Sheathing for corrugated board
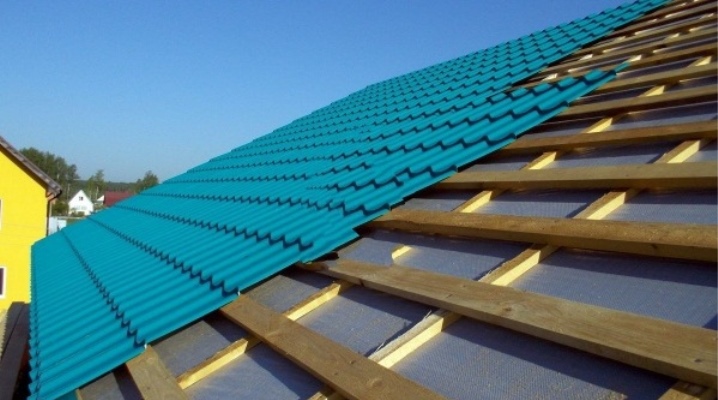
Profiled sheeting is a light, even material, comfortable to install, and therefore in demand. It is really easy to work with it, but only if you have chosen the correct fastening and competently prepared the base. The base is, among other things, the crate. If you make it not frequent enough, the sheets will bend, if you choose the wrong material for its construction, it will also not take out the corrugated board and will not be a quality base.
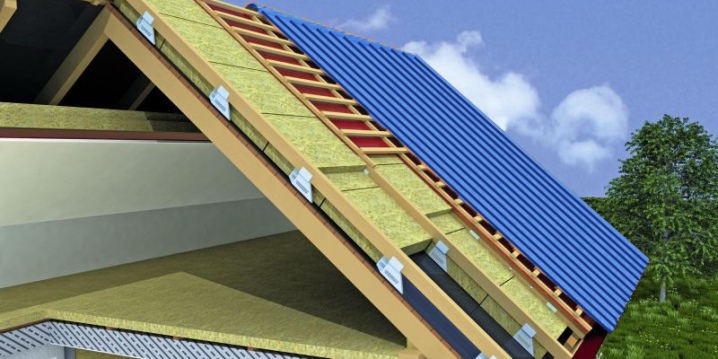
Peculiarities
The lathing has two main functions - to act as a base for fixing the finishing material, and also to be an interlayer between the waterproofer and the outer roofing layer. A special flooring forms a ventilation duct that does not allow the roofing sheet to aggravate its condition with condensate, undergo rotting and significantly reduce its service life.
The lathing for corrugated board is traditionally built of wood, but there are also options from metal or reinforced concrete slabs.
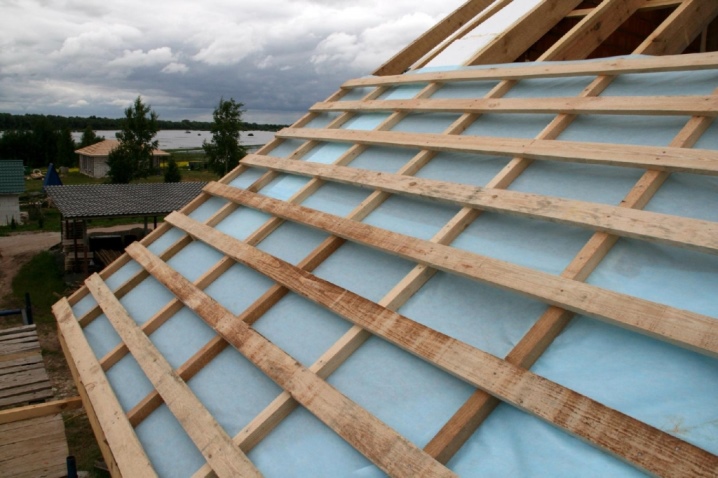
The metal structure is chosen if the corrugated sheets are thicker than 0.7 mm and if the slope of the slope is very small.
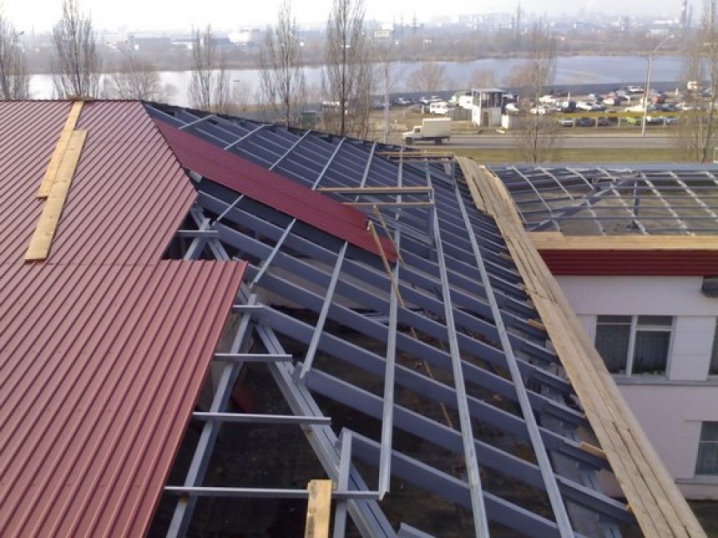
By the way, even before making calculations, you should navigate the brands of the material used, think over the slope of the roof. Snow and wind loads in the current region are certainly taken for consideration.
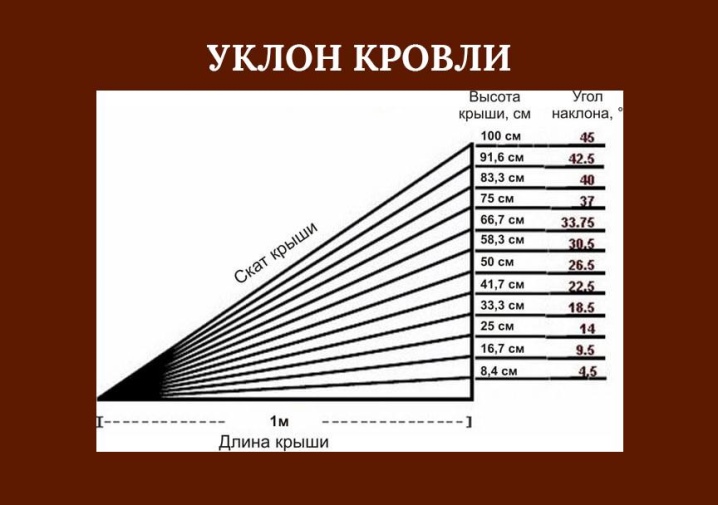
The lathing can be of two types.
- Wooden. For it, a timber or edged board of conifers is taken. It is almost always cheaper than metal structures, and easier to install.
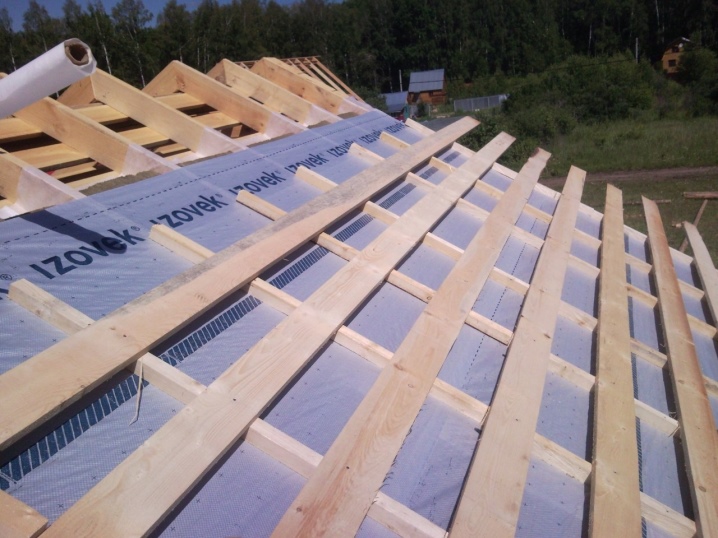
- Metallic. In terms of performance, it is in many ways better than wood - it helps to lower wind pressure, organizes free access to the elements of the roof, does not burn or rot, and has perfect smoothness.
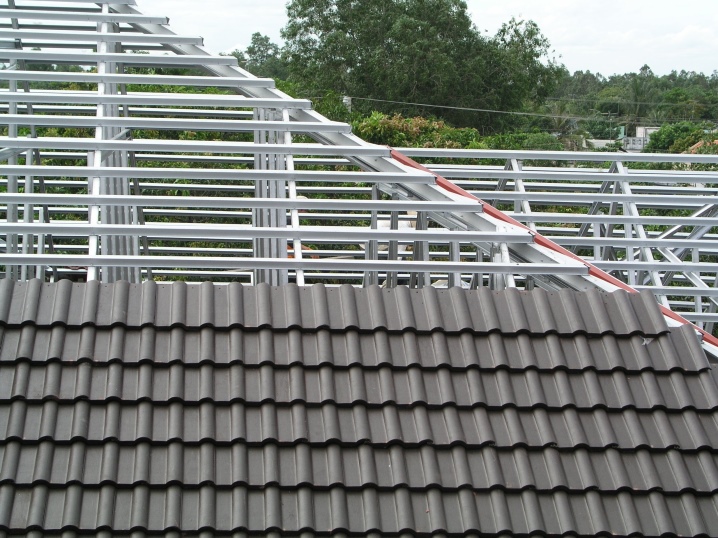
During the construction of the lathing, in addition to the slope of the roof, the wavelength and thickness of the future coating are determined in advance. The step of the crate will depend on this. Manufacturers of corrugated board are usually not lazy and note in the accompanying documents a list of requirements for laying the material. For example, in suburban construction, corrugated board with a profile having a height of 35 mm, made of steel sheet with a thickness of 0.7 mm, is usually preferable. And this material perfectly spreads on the crate, made up with a step of one and a half meters (taking into account the fact that the roof is designed for a load of up to 600 kg per square). This roof can be safely walked on during repairs or necessary cleaning.
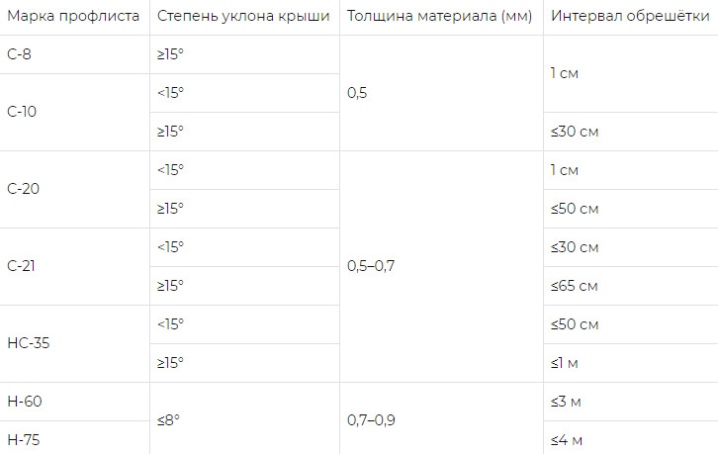
Flooring types
The device of a convincingly laid roof implies the use of different types of lathing: standard, sparse, simple. The choice of the type of frame depends on the climatic conditions of the region, the slope of the roof and, of course, the grade of the profile sheet.
Solid
Usually, this type of frame is made on roofs with a minimum slope of the slopes (up to 15 degrees). And this is taking into account the fact that profiled sheets of grades C8, C10 and C20 are used. Such material does not have a high degree of rigidity. The same type of lathing is used if you have to work on a problematic sector of the roof - for example, along the perimeter of dormers. The lathing helps to reinforce this structure.
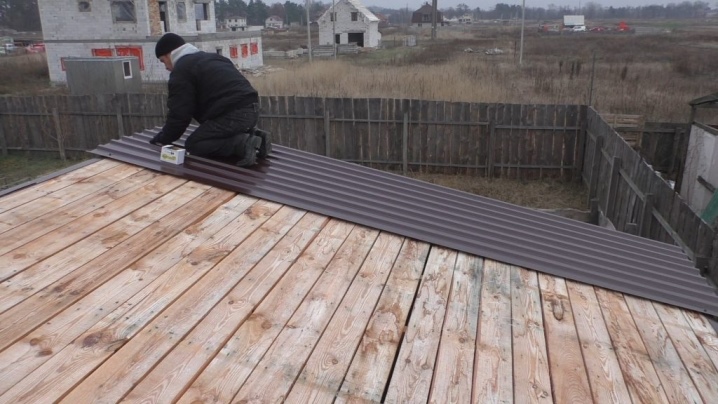
The step of the solid crate does not have a clear regulation. It is important to leave a sufficient gap, approximately 1 cm maximum, between adjacent boards. Why you need to maintain such a distance: the material tends to change size under the influence of thermal and humidity indicators.
If there is no such compensation gap, there is a risk of deformation of the tree, the consistency of the lathing will be at risk.
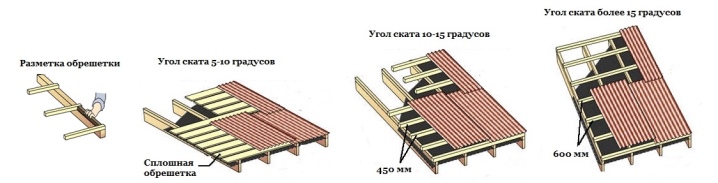
Sparse
This design is considered to be optimal for particularly rigid trapezoidal sheets marked HC-35 and above. For such a lathing, the step will be up to 1000 mm (but not less than 600). For a standard profiled sheet, such an interval is unacceptable, even if the roof is equipped with a rather big slope.
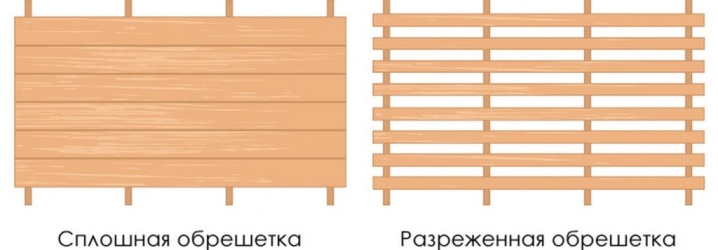
This type of lathing uses sawn wooden blocks and poles. The main requirement for them is a minimum moisture content, not higher than 20%, as well as in the absence of various kinds of deformations, knots and bends.
This crate must be treated with an antiseptic, or a fire retardant.
Besides, sparse type of flooring uses U-shaped galvanized profiles. This crate is equipped in one or two layers, but it is for the corrugated board that one layer is enough.
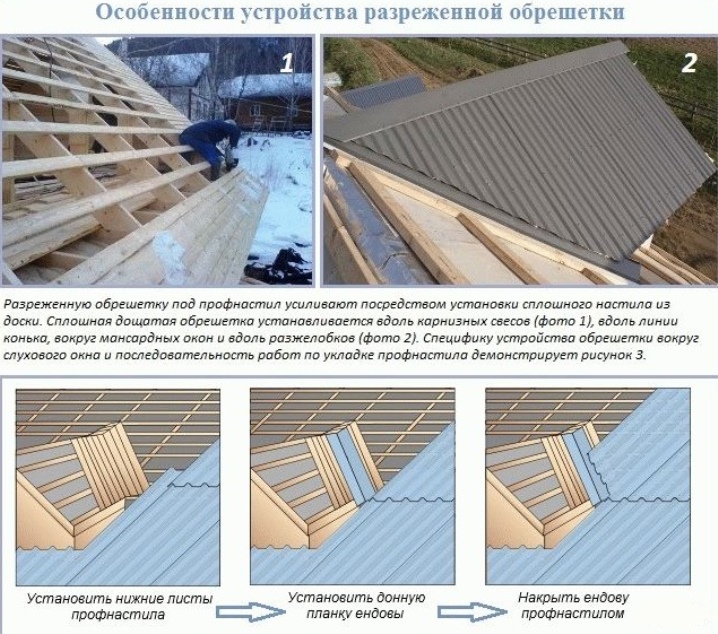
Normal
So they say about the crate, the frequency of the boards in which is from 200 to 500 mm. Such a frame type is used if you need to cover a roof that has a slope of 15 degrees. Used corrugated board C10, C20 and C21.
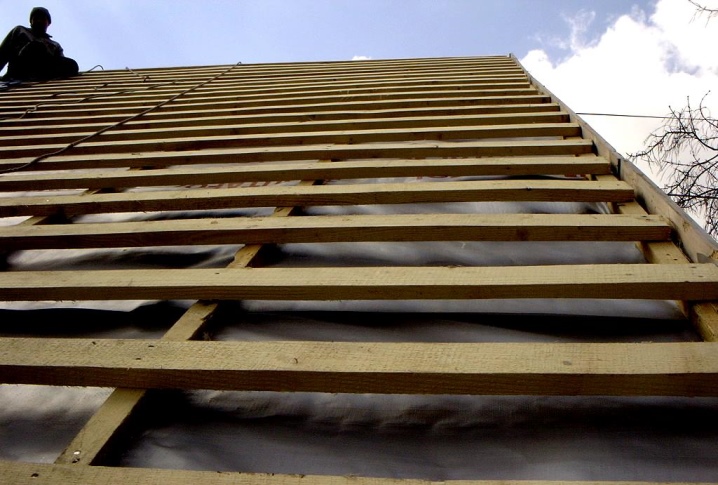
Calculation of materials
The device of a roof covering made of profiled sheets for a pitched, gable roof requires a high-quality calculation of the lathing interval, which depends on some factors.
- Climatic conditions. The choice of the ideal slope angle is based on current wind and snow hazards. The steeper the roof itself, the easier the snow will come off it, the water will leave (both from rain and melt). But for structures with a steep slope, and building materials, you will have to take more, that is, calculate the amount of materials for the new conditions. For example, a roof at an angle of 45 degrees will need one and a half times more lumber than a flat roof. In areas where there is a lot of snow during the season and little wind, steep roofs can be made. And where the winds are serious, it is better to make shallow roofs.
- Decrease the angle of inclination. Requires a reduction in the pitch between the lathing structures. If this is not done, the coating will bend after the first snowfall. A lot of snow accumulates on the flat roofs, and it, especially when wet, is definitely not lightweight. On a steep roof, the spacing can reach 900 mm, but the specific figures will depend on the marking of the corrugated board.
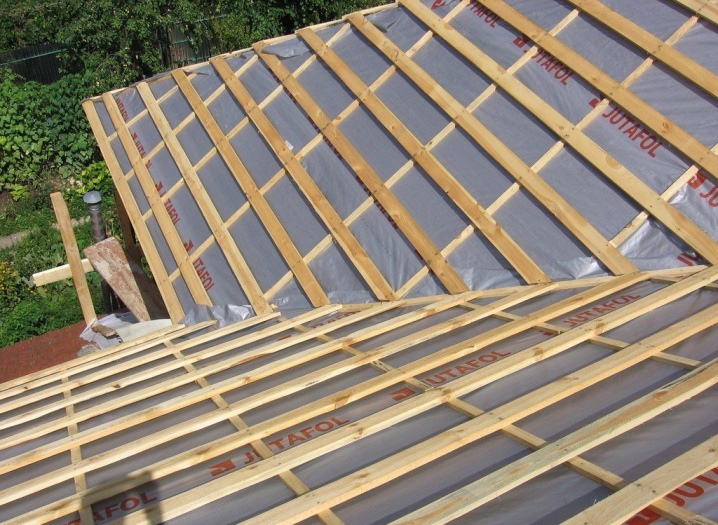
However, not everyone believes that step sizes should be seriously calculated. On some construction forums, craftsmen (often anonymous) assure that an experienced craftsman will do everything "by eye". But this is a dangerous path.
If you do not make calculations, the cost of the roof can simply be increased.
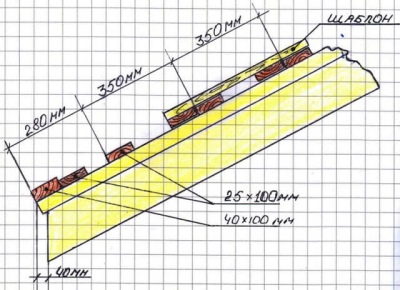
Finally, and more dangerous, the roof may not withstand the first serious snowfall, or even wind. And if such a roof needs repair, it will be problematic to move along it.
The rest of the calculations are hardly comparable with the numbers, they relate to calculations for the quality of the material - what to make the crate, so that it would not be very expensive, and there was no doubt about the strength of the structure. If this is a tree, then it is better to opt for oak, alder or spruce. The material should be perfectly dried, free from cracks, visually even and homogeneous. Before installing wooden elements, they are covered with special antiseptics and compounds that help to avoid rotting.
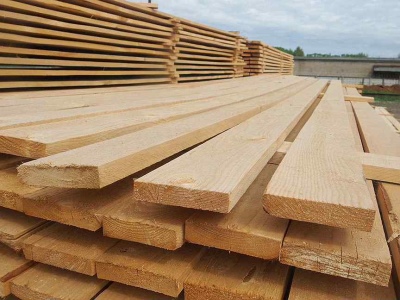
But in order to calculate how much of this high-quality tree is needed, you should rely on the width and length of the ramp, determining the step itself. And elementary mathematics is used. Do not forget that boards are also attached along the ridge and cornice, from which the step is counted. In the area of ventilators, pipes and other additional elements, the crate is necessarily reinforced.
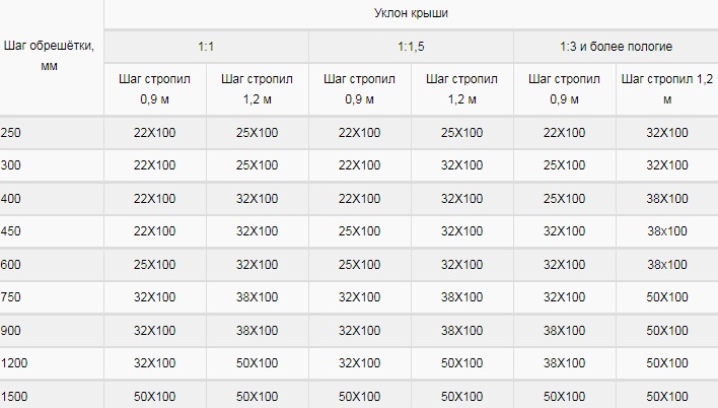
It is also important that the calculation of the amount of wood assumes a partial loss of material, which will be thrown away in the form of scraps. Therefore, about 15% of the spare material will have to be added to the already calculated amount of wood.
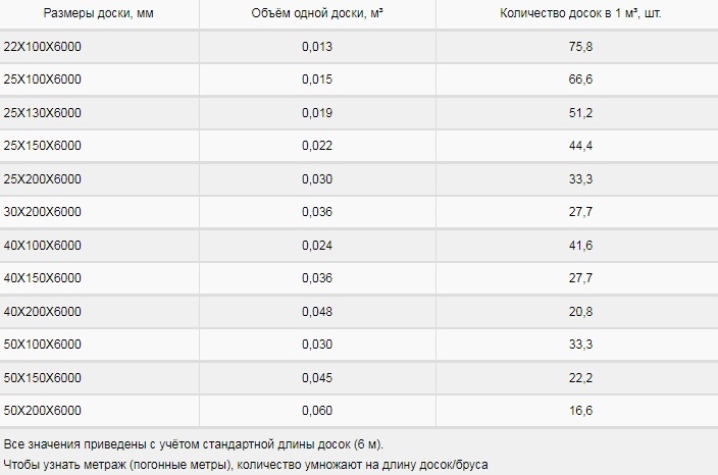
Mounting
The most important stage is installation.The installation of the lathing must first be “scrolled in the head”, that is, theoretically, to understand how the installation will take place, what parts it consists of. When the general outline is clear, it is easier to move on to practice.
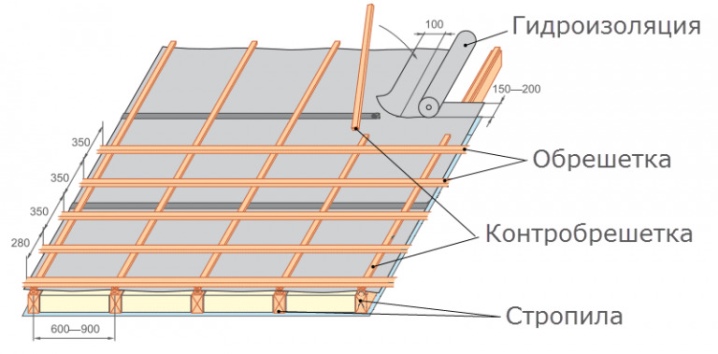
Do-it-yourself step-by-step instructions for installing the crate will help you with your work.
- Making calculations and purchasing materials. Accurate calculations will allow you to save money, not spend too much (both money and time for a potential rework). It is assumed to measure the width and length of the ramp, each of the measured values is divided by the selected interval of the crate. To the resulting amount, the material is added, which is to be used for the obligatory continuous sheathing in the chimney area and similar elements. The purchased material is treated with an antiseptic and moisture-repelling agents.
- Collection of the main elements of the frame. It is assumed that the ridge and the rafters are already in place - the crate and associated elements are already mounted on them.
- Laying waterproofing. This material is usually fixed with a construction stapler and staples.
- Fastening the bars to the rafters. These are 50 x 50 mm bars, due to which the ventilation gap is organized. It is needed precisely for the profiled sheet.
- Laying an additional waterproofing strip. It is laid in the ridge sector. A waterproofing strip will protect the ridge from water.
- Attachment of the hooks required for the installation of the drainage gutter.
- Installation of a counter-lattice. The fastening of the boards to the bars nailed in advance begins. Self-tapping screws are used for this. First, the elements are placed near the eaves, then, taking into account the calculated step, the remaining parts of the lathing are installed.
- Marking on bars. It is applied for convenience to indicate the pitch of the wooden lathing. However, you can also use twine.
- Fixing the boards. For this, nails or self-tapping screws are taken, their length is three times greater than the thickness of the sheathing board. If other fastener sizes are selected, wind load can be critical to the structure. But if the situation suggests that the crate should be spliced along the length, it is proposed to place the joints on the support (and it will be a bar). This is the same block that was previously fixed on the rafters. Experts advise against connecting two adjacent rows in parallel. This means that the joints should be staggered. These circumstances work for the reliability of the roof.
- Lathing bars are also fixed along the ridge part.
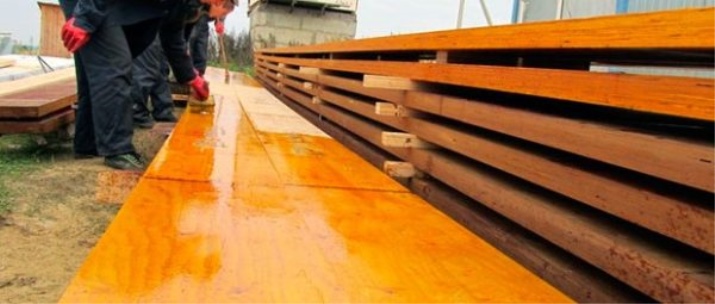
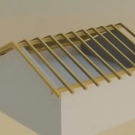
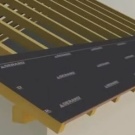
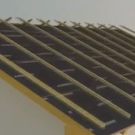
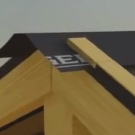
Expert advice can also be useful, which will help to competently save on the crate without deteriorating the quality of the future structure.
- A working section board should be used. And this is really beneficial: these boards are equal to the first grade sawn timber, but the cross-section is 5 mm less. That is, there will be more boards in one cubic meter, and, therefore, the savings on wood can be all 20%.
- Purchase sawing not in the high season. And this is also logical - at this time there is less demand for it, which means that you can count on decent discounts. And wood that has matured over the winter is considered convenient in sorting: damage and deformation are immediately evident.
- Buy materials in bulk, which is always cheaper. This applies to both rough and basic lumber.
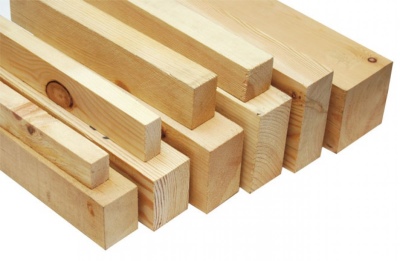
But buying boards of a lower grade is far from always profitable. Although the difference in price is tempting, a low-grade product requires further serious processing: it will need to be trimmed, all knots removed, and sanded. And these are also costly measures in terms of time, effort, and money.
It is necessary to resolve the controversial questions about the counter-lattice for corrugated board, because not everyone agrees that it is needed.
But experts advise not to abandon the counter grill.
Its need is due to a number of aspects.
- This kind of roof in particular requires a free flow of air.The counter-lattice laid on top of the waterproofing organizes the same ventilation passage, therefore, the roofing elements are protected from deformation and decay. The relevance of this information increases when it is decided to cover the roof with corrugated board with a low wave.
- Counter-rails manage to maintain waterproofing, prevent the material from sagging. The counter grill also helps the waterproofer to stay level, not to miss the proper tension level, and to do its job well.
- If the rafters are not processed well enough, counter-rails nailed along them will align the load-bearing roofing elements.
- Finally, this system will not give a chance to contact the waterproofer with the crate, which means that condensation accumulations that have come out of the insulation will drain into the drip without any problems. That is, there is no harm to the system and the isolator.
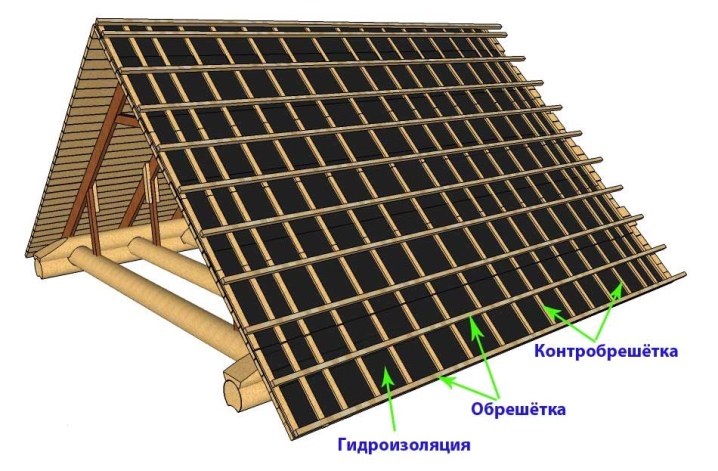
The counter lattice is laid without any particular difficulties. After the waterproofer is laid, slats are stuffed along the upper edge along the rafters (they are prepared in advance). The width of the bars is slightly less than the same parameter of the supporting rafters, and the thickness reaches 4 cm.The bars are harvested so that, according to the parameters of the slope height, they fall into 3 slats with an interval of 15-30 cm.
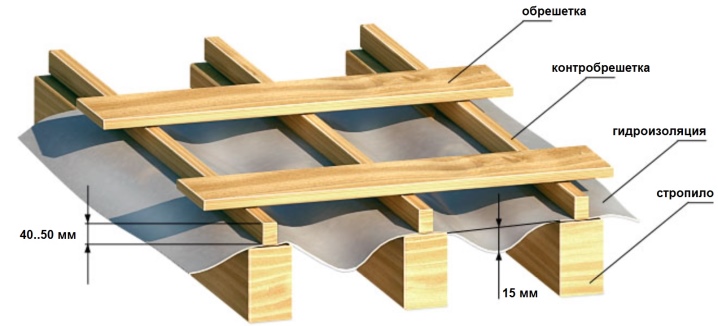
Fastening the profiled sheet
When the crate is finally built, it's time to fix the profiled sheet. To fasten the canvases, you will need special self-tapping screws based on a rubber gasket. How much fastener is required can be calculated in advance: there are at least 5 self-tapping screws per 1 square meter. Sheets are stacked from bottom to top, the upper canvas should literally cover the lower one along the edge.
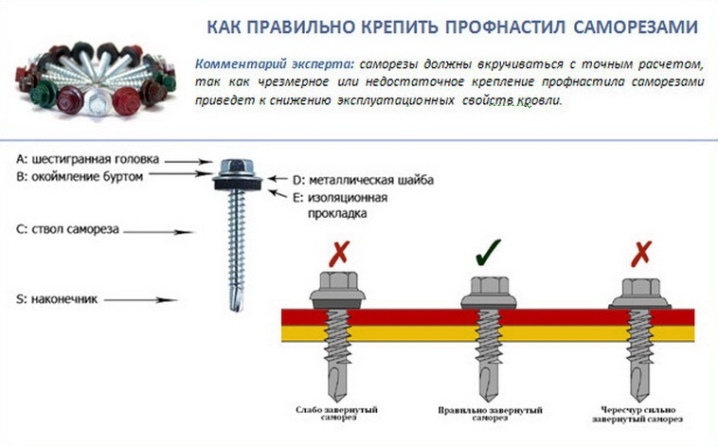
This is done so that excess water does not stagnate at the joints, but calmly flows from the roof.
What will be the width of the overlap is decided depending on the angle of the roof slope. Sheet joints must be treated with bituminous mastic, which provides the required waterproofing rate.
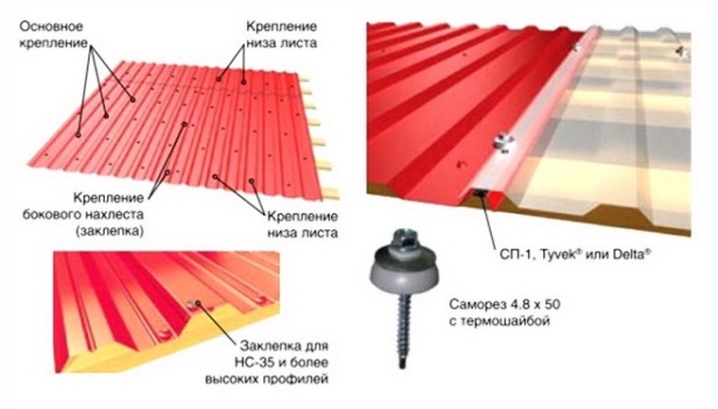
The fastening of the profile decking to the base assumes that the self-tapping screws will be screwed into the lower corrugation, in the overlap zones - into the upper one. It is necessary to fasten it at longitudinal joints in order to protect the structure from wind breakdown, and in order to level the roof. However, the roof must be visually uniform.
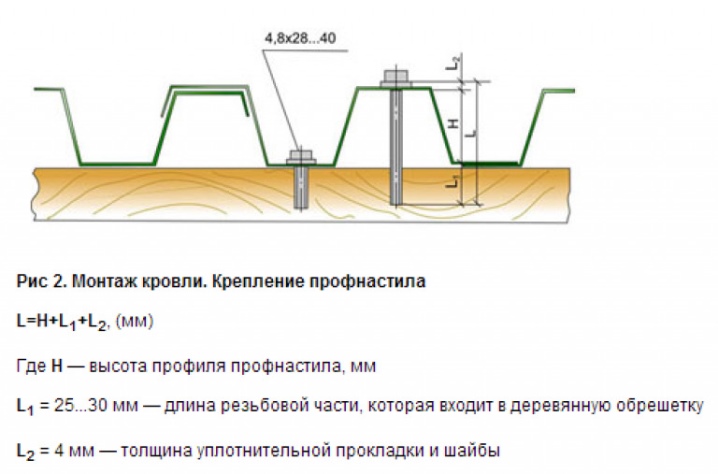
If the metal option is chosen, fixing the sheet can be a little difficult. And the point is in the characteristics of the metal itself. It should be recalled that it is advisable to take exclusively profiles with a metal thickness of no more than 2 mm for the lathing, if the metal is thicker, the load on the rafter structure will be excessive. Hence the conclusion on the self-tapping screws: they have a drill at the end that allows them to be screwed into the metal without creating holes only when its thickness is not higher than 2 mm. So that the process is not infinitely time-consuming, it is possible to fasten the corrugated board only to such a "lightweight" metal crate. The rest of the options (with a thicker metal profile) are not only not very correct to use, but also dangerous.
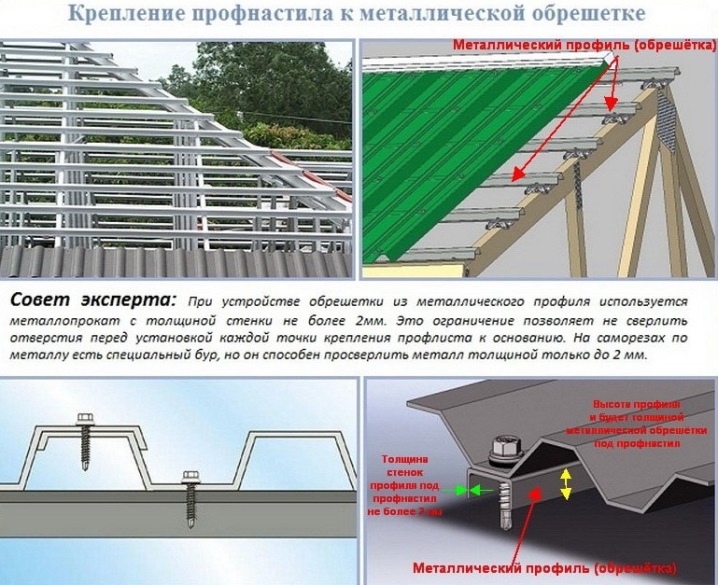
The fasteners also have their own requirements: if the sealing gaskets with which the self-tapping screws are equipped dry up and crack, the roof will leak. Therefore, you should purchase branded fasteners with a brand stamp on the head. Doubtful self-tapping screws can result in a loss of quality for the entire structure of the lathing with a fixed profiled sheet.
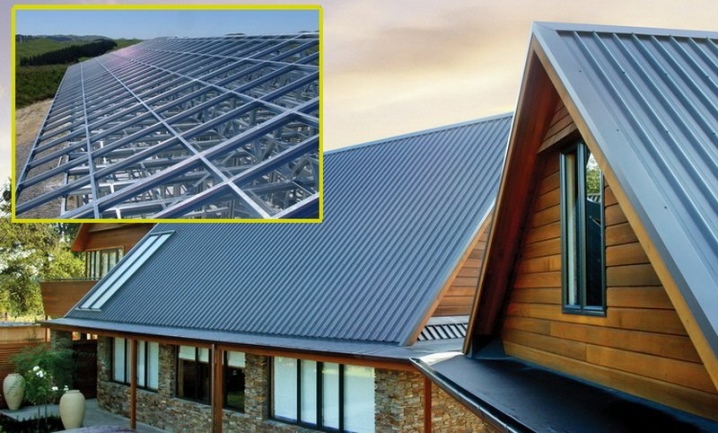
How to make a crate for corrugated boarding, you will learn in the next video.
The comment was sent successfully.