Indesit washing machine motors: varieties, check and repair
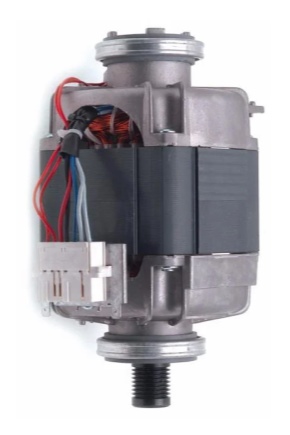
Over time, any technique fails. This also applies to the washing machine. After many years of operation, the drum may stop starting, then high-quality diagnostics are required to determine the cause of the malfunction.
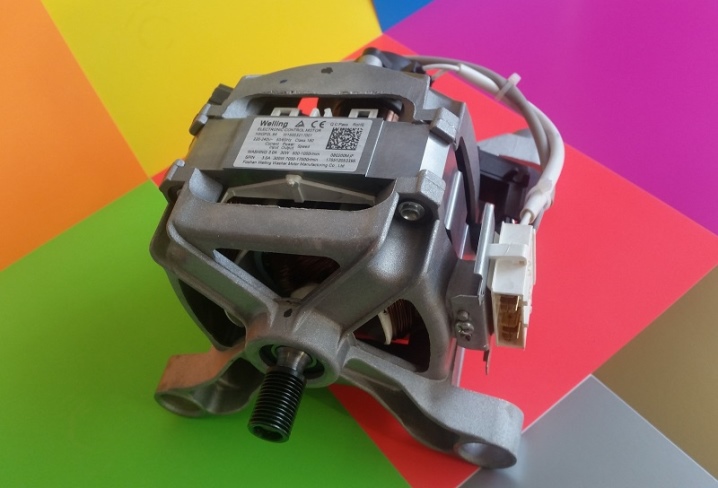
Views
The engine of the Indesit washing machine is the main component of its design, without which the operation of the device will be impossible. The manufacturer creates equipment with different motors. They differ among themselves in power and not only. Among them are:
- asynchronous;
- collector;
- brushless.
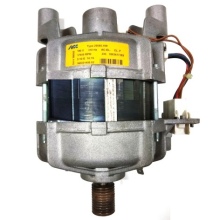
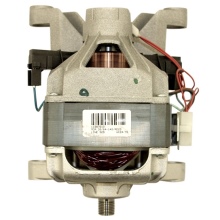
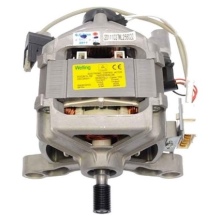
In old models of Indesit equipment, you can find an asynchronous electric motor, which has a simple design. If we compare it with modern developments, then such a motor performs a smaller number of revolutions. The engine of this type has ceased to be used in new models, because it is not only large and heavy, but also has a small efficiency. The manufacturer gave preference to the collector type and brushless. The first type is much smaller than an induction motor. The design has a belt drive. The advantages are high speed of work, regardless of the frequency shown by the used electrical network. The design also contains the following elements:
- brushes;
- starter;
- tachogenerator;
- rotor.
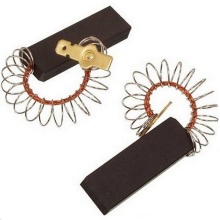
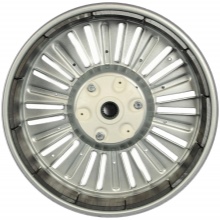
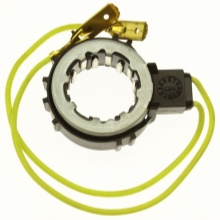
Another advantage is the ability, even with minimal knowledge, to repair the engine at home on your own. The brushless design features a direct drive. That is, it does not have a belt drive. Here the unit is directly connected to the drum of the washing machine. This is a three-phase unit, it has a multi-lane collector and a rotor in the design of which a permanent magnet is used.
Due to the high efficiency, the cost of washing machine models with such a motor is much higher.
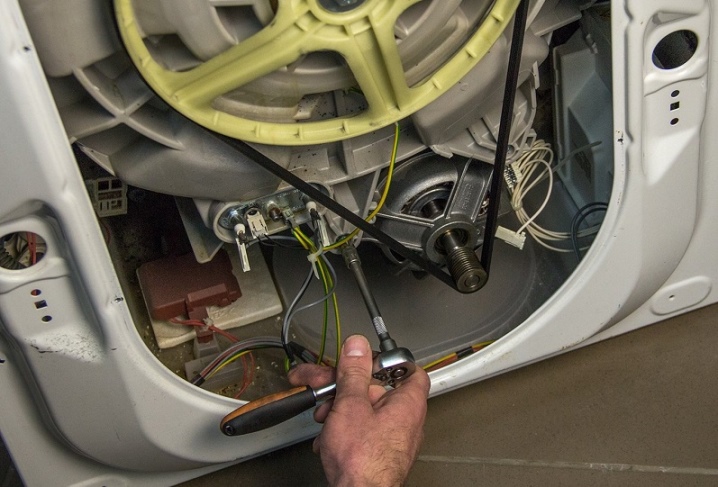
How to connect?
A detailed study of the wiring diagram allows you to understand the principle of the motor. The motor is connected to the network without a starting capacitor. There is also no winding on the unit. You can check the wiring with a multimeter, which is designed to determine the resistance. One probe joins the wires, the others are looking for a pair. The tachometer wires give out 70 ohms. They are being pushed aside. The rest of the wiring is also called.
In the next step, there should be two postings left. One goes to the brush, the second to the end of the winding on the rotor. The end of the winding on the stator is connected to a brush located on the rotor. Experts advise making a jumper, and then be sure to supplement it with insulation. A voltage of 220 V will need to be applied here. As soon as the motor receives power, it will begin to move. When checking the engine, it must be fixed on a level surface. It is dangerous to work even with a home-made unit.
Therefore, it is important to observe safety precautions.
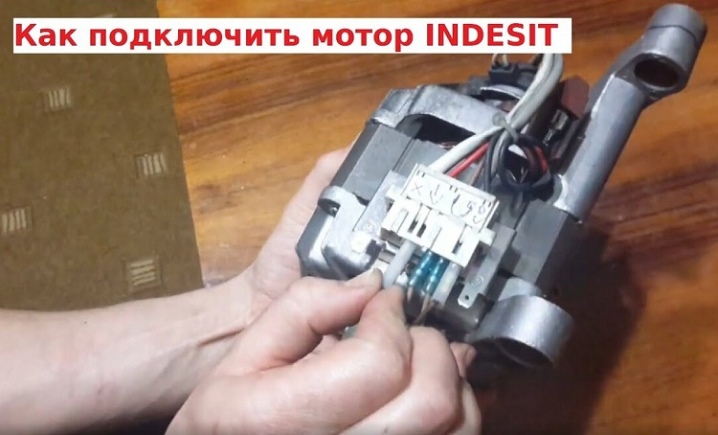
How to check?
Sometimes a motor check is required. The unit is preliminarily removed from the case. The sequence of user actions is as follows:
- the panel from the back is removed first, its small bolts are held around the perimeter;
- if this is a model with a drive belt, then it is removed, simultaneously making a rotational movement with a pulley;
- the wiring that goes to the motor turns off;
- the engine also holds the bolts inside, they are unscrewed and the unit is taken out, loosening it in different directions.
When performing the described work, the washing machine must be disconnected from the mains.When the preliminary stage is over, it's time to diagnose. We can talk about the normal operation of the motor after it began to move when connecting the wire from the stator and rotor windings. Voltage is required, since the equipment is turned off. However, experts say that it is impossible to test the engine in this way completely.
In the future, it will be used in different modes, so it will not be possible to give a full assessment.
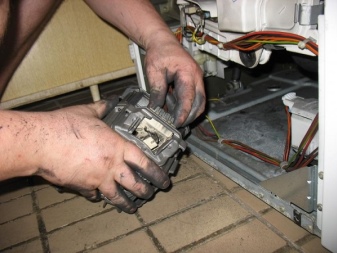
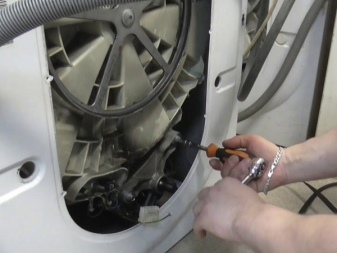
There is another drawback - due to a direct connection, overheating can occur, and it often causes a short circuit. You can reduce the risk if you include a heating element in the circuit. If a short circuit occurs, then it will heat up, while the engine will remain safe. When carrying out diagnostics, it is worth checking the condition of the electric brushes. They are necessary to smooth out the friction force. Therefore, they are located on both sides of the washing machine body. The entire blow falls on the tips. When the brushes are worn out, they decrease in length. It is not difficult to notice this even by visual inspection.
You can check the brushes for functionality as follows:
- you will first need to remove the bolts;
- remove the element after the spring has been compressed;
- if the tip length is less than 15 mm, then it is time to replace the brushes with new ones.
But these are not all elements that should be checked during diagnostics. Be sure to test the lamellas, it is they who are responsible for the transfer of electricity to the rotor. They are not attached to bolts, but glue to the shaft. When the motor gets stuck, they flake off and shatter. If the detachment is insignificant, then the engine may not be changed.
Correct the situation with sandpaper or a lathe.
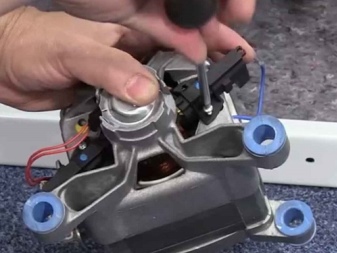
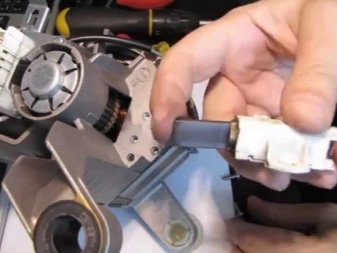
How to repair?
If the technique sparks, then it is strictly prohibited to operate it. Repair and replacement of some elements can be done at home on your own, or you can call a specialist. If there is a problem with the winding, then the engine will not be able to gain the required number of revolutions, and sometimes it will not start at all. In this case, there is a short circuit causing overheating. The thermal sensor installed in the structure instantly triggers and cuts down the unit. If the user does not respond, the thermistor will eventually deteriorate.
You can check the winding with a multimeter in the "Resistance" mode. The probe is placed on the lamella and the value obtained is evaluated. In a normal state, the indicator should be from 20 to 200 ohms. If the number on the screen is less, then there is a short circuit. If more, then a cliff appeared. If the problem lies in the winding, then it is better to contact the service center. The lamellas are not replaced. They are sharpened on a special machine or sandpaper, then the space between them and the brushes is cleaned with a brush.
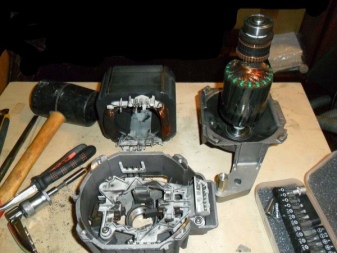
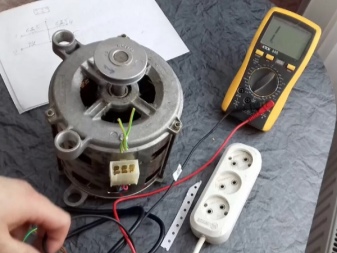
You can find out below how to replace the brushes in the engine from a washing machine without a soldering iron yourself.
The comment was sent successfully.