Everything you need to know about wide-flange I-beams
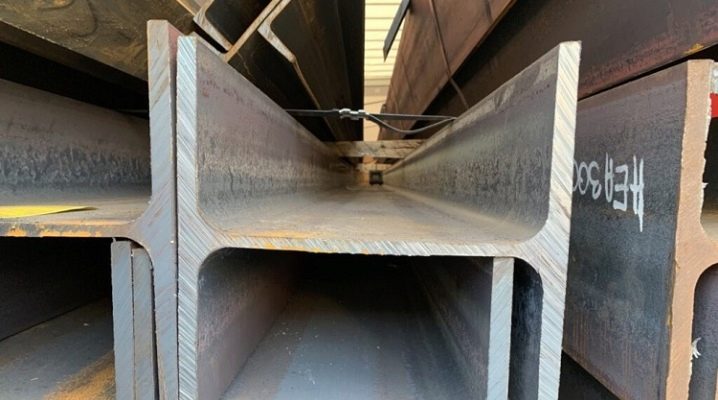
A wide-flange I-beam is an element with special characteristics. Its main feature is mainly bending work. Thanks to the extended shelves, it can withstand more significant loads than a conventional I-beam.
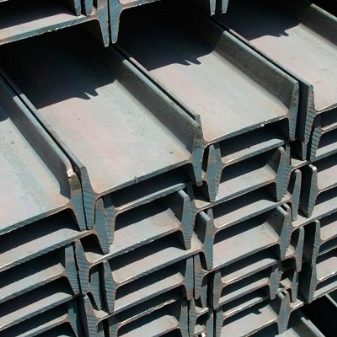
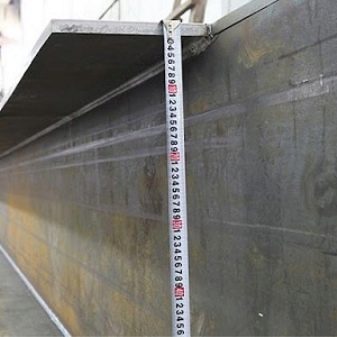
general description
Wide flange I-beams (I-beams) have an optimal ratio of flanges to the main wall, while the total length of the flange edges on either side is equal to the height of the main lintel. This allows the wide-flared I-beam to withstand significant loads from above, acting on one of the shelf sides.
Thanks to this, it becomes possible to use this element in construction when arranging interfloor ceilings in low-rise buildings. With the entry to the construction market of fast-building construction methods, the wide-brimmed I-beam has gained additional demand.
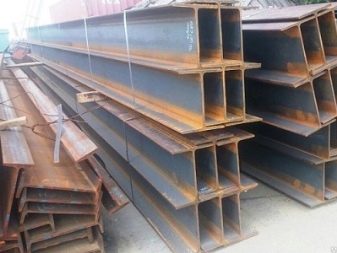
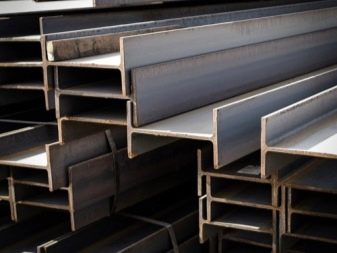
Features of production
The scheme for manufacturing an I-beam with wide flanges is not much different from a similar technology for the production of a simple I-beam or channel... The difference is manifested in the use of shafts and shapes that make it possible to repeat the section (profile) of an I-beam with wide flanges. For the production of SHPDT, steel grades St3Sp, St3GSp, 09G2S are used or a similar composition with good machinability and with suitable fatigue, impact-tough values of the corresponding parameters. The disadvantage of these grades of steels is their tendency to form rust in conditions of any noticeable humidity, which is why the elements after installation need to be primed and painted.
By special order, galvanized I-beams are produced - however, zinc is not very suitable for extreme temperatures, it gradually loses its properties, as a result, steel is exposed and rusts. A galvanized I-beam is not afraid of water, however, it is easily corroded by even the weakest acid-salt vapors, consisting of small splashes, as a result, the structure will sooner or later rust. First, a workpiece is smelted from the finished steel with certain parameters, which then, having passed the stage of hot rolling, is formed exactly into those elements that the builder is used to seeing them.
Hot rolled products do not have additional grinding: ideal smoothness, on the contrary, will prevent, for example, concrete from adhering to the I-beam surface.
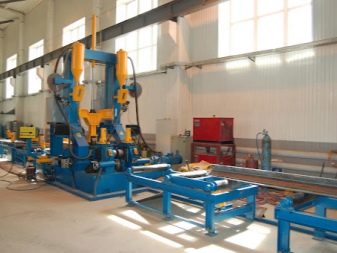
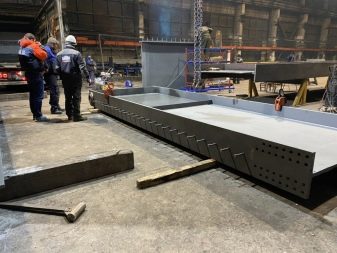
Dimensions and weight
To find out the weight of an I-beam, do the following.
- Using the thickness and width of the shelves and the main lintel, calculate their cross-sectional areas. The length in the section is multiplied by the width - more precisely, the width of the flange or the height of the wall by the corresponding value of the thickness.
- The resulting areas are added.
- The sum of these areas is the cross-sectional area of the product. It is multiplied by 1 m of the length of the workpiece (running meter).
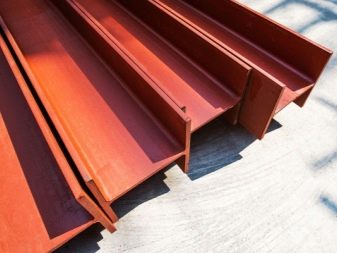
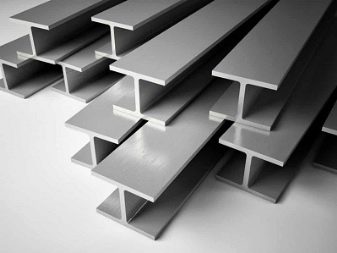
Having received the actual volume of steel that went into the manufacture of this meter, multiply it by the value of the density of the steels used in the manufacture of elements.
Denomination |
Total height of the element placed on one of the shelf sides |
Width of both shelves on one side |
Lintel wall thickness |
The radius of curvature of the wall to the shelves from the inside at the junction |
20SH1 | 193 | 150 | 6 | 9 |
23SH1 | 226 | 155 | 6,5 | 10 |
26SH1 | 251 | 180 | 7 | 10 |
26SH2 | 255 | 180 | 7,5 | 12 |
30SH1 | 291 | 200 | 8 | 11 |
30SH2 | 295 | 200 | 8,5 | 13 |
30SH3 | 299 | 200 | 9 | 15 |
35O1 | 338 | 250 | 9,5 | 12,5 |
35SH2 | 341 | 250 | 10 | 14 |
35SH3 | 345 | 250 | 10,5 | 16 |
40SH1 | 388 | 300 | 9,5 | 14 |
40SH2 | 392 | 300 | 11,5 | 16 |
40SH3 | 396 | 300 | 12,5 | 18 |
The density of steel for an I-beam is 7.85 t / m3. As a result, the weight of a running meter is calculated. So, for 20SH1 it is 30.6 kg.
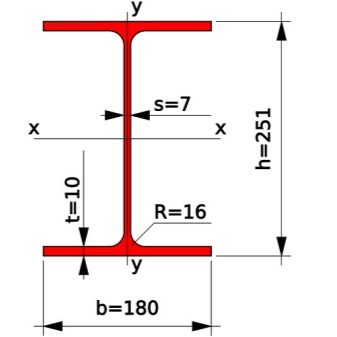
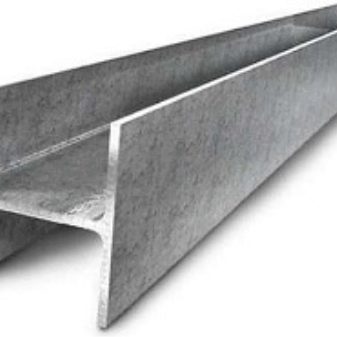
Marking
Marker "ШД" stands for accordingly - it means that in front of you is a wide-flange I-beam element. The number indicated in the assortment after the abbreviation "ШД" emphasizes that the width of the main wall in centimeters corresponds to the assigned value. So, ШД-20 indicates an I-beam with a 20-centimeter jumper.
However, a simplified marking, for example, 20SH1, means that a 20-cm wide-shelf element has the first ordinal value in the size table. Markings at 20 and 30 cm of the main height are the most demanded of the denominations of wide-flange I-beams. They are made with parallel flange edges, and W denotes wide flanges (literally). According to GOST 27772-2015, the product is also marked with a marker "GK" - "hot rolled". Sometimes there is a steel grade - for example, "St3Sp" - calm steel-3.
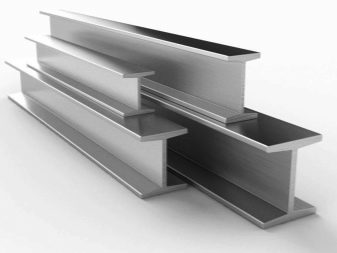
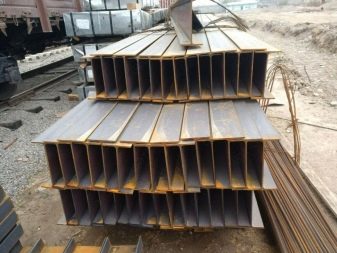
Applications
A wide-shelf I-beam is used for the arrangement of buildings due to the construction of a frame base and a structure of any complexity. The main application of SHPDT is the construction of load-bearing structures, in which this I-beam is used as elements of the rafter-roofing system, including additional supports and lathing. The most popular are the following designs:
- staircase-interfloor floors;
- metal beams that act as rafters;
- outrigger beams of balcony compartments;
- additional fixation of the pile foundation for the frame;
- frame-frame structures for blocks of temporary residence;
- frames for machine tools and conveyors.
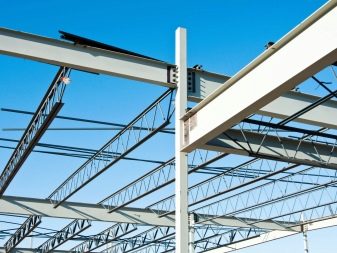
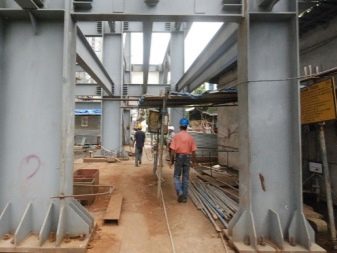
Although reinforced concrete, in comparison with this type of structure, is a more capital solution - it can stand for a hundred years before the construction is recognized as emergency, - frame-beam structures significantly reduce the period of a particular construction project, allowing you to save a certain amount of money. Using a wide-brimmed I-beam, the craftsmen are confident in the reliability and durability of the building: it will stand for its decades without losing its original properties.
Also, an I-beam with wide flanges is in demand in the carriage and automotive industries. It has proven itself no worse than a conventional I-beam or channel element.
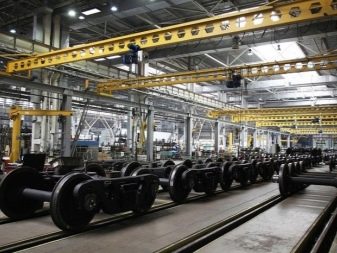
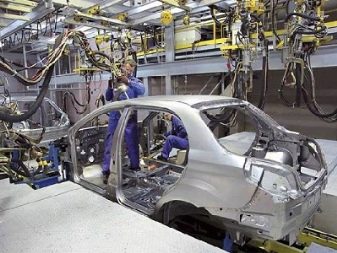
Connection methods
Docking methods include welding using nuts or bolts. Both of these methods are equally possible due to the good processing of the St3 alloy (or similar) by thermal and mechanical methods. This alloy is well welded, drilled, turned and sawn. This allows you to combine both joint options according to the project. Before welding, abutting edges and edges are cleaned to one hundred percent steel gloss. Annealing of parts before welding is not required.
If a welded structure is not needed, then a bolted connection is mainly used, for example, for a truss with chords. The advantages of bolted joints are that they do not need to be cleaned, and the threat of lack of penetration of the seam with not quite skillful (at first) use of manual arc welding is eliminated. The fact is that with poor-quality boiling, the seams can break off, and the structure will sag.
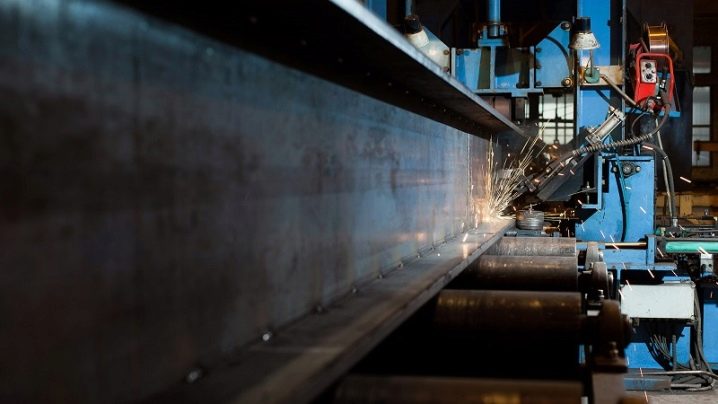
The comment was sent successfully.