How to make a quick-clamping clamp with your own hands?

Unlike its heavier counterpart, which has a lead screw and a lock / lead nut, The quick-clamping clamp allows you to quickly, in a fraction of a second, clamp the part to be machined or reworked.


Tool features
In quick-clamping clamps, the lead screw is either absent, or it is assigned a secondary role - set the range of width (or thickness) of the processed parts.
The base of the fixture is a quick plunger or lever clamp, on which the work performed by the master falls. The fact is that in standard screw clamps, when fixing or releasing a part, it would be necessary to screw or unscrew the lead screw, while applying a noticeable force.
There is no need to twist the lever clamp - it resembles a fastener on a suitcase from under a puncher or screwdriver: one or two movements, and the retainer is tightened (or loosened). The simple name of the quick-clamping clamp is "clamp": the axis sets only the direction, and the wheel with the lever acts as a clamp.

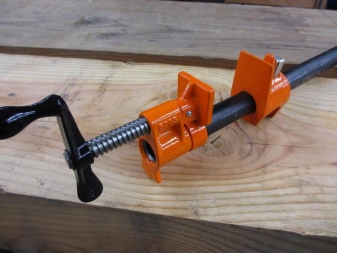
The quick-clamping clamp allows you to calculate the force required to clamp parts, such as those to be welded. Often, the master needs to observe a right angle, which the clamp will help to hold.
This device is easy to make yourself. This is reasonable: industrial counterparts reach 2 thousand rubles in price, but in fact it turns out that even a small amount of steel used in the manufacture of a clamp costs about 10 times cheaper than a finished factory product.

Necessary materials
Joiner's clamp can be made half-wooden - for example, its pressure pads. The experience of the craftsmen shows that the most durable tools are made entirely of steel parts. Tool steel used in the manufacture of, for example, Soviet and Russian-made pliers is not required - a simple one is also suitable, from which fittings, pipes, profiles are cast, and sheets are rolled.

For a powerful yet compact quick-release clamp that can be carried and transported without much difficulty, you will need:
- a professional pipe with a size of at least 30x20 mm;
- an overhead hinge used in furniture production - it must be strong enough so as not to break after several sessions of work, but to last a certain number of years;
- a bead plate removed from the magnetodynamic head;
- roller or ball bearing;
- a bushing that holds the plate with the bearing in a coaxial position;
- a piece of steel sheet with a thickness of at least 2 mm;
- holder (removable handle) removed from an old hammer drill or grinder;
- M12 stud with matching nuts and washers.



Of the tools you will need:
- grinder with a set of discs (cutting for metal and grinding);
- a welding machine (inverter type is often used - they are compact) with 2.7-3.2 mm electrodes;
- a drill with a set of drills for metal (you can use a hammer drill with an adapter for simple drills);
- construction tape, square, pencil (or marker).



Having collected the necessary equipment, you can start assembling your first quick-clamping clamp.
Manufacturing instruction
The procedure for making the base of the device with your own hands is as follows.
- Cut two identical pieces (for example, 30 cm each) from the section of the profile pipe, referring to the selected drawing.
- Cut one end of each piece at a 45-degree angle.From the side of the non-sawn end, weld a furniture hinge to each of the pieces.
- Drill a small hole in the marked plate removed from the speaker, install a bushing on the core. Mount the ball bearing on it.
- Cut a washer from a piece of steel sheet that coincides in diameter with the plate, weld it to the sleeve.
- Weld the bushing and core to each other from the inside. The spool mechanism (wheel) is ready.
- Adjust the wheel so that it is in the middle of the profile. Weld the wheel at this location. Weld the upper bearing cage.
- Cut out two levers from the same sheet of steel and connect the holes on the wheel, facing upward from the clamp, with the holes in its lower compression profile. Levers pivot on separate bolts.


The basic structure of the clamp is ready. By rotating the wheel, compression or dilution of the pressing sides of the tool is achieved. In the compressed state, a washer and a nut are welded to the wheel.
A handle from a drill or grinder is screwed into the latter.
Follow the steps below to make the hold-down plates.
- Cut square strips at least 3 cm wide from the sheet of steel.
- Weld these parts to the grooved nuts, screw the resulting parts onto bolts or stud trims.
- At the ends of the clamp, cut at an angle of 45 degrees, drill large holes, weld the axis of the clamping bars to the compression base.
- Fill in a ribbed pad on these planks.
When seated on the holes, the planks are not pressed in. They can be rotated to the desired angle.

Corner-based quick-action clamp
For the manufacture of another version, the quick-clamping clamps will be needed.
- A pair of corners measuring at least 50 * 50. Their steel thickness is at least 4 mm.
- A pair of steel studs - these are used as clamps.
- 6 nuts - they will provide the structure with the necessary movement.
- At least 2 pieces of sheet steel. Their thickness is at least 2 mm.
- Brackets (2 pcs.).

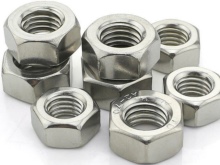

To make such a variant of the BZS, do the following.
- Weld both corners at right angles. There must be a technological gap between them - at least 2 mm.
- Weld in the middle of each corner along the bracket.
- Drill a hole slightly larger in diameter than the M12 nut, weld the nut in its place. A hairpin or a long bolt is screwed into it.
- Weld the nuts on one end of the stud, joining them together before this.

F-shaped quick-clamping design
The F-cam is more often made of wood. - for gluing small parts, soldering electronic components, where special effort is not required.
The clamp is not suitable for locksmith and assembly work, where a large clamping force is required. But by replacing the wooden clamping parts with steel, the master will expand the scope of its application.

To make it, do the following.
- Cut a strip of 30 cm or more from sheet steel (at least 3 mm thick).
- Make a movable and fixed clamping part from a profile pipe (rectangular section, for example, 2 * 4 cm). Their length is about 16 cm.
- Weld one of the cut profile pieces to the end of the guide, having previously set a right angle between them.
- Cut a longitudinal gap in another piece of the profile - with an offset of the guide from its edges. Drill a couple of holes for the pins in it - and insert them so that the movable part moves along the guide without noticeable effort. The gap should be, for example, 30 * 3 mm - if the width of the guide is 2 cm.Before the clamp is finally assembled (after technological adjustment), check its correct movement, make sure that the movable and fixed clamping parts converge tightly.
- Cut a groove in the movable part for the cam lever. Its thickness is about 1 cm. Also make the lever itself - to the size of the wide slot intended for it, but so that it enters and exits this channel without much effort. The length of the lever is about 10 cm, the cut-in channel for it should be about the same length.
- At a distance of 11 mm from the clamping surfaces (jaws), cut a narrow slot (about 1 mm thick). At its end - closer to the middle of the movable part - drill a small hole (through and through) about 2-3 mm, which protects the movable part from splitting. From the end of the clamping part to this hole - 95-100 mm.
- Saw out rectangular segments from sheet steel (thickness 2-3 mm) for the jaws. Cut a notch on the jaws from the pressure side and weld them onto the pressure parts of the clamp. The length of the jaws from the side of the clamp is about 3 cm.
- Immediately behind the jaws, closer to the guide, cut smooth (parabolic) indentations from the inner (clamping) side along the curved measurement. The distance from the jaws to the opposite face of these recesses is up to 6 cm. They help to hold parts and structures of round and oval sections (for example, a pipe).
- Drill a hole for the pin in the movable clamping part (at a distance of about 1.5 cm from the end of the jaw and from the bottom edge where the cam itself enters). Insert the cam lever, thread and secure the pin (so it does not fall out) - this will prevent the lever from getting lost.


The homemade clamp is ready. Slide the movable part onto the rail, tighten and recheck all three pins. Make sure the assembled instrument works accurately and accurately... Try to grip a round stick, a piece of plastic pipe or steel profile with it. If the clamp is strong, then the clamp is assembled correctly.
How to make a quick-clamping clamp with your own hands, see below.
The comment was sent successfully.