Overview of planers for metal and their selection
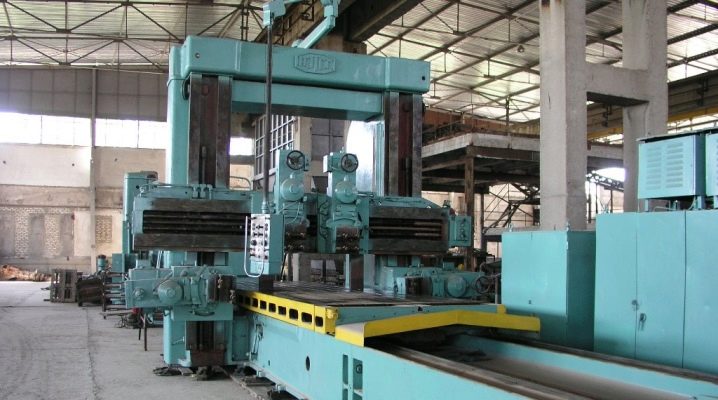
Planing is a special process that involves cutting off layers of metal from flat surfaces of various parts and template blanks. Planing is in demand in the industry and is used along with milling and grinding. To carry out the work, special planing machines are used. It is worth considering in more detail their structure, features and types.
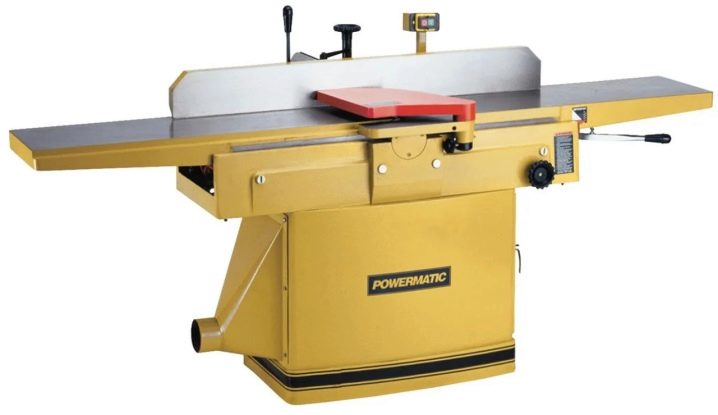
Device and purpose
High-quality cutting of the material is ensured due to the reliable functionality of the equipment used for planing. The planer is a robust structure, which includes the following components:
-
Control block;
-
bed;
-
support equipped with tool holders;
-
steel frame in the form of a portal or console;
-
the mechanism responsible for moving the table;
-
working surface with grooves for fixing the product;
-
electric type motor;
-
a pumping station that ensures the timely supply of cooling lubricants;
-
horizontal and vertical cross members.
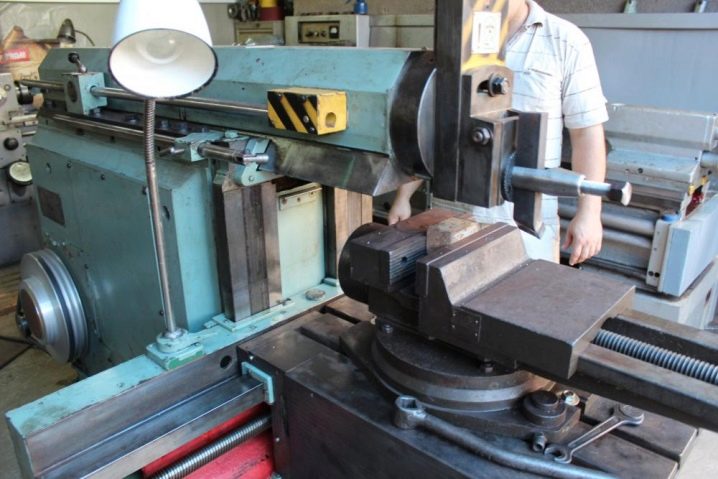
Each machine is labeled in accordance with the requirements of state standards. Marking is an alphanumeric designation through which it is possible to determine the machine group, the maximum size of the workpiece and other information.
The classic planer performs only one function - it removes a layer of material of a certain thickness from the workpiece being processed. The equipment is used to work with metal products, where high precision of work is required.
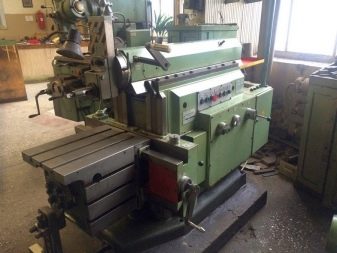
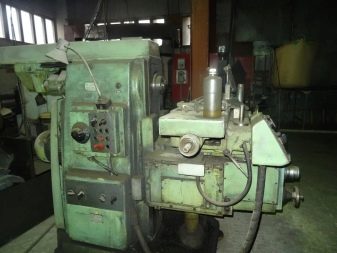
Planing machines are in demand in production and in private workshops of the installation, through which it is possible to improve the quality of the workpiece and achieve the desired result in a short time. Equipment pluses.
-
Versatility. The machines are capable of processing products from all types of metals.
-
Adjusting the cutting speed. The operator can adjust the optimal movement of the tool relative to the workpiece.
-
Large selection of cutting blades and other tools. With the help of additional equipment, it is possible to expand the functionality of the device.
-
Reliability. The design of the machine is characterized by increased strength and is able to cope with even the highest loads imposed by workpieces and tools.
-
The convenience of use. Plant control is straightforward.
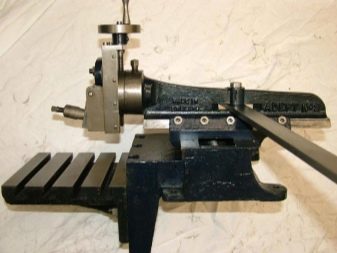
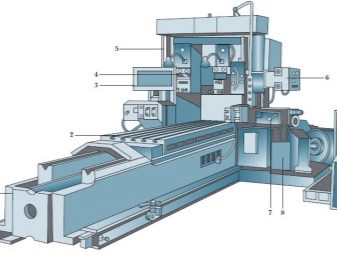
Among the disadvantages of metal planers are the noisy operation of the engine and the high level of vibrations that the tool gives out during cutting of the material.
Views
The key differences between the planing machine and other equipment - milling or turning units - are in the configuration of the workpiece planned for processing and the principle of the complex operation. The machine works mainly with flat products, where the cutter has the ability to process one or more sides of the part fixed on the work table.
Manufacturers produce a wide range of planers. According to the manufacturing technology, all models can be divided into two main types.
-
Longitudinal planing. Additionally, they are divided into designs with one or two posts. They are used for processing large workpieces, which makes it possible to install the complex at an industrial enterprise.
-
Cross planing. The peculiarity of the models is in the movable cutting part. At the same time, the workpiece is securely fixed in one position. Suitable for machining large parts.The advantage of the device is in increasing the cutting speed and wide functionality.
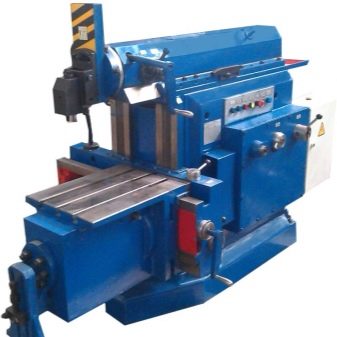
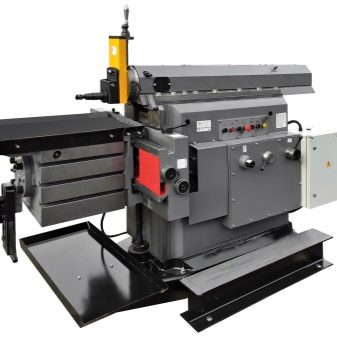
Special-purpose machines should be singled out as a separate category. The difference lies in the design of the complexes and the effect on the workpiece. Here are the main views.
-
Slotting with manual control. Used to form holes in metal workpieces. And also provide the ability to sample material for grooves, grooves, protrusions. The working tool of the slotting machine is a chisel, a feature of which is the teeth that play the role of traditional cutters. Some models have a swivel head, which expands the functionality of the installation and makes it possible to work at an angle.
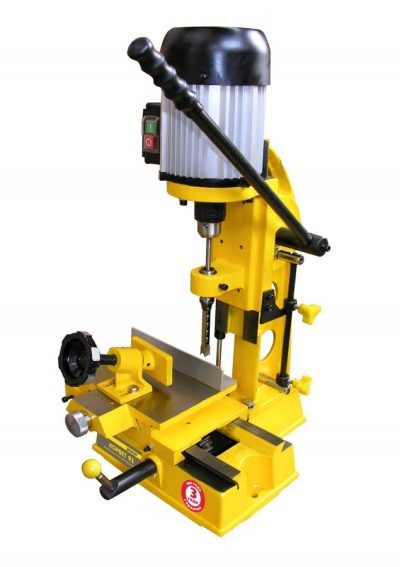
- Lingering. Additionally, they are divided into horizontal and vertical machines. They are mainly used for working with small workpieces where rapid chip removal is required.
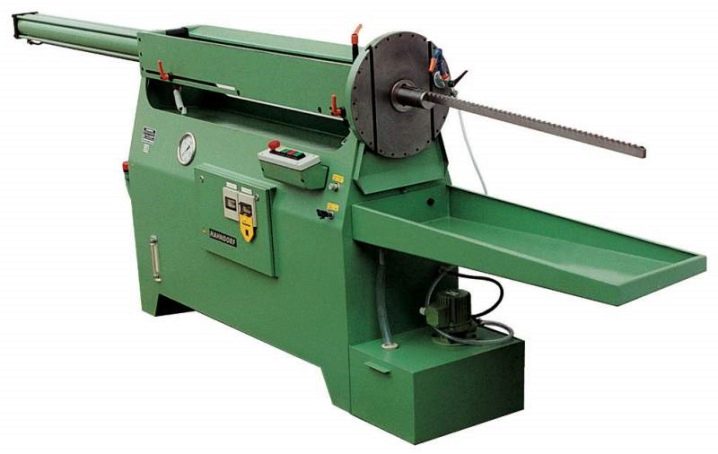
- Shaped planing. They are applicable in private workshops and in highly specialized enterprises, where attention is paid to cutting material from curved surfaces. And also the complexes do an excellent job of cutting metal on surfaces located in different planes.
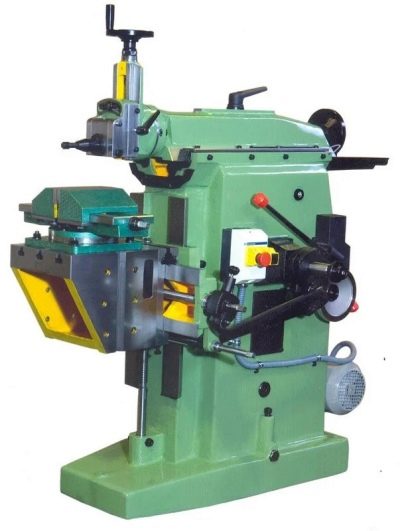
The speed and quality of the planer, regardless of the model, are influenced by the speed of the cutting surface, the smoothness of the components and the frequency of the blades. Correctly selected cutters in the required quantity will also help improve productivity.
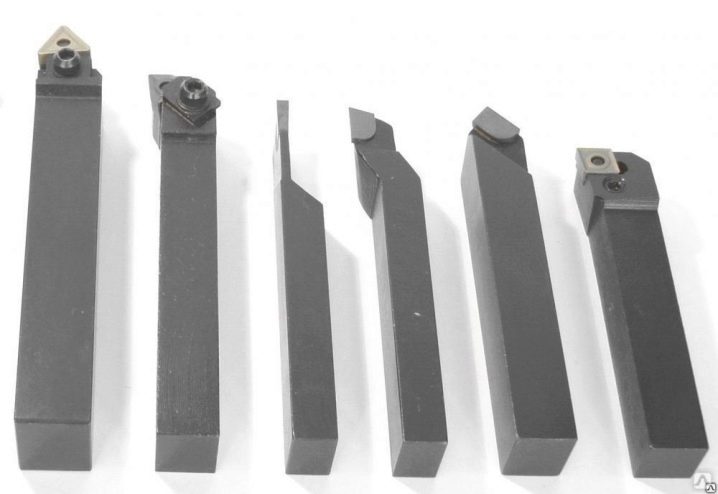
Rigging
Cutting off material is impossible without sharp steel cutters, which are equipped with equipment. Before proceeding with the processing of the workpiece, it is necessary to carefully approach the choice of equipment. Masters advise to consider when buying incisors:
-
sizes;
-
application area;
-
strength characteristics;
-
sharpness.
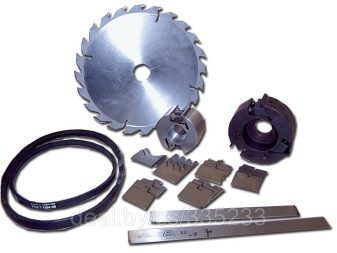
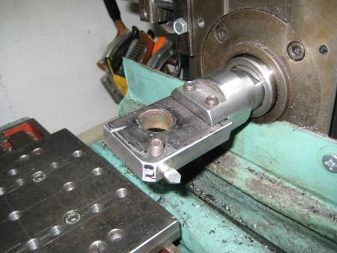
The main advantage of planers is ease of use. It is possible to install a new cutter without experience and special knowledge about the installation design. During work, it is worth taking care of the correct use of the cutters in order to extend the service life of the components.
For this, it is recommended to give preference to machines with a tilting fixing head, which will return the cutter to its place at the end of the process.
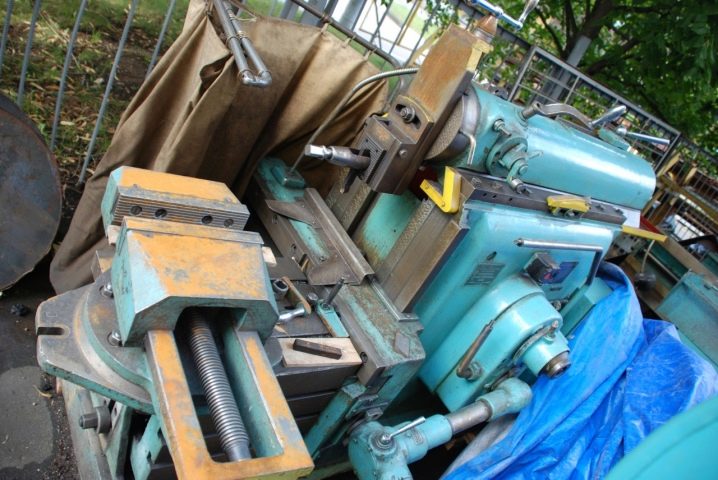
Nuances of choice
Buying a planer for metal requires a responsible approach. The choice of an installation that is not suitable for the requirements will lead to the impossibility of carrying out work or rapid wear of the components. When buying a machine, it is worth considering:
-
working surface area;
-
the power of the engine used;
-
the maximum speed of movement of the cutters;
-
available options for cutting material;
-
configuration and dimensions of equipment;
-
specifications;
-
the degree of protection of structures from moisture, dust and other influences;
-
the maximum workpiece weight that the machine can handle.
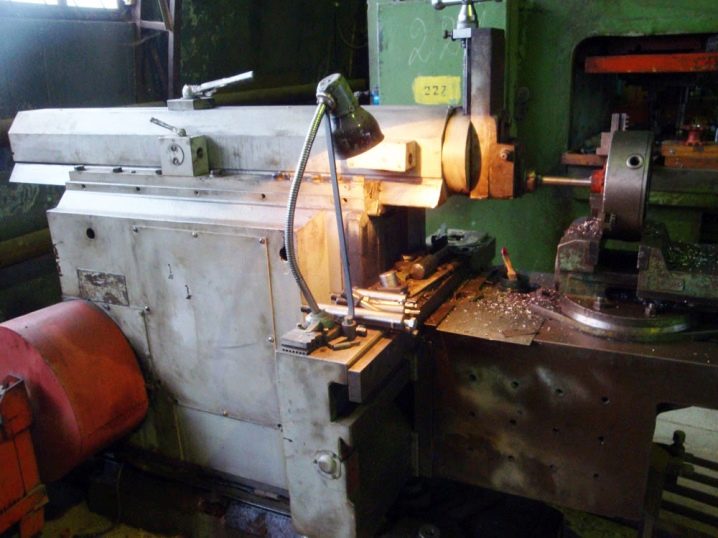
Additionally, you should pay attention to the manufacturer, the warranty period and the functionality of the equipment.
The comment was sent successfully.