All about blast furnace slag
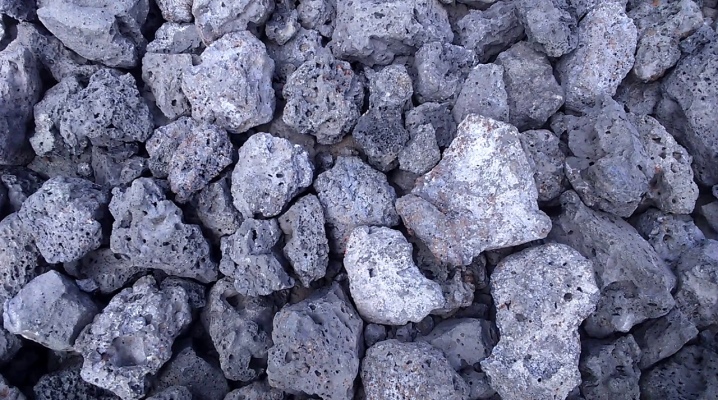
It is very important for consumers to find out what it is - blast furnace slag. The correct deep characterization cannot be limited to an acquaintance with the density of granular slag, with its differences from steelmaking, with a weight of 1 m3 and a chemical composition. It is imperative to find out what the use of crushing screenings is and what particular types of such products are.
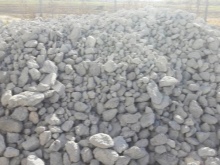
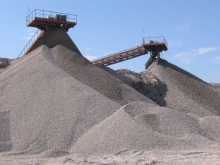
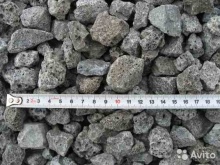
What it is?
The name "blast-furnace slag" refers to a specific type of artificial stone mass. They appear as a by-product of the production of blast-furnace metal smelting - hence the common name. Waste rock is fused with the fluxes contained in the charge, and this is how slag products appear.
If the blast furnace process is carried out strictly according to the technology, then the slag looks like a light product (light gray, with yellow, greenish and some other notes). If the manufacturer violates the established technology, then another color appears - black, this indicates a high concentration of iron in the manufactured products.
The texture of the slag mass also differs within wide limits. Known options:
- stone-like;
- glass-like;
- similar to porcelain.
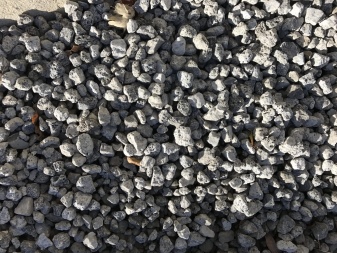
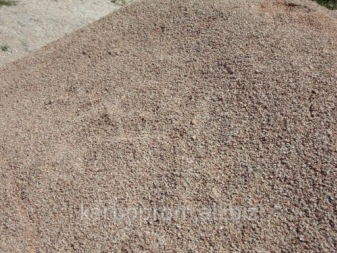
Composition and characteristics
Since even at one enterprise receiving raw materials from a stable range of suppliers, technological nuances can change, it is natural that in different cases the properties and composition of the slag are also quite significantly different. You can often read that this product is chemically close to cement. And this statement is not without foundation. However, there is slightly less calcium oxide in the slag mass, but there is clearly more silicon dioxide, aluminum oxide and other similar compounds.
It should be noted that oxides are usually present not in pure form, but as part of other compounds. Also, since the technological process implies a sharp cooling of the processed mass, the chemical composition of the slag includes aluminosilicate glass. It has an impressive ability to react with other substances. A separate important topic is the specific gravity of 1 m3 of blast furnace slag, which is also the bulk density, in fact (sometimes these concepts are diluted, but they still remain closely interconnected for obvious reasons). This figure can vary from 800 to 3200 kg, depending on the feedstock, processing methods and other technological subtleties.
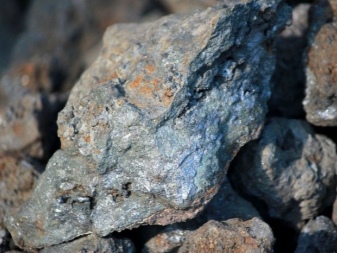
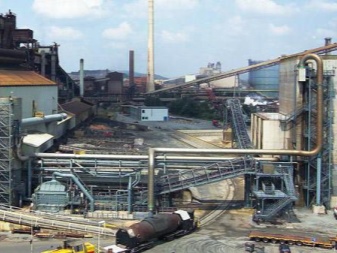
In practice, however, most slags weigh, however, not less than 2.5 and not more than 3.6 g per 1 cm3. Sometimes it is even lighter than molten metal. No wonder - otherwise it would have been impossible to clearly and competently separate the slag mass from the main product of metallurgical plants. Even the special GOST 3476, adopted in 1974, applies to blast furnace slag.
Note: This standard does not cover products derived from ferroalloys and magnetite ores of any origin.
The standard normalizes:
- the content of aluminum oxide and some other substances;
- the proportion of fragments that have not undergone full granulation;
- nominal size of a standard lot (500 tons);
- requirements for testing samples taken from each delivered batch separately;
- retesting procedure for questionable or ambiguous indicators;
- requirements for storage and movement of finished products.
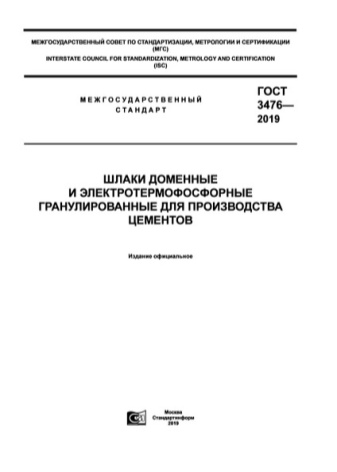
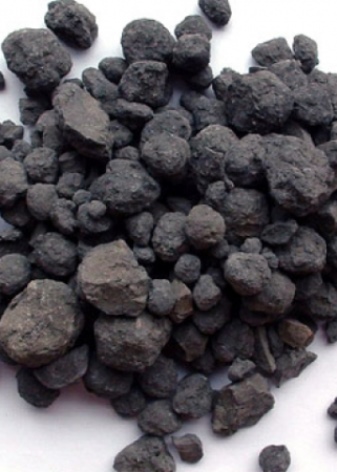
The standardized level of thermal conductivity of blast furnace slag is taken equal to 0.21 W / (mC). This is a pretty decent indicator, and still worse than that of mineral wool. Therefore, such insulation will have to be put in a thicker layer. In the characteristics of the delivered batch of goods, such a parameter as flakiness must be indicated. The greater the proportion of smooth grains, the less "adhesion" between them, and also the more difficult it is to prepare a solution and hold the mass together.
Its useful to note, unfortunately, the environmental friendliness of blast furnace slag is highly questionable. Its use in direct contact with the environment, for example, in road construction, causes serious risks, first of all, contributes to the spread of heavy metals. But if we exclude the erosion of the mass by soil, melt water and precipitation, then the problem is largely solved. Therefore, it is definitely not worth giving up the use of slag products - in any case, it is better than throwing it out directly. However, one must pay attention to the conditions of use.
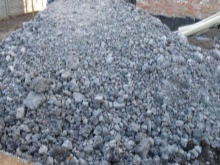
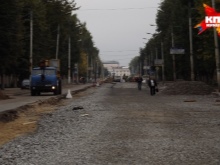
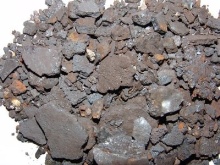
Differences from steelmaking slag
The main specificity is that such a product is obtained using a completely different technology. And therefore its chemical composition, and therefore, of course, its properties, are very different. Steel-smelting waste is denser and obviously not suitable as a simple mineral filler or insulation. but it is sometimes used as ballast in road construction or as an aggregate for asphalt mixtures.
The experiments are giving promising results, but still the classic blast furnace slag remains a more convenient and attractive product.
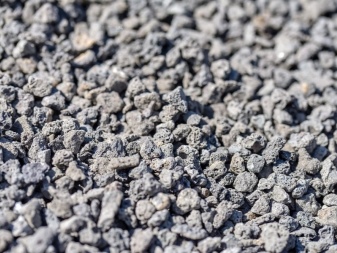
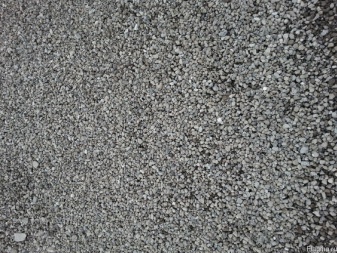
Production technology
Slag production is associated with smelting in a special furnace, for example, pig iron. The substance we need leaves the blast-furnace unit, being warmed up to at least 1500 degrees. Therefore, in order to be able to work with it, it is necessary to cool the slag. It would be too long to wait for this to happen naturally. Therefore, they practice:
- swelling (or otherwise, cold water supply);
- blowing with air jets;
- crushing or grinding on special equipment.
It should be noted that the processing method directly affects the composition and characteristics of the finished product. All granulators know about this, and therefore they take into account such a moment when a certain task is posed. For example, with air cooling, silicates and aluminosilicates will prevail in the slag. In some cases, the slag is also crushed mechanically - this procedure is used either while it is still liquid, or after partial solidification. Large pieces are processed into small grains in such a way that improves further work performance and improves the quality of the finished product.
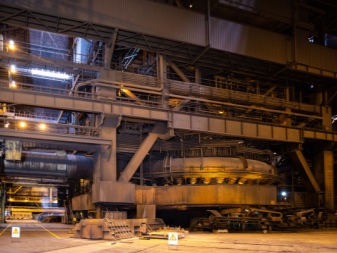
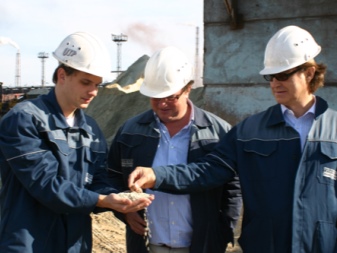
Of course, no one produces blast furnace slag on purpose. Let us emphasize again that this is always only a by-product of metallurgical production.
The production of granules can be carried out by various methods, using specific devices. Systems for wet and semi-dry granulation are known. In the wet method, the slag is loaded into reinforced concrete pools filled with water.
It is customary to divide the pools into a number of sectors. This approach ensures the continuity of the production procedure. As soon as the heated raw material is poured into one part, the other is already ready to unload the cooled slag. In modern enterprises, unloading is carried out by grab cranes. The amount of residual water depends on the porosity, and the porosity itself is determined by the features of the cooling process.
To make a semi-dry slag, they usually resort to mechanical crushing. A similar effect is achieved by throwing cooled, but not yet completely solidified slag into the air. As a result, the material is denser and heavier than the wet granulated material. The moisture content of the finished product will be 5-10%. The higher the melting temperature, the lighter the finished product will be.
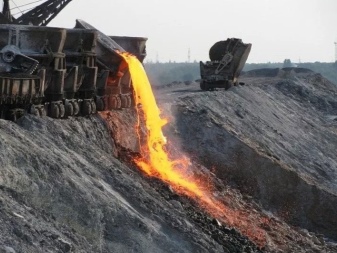
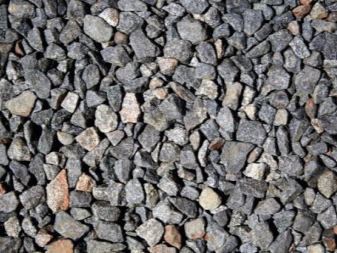
Views
Metallurgical blast-furnace slag is obtained by smelting pig iron. Depending on the fraction and on the bulk density, such a product is considered a porous or dense product. Crushed stone with a specific bulk density below 1000 kg per 1 m3 and sand with a specific bulk density below 1200 kg per 1 m2 are considered porous.
An important role is played by the so-called basicity modulus, which determines the alkaline or acidic nature of the substance.
During the cooling process, a substance can:
- keep amorphous;
- crystallize;
- undergo partial crystallization.
Ground slag is produced from granular grades by additional grinding. Depending on the target, a hydrophobic additive can be added there. The product usually meets the 2013 specifications. Dump slag is generated as waste. Its value directly for metallurgical production is not high, however, technologies for processing the dump mass are already emerging.
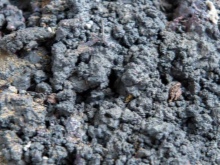
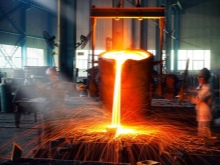
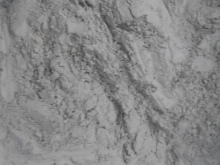
Scope of application
Blast furnace slag is widely used. Its main field of application is the production of building materials. So far, this area is developed unevenly in different regions of the country. However, the reduction in the distance of transportation of building materials to construction sites can only be welcomed. Abroad, not only blast furnace slag, but also steelmaking slag is used in road construction, but this is already a topic for a separate conversation.
A simple moldboard product is able to set quickly, which makes it analogous to cement. The use of such a mass in dumping road surfaces is gradually expanding. Also, in many places, they seek to strengthen the support pads of the foundations. There are developments on the use of crushing screenings as the main component of concrete. There are already a number of publications in which this experience is encouraged.
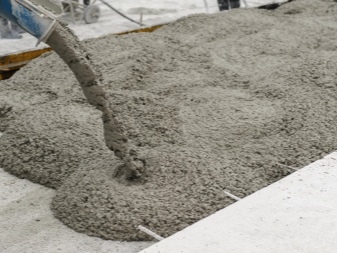
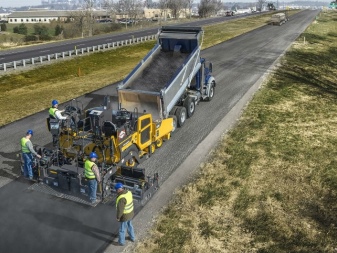
Crushed slag is produced by crushing the dump slag and passing it through screens. The specific application is influenced primarily by the material fraction. The use of such a product as:
- filler of durable concrete mixtures;
- ballast cushions on rail tracks;
- means of strengthening the slopes;
- pier and berth material;
- means of arrangement of sites.
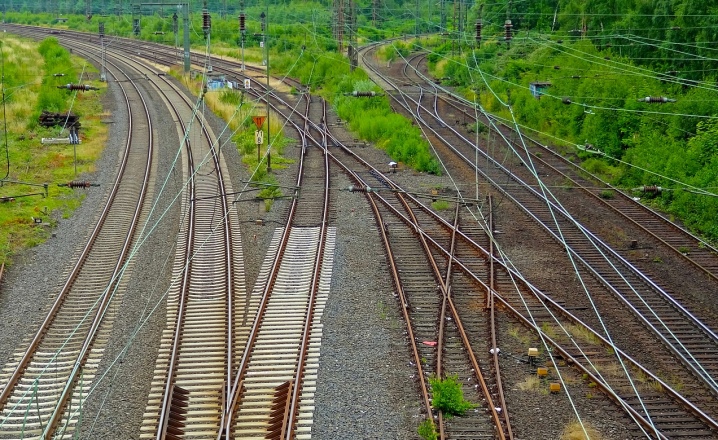
Granular slag is used to obtain cinder blocks. It is also needed for thermal insulation. Sometimes blast furnace slag is used for drainage: in this capacity it quickly degrades, turns into sand, but still works properly. The granular mass can also be used for sandblasting.
This application is very common, and the required product is offered by many leading manufacturers.

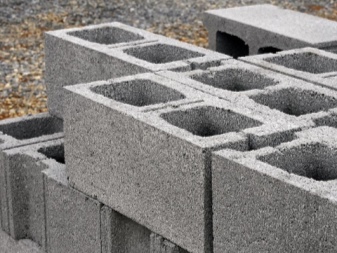
The comment was sent successfully.