Accessories for machine tools
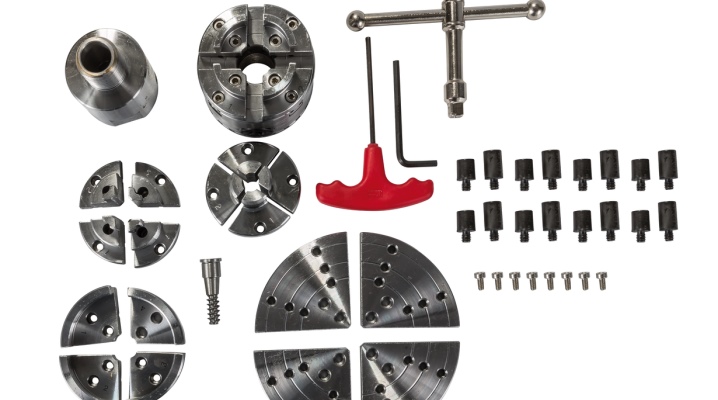
Tooling for metal cutting machines expands their technological capabilities and saves money. Instead of buying new equipment, you can use the existing one. From this article you will find out what kind of machine tools for CNC machines are and what they are for.
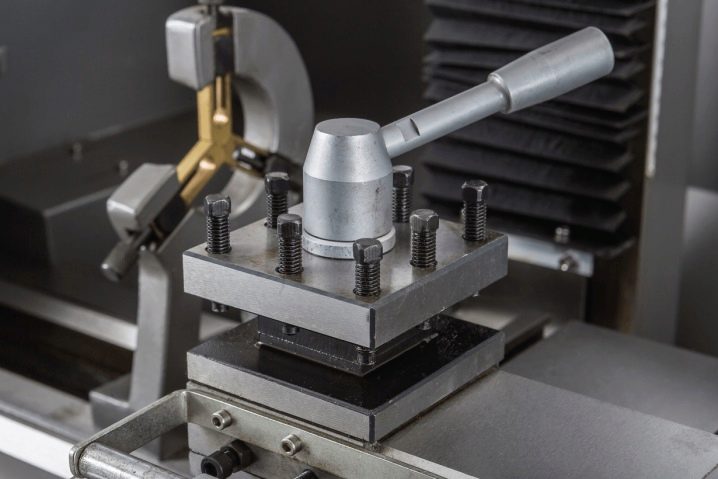
Primary requirements
Machine tooling is a fixture with which tools and workpieces are fixed on the machine. And also, thanks to the equipment, the machines can perform operations unusual for them. For example, Thanks to dividing cooking on a conventional vertical milling machine, gears can be cut. And the milling head on the turning equipment cuts the keyways.
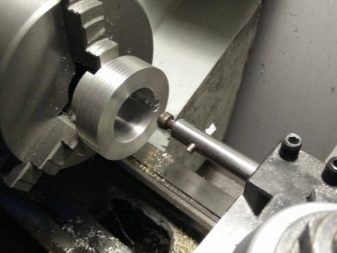
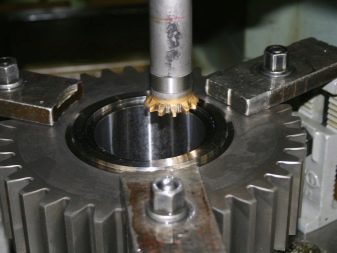
Accessories are not included with the equipment, they must be purchased separately. To get a good result, it must meet a number of requirements.
- Rigidity and damping qualities. Thanks to the rigid device, the part does not "walk" from side to side. It's good. But when roughing, rigid tooling will not smooth out the inevitable vibrations, and this will lead to inaccuracies. Therefore, for precision machines, the tooling must be made of hardened hardened steels, and for roughing, soft raw steel is needed.
- If possible, have a mechanized drive. It is important that the drive does not clamp the workpiece, but rather releases the fasteners. Then, if the hose breaks or the drive is short-circuited during operation, the workpiece will not fly out of the machine, but will remain in the fixture. It's safer this way. The workpiece can be securely fastened, for example, with a Belleville spring pack.
- The time to reinstall the workpiece should be 2-10% of the time of its processing on the machine. And it is necessary that the fastening elements do not intersect with the trajectory of the tool.
- The accuracy class of the tooling must be the same as that of the machine.
- And the standard is reliability, durability, low price.
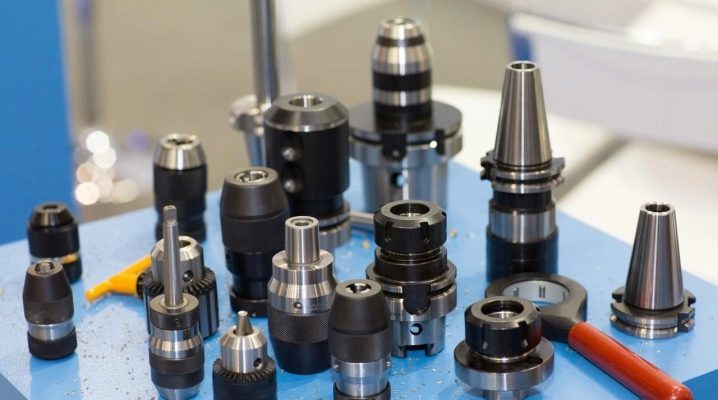
The requirements for machine tooling are the same everywhere. But its models for different machines are different.
What is needed for lathes?
In lathes, as in any other machine tools, tooling is used to:
- hold the workpiece and tool;
- measure dimensions;
- give additional support to the workpiece.
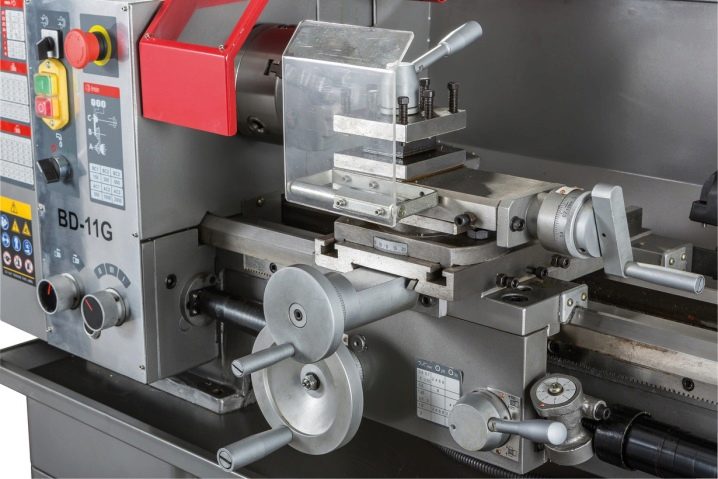
There are different types of popular rigs for these machines.
Chucks are needed to secure the workpiece. They are of several types:
- Collets hold short and fragile workpieces;
- driver ones are used for fastening long shafts;
- wedge-shaped ones ensure high installation accuracy;
- lever arms are able to fix workpieces of various sizes;
- diaphragms precisely center the part during finishing operations;
- for woodworking machines, a trident is needed - the simplest device to fix a soft wooden blank;
- The 3- and 4-cam have good precision and are easy to use.
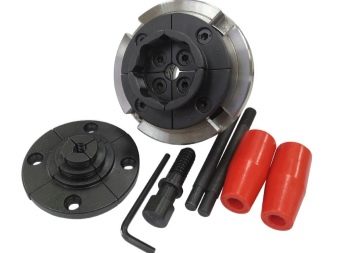
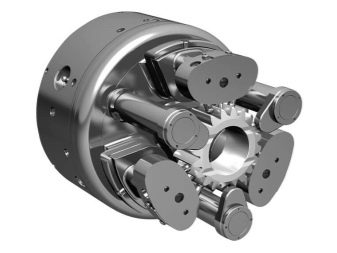
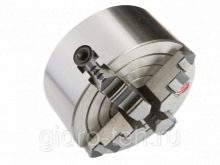
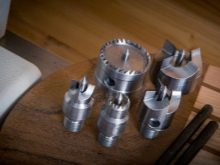
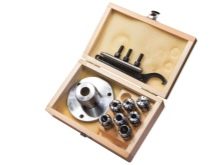
Chucks allow you to fix short parts cantilever and handle the ends.
- Plan-washers fix asymmetrical workpieces.
- The centers are needed to secure the shafts, which have center holes prepared. Unlike chucks, in the centers the basing goes along the axis of rotation of the workpiece, and not along the outer surface. Therefore, round workpieces are highly accurate.
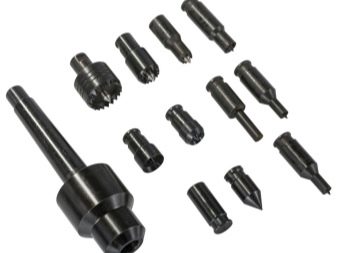
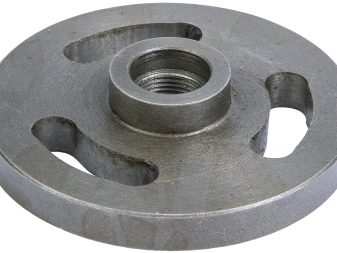
There are 2 types of centers.
- Non-rotating (persistent) are stationary during operation, and the workpiece rotates on the oil film. Such centers have increased accuracy, but are prone to overheating due to friction.The gear centers fixed in the spindle can transfer rotation to the workpiece.
- The rotating centers do not allow heating, but due to the inevitable play in the bearings, they have lower accuracy.
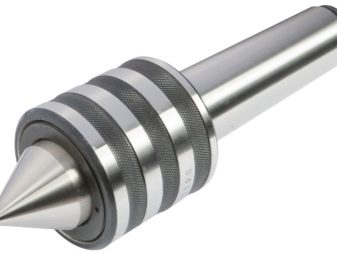
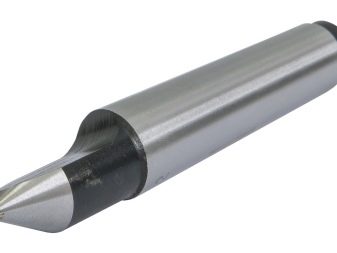
Taper centers are only suitable for shafts. And to install a workpiece with an internal hole, fungal centers are used.
- Lunettes are used when the workpiece is very long. This is an additional support that does not allow the workpiece to bend.
- Various lamps.
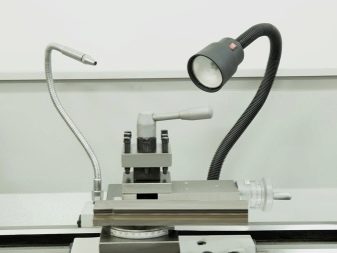
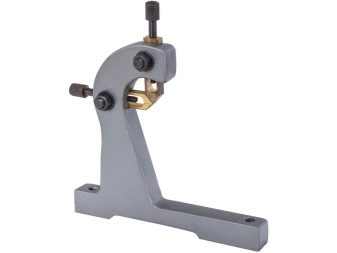
In addition, milling heads are installed on the lathe. It turns out a universal multi-purpose machine. But it is better to sharpen complex workpieces on specialized equipment.
Milling accessories overview
It faces similar tasks, but the designs are different.
Technological equipment for tool fastening can be of several types.
- The self-clamping chuck is used to grip end, end and finger mills. But often the tool is inserted directly into the spindle.
- The accessory bushing is used when the tool shank does not fit into the bore of the spindle. With its help, for example, a milling cutter with a cylindrical shank or a 7: 24 tool taper can be clamped in a spindle with a Morse taper.
- Mandrels are needed to secure disk and cylindrical cutters on horizontal milling machines.
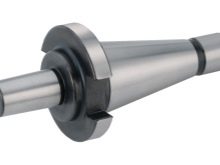
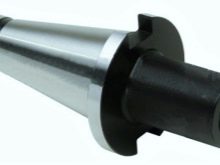
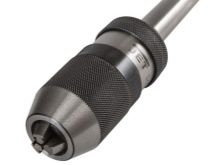
To fix the workpieces, special devices are used.
- The vice is used for small parts. Vices are self-centering when both jaws move, and not. Sponges are made of hardened or mild steel, plastic, rubber and others. Not necessarily flat, parts of complex shapes are installed in shaped jaws.
- Dividing heads allow precise cutting of splines or teeth.
- Tables are rotary and stationary. Some models can be folded back, allowing you to machine the workpiece from the side.
- Magnetic plates with permanent or electric magnets. The former are better because they do not heat up due to eddy currents and induction, as is the case with electromagnets. But the latter have a higher clamping force.
- Vacuum devices, clamps hold the workpiece in the desired position.
- Prisms and clamps, thanks to which the shafts can be clamped and machined, for example, a keyway.
- Pins and fingers. Needed for placing flat workpieces on the table. 3 pins are used to locate the part. This is logical, because to set the position of the plane, you need 3 anchor points. Therefore, the installation on the pins is more accurate. And to fix the workpiece, various clamps are used.
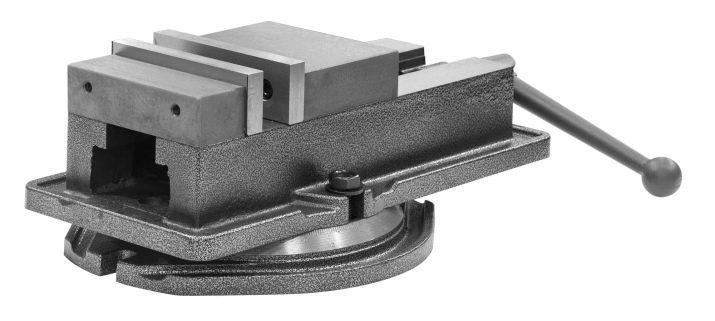
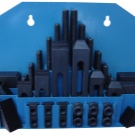
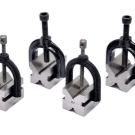
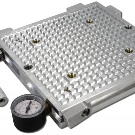
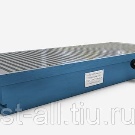
The functionality of the machine can be expanded by using a drilling, grinding or slotting head. But no matter how accurate the milling equipment is, grinding machines that need the appropriate tools give a mirror-clean surface.
Accessories for grinding models
They are similar to those used for other machine tools. For example, for cylindrical grinders you need:
- cam chucks with replaceable jaws;
- multi-leaf collet clamps;
- driver chucks, rests for long shafts;
- fixed and rotating centers, direct, reverse, fungal and others;
- dividing heads for finishing gears.
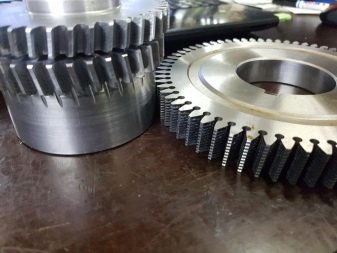
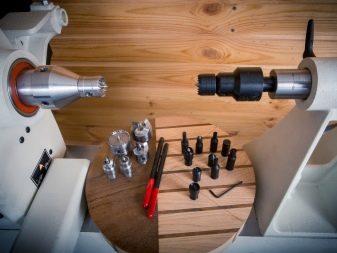
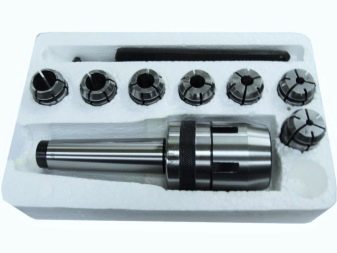
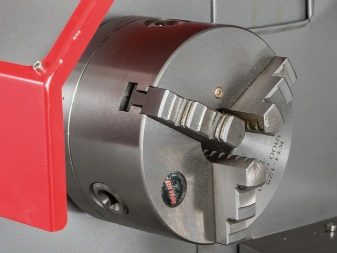
Tooling for surface grinding machines differs little from accessories for milling equipment:
- rotary tables;
- a vice with replaceable jaws for fixing workpieces - it is desirable that they be self-centering;
- prisms, clamps;
- mandrels for grinding wheels.
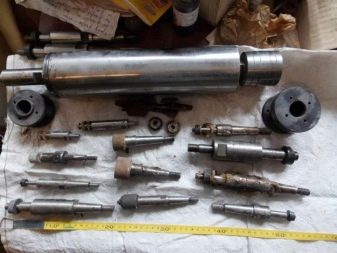
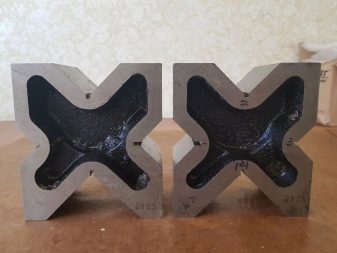
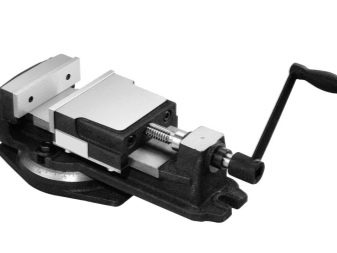
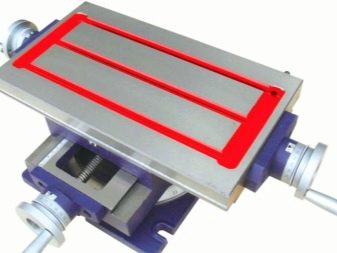
But the accuracy of the grinding attachments must be higher than for other machines. This is achieved by adjusting the gaps and backlash in the moving mechanisms.
But magnetic plates are used to a limited extent. When grinding on metal, a lot of metal dust is generated. And since the magnetic lines easily pass through the metal workpiece, the dust is poorly washed off by the coolant (cutting fluid), magnetically to it.
As you can see, tooling for machine tools expands the range of manufactured parts. And there is no need to spend money on new equipment. The only thing that should not be saved on is protective devices. Always follow safety precautions.
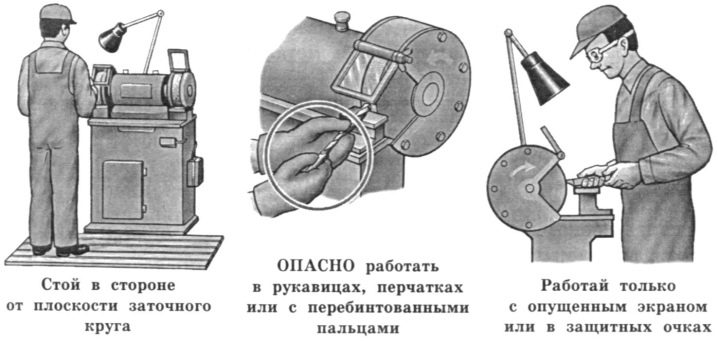
The comment was sent successfully.