How to make a metal clamp with your own hands?

The clamp is the simplest fixing tool like a mini vise. It allows two workpieces to be pressed against each other - for example, to pull boards together. The clamp is often used, for example, when gluing bicycle and car cameras, wood with rubber, metal, etc. This is a first aid tool, but it will not replace a locksmith's vice. Let's figure out how to make a metal clamp with our own hands.


Tool features
A self-made clamp is often surpasses the factory one in performance quality and downforce. Industrial clamps contain a steel screw, but for ease of use, the base is an aluminum alloy bracket. In order not to spend money on not quite high-quality tools that have flooded the market, it makes sense to make a clamp with your own hands - from steel reinforcement, a square or corner (or T-shaped) profile, etc.
The resulting structure will last for tens of years if you do not use it to fix heavy (tens and hundreds of kilograms) details.

One of the most common uses of the clamp is gluing wood (wooden blanks), which almost any homemade structure can handle.
What do you need?
Homemade metal clamps often require these parts.
- Profile - corners, brands, square or rectangular. As a last resort, round is suitable, but not rail. Choose a hot-rolled billet - it is stronger and more reliable than cold-rolled billets.
- Studs or bolts... If you do not trust the quality of steel, to which other metals are added these days, which worsen its properties, choose a smooth steel bar of a suitable thickness, buy a special cutter with a set of nozzles and cut the threads yourself.
- Nuts and washers. Match them to a specific stud.
- Striking plates - are machined from sheet steel or pieces of an angle on their own.




Of the tools you will need such.
- Hammer... If the clamp is strong enough, you may need a sledgehammer.
- Pliers. Pick the most powerful ones you can find.
- Bolt cutter - for fast cutting (without grinder) fittings. Prefer the largest one - a meter and a half long.
- Bulgarian with cutting discs (for metal).
- A pair of adjustable wrenches - the most powerful ones are designed for nuts and bolt heads up to 30 mm. Find the biggest key on sale. Wrenches for nuts measuring 40-150 mm are considered difficult to access - a motorized wrench works instead.
- Locksmith vice.
- Marker and construction square (right angle is the standard).
- Welding machine with electrodes.
- Drill with a set of drills for metal.




It is difficult to do without a vice. If the clamp being made is small, the vice will be replaced by a much more powerful clamp attached to the workbench.
Manufacturing instruction
There are several designs of homemade clamp. The drawing of each of them contains its own differences - in the shape of the bracket and counterpart, the length of the lead screw, etc. An excessively long clamp (a meter or more) is unlikely to come in handy.


Coal clamp
The carbon structure is sometimes an indispensable aid for the welder: such a clamp helps to weld thin profiles, sheet steel strips, corners and fittings at right angles. To make it, do the following.
- Mark and cut a rectangular profile, for example 40 * 20 mm. Its outer segments of 30 cm are taken as a basis.The length of the inner ones can be 20 cm.
- Cut from a sheet of steel (5 mm thick) square with a side of 30 cm.Cut one corner of it so that an additional piece is formed in the form of an isosceles triangle with sides of 15 cm.
- Weld to the base of the future clamp - cut sheet pieces of profile, large in length. Check the right angle with a construction square before welding these parts.
- Weld smaller pieces of profile to the square cut of sheet steel. To strengthen the mating part of the clamp, one more same trim and strips of steel may be required - if necessary, cut them from the same original sheet from which the sheet square was cut.
- Cut a piece from the half-inch steel pipe length 2-3 cm.
- Before welding the second piece of sheet from the other side, place it in the middle and weld on the running sleeve - the already cut piece of pipe. Its diameter is slightly larger than the M12 hairpin on the sheet trim already welded to the smaller pieces of the profile. Position it as close as possible to the welded corner of the mating piece and weld in this place.
- Insert the pin into the bushing and make sure its free play... Now cut a small piece of sheet steel (square 2 * 2 cm) and turn it into a circle. Weld the end of the stud inserted into the sleeve to it. A sliding element is formed.
- To prevent slipping, cut out a second square of the same size, drill a hole in it equal in diameter to the clearance of the sleeve, and grind it, turning it into a circle. Put it on so that the hairpin turns in it easily, scald this connection. A bearingless bushing mechanism is formed that does not depend on the thread of the stud. The use of conventional large washers is not allowed - they are too thin, will quickly bend from significant downforce, and homemade mugs made of 5 mm steel will last a long time.
- Weld up the second triangle cut on the other side of the counterpart.
- Cut another piece 15-20 cm long from the same profile. In its middle, drill a through hole, slightly larger in diameter than the thickness of the stud - the latter should pass freely inside.
- Weld on each side of this section of the profile, there are two locking nuts M12.
- Check that the stud can be easily screwed into the lock nuts.
- Weld the profile with these nuts to the main part of the future clamp. The stud should already be screwed into these nuts.
- Cut a piece of 25-30 cm from the hairpin (it is already inserted into the sleeve and screwed into the lock nuts) and weld a lever onto one of its ends - for example, from a piece of smooth reinforcement with a diameter of 12 mm and a length of 25 cm.A piece of reinforcement is welded in the middle to one of the ends of the stud.
- Check that the clamp is working properly. Its power reserve is equal to several centimeters - this is enough to clamp any pipe, longitudinal section of a sheet or profile.


The coal clamp is now ready for use.
To check the right angle, you can slightly clamp the construction square - there should be no gaps on both sides at the point where the profile adjoins the square.
Further, the clamp can be painted, for example, with a rust enamel primer.

Rebar clamp
You will need a rod with a diameter of 10 mm. A blowtorch is used as an auxiliary tool. Do the following.
- Cut pieces 55 and 65 cm from the rod. Bend them by heating them on a blowtorch - at a distance of 46 and 42 cm. The distance from the other end to the fold is 14 and 12 cm, respectively. Dock them and weld together at several points. An L-shaped bracket is formed.
- Cut off two more pieces of reinforcement - 18.5 cm each. Weld them approximately in the middle on the main part of the frame (bracket) - on the longer side of it. Then scald them together so that they don't drift apart. The L-shaped bracket becomes F-shaped.
- On the smaller side weld a 3 * 3 cm cut of sheet steel to the bracket.
- Weld to the end of the smaller piece of rebar two lock nuts M10.
- Cut a piece of hairpin with a length of 40 cm and screw it into these nuts. Weld a lever on it from a piece of smooth reinforcement 10-15 cm long. It should not touch the bracket when rotating.
- Weld the counterpart to the other end of the stud screwed into the bracket - a circle from the same steel sheet. Its diameter is up to 10 cm.
- Weld the same circle onto the end of the bracket (where the square is already welded). When pre-scalding, check the parallelism of the resulting clamping circles (jaws) of the bracket, then finally scald both joints.
The reinforcement bracket is ready for use, you can paint it.



G-clamp
The bracket is made of bent reinforcement welded in the shape of the letter P, its pieces or pieces of a rectangular profile.
You can bend a piece of thick-walled steel pipe for it - using a pipe bender.
For example, a bracket with a length of sections - 15 + 20 + 15 cm is taken as a basis. With the brace ready, do the following.
- Weld on one of its ends from two to several M12 nuts, lining them up... Boil them thoroughly.
- Weld a square onto the opposite end or a circle up to 10 cm in diameter.
- Screw on the M12 stud into the nuts and weld the same clamping circle onto its end. Tighten the resulting structure until it stops, check the parallelism of the closed jaws of the clamp.
- Cut a stud at a distance of up to 10 cm from the nuts - and weld the twisting double-sided lever to the obtained segment in this place.
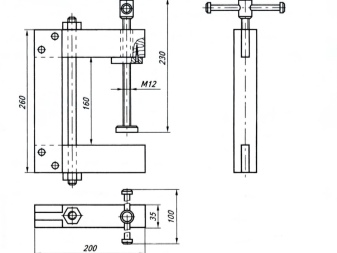

The clamp is ready for use. As you can see, there are dozens of options for the design of a steel clamp. There are more complex clamps mechanisms, but their repetition is not always justified. Even the simplest steel clamp will serve the user in welding profiles, fittings, pipes of different diameters, angles, T-bars of different sizes, sheet metal strips, etc.

How to make a clamp with your own hands, see below.
The comment was sent successfully.