Thermal insulation of facades: types of materials and installation methods

When building and designing the facade of a house, it is not enough to worry about its strength and stability, about external beauty. These positive factors in themselves will instantly depreciate if the wall is cold and becomes covered with condensation. Therefore, it is extremely important to think over high-quality thermal protection and choose the most suitable material for it.
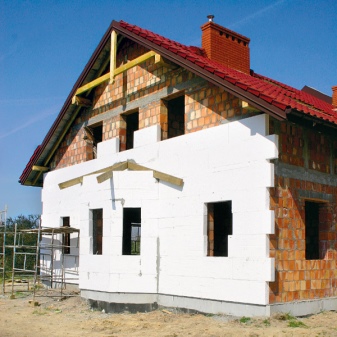

Thermal insulation methods
Thermal insulation of facades solves four main tasks at once:
- preventing cold in winter;
- prevention of heat in summer;
- reduction in heating costs;
- reduction of current consumption by fans and air conditioners.

The device of a heat-insulating layer from the outside is considered the most correct step by all technologists without exception. Professionals insulate dwellings from the inside only if external thermal insulation cannot be used at all for some reason. As practice shows, outdoor work:
- reduce the impact of weather and other adverse factors on the main structures;
- prevent moisture condensation on the surface and in the thickness of the wall;
- enhance sound insulation;
- allow the house to breathe (if everything is done correctly and the choice of material is accurate).

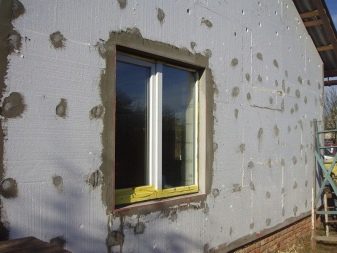
Wet plastering is more in demand than other schemes, and the overall cost and ease of implementation will allow it to remain the most popular option for a long time. The "pie" includes, in addition to the heat-shielding material, polymer-based glue, reinforcing structure and decorative trim. The formation of a hinged frame is mandatory for a ventilated facade and this inevitably makes the entire building heavier.
A prerequisite for the reliable operation of such a two-layer type of walls is to leave a gap through which air will circulate. If left unchecked, moisture will soak into other insulating materials and damage the walls themselves.

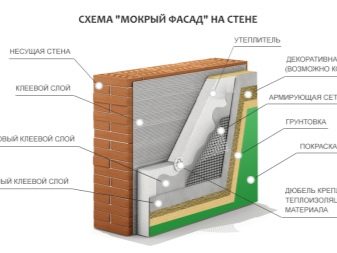
Another scheme is heavy plastering. First of all, panels are installed, which basically block heat from leaving the outside, and then a plaster layer is applied. It may seem that such a solution is better than a wet facade, because there are no restrictions on the density of materials. But at the same time, the quality of the insulator should be as high as possible.
Amateur builders often resort to this method, since it allows you not to level the walls to a perfectly smooth state.


If you need to insulate the facade of an old house for year-round use, the simplest solution is thermal insulation for siding. It is not only reliable and effective in preventing heat loss: the outer shell can look extraordinarily graceful; other options rarely achieve the same result.
A prerequisite is the formation of the frame. It is created by using either wood or steel parts treated with protective agents. Then a layer of a vapor barrier is always put, and only after covering it with thermal protection does it come to decorative panels.


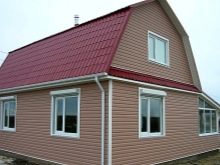
All of the above techniques are intended primarily for brick, panel or expanded clay concrete block houses. Wooden facades cannot be insulated with polymeric materials. Mostly fibrous structures are suitable for them. It is important to observe a number of conditions for thermal insulation:
- the readiness of the house at least to the level of the roof;
- the end of construction shrinkage;
- preliminary waterproofing and insulation of foundations;
- the end of the installation of windows, ventilation and all communications that enter the walls (out of them);
- optimal weather (no severe frost, significant heat, wind and any precipitation).


It is also recommended to complete the rough finishing of the interior, concreting and pouring the floors, and preparing the wiring. The walls are studied in advance, and even with the independent installation of thermal insulation, the advice of experienced builders will not be superfluous. When choosing a scheme, one should think about how to reduce the number of cold bridges to the limit. Ideally, there shouldn't be any at all. Warming with clay and straw is allowed only on wooden walls, but this is already an archaic approach, suitable only in isolated situations.
All components must be closely related to each other, therefore the selection of heat-insulating, vapor-barrier and waterproofing materials must be carried out simultaneously. It is not at all necessary to contact professional builders to obtain the necessary information. Most of the situations are successfully solved by purchasing completely ready-made insulation circuits, which are already completed with fasteners and other equipment in production. Working with such kits comes down almost exclusively to following the manufacturer's instructions. It will only be necessary to calculate the need for materials and not be mistaken with the choice of a specific type.


It is necessary to insulate panel facades taking into account such considerations as:
- favorable or unfavorable climate conditions;
- the intensity of precipitation;
- average strength and speed of winds;
- affordable budget;
- individual features of the project.

All these circumstances directly affect the choice of a suitable insulation option. It is better to contact the Criminal Code or a partnership of owners for drawing up an estimate. Outdoor work is most often entrusted to industrial climbers (you can do without their help only on the first floors). A membrane permeable to water vapor must be placed under the mineral wool.
If polystyrene is chosen for the insulation of any house, it is imperative to demand from the sellers certificates for the conformity of the material with the G1 flammability level (too often expert checks reveal a violation of this requirement).
If expanded clay concrete is covered with expanded clay slabs, it is necessary to check that their thickness is at least 100 mm, and the sheets themselves are laid tightly, excluding the appearance of seams. Vapor barrier when insulating such blocks is strictly required. Above expanded clay concrete walls that do not have external finishing, it is recommended to build on a brick cladding structure for greater energy efficiency. The resulting gap is filled with various insulation materials.
If you have no desire to resort to complex and time-consuming brickwork, you can use insulating blocks with cladding applied in an industrial environment.
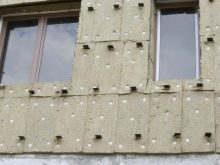
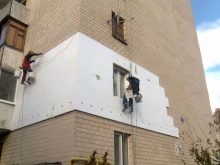

Types of materials
Having dealt with the basic schemes of facade insulation, you now need to find out what materials can be used for this purpose, and what are their specific parameters. According to professionals, it is very useful to use polyurethane foam. Since the composition is fully prepared for work in industrial conditions, it remains only to apply it using cylinders. Judging by the reviews, the assurances of the manufacturers of balloon-borne polyurethane foam about the combination of thermal protection with sound insulation are fully consistent with the truth. The strength and increased elasticity of the resulting polymer composition when it comes out has long attracted the attention of builders.
The polyurethane foam very quickly covers a large area and at the same time enters even the smallest gaps. It cannot rot or become a breeding ground for microscopic fungi.Even when exposed to open fire, the foam material only melts, but does not ignite. If it overlaps the metal base, it provides reliable protection against corrosion.
At the same time, one should beware of using polyurethane foam in places where direct sunlight or water can affect the material.


Sibit houses, which are quite popular now, can be insulated in the same way as any other buildings. Both wet and ventilated facades are acceptable. Professionals recommend covering the underground part with extruded polystyrene foam or other heaters that are impervious to water.
Fresh masonry, until 12 months have passed, is best left alone. If insulated before the end of this period, the sibit will not have time to dry and will become moldy.
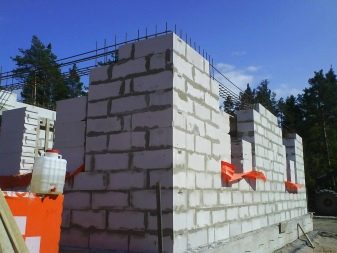

If it is impossible to slow down the construction for this time (and most often it happens), it is worth insulating with the help of EPS. Its layer is displayed above the ground, above the blind area by about 0.1 m. The fact is that if you just bury an uninsulated stone, it will not dry anyway, soil waters, found even in the driest earth, will greatly interfere with this. The base will be destroyed very soon.
The above-ground segment does not need to be overlapped so that it dries out. It is also recommended to warm up and ventilate the basement in the winter months, do not carry out wet work; water vapor impermeable plaster can be applied over EPSS.
If a house made of sibit or other material has served for some time, the drying problem disappears by itself. Then you can consider the possibility of insulating the facade with sandwich panels. A prerequisite is the use of film vapor barriers and the organization of ventilation gaps. Good protective properties are demonstrated by roofing material and glassine, which are applied to the walls themselves. High-density materials located in the circuit above the insulation should be protected from the wind.

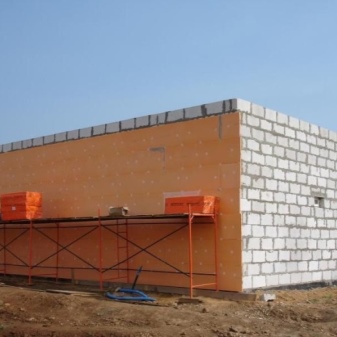
Returning to sandwich panels, it is worth emphasizing such their undoubted advantages as:
- mechanical fortress;
- reliable cover of the underlying layers from external influences;
- incombustibility;
- suppression of noise;
- ease;
- protection of metal parts from corrosion.



Sandwich panels are often recommended for wooden buildings that have been in operation for a long time. In them, not only cold containment is a problem, but also external protection of the external circuit that has weakened over many years. Due to the wide variety of panel formats, it is not difficult to select the ideal option for a specific purpose.
Modern enterprises have launched the production of panels with a wide variety of outer shells. There is aluminum, stainless steel, fibrous and particle boards, plywood, and sometimes even gypsum board. The advances of technologists make it possible to protect products from ignition by using a non-combustible layer.
A simultaneous combination of the highest practical and decorative characteristics is achieved by choosing steel sandwiches with an outer polymer layer. Those interested can even order an imitation of any natural stone.

During installation, the panels should be positioned so that the insulating fibers form a right angle with the sheathed base.
Purchasing a specialized tool will only bring savings in the long run. After all, there is no other way to cut sandwich panels in the required way quickly and efficiently, without unnecessary losses.


Insulation for outdoor use is often covered with clinker tiles. You can imitate its appearance on a wooden base using three methods.
- The actual use of clinker bricks. It is acceptable if the base of the foundation is wide.
- Use of facade thermal panels covered with a tiled layer. No cement is required.
- Plastic panels (the cheapest and easiest way to install).


It is worth mentioning the Lobatherm concept, which provides for the fixing of the insulation on the facade, the formation of a reinforcing layer based on a special mixture and glass mesh. You will also need to finish the surface with brick-like clinker tiles. A similar system is suitable for covering stone, brick, foam concrete and aerated concrete walls.
If all work is done correctly, you can guarantee the viability of the coating for at least half a century without repair.
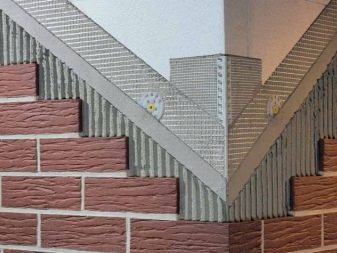
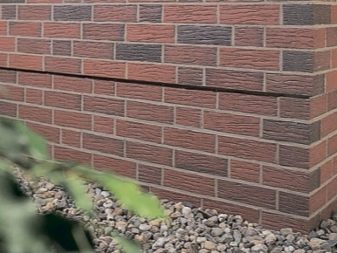
Heat-insulating plaster and finishing with special paint can be used only as an aid to enhance the protective properties of the main insulation. There is no need to seriously talk about insulation with cardboard and even more practical kraft paper.
Both materials provide wind protection rather than heat retention. The mass of cardboard is three times worse in its thermal characteristics than stone wool and is one third inferior even to an ordinary pine board. In addition, problems can be associated with the fire hazard of the material and the fact that favorable conditions for insects are created inside it.


It will be much more practical to insulate the facade with penofol, that is, foamed polyethylene foam. The advantage of this solution is that it effectively suppresses heat transfer by both convection and infrared radiation. It is not surprising, therefore, that an impressive level of thermal protection has been achieved. 100 mm of penofol are equal in their characteristics to 500 mm of a high-quality brick wall. In addition to these advantages, mention should be made of:
- ease of installation;
- impermeability to steam;
- reliable protection against overheating by the sun's rays.
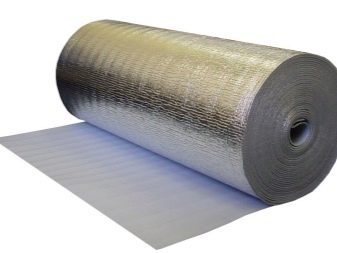

Such qualities make it possible to do without other waterproofing and vapor barrier coatings, significantly reducing the cost of repairs or construction. Penofol category A is distinguished by a one-sided arrangement of foil, it is not intended for the facade. But it gives excellent results when insulating the roof and various communications. Discharge B has foil on both sides, intended for thermal insulation of floors between floors in the first place. Finally, C materials can be used in the most awkward areas.
There are a number of other options - in some, the foil is supplemented with a mesh, in others there is laminated polyethylene, in others, the polyethylene foam is given a relief structure. The foil is capable of reflecting up to 98% of the thermal radiation incident on its surface. Therefore, it effectively copes with protection from the cold in February and from the heat in June or July. Penofol can be simply glued to a wooden base. It is also allowed by technology to attach with a stapler to staples or nailing.


It should be borne in mind that foamed polyethylene foam cannot "boast" of great rigidity, therefore, after its application, it is impossible to put additional finishing layers. Staples are worse than glue because they compromise the integrity of the material and prevent it from performing its basic functions. In addition, truly full-fledged insulation is possible only when using penofol in close conjunction with other protective materials.
Mechanically damaged areas of the insulator are restored manually using aluminum tape.

The use of felt, of course, has a much longer history than the use of penofol and other modern insulators. But if you look at the practical characteristics, then there are no particular advantages. The only plus that is beyond doubt is its impeccable environmental safety. If, nevertheless, a choice is made in favor of this particular material, the service life of the thermal protection will delight the owners.
You should definitely take care of impregnation with fire retardants in an organization licensed from the Ministry of Emergencies.


Styrofoam
While experts say relatively little about felt, the foam attracts much more attention.The controversy around him is very heated, and some are trying to prove the superiority of this material over others, and their opponents proceed from the assumption that it is insignificant. Without getting into the discussion, one thing can be said: foam is an attractive solution only with careful surface preparation. It is strictly imperative to remove from the walls everything that can interfere with work.
This also applies, among other things, to decorative elements, of which there are a lot of used houses for a long time. Experienced builders will certainly check the plaster for strength by tapping the surface. A plumb line or a long cord will help to identify various deviations from the plane and the slightest flaws. There is not even a special need to use a building level. Defective areas of the plaster layer must be removed, then a chisel is used to remove the influx of concrete and excess mortar in the gaps between the bricks.


You cannot mount the foam on a wall covered with oil paint, you will have to sacrifice a layer of it. Naturally, mold and greasy stains, traces of rust and salt seeping out will be categorically intolerant. Cracks deeper than 2 mm must be primed with compounds that penetrate into the thickness of the material. The preparation is carried out with the help of a maklovitsa brush. If irregularities of more than 15 mm are found, after priming, plaster is applied along the beacons.


The starting strips of the frames must correspond in size to the width of the insulating material. It is undesirable to make strips of glue continuous, dotted application will help to avoid the appearance of air "plugs". Laying and pressing the foam sheets to the wall should be immediately after applying the glue, otherwise it will have time to dry out and lose its bearing capacity.
All sheets are checked in turn by level, otherwise very serious errors may occur. If necessary, adjust the position of the slab, remove it completely, clean off the old glue and apply a new layer.

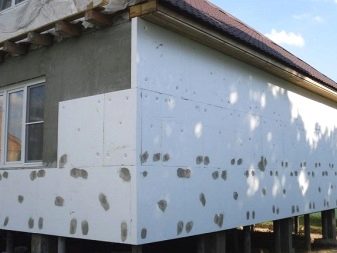
Glass wool and ecowool
Glass wool and ecological wool are very similar to each other, but there are also significant differences. So, glass wool is dangerous to health and is not very convenient in everyday work. It is categorically not suitable if you need to insulate the walls from the outside using the wet facade method. The advantage of glass wool is its absolute chemical inertness. In domestic conditions, there are simply no substances that would react with this insulation.
The low density allows you to avoid significant overloading of the foundation, which means that glass wool is compatible even with lightweight buildings. Its serious drawback is its high hygroscopicity, but there is no need to fear the action of open fire and strong heating. Even foil glass wool must be covered from the outside with layers of vapor barrier and waterproofing, otherwise it will not be able to fulfill the task. Glass wool can also be used as part of a ventilated façade, then it is laid on the crate or a spacer is attached between its parts.
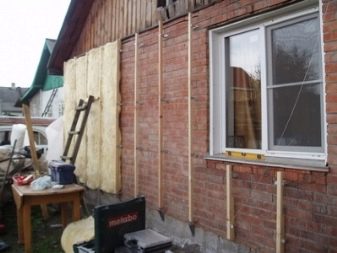
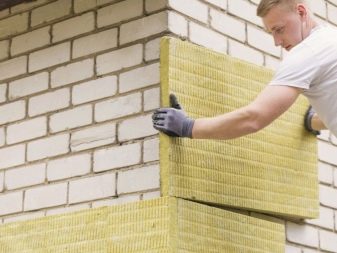
From the cotton layer to the wall surface, you should not put any films or membranes, they are still superfluous there. Moreover, the presence of glass wool in the gap between the vapor barrier layers will only make it inevitable that it will be damaged by the liquid. If such a mistake is made suddenly, you will have to disassemble the whole cake, dry the insulation and strictly observe the technology at the next attempt. Ecological cotton wool is similar in its properties, except that it is not so prickly and completely safe to use.
The choice between these two materials depends more on the specific brand than on the species.

Basalt slabs
Thanks to the latest technological developments, basalt wool can be used not only for filling inside walls. On its basis, excellent insulation boards are created.Andesites, diabases and other rocks formed as a result of volcanic activity are the initial raw materials in their production. After melting at temperatures of 1400 degrees and above, which is replaced by blowing in a rapidly moving gas stream, the liquid mass turns into threads.
Basalt slabs are widely used in the process of insulating frame houses, while the impact of street noise is also reduced.


The outer walls are covered with a preliminary crate. Always maintain a slight gap before finishing plating. To keep the plates on the rough wall, they are attached with self-tapping screws. The next layer will be a film that restrains the wind, and lastly, siding, wall paneling, porcelain stoneware or any other coating to taste and financial possibilities will be mounted.
The advantage of slabs based on basalt wool is excellent resistance to mechanical loads, including those arising during the installation of the front finish.


Polyurethane foam
PUF can be presented not only in the form of foam pumped into high-pressure cylinders. Professionals use a more complex mixture, applied to the facade using specialized equipment. One lease of it can significantly increase the cost of repair work. Not to mention the fact that it will not be possible to perform all the manipulations qualitatively, it is always necessary to entrust such processing to real masters.
It is important to take into account that the thermal conductivity of polyurethane foam (0.2 or even 0.017 W / mx ° C) found in advertising brochures refers only to ideal conditions and is never achieved in practice.
Even with the strictest adherence to technology and the use of the latest equipment, such figures can be reached only when the cells are filled with inert gases prohibited for environmental reasons. In most cases, on Russian construction sites, you can find polyurethane foam, the foaming of which is provided by water. Such material cannot reach even half of the advertised indicators.
If a coating with open cells is sprayed, less money is spent on finishing and insulation, but the protective qualities are reduced even more. And finally, gradually, even inside closed cells, processes occur that contribute to the volatilization of gases and their replacement by atmospheric air.
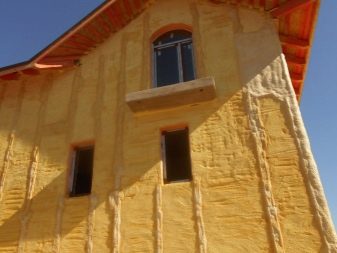

A high level of adhesion is not guaranteed for every type of polyurethane foam or on every surface. It is, in principle, unattainable with a polyethylene backing. Big problems await those who, under the influence of the manufacturers' promises, decide that the wall surface need not be prepared at all. Thus, a thin flaking plaster layer or dusty areas or greasy spots can devalue all efforts being made. Professionals always apply polyurethane foam only on perfectly dry walls, but for the formation of a structure with open cells, dosed moisturizing will be even useful.

Surface preparation
Do not assume that the condition of the facade insulated from the outside is very important only when applying polyurethane foam. Rather, the opposite is true: whatever is written in the marketing materials, careful preparation for work only increases the chances of success. The likelihood that the coating being formed will become unusable is significantly reduced. Often it is necessary to prepare walls for tiles, because they:
- looks great in almost any situation;
- durable;
- resistant to negative external influences.

Alas, the simplest way of leveling is unacceptable for street walls - installation of drywall sheets. Even their moisture-resistant varieties are not reliable enough, because they are not adapted to the effects of negative temperatures. You will have to use a variety of leveling mixtures.
Before using them, you still need to remove dust and dirt, eliminate the largest protrusions mechanically.Any mixture, including plaster, is mixed and applied strictly according to the manufacturer's instructions, "experienced advice" is categorically unacceptable here.
When using lighthouses, the very first ones are placed at the corners, and when the mixture hardens on the wall, it will be possible to stretch the threads, which will become the main guidelines for setting the remaining profiles. Important: the plaster is prepared in such an amount that it can be completely consumed in 20-30 minutes. In some species, the life cycle of the solution may be longer, but it is not worth the risk, it is more correct to leave yourself a margin of time.
To ensure that the tile does not fall off, the plastered wall will certainly be primed. The choice of colors and textures depends purely on personal preference.



It does not matter whether tiles are applied on the outside or not, when insulating a concrete house there are subtleties and nuances. So, before applying expanded polystyrene, the concrete layer must be covered with an antiseptic and a primer. Instead of plaster, leveling is often done with a mixture of cement and sand. Calculating the need for insulation material is not difficult, you just need to know the total area of the facade and prepare a supply of sheets by about 15%. Medium-sized sheets are optimal for work: very large ones are difficult to fasten, and if you take small ones, you will have to create a lot of joints that make the structure unreliable.
It will be necessary to take five dowels for all plates and provide for another 5-10% margin, as the practice of experienced builders shows, it is almost always used up. For your information: it is advisable to apply the antiseptic several times, this will only improve the result. With glue, not only the corners are always smeared, but also the very middle of the sheet; dowels are screwed in the same places. The styrofoam sticker is led from either of the two lower corners. The mixture will finally dry in 48-96 hours.

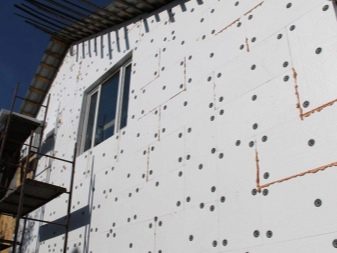
After the glue has dried, a reinforcing mesh is attached to the surface of the plates using the same composition. Then this mesh will need to be coated with glue on top, level it with a spatula and putty. Next comes a layer of primer, and above it finishing materials (most often siding panels) are placed. Concrete can also be insulated with special plaster. But by itself, this option is recommended only for the warmest regions of the Russian Federation.
A special approach is required when insulating a foam block home. Sometimes it is performed by lining the walls from the outside with blocks of the same low-density foam concrete. Reinforcing bars are used to connect the two planes. Such work is long and laborious and must be done by qualified bricklayers. For maximum efficiency, mineral wool, cellulose insulation, or liquid foam concrete are poured into the gap.

A good result is achieved when using polymer boards of various compositions, especially those finished with plaster. Poor vapor permeability can be compensated for by increasing ventilation. If you plan to cover the foam blocks with a ventilated facade, it is difficult to find a better solution than traditional mineral wool. The face layer is often siding or some kind of timber formed by metal parts.
Before installing the expanded polystyrene, it is worthwhile to mount a steel plate at the bottom, it will not only support the plates, but also prevent rodents from reaching them.
Experienced builders take care of roughening the polystyrene boards. They are rolled from the reverse side with needle rollers or manually incised using a knife. The glue can be applied to the surface of the boards with spatulas or notched floats. Important: before installing insulation with a thickness of 5 cm or more, it is worth spreading glue on the wall itself. This will increase costs, but is justified by the increase in the reliability of fixing the material.
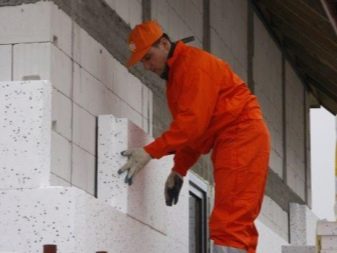
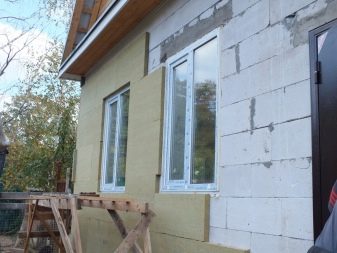
Before plastering work, only those metal nets that are resistant to alkalis can be installed.When insulating a monolithic house made of wood concrete, one must be guided by the climatic conditions of a particular region. In a number of places, the thermal characteristics of the blocks are good enough so that there is no danger of frost damage or hypothermia at home. But even under ideal conditions, it is required to carry out external finishing, for which plaster mixtures or siding with a vapor barrier are used. This solution allows at least to bring the dew point to the outer surface of the blocks.
In addition to wood concrete, there is another material that is safe in terms of thermal properties - aerated concrete. But, even having built a house from gas silicate blocks, it is not always possible to avoid additional insulation. The vast majority of construction crews use standard mineral wool and foam sheets.
The first option is better than the second, because the low cost does not justify the low vapor permeability. Other types of insulation are not at all competitive when working on the facade of aerated concrete housing.


Subtleties of installation
Do-it-yourself insulation of private houses with wall defects exceeding 2 cm is possible only after leveling the surface with cement solutions. After drying, these solutions are covered with a primer that stops destruction. For the installation of a ventilated facade, the base can be leveled using brackets. If mineral wool is used, the insulation can be installed using a wooden slatted frame. Anchors will help to strengthen the attachment to the walls.
On uneven surfaces, it is worth using a special mineral wool, which contains layers of different density. The least dense layer must be attached to the wall so that it goes around, envelops irregularities and makes the structure smoother. Then there will be no problems with the penetration of cold to the surface.
The finishing technology of the overlying layers can be any, as long as it is convenient. If polymer boards are applied to the wall, all layers are shifted horizontally by 1/3 or 1/2.
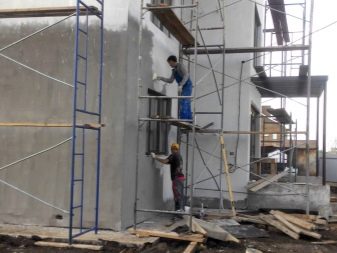

It is possible to increase the adhesion of the slabs by cutting off the corners of the side edges. To reduce the need for fasteners, screwing dowels into the edges of the joined parts will help. It is recommended to pay attention not only to the type of insulation, but also to ensure that its thickness is correctly determined, sometimes, the calculation with the help of professionals only saves money.
It is necessary to be guided by information about the coefficients of thermal resistance assigned for a particular settlement. The maximum layer of insulation must be mounted on top of reinforced concrete, because it is this material that has the highest thermal conductivity.

Useful Tips
The types of systems for external facade insulation of a stone cottage are approximately the same as for concrete surfaces. Ventilation gaps and air vents must be discharged strictly to the cold side, that is, outside. There should be at least one ventilation openings for air intake in each room. Then, both in the summer and in the winter months, the microclimate inside will be ideal. When insulating buildings from a cinder block, many experts recommend PSB-S-25 expanded polystyrene.
In the process of finishing cinder concrete, you cannot do without decorative plaster. Holes for dowels in this material are drilled exclusively with a perforator. External lines are measured with a laser or water level. The same requirement applies to other buildings, even dacha or garden outbuildings.
Full-fledged insulation of the premises attached to the houses is achieved only in a complex manner; for the same verandas, special layers must also be mounted under the floor and inside the roof overlap.


For information on how to insulate the facade of a private residential building, see the next video.
The comment was sent successfully.