Clinker panels for the facade: technical characteristics and subtleties of installation
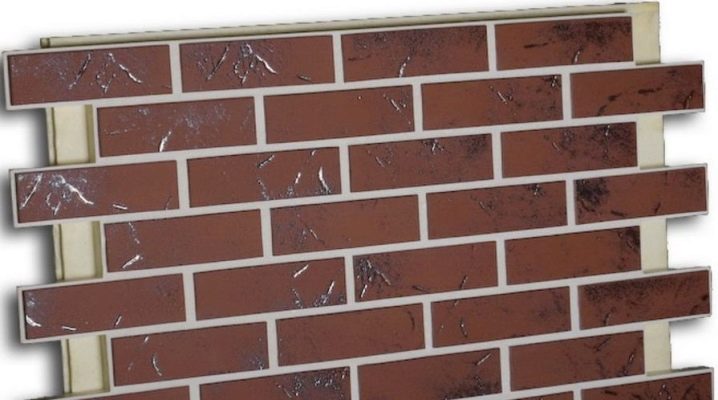
Clinker panels are a popular type of facade decoration. The material was developed and launched into production by specialists from Germany more than 40 years ago, and since then it has taken its rightful place in the market of building and finishing materials.
Specifications
The technology for making clinker has been known for a very long time and consists in extrusion processing of shale clay, after which the products acquire high performance qualities and surpass clay and concrete materials in terms of strength and frost resistance. Such cladding can often be seen on the facades of residential buildings and architectural monuments.
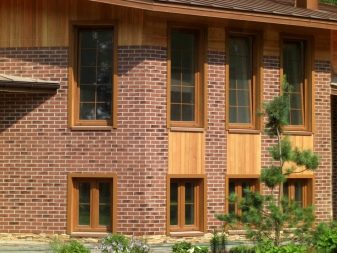
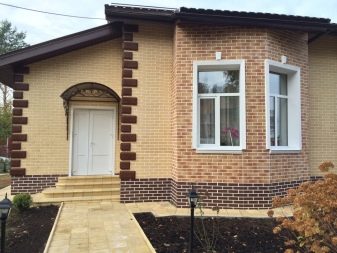
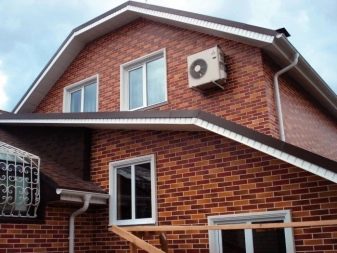
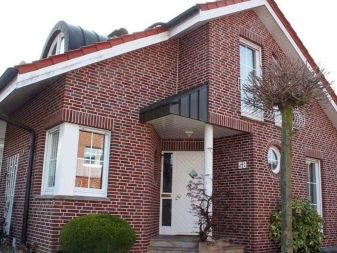
Clinker panel is a multi-layer module consisting of polyurethane foam sheet with a thickness of 2 to 8 cm, on which a ceramic decorative layer is fixed. Thus, the clinker panel is a unique finishing material that harmoniously combines decorative properties with a powerful insulating effect. The technology for the manufacture of tiles, which consists in placing ceramic blanks in special forms, followed by filling with a polyurethane foam composition, completely excludes delamination of the panel during operation.
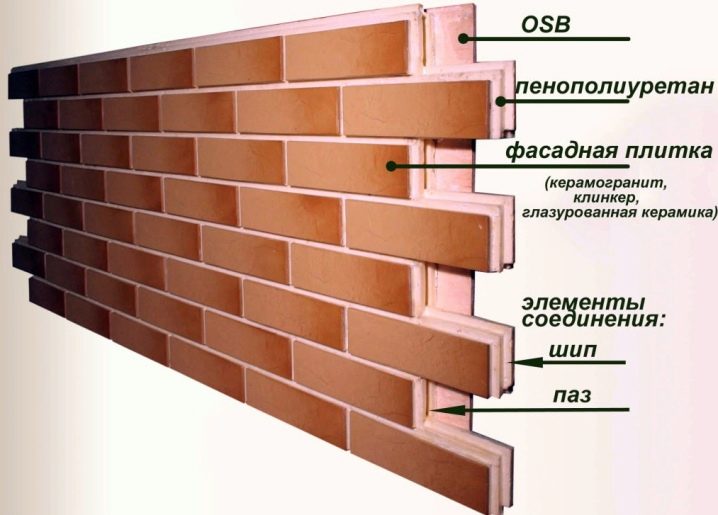
The size of the slab depends on its design and purpose, and averages 1090x359 mm. The cost also varies depending on the size, the number of layers and the manufacturer. The most expensive are German models. Their price reaches 12 thousand rubles per square meter. Italian companies offer products for 7 thousand rubles, and Polish manufacturers produce more budgetary collections, which cost an average of 5 thousand rubles. Domestic products are considered the most budgetary option. So a square meter of a panel, the basis of which is extruded polystyrene foam, can be purchased for only one and a half thousand rubles, polyurethane foam models will cost two and a half thousand, and panels that do not have insulation are sold for 1900 rubles.
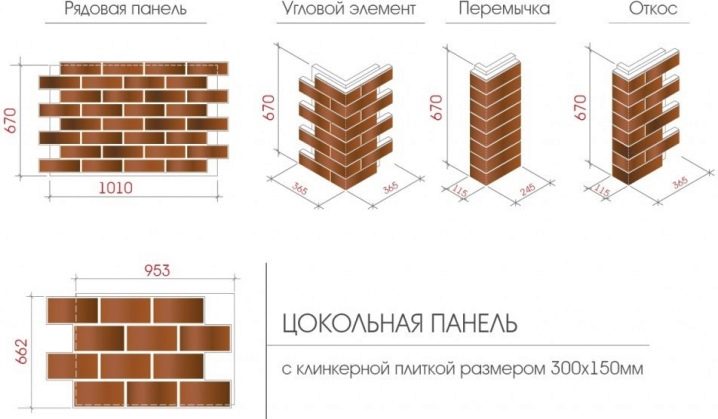
Advantages and disadvantages
High consumer demand and a large number of positive reviews are due to a number of indisputable advantages of this material.
- The design of the panels allows for a seamless facade cladding. This has a beneficial effect on increasing heat saving and makes it possible to significantly save on heating of housing. The thermal conductivity index of a clinker slab with an 8 cm thick insulation layer is equal to the thermal conductivity of a 70 cm wide brickwork or a 40 cm thick aerated concrete wall.
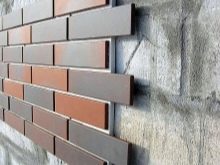


- Monolithic panels have an attractive appearance and eliminate the need to plaster facades. The material is produced in a wide assortment with a wide variety of colors and textures, which greatly facilitates the choice and provides ample opportunities for the implementation of bold design solutions. The clinker layer is made in the form of brickwork or stone, and can have both smooth and rough texture. The relief surface looks most impressive: it further increases the visual similarity of the clinker panel with natural material.
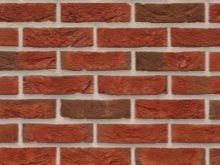
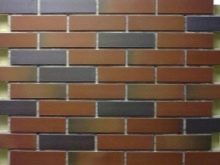
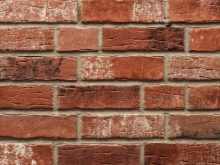
- Simple installation and easy maintenance. Thanks to the universal “tongue-and-groove” fastening system, the facade cladding does not require the use of expensive tools and the involvement of specialists.
- The panels are highly resistant to ultraviolet rays, and therefore do not lose their original appearance for a long time, and do not require measures for their restoration and repair.
- The materials are not of interest to insects and rodents, and are not susceptible to mold and mildew.
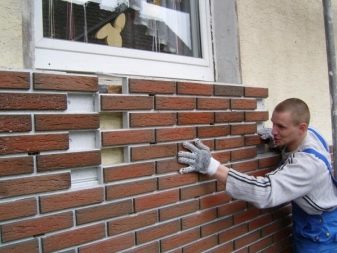
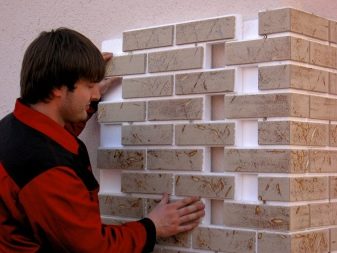
- The presence of special gaps on the reverse side of the double-layer panels provides the necessary ventilation of the facade, which makes it possible to do without the installation of additional ventilation equipment.
- The tight connection of the panels to each other guarantees the absence of cold bridges, the presence of which can lead to the accumulation of condensate and waterlogging of the facade.
- The high soundproofing properties of the material will reliably protect the home from extraneous noise.
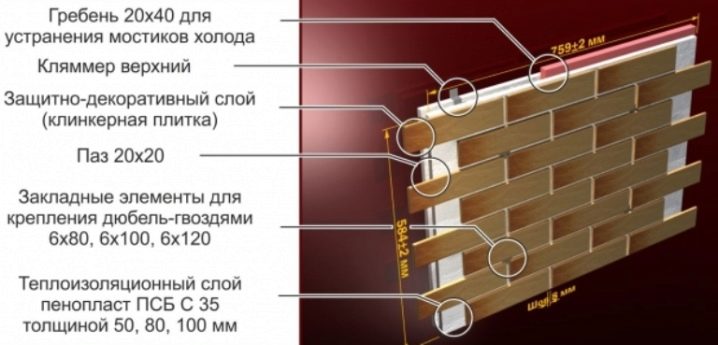
- The increased resistance to aggressive external influences of the environment allows the panels to be used in any climatic zone. The material tolerates temperature extremes well, is not afraid of excess moisture and can last more than 50 years.
- The panels are lightweight, so that clinker cladding does not significantly affect the foundation and load-bearing walls.
- Possibility of installation in any season. The only limitation is the application of inter-grouting. Its installation can only be carried out at positive temperatures.
- The presence of additional elements for the decoration of external and internal corners, windows and openings greatly facilitates installation and gives the building a finished look.
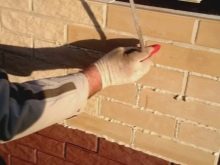
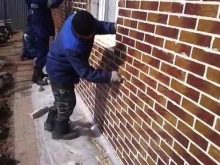
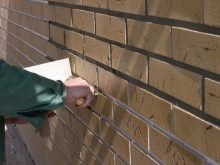
The disadvantages of the material include its high cost, which is especially noticeable when facing buildings with two floors and above. The downside is the fragility of the clinker layer. Ceramic coating does not withstand mechanical stress and strong impacts, has low fracture strength and requires particularly careful storage, installation and transportation. There is also a poor vapor permeability of the panels, which, if the installation rules are not followed, can lead to excessive moisture in the facade due to the formation of condensation.
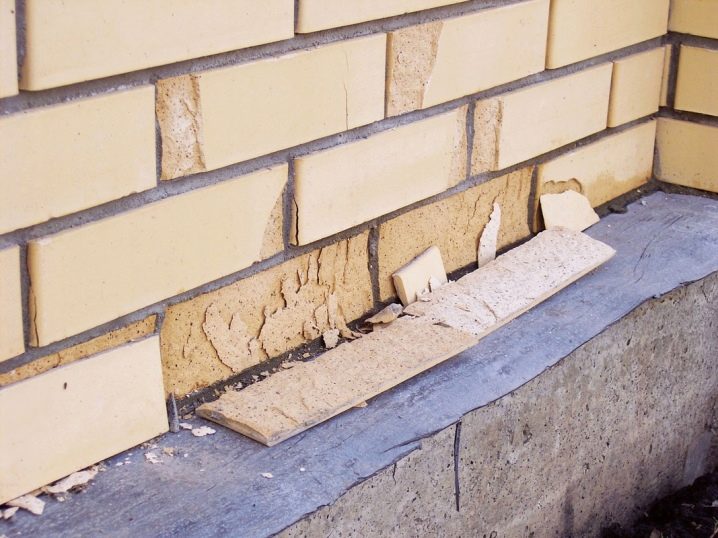
Varieties
Clinker panels are available in two- and three-layer versions. Three-layer models consist of a ceramic layer, expanded polystyrene and an additional heat-insulating base, with the help of which they are attached to the facade. An additional layer can be made of fiber cement, glass magnetic or oriented strand board. Fiber cement is characterized by environmental friendliness, good strength and durability. The glass-magnetic base attracts with flexibility and makes it possible to clad curved walls, and a slab on a wooden base has high noise and heat insulation properties, is lightweight and low in price.
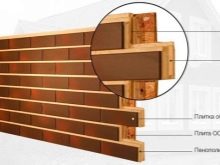
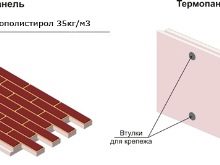
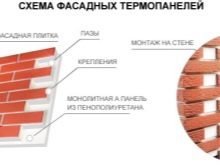
Each slab, regardless of the number of layers, has special holes and fixing grooves. In the process of production of three-layer models based on expanded polystyrene, a technology is used that provides closed perforation, which provides the finished product with a minimum vapor exchange. However, it should be borne in mind that the existing vapor permeability indicators are insufficient for full ventilation, therefore, clinker panels are not recommended for finishing the facades of wooden houses.
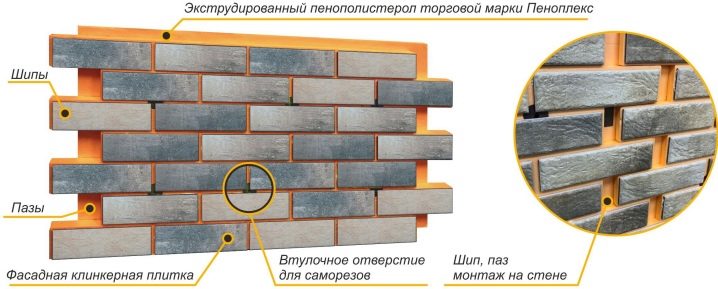
Two-layer models consist of a clinker decorative layer and a base made of OSB or DSP, and are intended for cladding facades that do not require insulation, or for those buildings where insulation has already been installed. Their main advantage relative to three-layer slabs is good vapor permeability, which is due to the absence of an insulating layer. Thanks to this quality, the walls of the facade have the ability to breathe, and excess moisture is freely drained outside. The service life of lightweight panels is 25 years.By location, the panels are divided into thinner wall and thick basement options. The height of the ceramic layer of the latter can reach 1.7 cm.
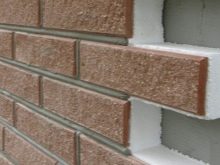
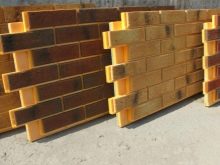
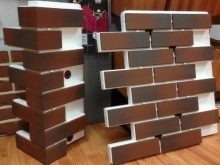
Subtleties of installation
Facing the walls of the building with clinker panels should begin with the preparation of the wall surface. To do this, it is necessary to remove all protruding elements in the form of air conditioners and shutters, remove the previous facing coating and treat the surface with an antiseptic and a primer. Then, you should proceed with the installation of the crate, which is necessary when installing a ventilated curtain wall and with large irregularities in the wall. The frame can be constructed from wooden bars or aluminum profiles. Wood planks should be pre-treated with special compounds that prevent rotting.
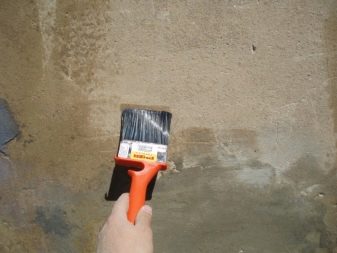
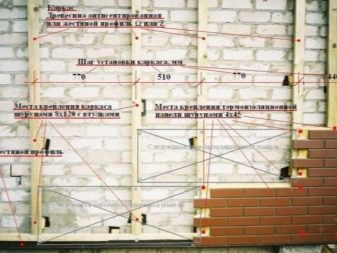
The guides must be fastened with self-tapping screws; the use of brackets is not recommended. Initially, the lower horizontal rail is installed, which should be placed at a distance of 20 to 40 cm from the ground and check its location using a building level. Each panel should be located on three vertical bars, therefore, when calculating the pitch between the slats, its dimensions must be taken into account. The gap between the bars and the wall is filled with polyurethane foam. After the installation of the lathing is completed, you can proceed to facing the facade with panels.
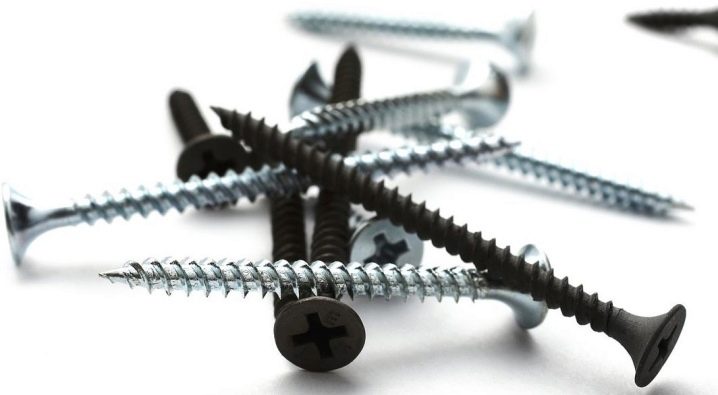
The installation of three-layer panels should be started from the bottom corner, moving from left to right. To do this, you need to install the panel on the first rail from the ground and fix it with dowels. Further installation is carried out on self-tapping screws and is made round. It is possible to proceed with the installation of each next row only if the installation of the previous one has already been completed. For each laid row, polyurethane foam should be poured. This will increase the rigidity of the structure and provide a more tight connection between the rows. The finishing of the slopes is carried out synchronously with the main cladding. After the installation is completed, the interpanel seams should be coated with frost-resistant putty.
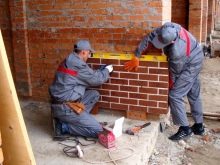
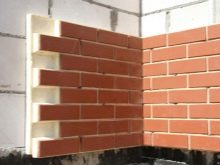
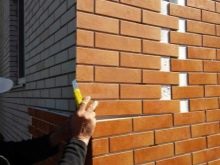
Lighter two-layer models without insulation are fixed to a wall or frame using an adhesive obtained from a dry mortar or foam glue. This type of installation has restrictions on the air temperature, which is regulated by the manufacturer of the used adhesive. Usually this figure corresponds to -10 degrees.
Clinker facade panels are a versatile option for finishing buildings. Combining excellent decorative qualities and high heat-saving characteristics, they allow you to stylishly and effectively decorate the facade and make the house warm and cozy.
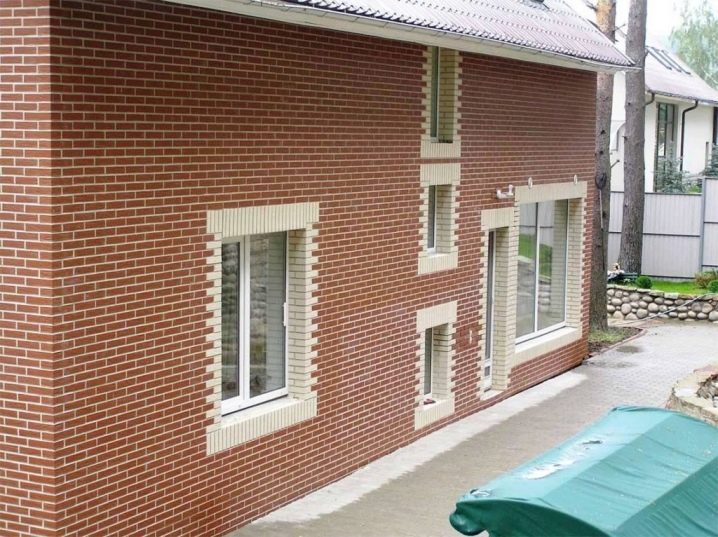
A detailed overview of clinker tiles and panels is in the video below.
The comment was sent successfully.