Sizes of polycarbonate sheets
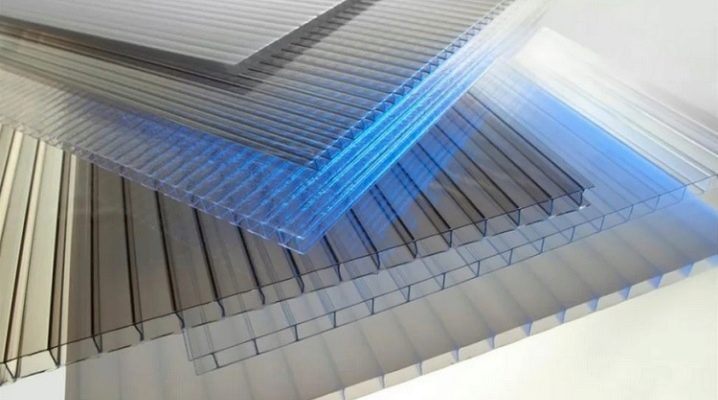
Polycarbonate is a modern polymer material that is almost as transparent as glass, but 2-6 times lighter and 100-250 times stronger.... It allows you to create designs that combine beauty, functionality and reliability.
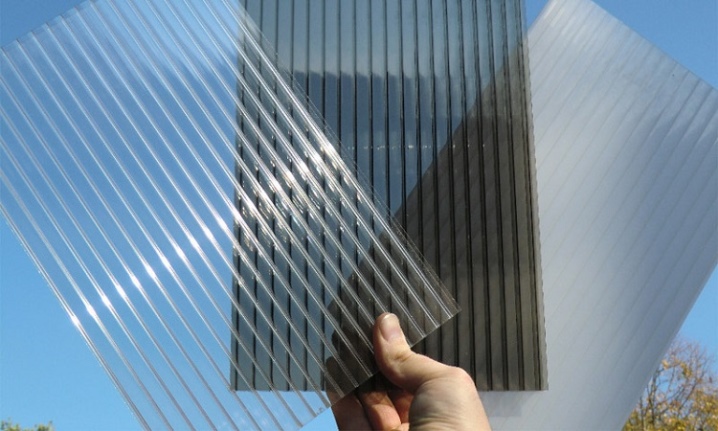
These are transparent roofs, greenhouses, shop windows, building glazing and much more. For the construction of any structure, it is important to make correct calculations. And for this you need to know what the standard dimensions of polycarbonate panels are.
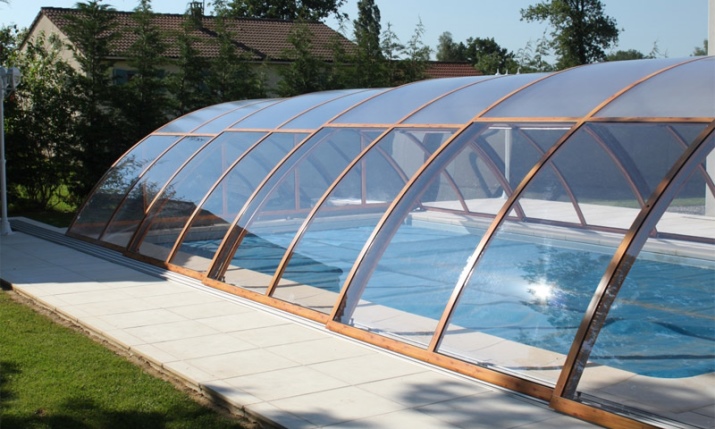
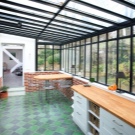
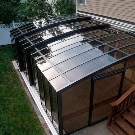
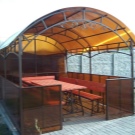
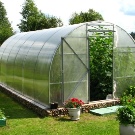
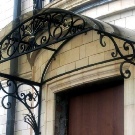
Dimensions of honeycomb sheets
Cellular (other names - structural, channel) polycarbonate are panels made of several thin layers of plastic, fastened inside by vertical bridges (stiffeners). Stiffeners and horizontal layers form hollow cells. Such a structure in the lateral section resembles a honeycomb, which is why the material got its name. It is the special cellular structure that endows the panels with increased noise and heat-shielding properties. It is usually produced in the form of a rectangular sheet, the dimensions of which are regulated by GOST R 56712-2015. The linear dimensions of typical sheets are as follows:
- width - 2.1 m;
- length - 6 m or 12 m;
- thickness options - 4, 6, 8, 10, 16, 20, 25 and 32 mm.
The deviation of the actual dimensions of the material from those declared by the manufacturer in length and width is allowed no more than 2-3 mm per 1 meter. In terms of thickness, the maximum deviation should not exceed 0.5 mm.
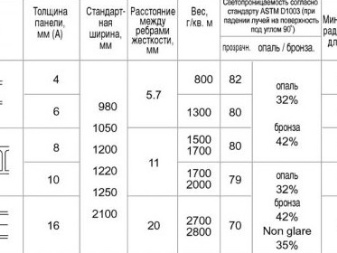
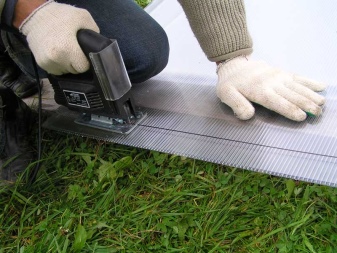
From the point of view of the choice of material, the most important characteristic is its thickness. It is closely related to several parameters.
- Number of plastic layers (typically 2 to 6). The more of them, the thicker and stronger the material, the better its sound-absorbing and heat-insulating properties. So, the sound insulation index of a 2-layer material is about 16 dB, the coefficient of resistance to heat transfer is 0.24, and for a 6-layer material these indicators are 22 dB and 0.68, respectively.
- The location of the stiffeners and the shape of the cells. Both the strength of the material and the degree of its flexibility depend on this (the thicker the sheet, the stronger it is, but the worse it bends). Cells can be rectangular, cruciform, triangular, hexagonal, honeycomb, wavy.
- Stiffener thickness. Resistance to mechanical stress depends on this characteristic.
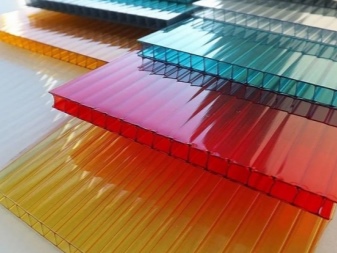
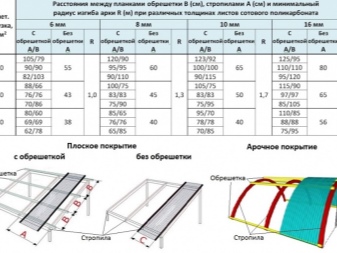
Based on the ratio of these parameters, several varieties of cellular polycarbonate are distinguished. Each of them is best suited for its tasks and has its own typical sheet thickness standards. The most popular are several types.
- 2H (P2S) - sheets of 2 layers of plastic, connected by perpendicular bridges (stiffeners), forming rectangular cells. The jumpers are located every 6-10.5 mm and have a cross-section from 0.26 to 0.4 mm. The total material thickness is usually 4, 6, 8 or 10 mm, rarely 12 or 16 mm. Depending on the thickness of the lintels, sq. m of material weighs from 0.8 to 1.7 kg. That is, with standard dimensions of 2.1x6 m, the sheet weighs from 10 to 21.4 kg.
- 3H (P3S) Is a 3-layer panel with rectangular cells. Available in thickness 10, 12, 16, 20, 25 mm. The standard thickness of internal lintels is 0.4-0.54 mm. The weight of 1 m2 of material is from 2.5 kg.
- 3X (K3S) - three-layer panels, inside of which there are both straight and additional inclined stiffeners, due to which the cells acquire a triangular shape, and the material itself - additional resistance to mechanical stress in comparison with sheets of the "3H" type.Standard sheet thickness - 16, 20, 25 mm, specific weight - from 2.7 kg / m2. The thickness of the main stiffeners is about 0.40 mm, the additional ones - 0.08 mm.
- 5N (P5S) - panels consisting of 5 plastic layers with straight stiffening ribs. Typical thickness - 20, 25, 32 mm. Specific gravity - from 3.0 kg / m2. The thickness of the inner lintels is 0.5-0.7 mm.
- 5X (K5S) - 5-layer panel with perpendicular and diagonal internal baffles. As a standard, the sheet has a thickness of 25 or 32 mm and a specific weight of 3.5-3.6 kg / m2. The thickness of the main lintels is 0.33-0.51 mm, inclined - 0.05 mm.
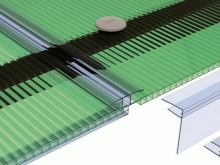
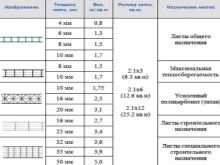
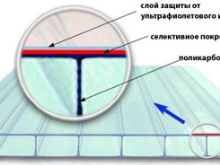
Along with standard grades according to GOST, manufacturers often offer their own designs, which may have a non-standard cell structure or special characteristics. For example, panels are offered with higher impact resistance, but at the same time lighter in weight than standard options. In addition to premium brands, there are, on the contrary, variants of the light type - with a reduced thickness of the stiffeners. They are cheaper, but their resistance to stress is lower than that of typical sheets. That is, grades from different manufacturers, even with the same thickness, may differ in strength and performance.
Therefore, when buying, this must be taken into account, clarifying with the manufacturer not only the thickness, but all the characteristics of a particular sheet (density, thickness of stiffeners, type of cells, etc.), its purpose and permissible loads.
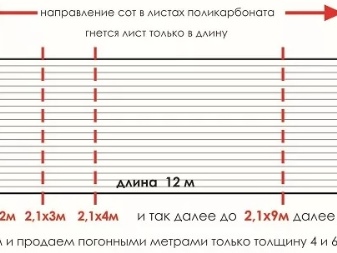
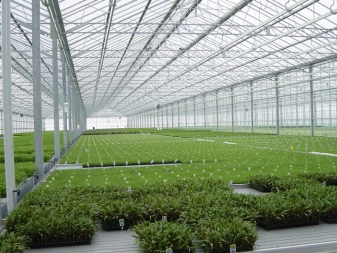
Dimensions of monolithic material
Monolithic (or molded) polycarbonate comes in the form of rectangular plastic sheets. Unlike honeycomb, they have a completely homogeneous structure, without voids inside. Therefore, the density indicators of monolithic panels are significantly higher, respectively, higher strength indicators, the material is able to withstand significant mechanical and weight loads (resistance to weight loads - up to 300 kg per sq. M, shock resistance - 900 to 1100 kJ / sq. M). Such a panel cannot be broken with a hammer, and reinforced versions from 11 mm thick can withstand even a bullet hit. Moreover, this plastic is more flexible and transparent than structural. The only thing in which it is inferior to the cellular one is its heat-insulating properties.
Monolithic polycarbonate sheets are manufactured in accordance with GOST 10667-90 and TU 6-19-113-87. Manufacturers offer two types of sheets.
- Flat - with a flat, smooth surface.
- Profiled - has a corrugated surface. The presence of additional stiffening ribs (corrugation) makes the material more durable than a flat sheet. The shape of the profile can be wavy or trapezoidal with the height of the profile (or wave) in the range of 14-50 mm, the length of the corrugation (or wave) from 25 to 94 mm.
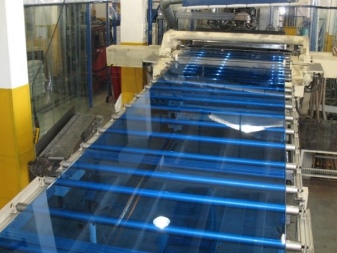
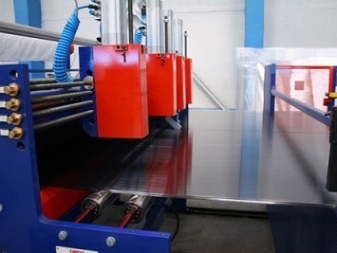
In width and length, sheets of both flat and profiled monolithic polycarbonate from most manufacturers comply with the general standard:
- width - 2050 mm;
- length - 3050 mm.
But material is also sold with the following dimensions:
- 1050x2000 mm;
- 1260 × 2000 mm;
- 1260 × 2500 mm;
- 1260 × 6000 mm.
The standard thickness of sheets of monolithic polycarbonate in accordance with GOST is in the range from 2 mm to 12 mm (basic sizes - 2, 3, 4, 5, 6, 8, 10 and 12 mm), but many manufacturers offer a wider range - from 0.75 up to 40 mm.
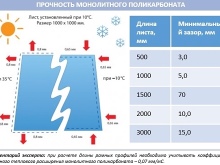
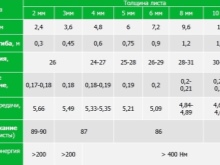
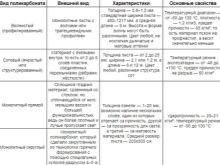
Since the structure of all sheets of monolithic plastic is the same, without voids, it is the size of the cross-section (that is, thickness) that is the main factor affecting the strength (whereas in a cellular material, the strength is strongly dependent on the internal structure).
The regularity here is standard: in proportion to the thickness, the density of the panel increases, respectively, the strength, resistance to deflection, pressure, and fracture increase. However, it must be taken into account that along with these indicators, the weight also increases (for example, if 1 sq. M of a 2-mm panel weighs 2.4 kg, then a 10-mm panel weighs 12.7 kg). Therefore, powerful panels create a large load on structures (foundation, walls, etc.), which requires the installation of a reinforced frame.
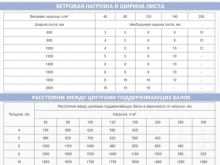
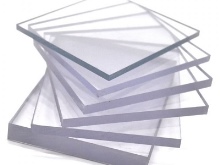
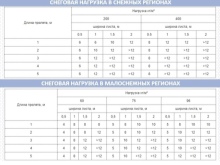
Bending radius with regard to thickness
Polycarbonate is the only roofing material that, with excellent strength indicators, can easily be formed and bent in a cold state, taking an arched shape. To create beautiful radius structures (arches, domes), you do not have to assemble a surface from many even fragments - you can bend the polycarbonate panels themselves. This does not require special tools or conditions - the material can be molded by hand.
But, of course, even with a high elasticity of the material, any panel can be bent only to a certain limit. Each grade of polycarbonate has its own degree of flexibility. It is characterized by a special indicator - bending radius. It depends on the density and thickness of the material. Simple formulas can be used to calculate the bend radius of standard density sheets.
- For monolithic polycarbonate: R = t x 150, where t is the sheet thickness.
- For a honeycomb sheet: R = t x 175.
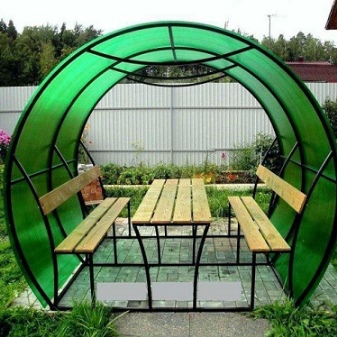
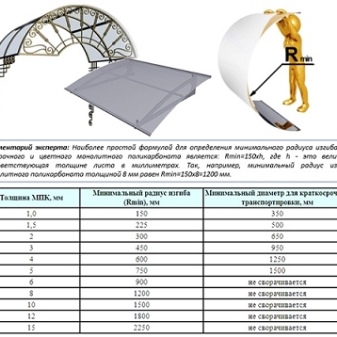
So, substituting the value of the sheet thickness of 10 mm into the formula, it is easy to determine that the bending radius of a monolithic sheet of a given thickness is 1500 mm, structural - 1750 mm. And taking a thickness of 6 mm, we get values of 900 and 1050 mm. For convenience, you can not count each time yourself, but use ready-made reference tables. For brands with non-standard density, the bending radius may differ slightly, therefore, before buying, you must definitely check this point with the manufacturer.
But for all types of material there is a clear pattern: the thinner the sheet, the better it bends.... Some types of sheets up to 10 mm thick are so flexible that they can even be rolled into a roll, which greatly facilitates transportation.
But it is important to remember that rolled polycarbonate can be kept for a short time; during long-term storage, it should be in a flattened sheet form and in a horizontal position.
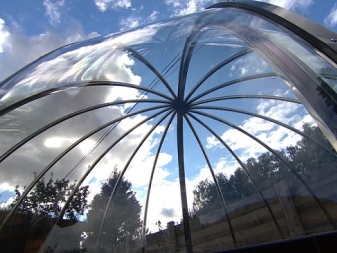
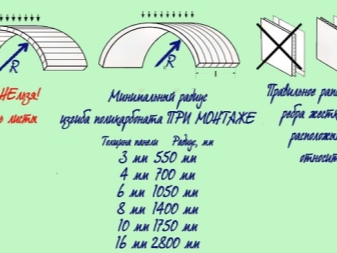
What size should I choose?
Polycarbonate is chosen based on what tasks and in what conditions it is planned to use the material. For example, the material for sheathing should be lightweight and have good thermal insulation properties, for the roof it should be very strong to withstand snow loads. For objects with a curved surface, it is necessary to select plastic with the required flexibility. The thickness of the material is chosen depending on what the weight load will be (this is especially important for the roof), as well as on the step of the lathing (the material must be placed on the frame). The greater the estimated weight load, the thicker the sheet should be. Moreover, if you make the crate more frequent, then the thickness of the sheet can be taken a little less.
For example, for the conditions of the middle lane for a small canopy, the optimal choice, taking into account snow loads, is a monolithic polycarbonate sheet with a thickness of 8 mm with a lathing pitch of 1 m.But if you reduce the lathing pitch to 0.7 m, then 6 mm panels can be used. For calculations, the parameters of the required lathing, depending on the thickness of the sheet, can be found from the corresponding tables. And in order to correctly determine the snow load for your region, it is best to use the recommendations of SNIP 2.01.07-85.
In general, the calculation of a structure, especially a non-standard shape, can be quite complicated. Sometimes it is better to entrust it to professionals, or use construction programs. This will insure against mistakes and unnecessary waste of material.
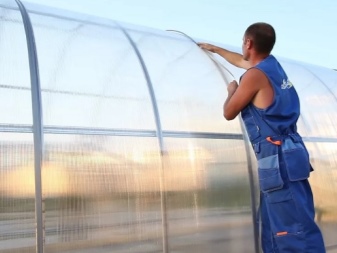
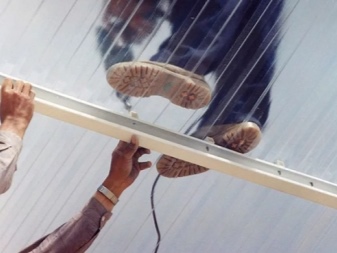
In general, recommendations for selecting the thickness of polycarbonate panels are given as follows.
- 2-4 mm - should be chosen for lightweight structures that do not experience a weight load: advertising and decorative structures, lightweight greenhouse models.
- 6-8 mm - panels of medium thickness, quite versatile, are used for structures experiencing moderate weight loads: greenhouses, sheds, gazebos, canopies. Can be used for small roofing areas in regions with low snow load.
- 10 -12 mm - well suited for vertical glazing, creation of fences and fences, construction of soundproof barriers on highways, shop windows, awnings and roofs, transparent roof inserts in regions with moderate snow load.
- 14-25 mm - have very good strength, are considered "vandal-proof" and are used to create a translucent roof of a large area, as well as continuous glazing of offices, greenhouses, winter gardens.
- From 32 mm - used for roofing in regions with high snow load.
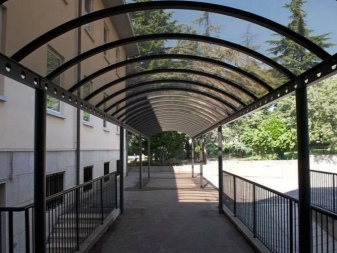
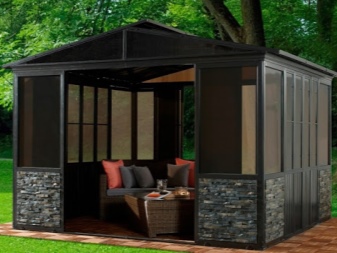
The comment was sent successfully.