All About Welding Clamps

When performing welding work alone, it can be very inconvenient (or even impossible) to weld the desired element in a certain place in the structure. Excellent helpers in solving this problem will be special clamps for welding, which we will take a closer look at in this article.

Peculiarities
Clamp for welding - This is a special device that serves as a fixture of some parts at the time of welding or processing. The specified device connects the individual elements of the welded structure as tightly as possible, which greatly facilitates almost any work with them.
Structurally, such a product consists of two main parts: frame and a movable device that presses the elements to be welded. By changing the distance between the frame and the movable part, a tight grip of the surfaces to be welded occurs. A threaded screw or a lever can be used as a clamping mechanism.
By changing the tightening force, it is possible to regulate the clamping density of the welding elements, which is necessary when fixing heavy workpieces.

Corner clamps are used for joining pipe blanks at different angles. Such a product is the most common, since it is used almost everywhere. It is quite suitable for welding at home, in the field of assembly of metal structures, as well as in industrial production. Based on the required angle, the clamp can have a constant joint angle or the ability to adjust the inclination of the parts.
Welding angle clamps have a number of undeniable advantages. Let's consider them.
- Thick-walled metal is used to increase the rigidity of the joints. Due to this, the likelihood of bending of the weld from overheating of the metal or other deformation during operation is reduced.
- Copper-plated threaded parts are used in the construction of durable clamps. This is done so that molten metal spatter does not destroy the thread, and the pressure mechanism lasts as long as possible.
- The use of the described device allows the welder not to hold one of the parts to be welded with his free hand, and the rigid fixation makes it possible to work with the electrode at any angle.

The quality of welding work depends not only on the skills of the welder himself, but also on the tool that he uses in his work.
Using such additional tools as clamps, you can not only significantly reduce the time for completing the task, but also get rid of the need to fit and stretch the workpieces for further work.
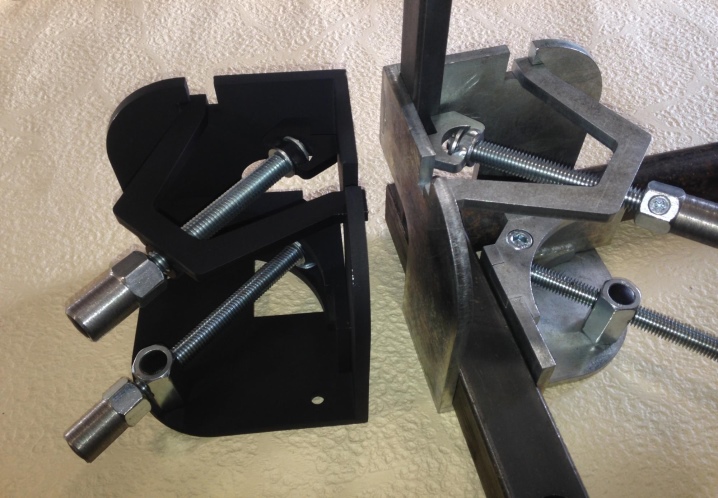
Varieties
Today there are a huge variety of clamps used for certain types of fixation.... Let's take a look at the most common types of these fixtures that can be found at any welding equipment store.
- Body clamps... This clamping mechanism can be used to clamp the workpiece to a variety of oblique and parallel surfaces. This device got its name due to the fact that the clamp is performed by the entire body. The product consists of 2 metal bars connected by a metal plate on one side. One of the bars is rigidly fixed at the end of the metal plate, and the second has a tightening screw and moves freely along the entire plate. To clamp the part, it is necessary to bring both bars together, and then press the remaining distance with the clamping screw.This type of clamps is considered the most common in welding.

- Screw clamp. It's also a pretty popular tool. It has a lot of versions, but the principle of operation remains unchanged: the clamp is carried out by tightening the screw. This product can be made in the form of a body clip. In this case, the clamping bolt passes through the bar, and the penny is made in the form of a lip. A good tool of this type should be made of tool steel by forging. Forged items are hardened and hardened to ensure durability.

- Magnetic clamp (magnetic angle)... This is another common type of clamps among welders, as it is designed to pre-fix two metal profile pipes and has the ability to quickly adjust without the need to unscrew the clamping screws. The described device can have various geometric shapes (triangle, square, pentagon).

- Ratchet clamp. The appearance resembles a large clothespin. It is clamped by hand, and the presence of a ratchet mechanism does not allow unclenching back. To loosen the clamp, you must press the special button on the handle.

- Vacuum clamps. They are 2 hand vacuum pumps fixed on a metal frame parallel to each other. Such a clamp is three-axis. The described product is used for joining two sheets of metal.

- G-shaped clamp. Well suited for welding. Such structures are made of tool steel, which provides them with increased strength and durability. The device can reliably fix together several necessary elements at once, with which welding work is carried out.

- C-shaped clamp. This is the same G-shaped clamp, but only it has the ability to grip it with a great distance from the edge of the table.

- Pipe. The design of such a device is based on a metal tube with a fixed lip, and the movable lip has a locking mechanism. The clamp is carried out by a screw, which is located on a fixed lip. It can be used for welding channels.

How to choose?
Before buying a clamp, you need to understand that there is no single (universal) type of clamping mechanism that is suitable for all occasions in life. Each of the varieties of these devices is designed for specific tasks.
- If you need to weld 2 pieces at a 90 degree angle and you only have G-clamps, it will be very difficult to solve the problem with their help, especially if you are welding round pipes.
- Angle clamp also does not help if you need to weld 2 sheets of metal together in one plane.
Therefore, the performance of certain welding work must be approached responsibly, knowing exactly what type of auxiliary tool will be needed in a particular case.
When the type of the required clamp is determined, it is necessary to make a choice according to the quality of the tool.

Pay attention to the area and thickness of the pressure jaws: the wider and thicker they are, the more clamping force they can withstand (and the area will also provide a secure grip of the workpiece). These are very important parameters that should not be underestimated, because during welding, the metal very often drags away from overheating, and unscrupulous clamps will allow the parts to be welded to move. This will inevitably lead to scrap or to further tension of the workpiece for subsequent welding.
Necessary pay attention to the thread and the design of the screw connections. As mentioned earlier, it is desirable that they be depleted - this is the best solution. And also look at the existing thread pitch - the larger it is, the more clamping force the nut can withstand. It is best to choose the maximum step, since such a product will last much longer.
The size of the clamp is equally important in choosing the perfect tool. Everything is individual here, so the expression "more" in this case does not mean "better" at all. Too large a clamp cannot be used in a small structure, and a small one, probably, may not be enough to clamp the dimensional element. That is why the size of the clamp to be purchased should be based on the maximum width of the two parts to be welded (plus a small gap).

For an overview of Bessey clamps, see below.
The comment was sent successfully.