How are self-tapping screws made?
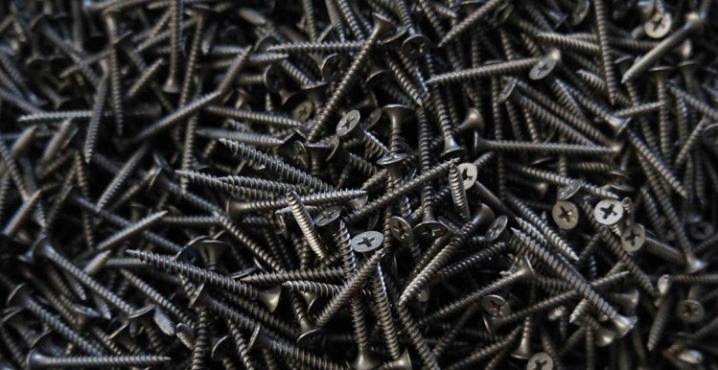
Knowing how self-tapping screws are made is useful even for those who are only going to use them. But for organizing a new production, something else is more important - what is the technology and what machines will be required for their manufacture. It is important to make a choice between Russian and other equipment, as well as carefully study the features of specific models.
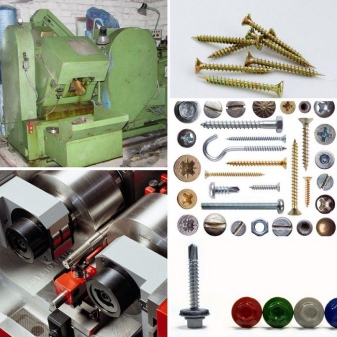
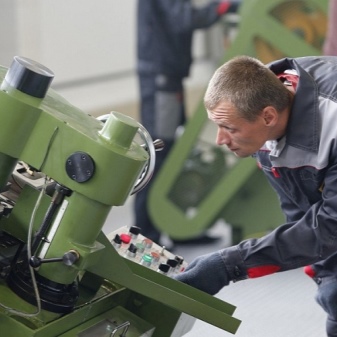
What raw materials are they made of?
The production process of self-tapping screws is unthinkable without the use of carefully selected raw materials of special brands. Three metals are most commonly used:
- brass;
- high carbon steel;
- steel with stainless properties.
The metal is usually shaped like rods or wires. Such products are made in any companies dealing with rolled metal products. Therefore, there are no special problems with obtaining raw materials. For 1000 kg of steel they take about 2500-3000 rubles.
This volume is quite enough for the production of half a million self-tapping screws or a similar amount.
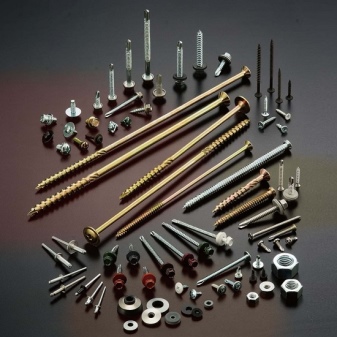
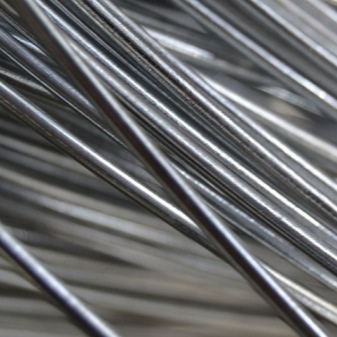
What should be the machine?
For the manufacture of self-tapping screws, a variety of equipment is needed, and the drawing mill is of great importance among them. It allows the production of thin metal rods. Such an apparatus is a furnace with special components (dies), which are equipped with systematically decreasing holes. The rod is heated to a high temperature. The number of dies passed directly affects the resulting diameter. The so-called cold heading machine also plays an important role in the working process. In this device, the finished bar is cut to the required size. Additionally, the head of the resulting self-tapping screws is formed. Finally, an additional slot appears on the head. Thanks to this, you can safely work with fasteners using a screwdriver.
It is impossible to do with the release of self-tapping screws and without a thread rolling system. As the name suggests, this device is designed to create carvings. The cutting step and the shape of the surface to be cut are adjusted using special dies. The conclusion is simple: in order to create products with different threads, you will have to create a stock of dies of different sizes. But it is not enough to simply make the grooves - it will also require processing in a hardening furnace.
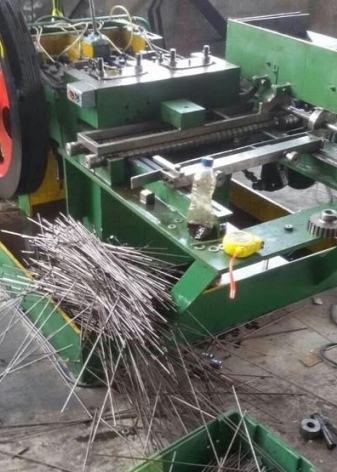
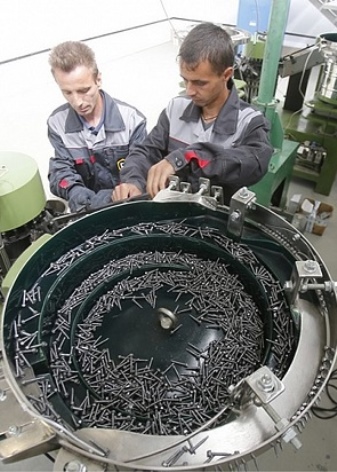
Without passing through it, the finished product will be too soft. It will be impossible to sell or somehow use it. The procedure is quite simple (externally): first of all, the metal is heated, and then its temperature is sharply reduced. Therefore, it is quite obvious that the stories about the multifunctional mini-machine for the production of self-tapping screws are somewhat cunning. If there are such devices, then their versatility is expressed only in a variety of cutting modes, and for each stage of work, for other technological operations, other installations will still be responsible.
It is also necessary to use, for example, electroplating baths. With their help, a special coating with anti-corrosion properties is applied. The nuances of technological processing are determined by the type of coating applied. However, you will definitely have to process screws in several baths. When electroplated, good drying will be required. It is not enough to lay the workpieces out in the open air. Drying on special equipment is desirable. You will also need packing machines. They put the finished products in special bags.
Modern automation is capable of itself counting the required number of self-tapping screws.
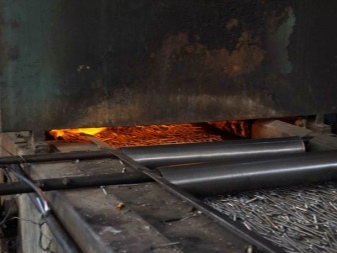
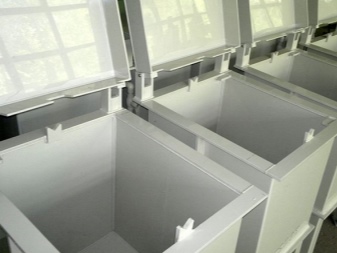
Popular brands
When buying machine tools from Russian manufacturers with low productivity (from 50 to 70 pieces per minute), you will have to pay from 170 to 200 thousand rubles. The higher the performance requirements, the more expensive the hardware will be. Systems from China making 250-300 self-tapping screws per minute cost from 500 thousand rubles. Some models sell for 700 thousand. Apparatuses of the same performance made in Austria and Germany are sold for 750-1100 thousand rubles per machine.
A number of American firms are diligently promoting their advertising. However, their entire function is reduced only to the formation and presentation of the brand. Almost all copies are made in China, and there are simple licensees in the United States. In technical terms, there is no difference for the consumer. In this case, the price will include costs and profits along the entire chain.
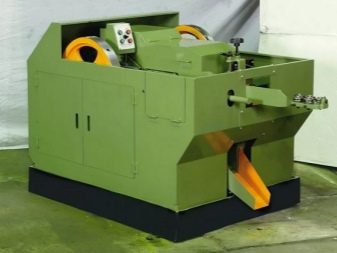
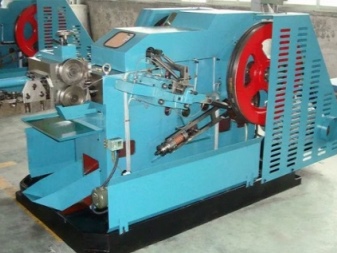
It is often considered that German-made stoves are very good. And in general, this is true. But this segment is dominated by continuous duty cycle designs. For small industries and semi-handicraft workshops, batch-type ovens will be more necessary. Products of this kind are supplied by some domestic firms. Raw materials in an intermittent cycle furnace are loaded into perforated barrels. These barrels are also used for filling in quenching tanks. Many auxiliary equipment is made by hand. Finding drawings and diagrams is not a problem now. You just have to carefully study the official technology to eliminate errors.
For small enterprises producing self-tapping screws, Candid AS3016 is ideal. It is a semi-automatic model that also allows screws and screws to be produced. The cost of such equipment is approximately 3000 conventional units. True, his productivity is not very high - a maximum of 25 fastening hardware per minute. The semi-automatic type of machine means that its operator will have to perform a number of manipulations, however, for novice craftsmen, this is the ideal solution.
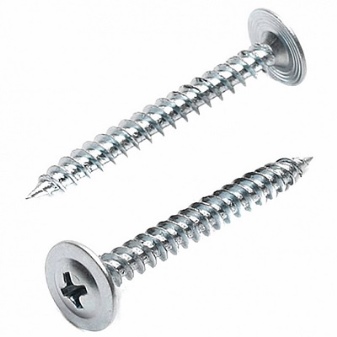
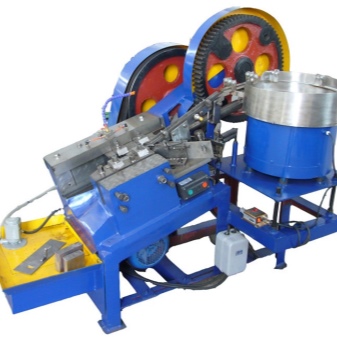
The main part of machines for the production of self-tapping screws is still made in China and Taiwan. In Russia, there are only a few organizations specializing in the production of such equipment. The costs of purchasing it, taking into account shipping rates, are quite significant. Among Russian suppliers, the undisputed leader is Samstal. Also noteworthy are the products:
- FOB;
- LianTeng;
- Innor.
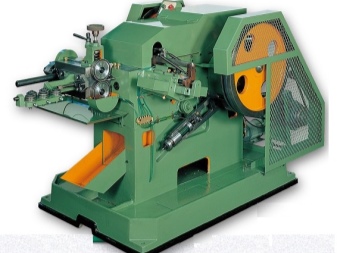
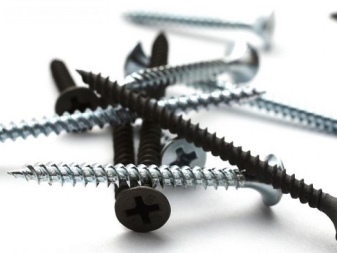
The simplest versions can produce up to 60 hardware per minute. Advanced designs make up to 250 units per minute. Some versions are configured to release other types of products. This allows you to expand the product range, and, despite the initially increased costs, such a decision quickly pays off. The cost of the most affordable automatic machine tools for the production of hardware with an estimated productivity of 50 pieces per minute is at least 13 thousand US dollars.
Models designed for qualified high-class professionals sometimes make up to 300 hardware per minute. An average Russian machine tool will cost about 90-100 thousand rubles. It will cost about 500 thousand rubles to purchase a complex line with all the necessary equipment.
It is not worth saving on this. Only high-quality equipment really pays for itself, and a number of cheap modifications wear out quickly.
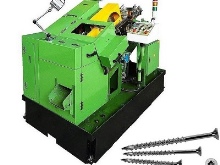
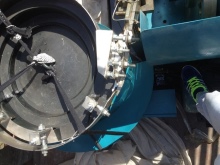
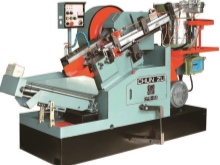
Technology
The production of self-tapping screws, of course, cannot be reduced only to the acquisition of suitable equipment. The first step in the technological process is naturally cutting wire into sections of the required length. At the same moment, a hat is formed. Next, finished products are transported along a conveyor belt to a specialized machine. It is there that the carving is applied; in addition to the already mentioned hardening, washing and drying, sorting is required. For your information: sorting and packing of self-tapping screws is not always carried out on special machines.A number of small factories are built in such a way that these operations are performed by specially engaged employees.
The simplicity of modern machines is such that, in principle, 1-2 people can be engaged in the whole process. There are also no particular difficulties with repair and maintenance. Threading machines hold workpieces in position using vibrating grips. Electroplating usually involves phosphating or oxidation. In some cases, white or yellow zinc is applied. In principle, once the coating has been applied, the self-tapping screws can be used immediately for their intended purpose. The hardening furnace can heat up to about 900 degrees. It contains a colder compartment; it can also be practiced to convey it to another oven at a lower temperature.
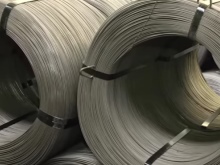

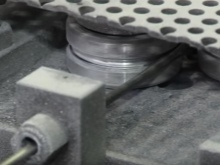
Drawing machines of good performance can only work normally when using lubricating and cooling fluids. Correct drawing implies not only the formation of the required geometric configuration, but also the improvement of the microstructure. In the production of self-tapping screws, equipment is used that does not have the function of winding material onto a coil. Another procedure, tempering, helps to correct material imperfections after hardening. For cold heading machines, the correct alignment of all components is very important.
Prepared products are dumped into silos or baskets. Cutting off the workpiece on a cold heading machine can be done both open and closed (using a sleeve knife). This method provides a plane-parallel cut and a uniform volume of individual workpieces. Therefore, there will be less difficulties with further processing.
Most often, self-tapping screws obtained on cold heading machines are made in accordance with DIN standards.
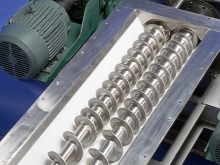
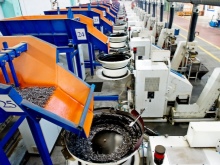
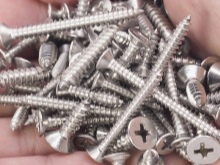
For how self-tapping screws are made, see the next video.
The comment was sent successfully.