All about cutting fluids for machine tools
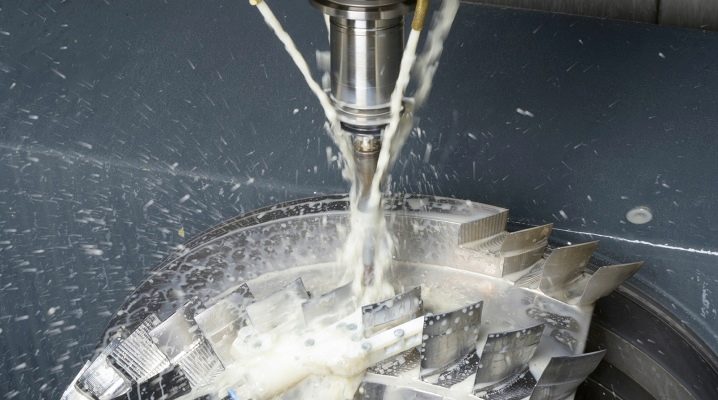
During operation, the parts of the lathe - replaceable cutters - overheat. If you do not take measures to forcibly cool the rubbing components that perform cutting, then the torches, as well as the parts they cut, will receive significantly more damage in a short time.
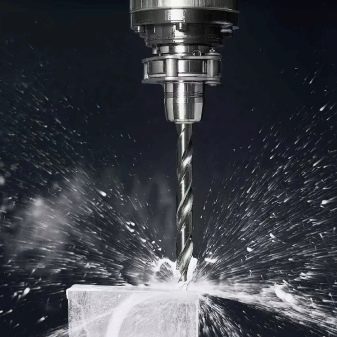
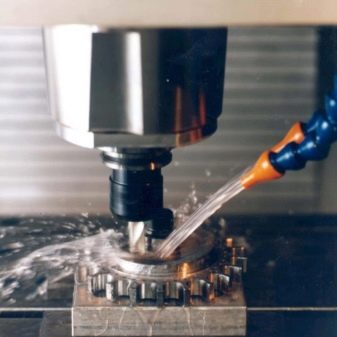
What it is?
Lathe coolant (cutting fluid) is used to reduce torch wear on any type of machine, including CNC machines. The latter, used for mass production (copying) of parts, need timely cooling many times more than manual machines, on which the control is carried out directly by the worker-operator. Threading, turning - both processes are accompanied by heating during friction. Both the torch and the workpiece heat up. As a result, when the machine is not lubricated, chips and microcracks appear on the parts. As a result, the number of defective parts increases dramatically. Blunt cutters destroy the drive and gearboxes of the machine faster. The work of the worker is also complicated - he gets burns and other work-related injuries. Normal and long-term operation of any processing machine or unit is impossible without coolant.
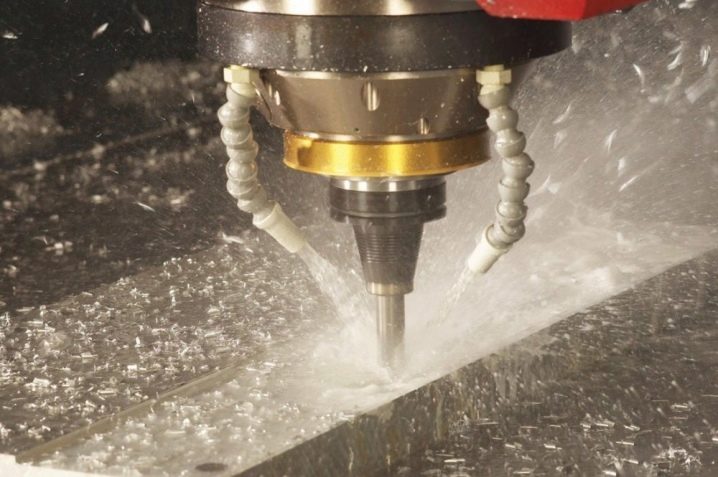
In addition to lubricating and cooling the rubbing elements, the coolant facilitates the removal of metal chips, dust from the surface of workpieces and cutters.
Description of species
Excessive heat generated during cutting and sharpening of workpieces can be removed with oil and water-containing substances. The composition of the cutting fluid assumes oil and water-miscible bases. For ease of use, the machine provides a spray nozzle with which this liquid lubricant is applied to the cutting edges of the cutters.
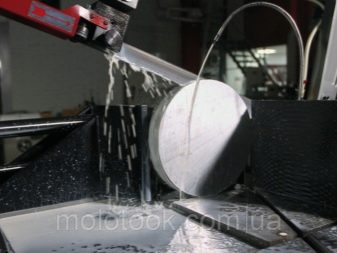
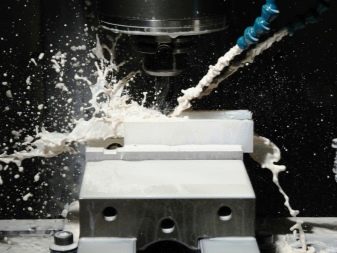
Oil
The oil evaporates extremely slowly - even at elevated temperatures. This makes it difficult to dissipate heat on the torch and workpieces. The advantage of the oil composition is that steel retains its properties. Consumption - much less than that of a water base, this reagent consists of 70% of standard "20" machine oil, 15% of 2nd grade linseed oil and 15% of kerosene, which increases the accuracy of threading; shaped cutters are used here.
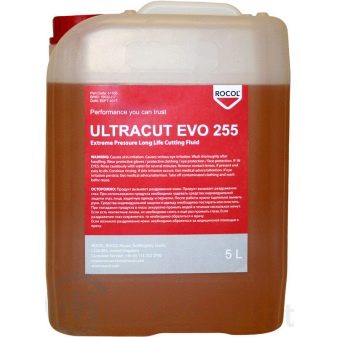

Sulfofresol contains a sulfuric additive. The cross-section across the part to be turned should be small. The disadvantage is the toxicity of sulfur, the inhalation of which can cause malignant diseases of the blood and lungs, therefore work is usually done in a gas mask. 90% sulfofresol and 10% kerosene are used for threading, deep drilling and finishing parts.
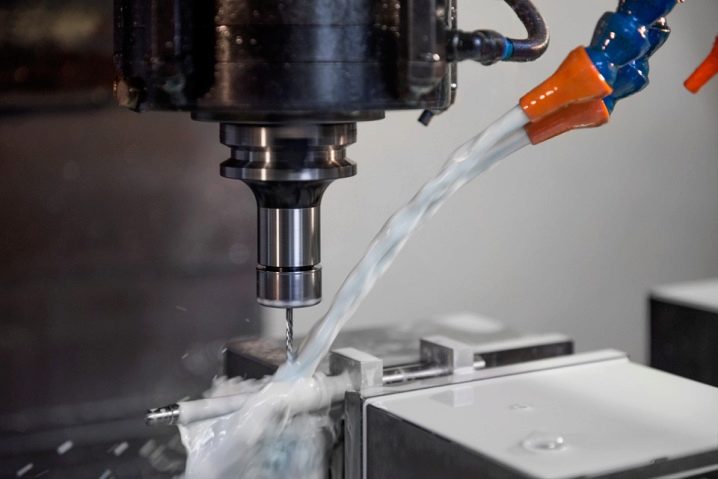
Regular kerosene is needed for turning aluminum parts. The second use of kerosene is the use of dynamic whetstones in the sharpening process.
Water miscible
Cooling lubricants include synthetic ones, for which water is used to dissolve. The advantage of such a lubricant is rapid heat dissipation, the disadvantage is increased consumption. because when the torch heats up to 100 degrees, the water quickly boils away. The heat capacity and heat removal of water is much higher than that of any liquid petroleum products.
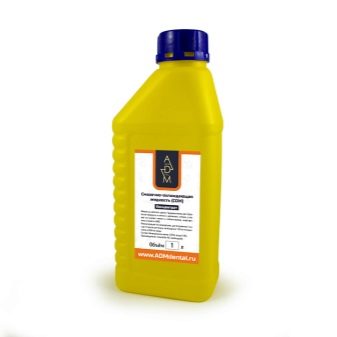
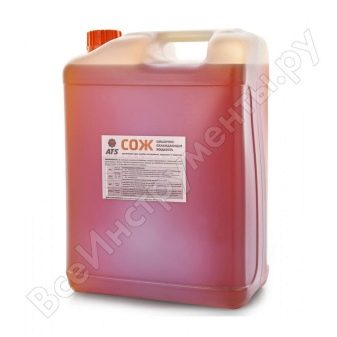
Soda ash dissolved in water - in an amount of 1.5% - is used for rough turning of workpieces. A similar composition has 0.8% soda and a quarter percent sodium nitrite. Soda can be replaced with trisodium phosphate - also in an amount of the same 1.5%.A solution with potassium soap (up to 1%), soda ash or trisodium phosphate (up to 0.75%), sodium nitrite (0.25%) prevents the premature development of corrosion on the high-speed steel of the cutter.
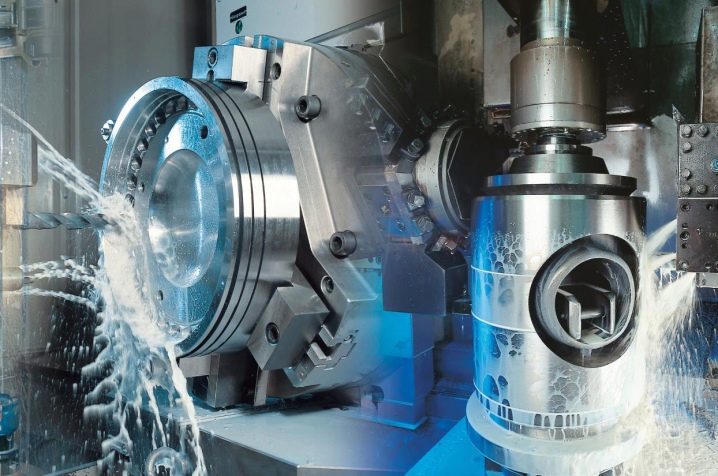
The following aqueous solutions are also used.
-
4% potash soap and 1.5% soda ash for shaped turning. The soap composition should not contain chlorine compounds.
-
Emulsol (2-3%) and tehsoda (1.5%) remove strict restrictions on the purity and smoothness of processing. Suitable for high speed turning.
-
5–8% emulsol and 0.2% tehsoda or trisodium phosphate allow you to sharpen almost any details "cleanly".
-
An emulsion based on oxidized petrolatum (5%), soda (0.3%) and sodium nitrite (0.2%) is suitable for turning with increased purity of performance.
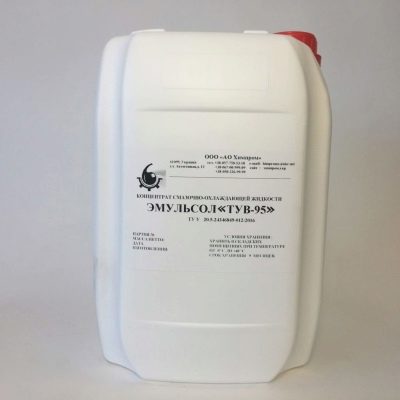
Having decided on the specific composition, check out the assortment (by brand).
Popular manufacturers
The most demanded, according to statistics, are manufacturers Henkel, Blaser, Cimcool... These firms have focused in advance on the production of cutting fluids. Companies producing engine oils for the Castrol, Shell, Mobil brands, specialized in machine oil, not machine lubricants. Dozens of other names can be counterfeits, toxic to people and damaging machines. Russian brands are also represented on the local market, but due to their low resistance to delamination, they are rarely used anywhere. The rapid loss of structure uniformity leads to rusting of machines and cutters, and they also foam and settle on contact with water.
Many workers are allergic to these products, and it is very difficult and expensive to dispose of these lubricants.
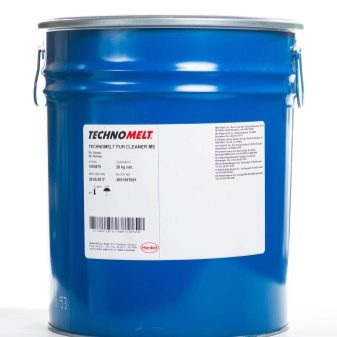
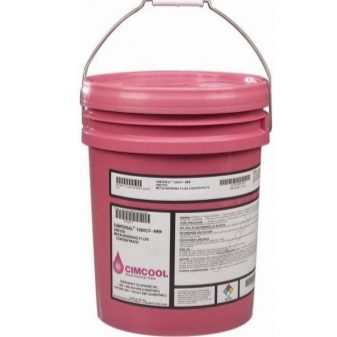
It is worth mentioning separately Oilcool compositionto which the additive Ecoboost 2000... This composition is produced in Russia - today it is a high-quality substitute for the above brands. For lathes on the Russian market, the following compositions are presented.
-
I-12, I-20 oil-based - comply with GOST 6243-1975.
-
Emulsifiers containing alkaline soap comply with the provisions of GOST 52128-2003.
-
Compositions based on polybasic alcohols, tall oils, triethanolamine are produced according to the conditions of GOST 38.01445-1988. Suitable for working with high-speed or alloy steel, stainless steel. The waste must be disposed of immediately.
-
Sulfofresols - comply with GOST 122-1994. It contains pure oil and sulfuric additives. Reduces abrasion, protects cutters and parts from rusting. Does not include water, alkalis and acids.
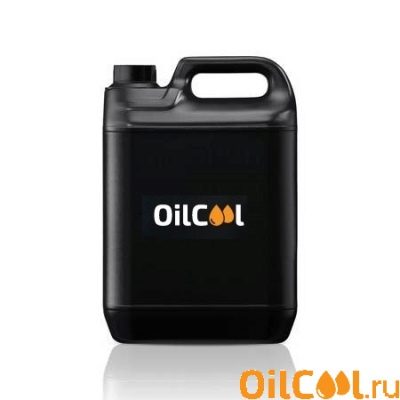
The advantage of the listed substances is their low viscosity. The composition quickly spreads over the surface of the cutter, preventing the chips from sticking to the cutter. The international assortment starts with the MobilCut brand.
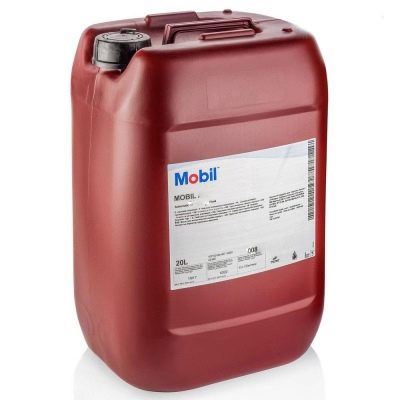
Nuances of choice
In addition to turning turning, the need for cooling lubricant is also observed among craftsmen whose activity is milling. The composition must be selected, guided by the type and type of work, the type and class of the machine, the list of actions, the consumables used and the method of introducing coolant. There is no one-size-fits-all solution for turning cutting. But you can get closer to it by choosing a composition that better cools and prevents the beats that arise in the process of cutting steel and non-ferrous metal. The processing of stainless steel does not negate the possibility of using anti-corrosion additives, which can either be included in a specific composition or be supplied separately. Stainless steel is a viscous and difficult material in turning and drilling, finishing, so the concentration of cutting fluid should be designed for cutting just such materials. The processing of aluminum and other soft non-ferrous metal forces to resort to compounds with anti-burr and anti-bump properties.
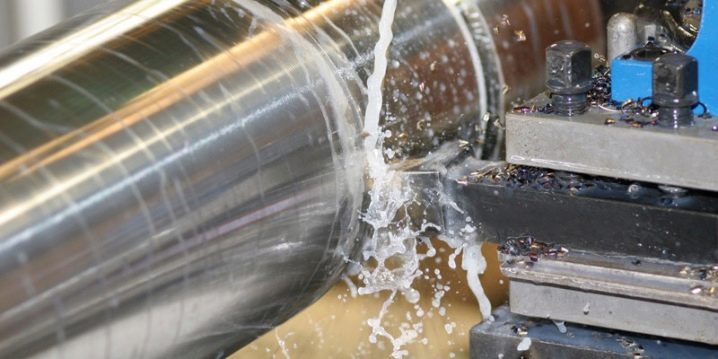
The coolant should not create fogging, support self-combustion, and form foam. To prevent scratching of the workpieces being processed, use "detergent" compounds.
Features of filing
The machine pump is equipped with tubes, at the end of which there is either a spray nozzle or a point nozzle, which provides targeted irrigation of the torch and the surface of the parts. The pressure in the system is 10 atmospheres or more. The so-called method. independent irrigation does not promote uniform spray of the composition over the torch and the work surface. Chip evacuation is difficult. This disadvantage is overcome by increasing the pressure - within reasonable limits, so that the pump and hoses remain intact.
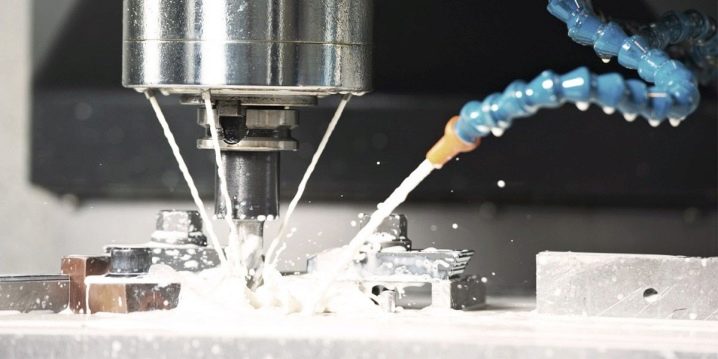
The spindle engaging method uses a thin and narrow spiral bore (outside) of the torch. The lubricant is supplied by means of a special path suitable for the chuck. Consumption of lubricant - according to the indications of the tank graduations - is economical, since it is immediately directed to the cutting edges. The chips that are scraped off during work are quickly and efficiently removed from the cutting edges.
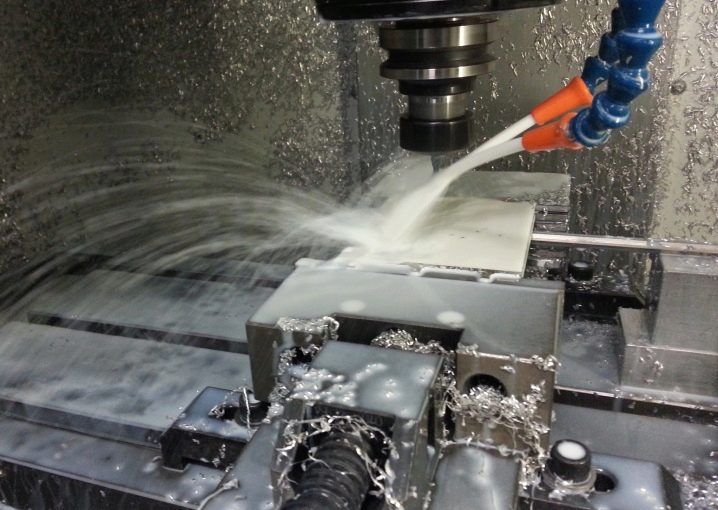
An independent supply system provides for the arrangement of a drip station. She found application in non-CNC machines. For its assembly, in addition to a dropper, capillary hoses, a primitive faucet or a capillary hose adjustable by the hall are used.
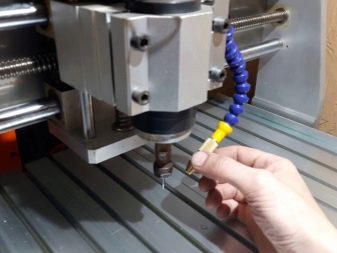

Application
The coolant is cleaned as it becomes cloudy with steel or non-ferrous metal microparticles. The simplest way to remove metal deposits from a liquid is to pass it through cotton wool or filter paper. The coolant replacement schedule is after 10 months. The waste is contaminated with the smallest iron particles, which are dissolved in it and easily overcome any filter.
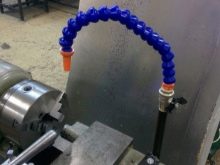
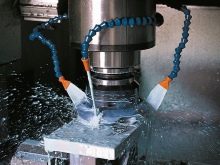
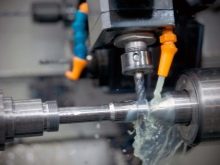
The comment was sent successfully.