Foundation waterproofing membrane
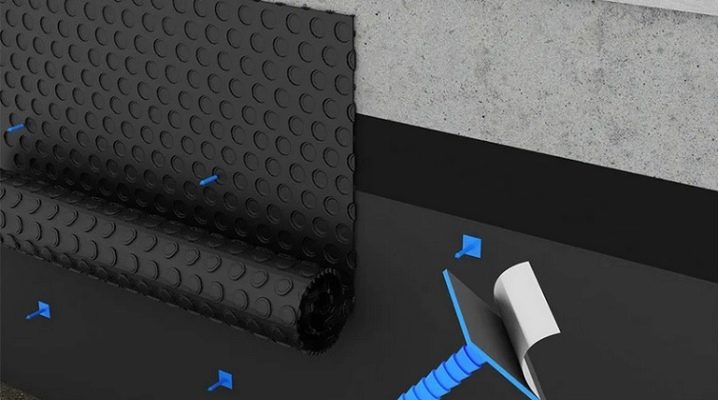
The foundation is the backbone of any construction project, so you need to take care of it first. There is a wide range of materials on the market today, one of which is a waterproofing membrane that performs a protective function.
We offer you more detailed information about this product, its technical and operational characteristics, as well as varieties.
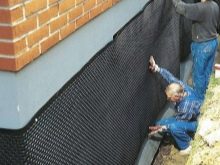
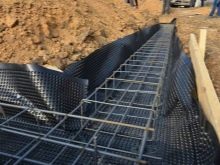
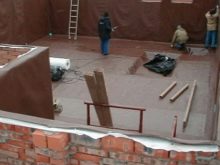
What is it and what is it used for?
The construction of the foundation of the house has voids that have a destructive effect on the structure, while reducing its thermal insulation. To prevent the humidity in the room from increasing, it is necessary to install high-quality waterproofing, which is laid under the foundation slab. There are many material options on the market, but one of the most popular is the membrane, which has a lot of positive characteristics. This material is a film that performs a protective function for concrete, in addition, it insulates the foundation.
For the manufacture of polyethylene and polymers, as well as various minerals and antioxidants are used. This composition affects the structure of the material, which is characterized by elasticity and porosity. The quality of protection is at the highest level, it also improves resistance to mechanical damage, which is no less important. The membrane consists of layers of polyester and fiberglass, which are reinforced with polymers, respectively, the color of the upper layer is black, and the lower one is colored, which makes it possible to detect damage in time.
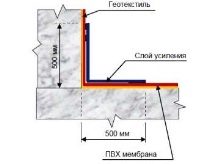
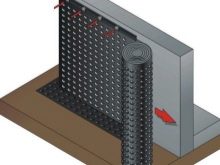
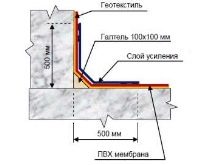
There are many areas of application of the profiled waterproofing membrane. It is installed under the slabs to protect the base from groundwater, especially when they run too high near the surface of the earth. If the soil is wet and the soil is heaving, you cannot do without such material. Also, the membrane is relevant in the construction of balconies and roofs, it protects artificial ponds, wells and pools. When arranging underground parking lots, tunnels or basements, the material is used everywhere.
It should be noted that constant humidity deteriorates the properties of building structures, whose load-bearing capacity is significantly reduced. And in order to extend the life of an object, it is necessary to install a membrane under the foundation at the initial stage. Elevator shafts, viaducts, bridge supports, flat and pitched roofs, walls and floors in rooms with high humidity (bathrooms, showers and saunas) are built exclusively with this material. This product is useful in places with sharp temperature changes.
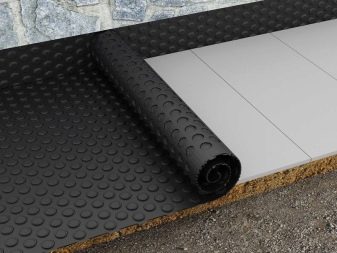
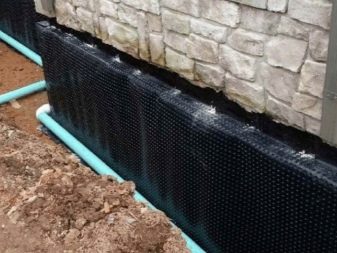
The main advantages include resistance to ultraviolet radiation, a long service life, which can be 50 years, resistance to high acidity and the influence of an aggressive environment, elasticity and water resistance. The membrane is not able to absorb much water, it can stretch and weighs a little. The material will protect the metal structure from corrosion, besides, it is environmentally friendly. You can handle the installation yourself if you follow the instructions, it does not take much time.
As for the shortcomings, the only drawback is the high cost, but due to the performance characteristics, such an investment will be fully justified.
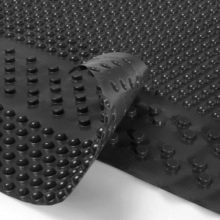
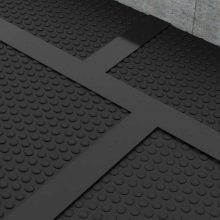
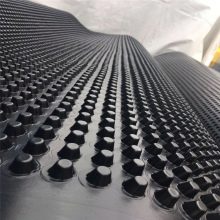
Views
The membrane is divided into two types, which are determined by the materials of manufacture and the scope of application, which is important to familiarize yourself with before purchasing.
Flat film
Such a membrane film is made from PVC, which may contain a synthetic polymer. The thickness of the material varies in the range of 0.2-2 mm, at least 0.4 mm is suitable for high-quality waterproofing. On the market you can find corrugated types, which are somewhat more expensive, but they have their own advantage - strong adhesion to the mortar. Such a material is ideal for insulating foundations that are laid no deeper than 10 m. It should be noted that a flat film membrane is also divided into subspecies, since the composition may contain additional components that affect the performance.
PVC film material is used most often, the first layer consists of plasticizers and fire retardants, to which chalk is added, and the bottom layer includes PVC with dyes. You can also find products made from TPO, which include polypropylene and rubber, which improve elasticity and durability.

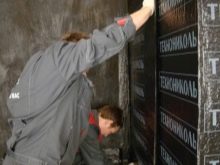
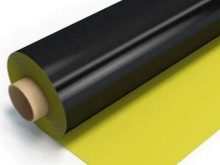
Profiled
For this, high-density polyethylene is used. This material has cells of different shapes, so the thickness may vary. Profile insulation protects the foundation not only from groundwater, but also from sedimentary waters, and also helps as drainage, for this it is combined with geotextiles. This type of polymer makes it possible to use the material for the base, which is laid more than 10 m deep.
The main advantages of this type of membrane include resistance to microorganisms, chemicals and aggressive environments. This is an environmentally friendly material that does not undergo decomposition, so it will last for many years, carefully fulfilling its protective function. The material is produced in the form of sheets, which can have round or square convex areas.
The profiled membrane is divided into pimpled and spiked, which can be used as a drainage membrane.
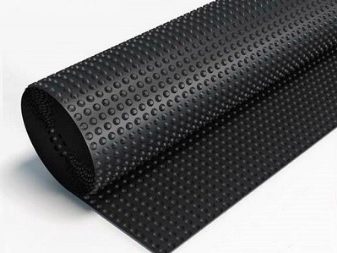
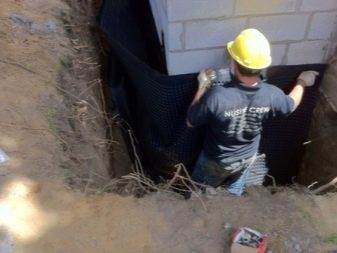
Top manufacturers
In the search for insulating material for the foundation and blind area, it is necessary to pay attention to a number of criteria, to take into account all the performance indicators of the product. There is a wide range of membrane manufacturers on the market, so it will not be superfluous to study the list of companies that have received an honorable place in the list of the best. Domestic manufacturers offer their goods on favorable terms, while you can get all the necessary information, as well as choose a material for insulation according to your own requirements.
These include the companies "Icopal", "Penoplex", "Sika" other. Firestone manufactures waterproofing material in Spain and supplies it throughout Europe. In the assortment you can find a wide selection of high quality products for blind areas and other tasks. Trade mark "Ondutis" has been offering roofing membranes with excellent vapor permeability for many years.
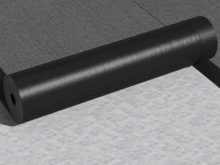
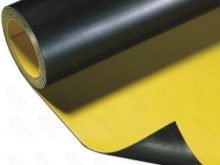
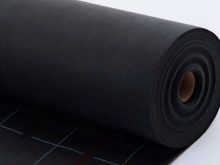
TechnoNICOL is engaged in the production of three-layer PVC insulation. The outer part is manufactured in such a way as to absorb ultraviolet rays, so the products are suitable for protection against moisture in a wide variety of conditions. Russian company "Stroyplastpolymer" produces a two-layer film, which has a reinforced coating and is suitable for roofing work, as well as a coating for waterproofing.
As for foreign brands, it should be noted Belgian brand Renolit SEwhich uses polymers to produce high strength insulation. The material does not lend itself to combustion and decay, is resistant to harmful effects and will last up to 50 years. Swiss company Sika represents a multilayer PVC membrane, including perforated, and the Dutch ICOPAL firm makes a single layer material that can be used in places with any climate.
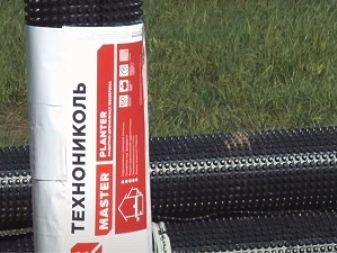
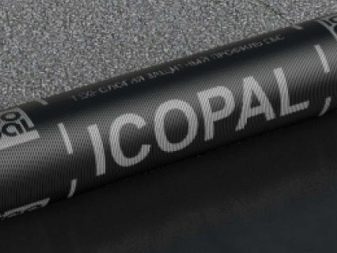
Mounting
Do-it-yourself installation technology is simple, if you follow the scheme correctly and apply the recommendations of specialists. Before you start laying the membrane, it is important to prepare the surface, find tools for fixing and laying. Preparatory measures are to cleanse, remove fungus and mold. It is important to check if there are any cracks in the base, if they are found, they should be fixed with mortar.
The surface must be level and free from damage. Once this work is completed, the primer mix is used. It is important to consider the direction of the web and how the mating sections are placed.
It is necessary to protect the insulating material from the bituminous composition, which negatively affects the structure; for this, geotextiles are used as a lining.
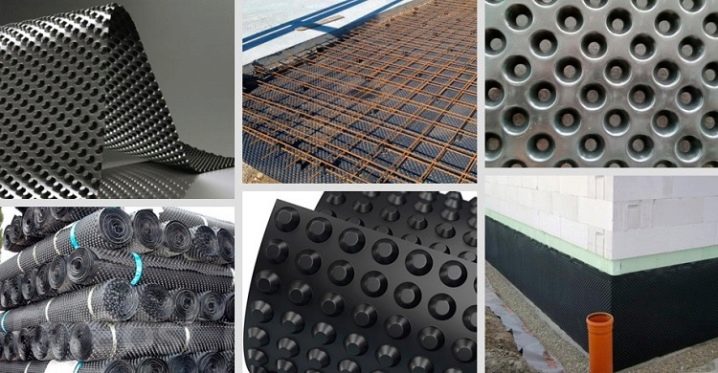
It should be noted that installation can be in several versions, it all depends on the type of membrane. Geotextiles are attached to the base, the overlap must be at least 15 cm. To connect the sections, use a building hair dryer, which will help to weld the material into a single whole. Membrane waterproofing is laid on the lining, the joints are covered with a protective strip. This method is suitable when it comes to the horizontal direction.
For the vertical, experts recommend opting for a profiled membrane. Here it is necessary to install plastic rondels, the distance between which should be 1 m horizontally and 2 m vertically. For fastening, a special glue is used that connects the membrane to the elements. After that, geotextiles are laid, which will protect against mechanical damage.

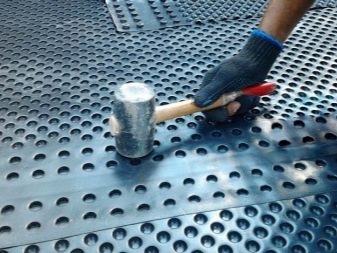
Nuances of welding
Installation work must be carried out carefully in order to obtain a quality result. The important thing is the welding process, which will provide reliable waterproofing protection. The membrane is installed in stages. As mentioned above, the surface is completely cleaned, all unnecessary is removed, then the joints are cleaned. It is recommended to carry out a test welding, wait an hour to check the quality of the seams, if everything is in order, you can start the main work.
Work with the membrane should be carried out at a temperature not lower than +15 degrees Celsius, otherwise the material will need to be additionally heated, and this is a laborious and time-consuming process. The material belongs to a new generation, it demonstrates reliable protection, which is actively used not only for the foundation of buildings, but also for roofing work.
It is important to remember that the installation must meet all the requirements.
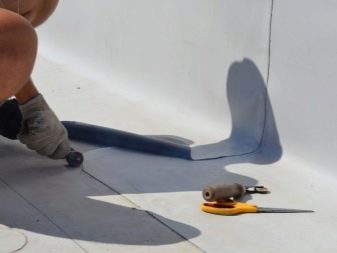
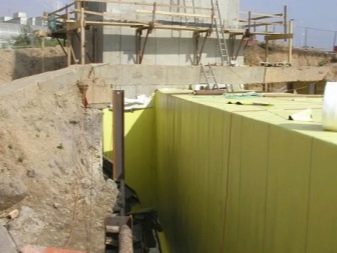
The comment was sent successfully.