Everything you need to know about profiled polycarbonate
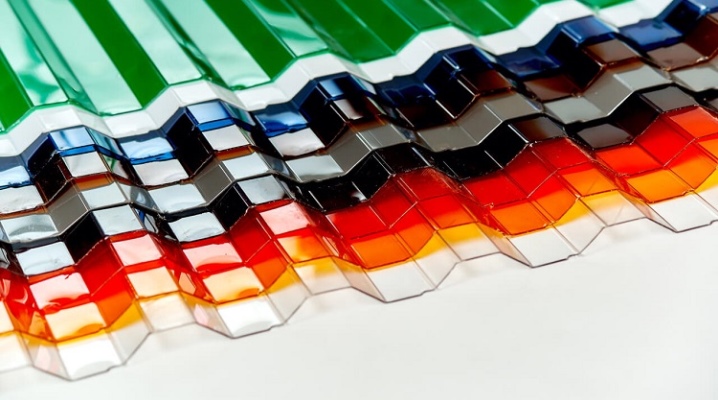
Profiled polycarbonate is a practical building material, in recent years it has been replacing traditional glass everywhere. It is distinguished by high technical and operational properties, durability and aesthetic appearance. The material is widely used in private housing construction and agriculture.
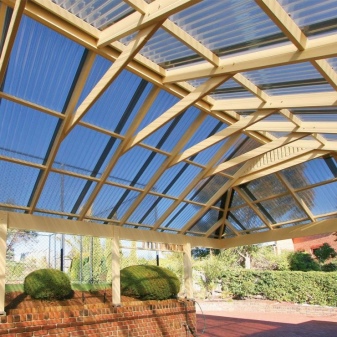
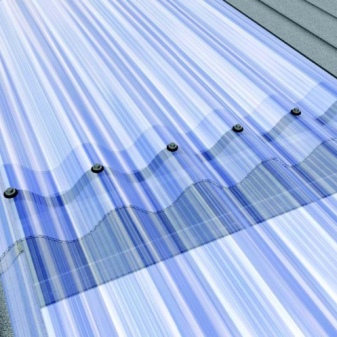
Peculiarities
Profiled polycarbonate is a technologically advanced building and finishing material. It is the result of the interaction of carbonic acid with bisphenol A, it is produced by extrusion, and then the surface is given a corrugated profile. Like a monolithic polymer, it contains no hollow cells in its structure. According to the parameters of light transmission, such polycarbonate is divided into transparent, translucent, and also matte.
The technical and operational parameters of this polymer are in many ways superior to traditional glass. With its low weight, it has high strength, impact resistance and increased load-bearing capacity.
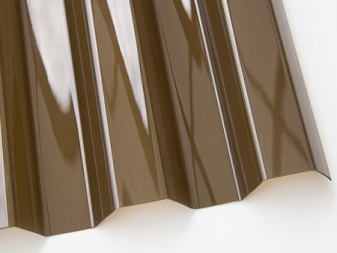
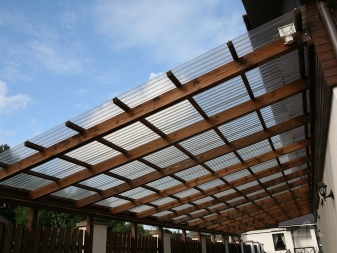
The exceptional custom parameters of the polymer have allowed it to completely replace silicate glass in a wide variety of construction areas. Today polycarbonate is widely used as a roofing and facade material. He has many virtues.
- Light weight. Polycarbonate for roof structures is 2-3 times lighter than silicate glass. Moreover, its weight is less than that of acrylic glass of the same thickness.
- Impact resistance. The impact resistance of the polymer is 150 times higher than that of simple glass and almost 10 times that of acrylic. Profiled polycarbonate is often called "anti-vandal material" and is widely used for the installation of outdoor infrastructure objects - bus stops, billboards and road signs. It is quite difficult to destroy such structures.
- Plastic. Polycarbonate boards are flexible, they are suitable for creating complex architectural forms without the use of heat treatment.
- Light permeability. The light transmission parameter of corrugated polycarbonate corresponds to 80-93%, depending on the thickness of the product. According to this indicator, it almost reaches the level of silicate glass and significantly surpasses acrylic glass.
- Ease of installation. The material is easy to process, and its compact dimensions allow you to perform all installation work quickly.
Of the minuses, we can note the low resistance to ultraviolet radiation, which causes wear of the polymer after 4-6 years. However, modern manufacturers have established the production of premium products - it assumes the presence of a film that blocks the negative effects of sunlight. Such material can last up to 20 years.
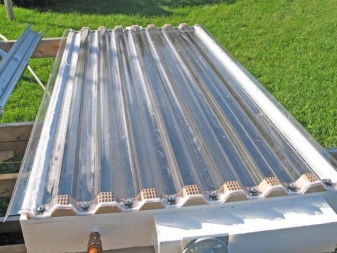
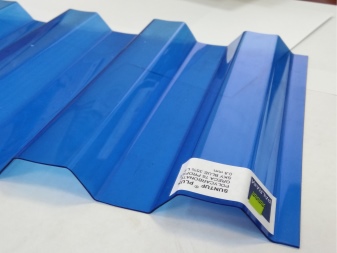
Species overview
Several versions of profile polycarbonate are produced, depending on the section parameters.
- Wavy (wavy) - its surface looks like slate, that's why this material is called "plastic slate" in everyday life.
- Trapezoidal - a similar polycarbonate has a trapezoidal profile, it looks like a profiled sheet.
- U-shaped - in the shape of the profile, it can also be compared with corrugated board, but it has reinforced stiffeners. Due to this, the bearing capacity of such a material increases many times over.
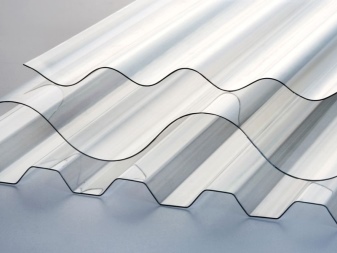
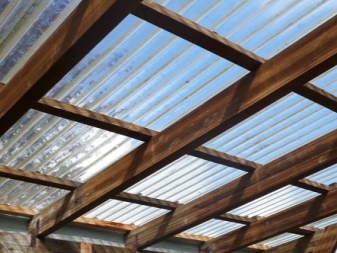
According to the level of transparency, the following types are distinguished:
- completely translucent;
- partially transparent;
- transparent colored;
- matte color;
- matt white.
As for the shade solution, corrugated polycarbonate is available in white, creamy, yellow, bronze, orange, red, garnet, terracotta, as well as blue, turquoise, green and purple.
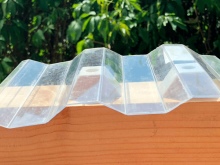
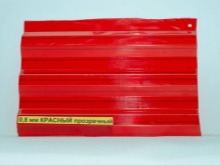
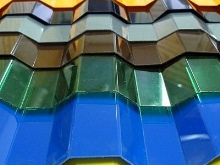
Dimensions (edit)
On the construction market, you can find several dozen different shapes and sizes of profiled polycarbonate. By thickness, this material is divided into several types:
- thin - 0.8-1 mm;
- medium - 1-1.5 mm;
- thick - 1.6-2 mm.
The width of one layer varies from 480 to 1870 mm for different profiles. The higher the sheet, the greater the cross-sectional parameters. For lightweight roofs, canopies and extensions to buildings, sheets with a length of 1.5-3 meters are usually used. If you install a roof with a small number of joints, then you can purchase sheets and 6-11 meters each.
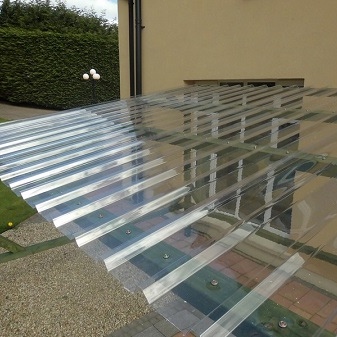
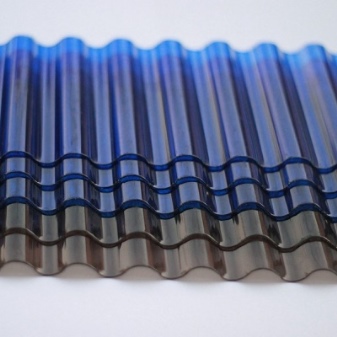
Manufacturers
Initially, profiled polycarbonate came to the domestic consumer from abroad, mainly from Germany and Israel - these countries are considered pioneers in this industry. Today the material is widely produced in our country. At least 20 plants and factories operate in this area in Russia. The most famous is POLYGAL - the Russian representative office of an Israeli firm.
The most popular of the large enterprises is Yug-Oil-Plast, which produces polycarbonate under the BORREX trademark. The high demand for the products is due to the exceptional quality of the products combined with low prices. Today the plant has more than a dozen production lines, thanks to which profile polycarbonate from this manufacturer can be found in any geographic region of Russia.
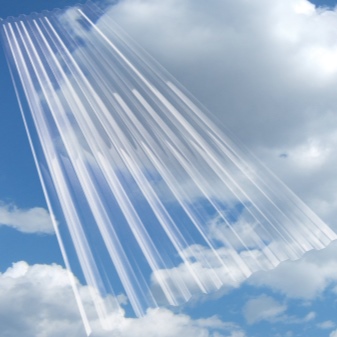
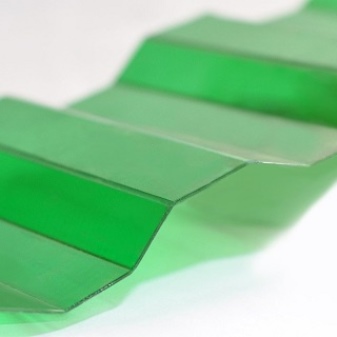
Although most manufacturers use roughly the same equipment, the difference in finished product quality can be quite dramatic. For example, the "Plastikalux-Group" factory gives a guarantee of up to 15 years for certain categories of its products, which is twice the generally accepted one.
Some manufacturers create polycarbonate exclusively from primary raw materials - polycarbonate granules (most often these are granules of the German manufacturer BAYER), others are trying to reduce the cost of products and purchase cheap blanks from Chinese companies, such polymers are extremely short-lived.
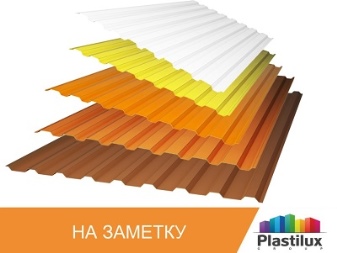
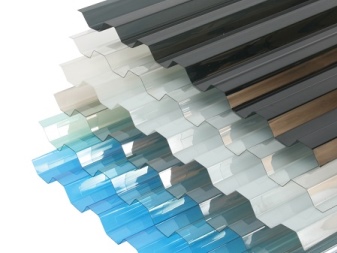
Nuances of choice
Nowadays, shops offer a wide range of various profiled polycarbonate boards. To choose the right material, first of all, you should pay special attention to the mass of the sheet - it should be less than that of glass structures. In addition, high quality polycarbonate must necessarily have good light transmission and evenly scatter the sun's rays. When cold, the sheets can be bent to the desired shape without the risk of damage. Properly manufactured polycarbonate is fireproof, withstands strong wind and snow loads, is shock resistant and does not change its characteristics in high and low temperatures.
Carefully inspect the purchased product - there should be no dents, scratches or chips on it. Air bubbles, irregularities and delamination are not allowed. Stiffeners should be located at an even right angle, the presence of waviness indicates non-compliance with the production technology.
It is desirable that the polycarbonate is covered with a protective film that neutralizes the effect of ultraviolet radiation. Such measures allow many times to increase the service life of sheets, prevent a change in shade, deformation and deterioration in the quality of the material.
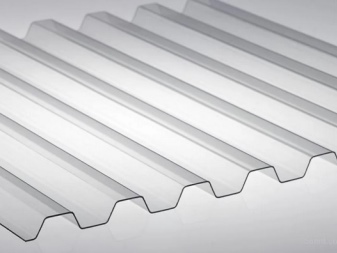
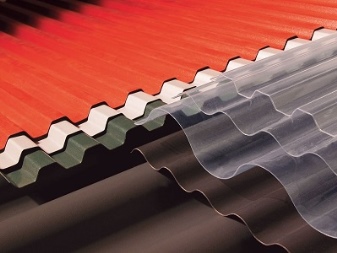
Applications
Profiled polycarbonate is lightweight and thin. This leads to the fact that many homeowners consider the material not strong enough. However, this is nothing more than a deceptive impression. Thin is not necessarily fragile.For example, ondulin is also lightweight and plastic, nevertheless it is widely used for roofing installation, and its service life exceeds 10 years.
Corrugated polycarbonate is widely used in a wide variety of applications. It has established itself as a quality and practical material.
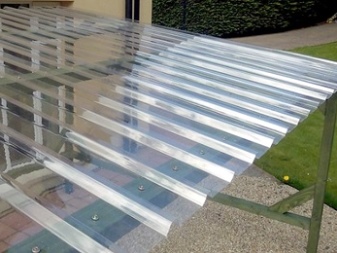
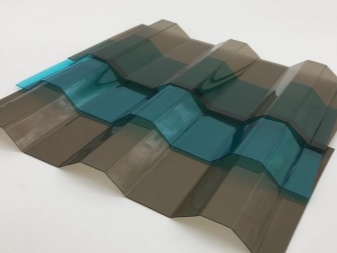
Industrial
In industry, corrugated polycarbonate is used in several directions at once:
- strip skylights;
- translucent pitched roof inserts;
- roof structures of industrial buildings of 1-3 categories of complexity;
- windows of shedovy lanterns.
The relevance of the material is due to the fact that a translucent polymer roof 2 mm thick increases the natural illumination of work structures by 50-65%. Thanks to this, you can minimize the cost of electricity and space heating. The installation of profiled polymer becomes a profitable investment that can pay off within 2-3 years.
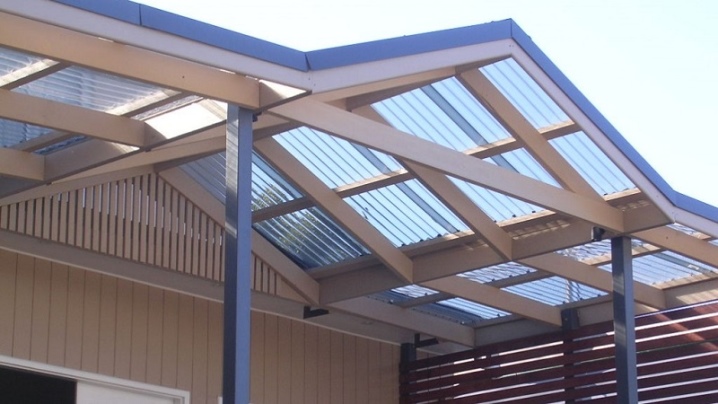
In private housing construction
The main area of application of corrugated polycarbonate is housing construction. First of all, it is used for the installation of canopies, awnings, open verandas, terraces and garden gazebos. However, the scope is not limited to this. Corrugated polycarbonate is widely used for the construction of fences, fences, installation of street fences and outdoor cafes. Polycarbonate has become widespread in the decoration of building facades. The walls of the building made of corrugated polycarbonate and sandwich panels do not require additional installation of window frames.
Nowadays, the material is in demand when decorating the walls of factories, factories and industrial workshops.
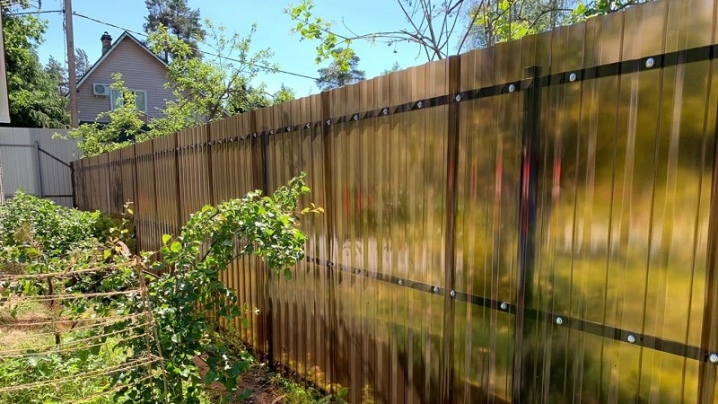
In agriculture
Due to the high throughput capacity, translucent profiled sheets have found their application in agriculture. They are used to equip greenhouses, hotbeds, greenhouses. However, wavy polycarbonate holds heat worse than cellular polycarbonate, so only cold-resistant plants can be grown in such structures. Heat-loving ones begin to lag behind in development, and this leads to a deterioration in yield parameters.
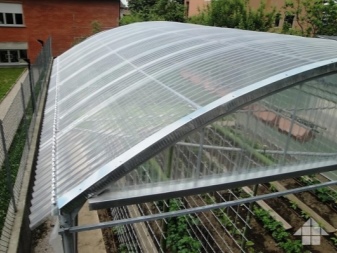
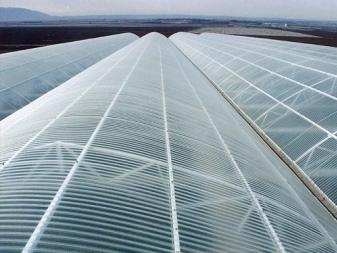
In animal husbandry
Corrugated polycarbonate is also used in animal husbandry. It is suitable for the device of a light-transmitting roof in chicken coops; it is used to construct skylights in pig farms and cowsheds. Translucent inserts multiply the natural insolation of livestock zones by 1.5 times, thereby increasing the profitability of an agricultural enterprise. This is evidenced by the well-known fact: to maintain high egg production in chickens, it is necessary to maintain a daylight hours in the hen house for at least 12-14 hours. A corrugated polycarbonate roof 1.5-2 mm thick copes with this task with ease. In bright rooms, the egg production of poultry increases to 200-250 eggs per year.
A sufficient level of illumination leads to a rapid weight gain of pigs, up to 250 kg, and also increases the milk yield of cows to 45 liters per day.
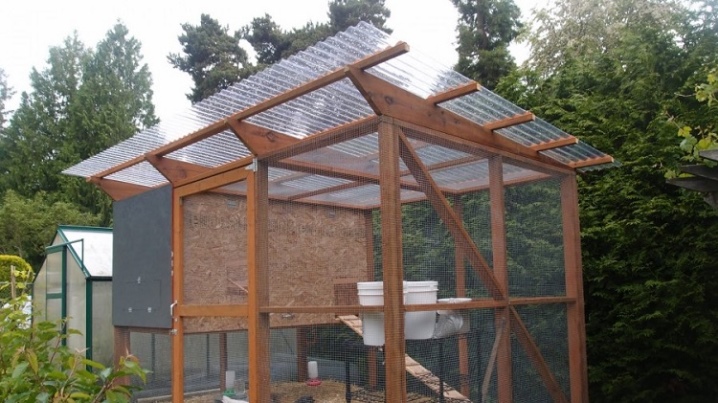
Installation rules
A small instruction on how to install corrugated polycarbonate with your own hands will help you do everything right. In order for it to fully cope with its functions, you should adhere to the rules for its installation and further use:
- the first step is to determine how many sheets you need;
- the material should be laid on the slope in long strips, parallel to the gable roof slats;
- only one where the overlap is about 9 percent of the width of the sheet can be considered a reliable joint;
- the width of the sheet also affects the step of the lathing, you can focus on the recommendations of the manufacturers or make a decision yourself;
- bending of sheets for the manufacture of an arched structure is allowed;
- to cut the panel, it is best to take a grinder and work at low speeds;
- polycarbonate should be fastened with self-tapping screws or bolts; thermal washers are used for fastening to the metal frame;
- when carrying out installation work, you should be extremely careful - if you press on the sheet at the wrong angle, it will break.
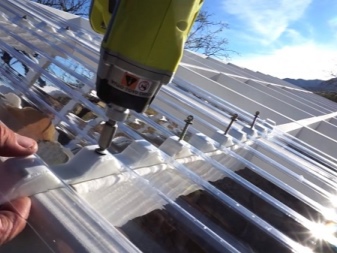
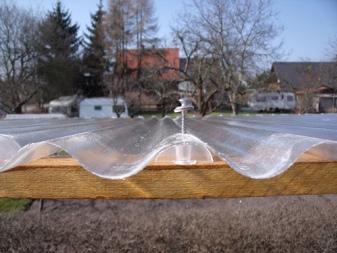
In the next video, you will find a short overview of Borrex profiled polycarbonate.
The comment was sent successfully.