All about horizontal drilling
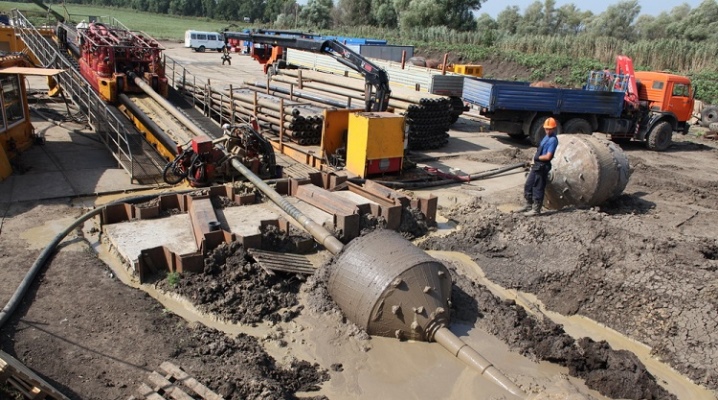
Horizontal drilling is one of the types of wells. The technology has become widespread in the field of construction, the oil and gas industry, as well as when working in urban crowded conditions. Let us consider in more detail what the essence of the method is, and what stages are the main ones for this type of drilling.
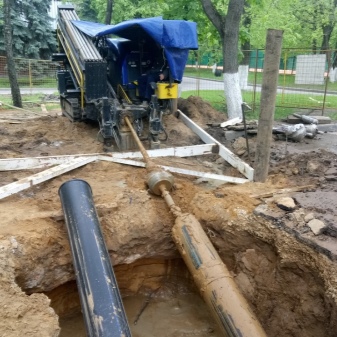
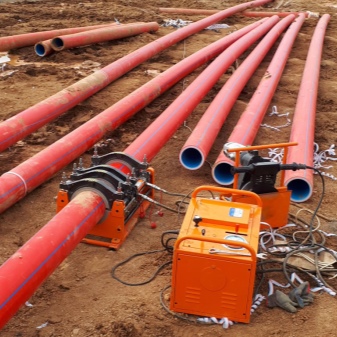
What it is?
Horizontal directional drilling (HDD) is a type of trenchless drilling that helps to preserve the surface of the landscape (for example, roadbed, landscaping elements, etc.). This technique appeared back in the 60s of the last century and is popular today. The technique makes it possible to reduce drilling costs, or rather, landscape restoration after this process.
On average, the cost of work is reduced by 2-4 times.
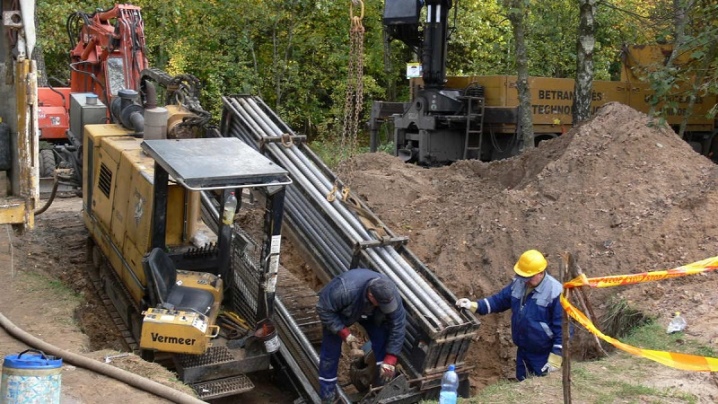
Technology features
In simple terms, then the principle of the method is reduced to the creation of 2 punctures in the ground (pits) and an underground "passage" between them using a horizontally inclined pipe laying. This technology is also used in cases where it is impossible to dig a trench (for example, on historically valuable objects). The technique involves the implementation of preparatory work (soil analysis, preparation of 2 sites - at the entry and exit points of the trench), the formation of a pilot well and its subsequent expansion in accordance with the pipe diameter. At the final stage of work, pipes and / or wires are pulled into the resulting trenches.
With HDD, both plastic and steel pipes can be laid in the trench. The former can be fixed at an angle, while the latter can only be fixed along a straight path. This allows the use of polypropylene pipes in trenches under water bodies.
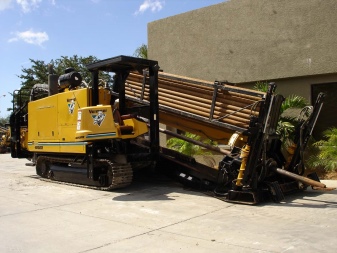
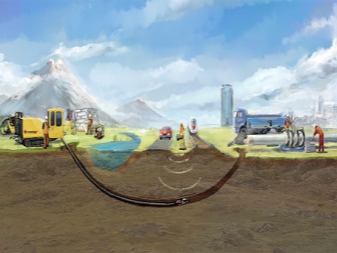
Horizontal drilling is effective in solving the following tasks:
- laying of electric cables, gas and pipelines to objects;
- obtaining wells for oil production and production of other minerals;
- renovation of communications that have undergone wear and tear;
- the formation of underground highways.
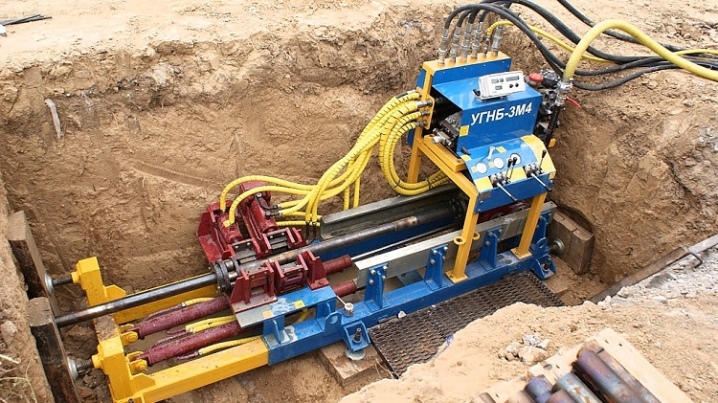
In addition to these savings, this drilling technique has other advantages:
- minimal destruction of the earth's surface (only 2 punctures are made);
- reduction of work time by 30%;
- reduction in the number of workers in the brigade (3-5 people are required);
- mobility of equipment, it is easy to install and transport;
- the ability to carry out work in any territory (historical centers, in the territory of the passage of high-voltage lines) and soils;
- the ability to preserve the soil without damaging its fertile layers;
- the implementation of work does not require a change in the usual rhythm: overlapping movement, etc.;
- no harm to the environment.
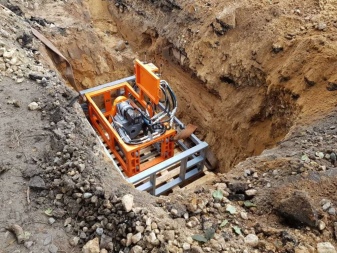
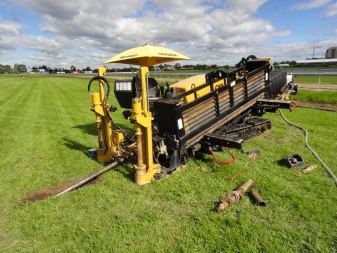
The described benefits contribute to the popularity and widespread adoption of the HDD method. However, it also has disadvantages.
- With the use of standard installations for deep drilling, it is possible to lay pipes with a length of no more than 350-400 meters. If you need to lay a longer pipeline, you have to make joints.
- If it is necessary to install longer pipes underground or to pass them at great depths, the trenchless method will be too costly.
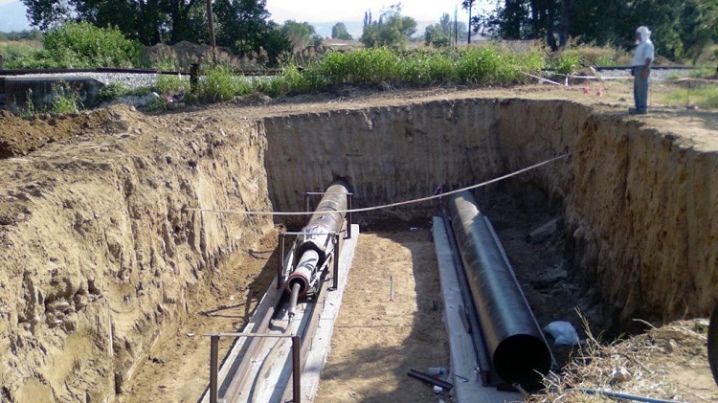
Equipment
To carry out HDD, machines and tools are used that can pierce the upper layers of the soil and go deeper.Based on the volume of work and the type of soil, these can be special rock drills, motor-drills or drilling machines. The first 2 options are usually used for personal use, while drilling machines are used on large objects, solid and hard soils.
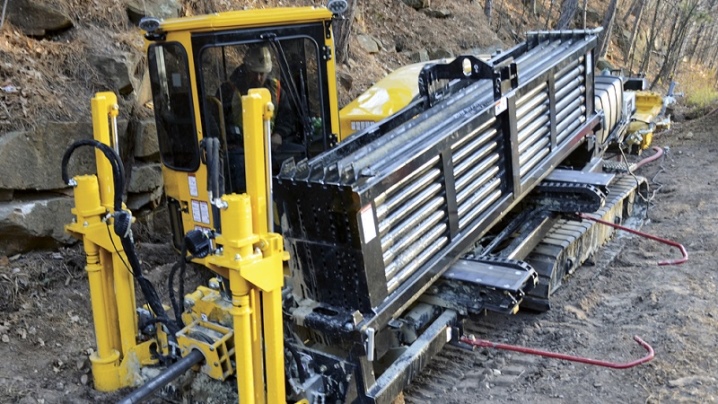
Cars
A drilling machine or HDD rig is a type of industrial equipment that operates on a diesel engine. The main functional elements of the machine are a hydraulic station, a carriage, a control panel. The latter allows the operator to control the operation and movement of the machine and looks like a special control panel. The creation of a trench itself is possible thanks to a drill. During rotation, the drill heats up, which is fraught with its rapid failure. This can be avoided by regularly cooling the metal part with water. For this, a water supply hose is used - another element of the drilling machine.
Drilling equipment is classified based on pulling force boundary (measured in tonnes), maximum drill length and borehole diameter. Based on these parameters, the power of the drill is calculated. A more compact analogue of a drilling rig is a motor-drill. Its main purpose is to carry out small earthworks. However, the piercing part of the drilling process in some cases is quite easily and quickly performed with a motor-drill. Since the motor-drill works as auger equipment, it is often called a press-auger machine. This rig includes a drill, rod and motor.
Drilling with a motor-drill is possible even by one person, the devices differ in the type of power and are divided into professional and for private use.
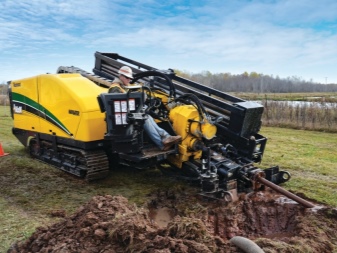
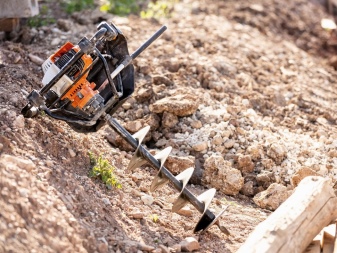
Locating systems
Such a system is necessary to accurately control the trajectory of the drill head and its exit at the location of the second puncture. It is a probe attached to the drill head. The location of the probe is monitored by workers using locators.
The use of a location system prevents the drill head from colliding with natural obstacles, for example, deposits of dense soils, underground waters, stones.
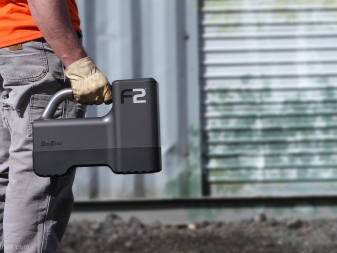
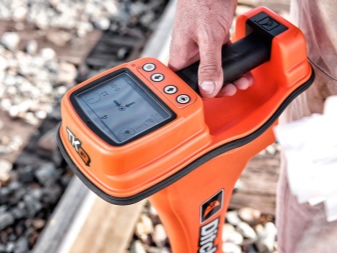
Supporting tools
This type of tools becomes necessary at the stage of puncturing the soil. Used rods, threaded screw tools, expanders, pumps. The choice of a specific tool is determined by the type of soil and the stages of work. Ancillary tools also include clamps and adapters, the main task of which is to help in obtaining a pipeline of the required length. Expanders are used to obtain a channel of the required diameter. The unit is supplied with water using a pump system. Generators ensure uninterrupted operation of the equipment, and the lighting system allows drilling even in the dark.
Auxiliary tools or consumables include copper-graphite grease. It is used to lubricate the joints of the drill rods. Horizontal drilling necessarily implies the use of bentonite, the quality of which largely affects the speed of work, the reliability of the trench, and environmental safety. Bentonite is a multicomponent composition based on aluminosilicate, characterized by increased dispersion and hydrophilic properties. The rest of the ingredients of the solution and their concentration are selected on the basis of soil analysis. The purpose of using bentonite is to strengthen the walls of the trench, to avoid shedding the soil.
Also, the solution prevents the adhesion of soil to the equipment and cools the rotating elements.
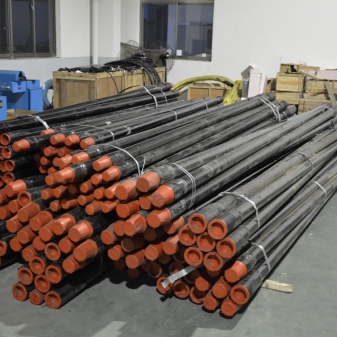
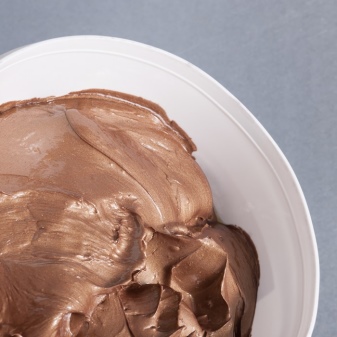
Step-by-step description of the process
HDD is carried out in several stages, and the general scheme of work looks like this:
- preparation of project documents, which reflect all the necessary calculations;
- coordination of the project with the owner of the site (if it is a private territory) and authorities (if it comes to carrying out work at municipal facilities);
- digging pits: one at the start of work, the second at the point where the pipeline exits;
- laying of the necessary equipment by means of drilling rigs;
- completion of work: backfilling of the pits, if necessary - restoration of the landscape at the site of the pits.
Before drilling a hole in the ground, care must be taken to prepare the landscape. To install universal drilling equipment, you will need a flat area of 10x15 meters, it is located directly above the place of the inlet puncture. You can do it yourself or using special equipment. Make sure that there are detours to this site. After that, the delivery and installation of drilling equipment takes place.
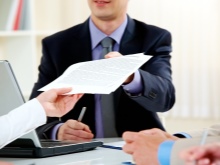
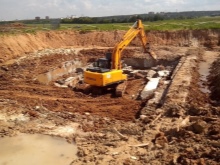
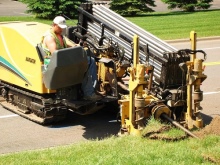
In addition to the HDD machine, equipment for bentonite slurry preparation will be required. It is used to strengthen the walls of the trench and remove soil from the canal. Installation for bentonite slurry is installed at a distance of 10 meters from the drilling machine. Small indentations are created in the vicinity of the intended puncture points in case of excess mortar.
The preparation stage also implies the installation and verification of radio communications between the workers of the brigade, soil analysis. Based on this analysis, one or another route for drilling is selected. The drilling area should be protected with yellow warning tape. Then the drilling equipment and the pilot rod are installed. It is fixed at the point where the drill head enters the ground.
An important step is to secure the tools with anchors to avoid displacement during HDD.
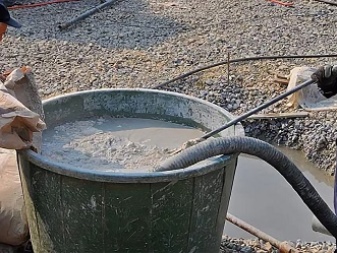
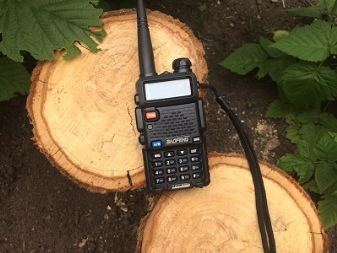
Upon completion of the preparatory stage, you can proceed directly to drilling. First, a pilot well is formed with a cross section of 10 cm. Then the equipment is re-debugged and the tilt of the drill head is adjusted - it should have an angle of inclination of 10-20 degrees relative to the horizon line. A pilot well is a training perforation, without the formation of which trenchless drilling is unacceptable. At this time, the functioning and serviceability of the systems is checked, and the features of the drill movement are assessed.
At the stage of formation of a pilot hole, it is necessary to adjust the tool for the angle of inclination of the soil, and also check the position of the drill head in relation to the landscape line. Just in case, bends are formed in the pits. They will be useful if underground waters or bentonite liquids are found in large volumes. The latter will prevent the collapse of the trench and the braking of the drill due to the adhesion of soil to it, overheating of the equipment.
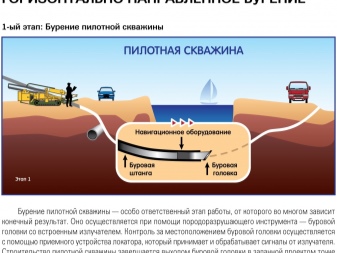
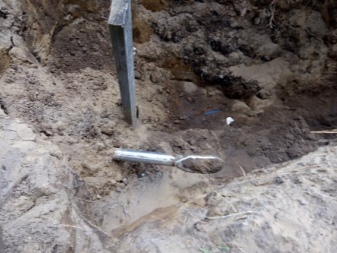
When preparing, it is important to make accurate calculations so as not to damage the previously laid pipe lines. The minimum distance from the pipes must be 10 meters. Then the process of the drill passing a given trajectory begins, and every 3 meters it is necessary to control and correct the direction of the tool. When the drill reaches the required depth, it begins to move horizontally or at a slight slope - this is how a trench of the required length is laid. After the drill has passed the required length, it is directed upward to the exit. Naturally, the point of the second pit is calculated in advance, and at this point the site is preliminarily prepared.
The final step is to remove the original tool from the ground and expand the hole with a reamer or rimmer. It is installed instead of the drill and allows you to increase the diameter of the pilot channel. During the movement of the expander, control and, if necessary, correction of the trajectory of the tool movement every 3 meters are provided.
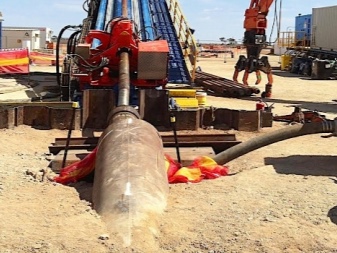
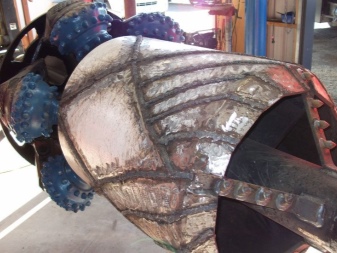
Rimmer moves along a trajectory opposite to the direction of the drill, that is, from the second puncture to the first. Depending on the required diameter of the trench, the reamer can pass through it several times. The diameter of the channel depends on the diameter of the pipes - on average, it should be 25% wider than the diameter of the pipes being laid. If we are talking about heat-insulating pipes, then the width of the channel diameter should be 50% larger than the diameter of the pipes.
If a large soil pressure is obtained in the channel and there is an increased likelihood of its crumbling, then a uniform distribution of bentonite is produced. After it hardens, not only the risk of crumbling, but also soil subsidence is excluded. For easier entry and passage of the tool through the soil, a special softening drilling fluid is used. With the HDD method, great attention is paid to the risk of soil shedding. In this regard, the strength of the pipe connection is additionally monitored so that they do not break under the weight of the crumbling soil.
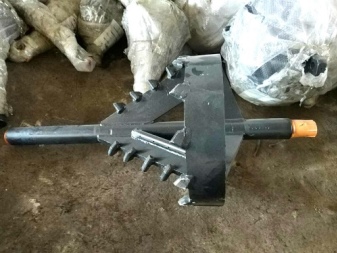
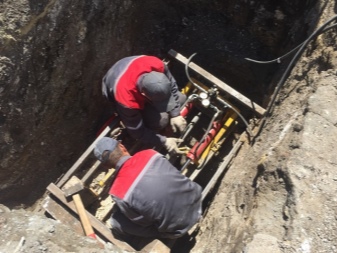
After the horizontal trench is ready, they begin to install pipes in it. To do this, brackets and swivels are attached to it, with the help of which it will be possible to tighten the pipe into the channel. A head is attached to the beginning of the pipe, for which the swivel will already be fixed. Pipes are also joined through the swivel, while the drilling equipment itself is turned off. For joining, they resort to using special adapters.
For small-sized wells and pulling small diameter plastic pipes, the force of the drilling machine is used. After laying the pipe in a horizontal trench, the HDD process is considered complete.
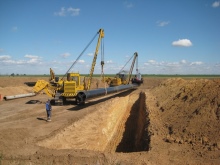
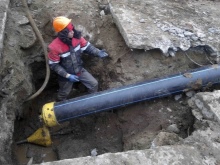
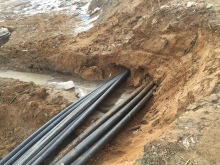
Scope of application
HDN is suitable for laying protective pipes inside which telephone, fiber-optic and power cables pass; for the installation of a pipeline inside which storm and sewage water, as well as drinking water, move. Finally, water pipes and oil and gas pipelines can also be laid using the HDN method.
The technique is also used in those cases when it is necessary to reduce the budget for repairs or reduce the number of workers. The decrease in financial costs is due to the absence of the need to restore the landscape after drilling, as well as the maximum automation of the process. Optimization of the size of the work team becomes possible due to the fact that workers are actually needed only to operate the machine.
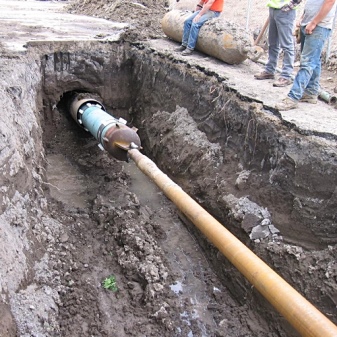
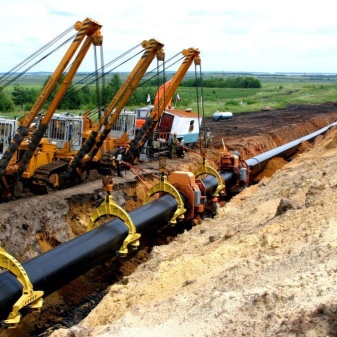
The technique is effective when installing pipelines in sandy, loamy and clay soils. The use of the described technology is justified if the trench runs under highways, in historically valuable areas or under water. In the latter case, the entry puncture is made through the river mouth.
Trenchless drilling is effective not only in dense urban areas and historical centers, but also in a private house, since it allows you to preserve plantings and buildings. As a rule, water supply and sewerage systems are laid at private property in this way.
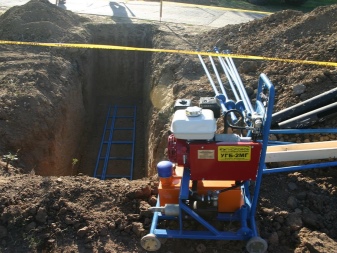
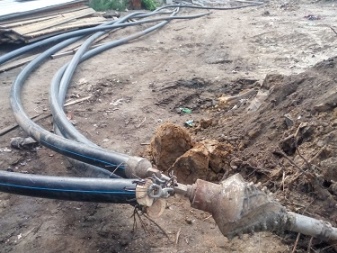
See the next video for how horizontal directional drilling works.
The comment was sent successfully.