Features of machine tool supports
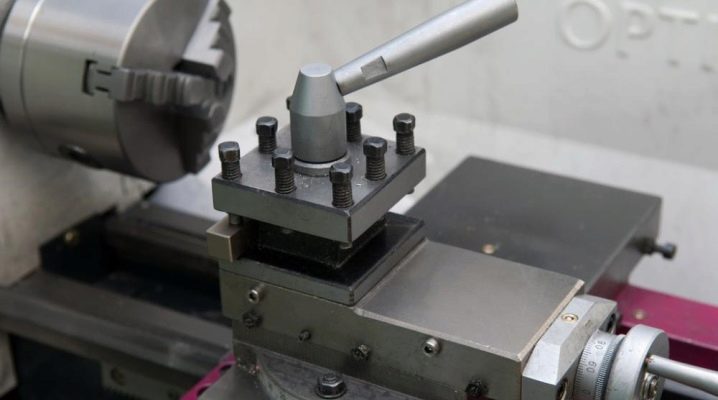
A lathe is equipment in demand in modern industry, one of the important elements of which is a support. It is worth considering in more detail what is the peculiarity of the node and how to use it correctly.
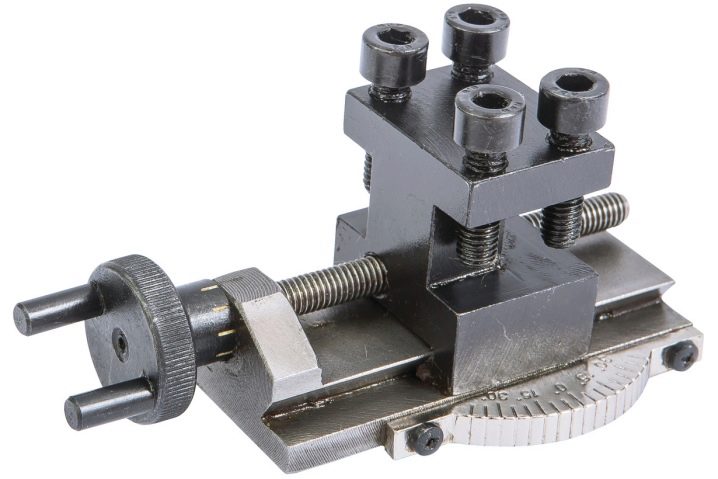
What it is?
A support on a lathe for wood or metal is a complex unit that is used to organize the effective movement of a tool holder with a cutter provided on it. With the help of the support, it is possible to move the element both in the longitudinal and in the transverse, oblique directions. Also, the mechanism is able to impart movement to the cutter along or across the bed.
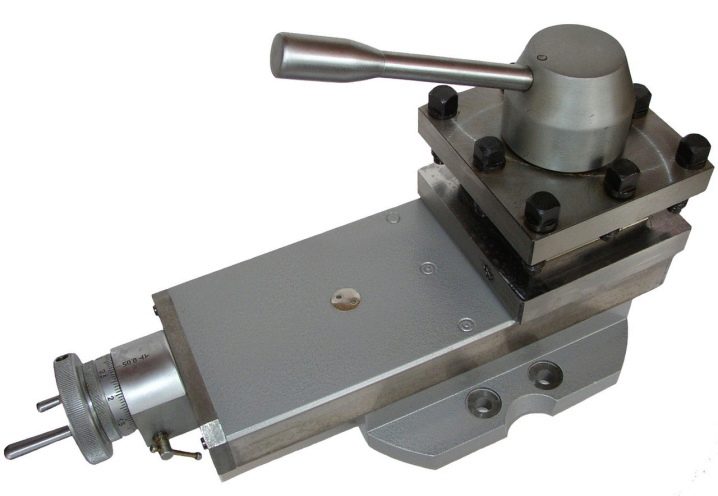
Standard caliper design includes:
- lower skids included in the longitudinal support;
- cross slide of the transverse mechanism;
- pivot plate of the upper support.
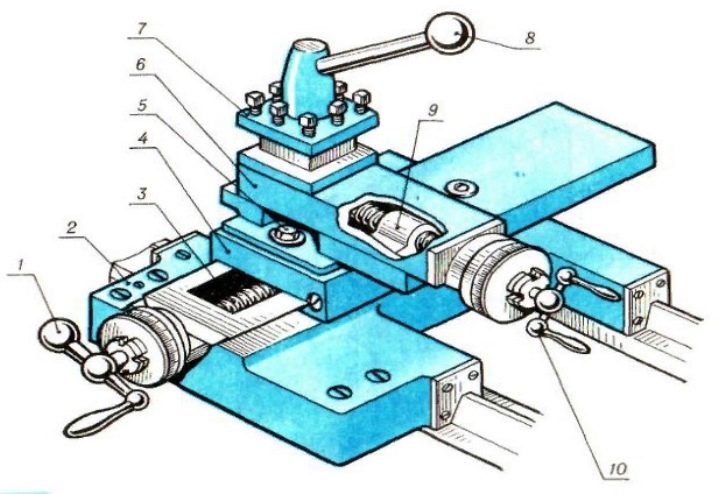
The principle of operation of the unit is based on the precise movement of the tool fixed on it for cutting or processing material. And now let's talk in more detail about each element of the complex mechanism, which serves to simplify the operation of the machine.
- Longitudinal. It represents the lower skids, the design of which includes all the mechanisms of the unit in the form of a drive, switching devices, an apron. Management - manual or mechanical. The lower slide is responsible for moving the caliper along the bed guides.
- Transverse. Purpose - transfer of direction to the plate, which is fixed on them, and also set the possible movement of the pivot support.
- Upper support. Looks like a carriage fitted with a slide. The elements are firmly connected to the guides of the rotary plate, therefore they move with it.
- Cutter head. Standard tool holder fixed to a horizontal platform. The mechanism is equipped with four working surfaces to which cutting tools or workpieces are attached.
- Apron - the basis of the structure, which is responsible for the direction of the components. It consists of bodies that regulate the start and stop of mechanisms, as well as transmit information about the amount of feed.
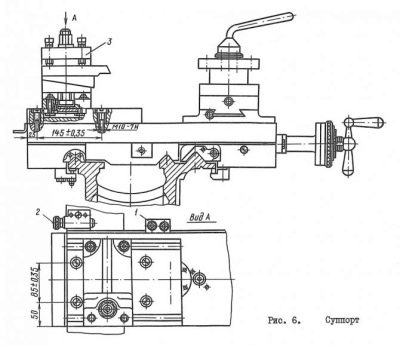
As for the possible directions of movement of the caliper, there are three of them.
- Transverse. When viewed relative to the axis of rotation of the workpiece, it is carried out perpendicularly. This method of moving the cutters is used if it is required to form a groove in the workpiece.
- Longitudinal. The support with the tool moves along the part. This solution ensures high quality cutting of the top layer of the material. Also, the thread is pierced by longitudinal movement.
- Oblique. Required to expand the capabilities of machine tools, as it allows you to organize cutting at an angle to the plane of the workpiece.
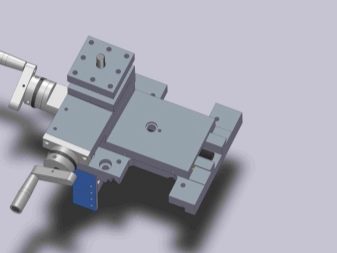
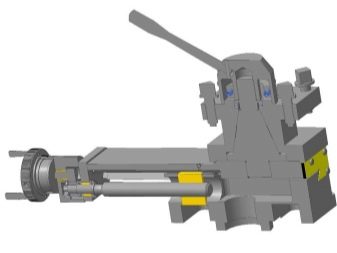
The support is an indispensable component of any machine, through which it is possible to achieve fast and high-quality cutting.
Species overview
Manufacturers produce different types of calipers for equipping lathes and CNC machines. All nodes can be divided into:
- mechanical;
- manual;
- automated.
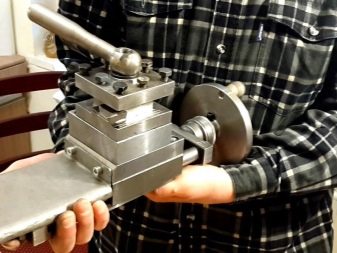
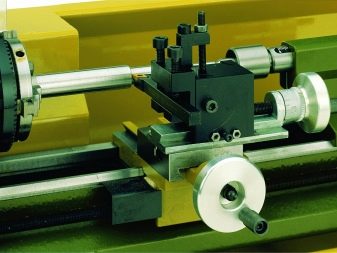
Each has its own pros and cons. The manual ones are suitable for equipping home installations that do not require much effort to operate. Mechanical and automated calipers are an option for industrial applications.
If the nodes are divided according to the principle of using torque, then they are grouped separately:
- threading calipers that rotate from the lead screw;
- specimens for feeding a cutting tool, driven by a propeller shaft;
- samples for thread formation - movement due to the lead screw;
- supports for facing, chamfering, where the manual drive is included in the work.
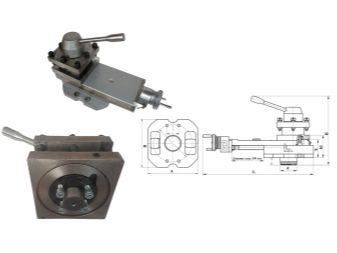
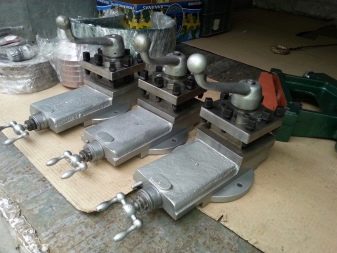
The back and front are an important part of any machine, so the purchase of such units is a must.
Adjustments
During operation, the caliper, like any other unit, wears out. Elements after several tens of operations require position correction and readjustment for correct continuation of work. Let's list the possible settings.
- Clearance adjustment. Over time, a gap appears between the slide, which should not be. An unwanted opening will impair the performance of the equipment and may interfere with the movement of parts. To correct the problem, you will need to return the guides to the desired position and eliminate the gap. To do this, you will need to use wedges.
- Backlash adjustment. The deviation is eliminated by adjusting the position of the fixing nut, which fixes the elements of the assembly in the required position.
- Adjustment of oil seals. Long-term operation of the equipment leads to rapid wear and clogging of the oil seals. You can track the need for repair or replacement of components by the appearance of dirty stripes that remain in place of the shifted bed. Adjustment in this case implies a thorough cleaning of the components and the use of oil as an impregnation.
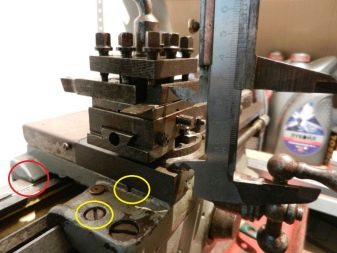
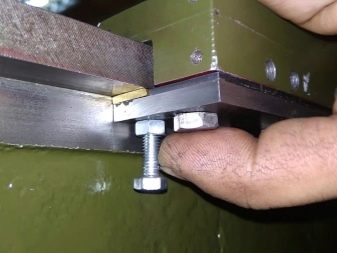
Timely maintenance of the caliper will prevent unwanted component failure and help save money on repairs or equipment replacement.
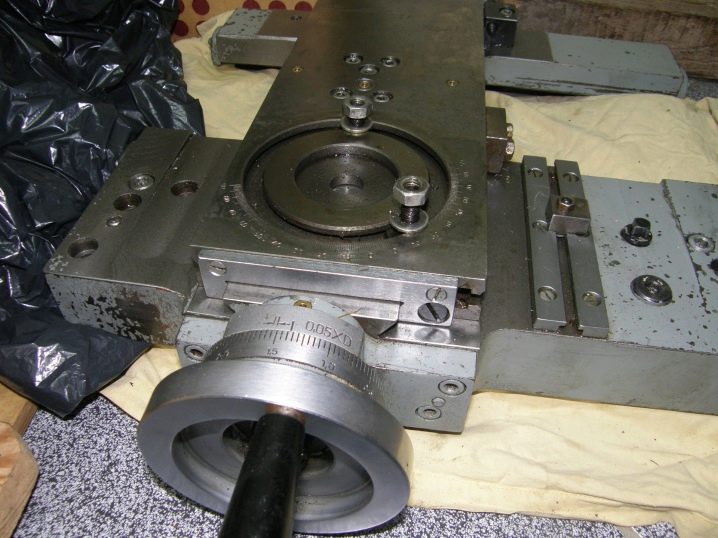
The comment was sent successfully.