All about turret lathes
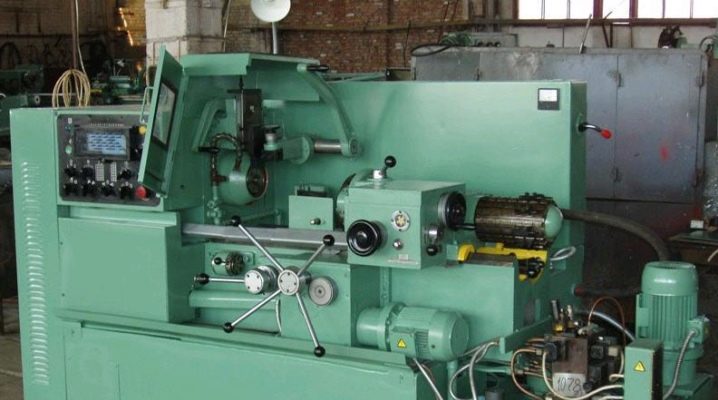
To carry out various operations for the processing of metal products, it is often necessary to use lathes. In a large category, we can distinguish units of the turning-revolving type, which are most widely used.
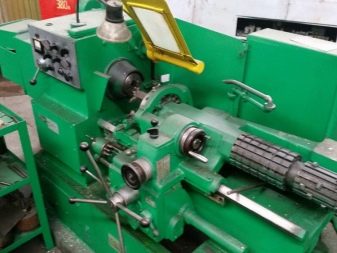
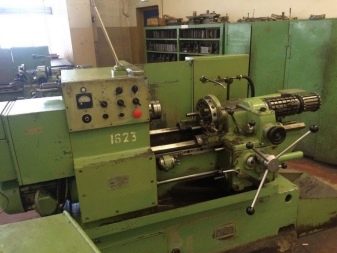
general description
The basic designation of turret-turning technology corresponds to typical turning installations. The difference is the presence of a multi-position rotary head. This structural element greatly increases the efficiency of the equipment and also reduces the time required to process each product. Besides, modern modifications of TRS with a CNC module have become widespread. They have a turret, special seating areas for the placement of cutting tools.
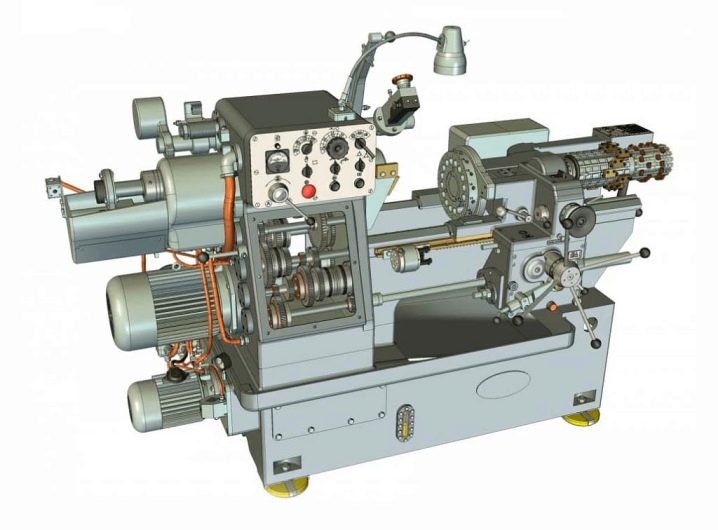
The required type of head structure is due to the rapid development of metalworking. The fact is that such a structural part in tandem with CNC allows to increase the processing speed of products by 2 times or more. In addition, it improves the parameters of the accuracy of the dimensions of the finished parts and the degree of roughness of their surface.
Speaking about turret lathe installations, it is necessary to identify the following key facts.
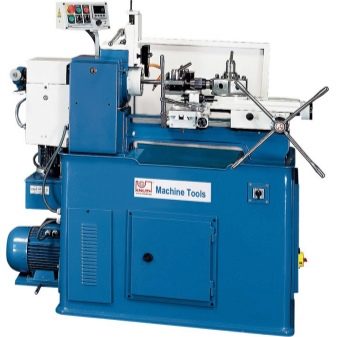
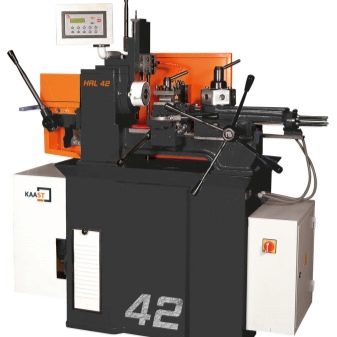
In most cases, this equipment is bought for industrial use. It is installed in workshops engaged in serial production of products; in all other cases, its use will not be economically justified.
Basic features of turret turning mechanisms provide the ability to perform processing of elements at a high feed rate at an increased speed... A special cooling liquid is supplied to the cutting area, which prevents overheating of the tool itself and the workpieces being processed.
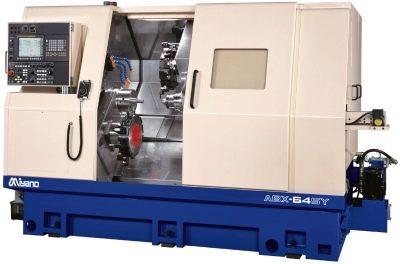
All the main units of such equipment are located by analogy with other lathes - this is what ensures the number of operations performed. In general, the technical parameters of such units provide the ability to quickly replace the cutting surfaces.
Views
Modern manufacturers offer a wide range of turret lathes. They differ in the mechanism of work, the range of operations performed, design features and some other characteristics. Let us dwell in more detail on the existing grounds for the classification of such installations.
By the type of workpiece being processed
Depending on the type of processed products, machines are for cartridge or bar work... Shafts of large diameters are fixed in the cartridge boxes. The bar section is smaller, but they have a rather impressive length.
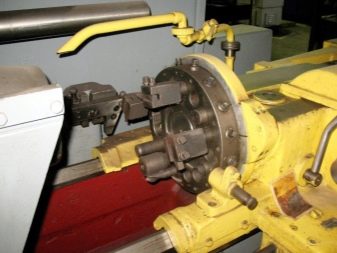
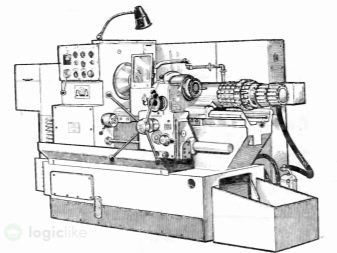
By position of the workpiece axis
By the placement of the axis of the workpieces to be machined, you can designate horizontal and vertical as well as inclined modifications... Machine tools with vertical and horizontal arrangement have received the maximum circulation, installations with an inclined axis are used much less often.
In addition, some models allow you to tilt the part for turning or other operations performed at a slight angle.
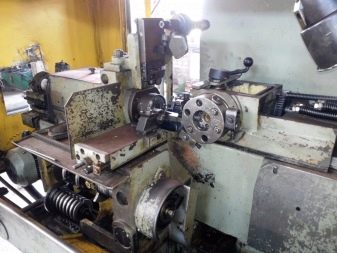
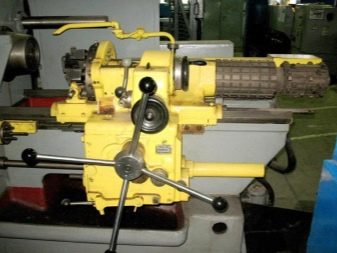
A separate group is made turning and revolving semiautomatic devices. They are in demand when working with rods of various diameters.Among the main features of such equipment are the following characteristics.
Single spindle machine, which has only one perforated spindle to accommodate the bar. In this case, the size of the cross-section of the hole is relatively small.
Additional equipment has the form of a unit responsible for feeding and holding the product in a static position.
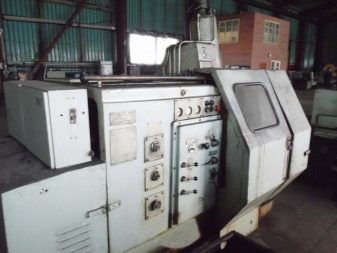
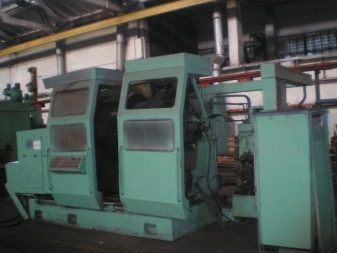
At the same time, the design provides for a device for retraction of the processed element after the end of the operation, due to which the maximum automation of production becomes possible.
The best manufacturers and models
Most domestic enterprises install standard TRS - 1P371, 1A365, 1N318, as well as S193A, 1365 and others... However, in the last decade, there has been a tendency to replace them with advanced technological versions with CNC. Modifications with CNC have many advantages, which are due to the increased degree of automation and functionality, as well as the exceptional accuracy of processing.
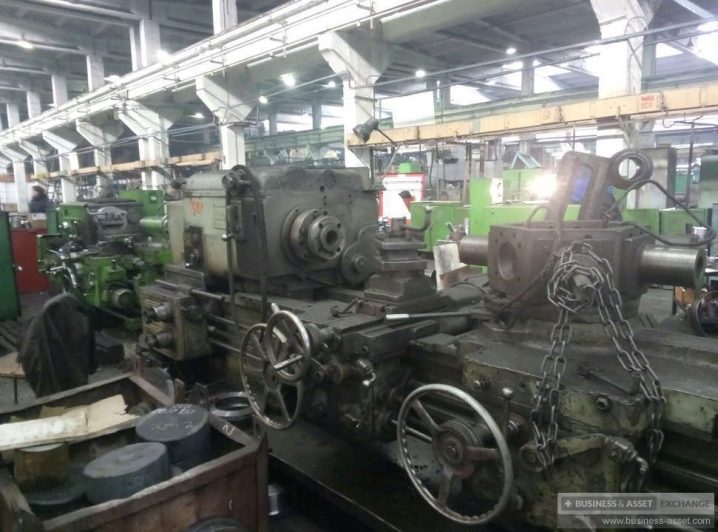
The equipment 1V340F30, offered by the Berdichev plant, is distinguished by its increased technical and operational characteristics. This unit is controlled through a CNC complex, and its design includes a head with 8 positions. The support is placed transversely, which allows processing:
-
single products with a cross section of up to 20 cm;
-
bar products with a diameter of up to 5 cm.
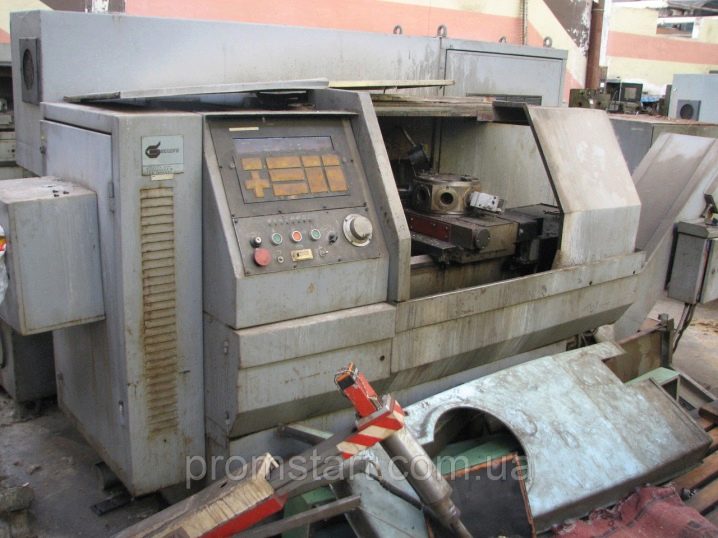
The 1P426DF3 unit, manufactured at the Alapaevsk machine-tool plant, is well known. This is a modern technology with a program control module. It is in demand for single, small and medium-sized production of metal products. It is not suitable for processing large batches.
The main feature was the location of the two heads on the cross support... One of them is hexagonal, designed to work with internal surfaces, the other is round, 8-position - for external ones.
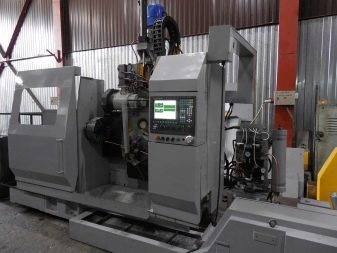
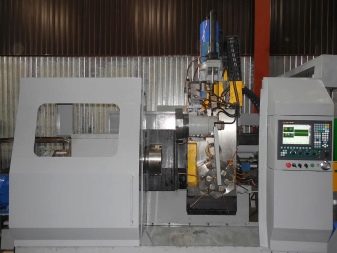
In addition, a lot of imported equipment, which is famous for its performance, has appeared on the Russian market of turning installations these days.
-
ST and DS units from Haas Automation (USA). These machines allow you to process alloy steel products, as well as stainless steel.
-
GS-200 machines from the company Goodway.
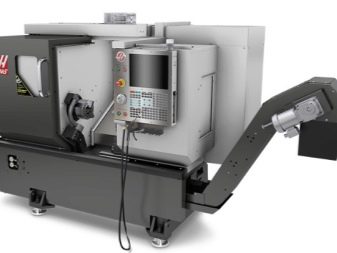
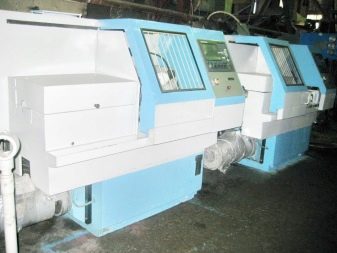
Components
Like other machines, turret lathe technology involves the use of components - guards, guide pipes and spindles... Today manufacturers offer a wide range of models, the number of spindles in which may vary. At the same time, the following key points are highlighted.
In the case of the horizontal position of the axis of the working head, the support can rotate around its own axis, as well as reciprocate along the direction of this axis. In this case, the rotation is performed simultaneously on several working positions, the total number of which often exceeds a dozen.
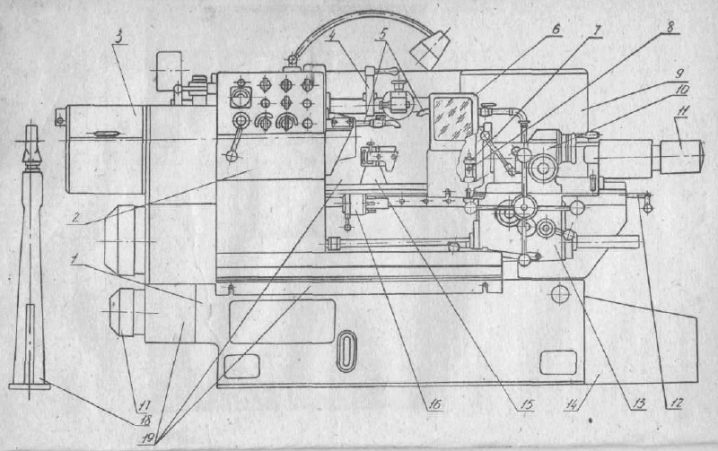
With an inclined as well as a vertical axis of the head, the caliper is either conventional or of the revolving type.
TPCs with CNC also assume a module that is responsible for high-precision machining with the ability to change the parameters of the head position. Usually, its main units are covered with a special casing. This increases the operator's safety many times over.
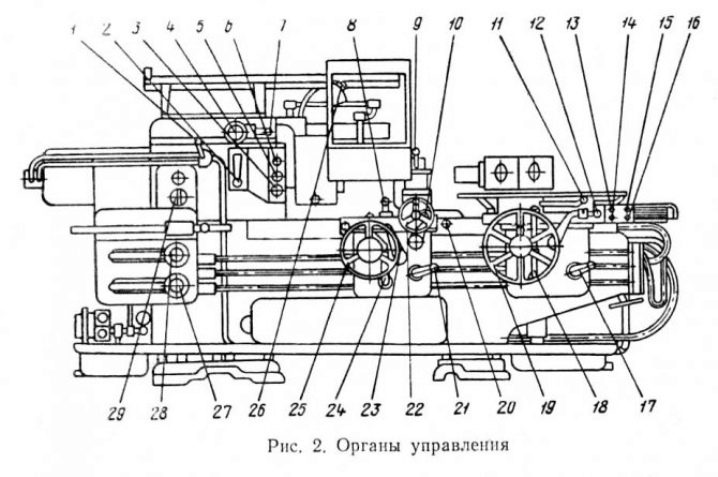
What kind of work is being done?
As already noted, the technical and operational parameters of modern turning-revolving devices allow performing a variety of operations. Variable products presented in the form of bodies of revolution can be used as blanks. The most common manipulations include:
-
turning on the outer surface, while the passage can be rough or finish;
-
cut when installing the cutting element;
-
threading - both internal and external;
-
grooving different depths and configurations.
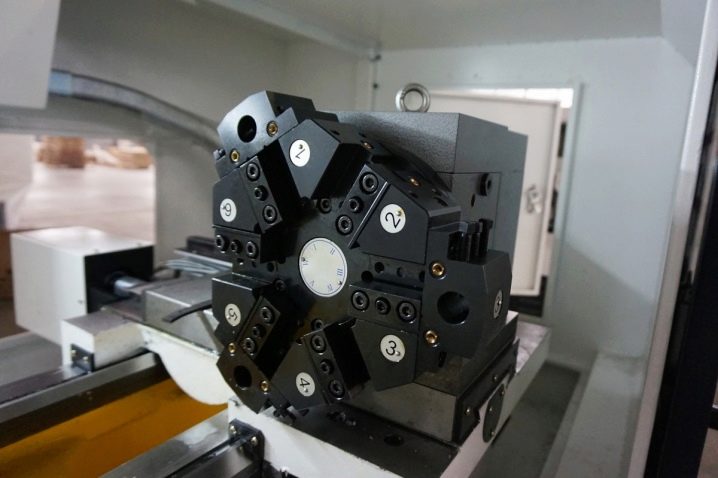
In addition to the standard cylindrical configuration, such machines are capable of processing other types of workpieces.
-
With profile shaped type - when a semi-automatic turning-milling machine is used, then turning, like any other processing, is performed through a curved template or by means of a copy ruler.
-
Conical - processing is carried out by means of a special copier. In addition, a conical surface can be obtained by the method of carrying out a one-time longitudinal-transverse feed.
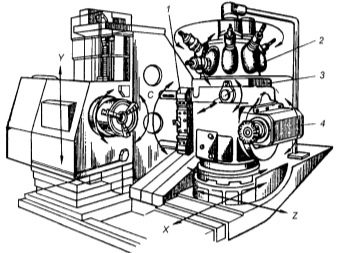
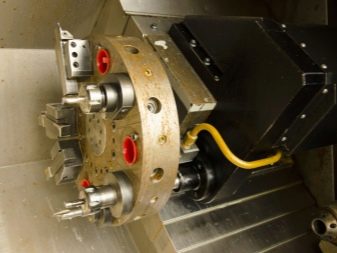
Compact turret turning mechanisms can be placed in a separate category. Such devices can even be installed in home workshops.
What to consider when choosing?
When choosing turret lathes, you need to focus on important criteria.
Accuracy category - to establish the possibility of using a certain modification of equipment for processing metal products, it is necessary to know what accuracy can potentially be achieved. The vast majority of versions provide for class H.
The maximum parameters of the part - section, length, as well as the layout of the working units among themselves.
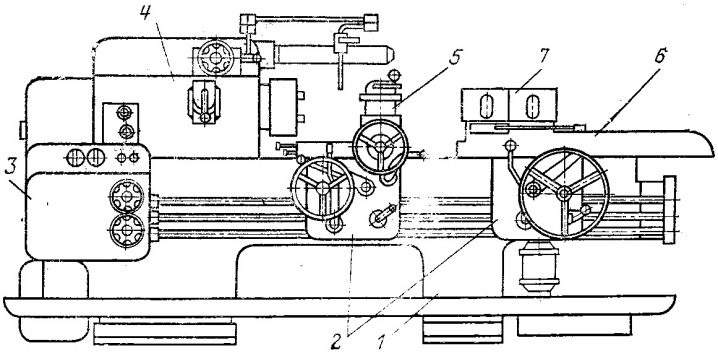
Workpiece material - usually on such machines, cast iron, high-, low-carbon or alloy steel is processed, turning of other alloys is allowed.
Limiting number of revolutions per unit of time - a workpiece with specified requirements for dimensional accuracy and roughness can be obtained exclusively by untwisting the parts to a certain speed. In this case, the total number of transmissions must be taken into account.
Manufacturers must indicate data on the maximum speed at which the isolated units can move when performing high-speed feed.
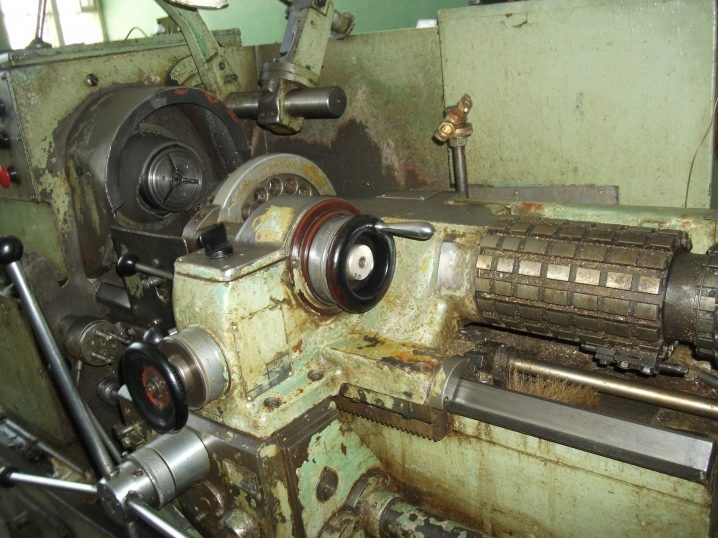
Motor power parameters and number of motors - as a rule, in small-sized installations, the engines have low power, since the processed parts are compact, and a little metal is removed for each run. In series production, motors must be able to withstand continuous loads.
Dimensions and weight of equipment - it is much easier to install mini-machines. In addition, large-sized ones need careful preparation of the working base.
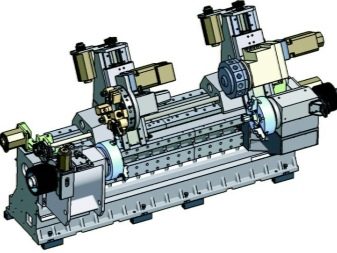
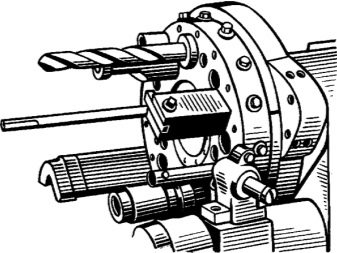
And also it is necessary to take into account that the kinematic diagram of the mechanisms can vary... For example, old-style models were created in such a way that replacement wheels of certain configurations were installed to form certain types of threads.
Protection - modifications with CNC require the installation of a protective cover. This minimizes the risk of injury during the operation of the equipment.
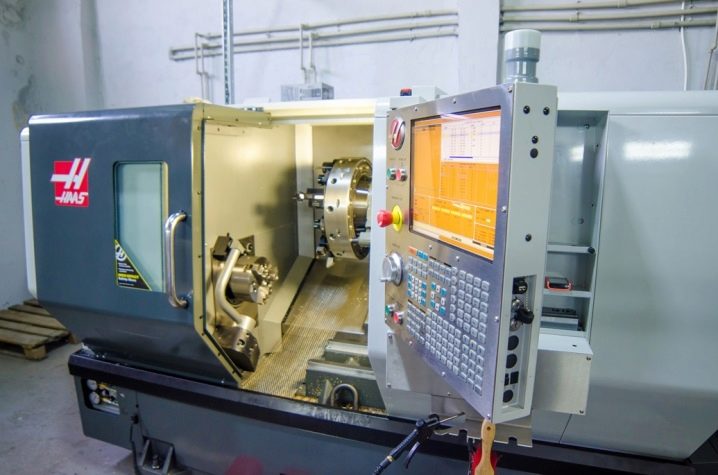
In modern turning devices, the installation of the necessary equipment, as well as cutting surfaces, is carried out with maximum accuracy. In such units, there is no need for manual replacement of the cutting tool - this significantly reduces the processing speed of each part. As a result, productivity is increased, which entails a decrease in the cost of processing workpieces. At the same time, the repair of such machines causes a lot of difficulties. Therefore, during their operation, special attention is paid to preventive maintenance, timely identification and elimination of problems.
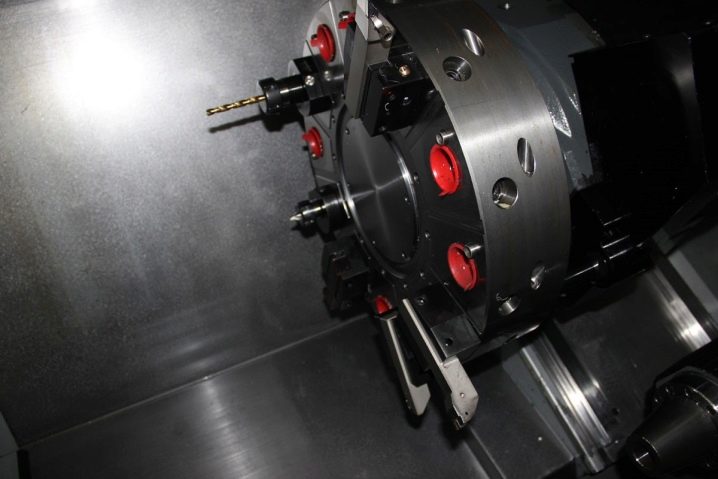
Setup features
Before starting to operate the turret turning equipment, it is very important to set it up. It includes several main stages.
-
Installation of equipment for fixing the workpiece, installation of cutting and auxiliary tools.
-
Setting the stops, necessary for guiding the rods and limiting the movement of the calipers.
-
Installing the control unit for cams, plugs, switches, handles and other devices in order to obtain a given frequency of movement of the spindle and the required speeds of the cutting tool.
-
Test processing a couple of trial elements, checking their suitability for subsequent operation.
-
Reconciliation and, if necessary, readjustment of the location of stops on the machine according to a given project.
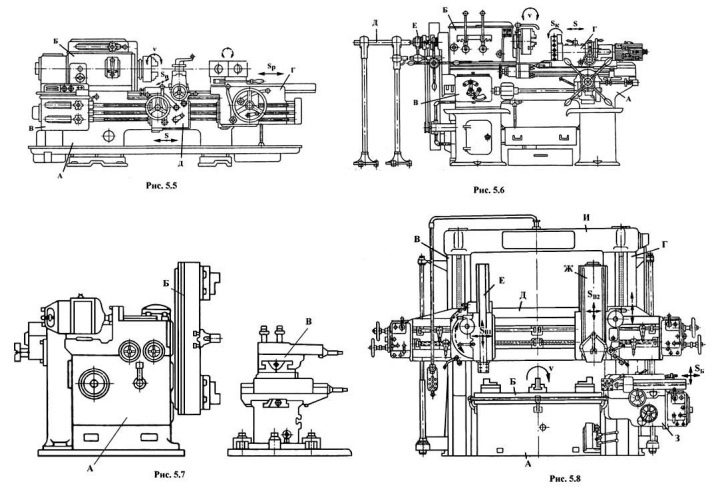
The comment was sent successfully.