Features of vacuum forming machines
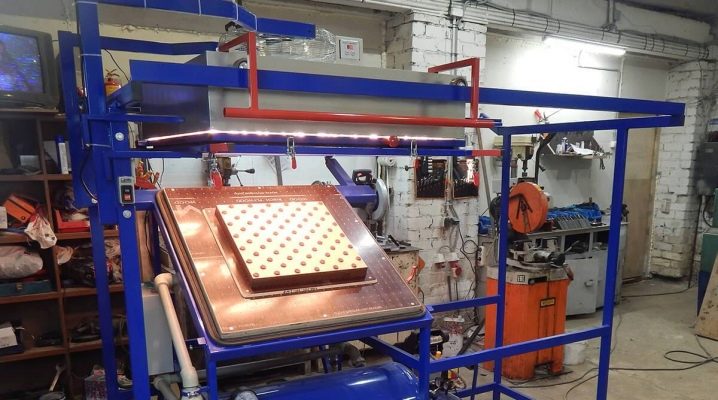
Vacuum forming is performed using special equipment (vacuum forming machine). It allows the manufacture of various polymer products of various shapes. Today we will talk about the features and principle of operation of such a technique.
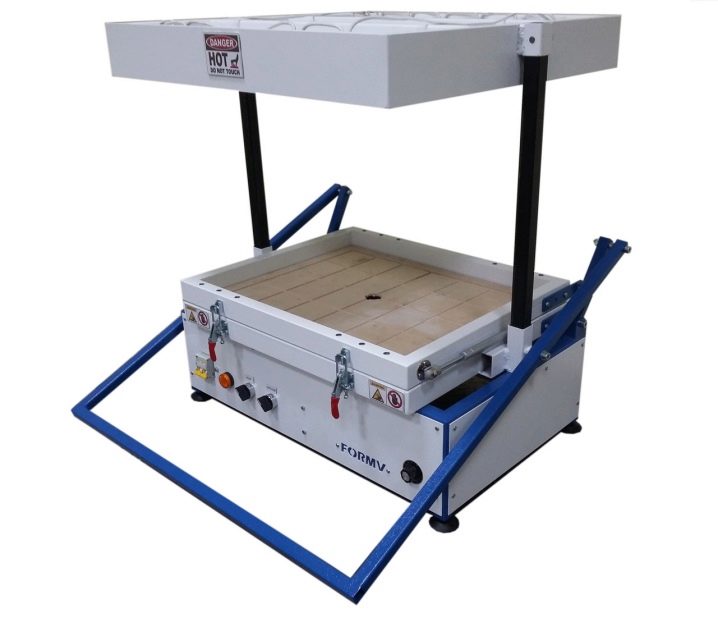
Device and principle of operation
Vacuum forming machines include special heating elements. They are the most important part of the design. These parts provide heating of the material to the specified temperature. In this case, the equipment must also maintain a temperature regime.
Various elements can be used as heaters. The most commonly used ceramic, quartz infrared heater, halogen lamp, KGT lamp.
It also includes a ventilation unit. It is designed to ensure uniform heating of the material. He is also responsible for cooling.
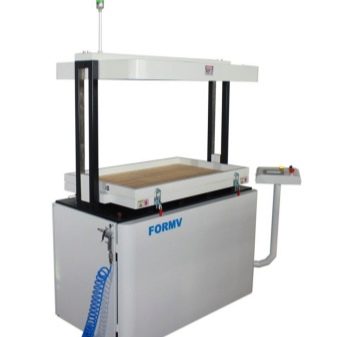
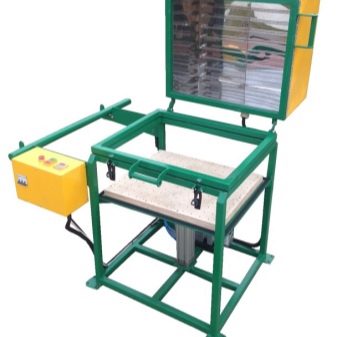
A vacuum pump is used to reduce the pressure between the workpiece and the mold. The clamping frame of the structure ensures the accuracy of the geometric dimensions of the product. The device also accommodates a large number of auxiliary small mechanisms, they are needed to control the supply of material.
The units can be produced with additional equipment: time indicator, sensor and system for adjusting the cost of cooling, a mechanism that protects the material from sagging, a system for switching from automatic to semi-automatic mode.
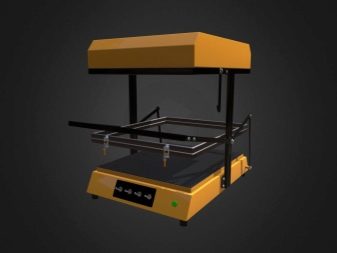
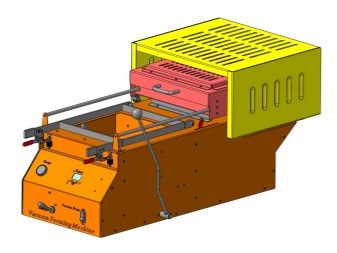
The mold is produced according to the following algorithm. The matrix is fixed on the equipment table. Next, a sheet of plastic is taken, it heats up. The heated plastic blanks are placed on the die, after which a vacuum is created.
The hot material begins to follow the contours of the die. After cooling, the molds made are obtained as an exact copy of the original product.
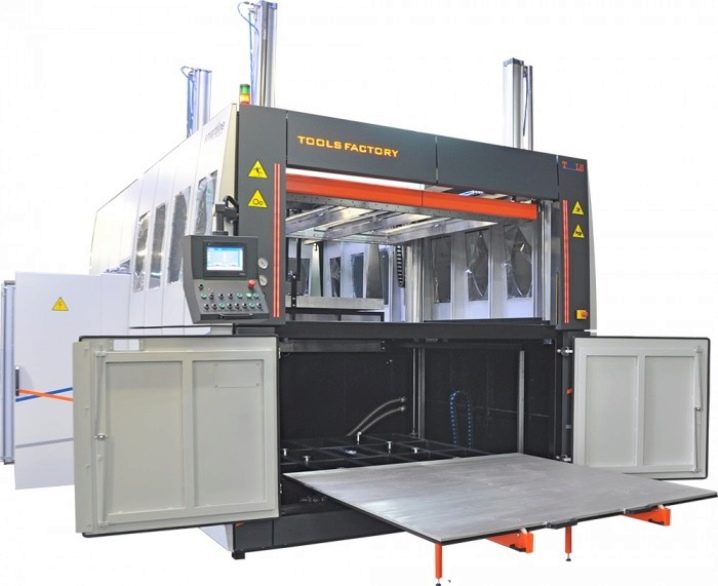
What are they?
Vacuum forming machines can be of various types.
-
Automatic. These models are fully automated. They independently feed the workpieces.
-
Semi-automatic. In such instances, the supply of blanks and the collection of the resulting products is done manually.
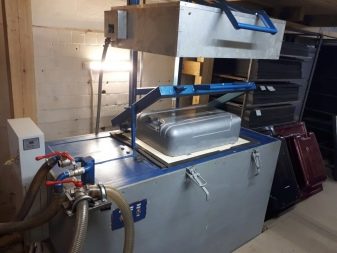
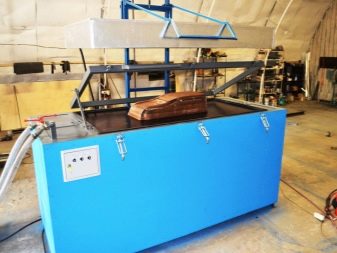
In addition, depending on the size of the manufactured parts, the following types of such units are distinguished: large-sized, medium-sized and small-sized. For home workshops, you can pick up mini-machines. Most often, such equipment is used for plastics, but there are also devices for ceramics.
Selection Tips
Before purchasing a vacuum forming machine, you should pay attention to a number of important nuances. Before purchasing, be sure to test the system to ensure that the main parts are in good working order.
And also look at the condition of the equipment case. There should be no damage on its surface. There should not be large gaps between the departments.
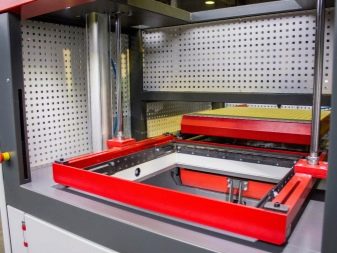
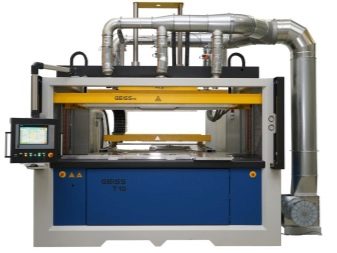
If you plan to purchase devices that have already been used in production, you need to find out in what conditions the equipment was previously operated. You should not buy units that have been used on a continuous basis under significant loads.
The dimensions of the desktop are important when choosing. After all, it is on this that the permissible sizes of plastic forms will depend.
In addition, the size of this part will also affect the total cost of the machine, so it is better to immediately calculate the required performance of the equipment in order to choose the most suitable option.
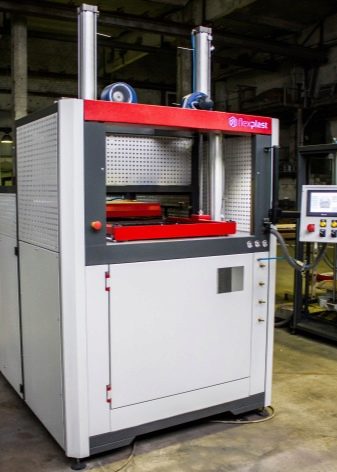
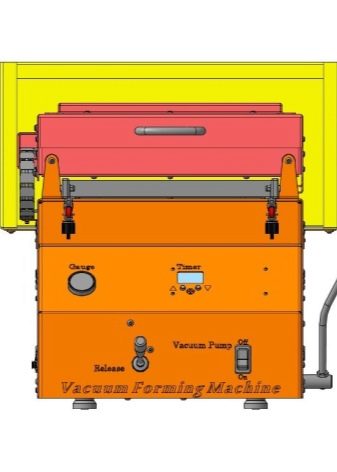
Applications
Vacuum forming devices can be used in various fields of production.
-
Advertising and souvenir products. Using this technique, you can make showcases, fountain pens, various souvenirs and gifts.
-
Plastic box. Vacuum forming machines allow you to make quality packaging for food, cell phones, light bulbs, stationery and more. Special blister packaging is gaining more and more popularity. It is a transparent film that easily takes the shape of the packaged items. Buyers will be able to evaluate the goods in such a film even before purchasing.
-
Volumetric letters. They are most often used in the design of restaurants, cafes, salons and various shops. They can be complemented by bright lights and decorative elements.
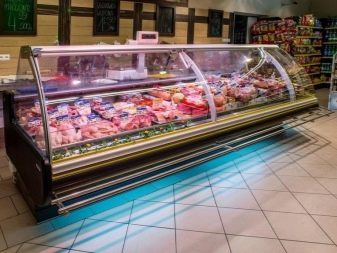
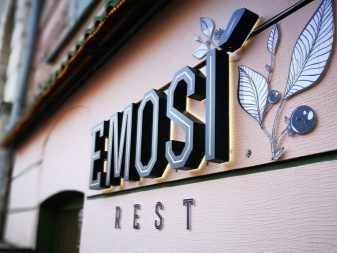
In addition, this equipment can be used in the production of cell phones, cameras, shoes and more. It is widely used in the furniture industry, printing industry.
How to do it yourself?
Now we will figure out how to make a simple homemade vacuum forming machine. First, you need to make a drawing of the future unit with all dimensional values. And also you should immediately prepare all the necessary tools and materials:
-
frames made of wood;
-
slats;
-
vacuum cleaner hose;
-
drill;
-
nuts and bolts;
-
Fiberboard sheets;
-
glue for carpentry work;
-
miter saw;
-
grinder;
-
sealing tape.
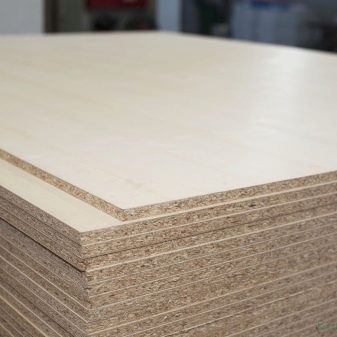
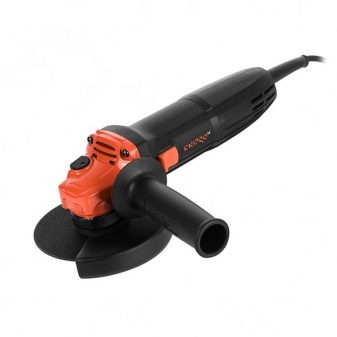
When everything you need is ready, you can get to work. First, you will need to cut a square-shaped panel out of fiberboard, it will later become a table of the structure. The wood strip should be carefully divided into four parts.
The boundaries of fixation of the vacuum chamber are marked on the panel, four parts of the cut strip are glued to them. After that, a hole is formed in the central part of the workpiece using a drill, its diameter should correspond to the diameter of the hose from the vacuum cleaner.
Further, all the cracks are well coated with a sealant. At the same time, the frame is covered with carpentry glue. All this is done in order to avoid the appearance of air gaps. A perforated panel with holes of the same size is fixed on top of a wooden lath with glue. It will be needed to allow air to pass through.
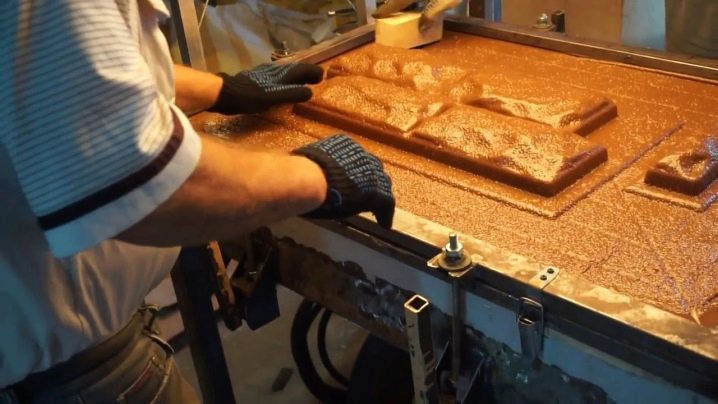
Then, two square-shaped blanks are carefully cut out of fiberboard sheets. In this case, frames are obtained for fixing plastic polymers. They overlap. In this form, everything is fixed around the perimeter with hardware.
A hose from a vacuum cleaner is inserted into the square panel. You can also use PVC tubing instead. All this is glued, the seams are necessarily sealed. If desired, it will be possible to install special stands for lifting the vacuum chamber.
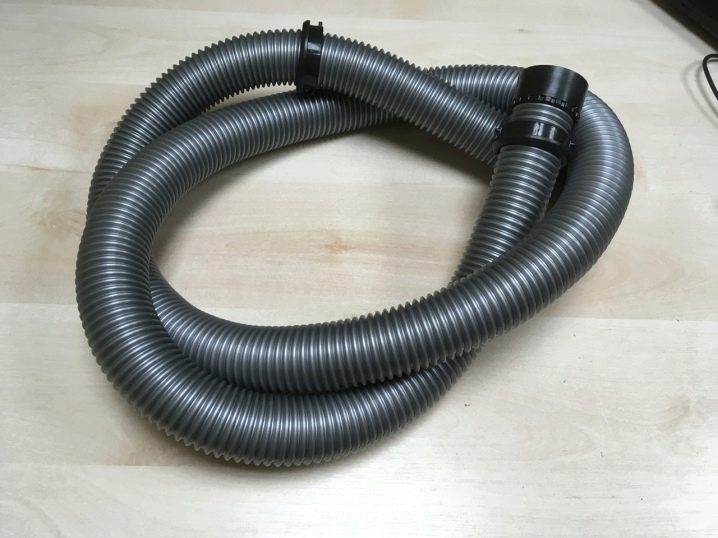
An airtight seal is glued along the rack frame. This will minimize the air throughput of the structure. After that, a sheet of plastic is clamped between two frames, it must be fixed in position with nuts and bolts, they must be tightened until they stop.
Next, the model of the required shape, from which the copy will be made, is installed on a perforated panel. In this form, everything is transferred as close to the oven as possible. A vacuum cleaner is connected to the hose. The frame with the fixed plastic sheet is sent to the oven to heat the material to the required temperature. This usually takes a few minutes.

When the material begins to gradually sag, you will need to turn on the vacuum cleaner and quickly remove the mold with the sheet from the oven. The material is applied to the model. At the same time, the vacuum chamber will immediately connect the original form and the polymer base. You need to wait about 30-40 seconds, after this time the vacuum cleaner is turned off.The plastic product is ready. Making such a device at home does not take much time.
How to make a vacuum forming machine with your own hands, see the video.
The comment was sent successfully.