Insulation of a wooden house inside: how and how is it better to do it?
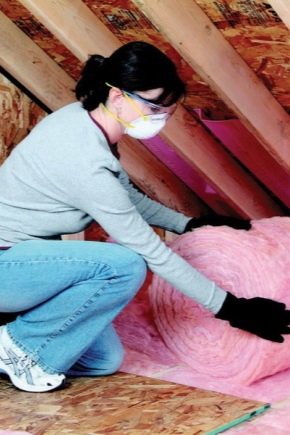
The wooden house can rightfully be considered the pride of the owners. Wood retains heat well and provides a favorable microclimate in the room, has an attractive design. However, in a number of cases, the heat-insulating properties of the material are not enough, therefore, the way out of the situation is to insulate the house.
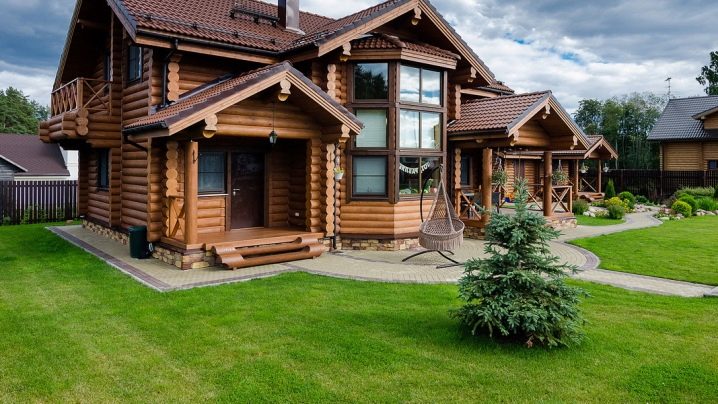
Features of the procedure
The most widespread is the external insulation of the house. However, if it is impossible to fulfill it, you have to resort to thermal insulation of the house, bath or summer cottage from the inside. It should be noted right away that as a result of these manipulations, the useful area of the room in most cases decreases. An exception is made only for a log cabin, which requires only warming between wedges.
With internal thermal insulation of a house made of any material, the humidity in the room always increases. It is clear that this negatively affects the walls, especially wooden ones. If the insulation is incorrect, already in the first year of operation, the insulation will get wet and lose its thermal insulation properties, and the wooden surfaces will begin to rot and become covered with mold.
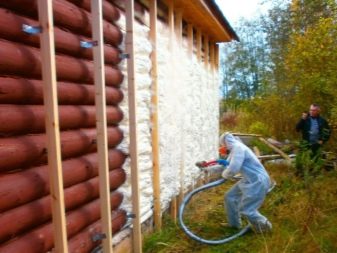
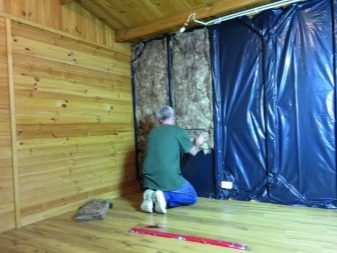
Avoiding such phenomena allows the mandatory installation of a vapor-permeable film and the creation of a powerful ventilation system.
When insulating a wooden house from the inside, it should be remembered that in terms of its effectiveness, it cannot be compared with thermal insulation from the outside. This is due to the fact that the wall insulated from the inside does not accumulate heat, therefore the heat loss is 8-15%. Moreover, cut off from a warm room by heat-insulating material, such a surface freezes faster.
Another important point is a comprehensive approach to isolation. Not only the walls will have to be insulated, but also the floor and ceiling. If the house has an unheated attic and basement, then it is more rational to give primary and main attention to these zones when insulating.
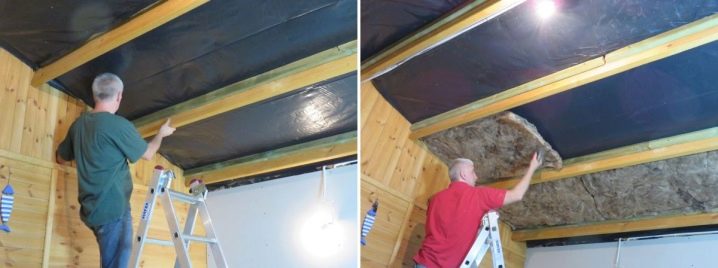
Colossal, up to 40%, losses of heat energy fall on windows and doors. It is important not only to use modern double-glazed windows and door leaves, but also to make sure of their correct and sealed installation, to take care of the insulation and protection of the slopes.
A common mistake when insulating a wooden house from the inside is to keep small gaps between surfaces., usually between floors and walls, walls and partitions, walls and ceilings. Such gaps are called "cold bridges" because heat escapes through them and cold air penetrates.
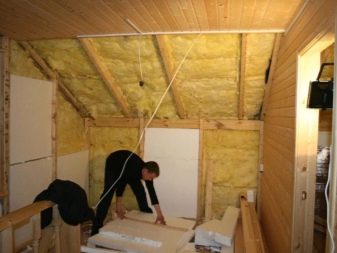
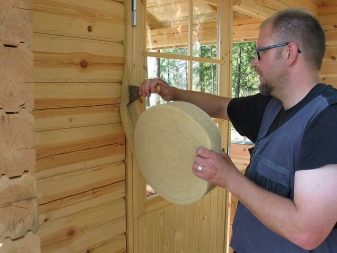
Characteristics of thermal insulation materials
For any heat-insulating material, the most important characteristic is the indicator of thermal conductivity. The lower it is, the less heat loss the house carries. It is measured in W / m × ° С, which means the amount of heat energy leaving through the insulation per m2.
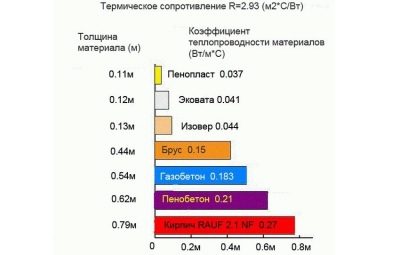
When choosing a heat-insulating material for wooden surfaces, one should pay attention to the vapor permeability indicators. The fact is that wood is itself a "breathing" material. It is able to pick up excess moisture from the air in the room, and in case of insufficient humidity, to give it away.
It is easy to imagine that when using a non-vapor-permeable insulation, moisture from the wood will not find a way out and will remain between the insulating material and the wood.This will turn out to be detrimental to both surfaces - a wet insulation has a high thermal conductivity, and the tree begins to rot.
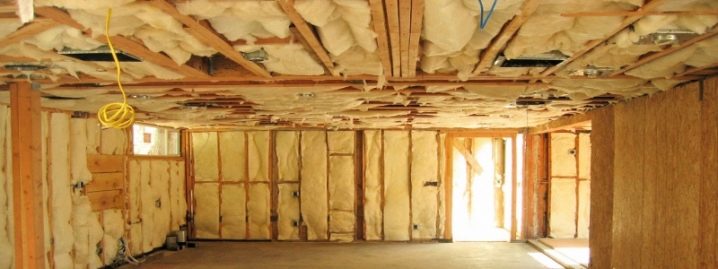
Another important criterion for a heat insulator is moisture resistance. It is usually achieved by applying water repellents to the insulation and using a waterproofing film.
If we talk about the mezhventsovy insulation, then it is impossible to close it with a waterproofing film, therefore the water resistance of the material, along with its thermal efficiency, comes to the fore when choosing a specific product. For indoor use, an environmentally friendly material should be chosen. It is important that it belongs to the class of non-flammable or does not support combustion, and also does not emit toxins when heated.
The biostability of a product directly affects its durability. If the insulation attracts insects or rodents, then in the process of their vital activity cracks and damages invariably appear in it, which causes the appearance of "cold bridges".
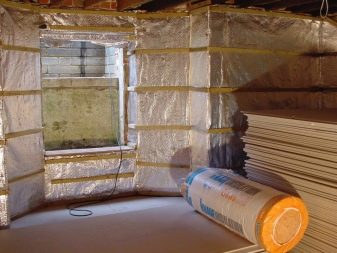
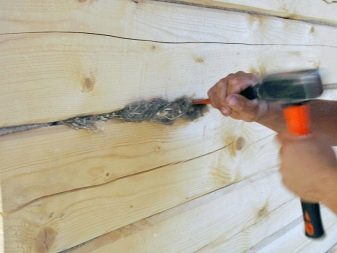
Among other paramount characteristics - ease of installation, variety of execution forms and options for density, thickness, affordability.
What is better to insulate?
The most common option for insulating a wooden house is mineral wool insulation. Usually, glass wool or stone wool is used to organize the thermal insulation layer. The latter is superior to glass wool in terms of technical characteristics, but most importantly, it is absolutely environmentally friendly.
Glass wool emits toxic compounds during operation, therefore it is not recommended for indoor use. In addition, it has the worst indicators of moisture resistance and fire resistance (although it has high fire-fighting characteristics - the combustion temperature is 400-500 degrees). Finally, it is prone to shrinkage and a decrease in thickness (and this leads to an increase in thermal conductivity), when laying it requires the use of not only a respirator (like all mineral wool insulation), but also workwear.

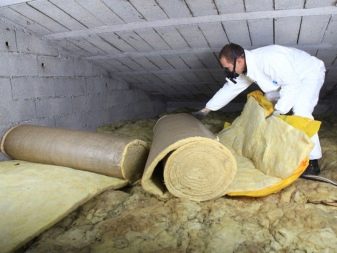
In this regard, the use of stone or basalt wool is more attractive. The basis of the material is processed rock, which is subjected to high-temperature heating (over 1300 degrees). Then, thin fibers are isolated from the semi-liquid mass. In a chaotic manner, they are formed into layers, after which they are pressed and exposed to high temperatures for a short time.
The result is a material of different hardness, produced in mats, rolls and tiles. Mats are the most durable, suitable for heavily loaded structures, including floor insulation under the screed.
For wooden walls, in most cases, tiled basalt wool is sufficient, it is also placed between the logs of the wooden floor. Roll products are useful for insulating flat horizontal surfaces, such as a ceiling.
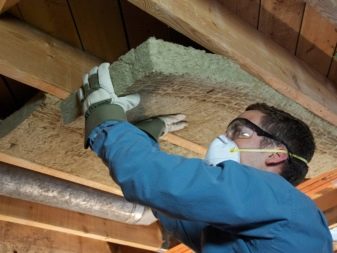
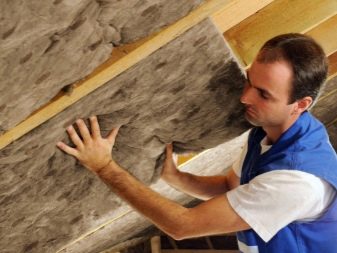
Thermal insulation properties are provided by the arrangement of fibers, between which air bubbles accumulate in large volumes - the best heat insulator. The coefficient of thermal conductivity of the material, depending on the density and grade, is 0.35-0.4 W / m × ° C.
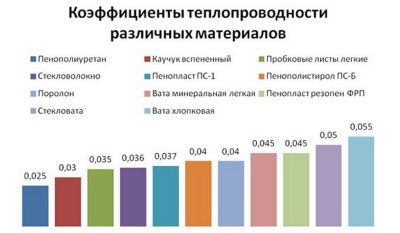
In addition to high thermal insulation, the material demonstrates good sound absorption performance. The sound insulation coefficient of impact noise reaches 38 dB, air - from 40 to 60 dB.
Unlike glass wool, basalt wool is characterized by low moisture absorption, which is 1% on average. In combination with a high vapor permeability - 0.03 mg / (m × h × Pa), this allows you to protect the wood from decay and maintain a healthy atmosphere in the house. The melting point of stone wool is about 1000 degrees, so it is considered a non-combustible material. In addition, thanks to the naturalness of the composition, it is possible to achieve the environmental safety of basalt insulation.
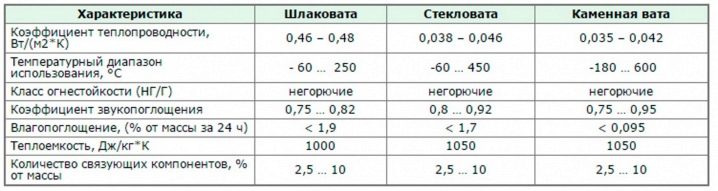
Ecowool is also suitable for wall insulation.80% of the material is cellulose chips treated with fire retardants and antiseptics, the rest is polymer resins and modifiers.
Ecowool belongs to bulk materials, but it is also possible to spray it onto the surface using special equipment. Despite the treatment with water repellents, the material requires a waterproofing layer. In terms of its thermal efficiency, it is inferior to stone wool.
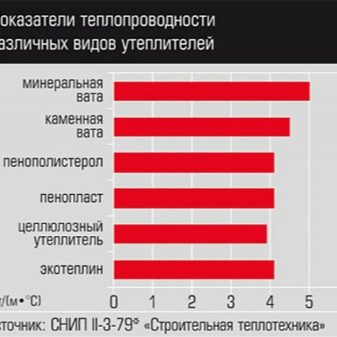
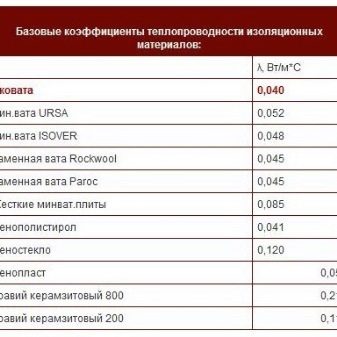
Modern insulation material - penofol, also suitable for internal insulation. It is a roll of foamed polyethylene (provides thermal insulation effect) with a foil layer applied on one side (reflects heat energy into the room). The presence of a metallized layer increases the strength and moisture resistance of the material, but makes it combustible (class G1).
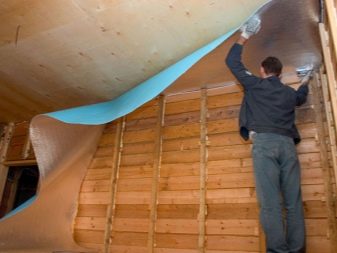
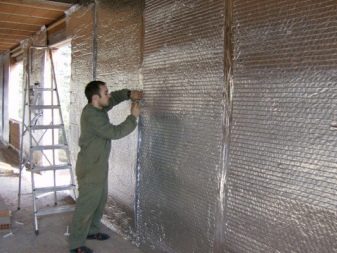
The well-known expanded polystyrene, which has similar thermal conductivity, is not recommended for use inside a wooden house. The point is that the material "does not breathe". The tree, as you know, is characterized by the ability to take excess moisture from the room and give it away if necessary. In the presence of a polystyrene foam layer, the tree simply cannot get rid of excess moisture, which will lead to the onset of rotting. In addition, polystyrene is toxic and flammable, and often becomes a home for rodents.
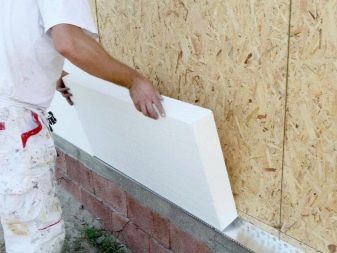
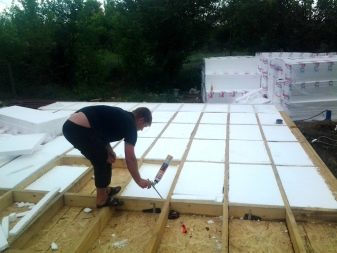
If, nevertheless, it is impossible to refuse its use, preference should be given not to polystyrene, but to extruded polystyrene foam. It is more environmentally friendly and has a higher fire safety.
Another durable and heat-efficient material is polyurethane foam (PPU), at first glance, is the optimal insulation. The low coefficient of thermal conductivity, as well as the features of application (it is sprayed onto the surface) allow not only to reduce heat loss, but also eliminate the risk of "cold bridges". However, polyurethane foam does not "breathe" and, if, in the case of using expanded polystyrene, it is possible to organize a vapor barrier between a wooden surface and a heater, then when installing PPU, it is impossible to create this layer. After 5-7 years, the walls under the polyurethane foam layer will begin to rot, and removing it is a rather laborious process.
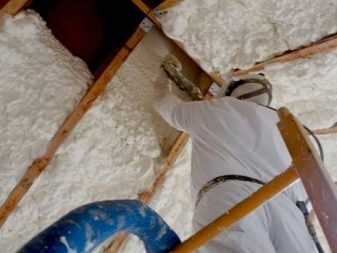
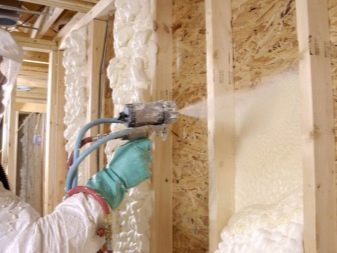
For mezhventsovy insulation, special materials are used. They can be of natural or synthetic origin.
The following types of materials are referred to organic inter-crown insulation, which are most often used for internal thermal insulation:
Linen insulation
For a long time, coarse, unsuitable for weaving linen fibers were used for these purposes. Today, tape insulation is also made on a plant basis and is called linen felt or linen batting. Differs in high density, vapor permeability (optimal for rooms with high humidity).
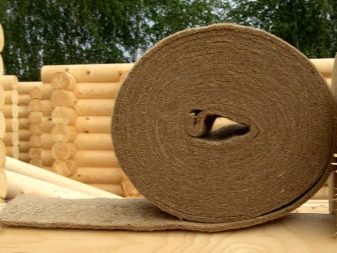
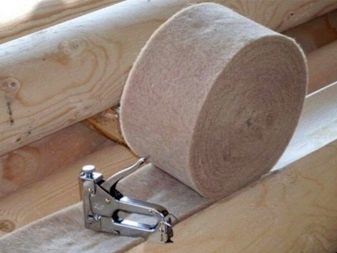
Jute
The insulation is based on recycled fibers of the bark of an exotic tree of the linden family of the same name. It is characterized by a high content of resins in the composition, which provides strength and high antibacterial properties of jute. It protects not only the space between the crowns, but also the wooden surface itself. However, a large amount of resin leads to inelasticity of the insulation. Over time, it becomes stiffer and seems to dry out, decreases in volume, which leads to the appearance of cracks. The combination of jute with flax batting makes it possible to neutralize this disadvantage.

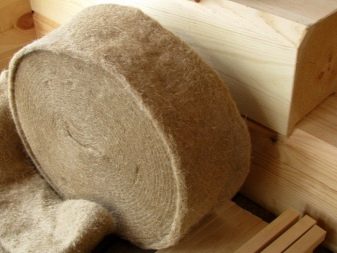
Felt
Natural wool material (sheep wool), which achieves unsurpassed heat and sound insulation characteristics. It is processed with water repellents and compounds that prevent insects and microscopic life forms from appearing in the insulation.
Among materials of artificial origin, synthetic winterizer, polytherm (synthetic felt on a polyester basis) and PSUL are popular. It is noteworthy that the name "polytherm" originally denoted a certain material of a Finnish manufacturer. However, over time, the term has become a household name. Today, it designates both a specific manufacturer and a type of polyester insulation.
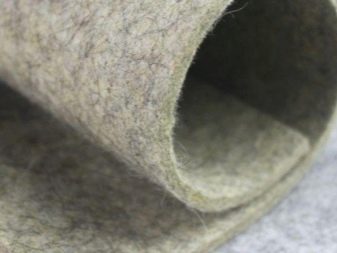
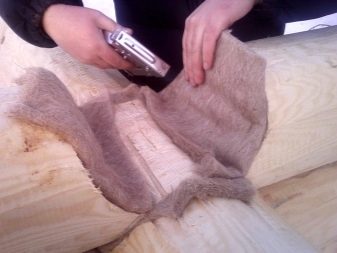
The abbreviation PSUL hides the following name - pre-compressed insulation. Its main ability is the property to shrink and expand in accordance with linear changes in the dimensions of the wood without losing its technical characteristics. In terms of thermal conductivity and moisture resistance, it exceeds the same values for natural insulation. At the same time, it is characterized by vapor permeability, biostability, environmental safety and fire resistance.
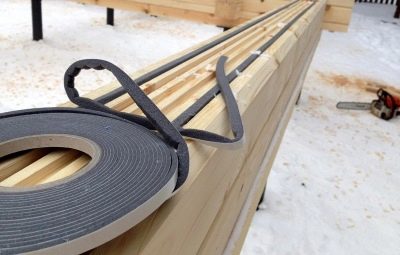
When insulating the seams between the joints, it is necessary to abandon the use of such heaters as tow and mineral wool due to their lower moisture resistance.
Manufacturers overview
When choosing a heater for a wooden house, it is worth giving preference to well-known, well-established brands.
- The leading position among manufacturers is occupied by the company Rockwool (Danish brand, which is also produced in 4 cities in Russia). The assortment impresses with its variety. Each section of the house has its own product line. So, for the walls, mineral wool insulation "Butts Light" and "Scandic" will be optimal. There are innovative mats for walls of different stiffness within the same mat, roll and slab counterparts. The disadvantage is the high cost (on average, 1500 - 6500 rubles / m2).
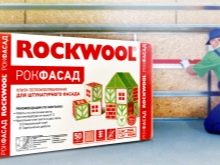
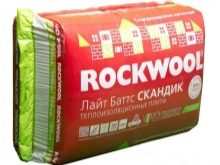
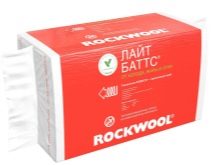
- Products from Germany are not inferior in quality - slab and roll mineral wool of trade marks Knauf and Ursa... To insulate a room from the inside, it is enough to select materials with a density of 10-25 kg / m3. The price is within 1200 - 3000 rubles / m2.
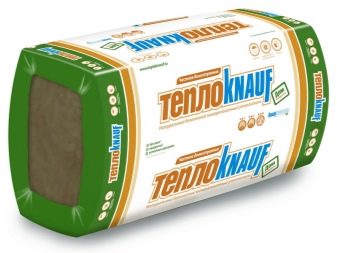
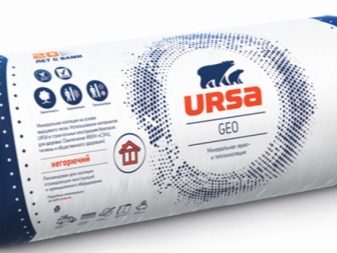
- Leading positions are also taken by French mineral wool insulation in plates, mats and rolls from the brand Isover... The collections include both lightweight products (with a density of 10-20 kg / m3) and rigid mats for frame houses (density 150-190 kg / m3). The cost is quite high - from 2,000 to 4,000 rubles / m2.
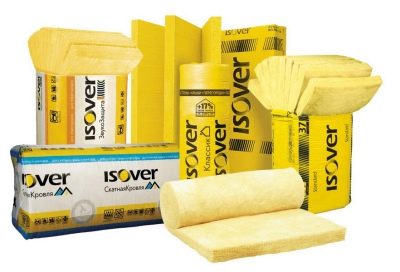
- Mineral wool produced in Russia, for the most part, is not inferior to Western counterparts in terms of thermal efficiency, vapor permeability and fire resistance. However, it has a more affordable price tag. User reviews allow companies such as TechnoNikol, Izovol.
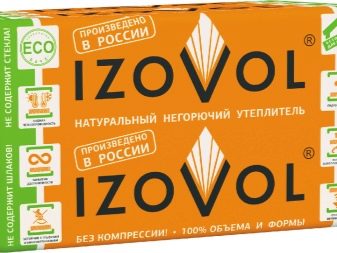
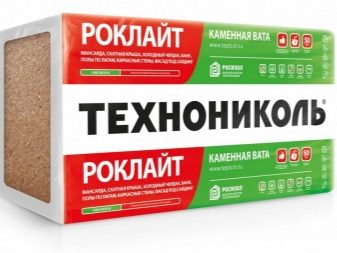
All the manufacturers mentioned above produce a type of thermal insulation wool that has improved sound insulation performance.
- Among the best manufacturers of ecowool, it is worth noting firms Isofloc (Germany), Ekovilla and Termex (Finland), as well as domestic companies "Equator", "Ekovata Extra" and "Nanovata".
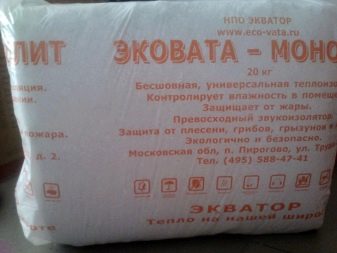
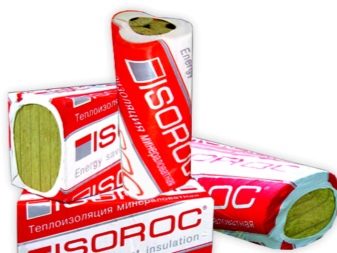
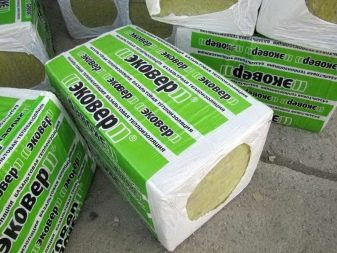
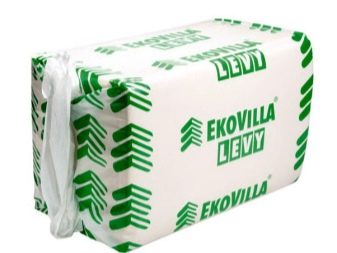
- Finnish mezhventsovy insulation "PoliTerm" is rightfully considered one of the most optimal for operation in domestic conditions. In addition to improved thermal insulation qualities, it is distinguished by the presence of special curly elements for the design of joints, corners, transitions in the house.
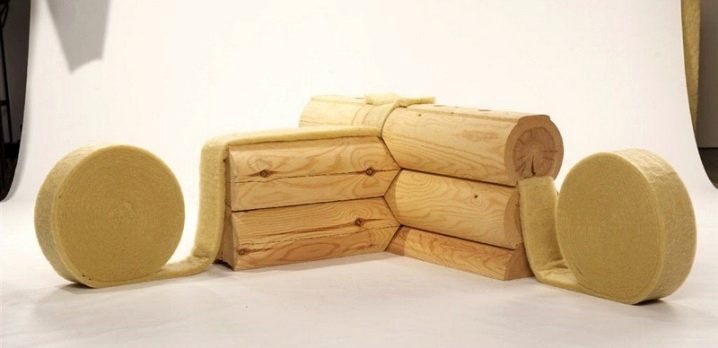
- A similar mezhventsovy heat-insulating material on a polyester basis is produced by a Russian brand "Avatherm"... According to the manufacturer, due to the highest performance characteristics, the material can serve up to 100 years. Popular brands of sealant are Weatherall and Neomid - Warm Joint.
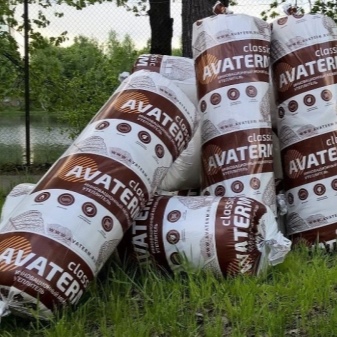
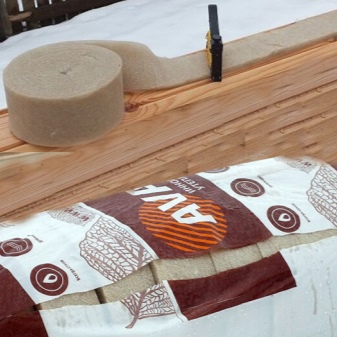
How to choose?
When choosing a material, it is important that its density corresponds to that required in a certain area of the house. In a number of cases (absolutely in all mineral wool products), the thermal conductivity, stiffness, weight and bearing capacity of the material depend on the density.
Usually, manufacturers indicate not only the density, but also the recommended scope of use of the material.
Pay attention to the storage conditions of the products.Mineral wool insulation should be stored in sealed original packaging, even slight soaking of the product is unacceptable. Expanded polystyrene is afraid of the sun's rays; under their influence, it begins to collapse.
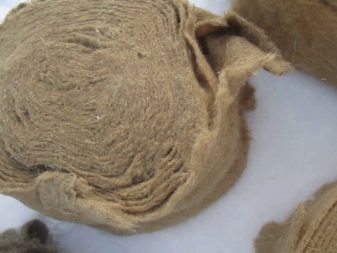
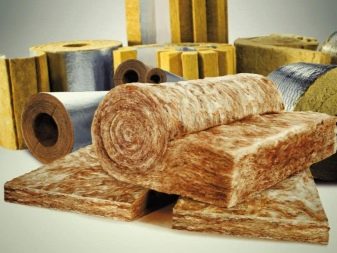
Types of technology
Depending on the type of materials used, as well as the installation methods used, the following technologies for thermal insulation of a wooden house are distinguished:
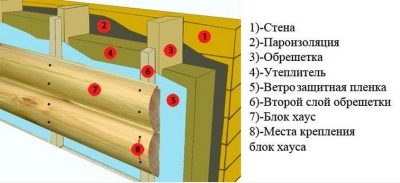
Warm seam
It is used for mezhventsovy insulation of log houses, for sealing the joints between the laying of the foundation and the walls. Suitable for objects in which additional wall decoration from the inside is not provided. For insulation, special mezhventsovy insulators are used, as well as silicone sealants. The advantage of this method is the lower labor intensity and cost of the process, the ability to preserve the natural beauty and vapor permeability of wooden coatings.
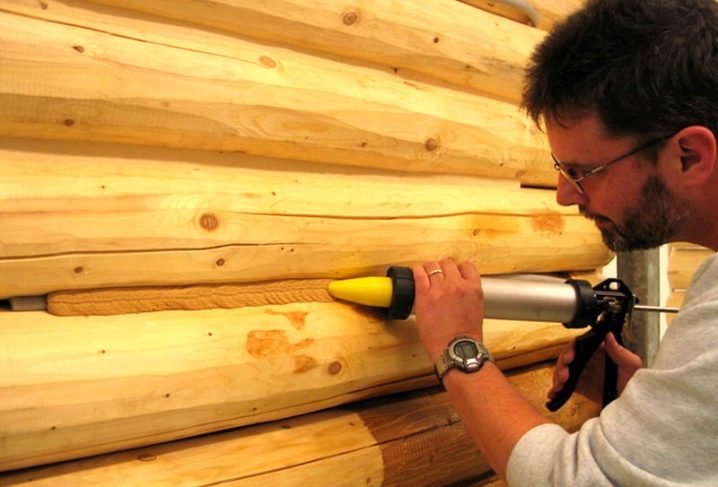
Insulation on the crate
It is provided for in the presence of interior wall decoration, as well as insufficient thermal efficiency of the mezhventsovy insulation. Without fail, it requires vapor barrier and walls and additional ventilation of the house, fastening the frame, fixing the insulation, continuous sheathing of the frame with plasterboard and attaching the finishing material to it. Such thermal insulation is effective, and so that there is no condensation, a gap is maintained between the insulation and the casing for air circulation.
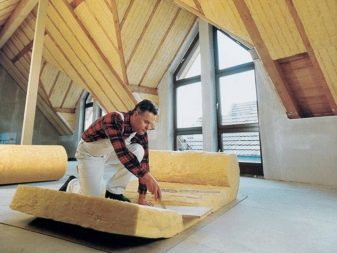
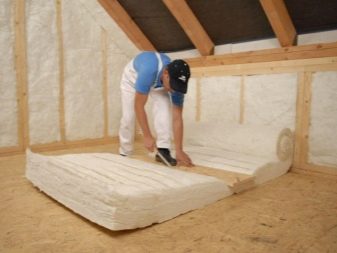
How to do it yourself?
- Regardless of the technology used, first of all the walls should be prepared... If you decide to do the work yourself, then you should start by cleaning them from dust, dirt, old coating. If cracks are found, they are treated with a sealant, all irregularities are cleaned. Before insulation, you should also remove all communications from the walls, check the wiring. The preparatory stage is completed by applying an antiseptic primer and fire retardants to the surface.
- Installation of vapor barrier film. It is attached to the entire surface with a gap of 10 cm and is fixed with construction tape. If financial resources permit, then instead of a vapor barrier film, it is better to use a more effective vapor barrier membrane. Let us remind you once again that vapor barrier is only one of the components of maintaining optimal humidity and a favorable microclimate in a wooden house. The second required "component" is the ventilation system.
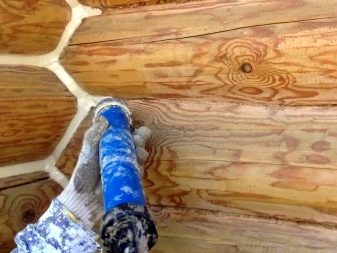
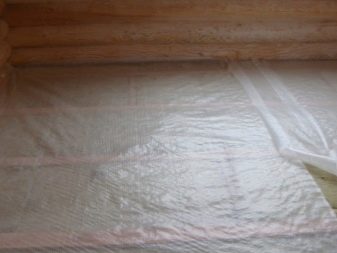
- Creating a wooden lathing, which is fixed to the walls of the house by means of brackets. The lathing is assembled from wooden logs, which are pre-treated with fire retardants and antibacterial compounds. The step of the lathing corresponds to the width of the insulation, and when using mineral wool products, it can even be 1-2 cm narrower. The most common, as already noted, insulation for wooden walls is mineral wool. Its layers are placed between the elements of the crate and fixed with dowels.
- Chipboard installation or plasterboard sheets as a facing layer. A small gap remains between the drywall sheets and the insulation layer, which provides better thermal insulation and allows the insulation to be ventilated. If ecowool is used as a heat insulator, then plasterboard sheets are immediately attached to the crate, and ecowool is poured into the formed gap. Plasterboard sheets are putty in several layers with preliminary treatment of each layer with fine sandpaper. After applying the finishing layer of putty, you can start fixing the wall decorative coating - wallpapering, painting, etc.
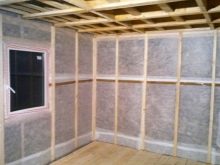
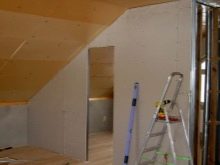
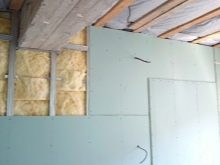
Today on sale you can find mineral wool slabs with different thicknesses in thickness.
The part of the slab that is attached to the wall has a looser structure, the outer surface is more dense and stiff. Such materials are glued to the wall using special mixtures.Due to the high rigidity of the outer side of the insulation, it is possible to do without installing the lathing. The material is covered with glue, reinforcing fiberglass is attached to it, on top of which plaster is applied in several layers, and paint or decorative plaster is applied to it.
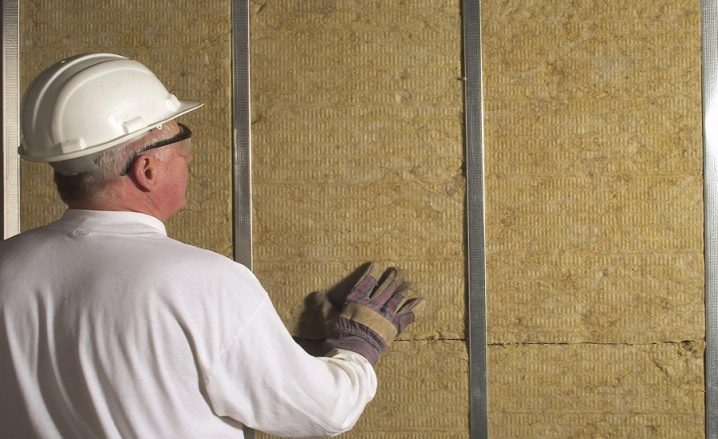
Wall cladding made of logs or timber looks somewhat different.
- Immediately after the construction of the building, the primary insulation of the gaps between the joints, which is also called caulking, is performed. To do this, a twisted inter-crown insulation is inserted into the gaps using a caulk or a spatula. When using synthetic materials, a sealant layer is applied over them.
- After a year (it is after so much time that the house gives the maximum shrinkage), repeated caulking is carried out. First of all, the condition of the wooden surface itself is assessed. If chips and cracks are found, they are filled with the same elastic sealant. Next, they check the quality of the insulation of the seams between the joints. It is better if this is done not only "by eye", but also with the use of a thermal imager.
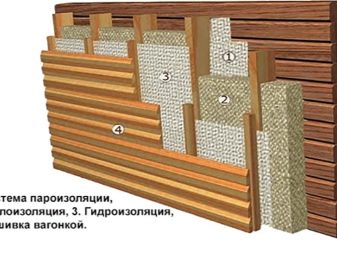
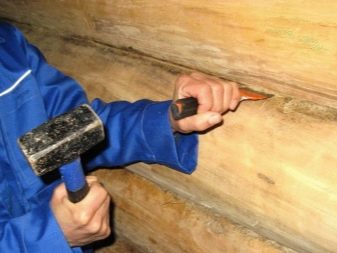
- If heat loss points are found, they will be caulked again. If additional insulation of log walls is not provided, then the joints are re-treated with a sealant, now for decorative purposes. Modern compositions are characterized by a richness of colors, so the user can choose a mixture to match the logs. Another option to close the joints is to use jute braid, which has an attractive soft golden hue and looks harmonious with most types of wood.
- If further thermal insulation of the walls is assumed, then the steps described above are performed (priming, creating a vapor barrier layer, installing the frame and fixing the insulation, fastening drywall, finishing). Ceiling insulation also implies the creation of a crate, under which a waterproofing coating is laid, for example, glassine. Further, with the help of self-tapping screws and special glue, the insulation is fixed to the ceiling. The next step is to cover the ceiling with plasterboard and finish cladding.
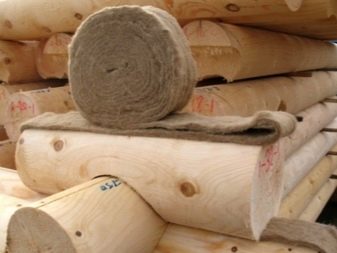
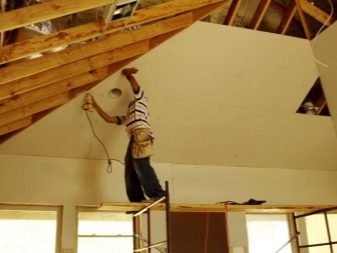
If there is a second floor, the ceiling is insulated. For interfloor floors, materials of increased rigidity are required.
If the house has an attic of an unexploited type, then bulk materials (expanded clay, ecowool) can be used to insulate it. For heated attics and attics, special basalt heaters of increased rigidity are produced. Insulation of maximum rigidity (from 150 kg / m3) is required for a flat roof.
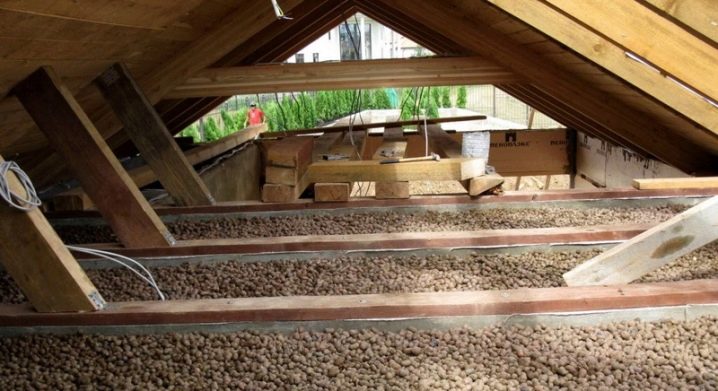
When insulating the floor first of all, it should be leveled, laid with an overlap and with a small (up to 10 cm) "creeping" on the walls of the waterproofing membrane. After that, lay wooden logs in increments of no more than 50 cm. Mineral wool (or expanded polystyrene) is placed between the logs. The insulation layer is closed with a PVC membrane, on top of which the flooring is mounted (usually chipboard or plywood sheets).
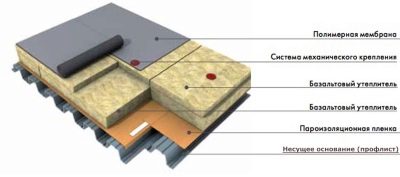
Helpful tips from the pros
Experts recommend carefully calculating the thickness of the material, since the indicators of its thermal efficiency depend on this. If the insulation layer is insufficient in the house, it will not be possible to reach the optimal temperature. An unnecessarily thick layer is not only unjustified financial costs, but also an additional load on the supporting structures, as well as a change in the location of the "dew point".
The latter term denotes the border where the moisture escaping from the room in the form of vapor turns into liquid. Ideally, this should take place outside the insulation, however, if the thickness is incorrectly calculated and the installation technology is violated, the “dew point” may end up inside the insulation.
It is also wrong to insulate a wooden house from the inside and outside. The surface of the wood is between 2 vapor barrier layers, which disrupts the natural ventilation of the material and leads to the onset of putrefactive processes.
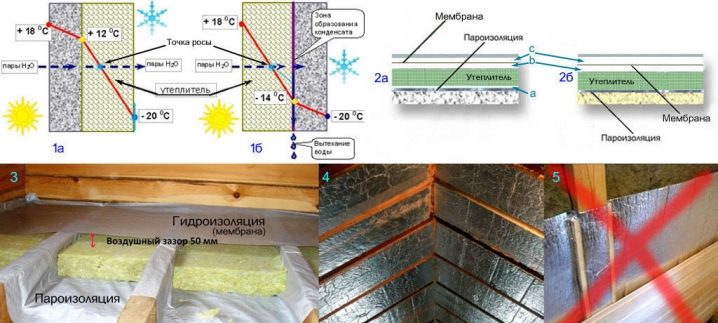
Professionals strongly recommend using outdoor insulation as more effective and correct for the operation of a wooden house. Insulation from the inside is an extreme measure. Thermal insulation work should be carried out in the warm season, in dry weather, since during this period the walls are as dry as possible. If you plan to insulate a newly built house, then you should wait a year. This is due to the fact that wooden objects shrink.
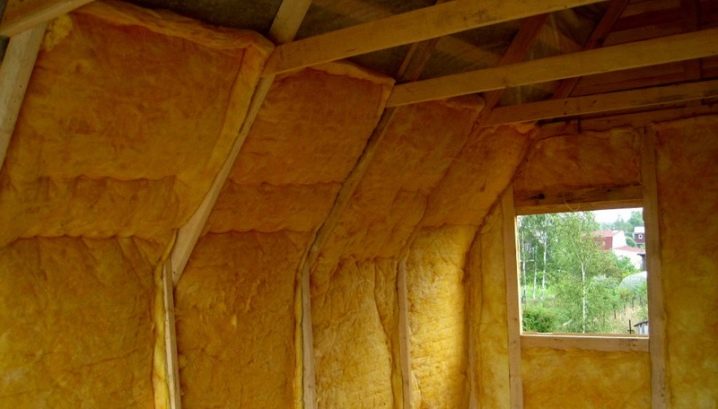
When installing the battens, make sure that its pitch matches the dimensions of not only the insulation, but also the drywall sheets. Otherwise, additional slats will have to be stuffed - an extra load on the frame and an increase in labor intensity. The best option is to select sheets of insulation and drywall of similar dimensions.
Despite the cheapness of polystyrene, as well as its low heat transfer, refuse to insulate wooden walls with this material.
- It has low vapor permeability, which will lead to decay of the walls, increased humidity in the house, the appearance of condensation on the walls and mold on the finishing material.
- It emits styrene hazardous to health, and therefore in some European countries there is a ban on the use of expanded polystyrene for interior decoration.
- It is a flammable material that releases toxins when the temperature rises. When using foam in a wooden structure, you can create a real fire trap.
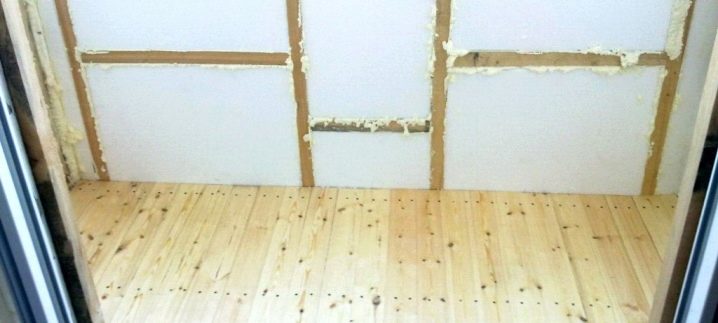
The sealant used for inter-crown insulation must be elastic and capable of shrinking and expanding during the shrinkage and thermal expansion of the wood. For use inside the house, an acrylic-based composition will be optimal. If you need a more durable sealant, then acrylic with the addition of polyurethane foam is suitable. An important point is that such a sealant cannot act as an independent insulation.
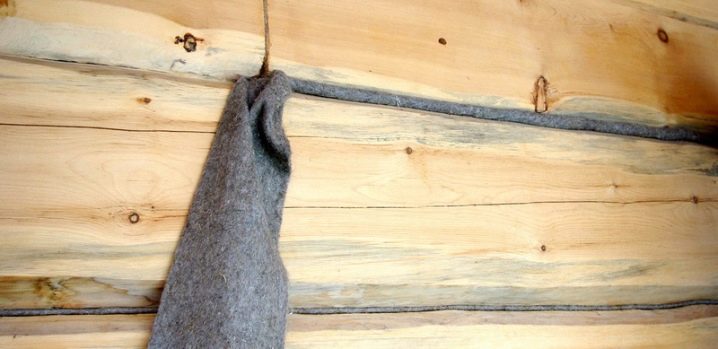
When insulating the gaps between the joints, it is important to carry out work around the entire perimeter of the building. That is, first, the first row of gaps is insulated around the entire perimeter, then you can move on to the second. If you first insulate one wall, and then the second, warping of the house cannot be avoided.
See the next video for more details.
The comment was sent successfully.