All about the foundations for paving slabs
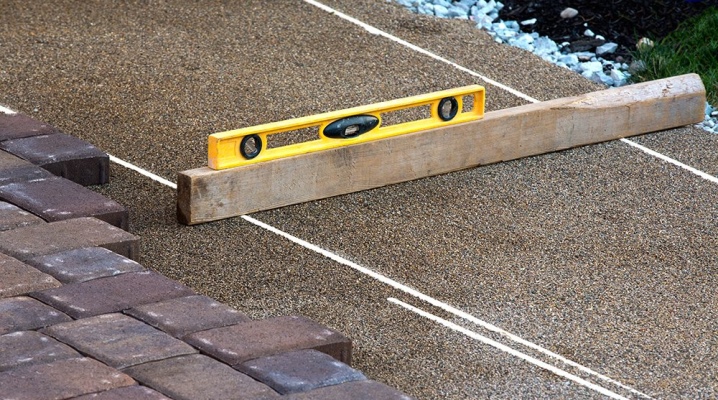
Arrangement of paths when laying paving slabs requires high-quality preparation of the base. From the material in this article, you will learn about the types of foundation, requirements for them, calculation of the material, the nuances of the work. In addition, we will show you how to properly make drainage and waterproofing with your own hands.
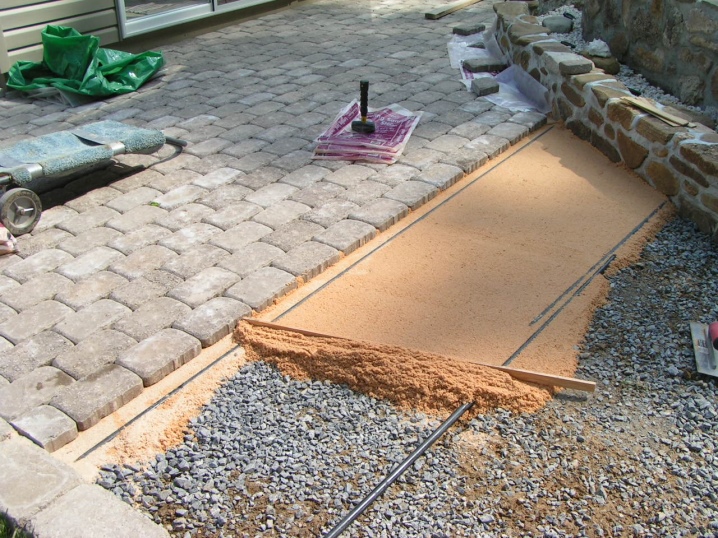
Primary requirements
The pie mounted under the paving slabs can be different. The support must be of high quality, otherwise the masonry may float over time. To prevent the slabs from falling on top of each other, it is necessary to comply with a number of requirements for the bases. The surface for laying should be flat, stable, strong, durable, buried in the ground. In addition, it must be waterproofed.
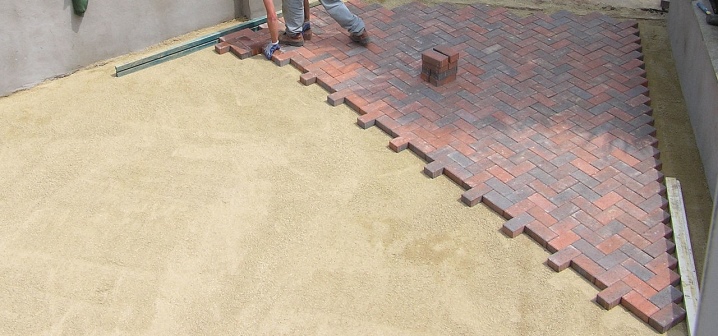
To begin with, it is worth considering the device of a drainage cushion. It will remove the accumulated moisture, preventing the destruction of the paving elements. This is a layer of drainage material that is placed on a prepared and compacted bottom.
To prevent water from entering from below, waterproofing must be carried out.
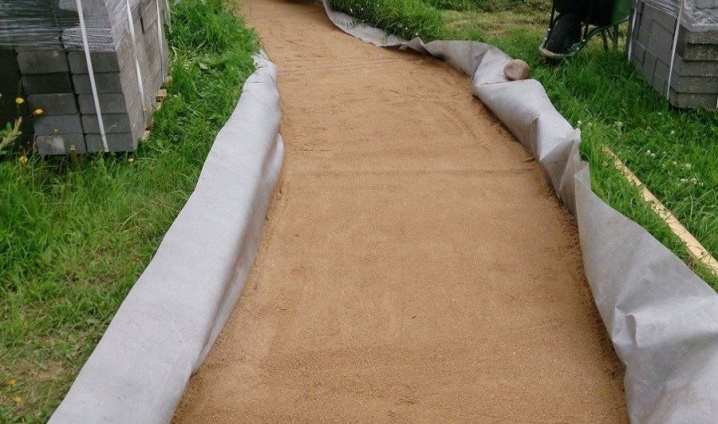
It is necessary to provide for the drainage of water entering the coating in the event of heavy rainfall. The gutter device is usually performed by creating a drainage groove under a slope. To make an even finish with identical seams, you will need to level each layer of the pillow.
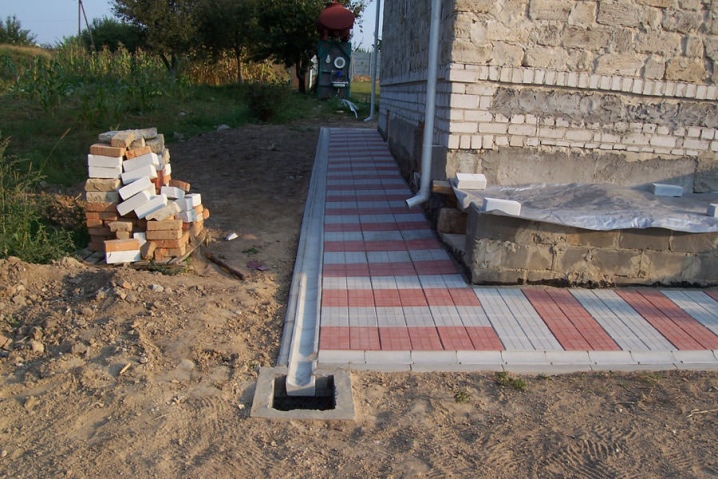
The base for paving slabs must exclude the displacement of the cladding elements, regardless of the load level. To equip sidewalk paths according to all the rules, you should use GOST 17608-91, SNiP Sh-8-76, SNiP Sh-10-75, instructions BCH-50-79, TU 400-1-190-79.
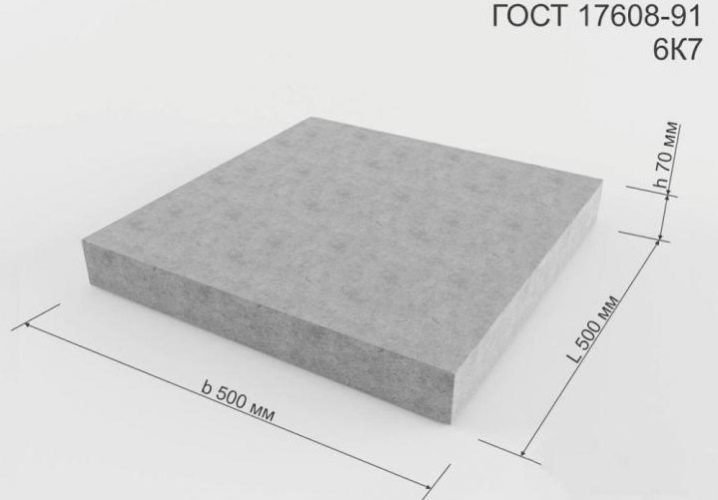
The structure of the device of prefabricated sidewalks for paving stones consists of several elements:
- underlying layer;
- base;
- tiled flooring.
As for laying on an old base, this issue is solved in different ways. If it is a tile, then its condition is assessed. Ideally, place the cobblestones on top of the pie you just assembled.
It is advisable to remove the old flooring, as it can cause deformation and premature destruction of the cladding.
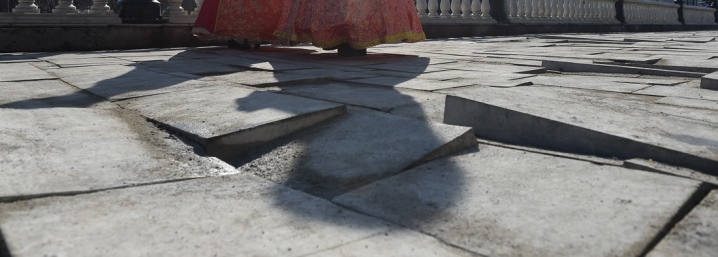
Views
The base for laying the facing material can be sand, sand-cement, concrete. Each type of material has its own characteristics. Regardless of the selected type of raw material, the cladding is done with the preliminary arrangement of the enclosing curbs.
Sand or fine screenings
Sand is used when tiles are laid under a standard volume of loads (for example, garden paths, footpaths).
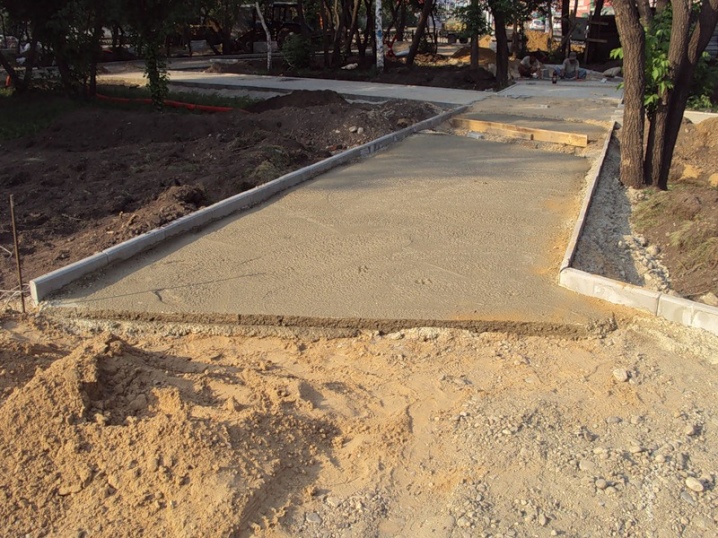
This type of base is excellent for water permeability, but it is not particularly durable. It is also bad that sand without gravel shrinks over time.
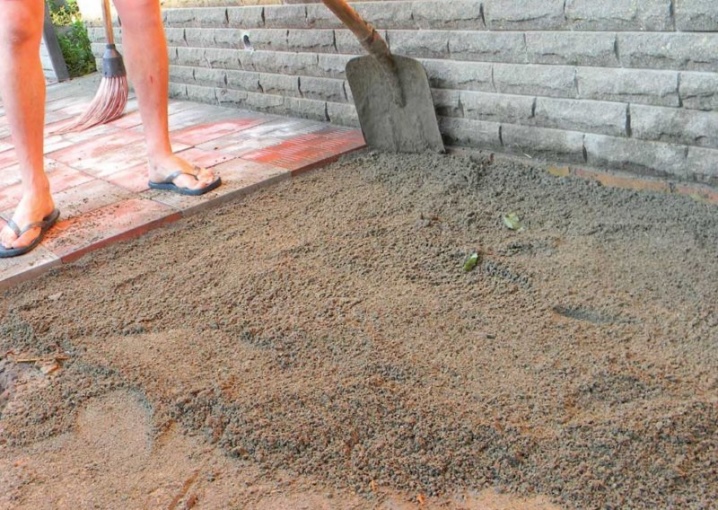
The thickness of the sand cake is made with this nuance in mind. In finished form, it is 7 cm. Sand filling should be carried out in 3 layers (each 2-3 cm). Each covered layer is leveled, watered, and then tamped. When the work is done by hand, more active sand flow is required.
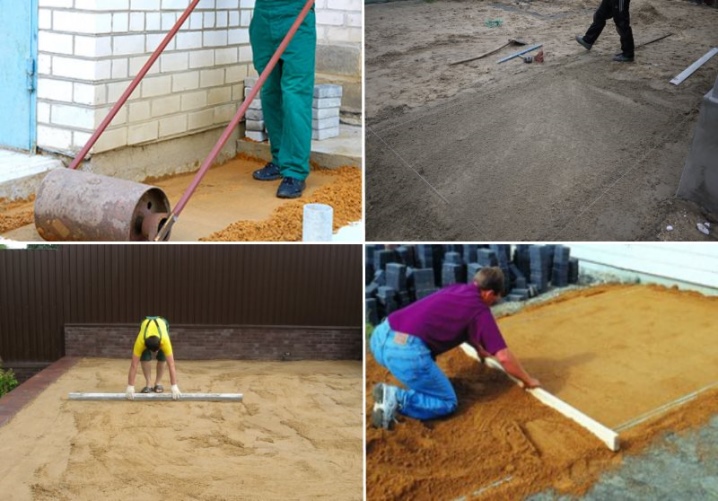
The top layer of the sand cushion is leveled with a plastering rule more carefully than others.
You cannot start laying tiles if the slope is not observed and the surface is uneven. This will affect the identity of the seams and the solidity of the coating.
Sand is a sealing material. Its top layer must be sieved. It is best to use river sand for installation. In this case, the tiles during installation will partially sink into such a pillow.
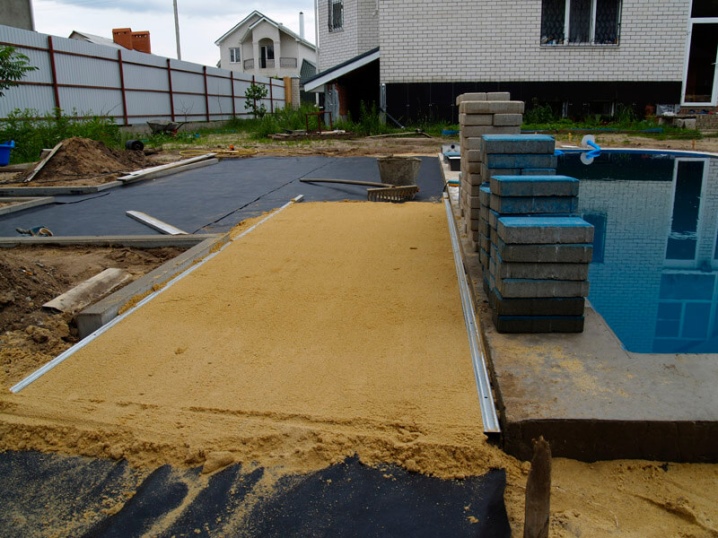
A mixture of cement and sand
In this case, a dry composition is used in the required proportions. The arrangement technique involves laying a gravel cushion. This type of foundation is considered the golden mean between sand and concrete. It is durable and reliable, while allowing moisture to pass through. Such material is better than sand alone.
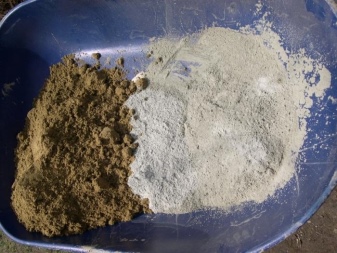
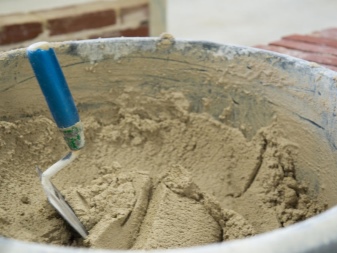
The sand-cement base is prepared for the installation of paving slabs of medium thickness. The overall structure of the cake consists of several layers: soil, sand, crushed granite, sand, dry mix (DSP). Paving slabs are laid on top, curbs and a drain are arranged on the sides.
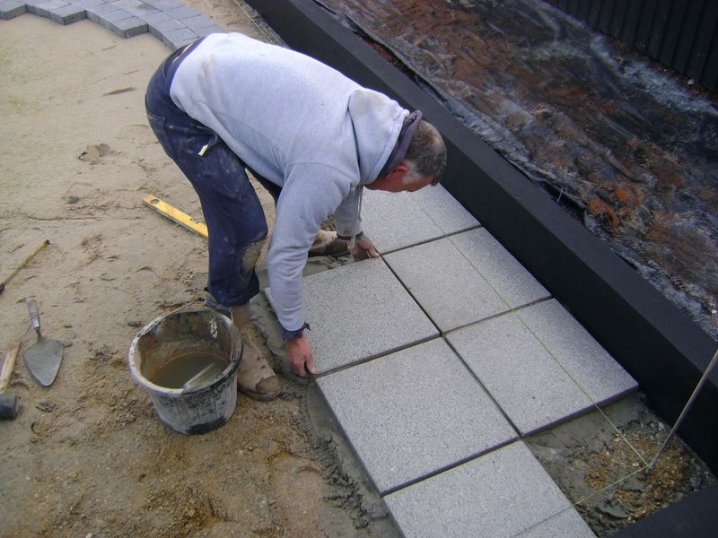
The device of such a base is performed according to the same scheme as the device of a sand cushion. The difference lies in the top layer, which is used as a dry mixture of sand and cement. This contributes to the creation of a monolithic pavement pavement.
To make the mixture, take 1 part of cement and 3 parts of sand. This layer is also tamped after backfill. If all the conditions for creating a base are met, a surface layer of a mixture of dry materials is formed on the surface of the geotextile.
It is necessary to install PCB strictly in dry weather immediately before laying paving slabs. This is because the cement hardens on contact with moisture.

Builders often cover the PCS layer in parts, while all the lower ones are covered and leveled completely over the entire area of the ditch.
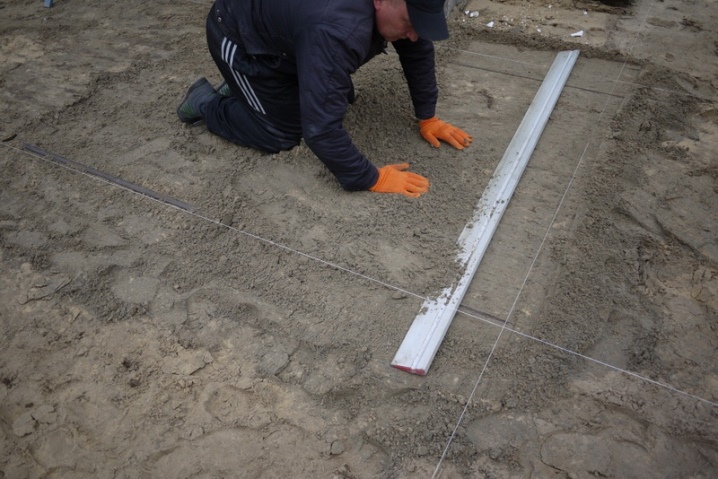
Concrete
Liquid building mixture is used in the construction of roads and access roads to houses and garages, car parking. In this case, a monolithic concrete screed is created. It helps to hide the unevenness of the base, excludes subsidence of the finished finish. This technology is used for tiled elements under heavy loads.
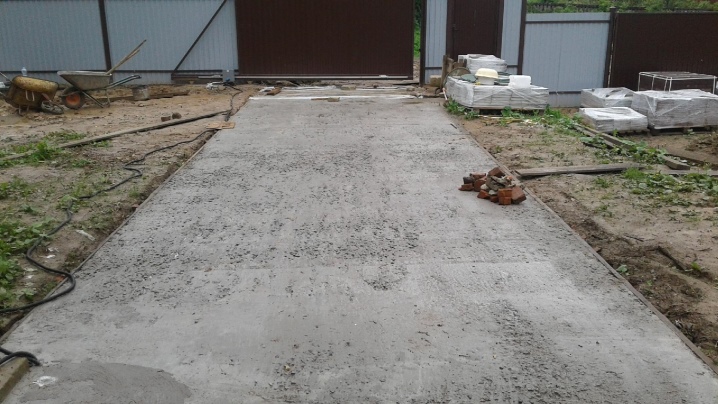
It is a sturdy, reliable, costly support. The concrete base is also chosen for the installation of thin slabs, which are attached with glue. Such a base is made after the installation of the formwork, reinforcement, installation of beacons. The formwork prevents concrete spreading during pouring if the upper level is higher than the ground level.
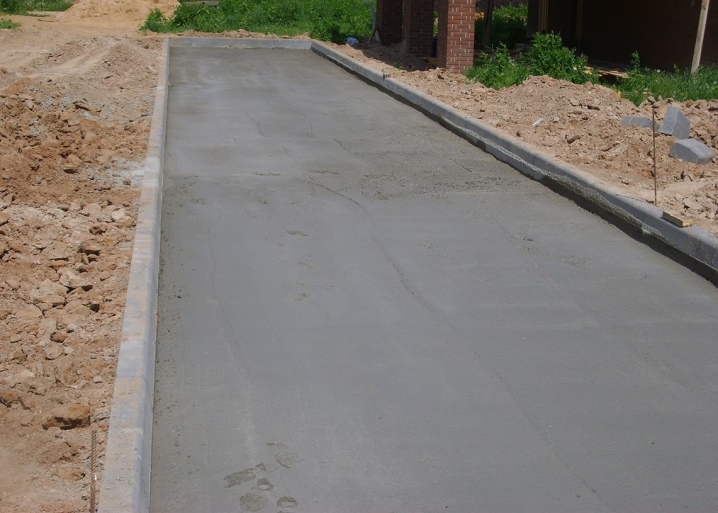
The installation of the formwork allows you to leave gaps for the further installation of the curbstone. The curb will keep the edges of the concrete pad straight.
In addition to planks, formwork can be made from plastic sheets. It can be fixed by means of stakes and spacers.
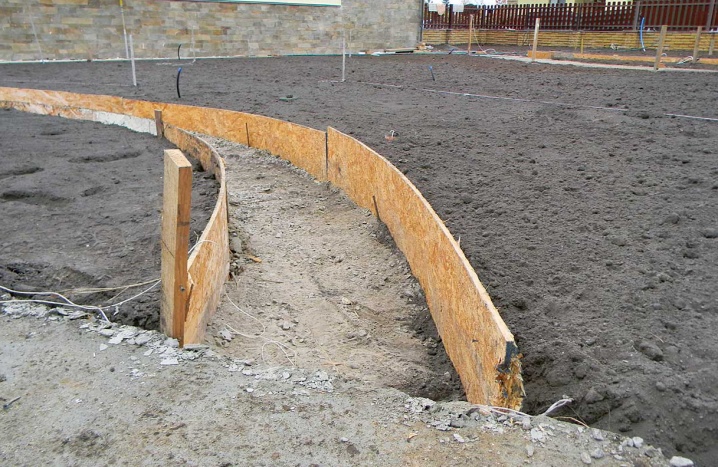
Reinforcing material (welded wire mesh) is placed on the bottom of the ditch, after which beacons are exposed. As beacons, a galvanized steel profile is used for mounting drywall. The lighthouses are fixed parallel to each other on a cement mortar.
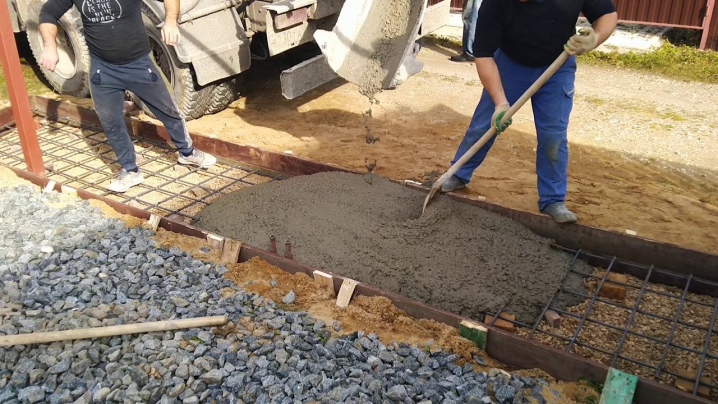
If a lot of mortar is needed to equip a concrete base, it can be ordered ready-made with delivery to the installation site.
If the farm has a concrete mixer, you can make the working solution yourself. The concrete base is poured in such a way that voids do not form in the mass.
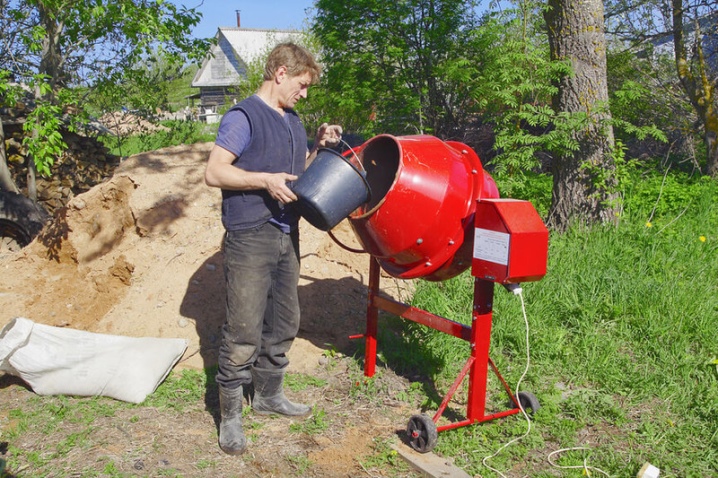
When the concrete is poured onto the mesh, the top edge must be leveled. If there is no plastering rule at hand, this can be done with a wooden lath. Filling is performed while maintaining expansion joints, compensating for possible thermal expansion. Wait until the concrete base is completely dry before proceeding with the installation of paving slabs.
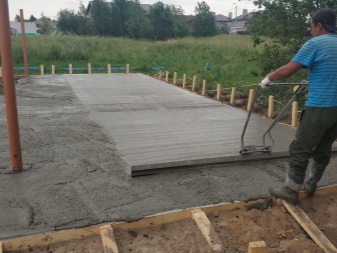
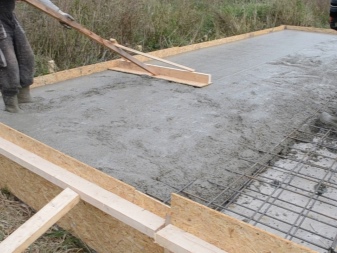
The consistency of the working solution must be correct. If the composition is too liquid or, conversely, thick, this will affect the quality of the pillow. The ratio of the components depends on the type of cement.
Failure to proportion will reduce the strength of the base. For work, cement M400 or M500 is used. First, dry components are combined, and after the composition becomes homogeneous, water is added.
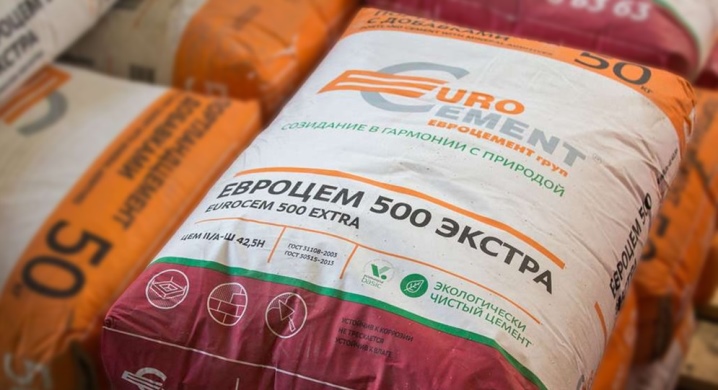
How to calculate materials?
To calculate the required amount of raw materials, use the formula for finding the volume. The result obtained is multiplied by the specific gravity of the material. The reinforcement is purchased based on the calculation of the assembly of the lattice rods with 20 cm cells. The number of border elements is determined by dividing the perimeter by the length of one module.
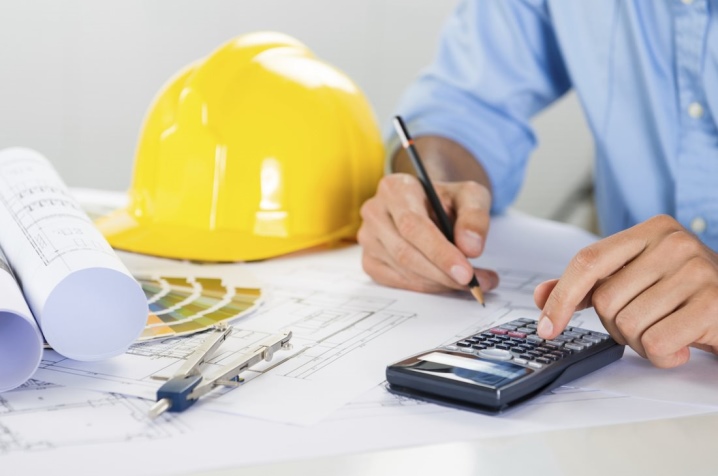
To correctly calculate the required amount of sand or crushed stone, you need to start from the device of the common pie. When laying on concrete, per 1 square meter, you need:
- sand - 0.15 cubic meters;
- crushed stone - 0.15 cubic meters.
When arranging paths, the dry mix takes about the same. When making light paths with a sandy base, the consumption is different:
- fine sand is needed 0.05 cubic meters;
- coarse sand or crushed stone - 0.1 cubic meters.
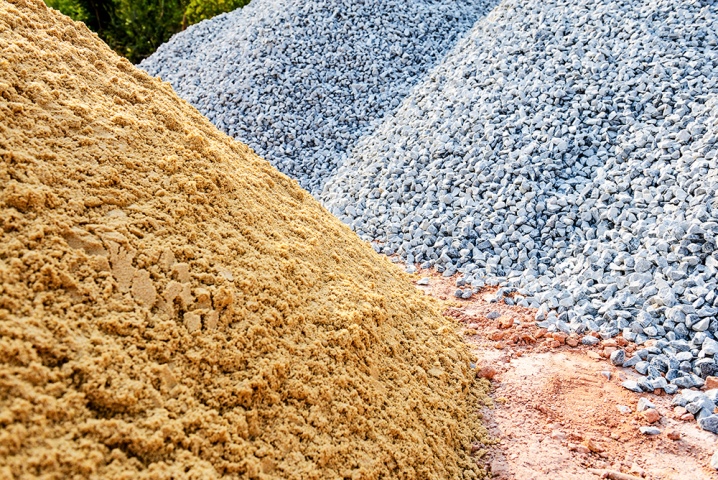
Excavation works
Having in hand the scheme of the planned finishing, taking into account the binding to the terrain and landscape, they are engaged in tracing. To do this, measure all sides, check the correspondence of the lengths and diagonals.
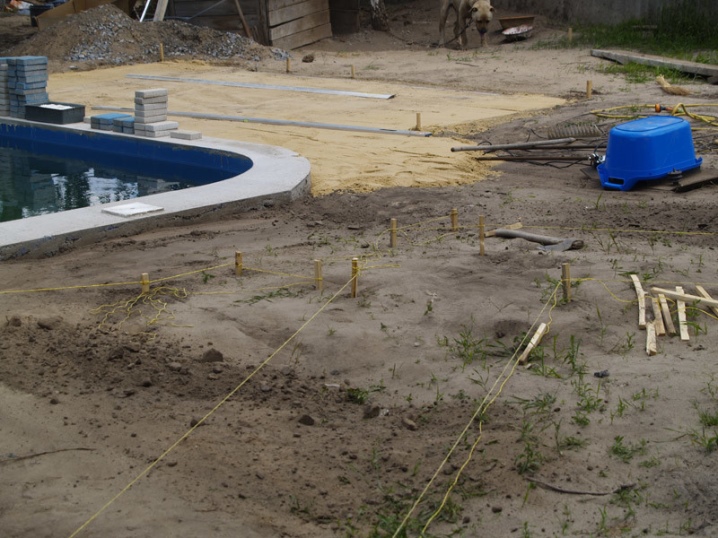
Regardless of the choice of the type of base, preparation begins with excavation. If you prepare the bed correctly, this will simplify the installation work and allow you to make the cladding as smooth as possible. The height of the soil layer to be removed depends on the type of base chosen. In this case, the total thickness of the layers to be laid is taken into account together with the tiles. The more there are, the more soil is removed.
When excavating, it is necessary to take into account the fact that the tiles must be laid flush with the ground (sometimes slightly higher). If it is lower, water will inevitably accumulate after heavy rainfall.
When performing excavations, the shrinkage of the used bulk materials and the soil itself is taken into account. The height of the excavation when arranging garden paths in the country and sidewalks is at least 20-25 cm. The base for areas with the greatest load must be reliable. If you plan to lay tiles for the parking area, you must remove a layer of at least 28-30 cm.
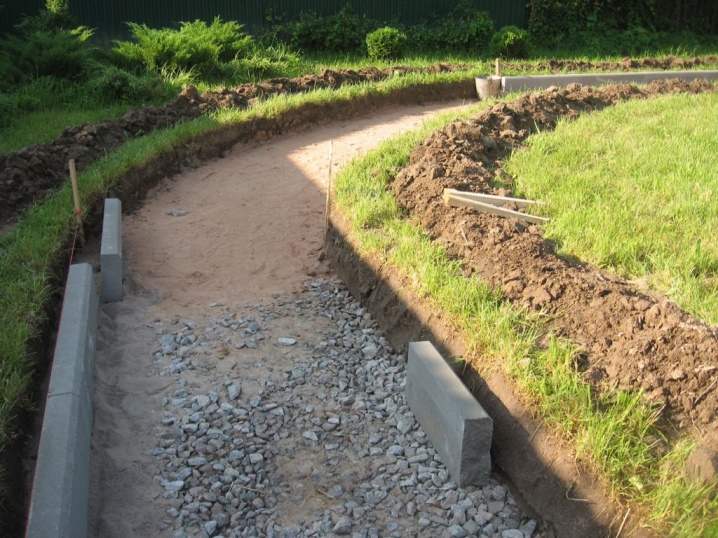
In the course of removing the land, they get rid of debris, stones, weeds. The fertile layer can be used for arranging beds or flower beds. Before laying drainage and waterproofing on the bottom, they get rid of the roots and everything that can later serve as a catalyst for the destruction of the laid paving stones. Large clods of earth break up, making the bottom of the ditch uniform.
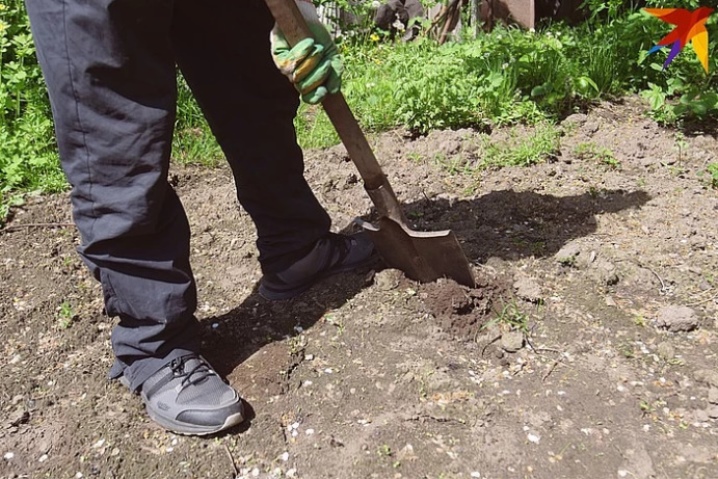
At the bottom of the trench, they form a slight slope in the direction away from the structure (up to 3%). The average slope for paving is 1 cm per linear meter. Then the bottom is rammed, giving the base more strength and reducing the percentage of earth shrinkage under the weight of the decks to be laid.
In the absence of an electric rammer, a compact compaction technique is used for compaction.
Next, they are installing the curb stone.
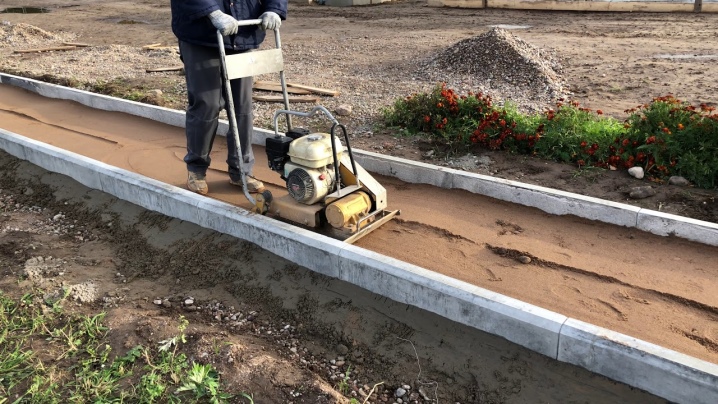
Drainage cushion
To prepare the trench for laying the track according to all the rules, use a layer of sand. The thickness should be at least 5 cm. It is distributed evenly over the entire trench bed. Then it is poured abundantly with water and compacted. The ramming is carried out using special equipment.
If it is not there, you can just wait for the wet sand to compact itself.
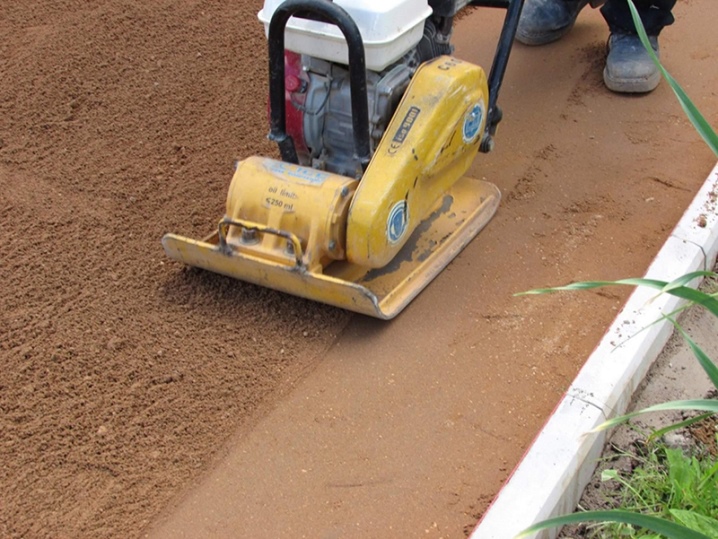
After that, they begin to lay the rubble. It is better to use material with a medium grain size. Large crushed stone will not be able to fill the base tightly. Given that it will sag over time, the original shape of the base will be broken. Too small stones are also not suitable for drainage: they will reduce the drainage properties of the crushed stone layer.
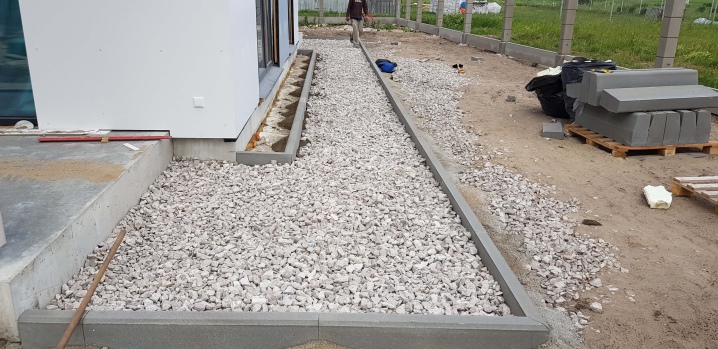
It is necessary to form a crushed stone layer with a tamper. If the interlayer is mixed with sand, then the base is moistened with water, then tamping is performed.
The thickness of the compacted drainage layer should not exceed 15 cm (2/3 of the total height of the sidewalk including the base).
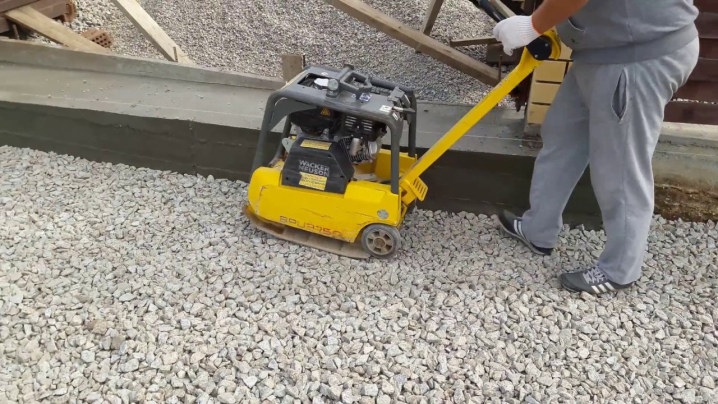
Instead of gravel, you can use gravel with a fraction of 2-3 cm. To improve the quality of the cushion, it is better to place gravel on the bottom in several stages. Compaction of thin layers is easier. If you use vibratory rammer equipment, work will be accelerated.
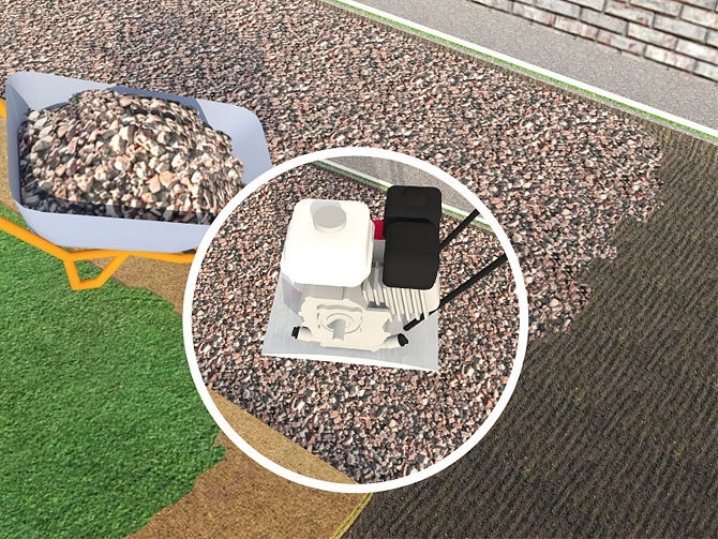
Waterproofing
The best waterproofing material is considered to be geotextile with a density of 150 g / m2. It is lined on the surface of the ditch after the drainage has been laid. It will prevent water from reaching the top layer. Geotextile has high strength, resistance to decay and decomposition, so it will protect the finish from moisture for a very long time. The geotextile fabric is laid with an overlap with the panels overlapping each other by about 12 cm (the total overlap is 25-30 cm).
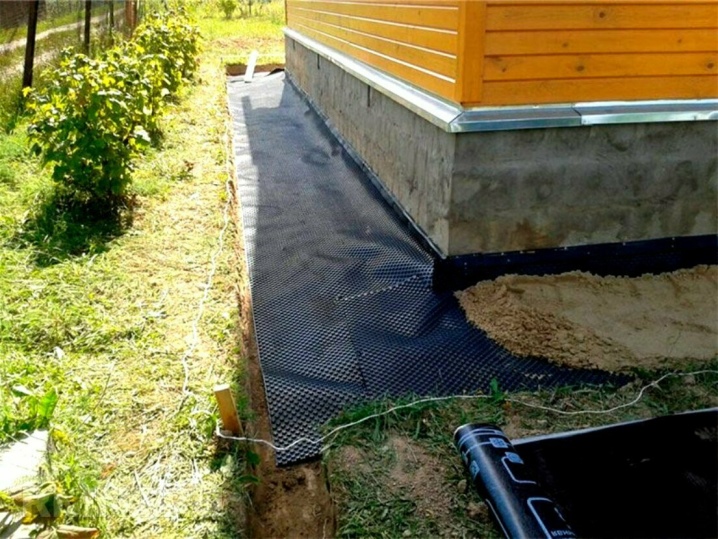
In its absence, a polyethylene film is used as a waterproofing material, folded into 2 layers. However, such a replacement is not as durable and reliable as geotextiles. During operation, it quickly deforms.
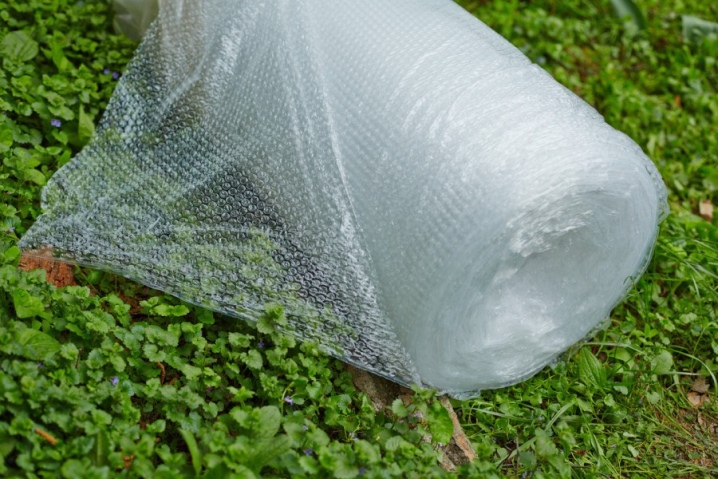
To increase the efficiency of moisture removal, waterproofing is laid with a slight slope. From above, they are backfilled with granite crushed stone in the direction away from themselves (without entering the open canvas). The poured crushed stone is distributed along the perimeter of the ditch, then leveled with a rake.
After that, ramming, wedging, and re-compaction are performed. Then choose one of the types of sub-base for laying paving slabs. It should be noted that its thickness is indicated already in a compacted form.
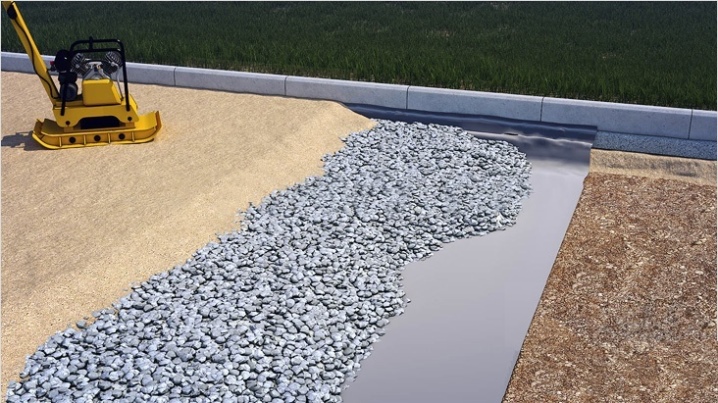
You can see the process of laying the base under the paving slabs in the following video.
The comment was sent successfully.