Locksmith chisels: purpose and tips for choosing
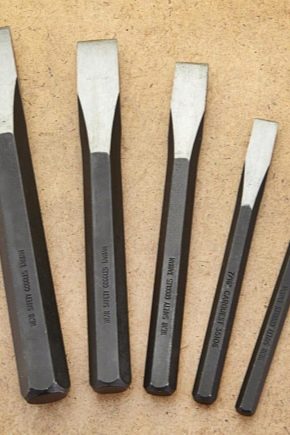
Some jobs require a special tool designed for mechanical impact with destructive force. Such a device is a chisel. He will be discussed in the article.
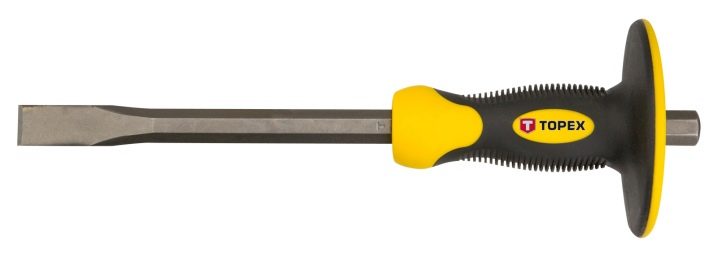
What it is?
Locksmith's chisel is an impact-cutting device for processing metal or stone. It is made of tool carbon steel. The tip of the tool is in the shape of a blade.
The tool is multifunctional, but it is mainly used for:
- breaking stones;
- metal felling;
- knocking down tiles;
- "Cutting" nail / rivet heads and similar fasteners;
- unscrewing / tightening bolts and nuts with "lapped" edges.
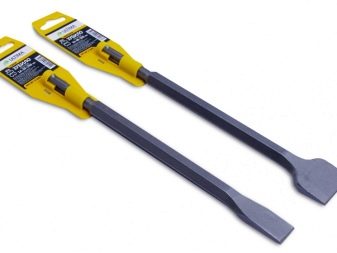
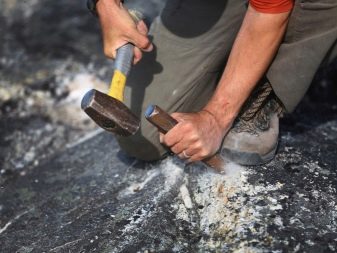
Device
The diagram shows the device of a carpenter's chisel: 1 - head, 2 - rod, 3 - blade.
In general, a chisel is a straight bar, in the section of which a rectangular, round, oval or multifaceted shape can be traced. It is sharpened on one side (working blade). The other end is intended for hammer blows. To ensure the safety of the master during work, a protective "mushroom" can be installed on the chisel. It is a hollow handle with a bead made of rubber, wood or plastic. However, it should be borne in mind that only construction options of the tool are usually equipped with a protective mushroom. On the same chisels, he, as a rule, is absent.
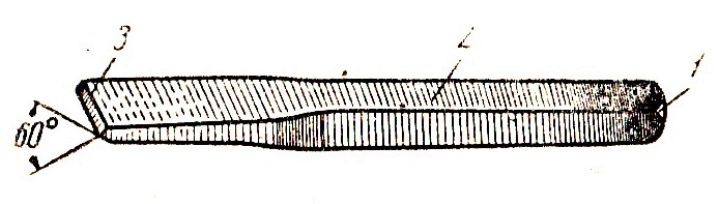
The working blade has double-sided sharpening with primary and secondary cutting angles. To increase the life of the cutting blade, it is slightly dulled. The shank and the working blade of the chisel are subject to heat hardening without fail.
Types and characteristics
There are about 20 different types of the tool in question. Let's list the most famous of them.
- Chisel - used for work with unhardened metal.
- Pike chisel - used with pneumatic devices (jack and chipper hammers).
- Chisel cross - equipped with a tapered cutting edge. Used to punch grooves or grooves in metal.
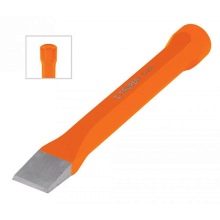
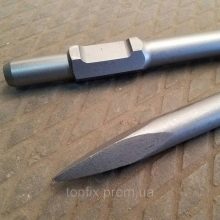
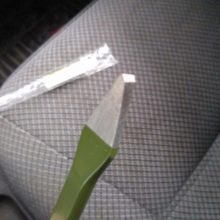
- Grooving chisel - a subspecies of a cross cutter with a shaped cutting edge.
- Blacksmith chisel - mounted on a long wooden handle (like a hammer). This allows the hand holding the device to be removed from the hot metal. The use of cold metal for cutting is not excluded.
- Scarpel chisel - a sharper device in comparison with the conventional model, used for working with stones. The working blade of this option is similar to a blade. It helps to smooth the stone, mainly used by sculptors. The tool is equipped with a rubber mushroom, which protects the master not only from blows to the hands, but also from the scattering of fragments.
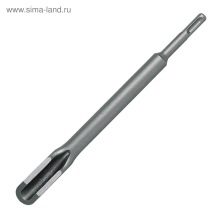
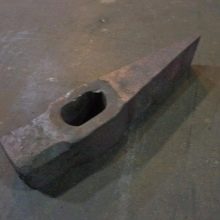
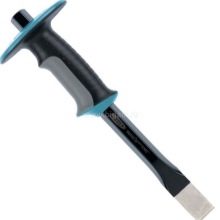
The main characteristics of the tool include the type of fixture, its purpose (for processing soft, medium hard and hard metals). The type of striking part (tapered or straight) is also taken into account. Chisels are manufactured in several variations of component parts (according to the requirements of GOST 7211-86). Allocate tools with a handle:
- flat oval section;
- oval section;
- hexagonal section;
- I-section.
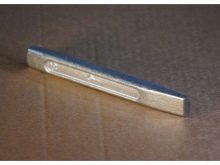
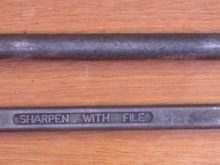
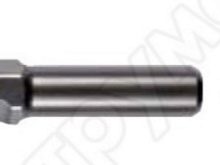
By the type of striking part, there are options that have:
- conical working and striking part in width;
- straight working striking part in width.
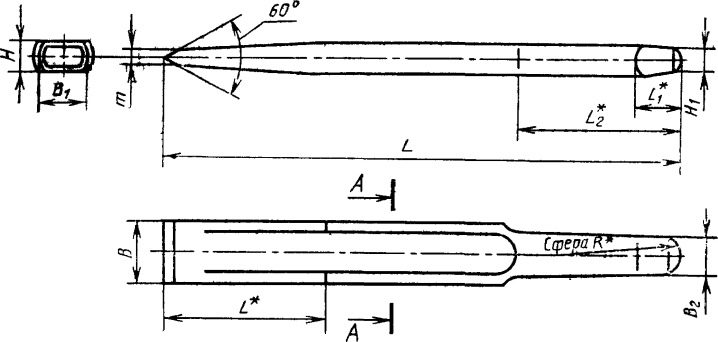
If the device is intended for cutting metals, when creating it, carbon steel of grades U7, U8, U9, U7A, U8A, etc. is used.If the tool is created for working rocks, they take structural options for steel 45, 50, 50X, which can be additionally equipped with carbide inserts, for example, from Pobedit.
The chisel with victorious brazing is suitable for working with concrete, metal, various breeds. Such a chisel will last longer than a device without soldering. It will also last longer without sharpening.
According to the technical requirements of GOST, the hardness of the chisels must correspond to certain parameters. For a working surface at a length of at least half from the cutting edge for steel grades 7ХФ, 8ХФ this figure is 56-60 HRC. For U7A, 8HF, a value of 54-58 HRC is provided. For the striking part at a length of at least one and a half times from the striking end for 7HF, 8HF, the established norm is 41-46.5 HRC. As for U7A, 8HF, here the indicators are in the range of 36.5-41.5 HRC.
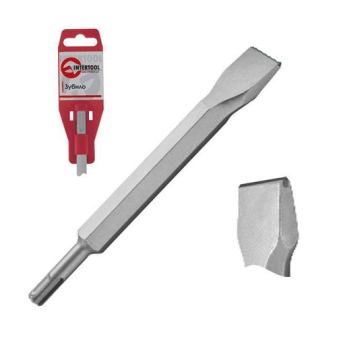
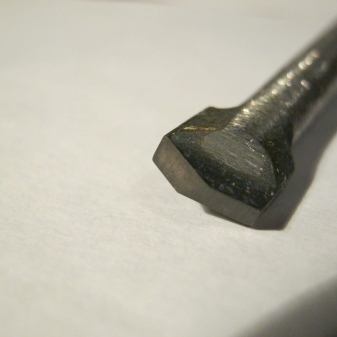
Other grades of steel can be used to create products. The main thing is that the mechanical properties of the material in the processed state are no worse than those of the varieties described above.
Chisels must have a protective and decorative coating. According to GOST 9.306 and 9.032, this can be:
- oxide with oil, phosphate with oil or chrome with a thickness of 9 microns;
- chromium 1 micron thick with a nickel sublayer applied by cathodic reduction with a thickness of 12 microns;
- galvanized with a thickness of 15 microns with chromating and phosphate, followed by painting the surfaces of the chisel with nitroglyphthalic enamel NTs132 of various colors according to class II;
- cadmium 21 microns thick with chromating;
- chrome 1 micron with a nickel sublayer 14 or 7 microns thick.
Chisel sizes vary. The length varies from 100 to 200 mm, including options with indicators of 125, 160 mm. The width of the working part can be 5-20 mm. In terms of weight, lighter versions can weigh between 210 and 380 g. Heavy ones (used with power tools) can weigh between 590 and 750 g.
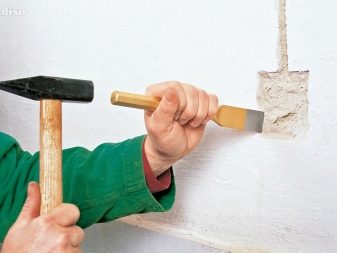
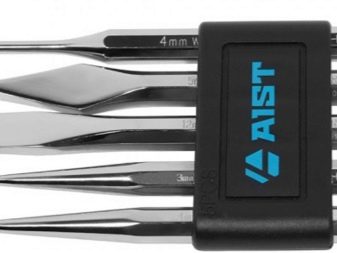
Sharpening angles can also vary. For soft metals, products with a sharper angle (about 35 degrees) are used. For hard metals, a larger angle is required (45-70 degrees).
Selection Tips
Before you buy a chisel, it is worth first of all to determine for what kind of work it will be used: construction or locksmith. The main difference between the tools is the presence or absence of the security element, which was mentioned at the beginning of the article. Due to this, the dimensions are reduced, and the working area of the tool increases.
It is also worth paying attention to the steel grade from which the chisel is made. The list of recommended material types is given above. The highest quality chisels have good toughness. This reduces the risk of blade particles chipping off during operation, making the tool safer. Chisels made from mild steel or with unhardened blades quickly deteriorate.
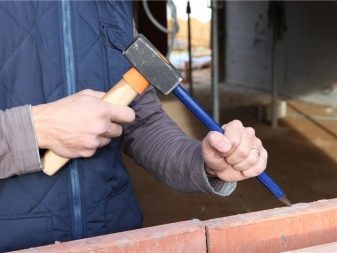
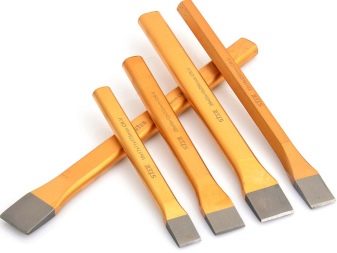
You should not choose cheap models from little-known manufacturers, they may turn out to be of poor quality. Give preference to trusted brands.
How to use?
- Before you start working with a chisel, you need to make sure that its working surface is intact. To do this, it is enough to inspect the edge of the blade for cracks, chips and similar defects. If you find them, it is not recommended to work with the tool in order to avoid injury.
- Be sure to use glasses and gloves when working. It is possible to supplement the device with a protective rubber pad, which will increase the level of safety of the master. Remember that the tool must be dry, otherwise it may slip out of the hand (this applies to both the hammer and the chisel itself). When working, it is necessary to carefully monitor that there are no strangers nearby.
- Don't forget to mark up the material. A thin but bulky sheet of metal can be cut on an anvil. The chisel should be kept upright. If the workpiece is small, but has a large thickness, it is better to clamp it in a vice. The sponges should line up with the markings.If the thickness of the metal is significant, then the marking line should be located 4 mm above them. The hammer strikes short and clear at the back of the chisel at the right angle.
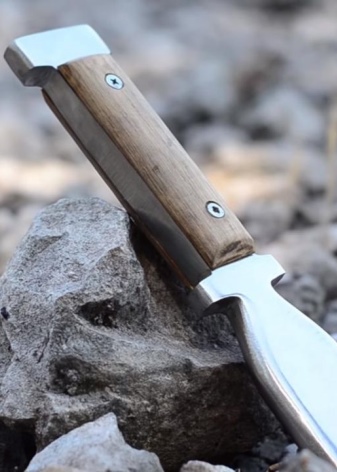
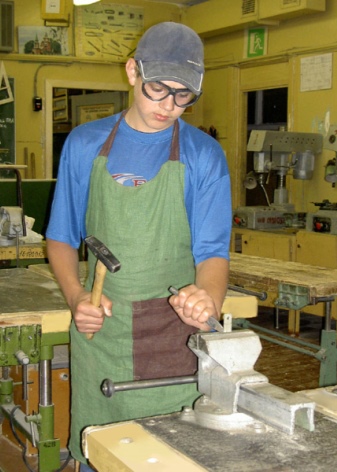
- When working with metal sheets, take into account their type and thickness (thick sheets should be cut in several passes). If you need to chop off a piece of wire with a chisel, do not try to do it in one blow, because the cut off part can fly off in a random direction, which will cause you to waste time looking for it. Better to make one light blow (cut) of a small size and break off the piece you need, which in the end will remain in your hands.
- Do not forget that the weight of the hammer must be at least several times greater than the weight of the chisel. Otherwise, the work will become a real problem: the hammer will slide off the surface of the striking part of the chisel, and the productivity will be close to zero. The condition of the hammer is also important, in particular, the reliability of its attachment to the handle. If the striking part of the tool jumps out of the holder during operation, there is a risk of injury.
- Remember that the chisel must have the correct sharpening angle. The harder the metal to work with, the larger the angle will be. For cast iron, hard steel and bronze, a sharpening angle of 70 degrees is assumed. For materials of medium softness and mild steel (brass, zinc, copper) - 60 degrees. For aluminum, a tool with a 40 degree sharpening angle is required.
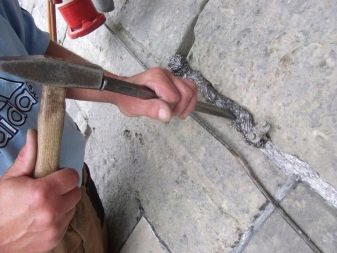
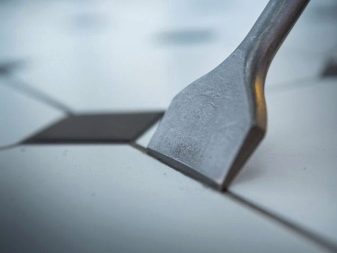
Sharpening features
To carry out self-sharpening, you need to prepare a small tank with clean water, into which you will periodically place the heated tool (in order to avoid softening its initial hardening). Sharpening is carried out on the end of the emery wheel. The chisel blade should be against the direction of travel of the emery wheel (to ensure that sparks are deflected downward). Depending on the ambient temperature and the speed of rotation of the emery wheel / stone, the chisel should be cooled for 30 to 60 seconds.
If you overexpose the edge, it can overheat and lose its hardness. This will make it impossible to handle hard materials. When sharpening, change the contact side of the cutting blade, as the chisel has a two-way escapement. Periodic flipping makes it possible to maintain the correct geometry. Sharpening can also be carried out on an emery stone, but this will take more time (in this case, the process is carried out by moving forward).
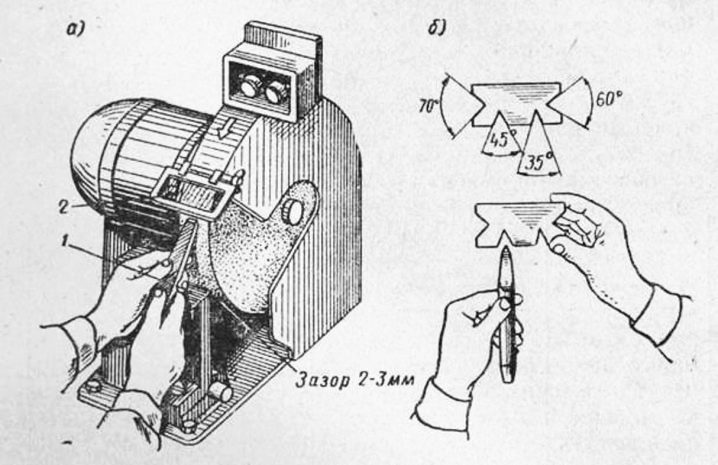
See below for more details.
The comment was sent successfully.