Features of metal chimneys
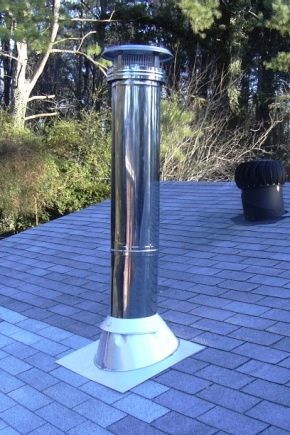
The choice of a chimney must be approached with all responsibility, because the functioning and safety of the entire heating system depend on the quality of this structure. Far from the last importance in this matter is the material from which the pipes are made. This can be brick, ceramic, asbestos cement, metal, volcanic pumice, or vermiculite. But since the most common type of chimneys is metal products, this article will focus on them.
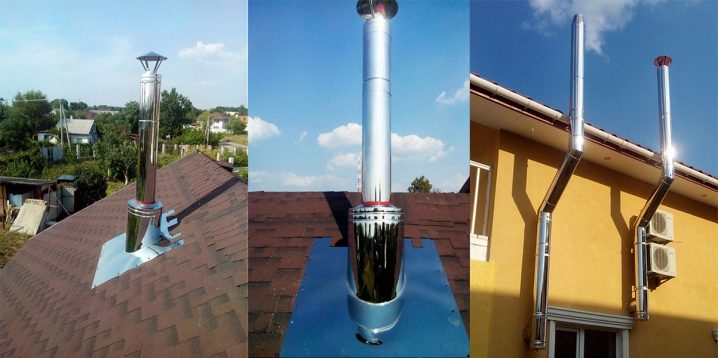
Advantages and disadvantages
A number of factors are attributed to the advantages of metal chimneys.
-
Low weight in comparison with other materials allows not to erect the foundation during installation.
-
All parts can be easily combined with each other as a constructor and do not require special engineering skills for assembly. Even a beginner can handle the installation of a metal chimney.
-
Durability and corrosion resistance thanks to high grade stainless steel.
-
Soot does not adhere to the smooth metal walls of such chimneys, which increases fire safety and relieves owners of the need to frequently clean the pipes.
-
The versatility of the design allows you to choose the optimal smoke exhaust system for any heating devices.
-
Possibility of installation both inside the building and outside.
-
Absolute tightness.
-
Relatively low price.
-
Aesthetically attractive and neat appearance.
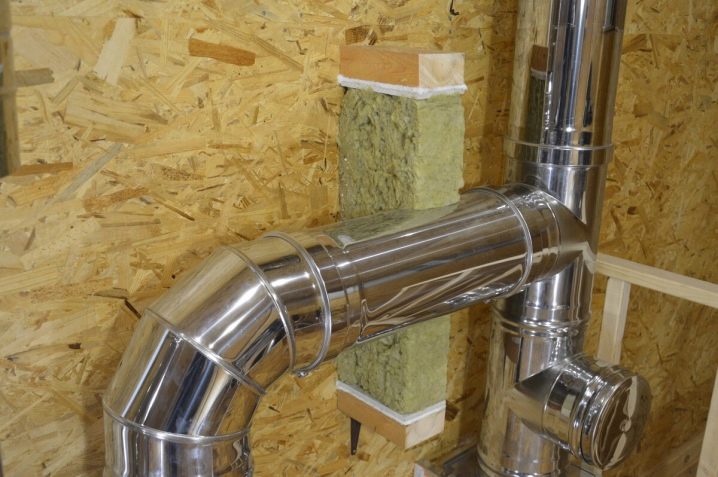
Of the disadvantages of such chimneys, only two can be noted.
-
The need to install a supporting structure if the pipe is very long.
-
Metal structures do not always fit into the architecture of a building in terms of design.
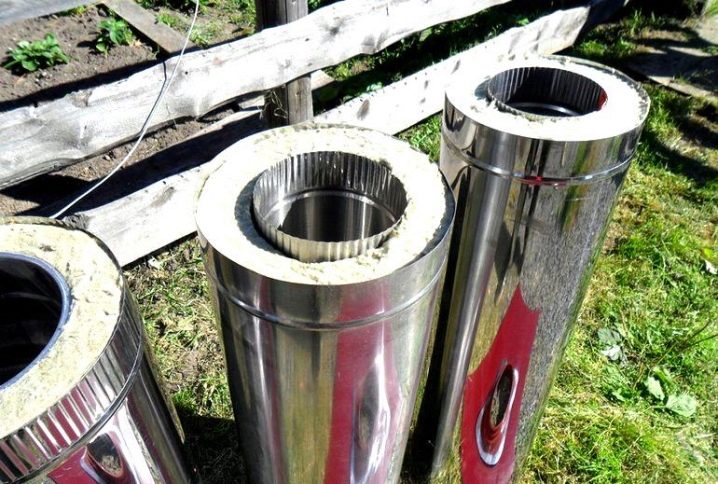
Varieties
Steel chimneys are available in single and double layers. The latter are also called "sandwiches". They consist of two metal pipes inserted one into the other, and a thermal insulation layer of stone wool between them. This option is the most fireproof, which means it is ideal for wooden buildings. "Sandwiches" are the most versatile version of chimneys that can be combined with absolutely all types of heating systems. The type of fuel does not matter either.
Condensation does not form on such pipes, which guarantees the correct operation of the chimney even with sudden temperature changes, and prolongs the service life.
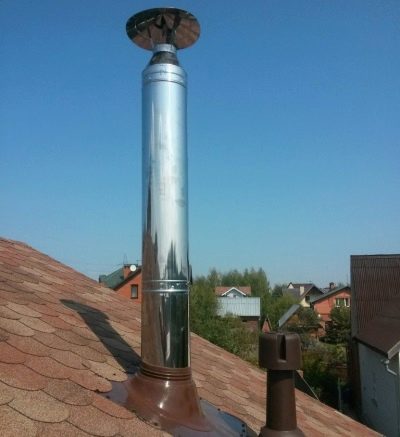
Single-layer ones are usually used in tandem with a water heating system and when installing gas ovens indoors. Installation of single-wall pipes outside the building requires additional thermal insulation. The main advantage of such pipes is their low price. Therefore, it is advisable to use them for country houses and baths.
And there are also coaxial chimneys. Like sandwiches, they consist of two pipes, but unlike them, they do not have thermal insulation. Such designs are used for gas-fired heaters.
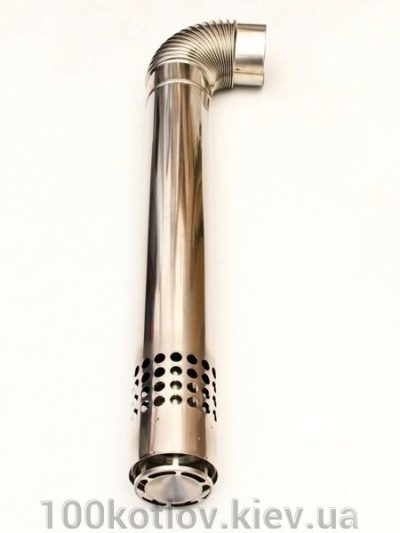
By the type of location, chimneys are divided into internal and external.
Internal
Indoor structures are located directly in the room, and only the chimney goes out. They are used for stoves, fireplaces, saunas and home mini-boiler rooms.
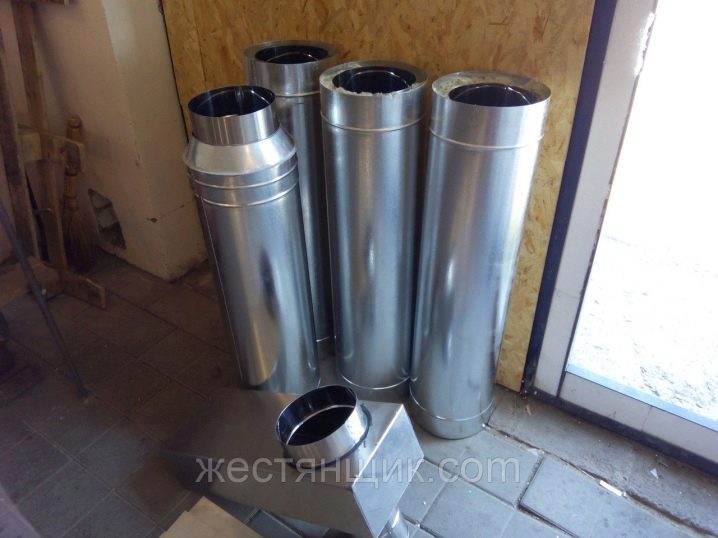
Outdoor
External chimneys are located outside the building. Such structures are easier to install than internal ones, but they require additional insulation to protect against temperature extremes. Most often these are coaxial chimneys.
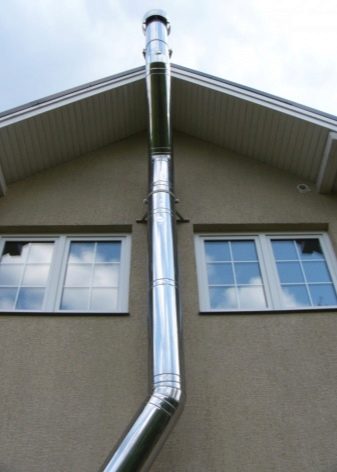
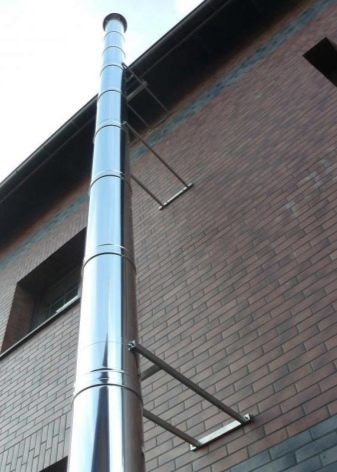
Manufacturing materials
In the vast majority of cases, metal chimneys are made of ferritic stainless steel. The choice of this material is due to the high operational requirements for chimneys, because as they are used, the pipes are exposed to high temperatures, aggressive constituents of condensate and a sticky deposit of soot, which corrodes the pipes from the inside. Therefore, the flue gas system must be made of the most corrosion-resistant material.
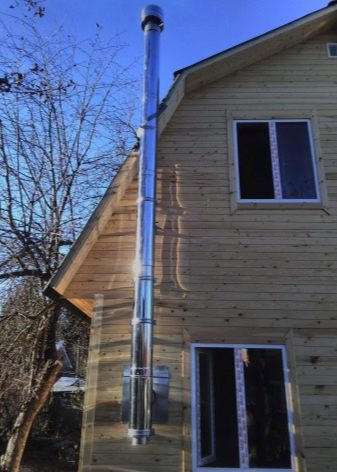
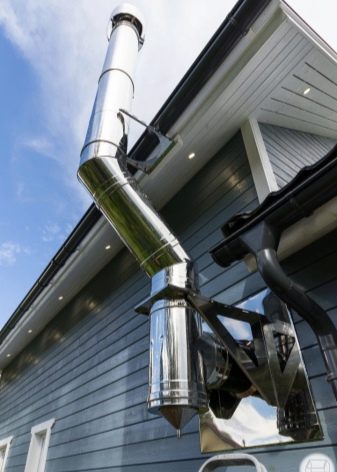
There are many different grades of steel available today. But only some of them are suitable for the production of chimneys.
-
AISI 430. It is used for the manufacture of only the outer parts of the chimney, which are not exposed to chemical attack.
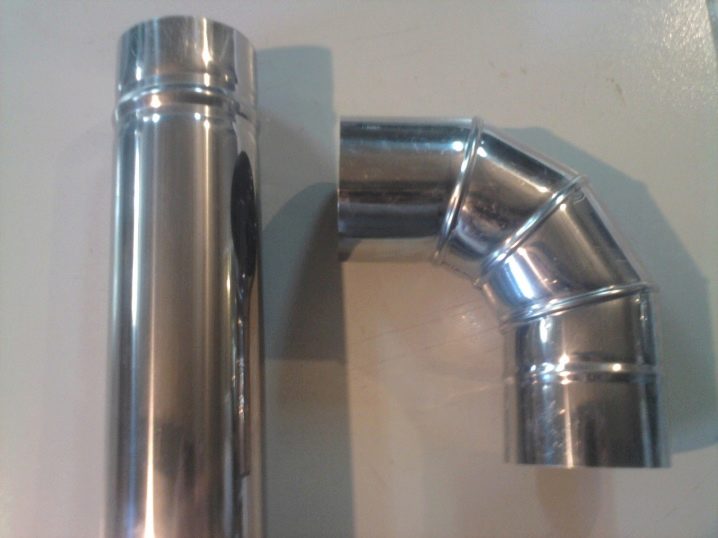
- AISI 409. This brand is actively used in the production of internal chimney pipes due to the content of titanium in the alloy, which increases the strength. But since this steel has a low resistance to acids, it cannot be used for heating devices operating on liquid fuel.
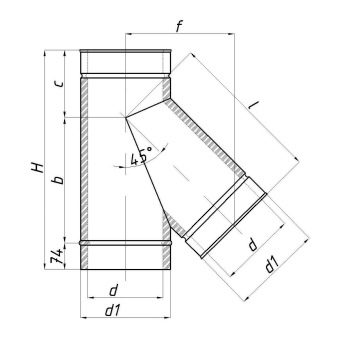
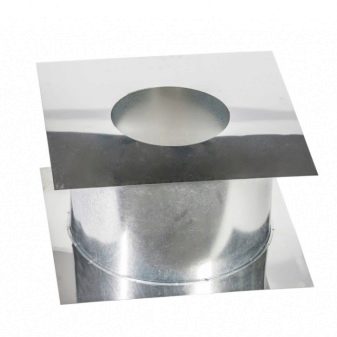
- AISI 316 and AISI 316l. High acid resistance allows these grades to be used for furnaces operating on liquid fuels.
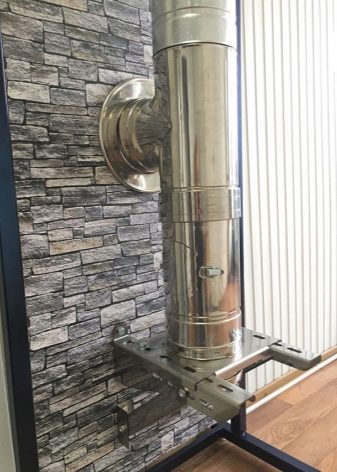
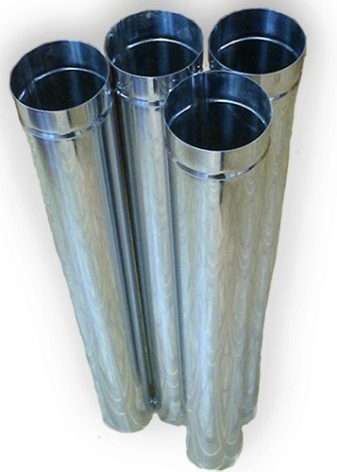
- AISI 304. The grade is similar to AISI 316 and AISI 316l, but is cheaper due to the lower content of molybdenum and nickel.
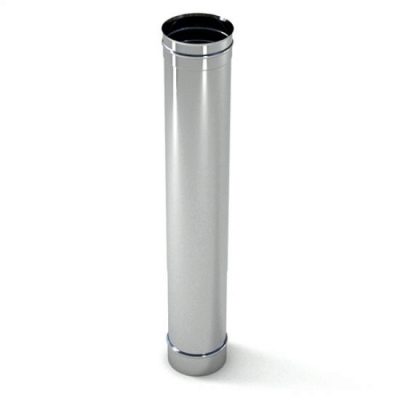
- AISI 321 and AISI 316ti. Universal grades that are used in most chimney designs. They are extremely resistant to mechanical damage and can withstand temperatures up to 850 degrees.
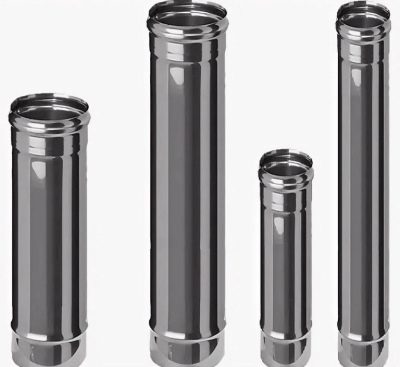
- AISI 310s. The strongest and most durable steel grade that can withstand temperatures over 1000 degrees. Usually used for the manufacture of chimneys in industrial plants.
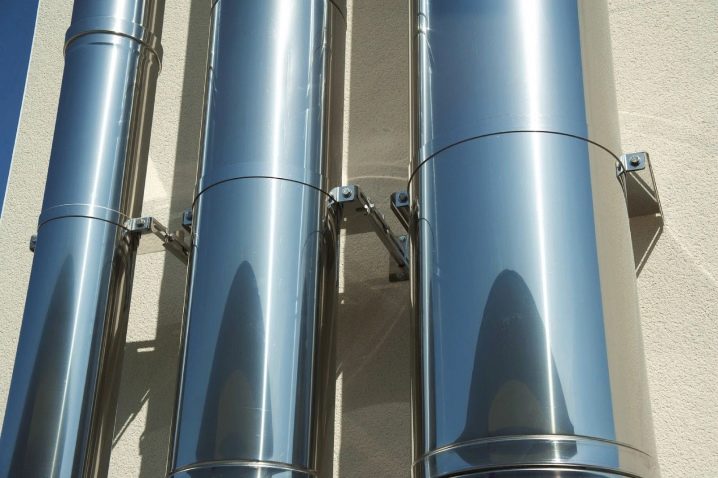
When choosing chimneys made of steel, you should be extremely careful. Some manufacturers sell galvanized steel products. Such pipes are much cheaper than from other types of steel, but they can only be used with gas appliances, because when heated above 350 degrees, zinc begins to release harmful substances.
In addition, parts made of galvanized iron pipes are often found defective, so you need to carefully check the goods before buying.
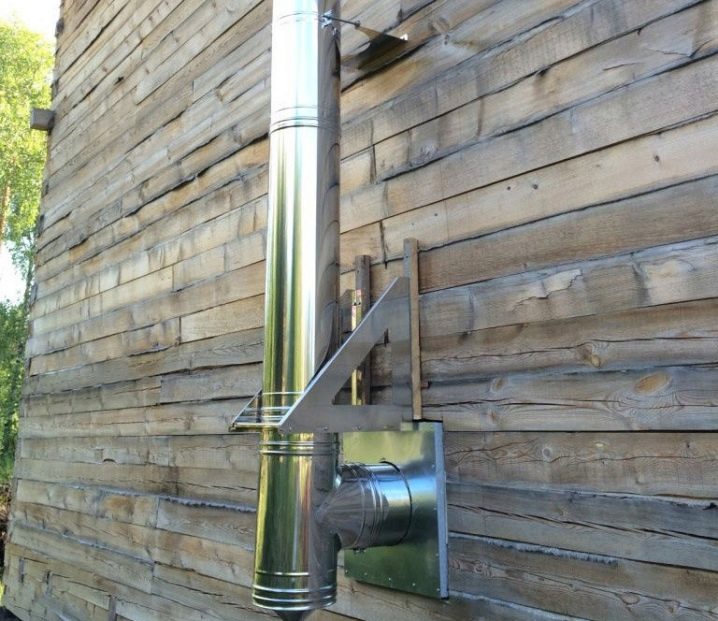
In the construction of country houses, baths and utility rooms, chimneys made of ferrous metal - a cheap iron-carbon alloy of steel - are popular. The characteristics of black steel are significantly lower in comparison with ordinary stainless steel, but for occasional use this is the best option on the price-quality scale. It is best to choose thick walled pipes made of low alloy steel, as they are more resistant to corrosion. For baths, it is advisable to build a chimney of boiler steel, which can withstand short-term heating at 1100 ° C and is designed specifically for joint operation with steam and water installations.

Section and height calculation
Before buying and installing a chimney, you need to make calculations. In the conditions of private construction, this can be done independently.
When calculating the height, it must be borne in mind that the minimum length of the entire chimney structure must be at least 5 meters, and when it comes to the roof, the pipe must rise about 50 cm above the roof. Optimum height: 6-7 meters. With a shorter or longer length, the draft in the chimney will not be strong enough.
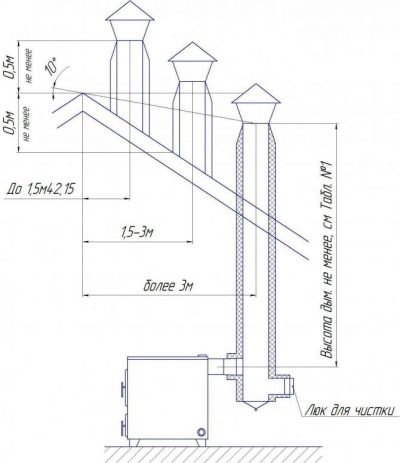
To calculate the cross-section of a pipe, a number of parameters must be taken into account.
-
The amount of fuel burned in one hour.
-
Gas temperature at the inlet to the chimney.
-
The gas flow rate through the pipe is usually 2 m / s.
-
Overall height of the structure.
-
The difference in gas pressure at the inlet and outlet. This is usually 4 Pa per meter.
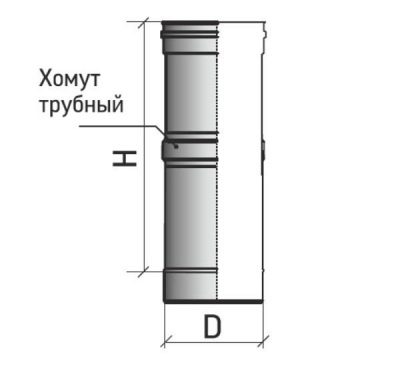
Further, the section diameter is calculated by the formula: d² = 4 * F / π.
If the exact power of the heater is known, experts give such recommendations.
-
For heating devices with a power of 3.5 kW, the optimal size of the chimney section is 0.14x0.14 m.
-
Chimneys 0.14 x 0.2 m are suitable for appliances with a power of 4-5 kW.
-
For indicators of 5-7 kW, pipes of 0.14x0.27 m are used.
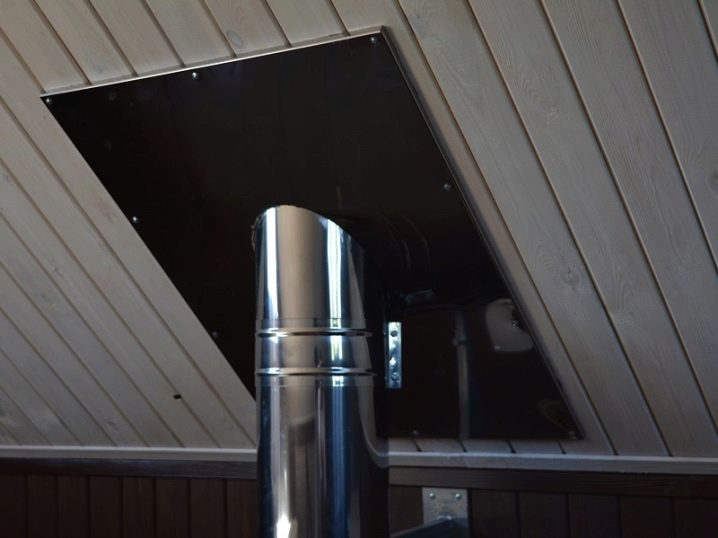
Installation nuances
Before assembling the chimney, you must make sure that there is technical documentation for the facility. It contains SNiP standards and a detailed assembly diagram.
Installation of the structure is carried out strictly vertically - only in this position is sufficient traction provided.
If for some reason this is not possible, then a small angle of up to 30 degrees is allowed.
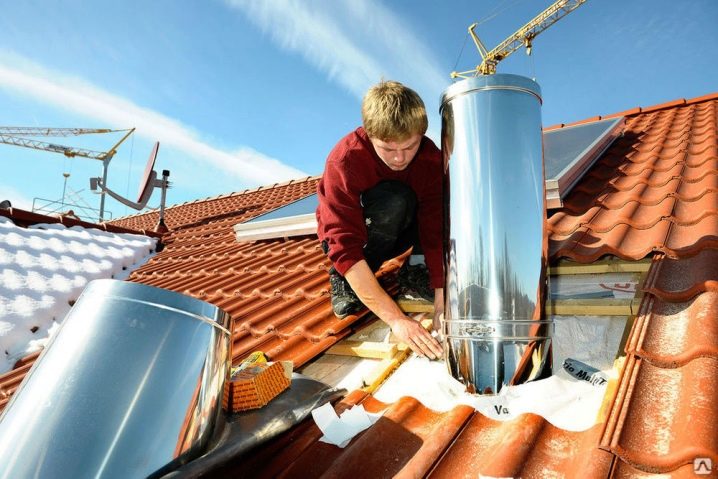
The distance between the pipe and the ceilings must be at least 40 cm.
A double-walled chimney should be straight, but two angles of 45 degrees are allowed. It can be installed both inside and outside the room, while single-walled ones are located only inside.
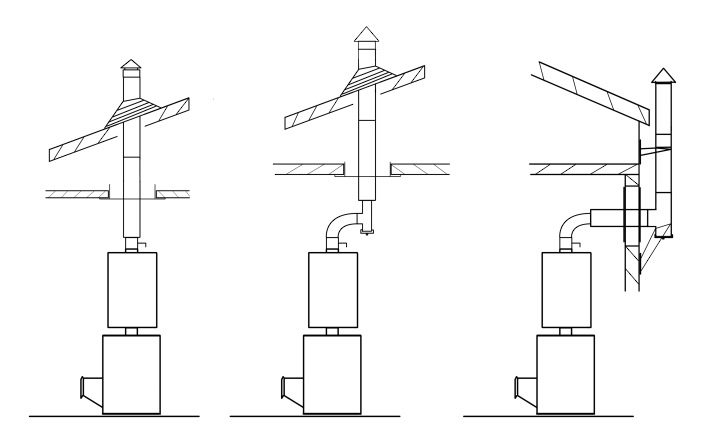
The assembly starts from the heater. First, install the adapter and pipe section to the main riser. The console and mounting platform will serve as a support. A plug is fixed at the bottom of the platform, and a tee with a revision door at the top. It is designed to clean the chimney and check its condition.
Next, the entire structure is assembled to the head. All seams are carefully coated with sealant. After it dries, check the level of traction and the quality of the joints.
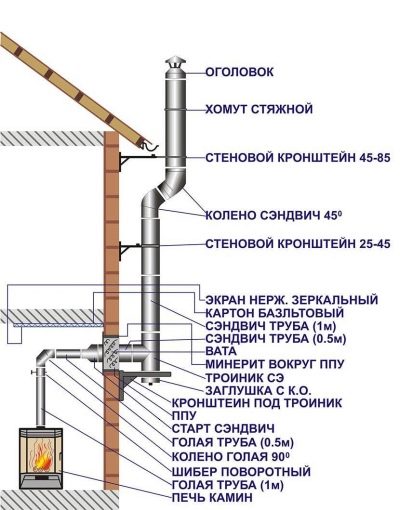
The chimney outlet can be designed through the roof or through the wall. The first option is simpler and more traditional. This design is stable, the flue gases are not overcooled and, as a result, condensation does not form, which leads to corrosion. However, there is a risk of a latent fire on the ceiling slabs. In this regard, the output through the wall is safer, but requires skill in the installation.
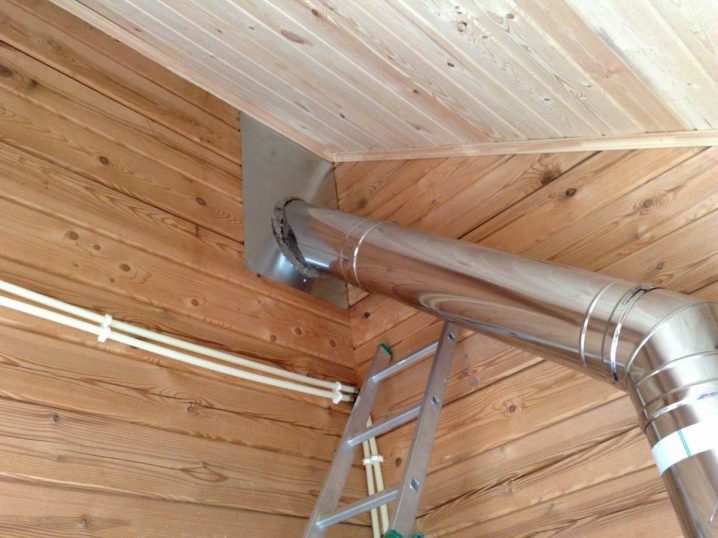
Care Tips
To prolong the life of the chimney, it is necessary to maintain it correctly and regularly. Here are some tips.
It is best to heat the stove with coal and wood with a low resin content - birch, aspen, fir, ash, acacia, oak, linden.
Household waste, plastic and raw firewood must not be burned in the house stove, as this leads to additional pollution of the chimney.
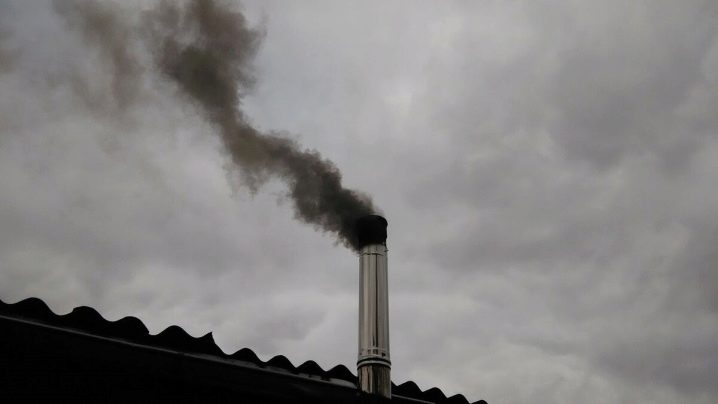
The soot adhering to the walls of the pipes gradually narrows them and reduces draft, which leads to the ingress of smoke into the room. In addition, soot can ignite and cause a fire. Therefore, twice a year, it is necessary to carry out a general cleaning of the chimney, and check all its components.
Chimneys are cleaned with a special metal brush, the diameter of which should be slightly larger than the diameter of the pipe. Currently, there are whole rotary tools for use based on a drill.
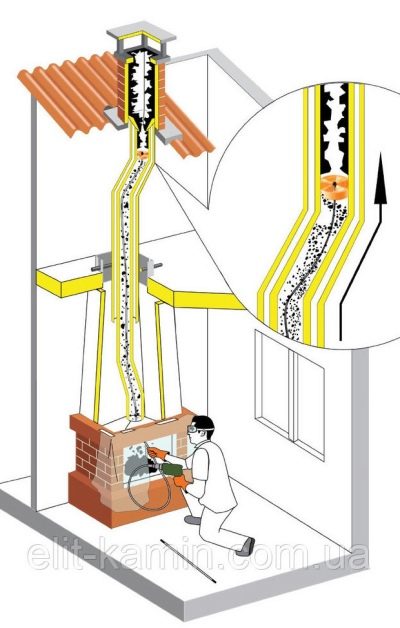
Mechanical cleaning is carried out exclusively in calm weather, so as not to accidentally fall off the roof. The oven door must be tightly closed so that dirt does not fly into the house, and in the case of a fireplace, hang it with a wet cloth.
For insignificant contamination, dry cleaning is carried out. These are either powders or an artificial chimney sweep log, which are put directly into the fire. When burned, the products release substances that soften the soot. It is recommended to arrange such preventive cleaning every two weeks.
And also to prevent the formation of a thick layer of soot, you can pour rock salt or potato peel inside the operating oven.
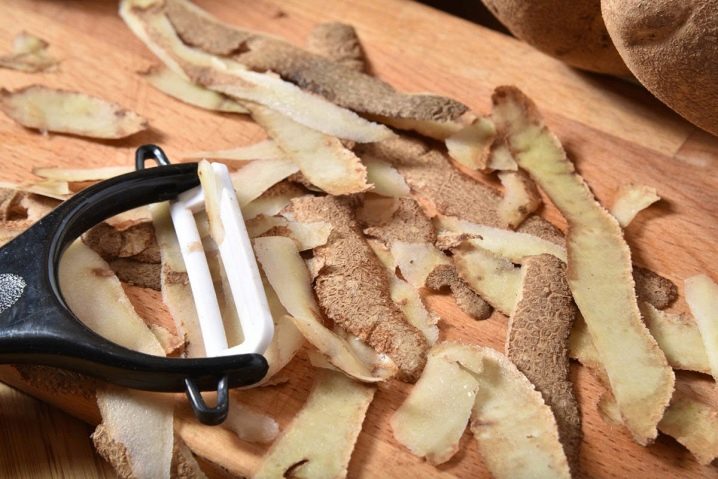
The comment was sent successfully.