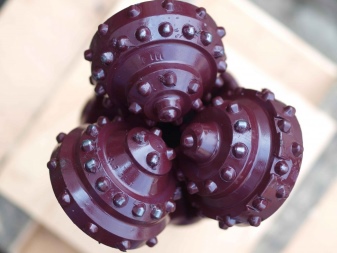
Lopastnoe
This equipment has a simple structure. A bladed chisel is a body with multiple blades. Used by for drilling soft soil. The mechanism is distinguished by efficient operation at high speeds. The tool is divided into subspecies: one-blade pointed chisel, two-bladed, three-bladed, three-bladed abrasive-cutting, six-bladed. All types, except for the one-blade, are used when drilling loose soil. The last three types are used to create oil and gas wells, since they are characterized by a large diameter.
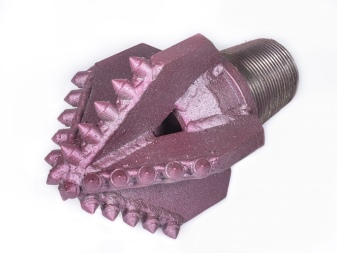
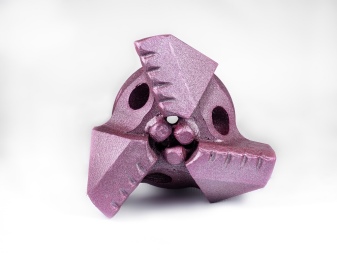
Milling
The milling chisel is distinguished by its primitive structure, strength, stability, it can withstand dynamic loads. The equipment has the form of a monolithic body with crushing mechanisms that ensure drilling efficiency. The tool is suitable for working with hard rocks, is not afraid of metal elements. Used for punching cement or concrete cork. The equipment is indispensable for drilling wells for oil, gas and water supply. Despite its effectiveness and high performance, there are a number of disadvantages. The milling bit is not used for drilling loose rock. And also fast passage is excluded. The instrument is characterized by primitive flushing, which is also a minor disadvantage.
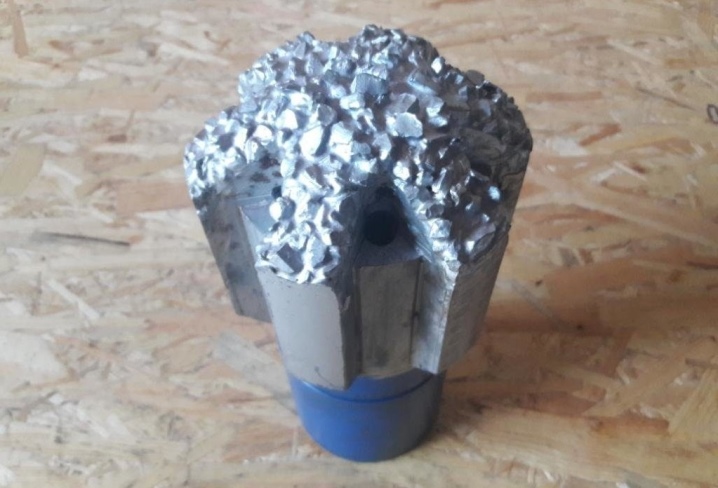
All types of bits have their own standard size, including the diameter of the tool and the designation of the connecting thread. The equipment is mass-produced in accordance with GOST 20692-2003.
To ensure that the mechanism does not wear out, a rational working method is calculated for each type of tool. The formula includes the RPM of the downhole mechanism, the load and the pressure in the pumps. For correct working off, the load must be at least 75% of the column weight. Otherwise, overloading and premature wear will occur. Underloading leads to a decrease in penetration.
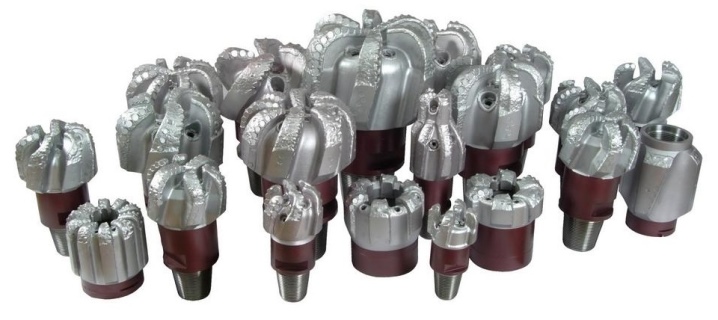
Popular manufacturers
A small number of companies are engaged in the production of drilling equipment. This is associated with significant manufacturing costs as well as low capacity in the drilling rig market.
Some of the popular bit manufacturers are domestic brands OJSC "VolgaBurmash" and NPP "BurinTech"... Plants supply the industry with roller cone tools and diamond cutters. The products are aimed at oil and gas production, therefore, they must meet all technological requirements. The equipment is produced using high technologies.
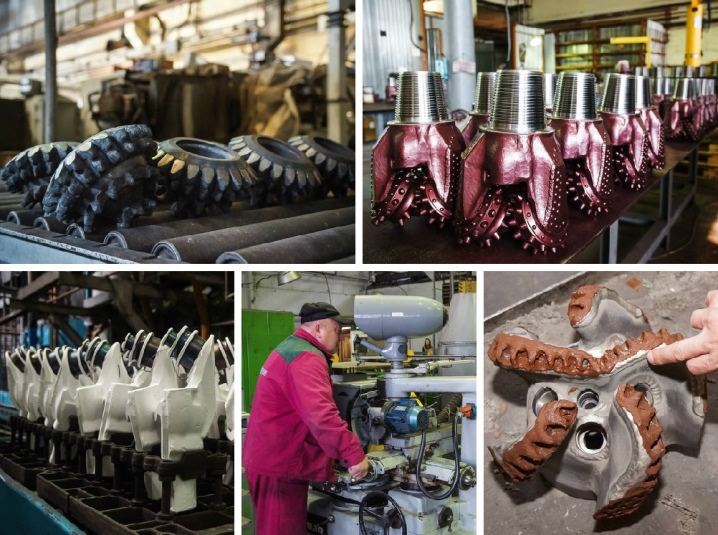
All models can be used to work at depths of up to 6,000 m. The bits are suitable for offshore drilling and drilling in an explosive environment.
The products are distinguished by their reliability and long service life. The body consists of reinforced parts. Some roller cone models are equipped with a special seal to protect the thrust bearing.
The tool has milling and carbide cutting equipment, is used for drilling wells, expanding the diameter of the bottom hole and other types of work.
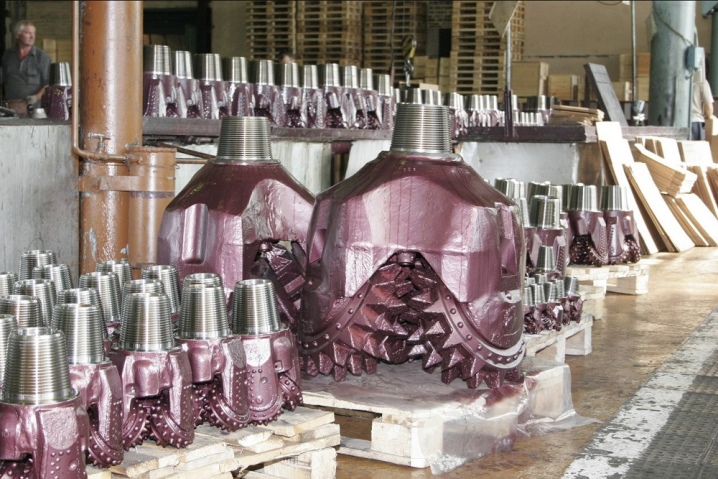
Another company "Targin" is engaged in the production of bits of its own production. Models are produced with the TarginTarbit marking. Drilling equipment and heads are suitable for work at depths from 43 to 490 m. The company also remanufactures worn out equipment and deformed PDC bits.
For the construction of water supply systems and the mining industry, factories are considered the main manufacturers of bits OJSC UralBurmash and CJSC Gormash. The tool used for geological and construction work is not subject to heavy stress. Therefore, the companies produce inexpensive standard tools for drilling water wells from 30 to 300 m. For the mining industry, brands produce roller cone and vane equipment. High technologies and high quality materials are used in the manufacture.
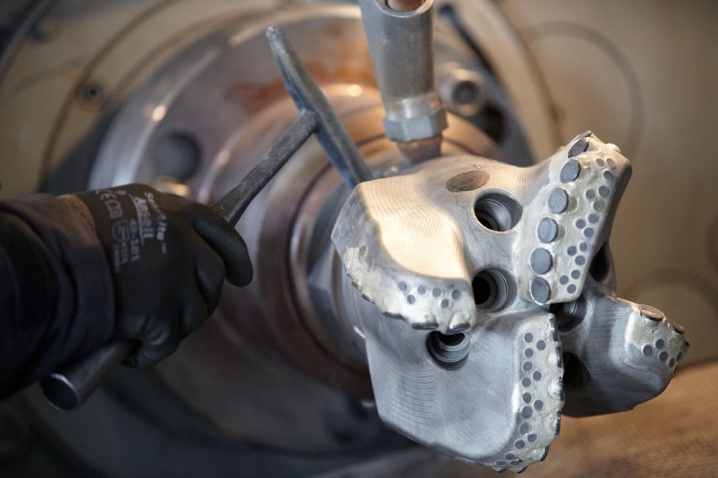
LLC "Plant of Drilling Technologies" - a company that also manufactures bits. The brand's assortment consists of mechanisms for prospecting, mining, hydrogeological industry, as well as for installing foundations and driving support piles. The enterprise produces roller cone and blade bits for drilling loose, soft soil. There are classic models for hard soil and low abrasion soil.
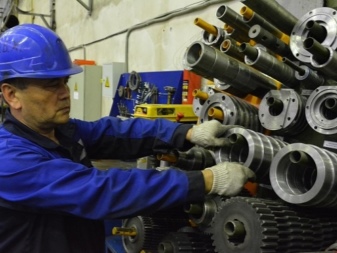
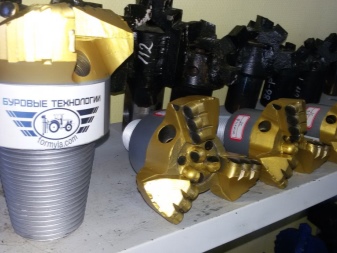
The paddle equipment for sticky soil has an original structure, which provides performance at high speed and increases wear resistance.
Drilling mechanisms are manufactured by Drilling Tool brand. The plant manufactures bits for small drilling rigs: auger tools and equipment with side and center flushing. For the geological industry, the production of blade mechanisms for drilling abrasive soil has been established.
The brand is a manufacturer of PDC tools. Diamond cutters have polycrystalline properties and are located on a minimum number of blades. This makes it possible to work at high speed. Wear-resistant elements are not afraid of the impact of soil of any hardness.
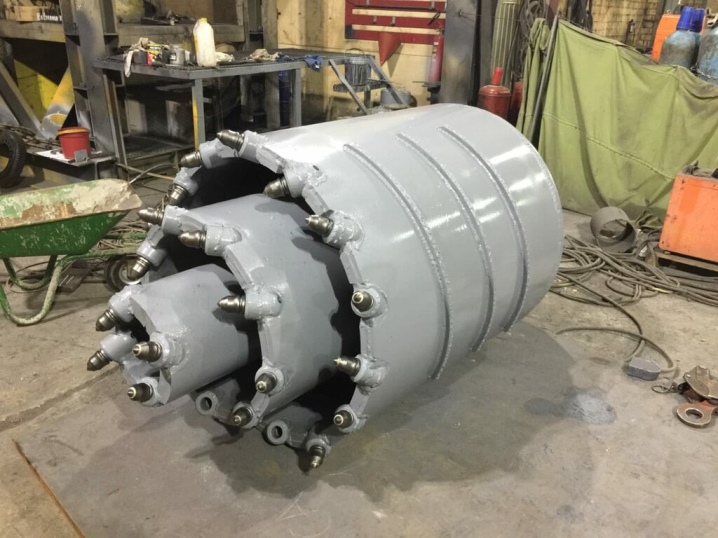
Nuances of choice
There are three main criteria for choosing a drill bit.
Appointment
For soft ground drilling and light work applications, it is best to choose roller cone or blade bits. The equipment is distinguished by its reliability and efficient operation at high speeds. Both types of tools are used for geological prospecting of soil samples and for drilling in medium-hard soil.
More difficult drilling conditions involve the use of diamond or milling bits. They are suitable for the installation of foundations and drilling of wells for various purposes.
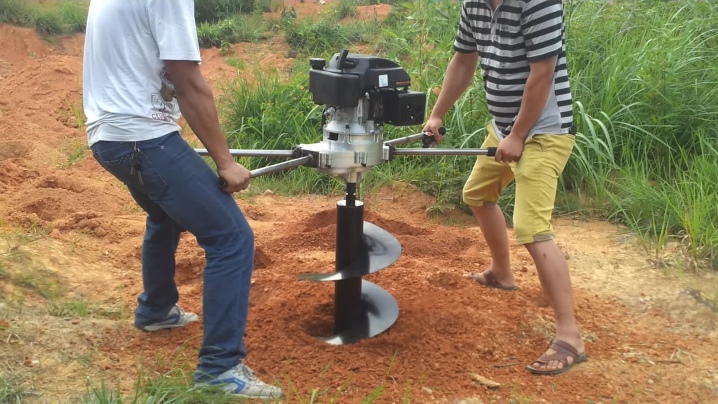
Material and quality
Reliable equipment can withstand heavy loads and is not subject to deformation upon impact. In the manufacture of mechanisms, carbon steel is used. This material comes in different qualities. When choosing, special attention is paid to the quality of the cutters. Their edge should not have chips, scratches, the material should not crumble.
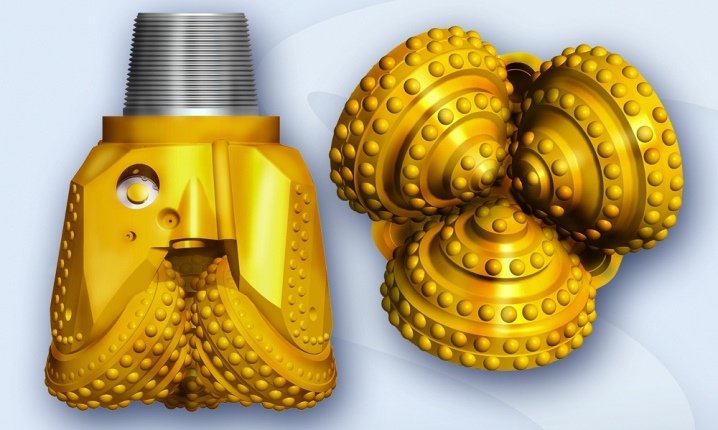
Some manufacturers use a special compound that is used to coat the main engine parts and cutting elements. The coating increases the service life and prevents the negative impact of the soil.
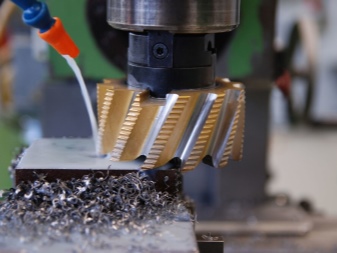
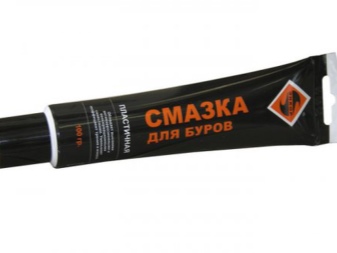
Flushing method
There are several types of flushing in the bits - central and side. Both systems have their pros and cons. The central type of flushing provides cooling and cleaning of the weapon, but on contact with the bearing, the jet loses pressure. The advantages of side flushing are the high pressure of the jet, which increases the drilling speed. However, the action of the liquid falls on a part of the periphery, when air with liquid and sludge is formed in the bearing operation zone.
For large installations, it is better to use a combined flush. This cleans the central element of the bottomhole together with the bearings, excluding the adhesion of sludge.
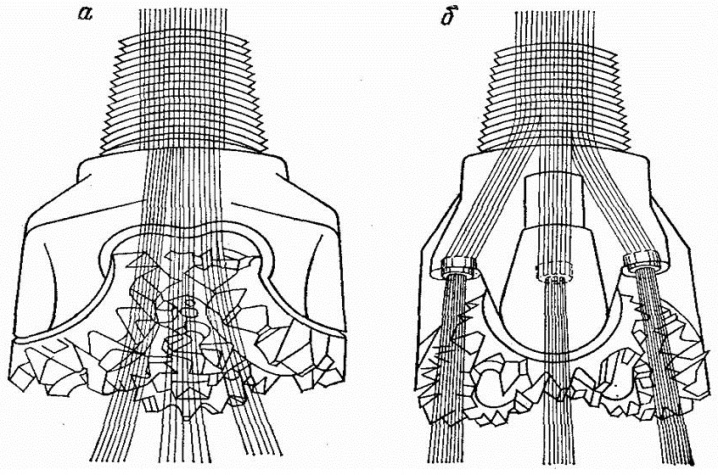
The drill bit is an indispensable tool for various industries. The equipment is divided into types and subspecies. Each tool has its own purpose and characteristics. Bit selection is based on several aspects. The given material will answer many questions and help you choose the right tool for a particular type of drilling.
In the next video, you will find out which bit is used to drill oil wells.
The comment was sent successfully.