All about the blind area
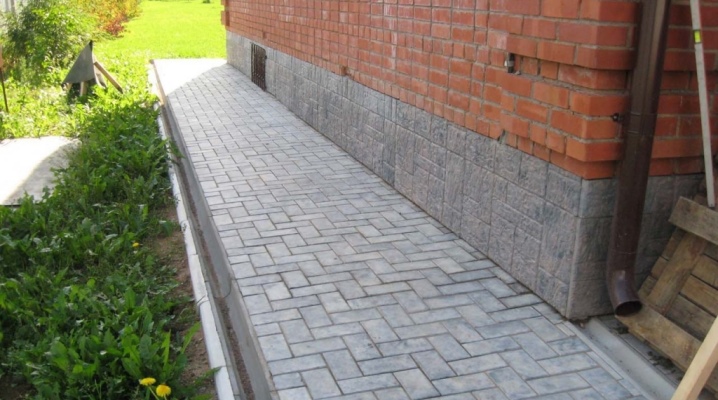
The blind area around the house is the very wide "tape" that an ignorant person considers a path. Actually, this is true, but it is just the top of the "iceberg". The main purpose of the blind area is to protect against the penetration of atmospheric and ground moisture.
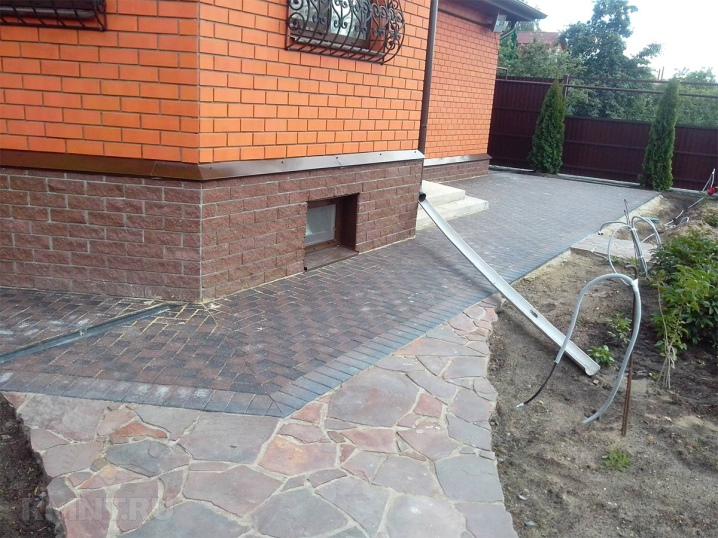
What it is?
The blind area has a complex design and different types of coverings for the upper part. There are several normative documents with different standards. This applies to the rules or SNiP (Building Norms and Rules), which indicate the technology for the correct execution of the blind area. It lists all the clarifying information, where the purpose of the structure is precisely defined, as well as construction requirements for the angle of inclination, width of the ditch, interaction with other structural details of the drainage system.
According to the established standards, the building must be surrounded by mandatory waterproof protection, the role of which is played by the blind area.
The structure is included in the system of envisaged water protection functions from local stagnation of atmospheric and ground moisture at the base of the house, because any construction violates the integrity of the soil.
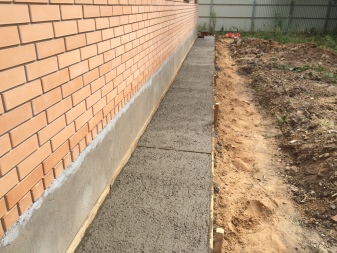
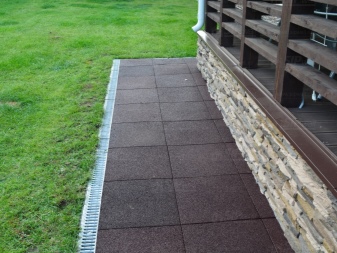
The purpose of the structure is to protect the soil, not the foundation. The base itself is covered with a layer of waterproofing, and the purpose of the blind area is to prevent groundwater, which can rise quite high in the rainy period and spring season, from destroying the soil adjacent to the house. The earth needs protection from excess water, since moisture negatively affects clay, loamy soils, liquefies them, deprives them of strength and bearing properties.
This is dangerous because the structures may simply not be able to withstand the load inherent in the project. It is for these purposes, as well as to take over some of the functions of protecting the foundation and erosion of the soil, that a blind area is being built.
Removing most of the loads from the waterproofing layer, the structure insures the concrete base of the building in parallel.
Well, one more, and quite significant indicator - the blind area is an integral part of the construction project and landscape design. It was the latter quality that stimulated the emergence of many solutions that turn the upper part of the blind area into a decorative and functional element, allowing it to be used as a sidewalk path.
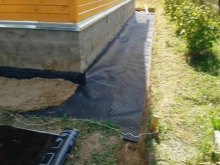
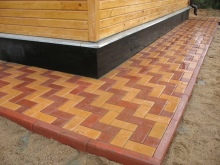
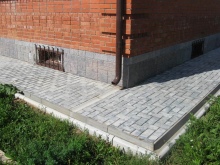
Requirements
Special requirements that prescribe the ratio of the dimensions of the blind area and the overhang of the roof are not spelled out in any GOST. Regulatory obligations for the width of the blind area removal by 0.2–0.3 cm compared to the removal of the cornice can be considered advisory, and during the construction of the structure around the house, it is not required to be guided by these data. Only 2 minimum width indicators are considered mandatory, taking into account the soil:
- on sandy soils - from 0.7 m;
- on clayey, they start from 1 meter.
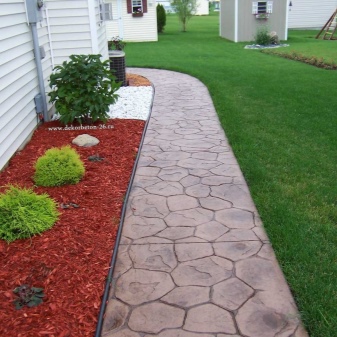
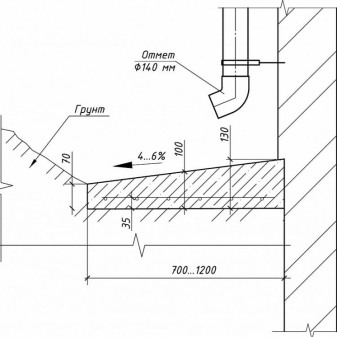
These data are indicated in the JV document for supervisory authorities. In cases where two-story houses do not have gutters, the roof overhangs must be at least 60 cm.
If the building is located on sandy soils, then the difference between the parameters of the blind area and the roof overhang may be equal to 0.1 cm and at the same time do not conflict with regulatory requirements.
From this it follows that the specified parameters of 20-30 cm are just the average and most convenient ratio of the blind area-roof overhang for most options.
As for subsiding soils, then slightly different conditions are imposed on the width of the blind area:
- Type I - width from 1.5 m;
- Type II - width from 2 meters.
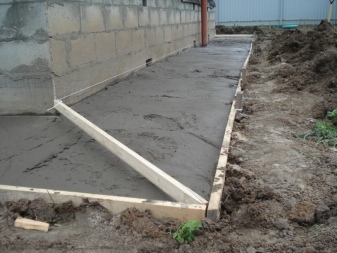
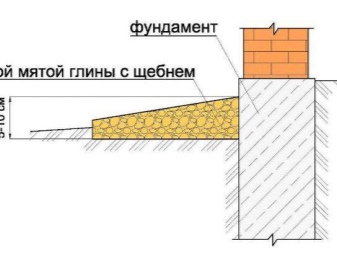
Despite these recommendations, the blind area should exceed the size of the ditch by 40 cm, and the slope angle varies from 1 to 10º. When the house is installed on subsiding soils, the minimum slope should be 3º. The outer edge is at least 5 cm above the soil horizon.
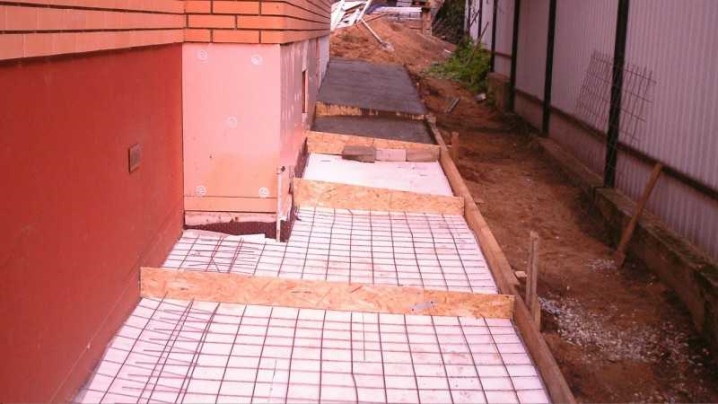
Views
Before proceeding with the construction of a blind area around a house, a bathhouse, in a country house or near buildings of a different type, it is necessary to decide which option is most suitable for the site, especially if the work will be carried out on heaving soils, especially for a temporary structure. There are 3 types of blind area.
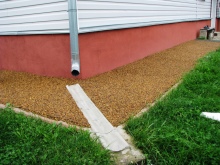
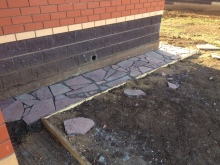
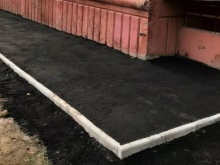
Hard
It is a monolithic tape made of concrete or asphalt concrete. For a concrete base, formwork, coupled with mandatory reinforcement, will be required. The use of asphalt concrete does not require formwork due to the material's resistance to mechanical bending deformations.
The execution of the base, as well as the pouring of the surface, is carried out in the manner used for the tracks, but with a mandatory slope from the base to the outside. Moisture protection is achieved through the use of appropriate special materials.
It is necessary to pay close attention to the solidity of the surface - cracks in the coating will lead to the penetration of water through the blind area. A prerequisite is the installation of a damper tape between the blind area and the plinth as a compensator for loads on reinforced concrete structures during temperature changes and protection against cracking in the event of shrinkage and other displacements of the walls.
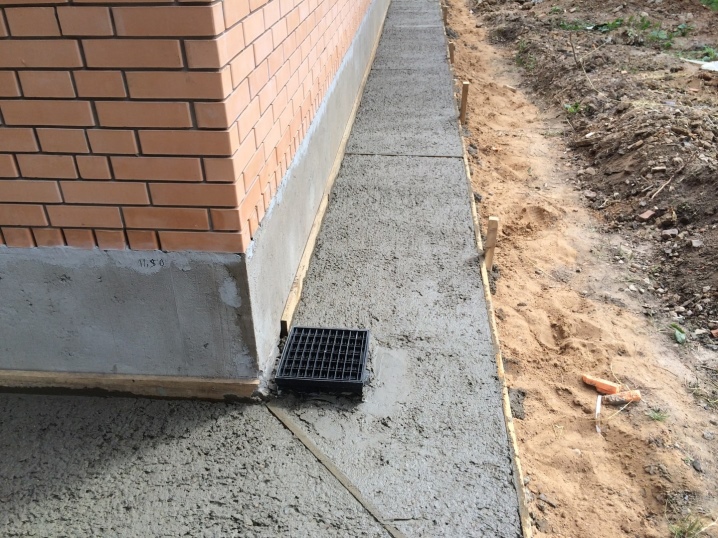
Semi-rigid
The surface of the blind area is lined with paving stones, clinker tiles or bricks. The same laying method is used as for sidewalks, areas covered with similar materials, with the need to lay waterproofing in layers of the blind area using:
- concrete;
- geomembrane laid on a dry mix of sand and cement.
This type of structure has not only functional value, but also decorative, being a kind of building accent.
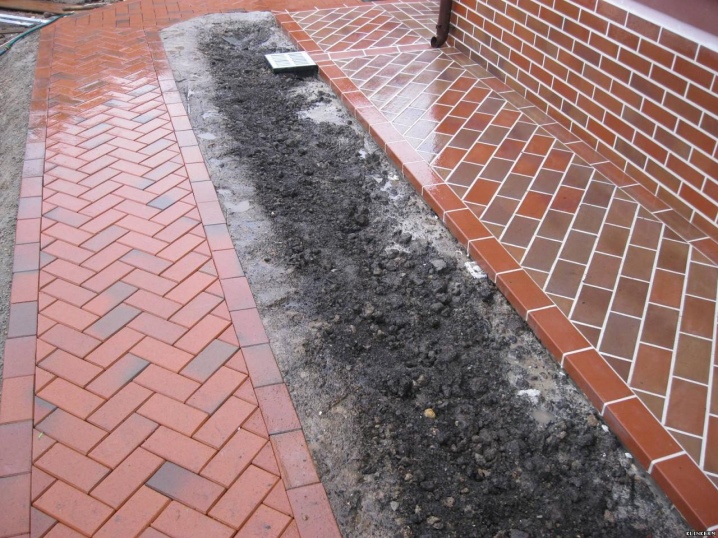
Soft
This is the classic way of arranging the upper part from a dense layer of clay or soil. A blind area of this type has always been used in rural settlements around residential buildings. Nowadays, such a budget option is sometimes used during the construction of small summer cottages, and colored gravel and similar materials are used as a decorative design for the top layer.
To enhance the waterproofing protection, a waterproof film is placed between the clay and crushed stone.
At the same time, it must be remembered that the blind area is still not just a decor. - serious savings during its installation may turn into negative consequences in the future.
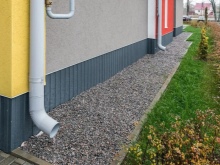
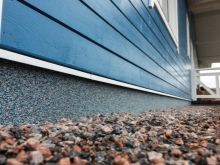
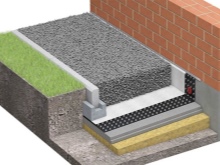
The soft type with the use of a profiled membrane is becoming more and more popular today. Algorithm of actions:
- the membrane is placed on the bottom of a 25-30 cm depression, rammed with a slope from the base;
- covered with a layer of geotextile with the obligatory capture of a part of the wall at the base of the house;
- after that, a crushed or sandy drainage layer is organized;
- from above, the structure is covered with fertile soil, arranging a lawn or flower beds with ornamental plants.
The second name of such a blind area is "hidden". An interesting solution, but it is not recommended to walk on it, for this you can additionally arrange a path.
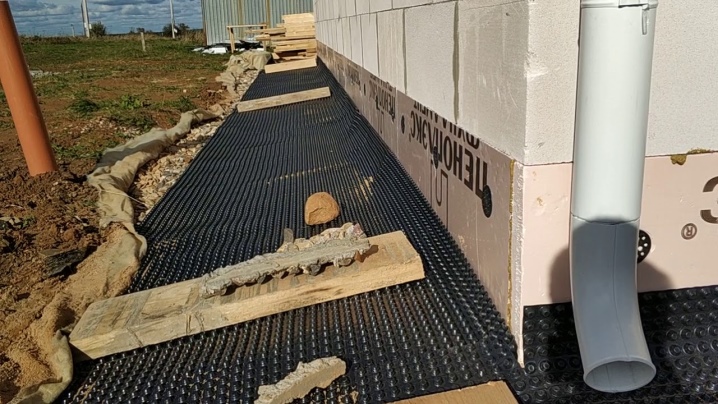
Materials (edit)
Concrete blind area is the most common method as it is a reliable and proven material. Knowing the technology of its organization, all the work can be done independently. Asphalt blind area is used in multi-storey construction, which is explained by several factors:
- the complexity of compaction - this requires significant effort;
- keeping the asphalt in working order - this requires a high temperature (about 120º);
- hot asphalt actively emits harmful substances - what is the point for the owners of country houses to pollute the clean air with urban "aromas".
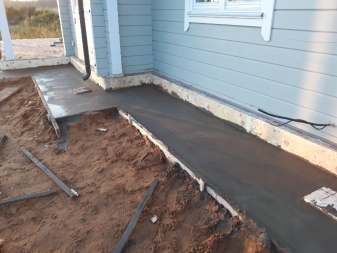
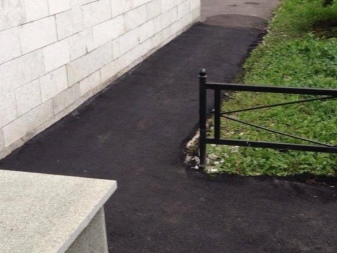
The top covering of the blind area is made from a variety of materials, thanks to which it differs in different types of rigidity.
- The ceramic tile option is referred to as the rigid type, since the tiles are laid on a concrete base. Clinker tiles are used as cladding. The tile coating is characterized by increased resistance to atmospheric and mechanical influences. Such a surface perfectly meets the task at hand, but its price is quite high.
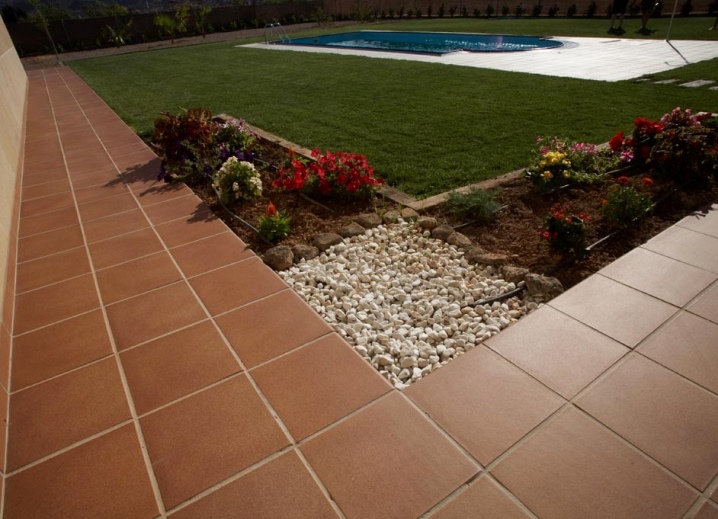
- An analogue of a ceramic coating is concrete paving slabs (paving stones). A relatively new type of coating, but despite this, the laying of the material is not particularly difficult.
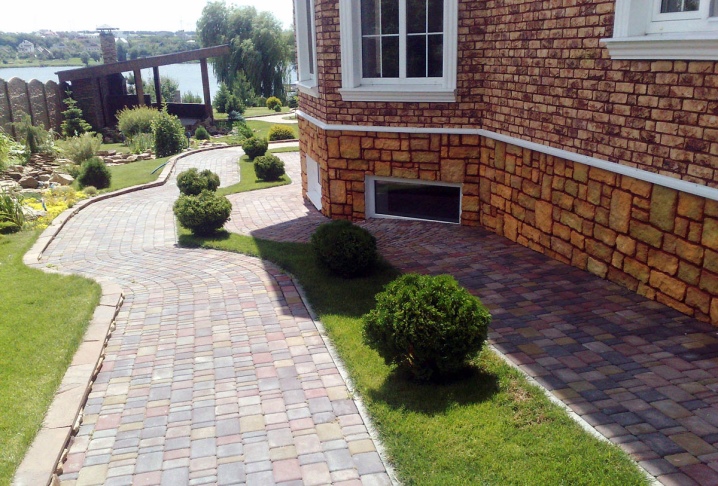
- The blind area made of stone, gravel, pebbles is not popular, since they are difficult to ram, and it is inconvenient to walk on them. In addition, such a crushed stone coating has to be constantly monitored - it can be washed out, grass grows through it and it must be weeded. Stone is a pretty good option, but it is expensive and difficult to install.
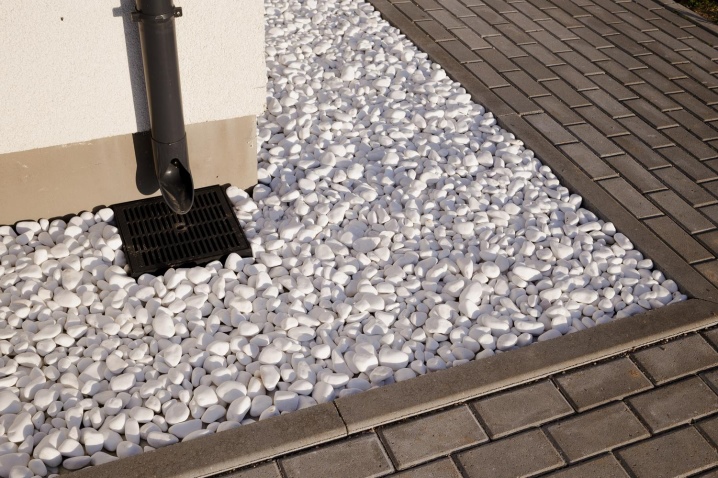
- Hidden blind area, where the top cover is soil, is used very rarely, however, made with the observance of technologies will serve for a long time and looks original, organically fitting into the surrounding landscape.
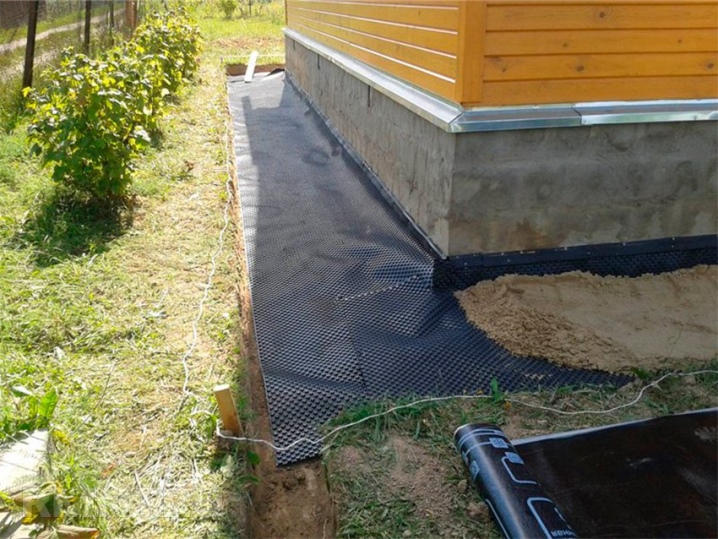
- Asphalt concrete blind area it is used infrequently due to the complexity of working with the material, but it is a reliable coating.
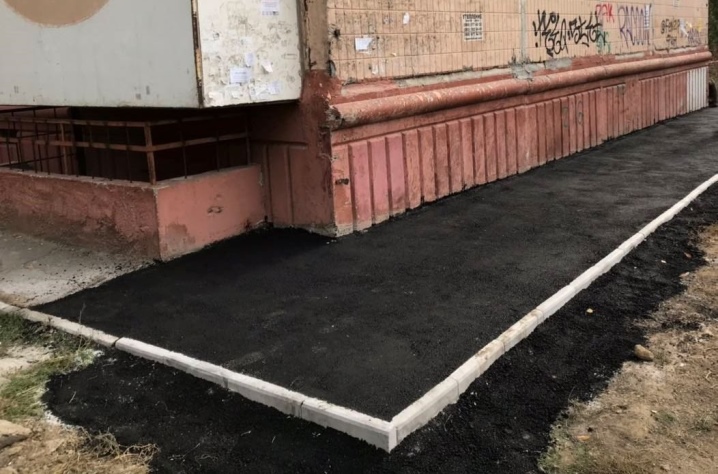
- Clay blind area. Probably the very first material from which the blind area was made. Houses built with such a blind area many decades ago are still in working order, which speaks of its distinctive properties. The clay coating must be reinforced as facing with pebbles and coarse stones.

Besides, sometimes the blind area is made of decking, brick, rubber crumb with a protruding border as a limiter. In the construction of the blind area, it is important to remember about creating a damper tape and reinforcing the structure with reinforcement and reinforcing mesh. In the section, the drawings of the blind area resemble a layer cake.
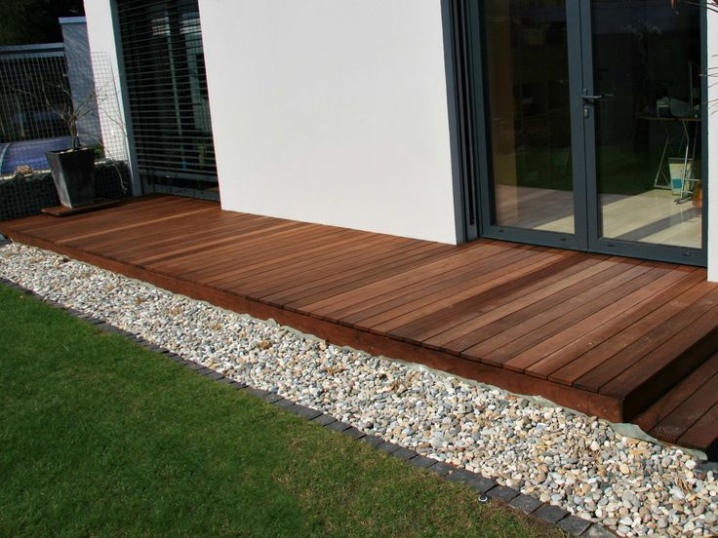
Dimensions (edit)
The width of the blind area is determined taking into account the soil on which the structure is being erected, because each type has its own subsidence indicators. For example, clay soil is classified into two types:
- Type I - there is no subsidence under its own weight, or subsidence indicators are equal to no more than 0.50 cm, which depends on the factor of external influence;
- Type II is prone to subsidence under its own weight.
On the basis of these indicators, the choice of the values of the preliminary layers necessary for laying the surface layer is determined. Taking into account the SNiP standards, the specialist determines the width of the blind area.
Many years of practice have proven the effectiveness of the values:
- I type of soil - width from 0.7 m;
- II type of soil - the width starts from 1 mm.
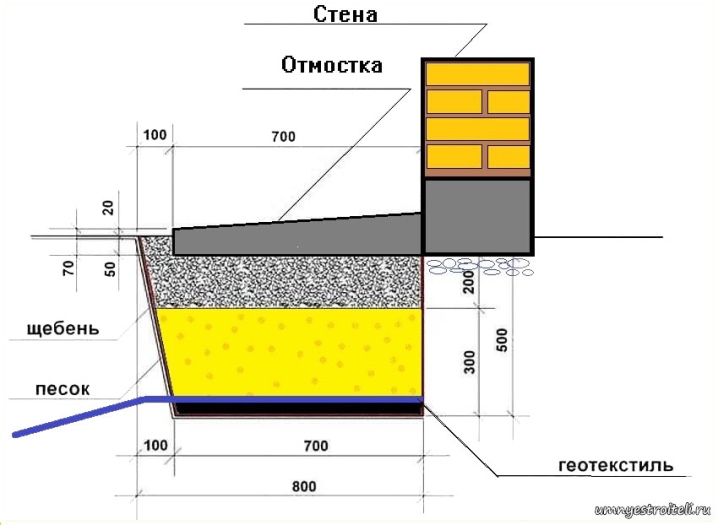
If the site is located on stable ground, the optimal parameters for the width of the blind area are 0.8-1 meter. The width can be considered satisfactory if it exceeds the removal of the roof ledge by 0.2 m for normal soil and 60 cm for subsidence soil. Finally, a decision is made on the parameters of the blind area after a decision has been made on the purpose of the structure:
- foundation protection;
- protection with periodic pedestrian operation;
- protection with constant use - a veranda, an entrance for a car.
As already noted, the length and height of the blind area is not regulated by GOST. It is most correct to calculate the length along the entire perimeter, since a rupture can have a negative effect on the integrity of the foundation.
An exception can be made only at the location of the porch. The optimum height of the blind area is considered to be from 0.70 m to 0.1–0.15 m. For a pedestrian belt, the requirements are more critical in terms of the cushion arrangement.Automotive area needs maximum strength - when choosing a slab covering, preference is given to vibropressed material, according to SNiP III-10-75.
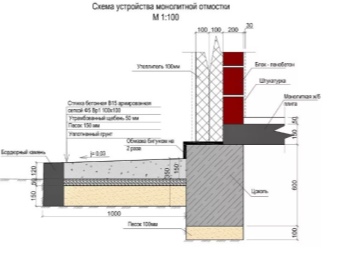
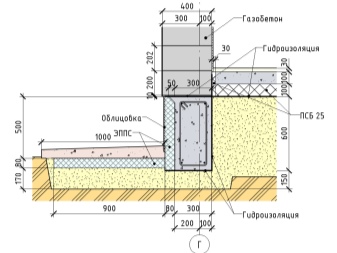
Improvement of the adjacent territory - according to the regulations, the blind area should be close to the foundation, the slope angle should be within 1-10º away from the house. The calculation is made based on the values of 15-20 mm per 1 m. Visually, this slope is almost imperceptible, but it performs the drainage function perfectly. It is impractical to make the slope more significant, since a large slope gives speed and destructive force to the water flow. Over time, it will begin to erode the outer edge of the structure and the surrounding soil. The drawings should accurately indicate all the data and schematically depict the entire structure of the blind area for a house or bath in a section.
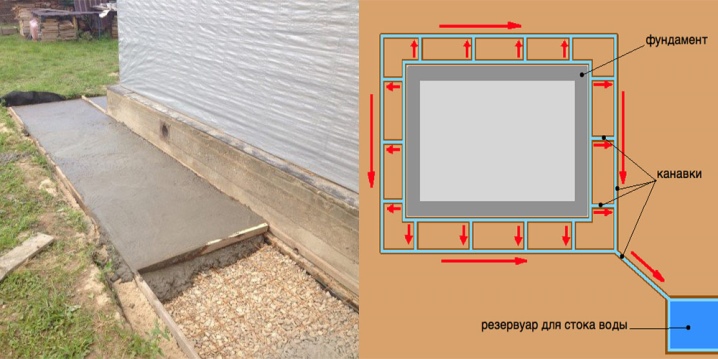
How to do it right?
Step-by-step instructions on how to make a tape around the house with your own hands, construction and decoration technology.
- Digging a pit for the blind area. A 20-30-centimeter layer of soil is removed to the width of the structure, a pit is dug, the bottom is compacted while forming a slope.
- The wall section is carefully compacted. The thickness of the compacted layer is not less than 0.15 m.
The depth of the dug ditch should be sufficient for all the underground layers to enter, and it was possible to cover the top layer with a pillow. If it so happens that the ditch turned out to be deeper than the projected, then the difference is minimized by compacted soil or clay, with the latter option being more preferable.
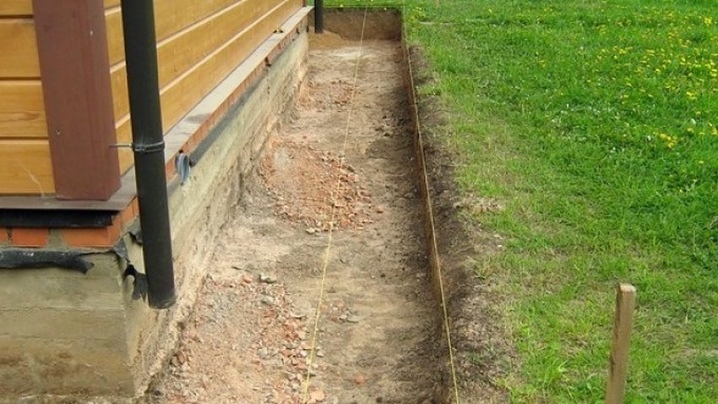
Pillow
The bottom layer of 40-70 mm fraction of crushed stone is most suitable for subsiding soils, which serves as an emphasis on formwork and reinforcement. After digging the soil from the basin, crushed stone is poured, leveled and compacted. After that, a finer fraction is poured with simultaneous wetting with water. Sand, which serves as a cushion for the blind area, comes in the second layer, it is processed according to the same principle - compaction and wetting with water. The deviation of the crushed stone layer is 0.015 by 2 meters and the sandy layer is 0.010 m by 3 meters.
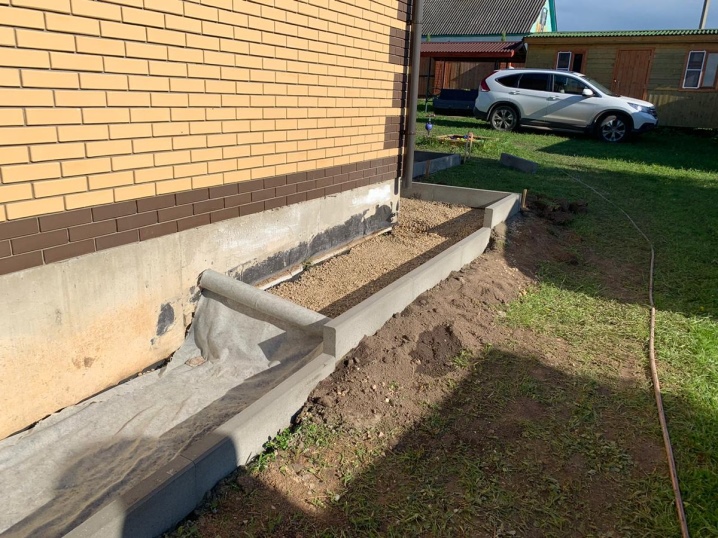
Waterproofing
The sand layer is covered with a geomembrane or polyethylene 200 µm thick. Waterproofing is needed for concrete to maintain the level of moisture it needs. In the regulations, this layer is referred to as "separating".
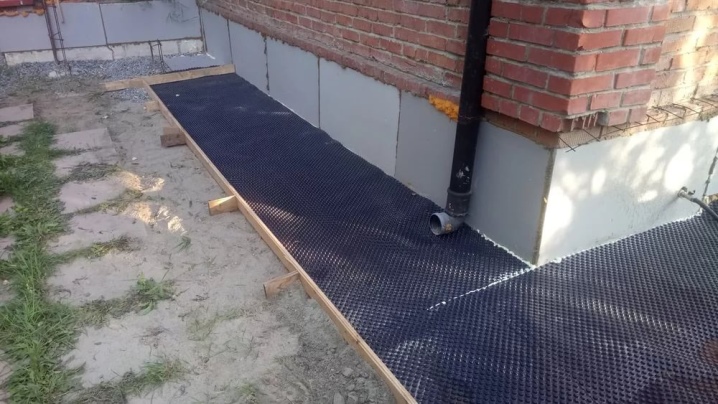
Warming
Working on unstable soils requires insulation with extruded polystyrene foam. When using 2 layers, make sure that the upper seams do not coincide with the lower ones.
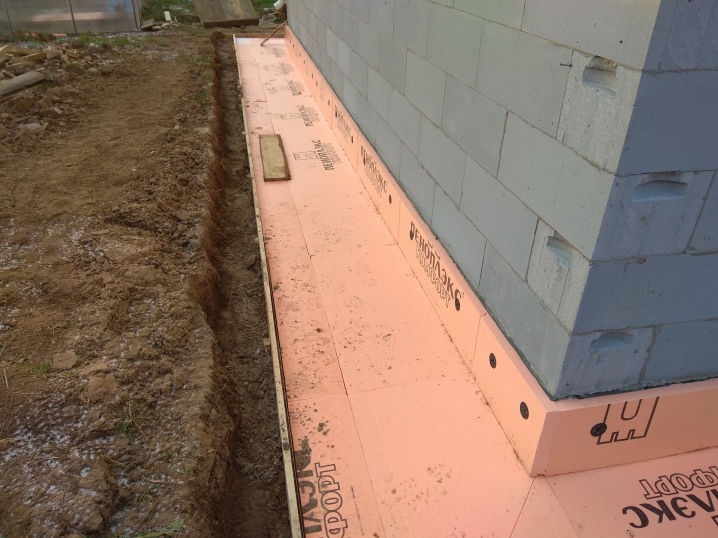
Formwork
Its installation is carried out from bars and wood. At the same time, the strips are laid to create expansion joints. As a rule, the slats are fixed at a given level in relation to the surface with a certain angle; concrete is poured, focusing on them. Rack sizes:
- width - 20 mm;
- section - over 25% of the thickness of the blind area.
To calculate the inter-seam distance, use the formula: the number 25 is multiplied by the height of the concrete base against the wall. The basement expansion joint is made of roofing material, folding it until a thickness of 0.5 cm is obtained.
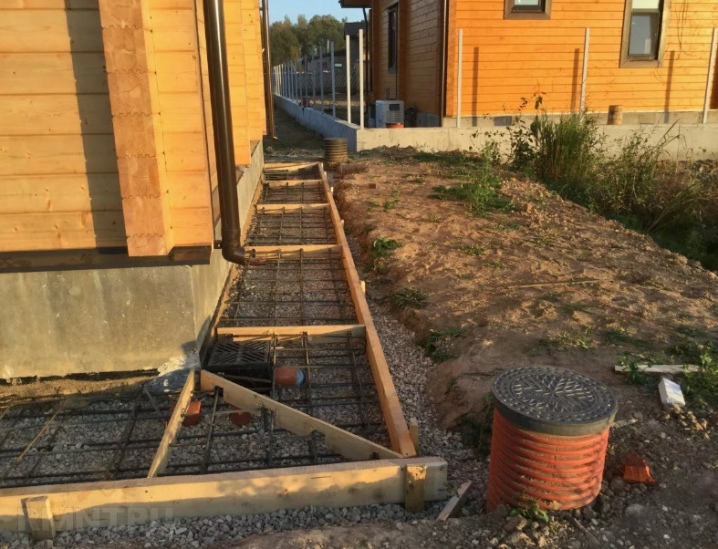
Reinforcement
The simplest and least labor-intensive way is to arrange with a reinforcing mesh. The strips are laid with an overlap, capturing several cells, after which they are tied, making a wire knot and keeping the distance from the waterproofing layer from 0.3 cm. These indicators are maintained on all surfaces of the structure - external, end, and so on.
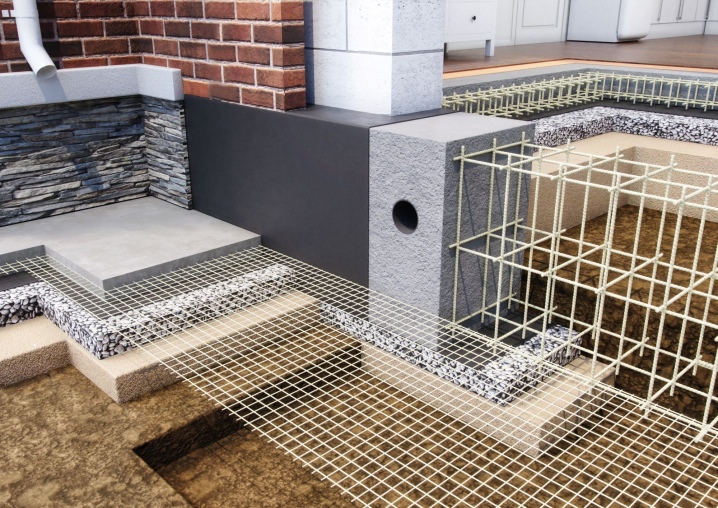
Concreting
For the manufacture of a concrete structure around a well or housing with a drainage tray, a grade of concrete material M200 is used. After pouring, the concrete is covered and moistened for two weeks, thus increasing its strength and protective functions. The iron-plating technology will qualitatively improve the performance of the monolith. For these purposes, 2 methods are used:
- dry ironing is carried out after pouring;
- the wet method is rather laborious, requiring special knowledge and skills.
The slats are removed after 2 weeks, filling the joints with a mineral-filled bitumen sealant.
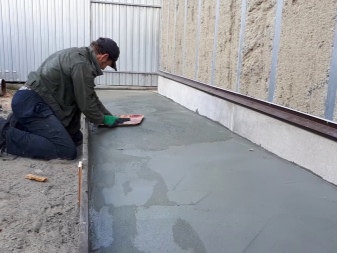
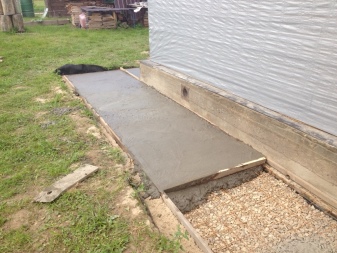
Finishing the surface of the blind area is possible with various materials, as well as applying a new layer over the old surface. The blind area may require repair after several seasons, for example, part of the tile has come off, the tightness of the structure adjoining the plinth is broken, and so on. It's easy to do this yourself, while not forgetting about drainage with stormwater:
- defective parts must be removed;
- prime the surface to be repaired;
- make the screed with a plastic mixture and restore the waterproofing;
- lay the reinforcing mesh and pour concrete, ironing and subsequent grinding.
The implementation of the technology in compliance with the sequence of stages will help to make a high-quality structure around the house.
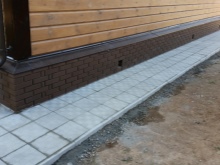
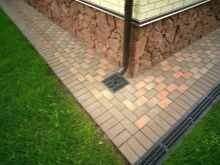

Possible mistakes
Since mistakes are possible at any stage of the work, especially if the owner of the house does it on his own, without special skills, you need to be careful, check the diagram and remember the main "dangers".
- Poorly compacted backfill can cause excessive shrinkage, which in turn will lead to a leak in the waterproofing or coating. The same can happen due to carelessness when construction waste gets into the backfill.
- Transverse cracking. The appearance of this defect occurs when the level of the bottom of the trenches and the degree of slope are not observed. Bottom unevenness is the uneven distribution of the crushed stone layer, which affects its bearing qualities and the appearance of cracks in the concrete layer.
- Damper and expansion joints. Their absence provokes the appearance of internal stress in the near-walled concrete layer, and, consequently, defects in the concrete monolith. In the hot season, internal stress arises in the wall layer, which causes the material to crack.
- The irrigation tap provided in the base means the presence of a mandatory separate gutter in the blind area.
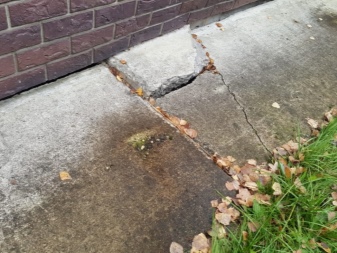
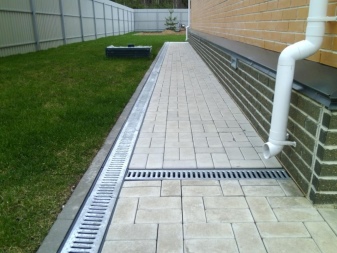
Besides, do not ignore the regulations regarding the maximum slope of the blind area, equal to 10%. If the cottage has an organized roof drainage system, then in the blind area, trays are mounted under the gutters with a slope of 15%.
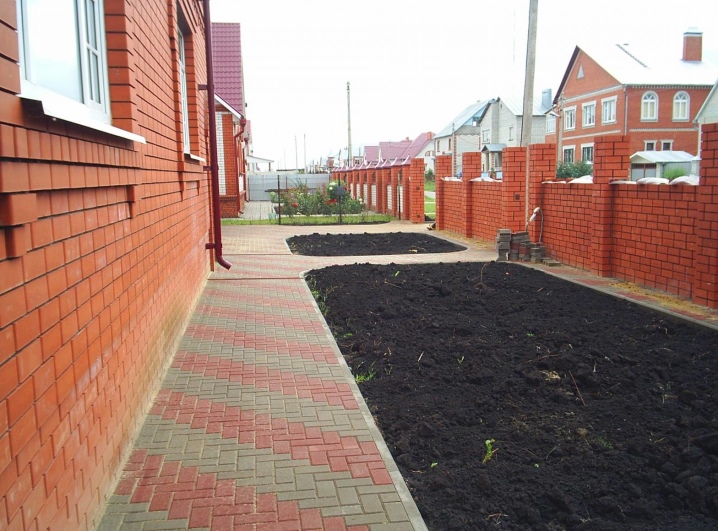
The comment was sent successfully.