CNC drilling machines

Control on the basis of a numerical program module is implemented in all types and types of machines: turning, drilling, milling. The only reason is the transition from single, episodic sessions of work to massive ones, affecting parties of billions of the same type and identical parts, which is the basis of successful activity.
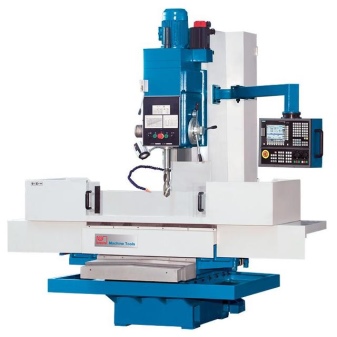
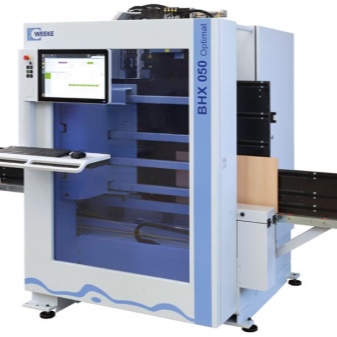
Varieties and their structure
The device of the simplest drilling machine is a movable drive, the chuck with a drill of which vertically moves along the guides. The object table, on which the part is fixed, moves in accordance with the settings of the program in the program unit, which issues the corresponding commands. This table can move forward or rotate depending on how a certain number of parts need to be processed. Part end clamps also move to securely hold one thick part or a whole stack of thin parts. For example, if the depth of the drill chuck is 10 cm, then 5 20 mm or 50 2 mm plates can be fixed on the reaming table.
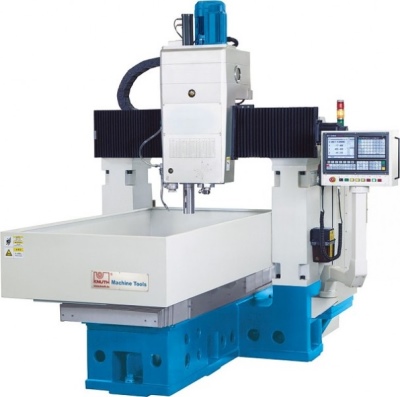
The X, Y and Z movement is shared between the actuator and the stage. So, the drive can move the chuck with the drill only in height, and the length and width between the drilled holes (according to the plan) are determined by the movement of the parts and the object table. In more advanced versions, the table is stationary: only the spindle with the chuck moves.
In all cases, coordinate-step installations are responsible for the movement, the basis of which is stepper motors with a complex system of rollers, gears and electronic driver boards, thanks to which the rotary-angular movements of the rotors of these engines are carried out.
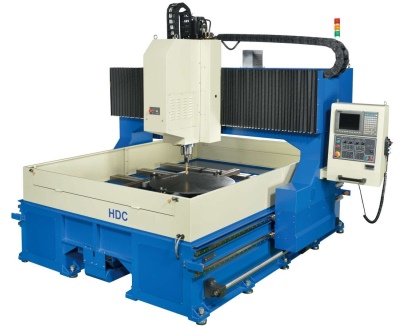
There are the following types of drilling machines.
With built-in rotary object table
High speed and accuracy are important here. The main components of this type of device include dynamic bridges and double vertical masts on parallel rails, suspended above the table. The device is completely autonomous. It works automatically, with minimal operator intervention. The calculator in this device is implemented on the basis of a controller built on IPC microcircuits.
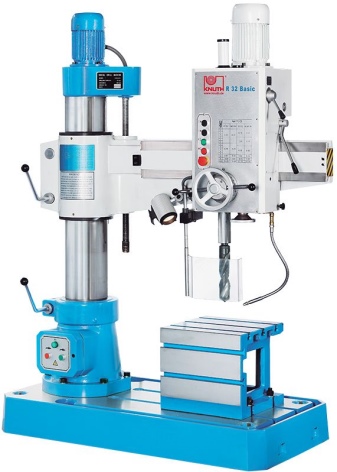
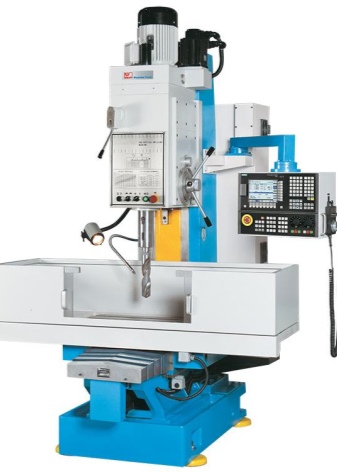
The elevator drive is built on the basis of a servo drive, as well as the spindle mechanism. There is an autodetector of the drill length, a determinant of the thickness of workpieces (or a set of identical parts stacked on top of each other). Additional functionality is a graphical software user interface that is understandable to every beginner. The machine has touch panels, on which the operator of the unit sets the required mode of operation and the type of workpieces to be processed.
On such a device, it is easy and simple to align the edges of the workpieces. Coordinates for work are set so that they can be conveniently combined with a specific process for drilling workpieces.
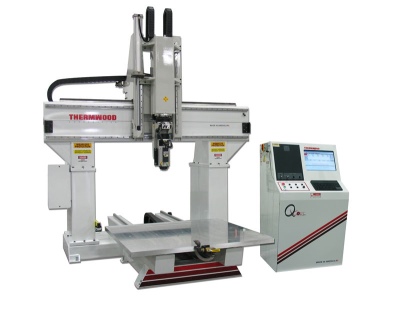
For the most accurate drilling, a software environment is used that independently corrects errors that occur when working on similar machines without CNC.
Gantry CNC boring machines
Such models are suitable for machining structural steel blanks: for example, parts for assembling towers and bridges. Advantages of gantry machines: avoidance of repetitive sessions, increased efficiency of production, reduced processing time and reduced overall cost of manufacturing components.
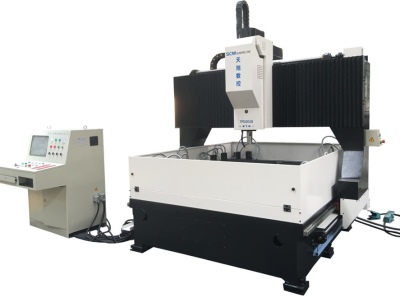
By the number of spindles, the machines are divided into single- and multi-spindle machines. On some models, there is a function for replacing drills on the fly (a consumables store is built into such a device). In terms of the number of operations, multi-operation devices are gaining more and more popularity, thanks to which, in addition to drilling, boring and milling (alignment) of workpieces are realized in production.
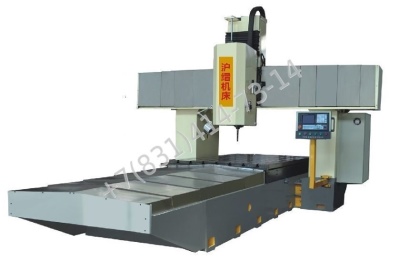
Varieties of vertical machines are represented by the following list.
- Single column with a stage. The drilled holes are 2-6 cm in diameter.
- Single column with a turret. Cutters can be changed automatically on the fly.
- Single column with tool magazine... The diameter of the holes is 5.5-6.5 cm.
- Radial with sleeve and spindle (or a movable column).
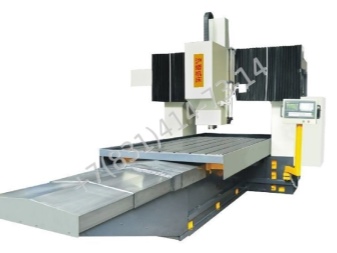
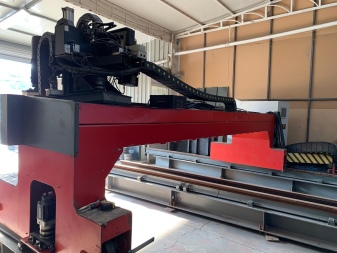
But there are also horizontal drilling machines. On the whole, they are like a machine in reverse: the drills move horizontally, and the spindle drives themselves move vertically. Scope - pre-drilling workpieces with ribs (if the thickness allows).
Having decided on the type of machine used, they check how suitable it is for a specific list of works.
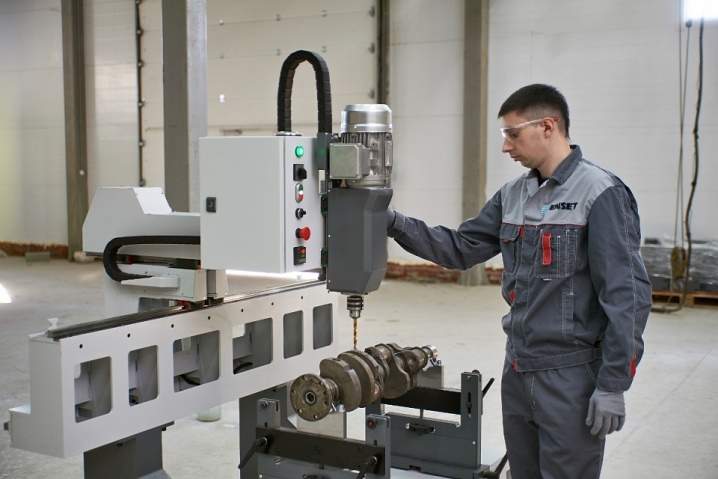
Appointment
A machine designed for metalworking will easily handle woodworking and non-metallic composite material. So, working on a model ProArc CNC Drill + 1640S can be carried out with metal plates. The drill diameter is 6-80 mm, so you can make a large hole using even a step or crown drill.
In this case, the thickness of the part does not exceed 10 cm. This model belongs to the list of the best of its kind. Suitable for small production when small structures need to be drilled out. The width of the table in this example reaches 60 cm, the length is up to 3 m. High-quality and high-precision work makes this device an extremely popular work tool.
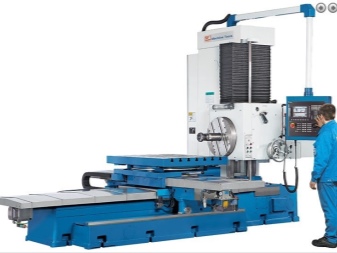
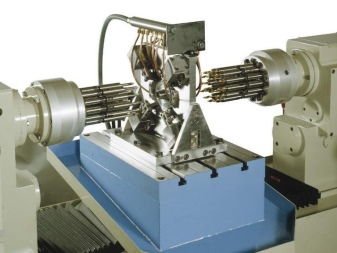
CNC boring machines are suitable for quick auto-alignment of parts from a set, which is set by the operator of the unit. The accuracy of the operations is checked using the built-in program. The automatic movement of the drilling drive and the object table is carried out by three coordinate readings with high accuracy. For example, the movement of a part (or tool) in height is carried out by means of stops, switches, plugs and perforated tape.
In the absence of a revolving mechanism in the machine, the drill is replaced with a quick release chuck.
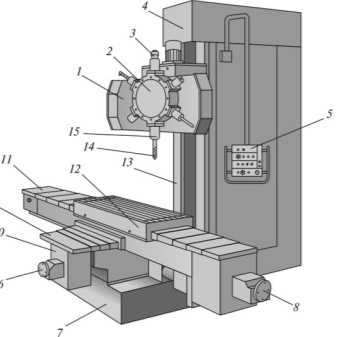
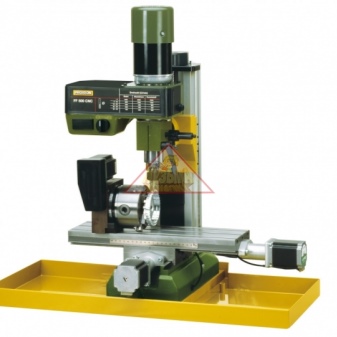
The purpose of metalworking machines is to drill holes in workpieces, where high accuracy is critical. Manual drilling will not provide it, no matter how hard the master tries. In a continuous production environment (for example, within one work shift), such equipment is irreplaceable. Machines for processing composite and wood materials are used, for example, in the manufacture of furniture. This includes drilling holes for Euro bolts (confirmation). The unit must have a large object table up to several meters long. But the range of use of CNC drilling machines is aircraft, instrument and shipbuilding. They are used as the main toolkits of the auto repair shop.
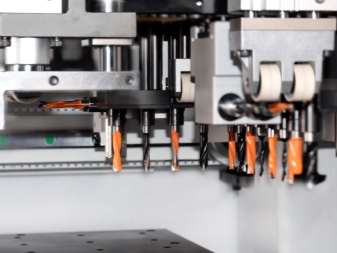

This specialized equipment with electronic control systems organizes control over the functional purpose of various equipment... For example, a CNC drilling center is equipped with universal workpiece recognition systems.
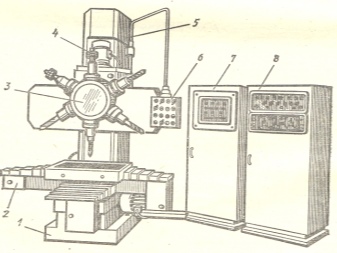
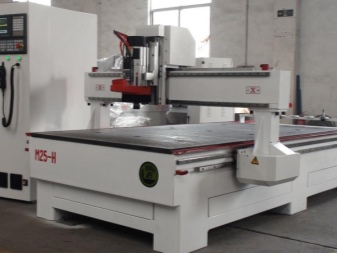
Choice
The selection of a CNC drilling machine is made according to the following criteria.
- Dimensions and weight of workpieces. Whether you drill relatively thin plates or whether you need to process bulky workpieces with considerable weight depends on your narrow profile.For work on steel and alloy non-ferrous metal (bronze, etc.), a high engine power (more than 1 kW) and the best drills from alloy high-speed steel will be required. If you need to drill through hardened steel, then only a diamond-coated drill (or tip) will help.
- If you need a machine for processing wood, then you should not overpay for its more expensive counterpart designed for processing steel. Such a machine can have both lower engine power and reduced dimensions.
- A machine for an exclusively home workshop or garage should not be large, occupying a space of 10 m2 or more. These are the costs of factories and factories where production is put on a conveyor stream. For a house or a small garage, such a machine will take only 1-2 m2.
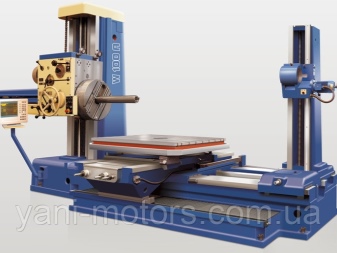
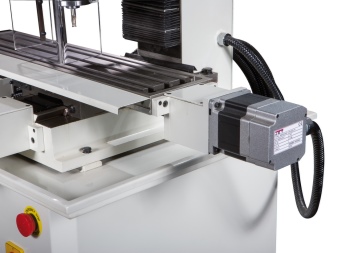
Do not buy machines about which there is not enough information. They will quickly fail.
The comment was sent successfully.