What are granite paving stones and where are they used?
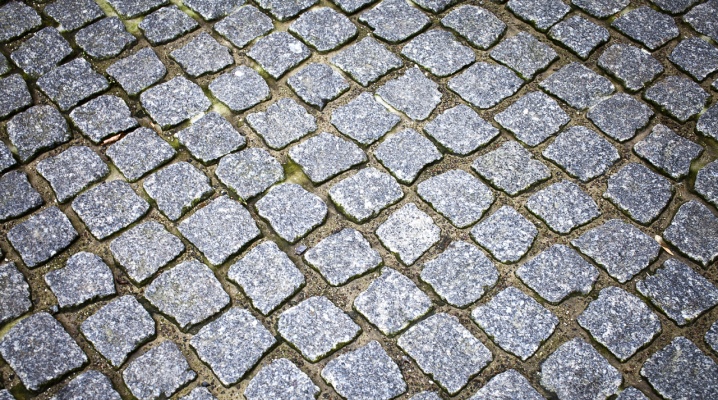
Granite paving stones are a natural material for paving paths. You should know what it is, what it is, what advantages and disadvantages it has, as well as the main stages of its laying.


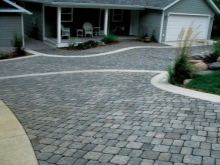
What it is?
The laying material has long been used in urban planning. It is based on igneous rock that emerged from the bowels of volcanoes under high pressure and temperature. Granite paving stones are natural stone of identical size and shape, which has undergone special processing. Its shape may vary.
Granite is a natural mineral, the strength of which is higher than concrete and other synthetic materials. Its compressive strength is 300 MPa (concrete has only 30 MPa).
A high-quality road surface is made of granite paving stones, densely laying the fragments on a sand (sand-cement) base.

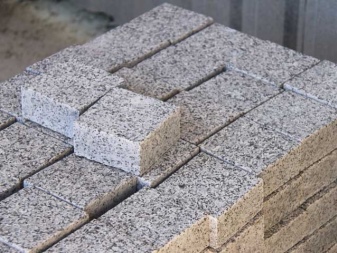
Advantages and disadvantages
The magmatic origin of the stone determines the main properties of the paving stone, explains its demand from the domestic buyer. This material has many advantages.
- It is environmentally friendly, does not pose a danger during installation, operation.
- Granite paving stones are highly durable. It can withstand colossal loads, is resistant to mechanical damage, high pressure and shock. The hardness of granite on the Mohs scale is 6–7 points (for iron and steel up to 5). The material is resistant to wear and scratches. It retains its original appearance for a long time.
- Due to their high hardness, granite paving stones are durable. Its service life is calculated in decades. In terms of durability, it surpasses analogues with cement components (better than asphalt, concrete). It does not age over time, does not crack, does not get dirty. It is not afraid of ultraviolet radiation, therefore it retains its original color for many years.
- Granite has a unique natural texture, which gives the paving stone a solid appearance. The mineral has minimal water absorption and high frost resistance. It is not destroyed by atmospheric precipitation (rain, hail, snow). The percentage of water absorption of granite is 0.2% versus 8% for concrete and 3% for clinker. It is practically indestructible.
- Granite paving stones are distinguished by a wide range of color shades. It is gray, red, black, greenish, brown. This allows you to create coatings with unique patterns. The coating does not react to road dust. It does not change its properties when it interacts with chemicals.
- The material has a rough type of front surface. Its advantage is the absence of puddles and water spills from rain. The water immediately goes into the cracks between the numerous fragments, without remaining on the surface of the stones.
- The laying technology allows the paving to be transferred to another place when the base subsides.
- Paving elements can have not only different shapes, but also sizes. This allows you to create patterns of varying complexity from them. For example, it is possible to create track boundaries. Moreover, they can be not only linear, but also curvilinear (winding, rounded). It is suitable for creating unique compositions and structures.
- Granite paving stones are stylistically versatile. Looks great with any style of landscape design, suitable for paving on streets near houses and structures in different styles of architecture. Suitable for paving areas under which underground utilities are laid.



However, with all the advantages, the material has 2 significant disadvantages. The paving stones are heavy. In addition, individual paving slabs can be slippery in winter. Therefore, in winter, it has to be sprinkled with sand or chopped rock.
Description of species
Granite paving stones can be classified according to different criteria. For example, it may differ in the shape of the stones. It can be traditional rectangular or rounded. Tumbled variety is considered a non-standard type of material. Thanks to the rounding, it resembles an old stone that has been serving for several years. It is used for laying footpaths. The dimensions of the material and shape comply with GOST standards.



Granite paving stones are classified according to the method of processing. There are 3 varieties, each of them has its own characteristics.
Chipped
This type of material is considered the most ancient. It has been used since the days of Ancient Rome. It was with him that the paving of paved roads began. It is a cubic laying material with predominantly identical lengthwise edges. It was chopped from large chunks of granite, so there are irregularities on each face of the paving stones.
In comparison with other varieties, chipped building material has deviations from the specified dimensions. Its standard dimensions are 100X100X100 mm. Other parameters are less common (for example, 100X100X50 mm). The standard color of this building material is gray. It is laid with seams 1–1.5 cm (depending on the curvature of the stones).



These paving stones are used for simple paving, although it is extremely difficult to maintain linearity when working with such stones. It is also difficult to lay out drawings from them. To do this, it is necessary to re-sort a large number of stones, which is unprofitable for laying paving stones of the budget type.
However, this type of building material is in high demand. During its use, under the weight of vehicles and walking pedestrians, the surface is polished without violating the rough geometry. This coating has a retro effect.


Sawn-chipped
Sawed-chipped bars are called pencils. In their production, pieces are sawn from a granite slab. It is placed on special equipment and cut into strips of a given width. Subsequently, stone blocks are split into fragments of a certain thickness.
All the sides of the finished granite paving stones are flat. Her curves are only up and down (those that pricked). Thanks to this feature, the blocks of this paving stone can be placed close to each other. Parameters for a square shape are 100X100X60 mm, for a rectangular shape - 200X100X60 mm. In addition, the material can have dimensions of 100X100X50, 100X100X100, 50X50X50, 100X200X50 mm.
Modern technologies make it possible to saw granite slabs into elements of different shapes (conical, trapezoidal). This allows you to lay out a wide variety of patterns (up to triangular and round).


Full-sawn
This type of granite paving stone is considered the most beautiful, it is more expensive than other types. All its sides are as even as possible, which allows for installation with virtually no seams. There is also a heat-treated variety. It has a smooth but non-slippery surface.
This is a brick-shaped paving stone with smooth edges. It is sawn on stone processing equipment using diamond tools. The standard module size is 200X100X60mm. Produced on order in other sizes (200X100X30, 100X100X30, 100X200X100, 100X200X50 mm).


It is more expensive than other analogues. Due to high-temperature processing with simultaneous melting of marble chips, it acquires a rough surface type. Such paving stones are laid in a "herringbone" pattern, "sprawling", creating minimal gaps between the elements. The coating is practically seamless.
Polished full-sawn granite paving stones differ from granite tiles in their greater height. It has the shape of a rectangular parallelepiped. Chamfered sawn paving stones have a 5 mm bevel on all sides of the top edge.It is laid without seams, it is more often used in individual construction.


Applications
Granite paving stones are actively used for arranging sidewalks, paths, and other external areas. It can be installed wherever a beautiful, solid and heavy-duty outdoor surface is required. For example:
- when improving the city (for paving sidewalks, squares);
- in gardening facilities (for arranging sites and walking paths);
- in the private sector (for the arrangement of garden paths and adjoining areas);
- for laying in places of greatest stress (at level crossings).


In addition, granite paving stones are a practical material for arranging barbecue areas, parking lots, driveways (areas in front of commercial facilities). It is used for paving the blind area of houses.
Laying technology
It is possible to lay granite paving stones on different types of bases. In addition to sand and sand-cement base, it can be placed on a concrete base. The laying technology is similar to the laying technique of granite paving slabs. The process consists of a series of sequential steps with the obligatory preparation of the foundation. The paving base is prepared in a certain way.
- The boundaries of the site are correctly marked, taking into account the height of the curb stone, using stakes and cords.
- Excavation is performed. The depth of laying the base of sand and crushed stone is 15–40 cm, of concrete - 40 cm. Sod and fertile soil are laid separately.
- During excavation, a slight slope is made for the drain. The slope towards the drain is 5%.
- On the sides, earth is dug out for the construction of curbs.
- In order to prevent the appearance of vegetation, the bottom of the trench is treated with a herbicide. It will prevent the germination of plants that destroy the paving stones.
- The bottom is compacted. With a small amount of work, this is done manually. With a large one - with a rammer.
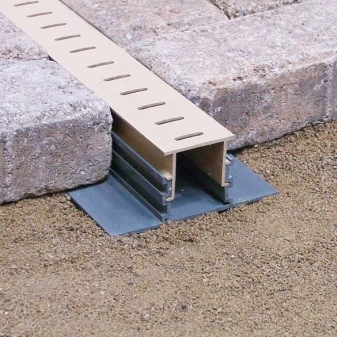

The further course of work depends on the type and structure of the base.
On the sand
The structure of such a laying consists of paving stones, sand and compacted soil.
- The compacted soil is covered with a geotextile, covered with a layer of sand of 15 cm (a margin for shrinkage is given).
- The sand layer is leveled, spilled with water, rammed with a vibrating plate.
- A cord is pulled at the height of the upper edge of the curb.
- Crushed stone is placed in the curb gutters, and cement mortar is poured on top with a layer of 1.5 cm.
- The curb is installed, leveled and concreted.
- Paving stones are laid according to the paving scheme. Where necessary, trim with a rubber mallet. The gaps are controlled with plastic inserts.
- Clean river sand is stuffed into the gap between the fragments.
- The surface is compacted with a vibrating plate, then it is moistened.
- After 2 days, the final compaction of the paving stones is performed.


On crushed stone
A large number of layers are required: paving stones, DSP, sand, crushed stone, compacted soil. The sequence of work includes a number of actions.
- The rammed earth is covered with a geogrid.
- Top covered with a layer of crushed stone 10–20 cm thick.
- Leveling and compaction of crushed stone is carried out.
- Install side curbs.
- Geotextiles are placed to delimit the layers.
- A layer of sand 10-15 cm thick is poured on top of the crushed stone. It is moistened and tamped.
- Then a layer of dry DSP is laid (5–10 cm thick).
- Start laying paving stones.
- The coating is poured with water from a hose. Watering should be moderate.
- To fill the joints, DSP is used as a grout. It is scattered on the surface. Residues are removed with a brush.
- Moisten the surface.


On concrete
For paving the areas with maximum load, you will need paving stones, central heating systems, reinforcement network, concrete, sand, gravel, compacted soil.
- The prepared base is covered with a geogrid, covered with rubble 15 cm thick.
- A layer of rubble is leveled, then tamped.
- Formwork with stakes is built using boards 4 cm thick.
- If the paving area is large, installation of expansion joints is performed.
- Mix the mortar and lay out the concrete. The layer thickness is 5–15 cm (with 3 cm reinforcement).
- Expansion joints are filled, treated with grout.
- Install curb stones.
- DSP is poured onto the concrete screed with a layer of 3 cm.
- Paving stones are laid.
- The surface is moistened, the joints between the tiles are filled with DSP (as when working with crushed stone).
- The coating is rammed with a vibrating plate.


Everything is excellent.
The comment was sent successfully.