Drying oil: varieties and application
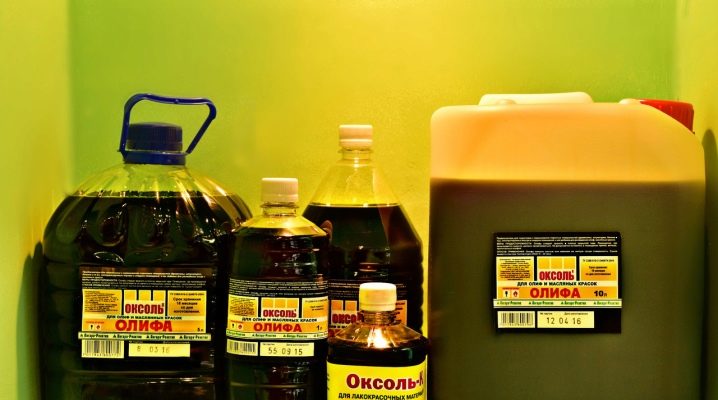
Decorating premises often means processing them with paints and varnishes. This is a familiar and convenient solution. But in order to correctly apply the same drying oil, it is required to thoroughly study the features of such a coating and its varieties.
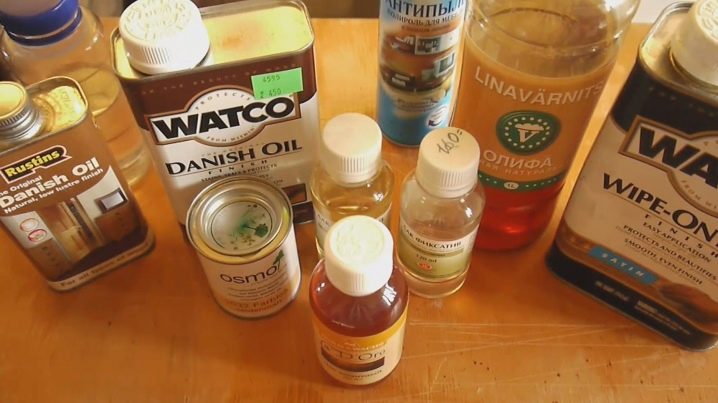
What it is?
Wood is back among the leaders in consumer preferences, and plastics and other synthetic materials are losing demand. But it is important to understand that wood needs professional high-quality processing, and drying oil allows you to cover the wooden base with a protective film, while ensuring a high level of sanitary safety. The main part of such compositions is formed by natural ingredients (vegetable oils), and they account for at least 45% of the mass.
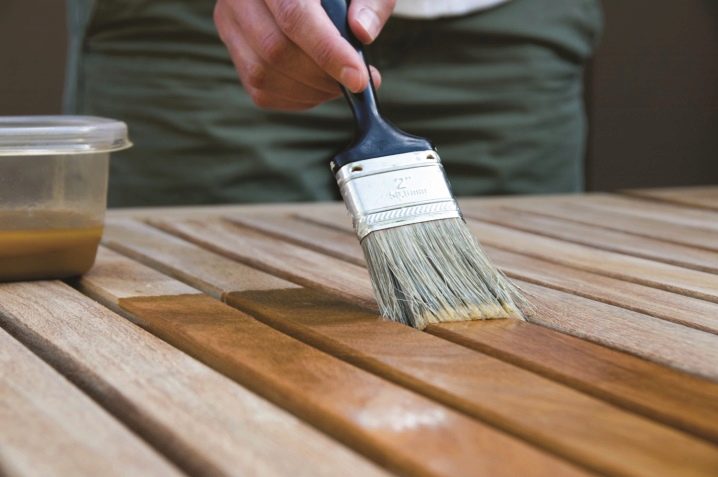
Application features
Drying oil was first mastered by artists several centuries ago. Manufacturing techniques have changed little since then, but there are several key material varieties that need to be applied in different ways.
Processing with a combined composition is practiced due to its great cheapness. (up to a third of the mixture falls on the solvent, mainly white spirit). The drying speed increases sharply, the reliability of the created layer is very high. Basically, such combinations are used for external finishing of wooden surfaces, from which the unpleasant odor quickly disappears.
All drying oils, excluding natural compounds, contain substances that are prone to fire and even explosion, so they should be handled with the utmost care.
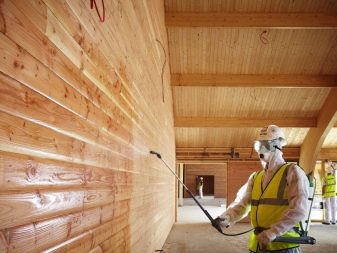
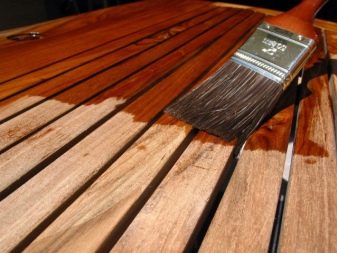
When covering a tree, natural linseed oil dries for a maximum of 24 hours (at a standard room temperature of 20 degrees). Hemp formulations have the same parameters. After a day, mixtures based on sunflower oil retain their stickiness a little more. Combined materials are more stable and are guaranteed to dry out in 1 day. For synthetic varieties, this is the shortest period, since the level of evaporation is less.
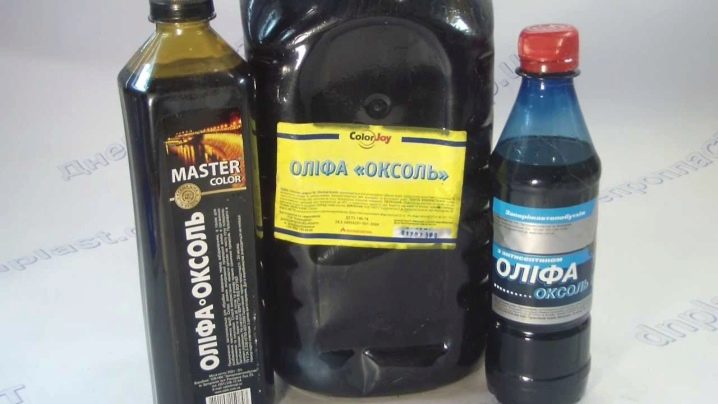
Often (especially after long-term storage) it becomes necessary to dilute the drying oil. Natural mixtures are kept in the best condition, as vegetable oils can remain in a liquid consistency for a long time. Given the danger of such compounds, in order to dilute the thickened mixture, you need to thoroughly prepare.
This requires:
- choose a room with excellent ventilation;
- work only away from open flames and heat sources;
- apply strictly tested formulations recommended by the manufacturer for a specific material.
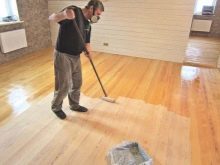
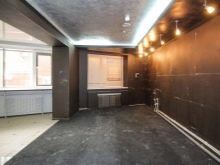
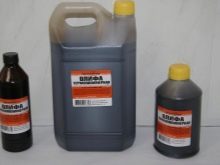
When working with synthetic materials, as with mixtures of unknown chemical composition, rubber gloves must be worn before dilution.
It is important to remember that in case of contact with the skin, certain substances can provoke chemical burns.
Most often, when diluting drying oil, they are used:
- White Spirit;
- castor oil;
- other industrially manufactured chemicals.
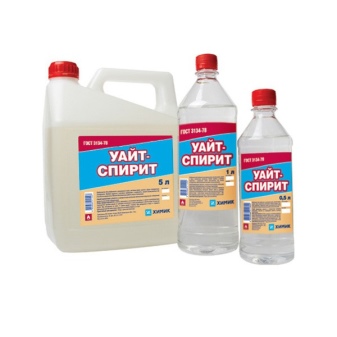
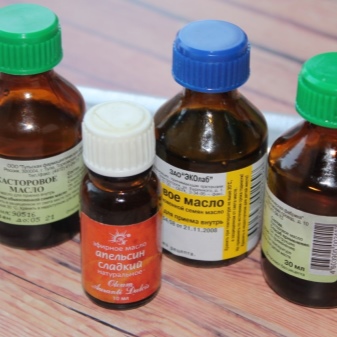
Typically, the concentration of the added solvent in relation to the weight of the drying oil is a maximum of 10% (unless otherwise provided by the instructions).
Experienced specialists and builders do not use drying oil that has remained in a hermetically sealed container for more than 12 months. Even if the liquid phase, external transparency and the absence of precipitated sediment are retained, the material is no longer suitable for work and represents a great danger.
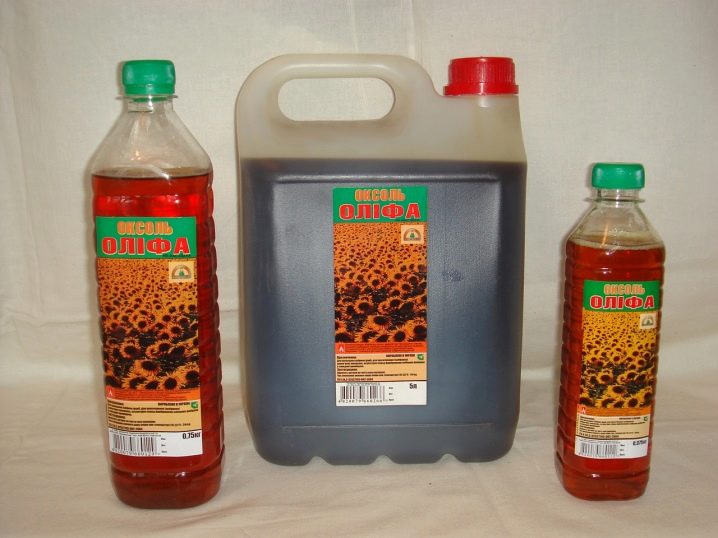
If you are confident in the quality of the protective coatings that have produced a precipitate, it is sufficient in most cases to filter the liquid through a metal sieve. Then small particles will not end up on the surface of the wood, and it will not lose its smoothness. You can often hear statements that drying oil should not be diluted at all, because it still will not restore its characteristics. But, at least, the fluidity and viscosity will improve, the penetrating ability will increase, and therefore it will be possible to cover the area with linseed oil that does not require an increased quality of processing.
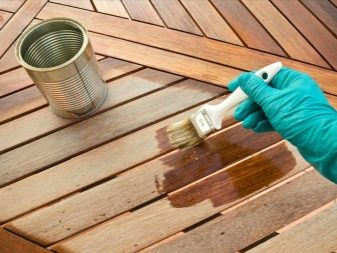
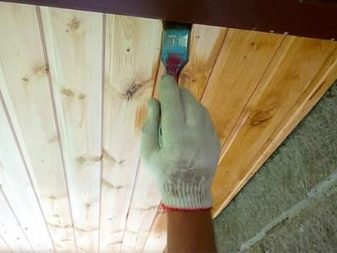
Wood stabilization with drying oil implies that the processed products must be completely immersed in the liquid.
During operation, the quality is checked in stages, carrying out control weighing at least three times:
- before soaking;
- after final impregnation;
- after the end of the polymerization process.
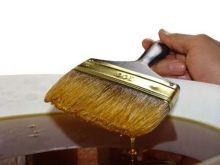
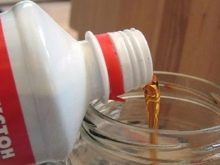
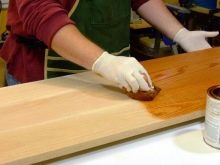
To dry the polymer and make it harden faster, the bars are sometimes placed in an oven or boiled in boiling water. Window putty can be made on the basis of a mixture of drying oil and ground chalk (they are taken, respectively, 3 and 8 parts). The readiness of the mass is judged by how homogeneous it is. It must be pulled, and the resulting tape must not break.
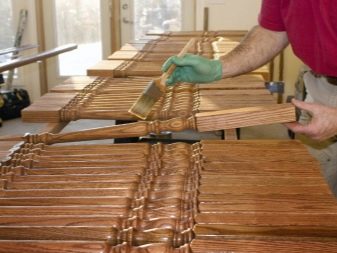
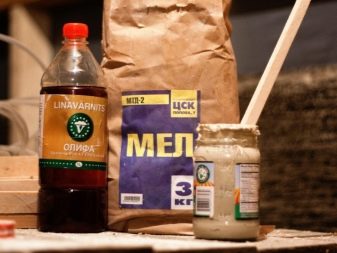
Types: how to choose?
Regardless of the abundance of manufacturers, the production methods are about the same, at least with regard to natural formulations. Vegetable oil is taken, heat treatment is carried out and desiccants are introduced at the end of filtration. GOST 7931 - 76, according to which such material is produced, is considered obsolete, but there are no other regulatory documents.
The composition of drying oil can include various types of desiccant, first of all, these are metals:
- manganese;
- cobalt;
- lead;
- iron;
- strontium or lithium.
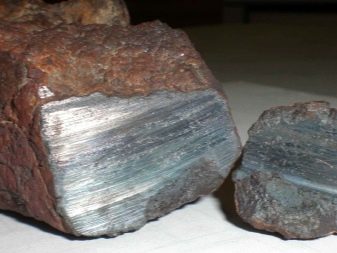
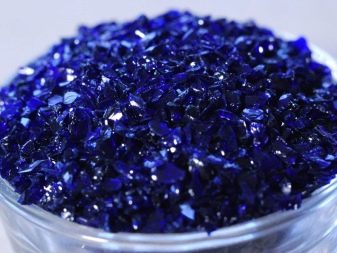

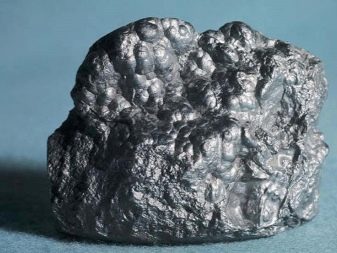
When familiarizing yourself with a chemical recipe, you need to focus on the concentration of reagents. The safest are considered by experts to be driers based on cobalt, the concentration of which should be 3-5% (lower values are useless, and large ones are already dangerous). At a higher concentration, the layer will polymerize extremely quickly even after drying, because the surface will darken and crack. For this reason, painters traditionally use varnishes and paints without the introduction of driers.
Drying oil of the K2 brand is intended strictly for interior finishing work, it is darker than the 3rd grade. The presence of such a substance increases the uniformity and uniformity of drying. A brush is required to apply the material.
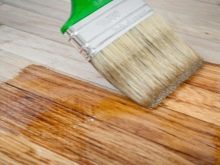
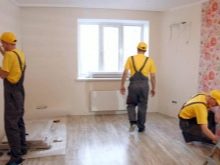
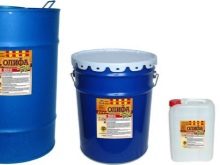
Natural
This drying oil is the most environmentally friendly, there is also a drier in it, but the concentration of such an additive is low.
The main technical characteristics (properties) of natural drying oil are as follows:
- share of desiccant - maximum 3.97%;
- drying takes place at temperatures from 20 to 22 degrees;
- final drying takes exactly one day;
- the density of the composition is 0.94 or 0.95 g per 1 cubic meter. m .;
- acidity is strictly normalized;
- phosphorus compounds cannot be present by more than 0.015%.
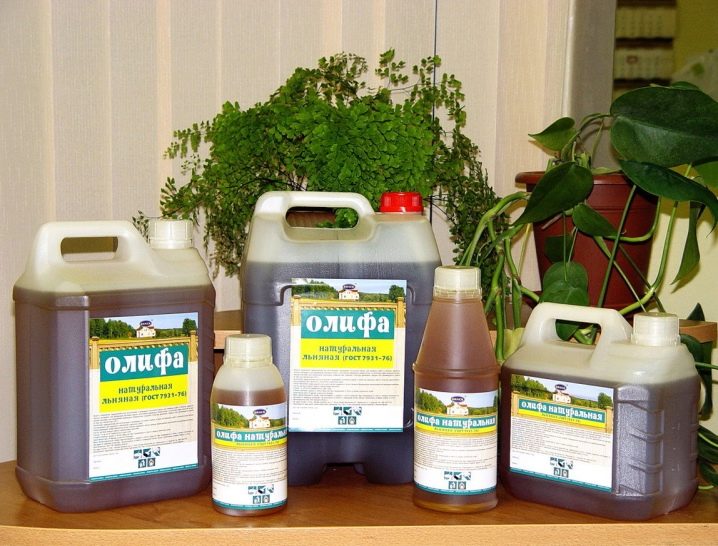
Subsequent surface treatment with varnishes or paints is not possible. The wood completely retains its decorative parameters.
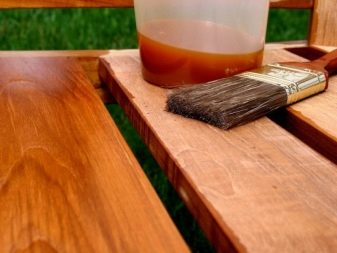
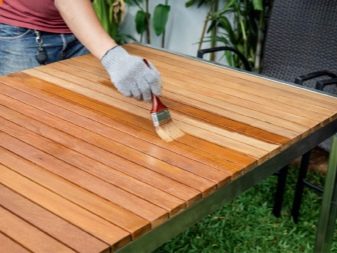
Oksol
Oksol varnish is obtained with a large dilution of vegetable oils, such a combination of substances must comply with GOST 190-78. The composition must necessarily contain 55% of natural ingredients, to which a solvent and a desiccant are added. Oxol, like the combined drying oil, is inappropriate to use indoors - solvents emit a strong unpleasant odor, sometimes remaining even after hardening.
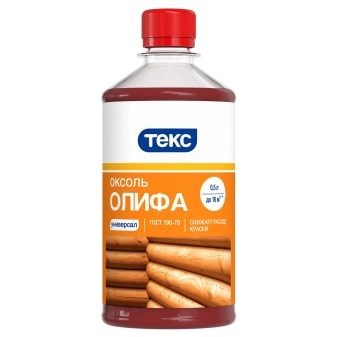
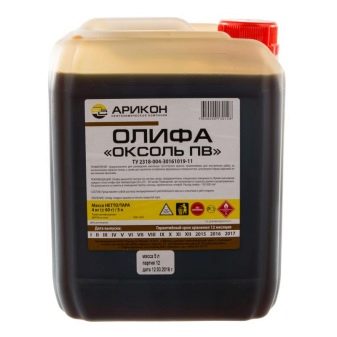
The advantage of this mixture is its affordable price. With the help of the composition, oil paints and varnishes can be diluted, since the intrinsic protective properties of the material are not enough in practice. Of the various oxols, flaxseed oil formulations are best used, which form a stronger film and dry faster.
Oksol is divided into several types. So, the material marked with the letter B can only be used for outdoor work. The composition of the PV is needed when you need to prepare a putty.
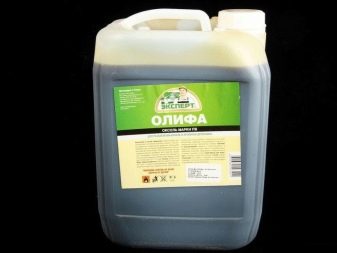
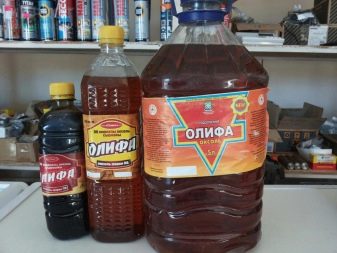
In the first case, for the production of the mixture, you need linseed and hemp oil. Oxol category B can be used to obtain oil or dilute thickly grated paint. Such mixtures cannot be used in flooring.
Oksol varnish of PV brand is always made from technical camelina and grape oils. It also contains vegetable oils that cannot be used in food directly or by processing: safflower, soy and unrefined corn oils. The raw material should not contain more than 0.3% of phosphorus compounds, there should be even less of them, depending on the counting method. Opening metal packaging is only allowed with tools that do not produce sparks upon impact. It is forbidden to make an open fire where drying oil is stored and used, all lighting devices must be mounted according to an explosion-proof scheme.
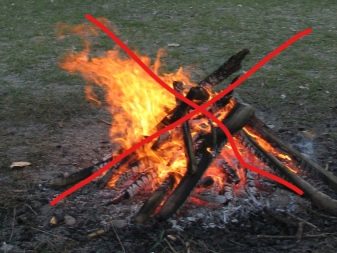
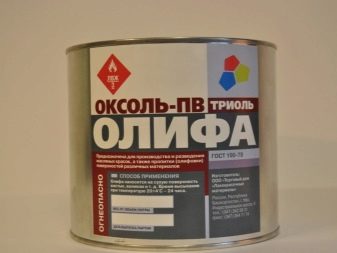
Oksol drying oil can only be used:
- outdoors;
- in intensively ventilated areas;
- in rooms equipped with supply and exhaust ventilation means.
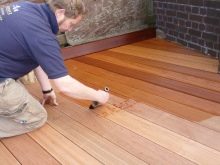
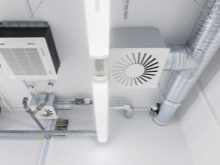
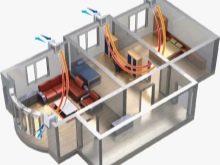
Alkyd drying oil
The alkyd variety of drying oil is at the same time very cheap, the most durable and mechanically resistant. Such mixtures are needed where heavy rainfall constantly falls, there are temperature drops and solar radiation. The surface of outdoor timber structures will remain in excellent condition for at least several years. But alkyd compositions are allowed only as a means of pretreatment, in a stand-alone form they are not effective enough. It is inappropriate to use them indoors as well due to the strong unpleasant odor.
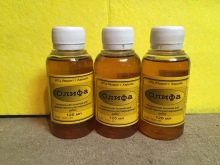
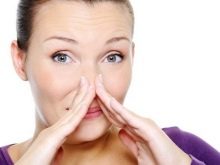
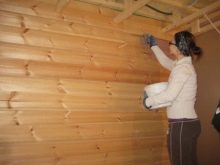
Alkyd varnish should be applied to wooden surfaces with paint brushes, and they are cleaned in advance and monitored for dryness. Approximately 24 hours after the first layer, you need to put the next one, while the temperature is 16 degrees or more.
Drying oil based on alkyd resins is divided into three main groups:
- pentaphthalic;
- glyphthalic;
- xiftal.
Basically, such materials are supplied in transparent containers, occasionally in barrels. Approximately 20 hours after impregnation, the wood can be painted over.
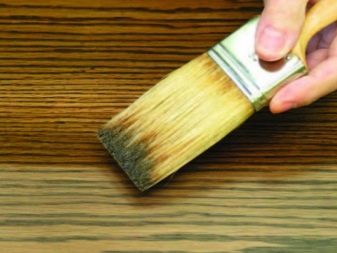
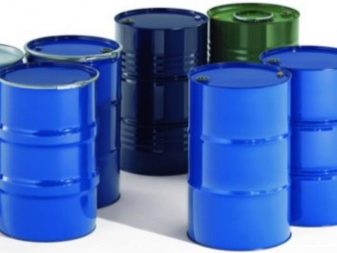
The colors of the drying oil are determined by the iodometric scale method, like many other paints and varnishes. The color is influenced by the tone of hydroxycarboxylic acids and the type of used vegetable oils. The lightest tones can be obtained by using dehydrated castor oil. Where an electric current flows, dark areas are formed, they can also be caused by strong heating and the appearance of significant volumes of sludge.
As for the expiration date, the current state standards do not prescribe it directly.
The longest storage time for drying oil is 2 years (only in rooms that are maximally protected from negative external factors), and for 2 - 3 days you can leave it in an open place. Towards the end of the shelf life, the material can be used, if not for protective purposes, then as a means for ignition.
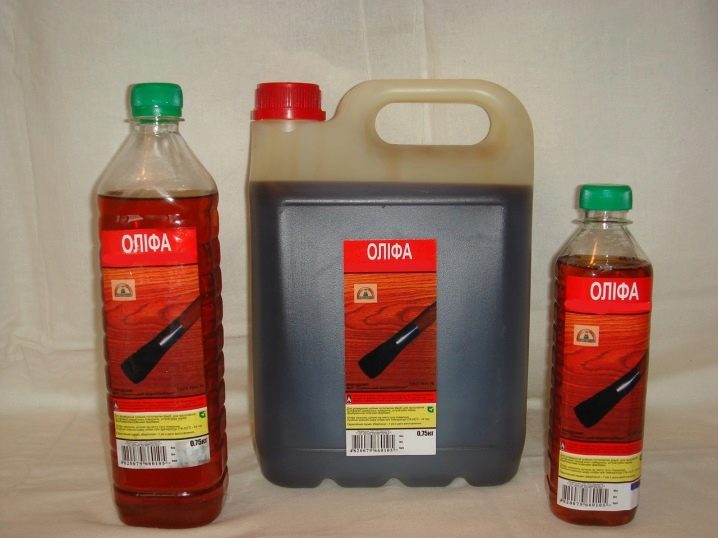
Polymer
Polymer drying oil is a synthetic product obtained by the polymerization of petroleum products and diluted with a solvent. The smell of such a material is very strong and unpleasant, under the influence of ultraviolet radiation, a rapid decay occurs. Polymer drying oils dry quickly, give a strong film with a glossy sheen, but the joinery is poorly impregnated with them. Since the formulation does not include any oils, the settling rate of the pigments is very high.
It is advisable to use polymer varnish when thinning oil paint dark colors, intended for secondary painting work; it is imperative to intensively ventilate the room.
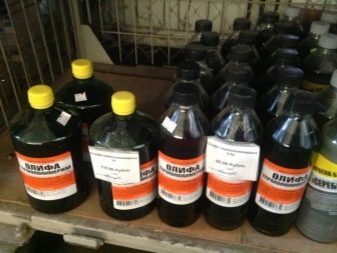
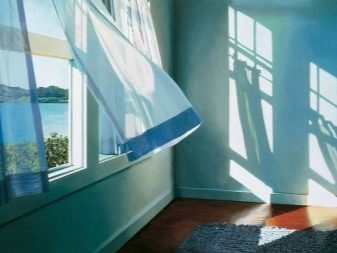
Combined
Combined drying oils differ little from partially natural ones, but they contain 70% oils, and about 30% of the mass falls on solvents. To obtain these substances, it is necessary to polymerize the drying or semi-drying oil and free it from water. The key area of use is the release of thickly grated paint, complete drying occurs in a maximum of a day. The concentration of non-volatile substances is at least 50%.
The use of combined drying oils sometimes gives better results.than using oxol, especially in terms of strength, durability, water resistance and weather resistance. Consideration should be given to the risk of thickening during long-term storage due to chemical reactions between free fatty acids and mineral pigments.
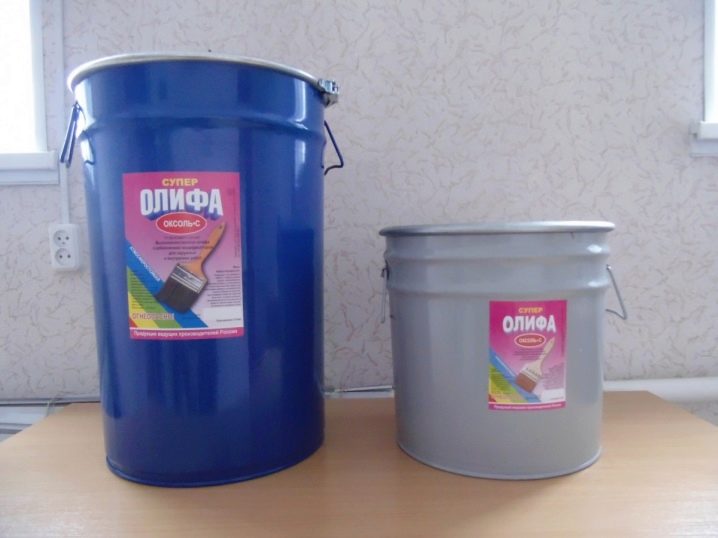
Synthetic
All drying oils of the synthetic series are obtained by oil refining; GOST has not been developed for their production, there are only a number of technical conditions. The color is usually lighter than natural formulations, and the transparency increases. Oil shale oils and ethinol give a strong unpleasant odor and dry for a very long time. The shale material is obtained by oxidizing the oil of the same name in xylene. It is mainly used for dark tint and paint thinning to the desired consistency.
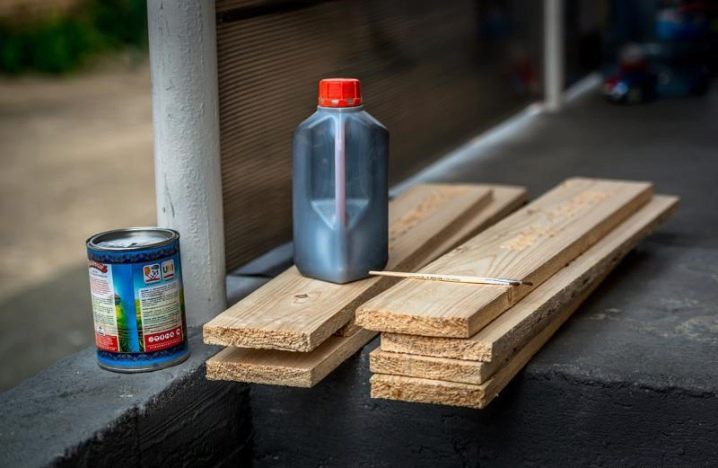
It is unacceptable to use synthetic impregnations for floorboards and other household items. Etinol is lighter than shale material and is produced using waste from chloroprene rubber. The created film is very strong, dries quickly and outwardly shiny, it effectively resists alkalis and acids. But the level of its resistance to weathering is not great enough.
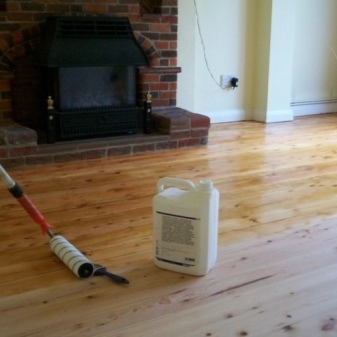
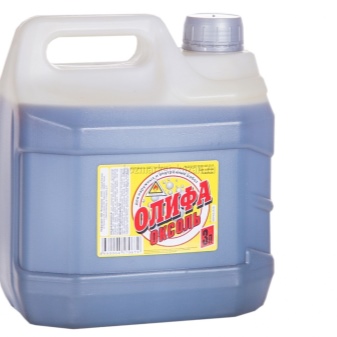
Compositional
Composite drying oil is not just lighter than natural or oxol, but sometimes has a reddish tint. The cost of the material is always one of the lowest. But it is used only in extremely rare cases, the paint and varnish industry has not used such a substance for a long time.
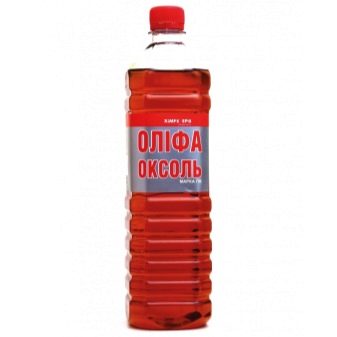
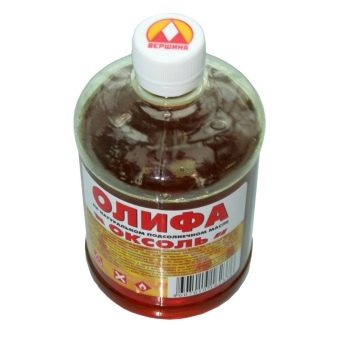
Consumption
To ensure the minimum consumption of material per 1m2, it is necessary to choose oxol, especially since all combinations of this series dry faster than a natural mixture. Linseed oil is consumed at 0.08 - 0.1 kg per 1 sq. m, that is, 1 liter of it can be located on 10 - 12 sq. m. Consumption by weight for plywood and concrete for each type of drying oil in a particular case is strictly individual. It is necessary to find out the relevant data in the instructions from the manufacturer and in the accompanying materials.
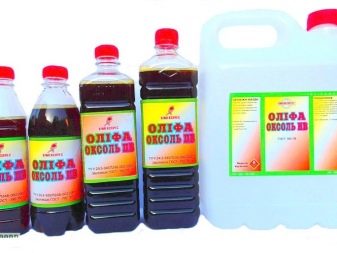
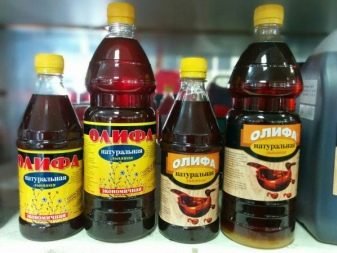
Usage Tips
Drying time is reduced when choosing solutions with the addition of polymetallic desiccants. Natural linen material will dry in 20 hours mixed with lead, and if you add manganese, this period will be reduced to 12 hours. By using a combination of both metals, the wait can be reduced to 8 hours. Even with the same type of desiccant, the actual temperature is very important.
When the air warms up to more than 25 degrees, the drying rate of drying oil with cobalt additives doubles, and sometimes triples with manganese additives. But humidity from 70% sharply increases the drying time.
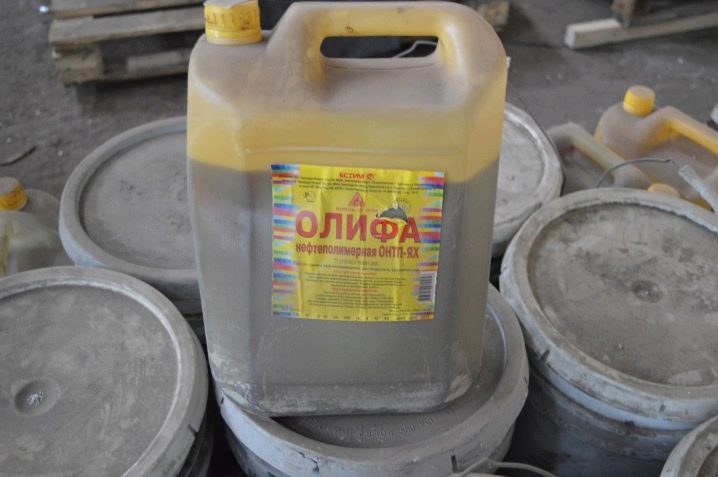
In some cases, users are not interested in applying drying oil, but, on the contrary, in an effective way to get rid of it. Such material is removed from wooden surfaces using gasoline, which is rubbed onto the desired area. Wait 20 minutes and the oil will collect on the surface. This technique will only help against the surface layer, the absorbed liquid can no longer be removed outside. White spirit can be considered a substitute for gasoline, the smell of which is somewhat better, and the principle of action is similar.
It is okay to use paint thinner, but not acetone, because it will not work. Linseed oil and wood stain should not be confused, the role of the latter is purely decorative, it has no protective properties.
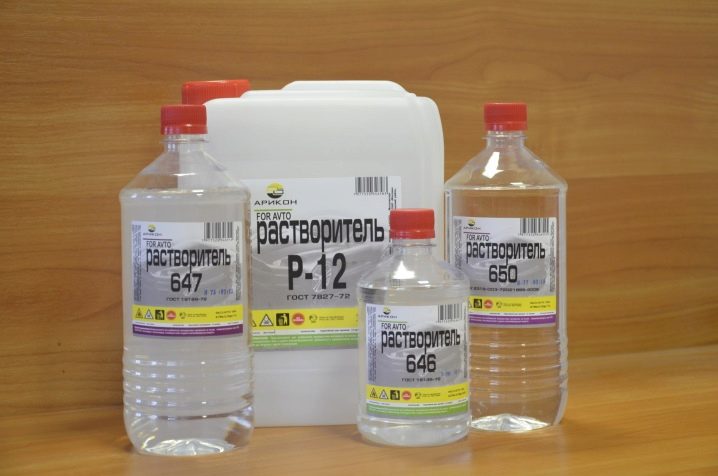
It is very important to escape from the smell in the apartment for a large number of users making repairs.It is worth putting furniture in the kitchen or finishing work, as this unpleasant smell begins to haunt the tenants for several weeks or even months. Therefore, after processing, it is necessary to ventilate the room for at least 72 hours, preferably even at night. The room itself needs to be sealed to remove unwanted "odor".
Then newspapers are burned. Better not even burning them in fire, but slow smoldering, because it produces more smoke. Collected smoke must not be ventilated for at least 30 minutes. You should not act in this way if varnishing was carried out.
Without fire, you can get rid of the smell of drying oil with water: several containers with it are placed in the room and changed every 2-3 hours, the release from the unpleasant smell will occur on the second or third day. Putting salt next to the surfaces decorated with linseed oil, it is changed daily, freshness will come on the third or fifth day.
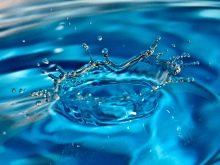
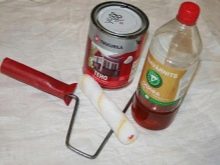
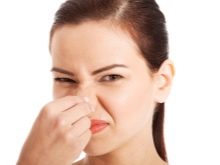
Many are interested in the question of whether it is possible to apply varnish over drying oil or not. Both types of materials form a film. When the varnish applied to the fresh drying oil dries, air bubbles form. Dyes NTs-132 and some other paints are compatible with such impregnation. It is unacceptable to apply the coating at subzero temperatures, moreover, oxol is applied at temperatures of at least +10 degrees.
Tile adhesive (waterproof) is made from 0.1 kg of wood glue and 35 g of drying oil. Linseed oil is added to the melted glue and mixed thoroughly. With subsequent use, the ready-made mixture must be heated, it is useful not only for tiles, but also for joining wooden surfaces.
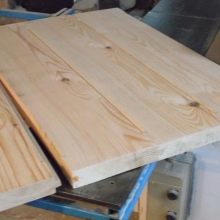
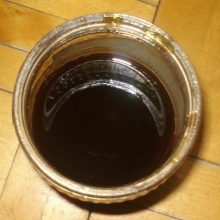
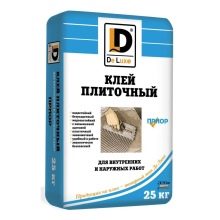
How to do it yourself?
In the absence of factory products, quite high-quality drying oil is often made at home from sunflower oil. To get a product based on linseed oil, you will need to slowly heat it up, achieving evaporation of water, but not warming it above 160 degrees. The cooking time is 4 hours; it is undesirable to cook a large amount of oil at the same time. By half-filling the vessel, you can provide increased protection against fire and provide significant performance.
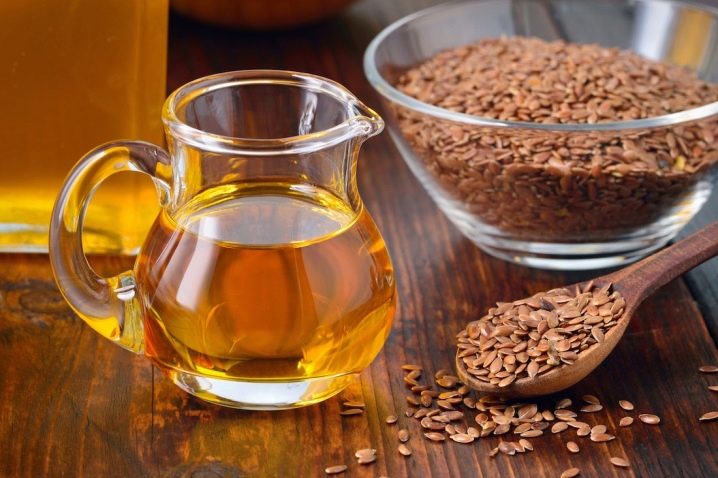
When foam appears, you can introduce a desiccant in small portions - only 0.03 - 0.04 kg per 1 liter of oil. The subsequent cooking time at 200 degrees reaches 180 minutes. The readiness of the solution is assessed by the complete transparency of a drop of the mixture placed on a clean thin glass. You need to cool the drying oil slowly at room temperature. A siccative is also sometimes obtained by hand: 20 parts of rosin are combined with 1 part of manganese peroxide, and the rosin is first heated to 150 degrees.
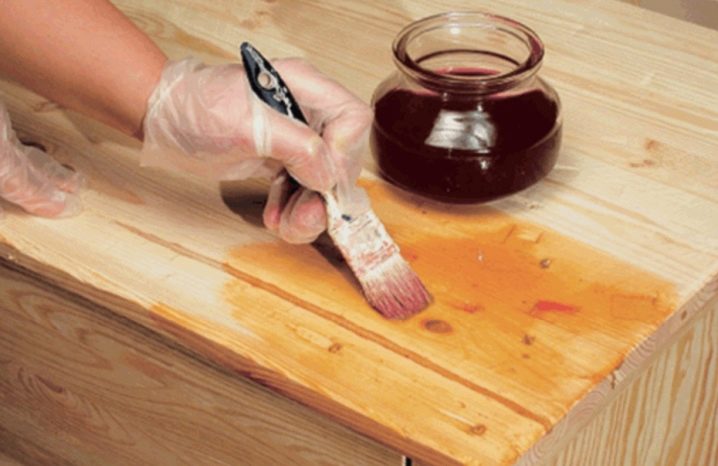
For information on how to properly apply drying oil, see the next video.
The comment was sent successfully.