Isoroc insulation: features and scope
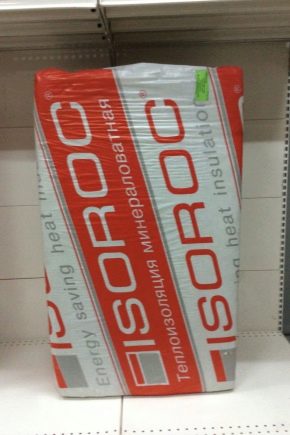
The TOP-list of the best modern thermal insulation materials, along with European heaters, also includes Isoroc products from Russia. Having entered the market in 2000, this company has managed to quickly gain the trust and respect of professional and novice builders. Evidence of this is the entry of the company into the international concern Saint-Gobain, which is a leader in the production of building materials and the development of innovative technologies in the construction industry.
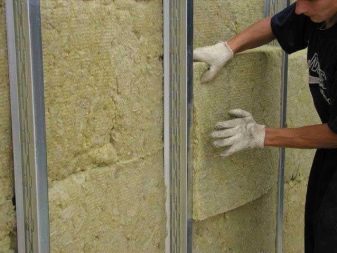
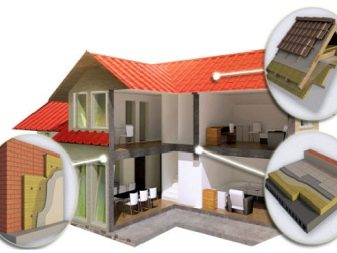
Features of production
Modern insulation Isoroc is made of basalt or gabbro using technologies developed in Germany, using equipment from the Swedish company Ungers.
The process of creating a thermal insulation material consists of several stages:
- Under the influence of high temperatures (up to 1500 ° C), the rock is melted.
- The melt is placed in a centrifuge, in which it is drawn into "filaments".
- The resulting fibers under the influence of air masses move into the fiber deposition chamber, in which dedusting and water-repellent components are added to them.
- The processed basalt fiber enters the apparatus, where it is distributed and the individual threads are firmly woven together. When weaving, the fibers are placed in different directions to increase the strength of the fabric.
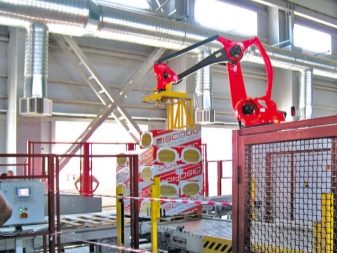
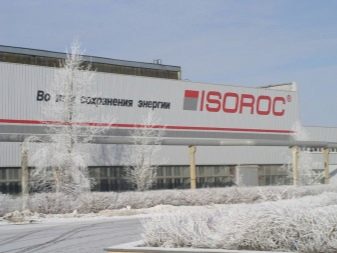
- Subsequently, the resulting material is pressed under high pressure and again subjected to heat treatment. When heated again, the fiber polymerizes, forming a material resistant to mechanical damage (tearing, cracking).
- The finished insulation is cut into plates or mats and placed in heat-shrinkable packaging.
In the production process, everything is taken into account: from the quality of raw materials to the exact observance of the proportions of components and technologies. At all production stages, dozens of different parameters are constantly monitored, which guarantees an exceptionally high quality of each batch of products.
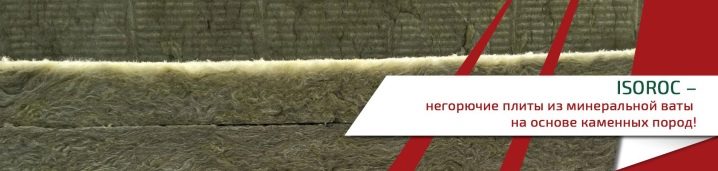
Insulation specifications
Due to its composition and manufacturing technology, Isoroc insulation acquires the following technical characteristics:
- High density, which affects the strength of the material and its resistance to deformation. Depending on the density, the scope of use of the material is determined, and its cost changes.
- Compressibility indicators - from 2 to 20%.
- Thermal conductivity varies in the range of 0.04-0.042 W / mK, due to which the material retains heat well. This effect is achieved due to the large number of air pores formed in the material during the production process.
- Good vapor permeability avoids the accumulation of condensation inside the room and the formation of mold.
- Fire safety. The stone fibers of the heat insulator do not ignite even in contact with an open fire and can withstand temperatures up to 1000 ° C.
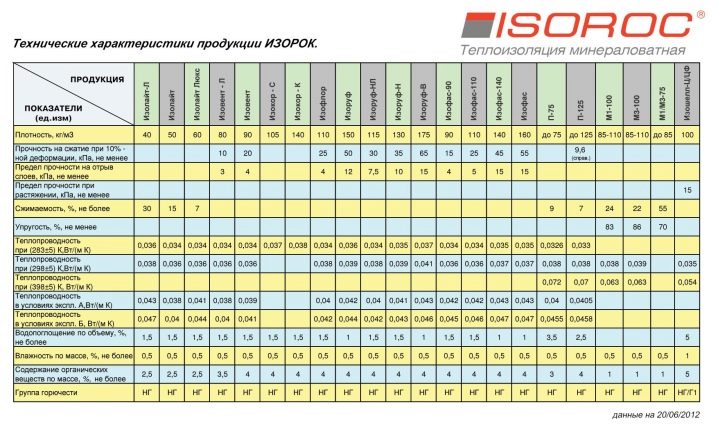
For different models of insulation, the characteristics are different, but at the same time, all products always contribute to:
- improving the indoor climate;
- significant improvement in heat and sound insulation properties;
- reducing the load on the base of the building (foundation).
In addition, any Isoroc model reduces repair costs.
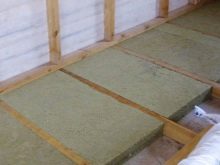
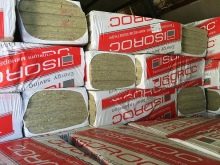
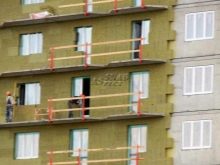
Advantages and disadvantages of the material
Compared to most insulation materials, Isoroc basalt insulation has a number of advantages, including:
- high hydrophobicity;
- good resistance to external negative influences (mechanical and natural);
- ease of installation and operation;
- environmental friendliness;
- light weight.

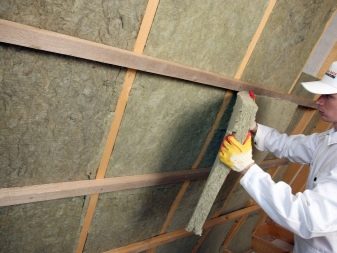
In addition, it does not deform, does not crumple over time, microorganisms do not multiply on it, and insects with rodents prefer to stay away from it. Thanks to all this, basalt insulation has a long service life and does not require replacement for a long time.
As for the shortcomings, only the rather high cost of the material can be attributed to them.
Scope of application
Isoroc mineral wool has found application in a wide range of construction and repair work. Most often it is used for:
- roofs (both flat and pitched);
- attic and basement floors;
- walls inside the house;
- external facades (for plastering or on ventilated curtain facades);
- floor;
- sandwich panels or three-layer concrete structures;
- industrial equipment and pipelines.
High quality and a wide range of insulation make it possible to use it both in large and low-rise private construction.
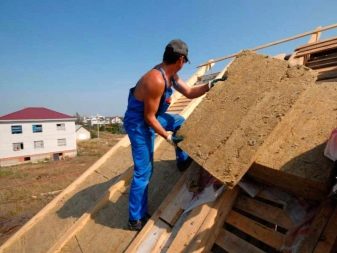
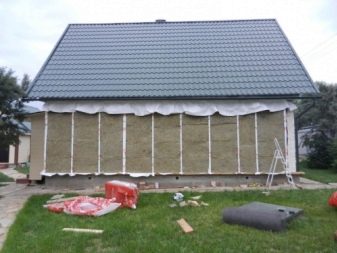
Insulation types Isoroc
The assortment of the company includes several options for insulation. The most popular and demanded ones are:
- Isolight and its modifications. This type of thermal insulation material is intended for insulation of horizontal, vertical, inclined surfaces of any type. It is suitable for use on frame walls, interfloor ceilings, in three-layer masonry, ventilated facades. Plates of conventional Isolight insulation have a density of 50 kg / m3 and are considered the best option for low-rise private construction. In addition, the model range includes mineral wool slabs with a density of 40 kg / m3 (Isolight-L) and 60 kg / m3 (Isolight-Lux). With different densities, all materials from this series have similar characteristics. So, the indicator of water absorption of any of these heaters, even with prolonged exposure to moisture, does not exceed 1 kg / m2, and the thermal conductivity varies from 0.33 to 0.40 W / (m. K), depending on the operating conditions.
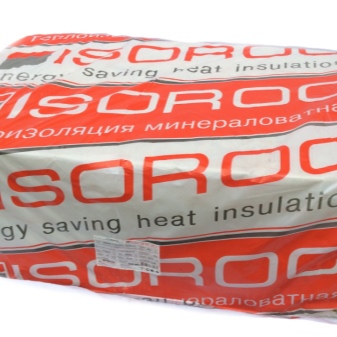
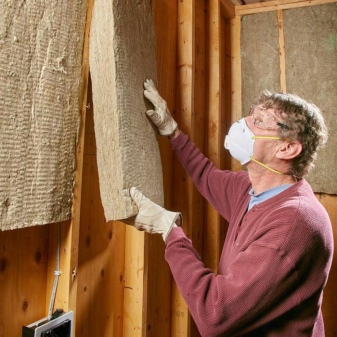
- Ultralight - one of the novelties in the range of thermal insulation materials. The main distinguishing feature of this type of insulation is its reduced density - 33 kg / m3. At the same time, the manufacturer offers plates with a thickness of 100 mm and 50 mm. Otherwise, the performance standards of Ultrlight practically do not differ from the heaters of the previous series.
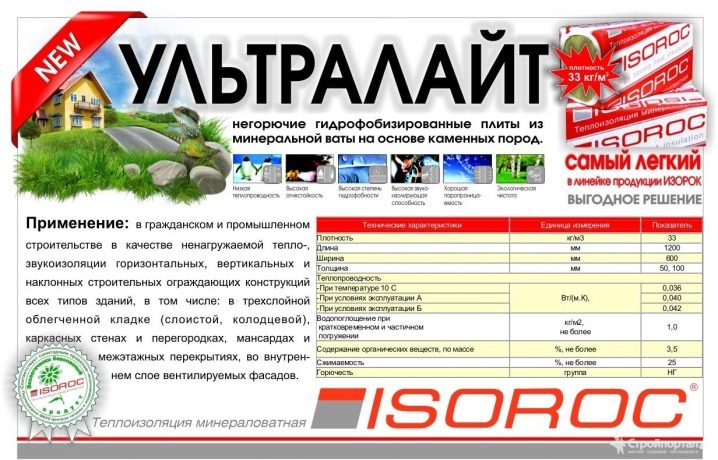
- Isoroof - material intended for thermal insulation of a flat roof made of steel corrugated board and interfloor ceilings. It can be laid both on top of a cement screed, and directly on a concrete or reinforced concrete base. This type of insulation has a high density - 150 kg / m3, thickness from 40 to 130 mm. At the same time, it is quite elastic, easy to process, inert to chemicals and not susceptible to biological effects (mold, rot). In this series, modifications are also presented with the Isoroof -B (Isoroof-T), -H (Isoroof-B), -NL (Isoroof-BL) marking. They differ from each other in density and are used to create a two-layer thermal insulation system.
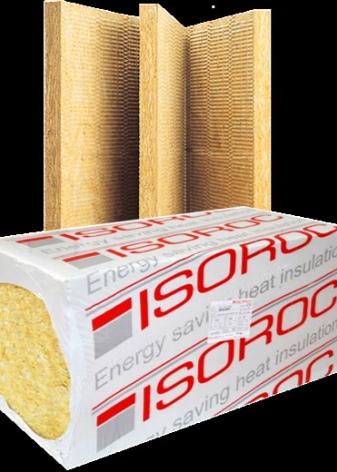
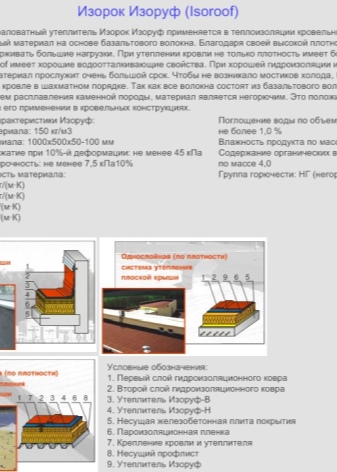
- PP 75 and PP 125 - materials suitable for thermal insulation of buildings, structures and insulation of industrial equipment, the surface of which can be heated to + 400 ° C. The first type has a lower density (up to 75 kg / m3), but has more flexibility, which allows it to be used on curved surfaces (for example, pipelines). Insulation marked PP 125, in turn, bends and changes shape much more difficult, but has a density of 12 kg / m3 and a strength of at least 10 kPa.
- Isovent - refractory plates, most often used to insulate saunas and baths. Lined with aluminum foil, metal mesh or fiberglass fabrics, during installation it does not require the use of additional polymer membranes. In addition to the basic insulation, the series includes modifications of SL and L. The main difference between the models from each other is density.Isovent has the highest indicator - 90 kg / m3. At the same time, basalt fiber slabs of this type can have a reduced thickness - 40 mm. As for other modifications, their thickness parameters vary between 50-170 mm. The density of the insulation labeled SL is 75 kg / m3, and L is 80 kg / m3.
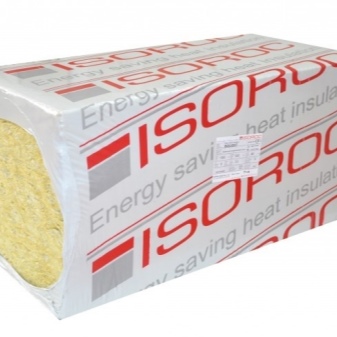
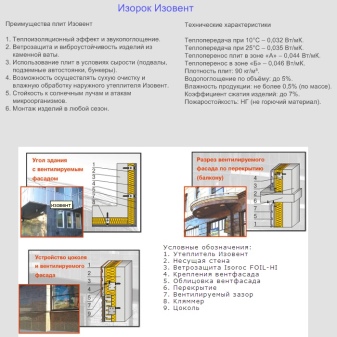
- Isofloor - one of the best options for installation on intermediate floors and floors. It can be installed under cement screed and self-leveling floors. Also suitable for insulating sandwich panels with a metal sheath. With a density of 110 kg / m³, mineral wool slabs of this type have increased strength, which allows them to withstand significant loads without deformation and loss of their performance.
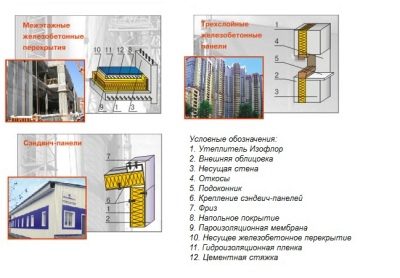
All Isoroc mineral wool boards are sold in packs of 4 or 8 sheets. The weight and dimensions of the package depend on the density and dimensions of the insulation itself.
Installation rules
The quality of insulation with Isoroc basalt mineral wool slabs largely depends on how they were installed. Therefore, non-professional and novice repairmen for installing insulation it is worth using the advice of experienced craftsmen:
- For fixing the plates, special adhesives and disc dowels are used.
- In order for the structure to be as strong and durable as possible, for laying the thermal insulation, it is necessary to build a frame from a metal profile or wooden bars.
- If necessary, use an assembly knife to cut the slab of basalt fibers. With a high density and thickness of the material, the knife is replaced with a hacksaw.
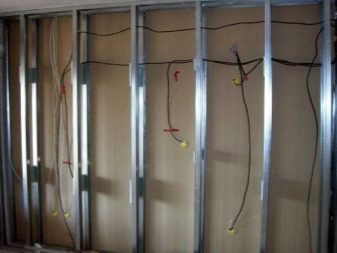
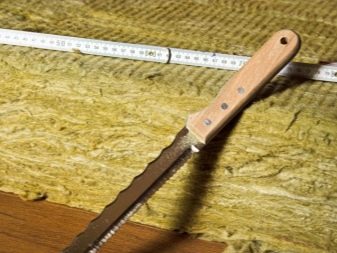
The process of installing thermal insulation itself consists of several stages:
- Installation of a metal or wooden frame. For this, the profile or bars are fixed in a strictly vertical position. The distance between the supports depends on the width of the mineral wool slab - the insulation should fit tightly between them.
- Isoroc slabs are fastened to stone surfaces with nails at the rate of 5-6 dowels per 1 m2. In other cases, glue is used for fastening.
- A windproof membrane is laid on top of the basalt wool, all joints of which are carefully glued with adhesive tape.
When insulating a roof, floor or facade, the installation rules may differ slightly. An important condition for laying the insulation is the presence of a ventilated gap between it and the external finish. It is necessary so that the moisture trapped by the vapor barrier film is not absorbed into the finishing materials.
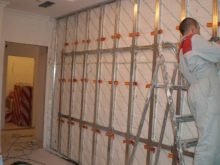
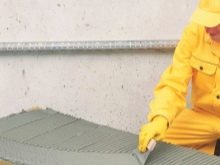
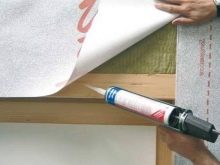
Reviews
Numerous customer reviews testify to the popularity and high quality of Isoroc brand heaters.
Most of those who insulated their houses with mineral wool boards from this manufacturer highly appreciate the thermal insulation qualities of the material. At the same time, they note that after installing basalt insulation boards, even at low external temperatures, energy consumption is significantly reduced, since the air in the room heats up faster and stays warm longer.
Also, when using basalt fiber insulation, steam does not accumulate inside the room, which not only increases comfort, but also extends the service life of finishing and other building materials.
Along with the performance of the material, the ease of transportation and installation of the insulation deserves high marks.
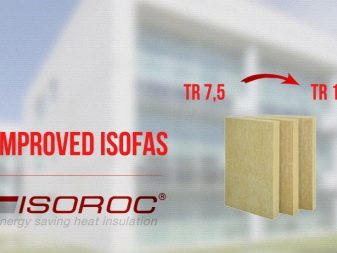
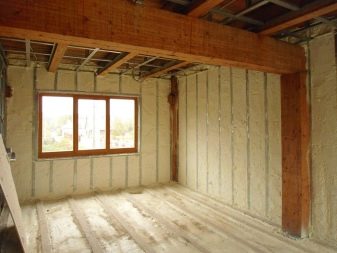
For an overview of Isoroc insulation, see the next video.
The comment was sent successfully.