End profiles for polycarbonate
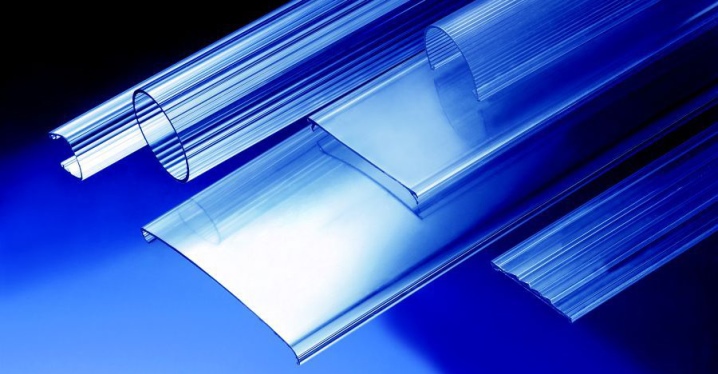
Every year new technologies appear in the field of construction, modern modular systems of structures from high-quality raw materials with optimal characteristics and operation are being developed. Among them, in the first positions is polycarbonate (durable plastic). The article will discuss the end profiles for its installation.
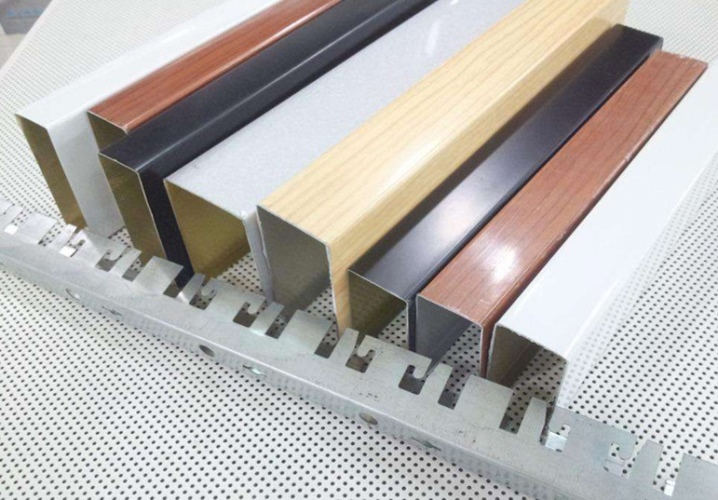
What is it and why is it needed?
Various structures are made from polycarbonate: trade pavilions, balcony sheds, canopies for entrances, garden, farm greenhouse and greenhouse structures, exhibition galleries, frames of bus stops and station complexes, hangars for cars and many other structures.

This translucent (transparent) material has moisture resistance, excellent strength and light weight, while at the same time it protects against ultraviolet radiation and radiation. When installing polycarbonate sheets, special accessories are used, including end (side) UP-profiles.
A profile is a cross-sectional shape of a rolled product. Construction profiles are used for joining materials in different planes and have protective and decorative functions. They cover the cylindrical or rectangular transverse face of the projected object.
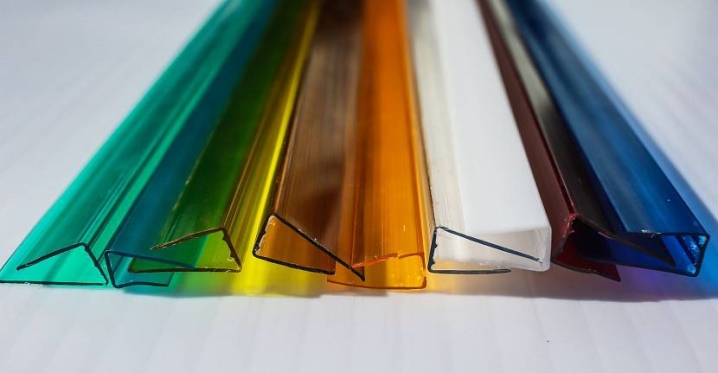
The construction of polycarbonate is rack-and-pinion; slats or honeycombs with grooves are used. The end profiles close the formed cavities of the panels during joining, seal them, ensure the drainage of condensate from the cavities and allow you to create complex projects of structures. In addition, the components are widely used in advertising, design art and other fields.
The service life of the components varies from 5 to 20 years.
Varieties
There are many varieties, which, depending on the purpose, are attached to a smaller or larger face of a polycarbonate sheet. Conventional UP-profiles are produced in widths that are multiples of 2.1, that is, 2.1, 4.2 and 6.3 meters. The end profile for polycarbonate UP-4, -6, -8, -10 is produced in packs of 50 units, UP-16 - 30 units.
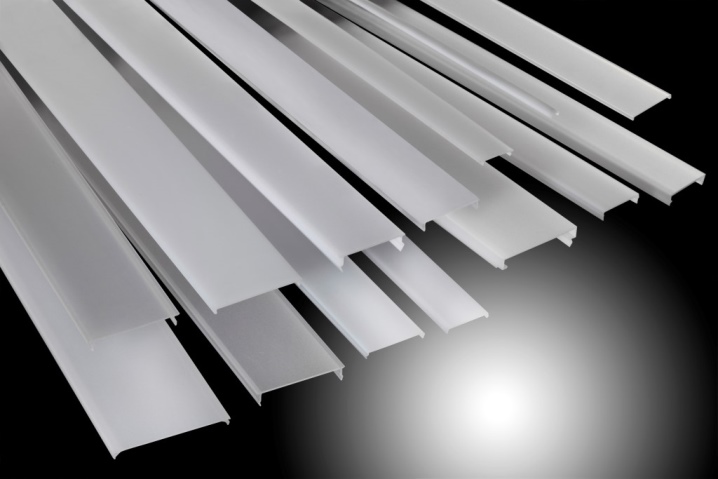
Polycarbonate is divided into monolithic, honeycomb and cast. Produced in sheets of different thickness from 4 to 10 mm, 16 and 25 mm, weighing from 0.8 to 1.7 kg according to GOST R 567-2015.
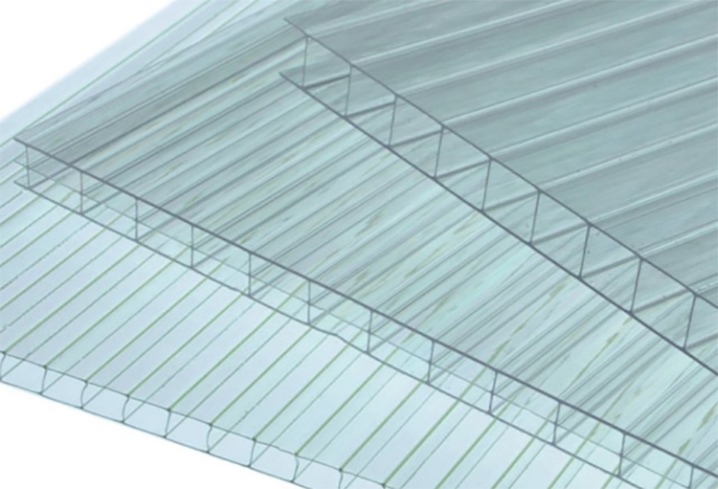
End profiles for polycarbonate are most often composed of aluminum and polycarbonate. The range of colors is varied: white, blue, yellow, red, green, bronze and chrome, colorless transparent colors are available depending on the basic tone of the building material. Today, profiles compatible with cellular polycarbonate panels are produced both in color and in the following technical characteristics:
- operation at low and high temperatures;
- impact resistance;
- cold bending radius;
- thermal expansion.
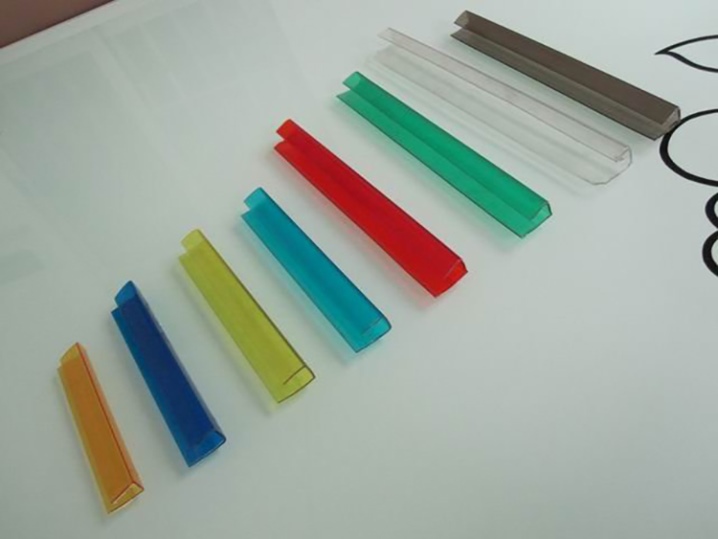
The characteristics of profile fasteners include the cross-sectional shape, weight, geometric dimensions, wall thickness and length.
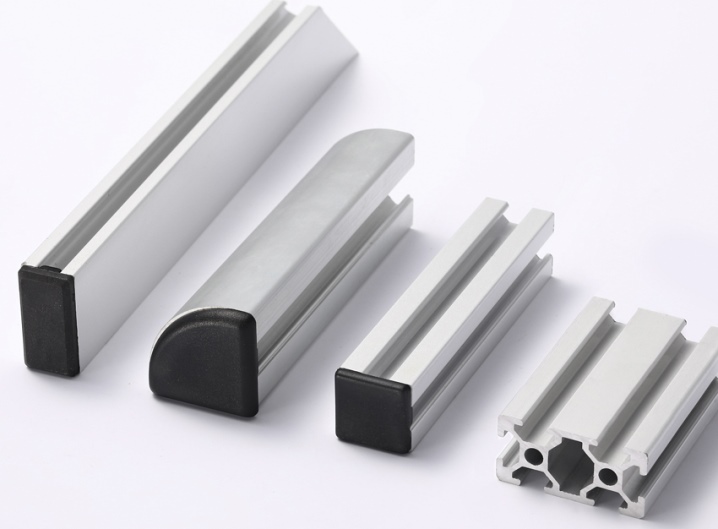
Several standard types of profiles are produced:
- end profiles with a thickness corresponding to polycarbonate;
- closing aluminum with rubber seal 3.5 and 4 mm;
- mortise aluminum for plate 18 mm;
- for cellular polycarbonate panels with a thickness of 4 and 6 mm;
- profile for an invoice tape 8-10 mm;
- polycarbonate profile (U-shaped section) for 8 mm panels; 10 mm and 16 mm with standard 2100 mm width.
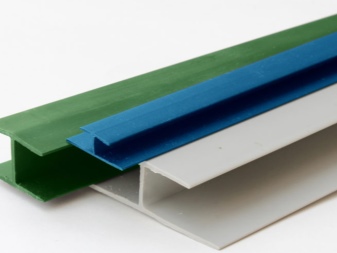
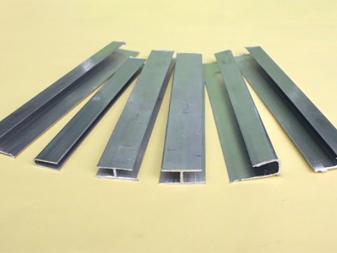
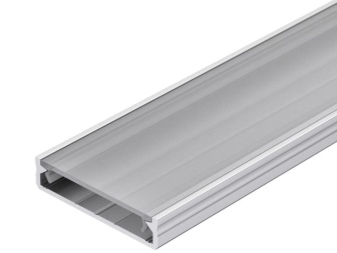
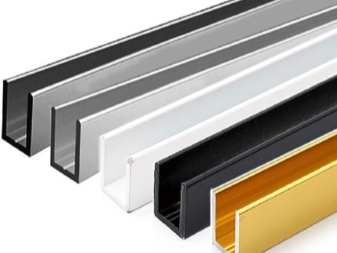
Aluminum profiles with rubber seals are used for covering heated rooms and large architectural structures with panels from 16 to 25 mm thick: these are swimming pools, covered gazebos, sports facilities.
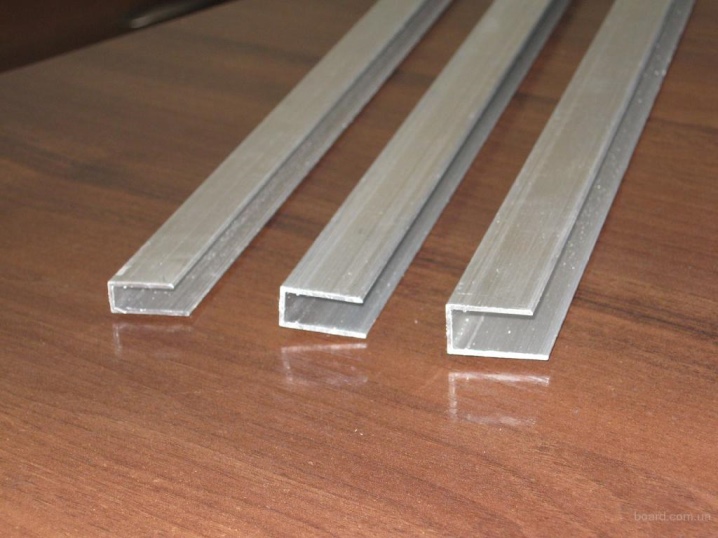
The more robust aluminum end profile is mounted in monolithic panels with a size of 8-25 mm. Installation is carried out with fasteners (self-tapping screws) with a diameter of 20 mm with a thermal washer made of metal, sometimes polycarbonate. Through-fastening of parts with a distance of 500 mm between them; 800 mm applied to panels with a thickness of 8-10 mm; 16 mm.
The advantages of these options are:
- aluminum is not subject to corrosive effects and ultraviolet burnout;
- hermetically combines with polymers;
- easy to paint;
- easy to assemble and dismantle;
- the end profile for polycarbonate does not need to be glued or use any other additional fixing.
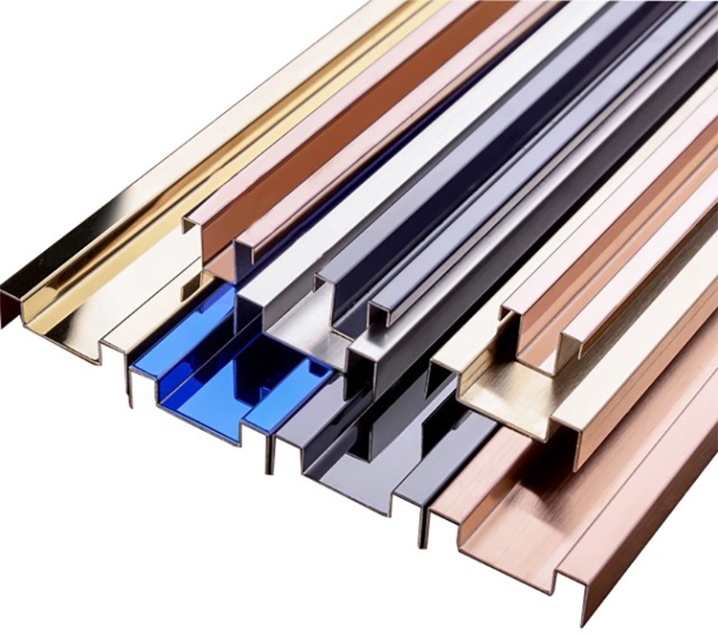
Installation
The installation diagram of polycarbonate sheets using end profiles is indicated by the manufacturer on the outside of the building sheet, on a protective shipping film, and you can also check it with the seller of the goods.
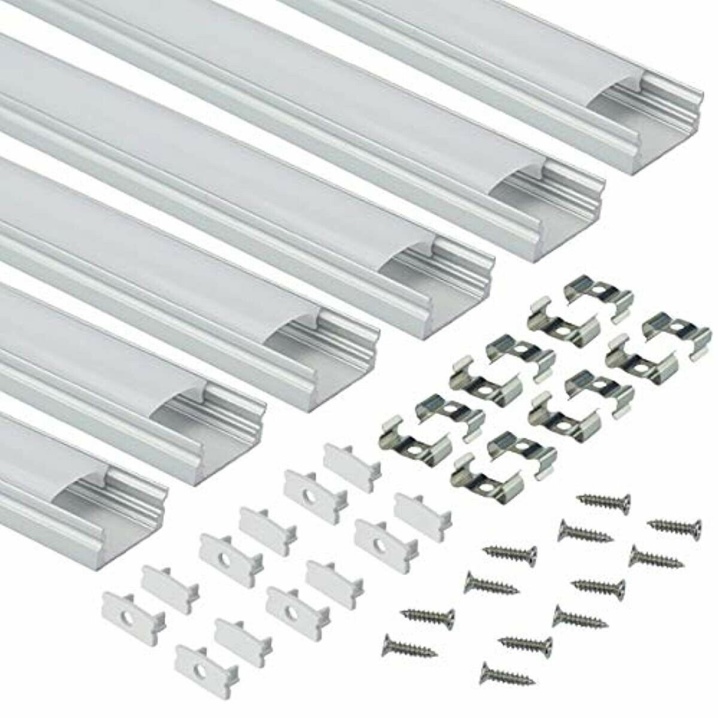
In order to correctly install and reliably mount the structure, you must act in the prescribed manner:
- lay the cellular polycarbonate on the supporting base, fasten it with self-tapping screws and fix it with a thermal washer;
- the sheets are connected from above and below with a detachable profile, closed with a lid and a roofing screw;
- then the end profile of the required length is measured and cut off with a non-sharp knife, the ends are cleaned to a smooth state;
- from the end side of the polycarbonate, it is imperative to glue a sealing tape to the sheet at the top, and perforated at the bottom (with a pitched, front and arched arrangement of the object);
- holes are made in the profile for the outflow of condensate with a step of 30-40 mm;
- fix the sealant symmetrically relative to the middle of the end, then the profile, which is securely put on the edge of the panel;
- should be fixed with a small margin between the inner wall and the end (3 mm);
- leave a clamp of the edge of the honeycomb polycarbonate sheet in the profile of 15-17 mm;
- for connection of monolithic panels use an aluminum connecting end profile, clamping the edge of the sheet at least 20 mm.
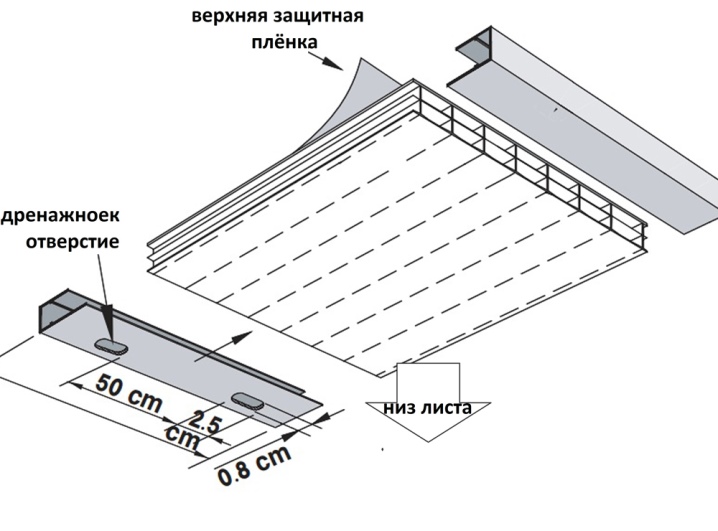
Note! Cutting a profile, like polycarbonate, is carried out using a circular saw - "grinder", "parquet", hand jigsaw, electric jigsaw or metal scissors, a mild knife at the recommended angle of inclination of 30 degrees.
The process of installing end profiles for polycarbonate in the video below.
The comment was sent successfully.