What is a curb and how is it made?
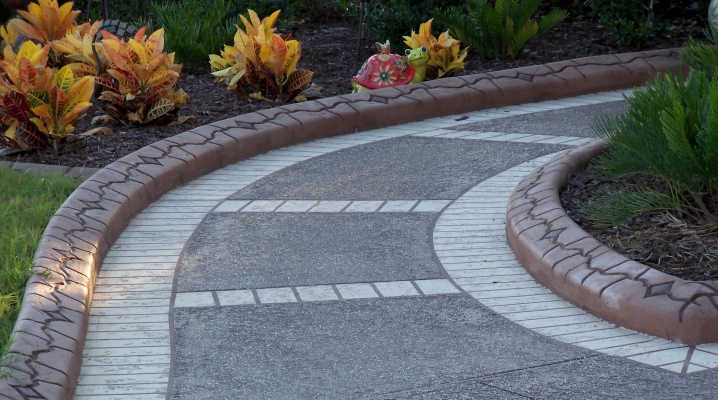
The side stone, or curb, is an integral part of any urban or suburban architecture. This product is used as a separator for roadways and sidewalks, bike paths, lawns and other areas.
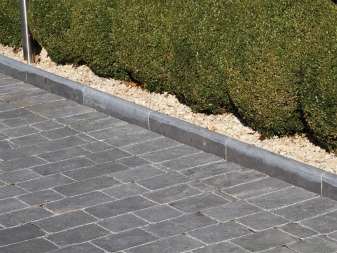
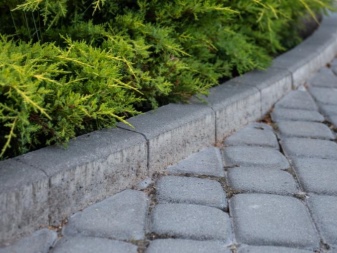
What it is?
The product creates a reliable barrier against roadside erosion, soil slippage, contributes to the long service life of the tiled surface, since the elements do not deform from mechanical stress and natural influences. The curb can be concrete or plastic, which differs from the classic curb in that when installing under it, it is not necessary to lay a seal and create a depression.
The lower part of the curb need not be sunk into the ground, while the upper part, on the contrary, should protrude above the dividing zones. With curbs, any landscape has a neat and complete look.

How is the curb made?
Like any building product, the curb must have certain characteristics and comply with established standards. The product is made using two technologies.
- Vibration casting. Provides correct dimensions and clear geometry. Production is aimed at increasing the density of concrete and reducing its porous structure. Structurally, this is a two-piece product, that is, it has an inner and an outer part.

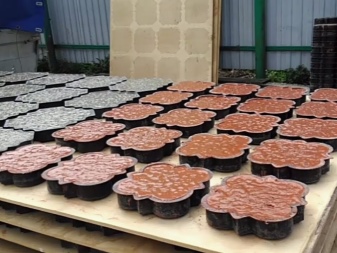
- Vibrocompression. The produced curbs are distinguished by the presence of chips and cracks, that is, they are low-decorative. The technology increases the porosity of concrete, which negatively affects the strength of the material and its frost resistance. However, manufacturers guarantee a 30-year period for such products, noting their focus on installation in conditions of high humidity and temperature changes.
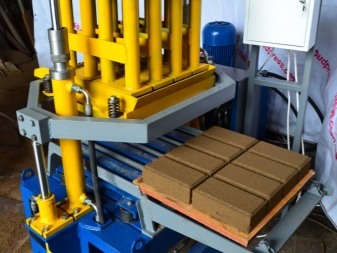
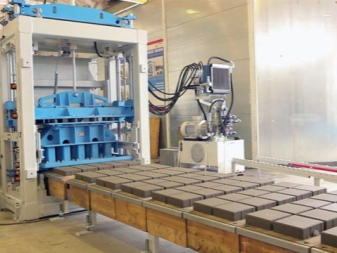
Both methods have disadvantages and advantages. There are no specific manufacturing rules, differences are classified based on the material chosen for production, and the choice is not limited to concrete.
The range of curbs is not wide. The decorative component leaves much to be desired - this is the primary reason that many home craftsmen choose to independently make road or garden curbs. Thus, outside the workshop, you can get products with any section and different colors.
The required qualities are given to the finished elements with the help of dry building mixtures. They provide the curb with resistance to moisture and low temperature. Products can be dyed at the kneading stage by adding special dyes to the mass. This approach is more costly financially, but the laid curb will not need to be periodically updated for protection and an attractive appearance.
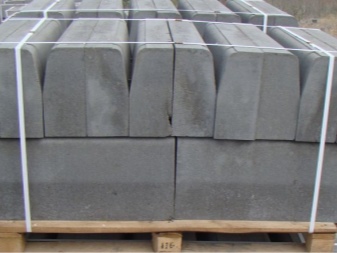
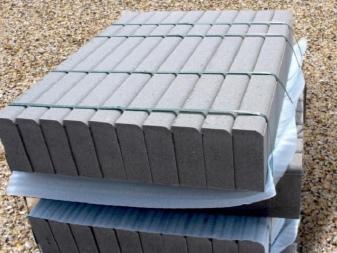
Species overview
Modern curbs are made of bricks, plastic, wood, concrete and metal. But any option should be:
- durable;
- resistant to temperature changes;
- moisture resistant;
- practical for use and care;
- aesthetically pleasing.
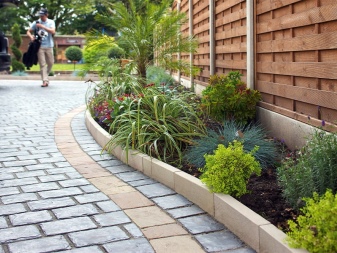
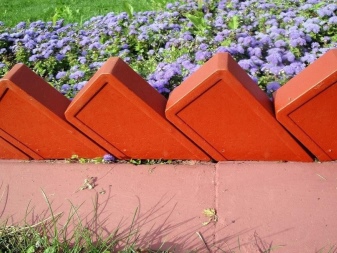
All curbs are created on a natural basis and have an attractive appearance, serving as a decoration for any type of roadway. The quality of the material makes it possible to install the sides on almost any object (along the highway, sidewalks, on the basement of the house).
Several types of side stone are produced:
- road;
- garden;
- trunk;
- sidewalk.
Fences are classified according to the type of raw materials used.
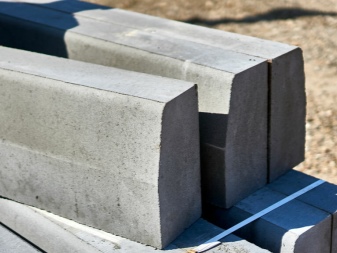
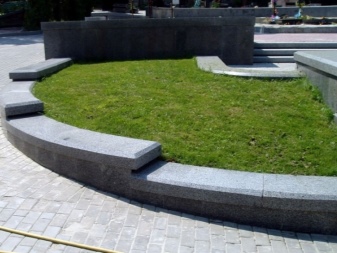
Vibropressed (curb)
With their high strength, these fences serve for a long time with a significant change in temperature conditions. The moisture resistance of the material allows laying the sides in all climatic areas.
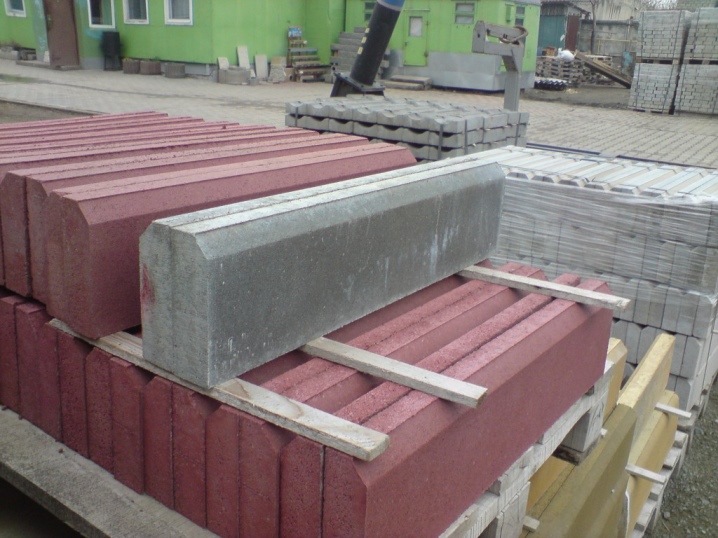
Reinforced concrete
Reinforced concrete structures are made of reinforced concrete of fine fraction, which is characterized by durability and resistance to mechanical damage.
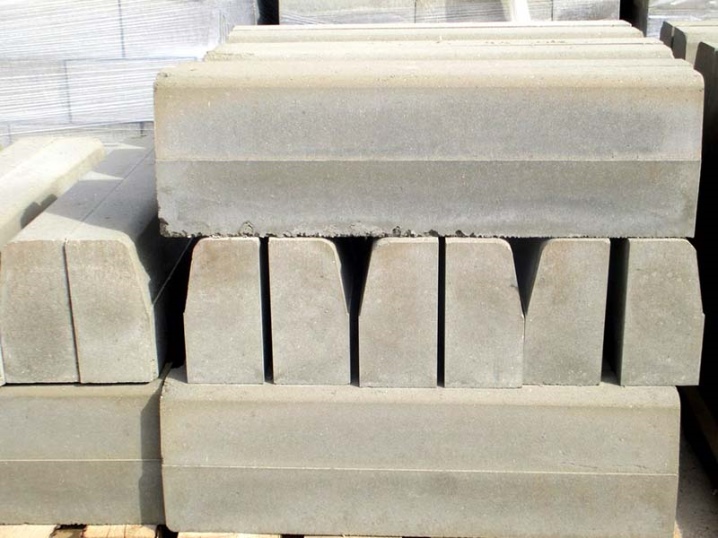
Granite
The most durable, but also the most expensive curbs. Resistant to strong temperature changes and abrasion.
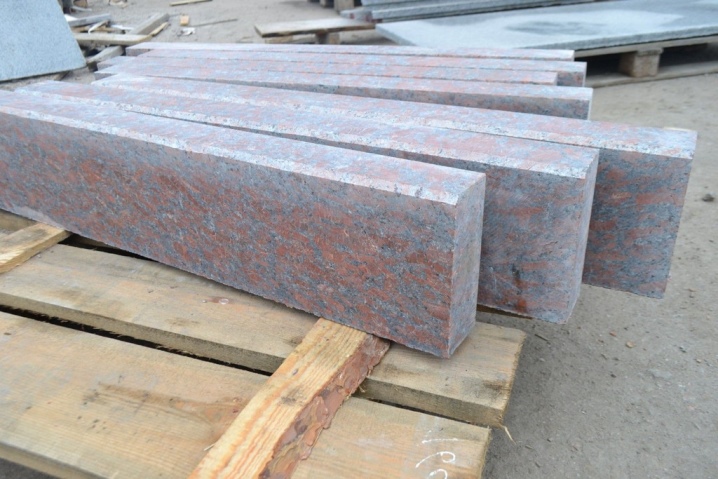
Concrete
They are widely used in the process of laying roads to separate carriageways and pedestrian areas. Manufactured according to GOST by pressing or casting.
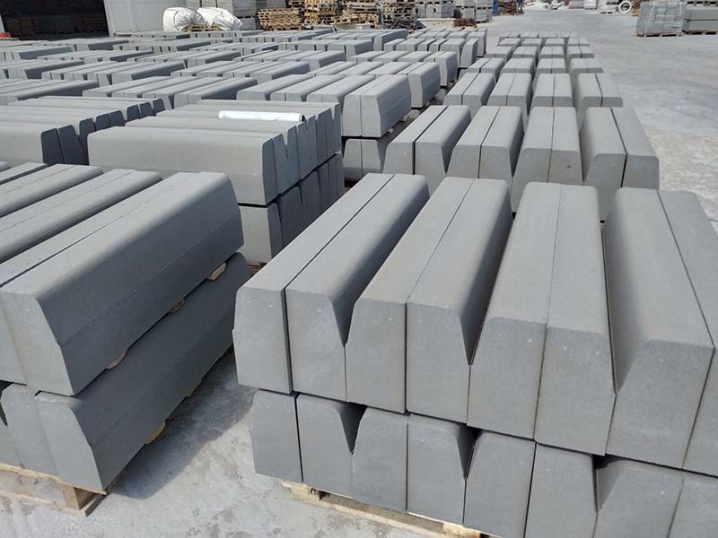
Vibrocast
Manufactured by casting, the curbs are geometrically disturbed. This is due to the fact that a liquid concrete solution is used in the production. Air remains in the solution, so the structure of the elements is porous and not strong enough.
This type of curb stones is inferior in price to curb stones, but is available only in gray. The presence of a reinforcing frame complicates the installation of cut curbs. When installed, the docking points look rough.
The complexity also lies in the installation at planned turns. When creating semicircular shapes, the reinforcement is cut not without prejudice to the appearance of the product as a whole.
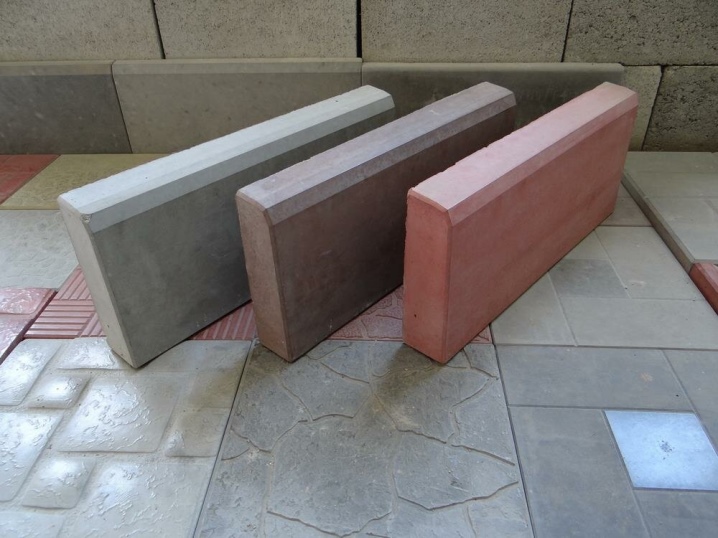
Plastic
Lightweight plastic is easy to process, so you can easily build a radius curb from it and create a fence of almost any shape - from straight to rounded. A plastic curb is considered a repairable material, since individual sections can be easily replaced if damaged, which makes it very difficult to work with stone curbs.
The plastic curb can be colored, which will allow you to quickly and economically decorate the landscape. Plastic fencing looks especially good on playgrounds or sports grounds and summer cottages.
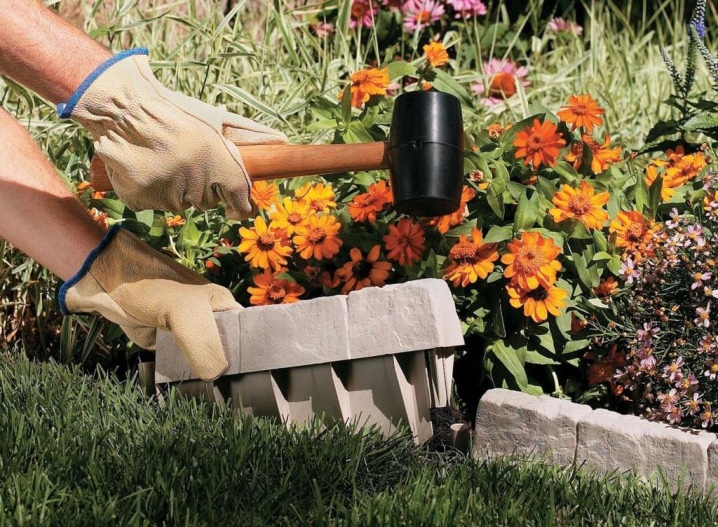
Among the shortcomings, it is worth noting weak fire resistance, low resistance to weathering and mechanical damage.
Also, the classification of curb stones is carried out regardless of the type:
- BKU - products intended for installation along bike paths and pedestrian zones;
- BKR - designed to be placed on roads and sidewalks where there is a turn;
- BKK - is used to decoratively highlight a certain territory, it is distinguished by a conical surface on top.
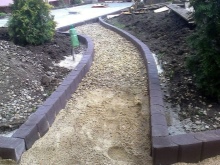
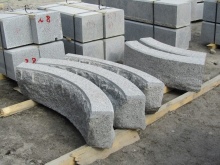
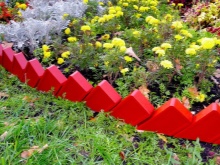
Dimensions and weight
Curb stones, according to GOST, are made on the basis of a curb stone. In the Soviet period, the standards were 10x1.5x3 cm, and now curbs can be made to any size. The curb can have different dimensions. How much a product weighs depends on the material of its base. For example, a meter-long vibropressed curb weighs from 35 kg. Of course, the weight of plastic is significantly different from vibrocasting, especially from granite and reinforced concrete structures.
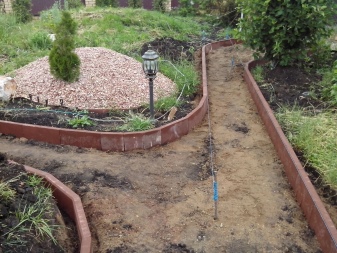
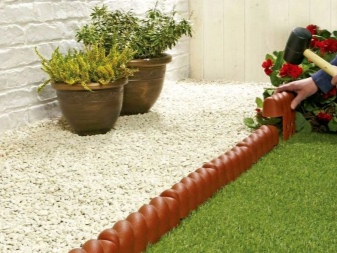
The curb is set so that the protruding part is above the boundary plane. The height of the structure is from 35 cm, if necessary, a higher curbstone is ordered.
The width of the curb is inferior to the border. The purpose of this structure is to delimit lawns from the sidewalk, separate bike paths from the rest of the spaces, strengthen the asphalt road on highways and decorate the street space. The length of a standard curb usually starts from half a meter.
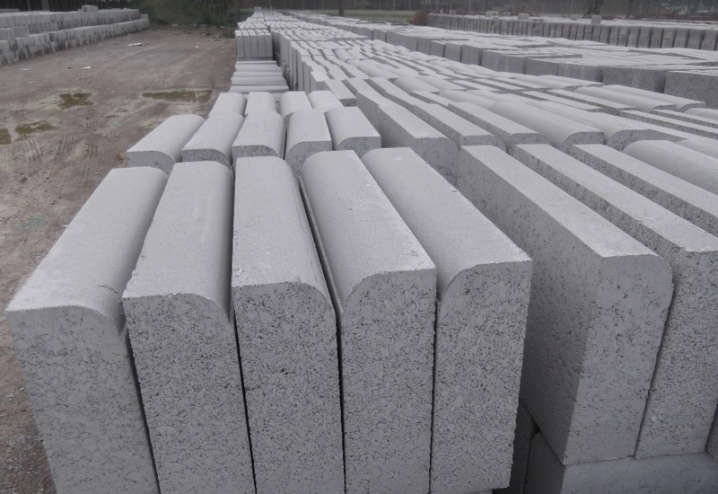
How to install correctly?
The curb can be purchased in the construction market, and then make an independent installation. The work is not difficult from a technical point of view.
- It is necessary to define the terrain and preliminarily depict everything schematically in order to "transfer" the sketches to the "ground" afterwards.
- According to the scheme drawn up, drive in the pegs and pull the rope (fishing line), forming the future placement of the side stones.
- Determine the depth of the trench and dig it out.Naturally, there is no need to dig a half-meter trench on a personal plot (only if necessary).
- Make drainage. The depth of the excavation is determined based on the volume of the compacted crushed stone substrate. A sufficiently compacted base prevents shrinkage and deformation of the curb structure during operation.
- Tamp the filled up crushed stone and sand. Crushed stone will form the basis for the sand layer.
- Prepare a cement mortar of a suitable consistency.
- Set the curb by leveling the horizon under the line or a level by tapping on the curb with a rubber mallet.
- After the level is determined, you can start filling the voids, in parallel checking how level the curb is.
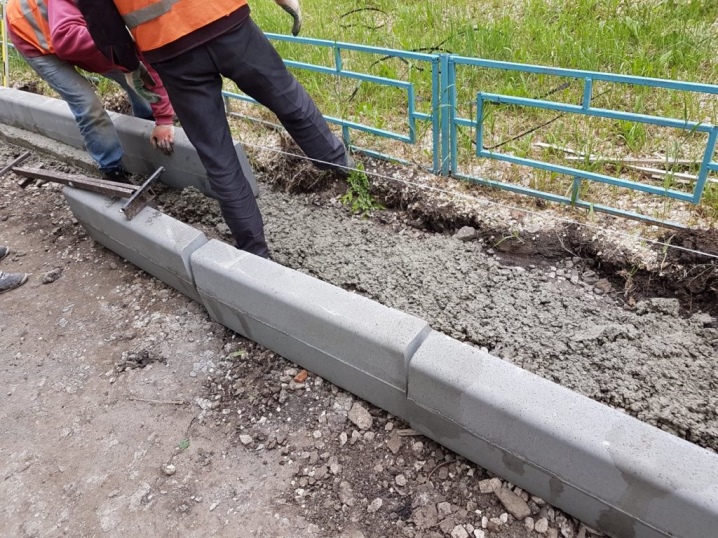
It is advisable to put a separating layer of geotextile under the rubble. Its presence will exclude the appearance of soil and voids in the rubble, and also will not allow the entire structure to deform. Dry sand must be moistened, otherwise it will be simply unrealistic to compact it in the future. Dumping of fines contributes to the leveling of the curb with great accuracy.
This completes all the preparatory steps. Then the installation of the curb elements is carried out according to a typical installation. To control the curb device horizontally, you will need a building level.
Another version of the curb device involves the installation of elements on top of a concrete solution. It also fills the gaps between the side stone and the walls of the dug groove.
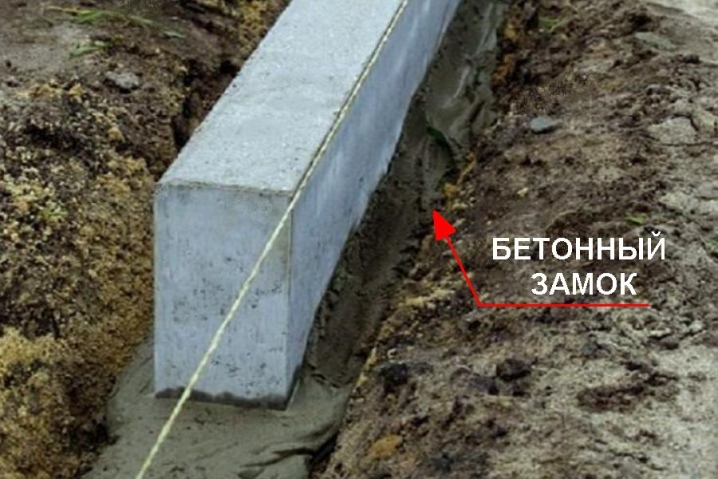
With a larger sole area, the structure is strengthened in relation to static and dynamic loads.
If the installation of the curb occurs before the paving slabs are laid, it is permissible to ram the base no earlier than two days later. The structure needs up to 48 hours for it to finally settle down. This will reduce the likelihood of cracks or damage to the joints.
Curb elements can be bought ready-made or made with your own hands. To create bumpers on your own, it is convenient to use ready-made forms or make blanks with your own hands. In this case, you will need to install the formwork.

Any block size is possible. The only thing to consider is the length of the section in relation to piece curbs - it should be up to 2 m. Otherwise, it will be difficult to put the curb structure, and it will quickly collapse.
Curly elements laid on top (a mixture of building components, in the classic version - quarry sand and construction cement) or sand can slide along the perimeter. In this regard, such a facing material must be placed in a rigid concrete box. The curb will add completeness to the exterior, prevent soil displacement in the paving area and keep the surface clean.
It is not allowed to install concrete products on top of a fertile layer prone to subsidence after decomposition of organic content.
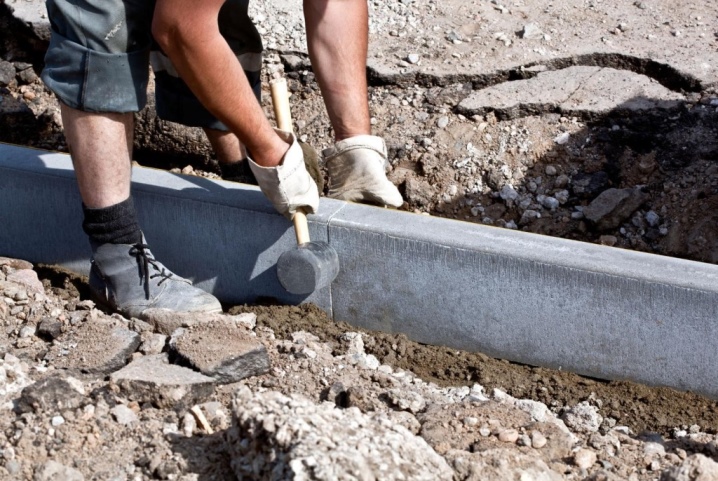
In the paving area, it must be removed entirely. The standard pit depth is greater than the width of the paving stone, but is inferior to the curb in vertical dimension. Therefore, you need to perform the actions in the following sequence.
- Pour sand into the pit if there is a low GWL or crushed stone in wet soil. Spread over the bottom, leaving approximately 10 cm to the ground (5 cm of the contact layer on which the tiles are to be laid, taking into account its thickness).
- Along the perimeter of the pit, make trenches according to the size of the curb element, 2 cm of the sand-concrete mixture on which it is installed, and the substrate layer (15-20 cm).
- Aggregates are compacted using an areal vibrator (vibrating plate) or a manual rammer. It is not recommended to water the sand with a bucket / hose in the groove, it is better to wet it well before laying it in the trench.
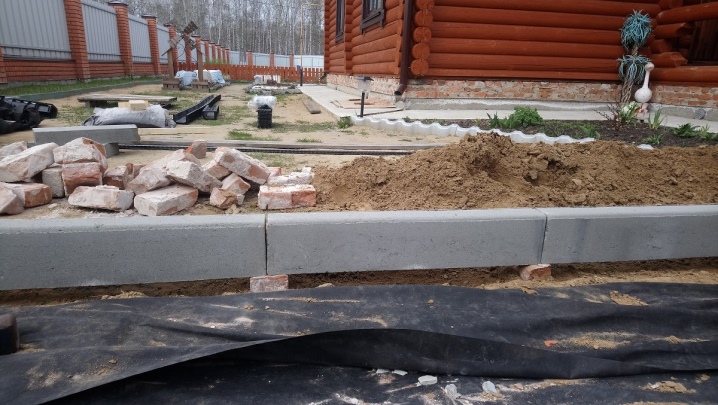
To make it easier for the master to put the curb under the tile and fix it with concrete from the outer or inner edge, the trench should be 2 times wider than the curb itself (4 cm on both sides).
The curb manufacturing process is as follows:
- preparation of a mold for pouring;
- preparation of a dry mixture in the calculation of 3 parts of sand to 1 part of cement, thorough mixing of the components with each other;
- the addition of fine crushed stone in the calculation of 3 parts of crushed stone to 1 part of the cement-sand mixture, the subsequent filling of the mixture with water and stirring (no lumps and air bubbles should remain in the solution).
To facilitate installation work, you need to make a slight bevel on one side of the product. This will work if you cut off the excess. For a more complete type of paving, sidewalk curbs are suitable.
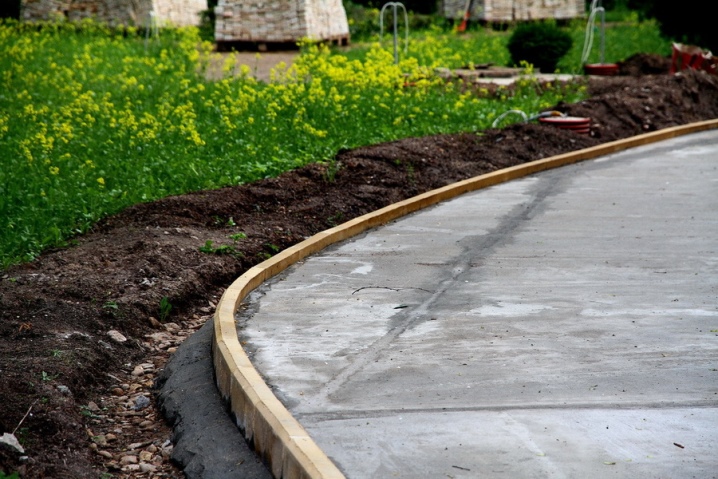
In addition to the aesthetic function, road curbs play a supporting role. A storm drain is installed along the paths to regulate the direction of wastewater.
Therefore, it is important to choose a high-quality curbstone that assumes a long service life.
The curb elements are laid at the level of the cord. In this case, the curb elements are aligned in height. It is necessary to pour the solution into the trench where required.
The butt joints are filled with mortar and the structure is left to harden for 24 hours. Soil is poured into the gap, ramming in the most careful way. It should be remembered that you need to lay out the tiles after the border has been installed.
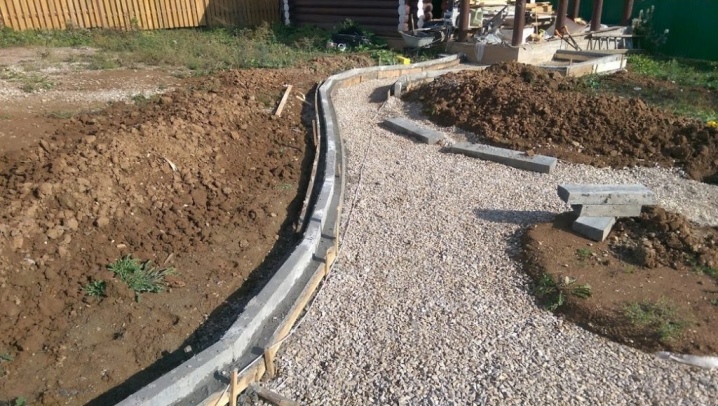
Installation of PVC curbs
If we compare the work with plastic and concrete restraints, then plastic wins in simplicity. Installation of PVC elements is much easier, which is facilitated by their light weight.
Technology:
- a groove is dug in the right place at a depth of 10 cm;
- pegs are driven in there, located at the base of the pvc-curb;
- separate elements are connected with a "lock", assembling a single row of them;
- the fence is leveled at the building level, the groove is filled up.
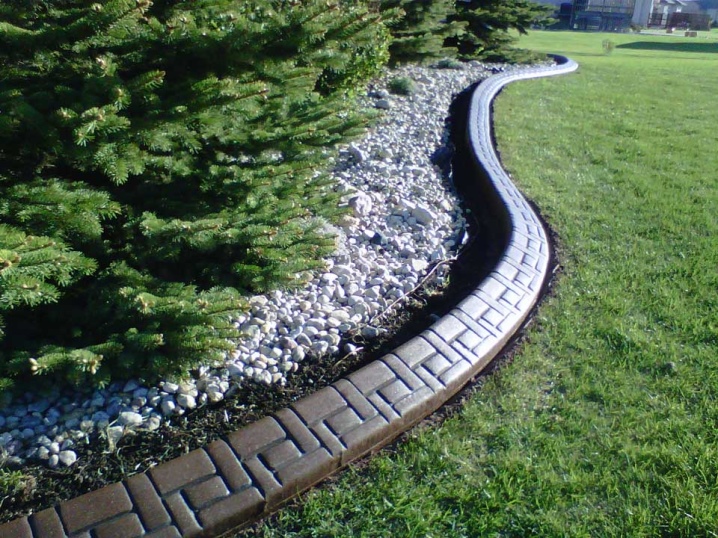
The peculiarity of installing such a curb is that there is no preliminary preparation stage. Plastic fencing is suitable for decorating flower beds in personal plots.
The correct sequence of stages in the installation technology of curbs of any kind is a guarantee of high-quality work.
How to make a curb with your own hands, see below.
The comment was sent successfully.