All about threading machines
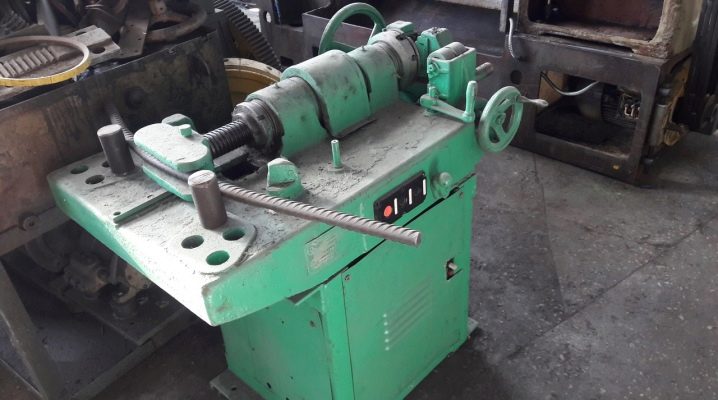
On different types of round metal products, you can find cylindrical and metric threads. In addition, when installing pipelines for various purposes, threaded connections are used, the quality of which directly affects the tightness of the entire system. Given the importance and characteristics of thread formation, it is important to know everything about specialized threading machines. Now in the corresponding market segment there is a fairly wide range of such modern equipment.
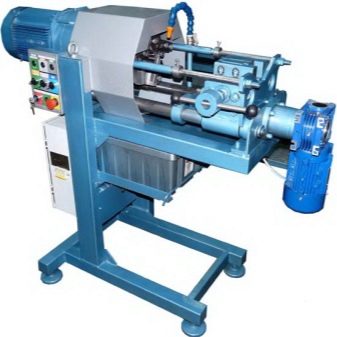
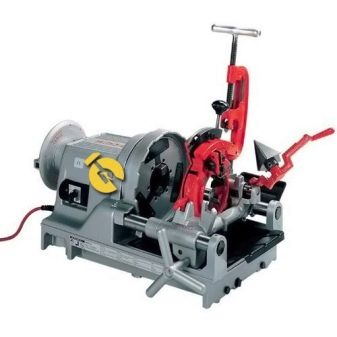
general description
Initially, it should be noted that one of the main features of threading machines is their high productivity. A wide range of devices with manual, semi-automatic and fully automatic control are now available on the market.
It is important that the machines belonging to the last two categories are relatively compact in size and at the same time ensure the maximum quality of work.
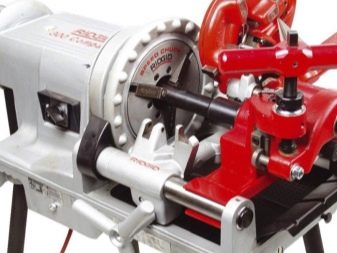
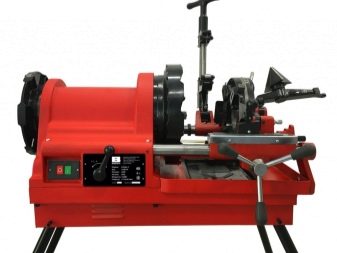
Depending on the nature of the operations being carried out, modern machines allow you to adjust the rotation speed, as well as the supply of working tools. The latter are taps and dies for cutting internal and external threads, respectively. Taking into account the step and configuration, the parameters of the movement of the spindle are set, in which they are fixed.
The machines on sale today can be with vertical and horizontal cutting elements. With their help, the following types of threads are created on machines:
- metric and inch on pipes;
- conical;
- trapezoidal;
- with a cylindrical profile.
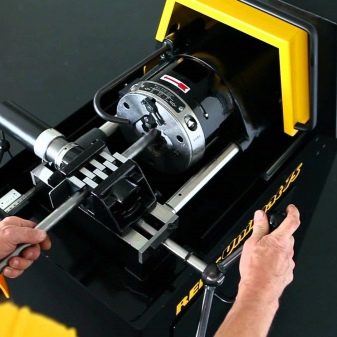
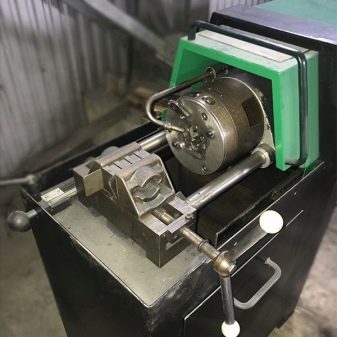
Due to the use of additional working elements, it is possible to vary the pitch of the formed thread, as well as its shape and inclination, in a wide range. For example, for the fastest, but at the same time, high-quality threading on a pipe, conical removable nozzles are used. It is important to remember that the performance of any machine directly depends on the following key indicators.
- The power of the device. This indicator is most relevant for equipment used in the continuous production of large batches of products. In such situations, the power of the machines reaches 2.2 kW, while 750-watt models will be enough for domestic purposes and small workshops.
- The frequency of rotation of the working part, which determines the speed of work. For modern models of threading machines, this value varies in the range of 28-250 rpm. It is worth noting that professional units have at least three high-speed operating modes. Naturally, for the needs of relatively small workshops, and even more so for the devices included in the arsenal of a home craftsman, a minimum indicator is sufficient.
- Sizes of workpieces that can be processed on the installation, as well as the length of the applied thread. For example, if we are talking about the manufacture of bolts, then the dimension in the ranges from 3 to 16 and from 8 to 24 mm will be relevant. Predictably, for machines used in production, these figures will differ significantly.
- The weight of the equipment, on which its mobility directly depends. The models currently on the market have a minimum weight of 50 kg. Such devices are quite easy to carry.
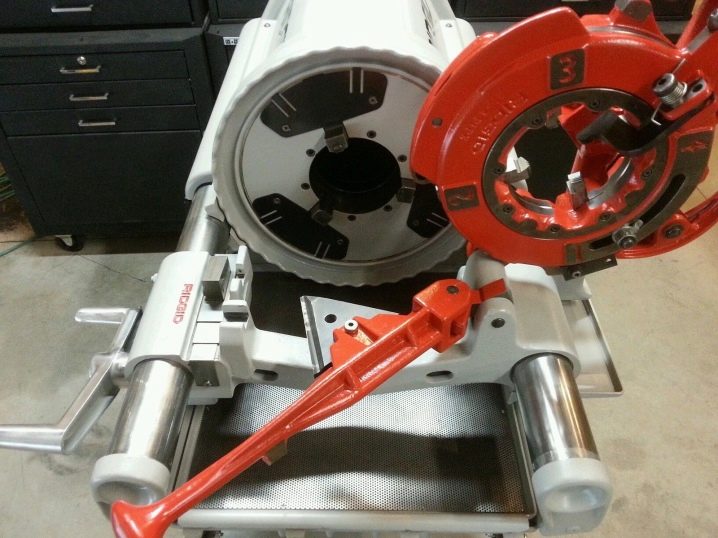
Analyzing the performance of the described equipment, it is necessary to highlight the following most important points.
- Ease of operation, maintenance and repair of machines.
- The ability to customize the units with minimal time costs.
- No need for special training of operators.
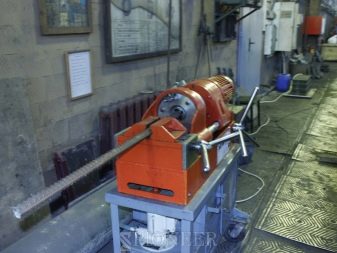
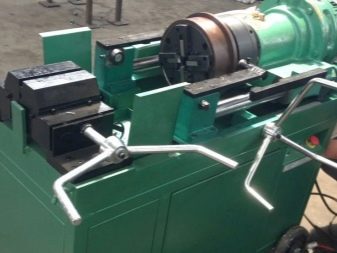
In addition to all of the above, it is worth focusing on the durability of modern threading machines. Leading industry manufacturers attach particular importance to this parameter, which is confirmed by relevant reviews.
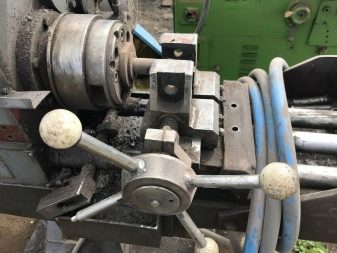
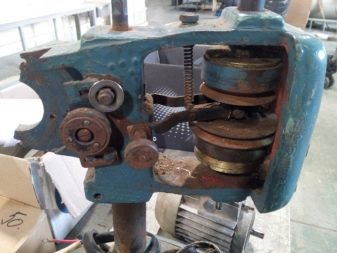
Species overview
It is possible to classify the existing threading machines by their type, as well as by the way of control. In the second case, two options are possible.
- Hand-held units, which are focused on household use and are designed to process workpieces with a diameter of 50 mm.
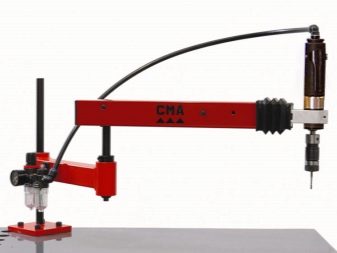
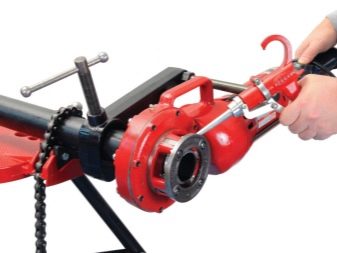
- Electrical equipment models used primarily by professionals. The list of their main distinguishing features can include a solid weight and corresponding dimensions, as well as a fairly high cost. Moreover, such machines are characterized by increased accuracy and productivity.
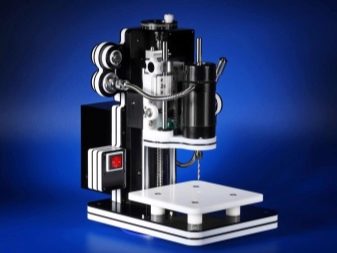
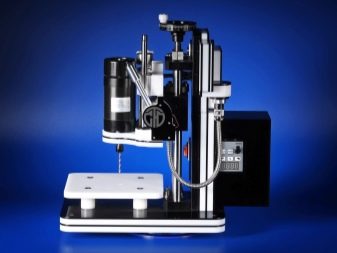
A separate category is represented by automatic devices that operate in accordance with a specific program.
In such cases, the operator only needs to fix the workpieces and enter the necessary parameters.
Regardless of the type, thread cutting machines are divided into desktop and floor-standing. The latter, in the overwhelming majority of cases, are large in size and weight. The main advantages of the desktop include portability and maximum ease of use.
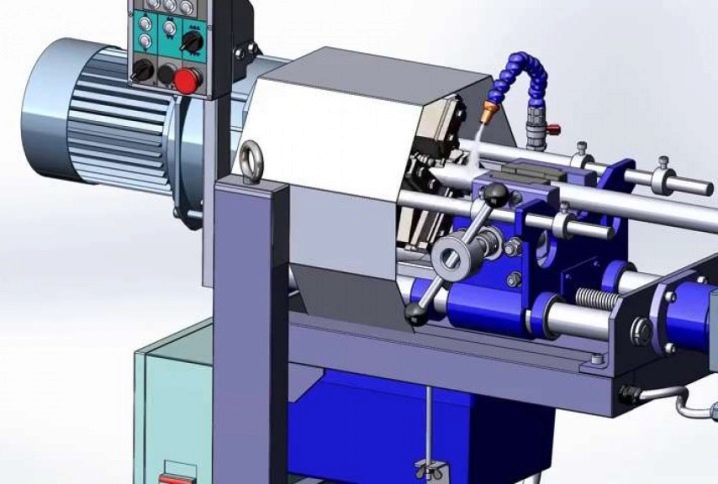
Thread rolling
In this case, the principle of the machine is based on plastic deformation of the material. It is important that no chips are removed. The exposed workpiece is passed (rolled) between the working elements of the unit, which have a round or flat shape. During processing, the surface is compressed, and the metal, at a certain pressure, begins to fill the cavities between the turns of the heads.
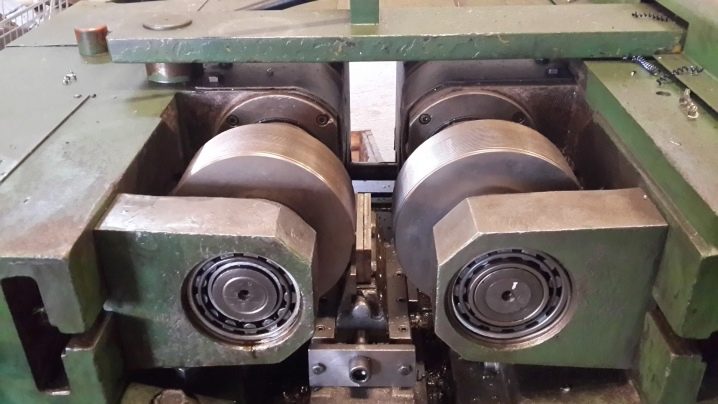
The working tools here are threaded segments, as well as rollers and dies. Thread rolling, as a rule, is carried out on models of units equipped with fully automated control systems or using semiautomatic devices. In some cases, lathes and revolving machines are successfully used. In a similar way, metric threads with a different profile are formed.
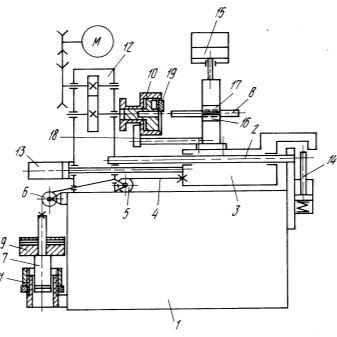
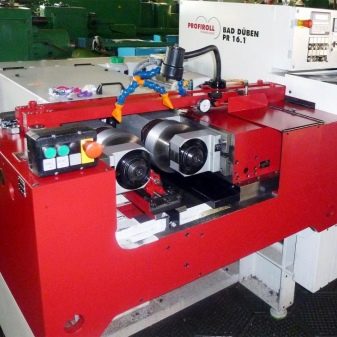
Thread milling
Machines belonging to this category are used in production areas. Such models are equipped with disc and comb cutters, and the principle of their operation is based on shaping advancement. During the operation of the machine, the workpiece slowly rotates, in parallel, the cutting working element is fed. As a result, it turns out to create threads with a sufficiently large pitch in long sections. The key to quality work is the consistency (strict synchronicity) of the submission.
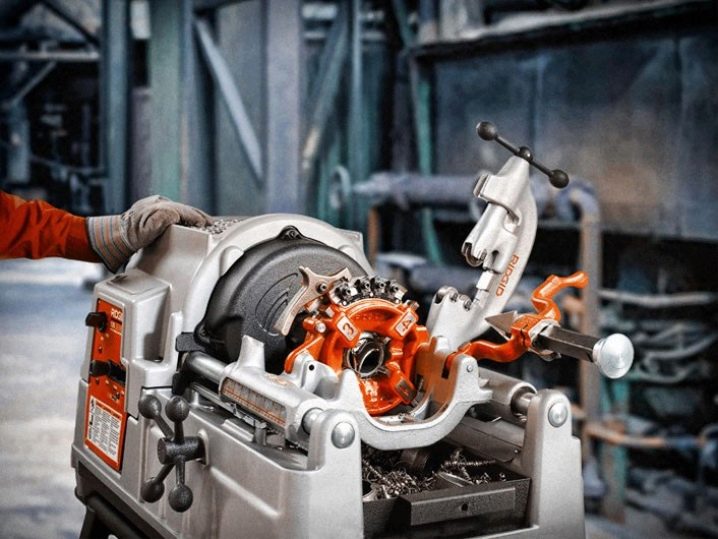
Comb cutters, which are a set of disc elements, are used to create fine threads along the entire length. Synchronous application of threads allows you to significantly speed up the work when you need to create both internal and external threads.
Thread Grinding
Grinding is the optimal solution when you need to make thread gauges, knurling rollers, hob bits and lead screws. In this case, single-strand and multi-strand abrasives are used. The production schemes in this case are largely identical to the milling discussed above. The difference is that the function of the cutters is performed by grinding wheels. In this case, single-thread and multi-thread are used as disc and comb cutters, respectively.
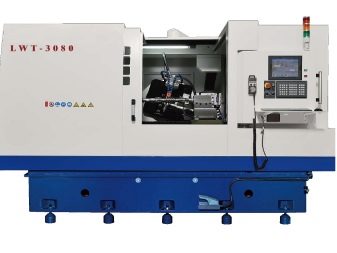
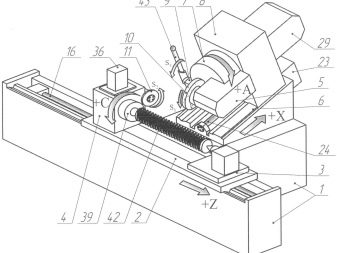
Abrasives with a profile corresponding to the configuration of the applied thread during the operation of the machine make circular movements.In this case, the workpiece to be processed is fed longitudinally with rotation, depending on the step. This technology provides the ability to form threads with maximum precision, as well as a wide range of parameters.
When working with multi-strand abrasives, the axes of the grinding wheel and the workpiece are parallel. Cutting in such situations is carried out with longitudinal feed and so-called plunge grinding. It is worth noting that when using the described cutting method, slight distortions of the formed thread profile are possible.
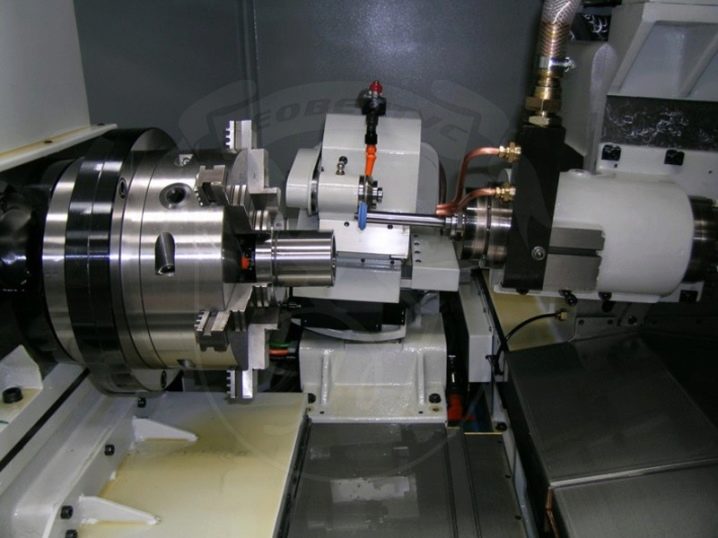
Popular models
Taking into account the demand for thread-cutting devices and the breadth of their applications on the market, many manufacturing companies present their model ranges. At the same time, their catalogs are constantly updated and replenished with new product images. Taking into account the numerous reviews and reviews, the following most popular models of such equipment can be distinguished.
- Turbo-400 2V - a unit capable of cutting threads on workpieces up to 2 inches in diameter. The model is equipped with a quick-opening head and is used in large industries, as well as in workshops with varying degrees of workload and services.
The machines have proven themselves well when broaching pipelines for various purposes.
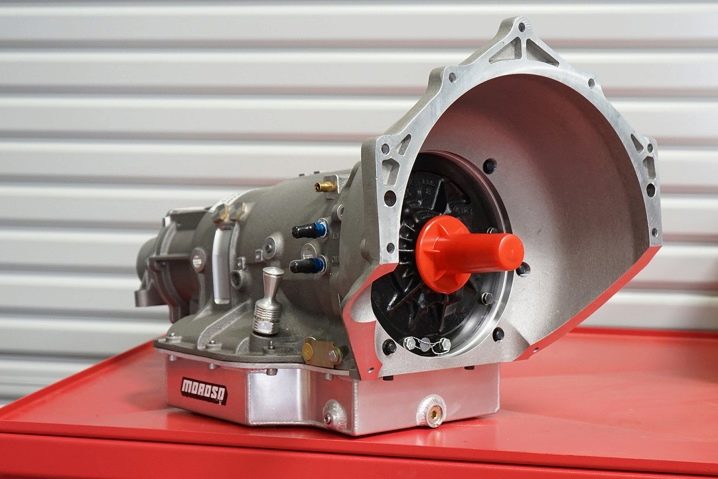
- Turbo-500 - a model, most of the technical and operational characteristics of which are identical to the previous one. The machine is also equipped with a quick opening cutting element and is characterized by increased productivity.
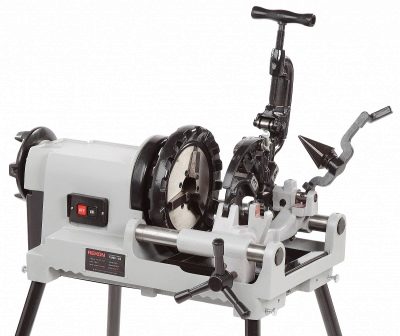
- Machine "Compact"designed for machining workpieces with diameters ranging from 1/8 to 2 inches and forming threads on 6-12 mm bolts. The unit received a 1700-watt power unit, which allows the spindle to reach speeds of up to 38 rpm. The weight of this machine is only 52 kg.
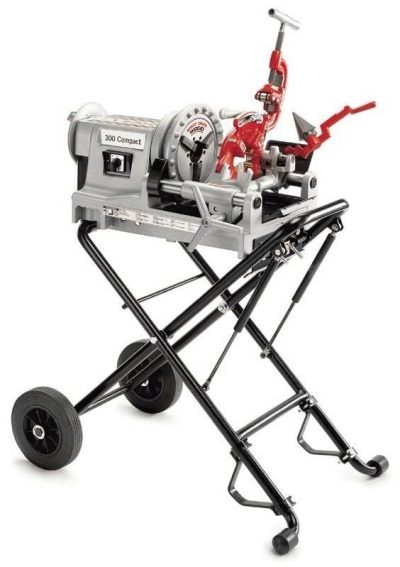
- RoPower R-50 - a device equipped with a universal working part for quickly creating high-quality threaded elements from 1⁄4 to 2 inches. It has found application both in industrial production and on large construction sites, as well as in small workshops.
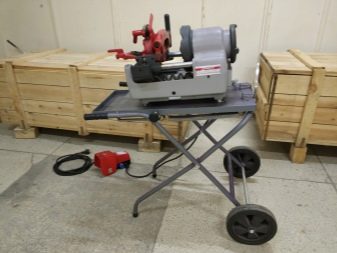
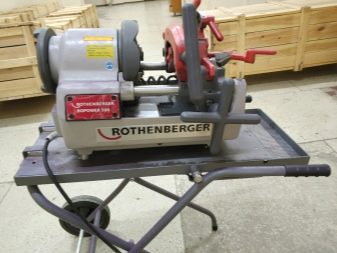
- Tornado and Magnum models of the REMS family - machines characterized by good performance and focused on the creation of threads on pipe rolling with a diameter of up to 2 inches and bolts of 8-60 mm. In addition, the equipment is used for cutting, grooving, deburring, and nipple production. The equipment is operated in the conditions of production shops, construction sites, assembly areas and workshops.
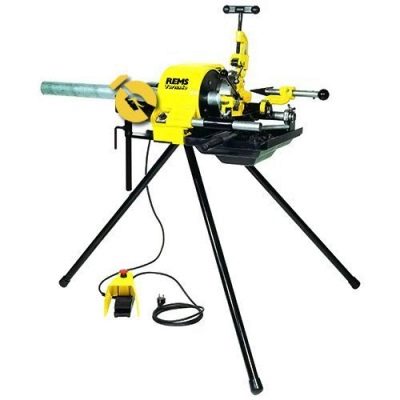
Selection options
When choosing a specific model of the equipment under consideration, it is necessary to focus on the whole list of technical and operational characteristics.
- The design features of the unit, the list of which includes dimensions, weight, level of protection of the cutting zone itself and all moving working elements, as well as their location. In the latter case, we are talking about the vertical and horizontal layout of the machines.
- Type of drive. For many years, the overwhelming majority of models were equipped with mechanical units, since they are characterized by compactness, ease of use and reliability. At the same time, it is worth considering that sometimes such units fail quickly enough.
- In situations with machine tools equipped with electric motors, it is important to focus on the type of network to which the equipment is connected, as well as on the availability of an overheating protection system. It is important to remember that power is not a measure of performance here.
- Clamping mechanism characteristics. This point is due to the corresponding loads arising in the process of performing the described work. Predictably, the accuracy of cutting will be directly determined by the reliability of fixing the workpieces.
- The presence of a system for supplying lubricant and coolant to the threading site. This point is most important in cases where workpieces made of carbide materials are processed.This process is associated with significant heating of the working tool and the product itself. Such an effect accelerates the wear of the former and negatively affects the quality of the latter.
- Process automation. Now the popularity of models equipped with modern digital control systems is growing steadily. They are capable of providing maximum precision with increased productivity. Moreover, most of the process does not require human intervention.
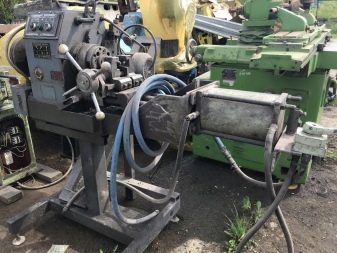
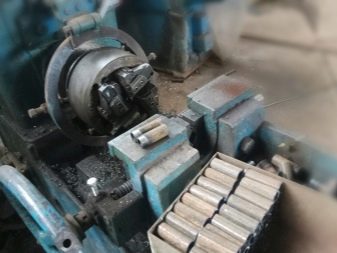
In addition to all of the above, the list of determining factors includes the brand of the machine.
It is recommended, whenever possible, to give preference to products from well-known manufacturers. The financial side of the issue, as well as the ratio of price and quality of equipment, will be no less important when choosing.
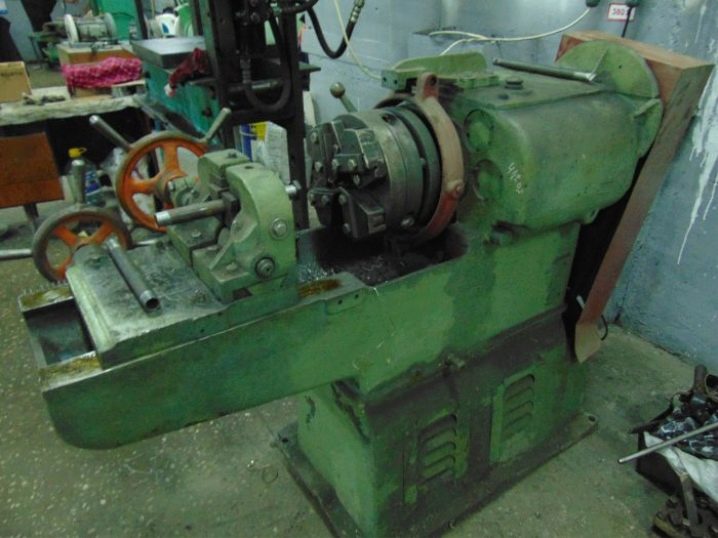
Areas of use
Taking into account the performance and functionality, threading machines are widely used today in many areas. This refers to industry, as well as large construction sites. At the same time, samples of equipment designed to solve everyday problems are on sale.
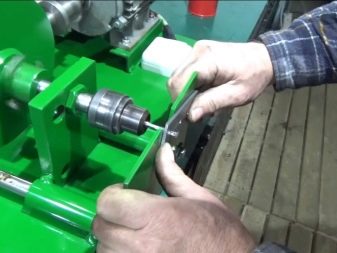
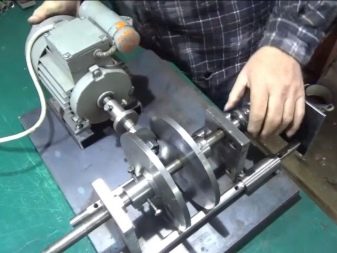
Modern models of the equipment under consideration make it possible to form inch and metric threads in holes, as well as to create tapered threads on reinforcement. Compact models will be indispensable if you need to roll threads on knitting needles, studs and a bar for nuts of a certain size.
In addition to performing work with pipes and rolled products, the machines are used for deburring and chamfering, both external and internal, as well as for deburring.
By the way, the described units allow you to work both with metal and with other materials. A striking example would be the formation of threads on cuttings for various tools.
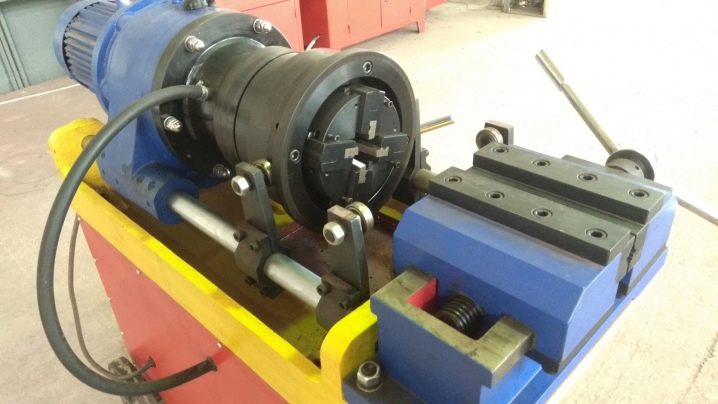
The comment was sent successfully.