Natural drying oil: properties and application features
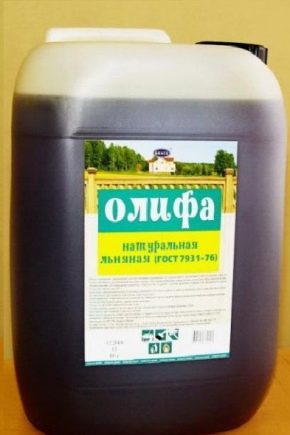
During the times of the Soviet Union, drying oil was practically the only means with which wooden surfaces and buildings were treated. The fans of this material have remained to this day.
Drying oil is a film-forming paint and varnish substance based on natural oils or heat-treated alkyd resins.
It reliably protects wood from rotting and the appearance of fungus, and is also used for the manufacture of oil putties and paints.
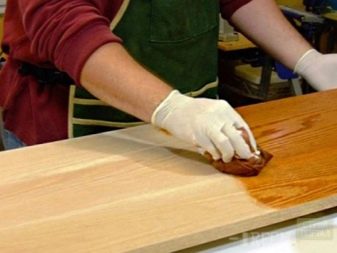
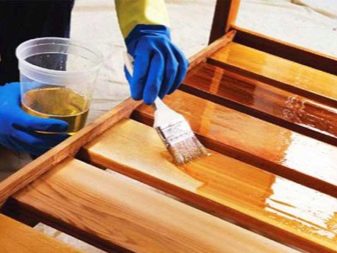
Types, composition and properties
Nowadays, many homeowners seek to protect themselves and their households from unnecessary chemicals. In this regard, drying oil is rightfully considered a unique material! More than 90% of its composition is accounted for by components obtained from flax, hemp, sunflower or rapeseed. The remaining 5% are synthetic compounds, but their amount is so insignificant that they cannot have any adverse effect on humans. Moreover, the lower the percentage of synthetics in the drying oil, the longer the wood product lasts after processing.
When choosing drying oil, be sure to focus on its composition - the more natural ingredients it contains, the more protection the wood will receive.
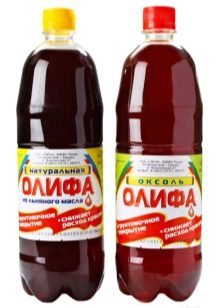
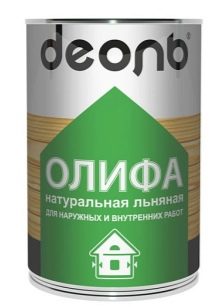

In the old days, drying oil was called "boiled butter". Today, the technology of its production practically does not differ from the "ancient" methods. However, the variability of the composition led to a large number of varieties of drying oil with very different properties.
Oil varnishes are made from vegetable oils with the addition of special substances, causing the acceleration of their drying - succates. For this purpose, compounds of cobalt, lead, strontium, zirconium and iron are used - the name of these elements raises doubts about their safety for human life and health, however, their share is negligible, so you can not be afraid of negative effects on the body. But if you want to play it safe, then give preference to compositions with cobalt - this metal does not have a negative effect on the physiological processes of adult and children's organisms. You can also purchase a 100% oil-free formulation.
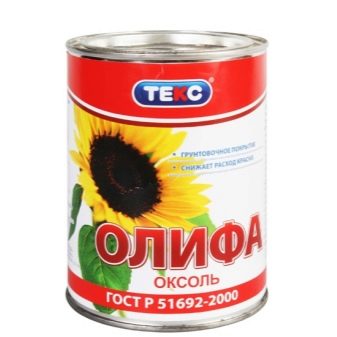
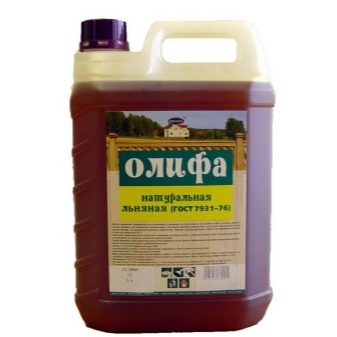
The desiccant absorbs oxygen from the air, thereby oxidizing the oil. Moreover, after it dries, oxidative reactions do not stop, which is why the proportion of such additives is extremely small, otherwise the coating quickly darkens and becomes brittle.
Drying oils with and without desiccants have some differences in their operational parameters:
- Oil varnishes harden in 24 hours, and in the hot season 5 hours are enough for them to form a dense protective film. Drying oil dries without driers for 5 days, keep this in mind when planning repairs in the house.
- The composition without desiccant penetrates deeper into the wood fibers and in the future protects it more reliably from moisture and mold. Compounds with additives will not be absorbed so deeply, and in the future, the film may crack and peel off.
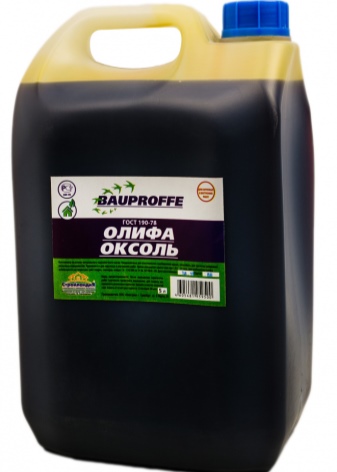
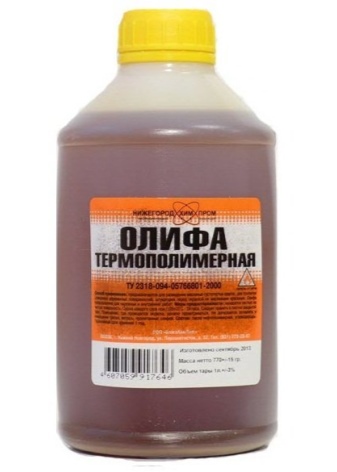
The performance characteristics, in particular the drying rate, are also influenced by the oils used for production. The drying oil from linseed and hemp oil hardens the fastest. This is due to the large amount of polyunsaturated acids in their composition (the iodine number is 175-204 for the first and 145-167 for the second).Sunflower oil dries much more slowly, therefore, it must contain insignificant desiccants, but linseed oil from nut and poppy seed oil without additives will take quite a long time to solidify. Castor, olive and grease linseed oil will not solidify at all without driers, it only thickens, without forming the necessary film coating - the iodine number of the oils that make up them is negligible.
To accelerate the drying rate, manufacturers have released a series of drying oils based on synthetic components.
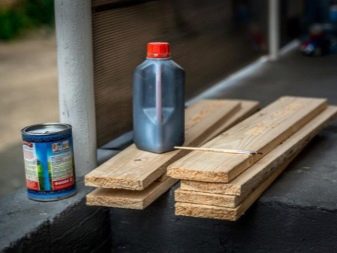
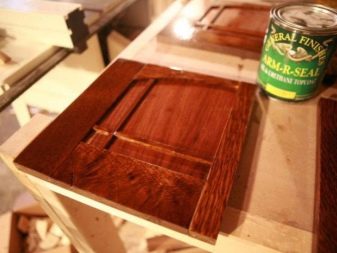
Combined compositions are closest to oils - they consist of 2/3 of oil and 1/3 of white spirit or other solvent. These mixtures are distinguished by a lower cost and a high curing rate, therefore they are widely used in external facade works. By the way, contrary to popular belief, combined drying oils have almost no pungent odor.
When a large number of additives are added to oils, drying oil oxol is obtained. It contains oil (55%), white spirit (40%) and desiccant (5%). Oxol has a good solidification rate, however, it has a pungent chemical odor that does not fade for a long time.
Oksol in appearance is no different from natural, but its price is significantly lower than oil formulations.
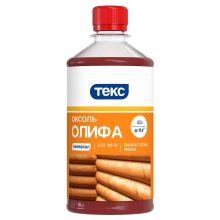
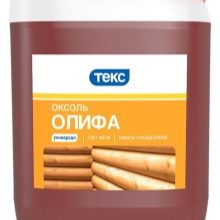
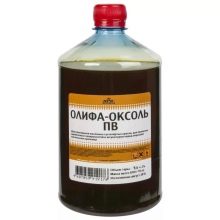
Distinguish between brands B and PV. Linseed oil B is made using linseed or hemp oils; it has found its application in the paint and varnish industry for the cultivation and production of facade paints.
For the manufacture of oxol VP use sunflower, safflower or corn oil. This formulation is popular due to its extremely low cost. However, its performance leaves much to be desired - such oxol does not create a strong and durable coating, therefore the scope of its use is limited to diluting paints.
It is not recommended to use it for covering wooden products.
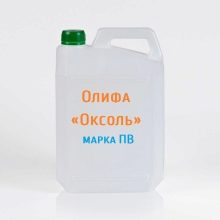
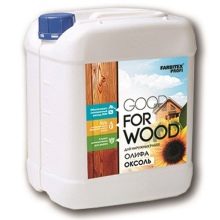
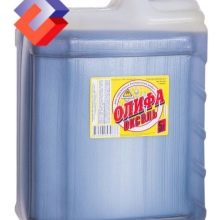
Another type of drying oil is alkyd. They are made from resins diluted with solvents and modified oils. By analogy with oil varnishes, a desiccant is added, as well as white spirit. Such compositions are more economical than oil ones, since in order to make 1 ton of alkyd drying oil, only 300 kg of oil are required. This significantly reduces the cost of the product, but makes it unsafe for indoor use.
In addition, alkyd compounds are resistant to the negative effects of the external environment, temperature and humidity extremes, and are resistant to direct ultraviolet rays. This drying oil is recognized by consumers as the most optimal in terms of price / quality ratio.
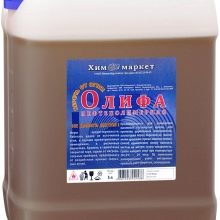
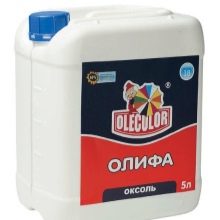
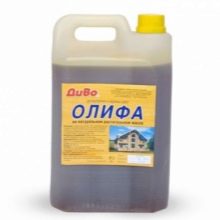
Separately in the assortment list of drying oils are synthetic brands. They are made from refined products, they are not subject to GOST 7931-76, they are manufactured according to TU. They harden for a long time, smell unpleasant, and after hardening they give a glassy fragile film.
Such compositions are usually used to dilute enamels.
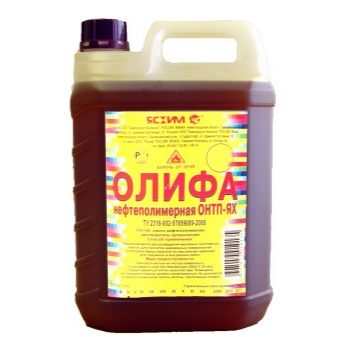
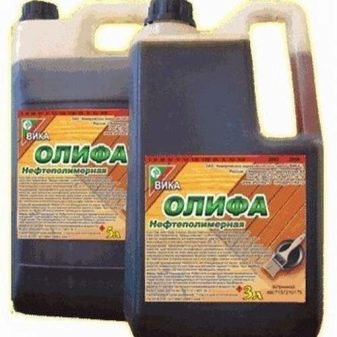
Advantages and disadvantages
Oil varnish has a number of undoubted advantages, due to its technical parameters:
- the proportion of oil and additives - 97: 3;
- drying speed does not exceed 24 hours at an air temperature of 20-22 degrees Celsius;
- density - 0.93-0.95 g / m3;
- sludge - no more than 0.3;
- acid number - 5 (mg KOH).
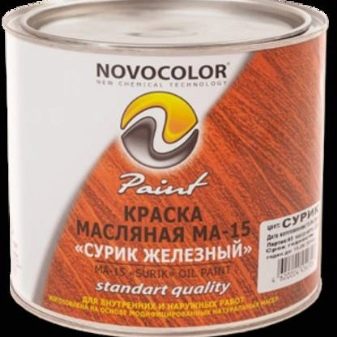
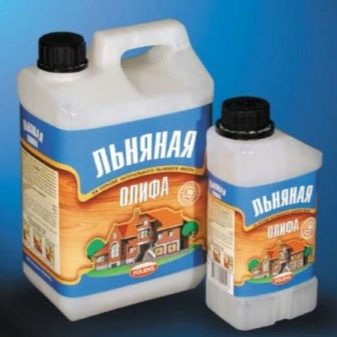
The advantages of the material are obvious:
- Natural linseed oil has practically no solvents, so it does not give off a pungent odor and is considered safe for the health of children and adults.
- The oil components penetrate deeply into the wood fibers, thereby increasing their service life by several decades, even if the surface is used in high humidity conditions.
- Impregnation with natural linseed oil creates a film that protects the wood from the growth of fungus and rot.
- The use of natural and affordable raw materials makes drying oil not only environmentally friendly, but also a cheap material that has proven its effectiveness for many years.
- The use of drying oils at the stage of preparation for finishing leads to savings in the consumption of materials for painting.
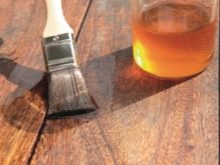
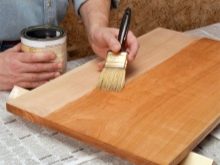
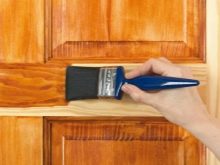
The disadvantages of many include the speed of drying - after processing, the surface dries within a day, so repair work is stopped.
Manufacturers
Very often, from people who have covered plywood, window frames and other surfaces with linseed oil, you can hear that it hardens for too long. Experts say that if the material does not dry out within 24 hours at room temperature and humidity up to 60%, then most likely it is a poor-quality product, an oil mixture sold under the guise of natural drying oil.
Non-drying composition is a marriage or a fake.
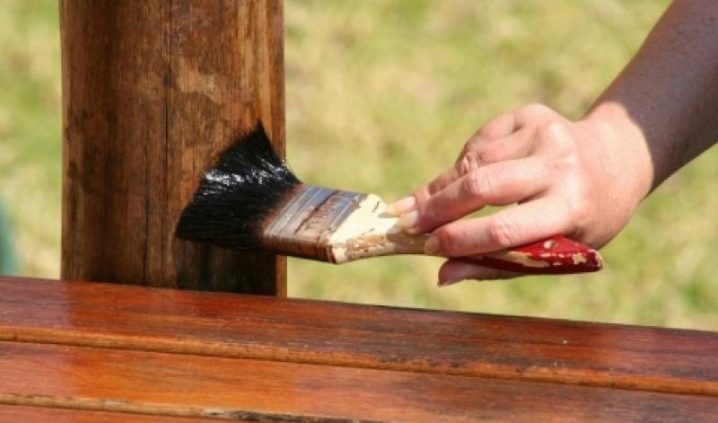
In order to avoid the unpleasant consequences associated with the acquisition of an unsuitable composition, buy products from trusted manufacturers.
High-quality drying oil is allowed in Russia:
- Ufa paint and varnish plant;
- Kotovsky paint and varnish plant;
- Perm paint and varnish plant;
- Management company ZLKZ;
- Azov paint and varnish plant "Divo";
- Bobrovsky experimental plant.
The drying oil produced by the Estonian company Vekker has proven itself very well.
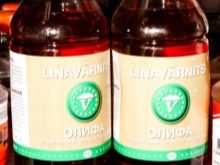
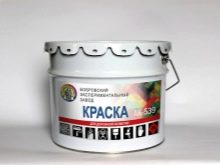

Its exceptional quality has expanded its scope of application beyond the construction industry. This composition is widely used by painters to create and restore icons.
How to choose?
Before you buy drying oil, you should look at its color and consistency. Normally, the shade ranges from yellow to dark brown. Suspended particles, stratification and lumps should not be observed in the solution.
The label must indicate the number of GOST or TU, if you buy a composite drying oil, the name and address of the manufacturer, composition and technology of use.
As for the areas of application of different types of drying oils in repair work, follow a simple rule: for external coatings, combined compositions with an oil content of up to 45% are suitable, for internal coatings, you should give preference to an improved brand, in which the percentage of natural components is from 70 and above.
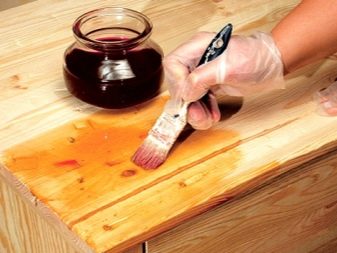
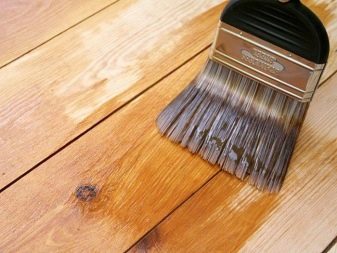
Can I do it myself?
You can make drying oil with your own hands at home. For this, as a rule, sunflower and linseed oil is used.
For production, you will need a metal container, a heating device, manganese peroxide, rosin, as well as personal respiratory and skin protection.
The drying technology is simple, but requires caution and adherence to safety rules.
The oil is poured into a container and heated over low heat to a temperature of 110 degrees.
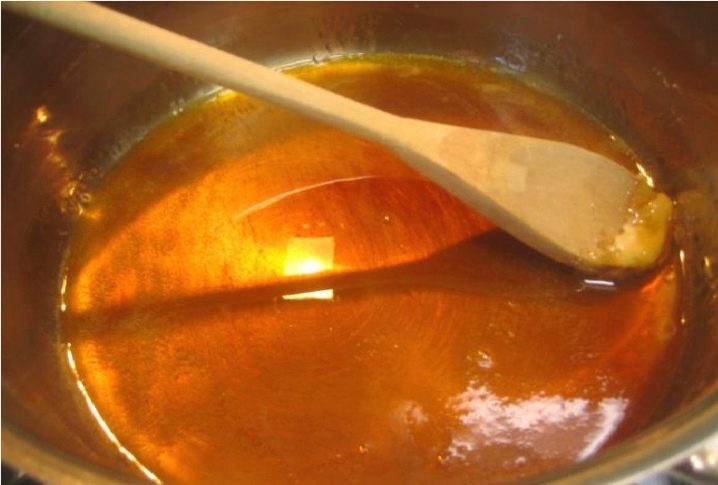
At this moment, the evaporation of water will begin, which can be seen with the naked eye. The oil should be digested within 4 hours. During this period, it is necessary to ensure that the temperature does not exceed 160 degrees. After the required period has expired, a desiccant is added to the oil (it can be made from rosin and manganese peroxide in a ratio of 20 to 1) at the rate of 30 g of substance per 1 liter of oil. The mixture should be cooked for another 3 hours, after which the drying oil is considered ready. By the way, readiness is checked very simply - a drop of the composition is placed on the glass, and if it is transparent, then the drying oil is ready.
When the desiccant is added, increased foaming and flaking is observed; to reduce the intensity of this process, you can add a little ready-made factory drying oil to the container.
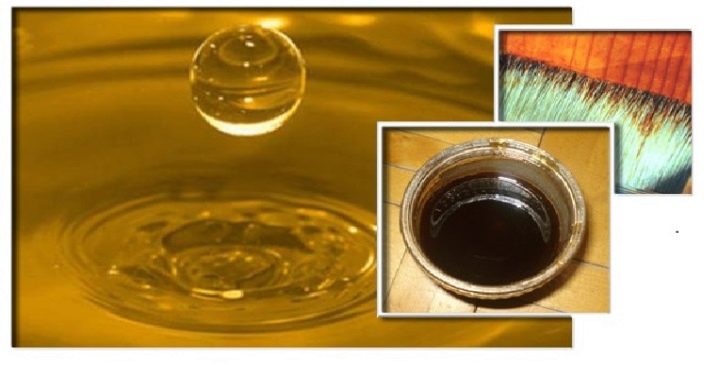
In the next video, you can watch how to make natural linseed oil drying oil at home.
Application features
In order to apply drying oil, no special construction skills are required.
The technology is extremely simple for both repair and art work:
- Before application, the surface to be treated should be cleaned of traces of old coatings, grease and dust;
- The surface should dry out, since the use of the composition on damp wood does not make sense;
- For coating, a roller or brush is required - large flat surfaces are processed with a roller, and small elements and corners - with a small brush;
- To achieve the desired result, one or two layers are enough.
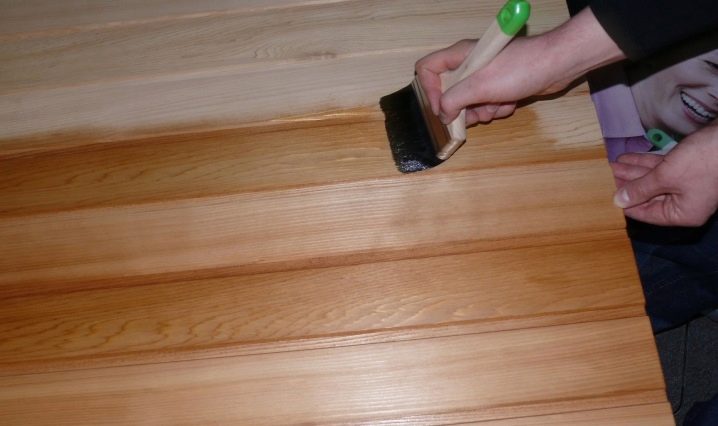
A few tips:
- The thickened drying oil can be diluted with a solvent or nefras.
- Before use, the drying oil must be thoroughly mixed. This gives the structure an increased saturation with the necessary oxygen.
- When carrying out interior work, it is extremely important to ensure maximum ventilation. It helps to reduce drying times and weathering of unpleasant odors.
- Protect your hands from contact with the substance when working. If you do get dirty, then moisten the skin with vegetable oil, and then rinse well with running water and soap.
- Remember that drying oil has a high fire hazard, so store it in a place inaccessible to sparks, do not carry out welding work and do not smoke near the treated surface.
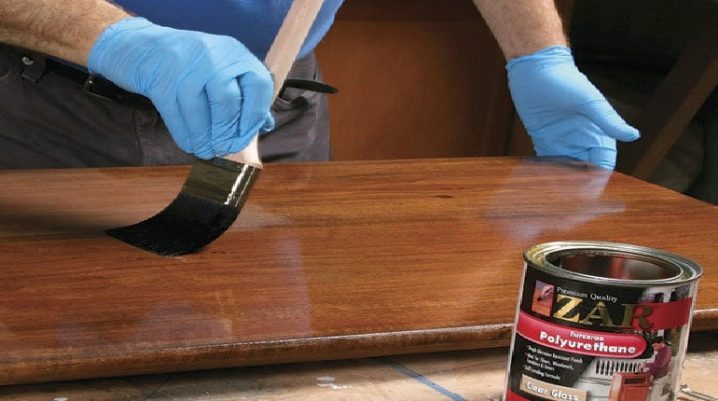
The comment was sent successfully.