All about tenoning machines
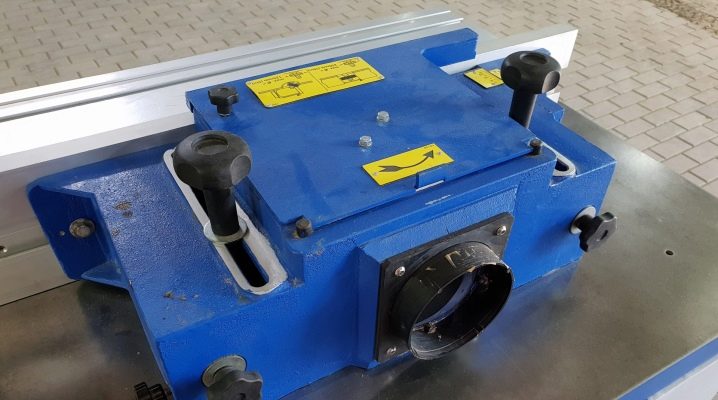
You need to know everything about tenoning machines no less than about other types of woodworking equipment. Wood tenoning machines can be used for box tenon and chairs. Among them there are double-sided models, machines for making beehives and other types of machines.
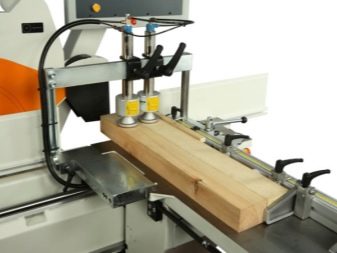
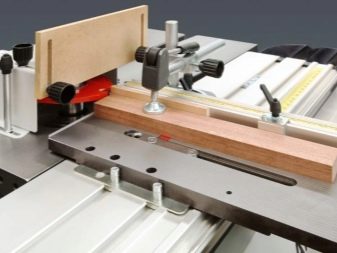
general description
The assembly of joinery and building structures, furniture is unthinkable without the use of sophisticated equipment. Among it, tenoning machines stand out especially. They are also suitable for joining short bars. After this procedure, large parts with impressive length are obtained. Stud connections can be of different types - but any decent machine will do them without any problems.
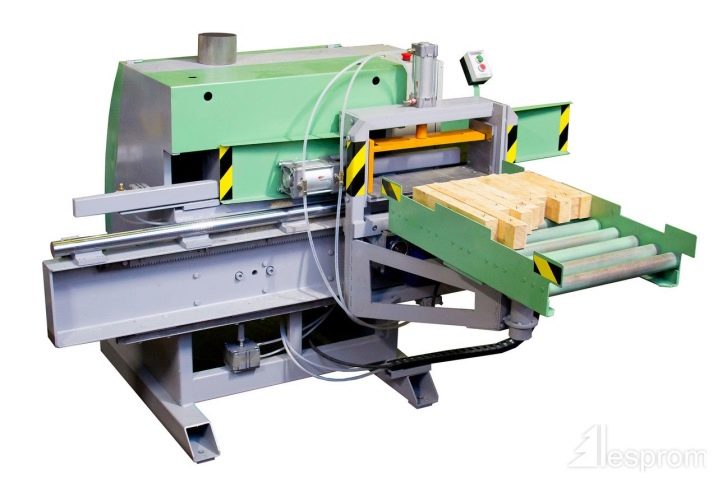
In any large-scale production, a CNC tenoning device is used. It is the most versatile and allows you to create any kind of spike joints in large quantities in a short time. The setup is not difficult and takes place in a short time.
Tenoning machines only work on wood. They differ in variable feed rates.
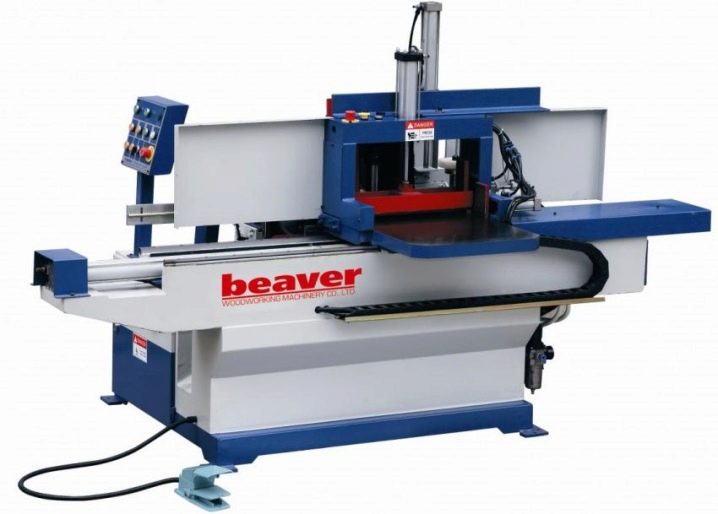
This solution allows you to work with small tools. In turn, small devices are capable of achieving high manipulation accuracy. Users can resort to dozens of different technological operations. Tenoning equipment is often controlled from a PC in a convenient graphical mode. The main work is performed by special cutters for splicing.
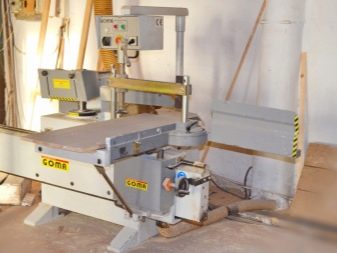
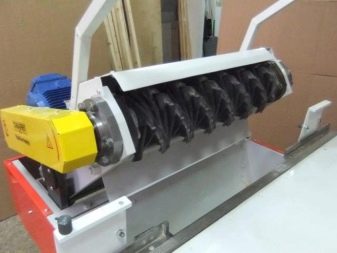
The difference between them can be expressed in:
-
section;
-
the number of knives;
-
splice height;
-
the size of the thorns.
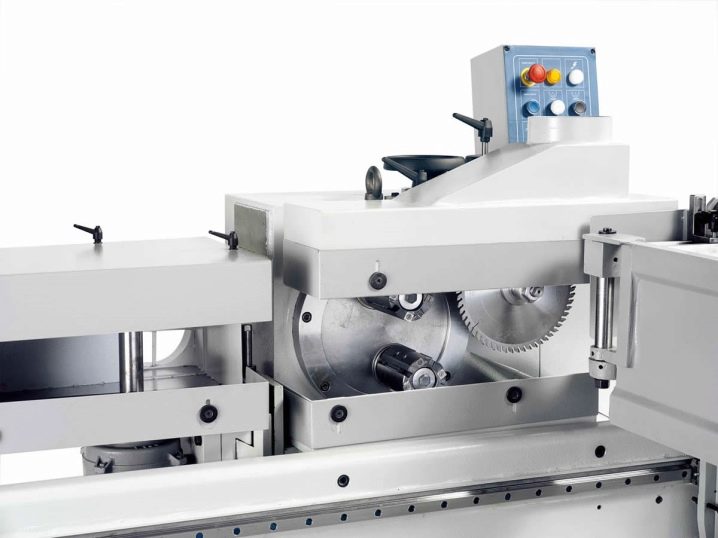
Even the best tool will wear out frequently. Therefore, auxiliary interchangeable sets of knives for cutters are supplied by many companies. The highest speed also plays an important role. Also significant characteristics can be considered:
-
body material;
-
cutter construction material;
-
landing diameter;
-
number of teeth.
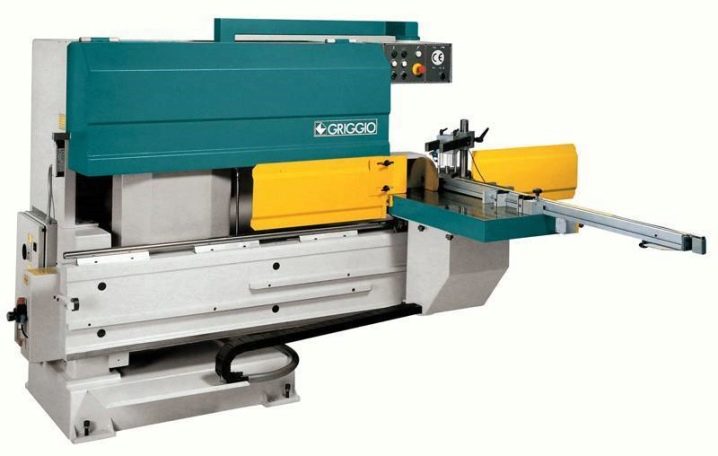
The structure of the tenoning machine is very well thought out. The details are arranged in it in the order of the performed technological manipulations. It usually starts with facing. The sawing mechanism is responsible for this operation. Then, as needed, a special head forms an eyelet. When it is ready (or after this stage), they move on to using tenon heads.
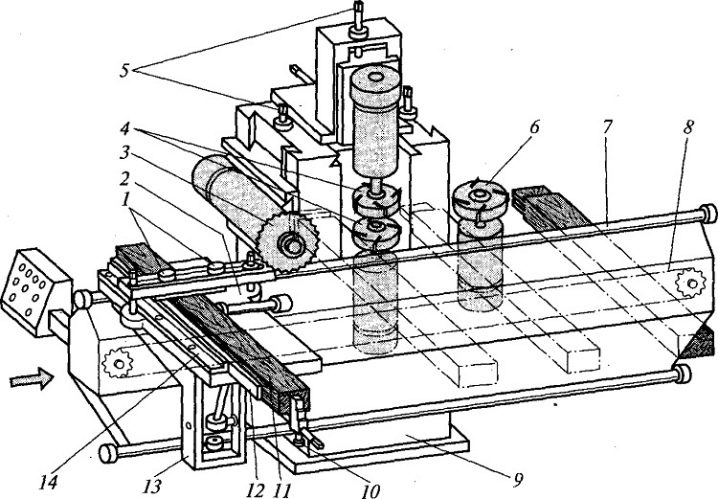
Species overview
The topic of tenoning equipment classification is not as simple as it seems. Most often, in practice, there are devices designed to receive frame, window and door blocks. The difference may relate to the number of sides to be processed and the characteristics of movement. The woodworking parts of the tenoning machine are both vertical and horizontal. Along with cutters, saws can appear in this role.

Modifications of the pass-through type are predominantly double-sided and are suitable for creating a straight frame tenon. The eyelets will be formed together with it. All this is created simultaneously from both sides, which is extremely practical. The experience in the production of such equipment has been around for about 80 years. Modern double-sided walk-through machines work cleaner than their old prototypes and leave much less small chips and other deformations.
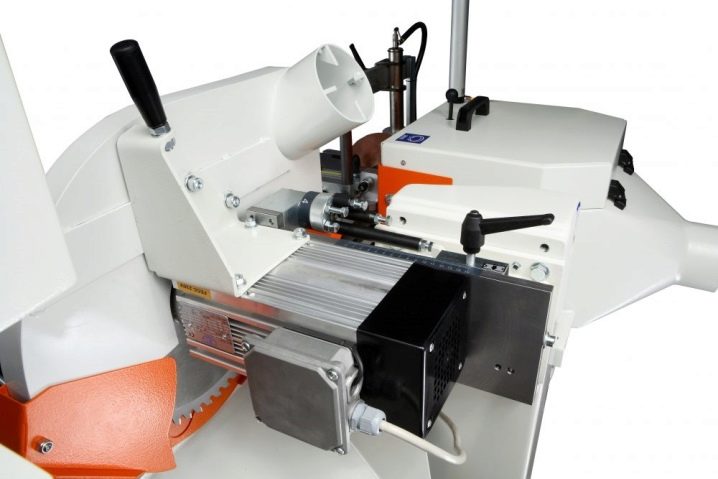
One way or another, but all options mill the spikes and the lugs intended for docking with them. The most basic difference is between box tenon machines and frame tenons. The technology of forming parts divides the technique into one-sided and two-sided formats. Models designed for a box spike can usually also make a "dovetail". They are mainly used in small and medium-sized manufacturing enterprises.
The tenoning machine for making beehives stands apart. In this case, straight spikes are produced in the same way.
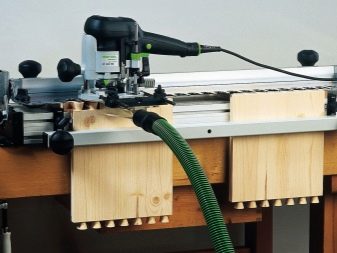
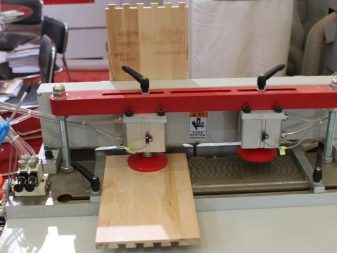
The placement of the push-on elements on the key is optional. As with conventional milling equipment, they simply need to be tightened. The distance between the cutting edges of the cutters is selected using a proven solution - gauge rings.
Other technical solutions may be used in the manufacture of chairs. They are based on the formation of an oval spine. The power of the devices and the number of revolutions developed differ significantly in different designs. The same technique can come in handy for working with blanks:
-
cabinets;
-
tables;
-
lunch groups;
-
other solid wood furniture.
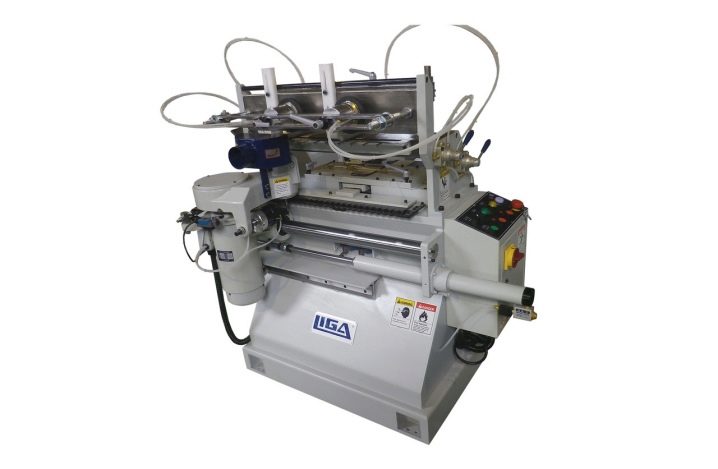
Most often, the heads have autonomous drives. Almost every manufacturer uses numerical control in their machine tools. Thanks to this option, it is possible to change the cutting part and set up the technological chain in a minimum of time. All single-sided models are positioned by default.
When the work piece passes under the cutter, the carriage will return the table to the starting point, the semi-finished product will flip over, and the machine will continue machining from the other side.
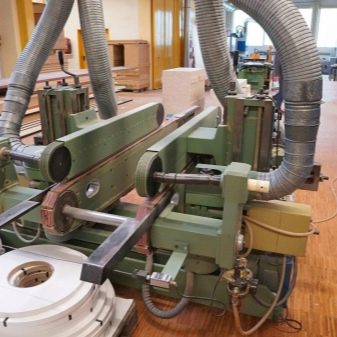
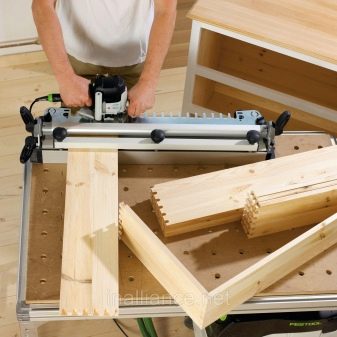
Double-sided (they are also positional-through) machines imply the supply of blanks with an unlimited chain conveyor with a lock. The system holds the processed semi-finished products well from both sides. Sawing is also done in two-sided mode. One of the working columns is rigidly fixed, while the other moves as needed. For this movement, guides are used; the system always adapts to workpieces of a certain length.
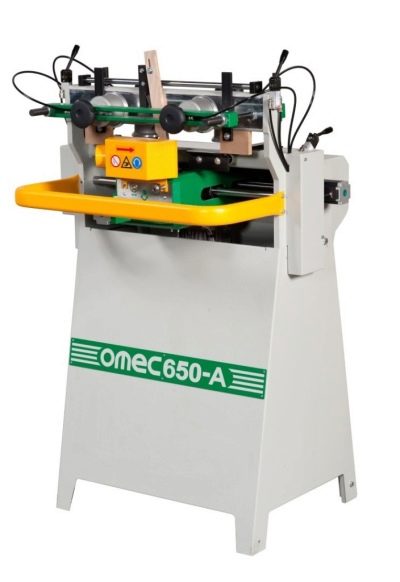
Top Models
Japanese is very popular. Makita 5500 S machine... The compact device has a program control unit. A pair of motors drives 2 pairs of saw blades. The cleanliness of the cuts and the speed at which they are cut can be flexibly varied. Manipulations with a tree of almost any length are possible.
Technical features:
-
network cable 5 m long;
-
diameters of discs - 23.5 and 18 cm;
-
thoughtful double insulation;
-
lack of a smooth start;
-
weight - 68 kg;
-
dust removal circuit;
-
the length of the spikes obtained is up to 9 cm.
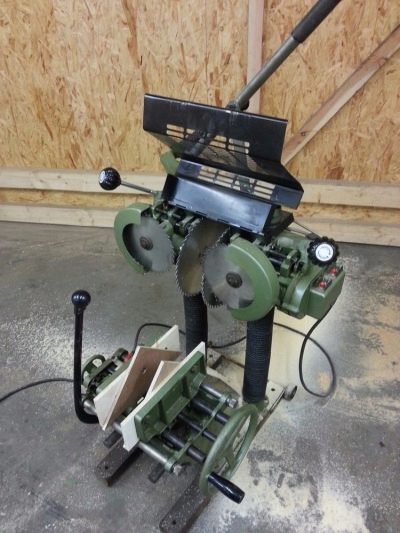
Chinese praise for power machine МХВ 3515 Сoperating on the basis of a hydropneumatic system. With this device, you can process the ends of the bars and cut the toothed spikes. Automatic glue application is also provided, which guarantees a reliable splicing. The machine is ideally designed for the production of first-class joinery and beams, as well as wooden panels.
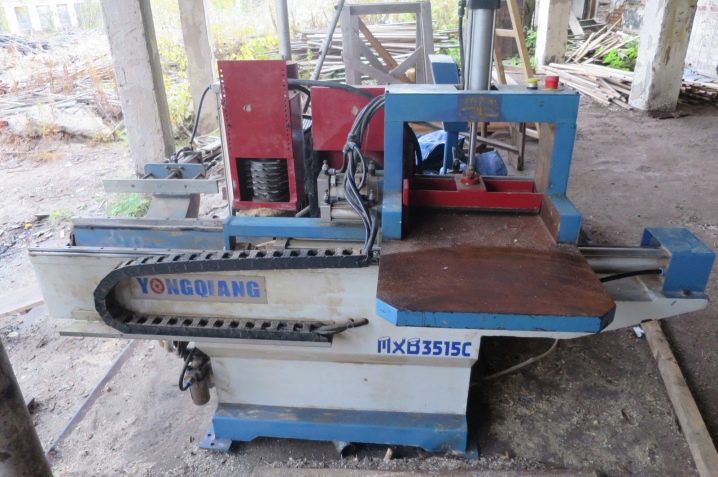
Choosing a double-sided tenoning machine, many prefer RH-826 AST... Its speed is infinitely variable, and a variator is used to change it. Overall, the system runs smoothly and reliably. The milling spindle rotates at 7200 turns per minute. Therefore, the quality of the material produced is beyond doubt.
The main components and assemblies are grouped compactly. Cast beds are powerful, which makes it possible to damp any vibration more efficiently. The length of the workpieces can vary from 50 to 180 cm, and their maximum width is 57 cm. The saw section is 25 cm. The saw support tilts up to 45 degrees, while the saws make from 3300 to 3650 revolutions per minute.
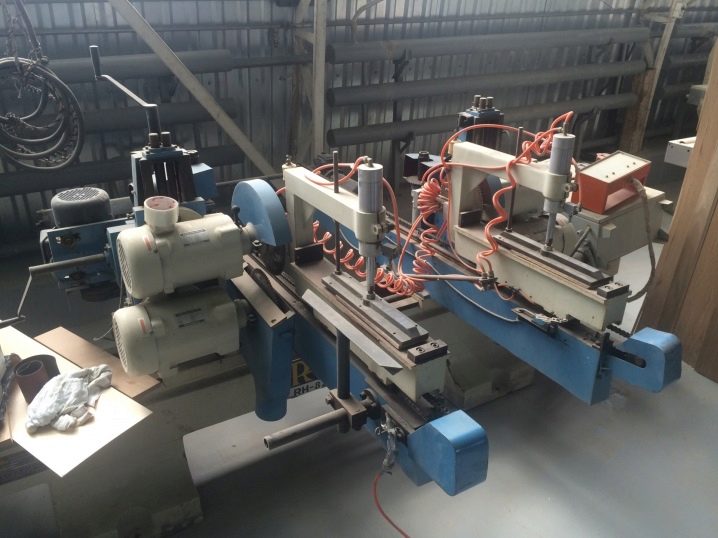
Feeding can take place at speeds of 5 - 30 m / min. The electric motors of the sawing shafts develop a power of 1.5 kW (each of 4). Both electric drives of the milling spindles have a power of 2.2 kW. The spindles themselves have a landing diameter of 3 cm. Their torsion will occur at a speed of at least 6600 revolutions, and the total mass of the apparatus is 1120/1300 kg, depending on the configuration.
Also worth looking at is the OMEC 650-A. Such a machine is well suited for box spikes. The greatest length of blanks is 150 cm, and their width is up to 40 cm.The apparatus producing spikes up to 1.6 cm in height has an electrical power of 1.75 kW. You can also make a "dovetail" on it.

Features of operation
Tenoning machines are best mounted on the ceiling. For this purpose, they are retrofitted with special clamping modules. Scoring saws help to take wood. The workpieces are fed to the miter saws, and the processing can be finished with a pair of removable milling cutters. By accelerating the rotation of the spindle, they achieve greater accuracy and higher quality of the resulting grooves.
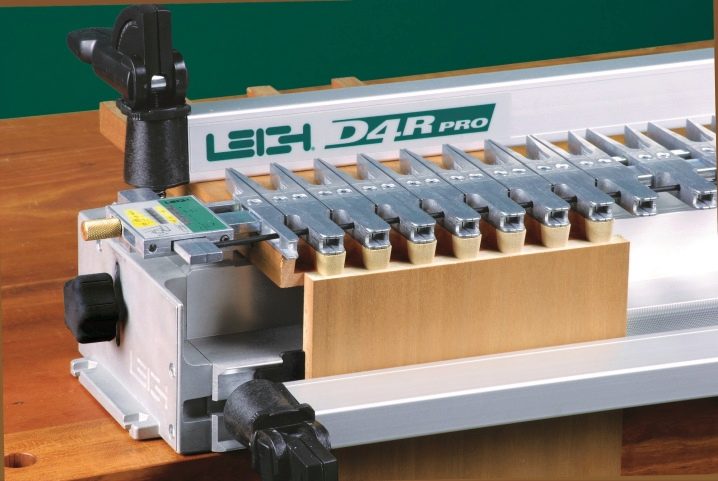
Correct installation of the saws on the spindles is very important. Reliable operation of assembled cutters, including lug discs, is ensured when assembled outside the machine. The cutters are mounted according to the template, strictly following the instructions. Before starting the device, it is necessary to assess the reliability of the fixation of the incisors; double-sided machines require precise installation of the movable pedestal.
The spindles are set up with a complete or incomplete template from a variety of materials; in any case, it must be significantly more accurate than the part being received.
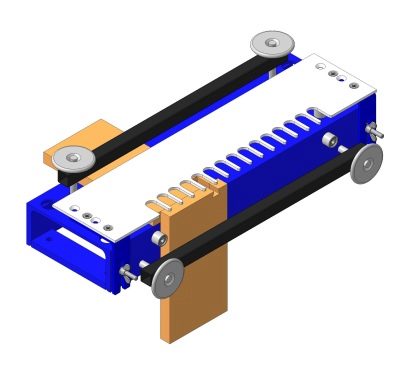
The comment was sent successfully.