Desiccants: properties and applications
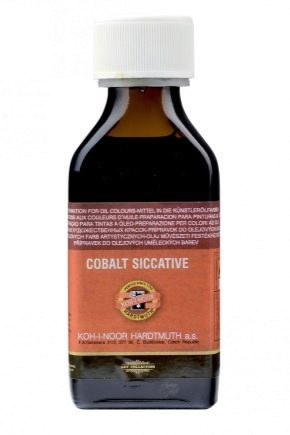
Preparing for painting, people choose their own enamels, drying oils, solvents, learn what and how to apply. But there is one more very important point that is often overlooked and not taken into account. We are talking about the use of driers, that is, special additives that accelerate the drying of any paint and varnish material.
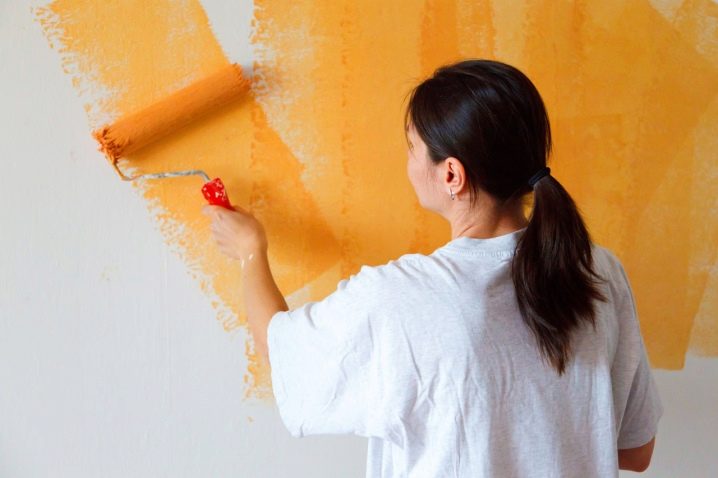
What it is?
A siccative is one of those components, the introduction of which allows manufacturers to diversify the recipe and adapt it to specific situations, to areas of use. It is added to various paints and varnishes to speed up the drying process.
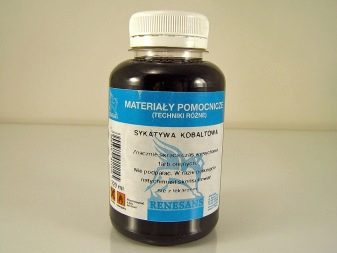
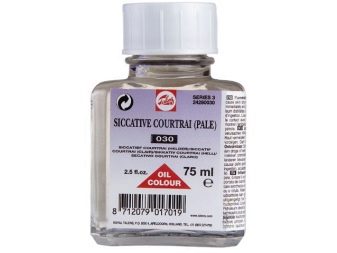
Varieties of compositions
In terms of chemical composition, driers are metal salts with high valence. Also, this group may include salts of monobasic acids (the so-called metal soap). Accelerating drying reagents are applicable to any existing type of paint and varnish material.
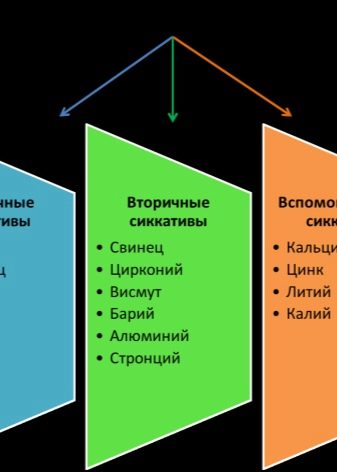
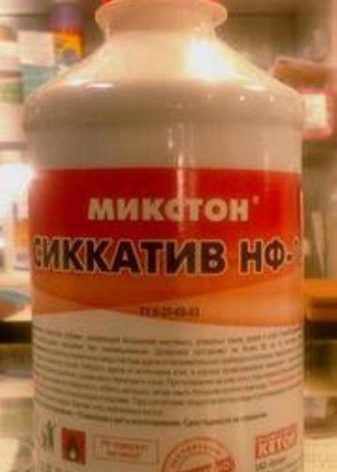
First of all, cobalt and manganese reagents, as well as lead, began to be used. A little later, the use of zirconium salts and some other elements began. The vast majority of modern mixtures are made without lead, because they have a negative effect on human health. Chemists and technologists classify catalysts into first-line substances (true) and second-line compounds (promoters). A real accelerator is a metal salt with a changing valence, which, upon contact with the target substance, enters into a reduction reaction, then oxidizes to a substance with an increased valence.
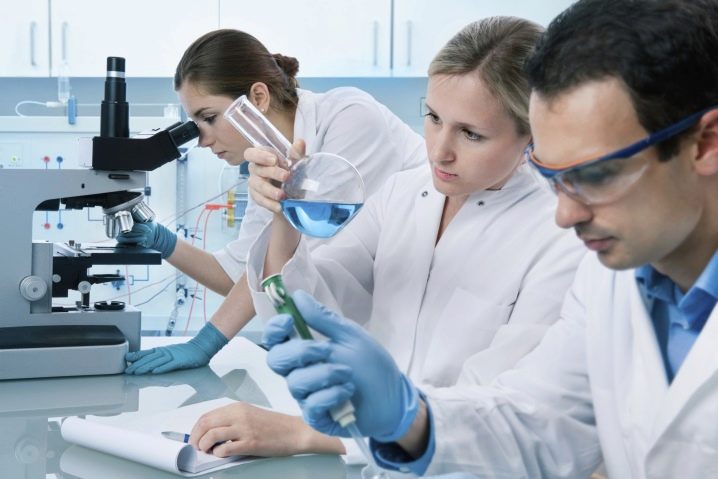
Helping compounds are salts of metals with unchanged valence. These include zinc, barium, magnesium and calcium compounds. Their role is to increase the effectiveness of conventional mixtures by reacting with carboxyl groups of substances that form a film. The developers take this into account and are increasingly using combined formulations.
- One-piece driers based on cobalt are recognized as the most effective, but their effect affects only the surface of the paintwork film. Therefore, such a metal is suitable only for a very thin layer or, on the eve of baking, can be used by itself.
- Lead dIt acts in its entirety, it is quite poisonous and is capable of forming sulphide spots, as an independent drug is rarely used.
- Manganese active both on surfaces and in thickness. The trivalent type of metal is dark brown and this can distort the appearance of the coating. When working, it is required not to deviate from the standard recipe - an excess of manganese only weakens the effect, contrary to obviousness.
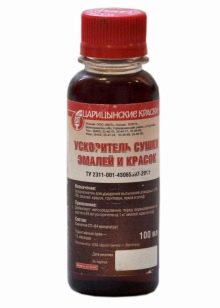
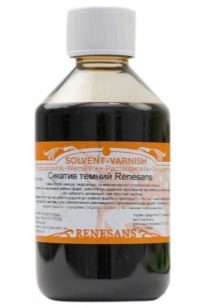
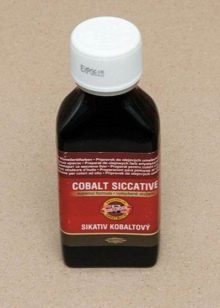
There are two manufacturing methods - melting and deposition. In the first case, thermal action is practiced on oils and resins, which are then fused with metal compounds. This is a very simple and effective technique. The precipitated substances are obtained by conducting a reaction between metal compounds and salt products of acid processing. Such driers are distinguished by a clarified color and contain a stable concentration of intensely active metals.
- Zinc makes the drying of the surface slower, and the main volume faster, while forming a strong film.
- Calcium acts as a promoter in complex mixtures, thanks to which drying becomes easier in the cold.
- Vanadium and Cerium they act in the volume of paint, but their disadvantage is yellowness, which appears in the applied coating.
- Substitutes for lead in modern drugs are combinations of zirconium and cobalt.
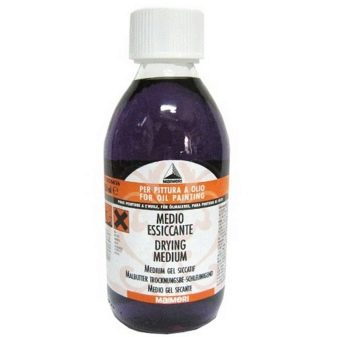
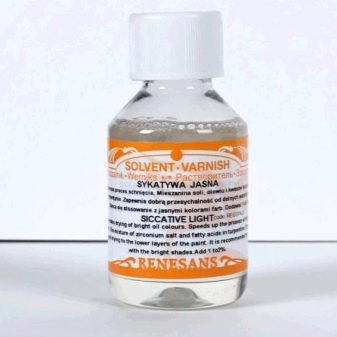
As for organic acids, there are four main groups of driers:
- naphthenate (produced from oil);
- linoleate (obtained from linseed oil);
- rubberized (made from rosin);
- tallate (based on tall oil).
Fatty acid mixtures (such as fatty acids) are formed by dissolving a salt of a multivalent metal in a fatty acid or by mixing such solutions with naphthenate acids. The use of such substances is possible both with varnishes, alkyd-type paints, and in combination with flax oil. Outwardly, it is a liquid transparent to light, in which 18 to 25% of a non-volatile substance is present. The concentration of manganese ranges from 0.9 to 1.5%, and lead may be higher, at least 4.5%.
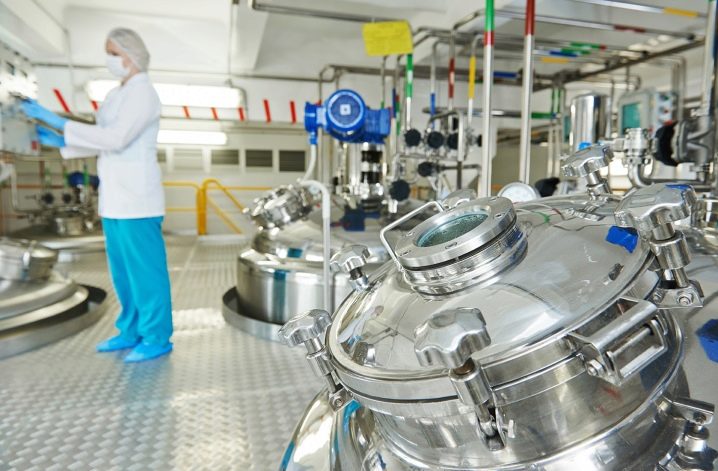
Fatty acid desiccants interact with linseed oil, preventing haze and sediment. The minimum flash point is 33 degrees Celsius. Important: ready-to-use desiccants of this group are poisonous and can cause a fire. If 6 months have passed after the date of release, you need to carefully check the substance, whether it has lost its qualities.
NF1 is a lead-manganese combination. It is a liquid substance obtained by the precipitation method. Earlier analogues of this mixture are NF-63 and NF-64. It is necessary to add a drying accelerator to dyes of oil and alkyd nature, to enamel and lacquer materials, drying oils. NF1 is perfectly transparent and homogeneous, does not have the slightest sediment or impurity. Can be used in conjunction with catalysts based on Co. The best among them are NF-4 and NF-5. When mixed with paintwork materials, the chemical is introduced in small portions, maintaining the concentration of a maximum of 5% of the amount of the film former. The digital index after the letters NF indicates the chemical composition of the drug. So, number 2 shows the presence of lead, number 3 - the presence of manganese, 6 - calcium, 7 - zinc, 8 - iron. Index 7640 shows that the drug is formed by combining cobalt resinate with oil and a solution of lead and manganese salts in white spirit. A similar tool can be used to restore the lost pattern of moiré enamels.
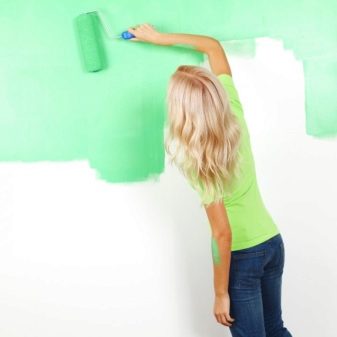
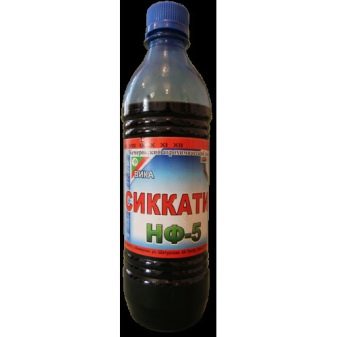
Important: using any desiccant, you need to pay attention to the dosage. Excessive introduction of the reagent dramatically lowers the drying rate of the films and can even change the shade of the dye composition, especially if it is initially white. Cobalt octanate dissolved in white spirit can have an opalescent effect. The largest share of non-volatile substances is 60%, the concentration of metals ranges from 7.5 to 8.5%. There are no copper driers; only pigments are produced on the basis of this metal.
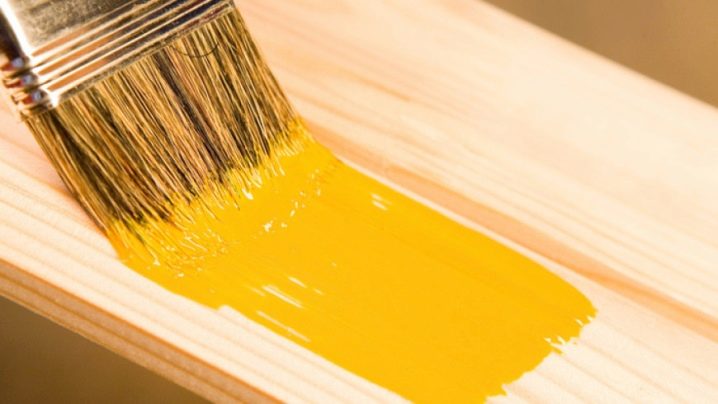
Manufacturers
Among the various brands of driers, the first place is deservedly worth putting the company's products Borchers, whose production is very perfect and meets the latest technological requirements. Judging by the reviews, such mixtures should be introduced in very small concentrations, they are quite economical and practical, and avoid many problems.
Another leading German manufacturer is the concern Synthopol, he also produces high-quality and solid products.
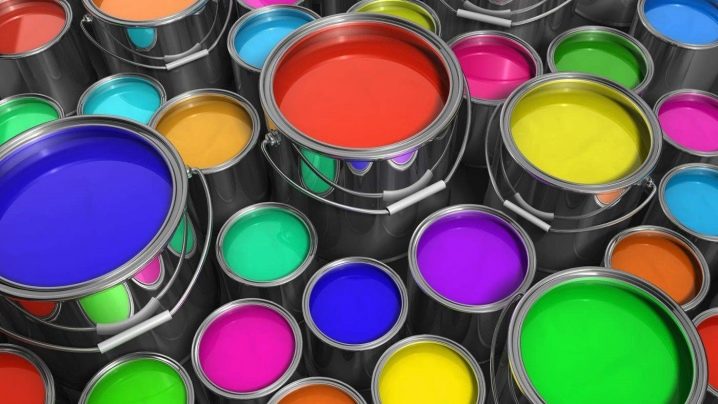
DIY making
The recipe for making driers is relatively simple. To obtain a mixture suitable for processing drying oil, corresponding to GOST, it is necessary to use fused resinate. Porcelain (at least metal) dishes are filled with 50 g of rosin. It is melted at temperatures of 220-250 degrees Celsius. After melting, the substance is stirred and 5 g of quicklime is added to it. Replacing the lime with 15 g of lead lithium, which is ground with linseed oil to a paste, and then introducing small portions into the rosin, lead resinate can be obtained. It is necessary to stir both versions of the compositions until a homogeneous mass is formed. The drops are periodically removed and placed on transparent glass, as soon as they become transparent themselves, it is required to stop heating.
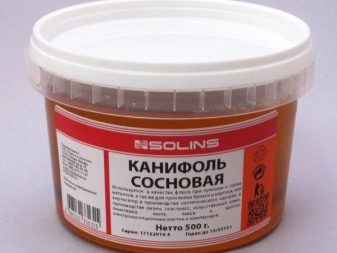
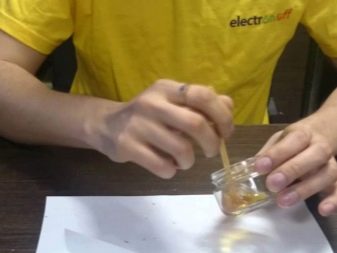
You can also prepare manganese oxide, obtained from sodium sulfite and potassium permanganate (more precisely, their solutions). Upon mixing, a black powdery precipitate is formed. It is filtered and dried in the open air, no heating is needed, it is even harmful.
Scope of application
The use of driers for oil paints has its own subtlety; if an excess of oil derivatives forms in the paint layer, it can soften again. The reason is that polymerized oil is prone to colloidal coagulation. Combined varnishes, according to some experts, may not include desiccants, because the inclusion of cellulose nitrate increases the drying rate. But in water systems, as with the need to get the most rapidly drying varnish, it is necessary to add a desiccant.
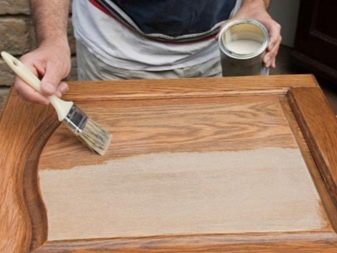
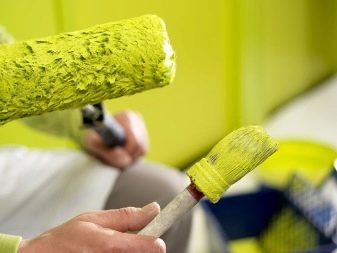
Practical experience has shown that significant temperatures eliminate the need for solidification accelerators. Always use the desiccants recommended by the paint manufacturers.
Usage Tips
The calculation of the amount of desiccant that needs to be added to the PF-060 alkyd varnish for effective hardening ranges from 2 to 7%. With the introduction of such an additive, the drying time is limited to 24 hours. This result is achieved even with the abandonment of lead-containing preparations in favor of more modern technological solutions, which are still met with distrust by many. The shelf life of driers in most cases is six months.
Important: recommendations for the introduction of a desiccant do not apply to any ready-made mixtures in principle. Already in production, the required amount of all substances was initially introduced there, and if not (the product is of poor quality), it will still not work to assess the problem and fix it at home. In relation to the film former, you can enter from 0.03 to 0.05% cobalt, from 0.022 to 0.04% manganese, from 0.05 to 2% calcium and from 0.08 to 0.15% zirconium.
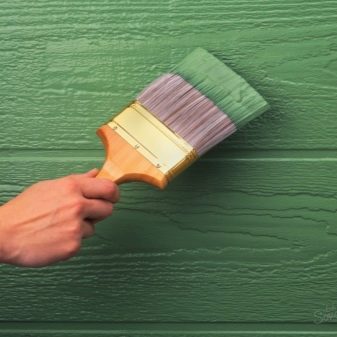
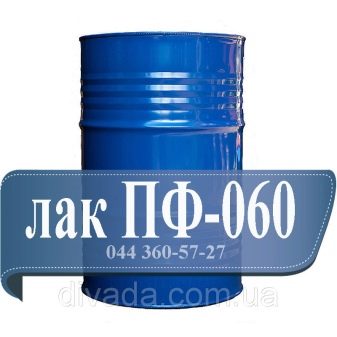
Attention! The proportions are indicated in terms of pure metal, and not on the absolute volume of the mixture, its amount, of course, is somewhat higher.
In the presence of soot, ultramarine and some other components in the coloring matter, the surface effect of the desiccant is weakened. This can be dealt with by the introduction of increased doses of the drug (both immediately and in separate portions, more detailed recommendations can only be given by a qualified technologist).
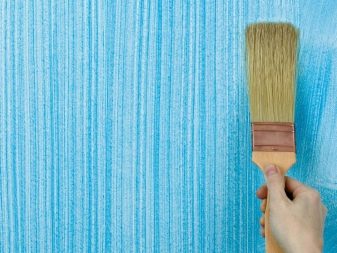
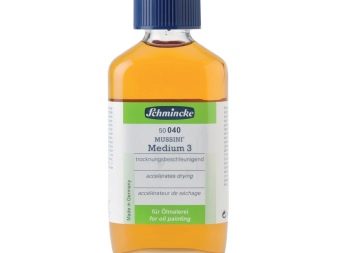
How to use a drying oil drier, see the next video.
The comment was sent successfully.