How to prevent the clay from cracking?
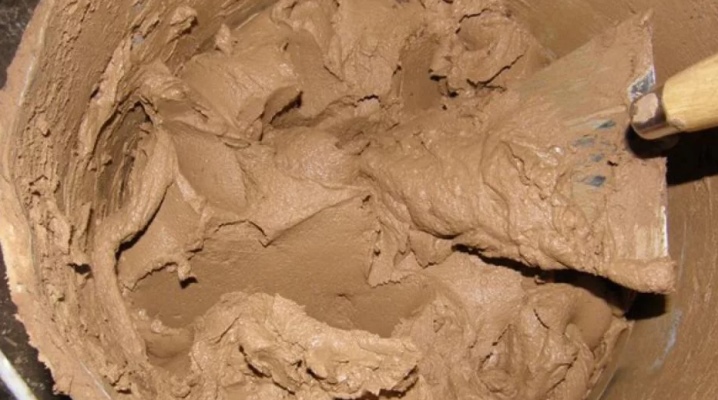
Clay is often used in the decoration of baths, it is environmentally friendly and, as a rule, has a spectacular appearance. However, it happens that areas near the firebox are covered with cracks. How to be in this situation - we will consider in more detail in our article.
Why does it crack when dry?
By its nature, clay is a sedimentary rock. In dry form, it has a dusty form, but when water is added, it acquires a plastic structure. Clay contains minerals from the group of kaolinite or montmorillonite, it can also include sandy impurities. Most often it has a gray color, although in some places rock of red, blue, green, brown, yellow, black and even lilac shades is mined - this is explained by additional impurities present in different types of clays. Depending on such components, the peculiarities of using clay also differ.
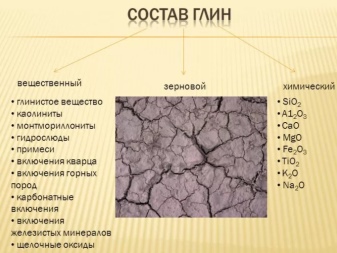
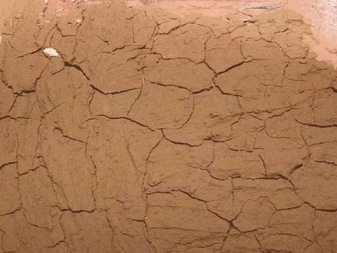
The exceptional plasticity of the rock, fire resistance and good sintering properties, combined with excellent waterproofing, determine the widespread demand for clay in the production of bricks and pottery. but often in the process of twisting, drying, sculpting, as well as in the final firing, the material is covered with cracks. The reasons for this may be different - some types of clays are dryish, they contain a large proportion of sand, others, on the contrary, are too oily.
Most often, clay coatings crack in baths, wells, and various utility rooms. The reason is improper finishing, cladding without taking into account the technical parameters of the clay and its characteristics. Therefore, an important role is played by the professionalism of the master, who decorates the walls of the bath, makes a pipe, etc.
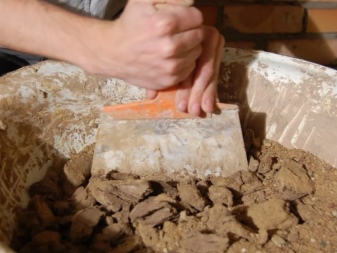
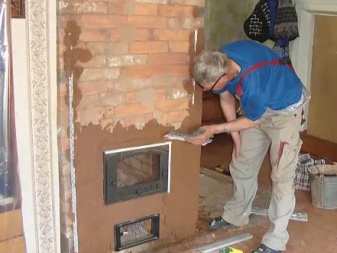
A number of factors can influence the appearance of cracks.
- Long stove downtime in cold weather. If the firebox is not used for a long time, then with strong heating, the plaster can burst due to a sharp overheating of the cooled hearth.
- Excessive haste when testing a freshly laid firebox. In this case, cracks appear when the materials have not dried well enough and have not gained the required strength.
- Inadequacy of the clay used for the required level of thermal stretch.
- Overheating the hearth. This happens when fuel is used that emits more thermal energy than the stove can withstand. For example, when using coal in a wood-burning hearth.
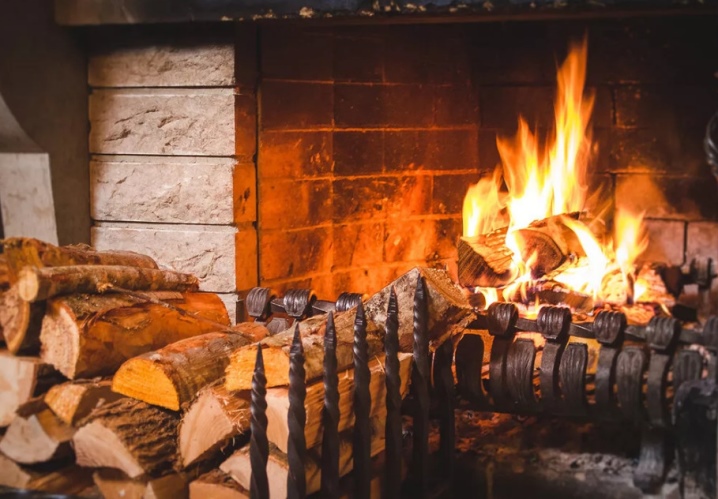
The reason for the cracking of the clay base can be finishing errors. In a similar situation, with strong heating, areas appear in the facing material where strong temperature drops occur.
- Too thick layer. To prevent the appearance of cracks during plastering, the clay must be applied in a layer no more than 2 cm thick. If there is a need to apply a second layer, then the first must have time to fully grab - in warm, dry weather, this usually takes at least one and a half to two days. If clay plaster with a thickness of more than 4 cm will be applied, then additional surface reinforcement with a steel mesh will be required.
- The plaster dries out too quickly. It is best to work with clay at a temperature of + 10 ... 20 degrees. If the weather is too hot, then it is better to pause or moisturize the walls abundantly.
The fact is that at elevated temperatures the treated surfaces absorb moisture very quickly - abundant moisture prevents the surface from drying out.
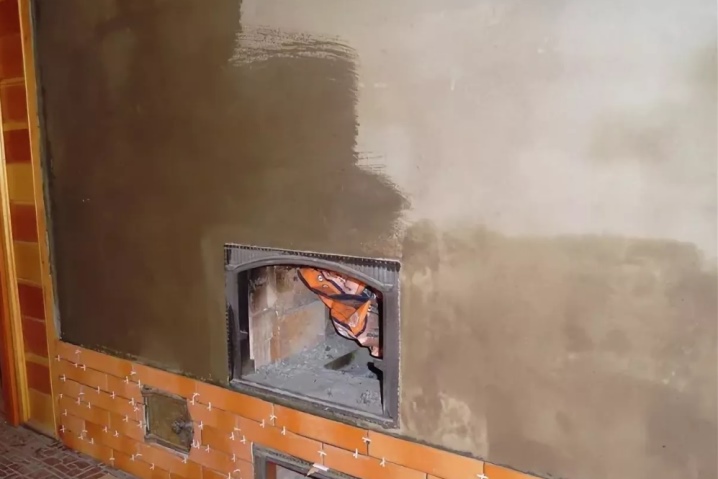
What do you need to add?
The clay surface is often cracked if the mortar is too greasy. Clays of increased plasticity are referred to as "fatty"; when soaked, the greasy component is very well felt to the touch. The dough from this clay turns out to be slippery and shiny, it contains almost no additional impurities. To increase the strength of the mortar, it is necessary to add to it "emaciated" components - burnt brick, potter's battle, sand (ordinary or quartz) or sawdust.
The opposite situation also happens when the coating of "skinny" clay is cracked. These compounds are low-plastic or non-plastic at all, rough to the touch, have a matte surface, begin to crumble even with a light touch. Such clay contains a lot of sand and compounds that increase the fat content of the mixture must be added to it. A good effect is given by egg white and glycerin. The desired effect can be achieved by mixing "skinny" and "oily" clay.
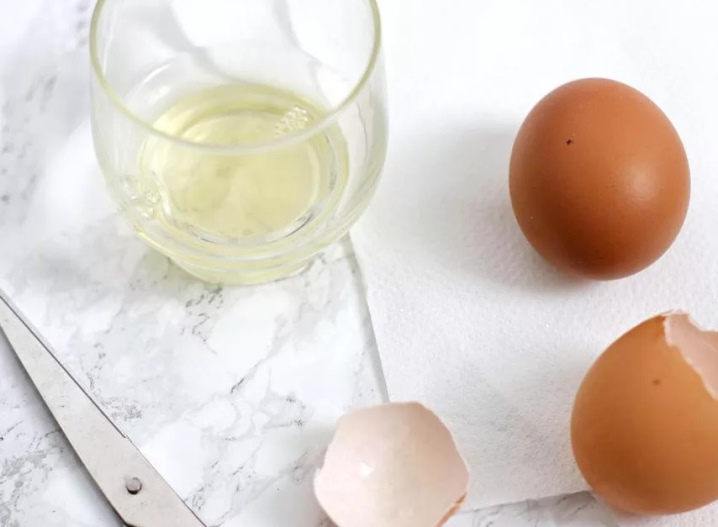
There is one more working way - to stir the solution. It consists in adding water to the resulting clay mixture and thoroughly kneading the resulting mass.
This solution should settle well. Moisture remains in the top layer that needs to be drained. In the second layer, liquid clay settles, it is scooped out and poured into any container. After that, they are left in the sun so that all excess moisture evaporates. Undesirable additives remain at the bottom, they can be thrown away. The result is an elastic clay with a consistency reminiscent of a tough dough.
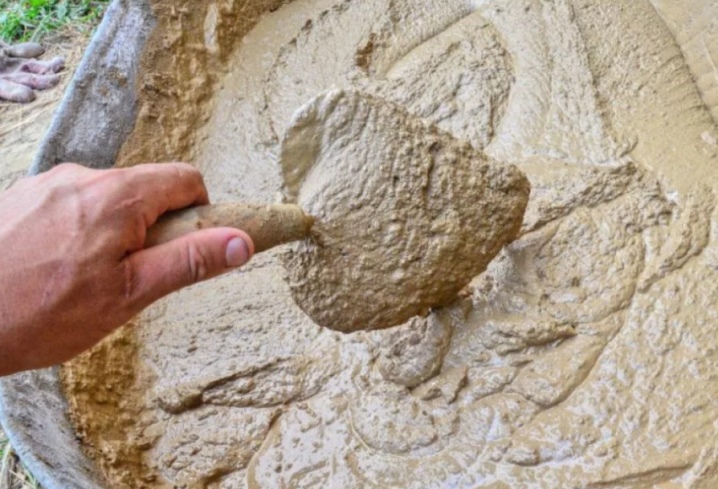
What is the most stable clay?
Chamotte clay is usually used for finishing furnaces and furnaces - it is of the best quality and resistance to cracking. This is a fire-resistant substance, so all stoves made from it are practical and durable. You can buy such clay on every construction market, it is sold in bags of 25 kg, it is inexpensive.
On the basis of chamotte powder, a working solution is prepared for surface coating; there are several types of mixtures.
- Clay. Chamotte and building sand are mixed at the rate of 1 to 1.5. Clay mass of this type is used for plastering the first layer and repairing breaks.
- Lime-clay. Consists of lime dough, clay, and quarry sand in a ratio of 0.2: 1: 4. The mixture is in demand during secondary processing, such a composition is highly elastic, therefore it resists cracking.
- Cement-clay. Formed from cement, "oily" clay and sand, taken in a ratio of 1: 5: 10. It is the most durable mortar. The mixture is in demand when plastering furnaces that are exposed to strong heating.
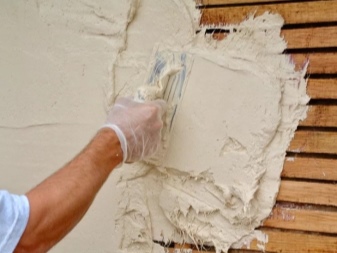
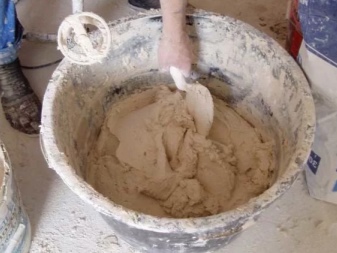
A special grout helps to increase the strength of the clay mixture; it is presented in a wide range in hardware stores. Of course, such a solution will not be cheap, but for facing fireplaces and stoves it will be the most practical solution. However, if you do not have the opportunity to make such a purchase, try making its analogue with your own hands.
This will require:
- clay;
- construction sand;
- water;
- straw;
- salt.
The clay must be thoroughly kneaded, kneaded, filled with cool water and kept for 12-20 hours. After that, a little sand is injected into the resulting solution. In the course of kneading the working components, table salt and chopped straw are gradually introduced to them. Clay with sand is taken at the rate of 4 to 1, while 40 kg of clay will require 1 kg of salt and about 50 kg of straw.
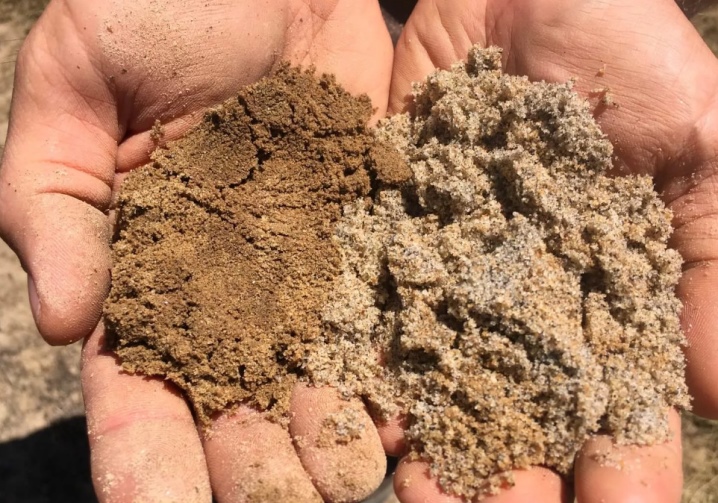
This composition can withstand heating up to 1000 degrees and not crack.
To prevent the clay from cracking, many bath owners use heat-resistant glue. It belongs to the group of ready-made facing mixtures, it is intended for the installation of fireplaces.The main advantages of the composition are resistance to high temperatures and durability.
This glue consists of fire-resistant types of cement and chamotte. Nowadays, manufacturers offer adhesive mixtures of two types: plastic and solid. The first type is relevant when sealing cracks, the second is preferred when plastering the entire furnace surface. The main advantage of this composition is its quick drying, therefore it is recommended to mix the solution in small portions.
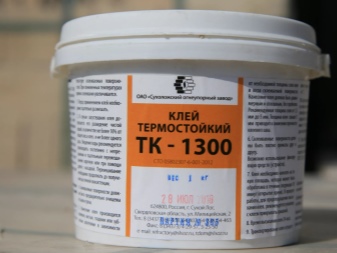
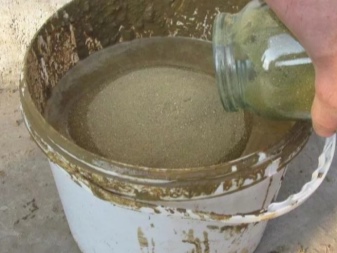
The comment was sent successfully.