Features of horizontal boring machines
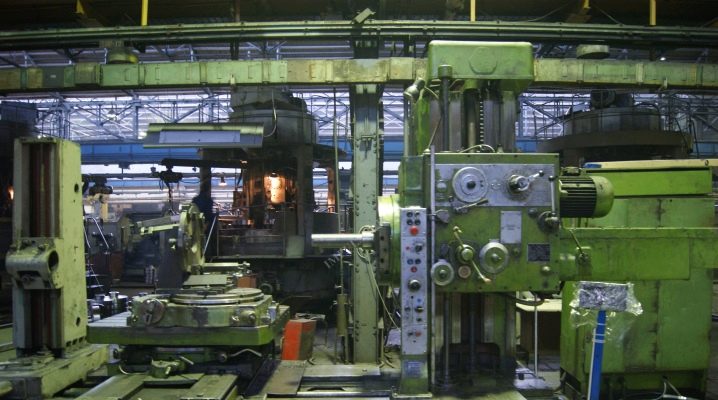
For the processing of metal blanks, there is a large number of equipment that differ from each other in the way of work, scope, and capabilities. Among the most popular machines are horizontal boring machines, as they are multifunctional and allow you to perform tasks of varying complexity.
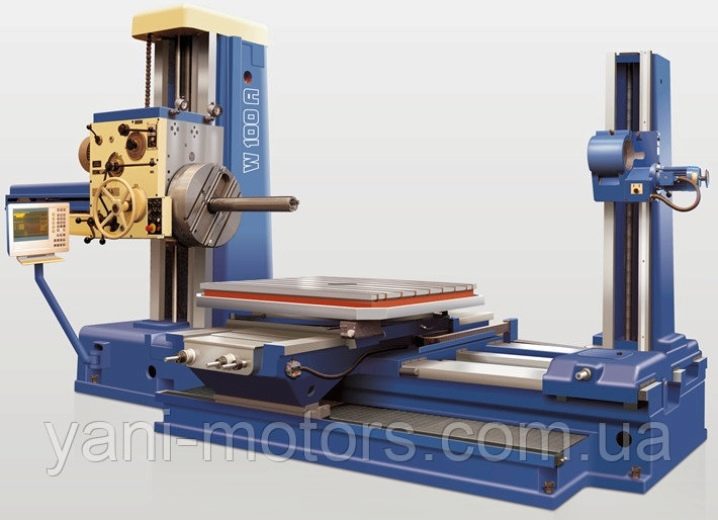
Device and principle of operation
The principle of operation of these products is to perform various operations with the prepared material using a spindle and a fixed tool. As a rule, the most used of them are drills, reamers, cutters, countersinks and many others. The rotation of these parts allows the metal to be processed in such a way that the final product most closely matches the way the worker or manufacturer envisions it. There are no serious features of the principle of operation, since the machines themselves have one purpose of operation - to make a finished part from a workpiece or to bring it to a certain state for subsequent work with a different technique.
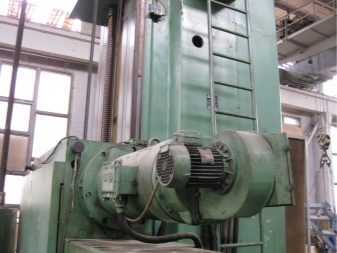
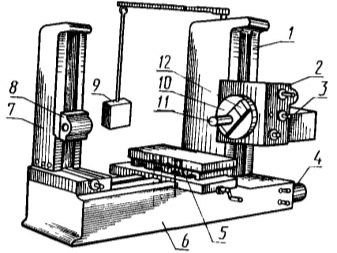
Many models and their modifications allow us to say that the variability of the use of horizontal boring machines is very diverse. For example, semi-professional units mainly have a fixed working table and a very mobile spindle that rotates in different directions and processes metal structures. There are also models with a high degree of automation.
Their feature is that the spindle is completely motionless, which cannot be said about the desktop. It can move in height, length, width - all axes. And already according to this technology, the position of the workpiece relative to the main equipment changes.
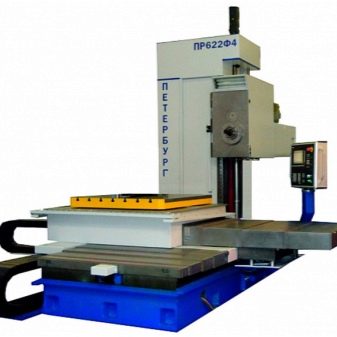
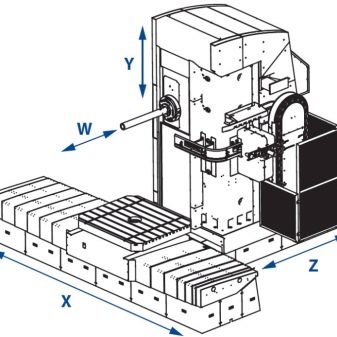
A slightly different principle of operation for products with CNC. In this case, the main stage of preparing the machine is programming, which consists in creating an approximate workpiece in the application, specifying all the necessary parameters and translating this into reality through automated mechanisms. Simulation programs using editors allow you to create a variety of models in the form of geometric shapes, select a processing method and a tool, set coordinates and vector guides, variations in spindle movement and much more.
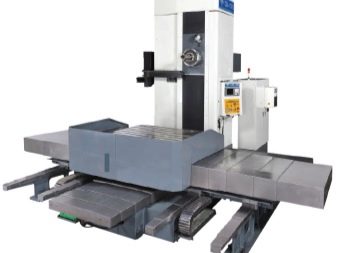
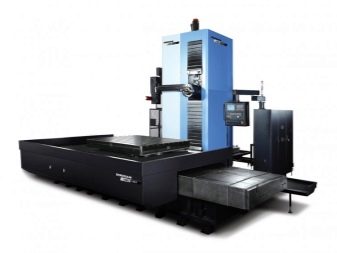
Also, the functionality of CNC is not limited to only one stage of work - there can be a large variety of them, from purely rough processing to finishing and the last. This is one of the advantages of such machines, because all phases can be carried out on the same equipment, if possible in a particular situation.
As for the device, it is also different. But there are also common features inherent in all machines, without exception. Firstly, this is the presence of a table where the processed raw materials are located and the tool works. The fastening depends on the manufacturer of the equipment and the method used by the manufacturer. Secondly, each machine has units, which include the spindle and other elements, if they are provided by the package.
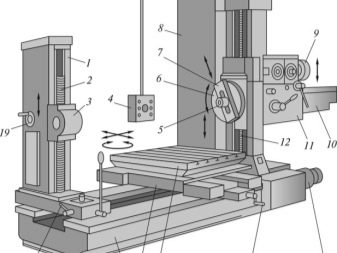
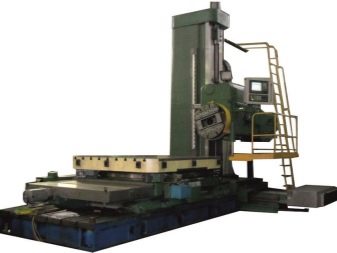
Specifically, in horizontal boring models, the entire working base is on top, but the free movement of the tools or the working table allows processing workpieces on all sides.
Naturally, the entire structure is located on a bed, the workmanship of which must be at a high level, because deficiencies in this component can lead to inaccuracies in the work. If in household production this is not so scary, then with serial production you can suffer considerable losses, which is inadmissible. Also, the device of the machines includes racks. Their purpose is to create a place where tools and controls can be secured. It is this set that is standard and is found on all machines.
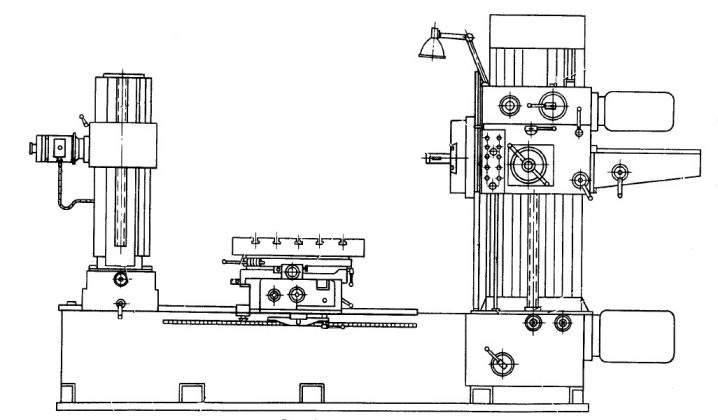
As with any similar technique, horizontal boring models have individual schemes for assembly and repair. But this is done only by specially trained personnel, which should be at every enterprise using these units. Due to the complexity of the design of units and all technologies, it is not recommended to make any major changes on your own. Only a trained person can schematically understand the method of work, since all the drawings and details specified in the documentation are collected together, which makes it difficult to perceive the individual mechanisms of technology.
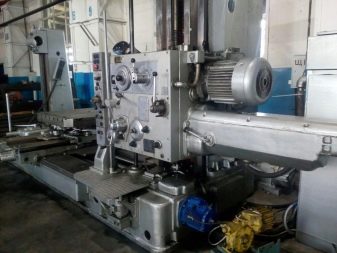
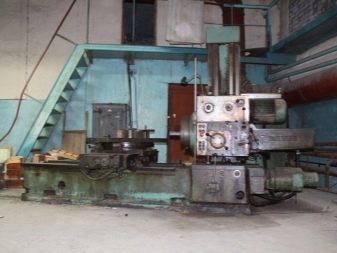
Appointment
The horizontal boring machines are very versatile and can be used in a wide variety of variations. The main working operations are cutting internal and external threads, drilling blind and through holes, milling, countersinking, trimming the ends of workpieces and much more. As mentioned above, this type of technique is equally good at different stages of working with the material, and therefore is equipped with a wide range of tools. Particular attention should be paid to the classification of equipment. Type A machines are best suited for finishing small workpieces that require high precision and appropriate spindle tool size.
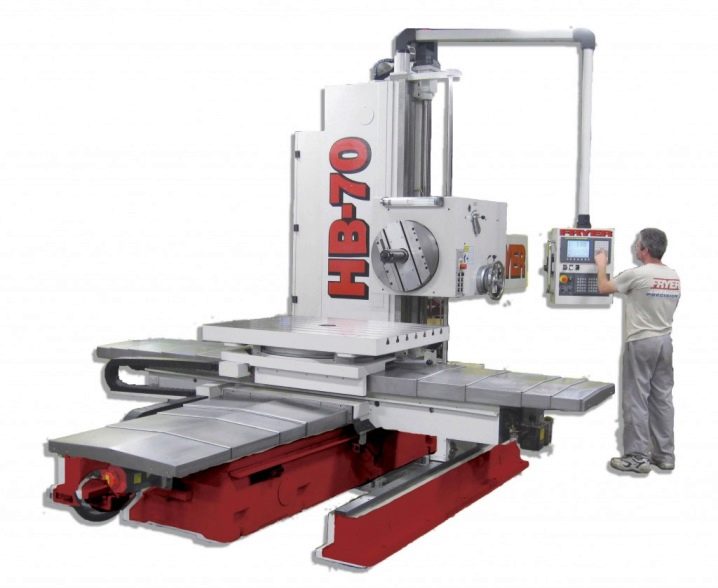
These models can be semi-professional and used in small production for the manufacture of small parts, some components of prefabricated structures. Models of type B are already larger in size and have a considerable size of the desktop, on which a medium-sized workpiece can be placed. Naturally, such equipment is more expensive, but it is more functional and can perform a considerable part of the tasks of type A machines. Even for use at large enterprises, type B units are in great demand due to the ratio of cost, repair capabilities, and also functionality.
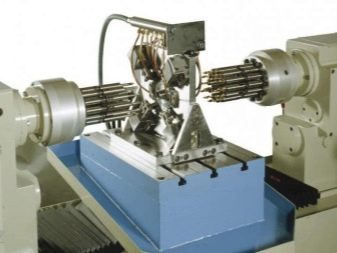
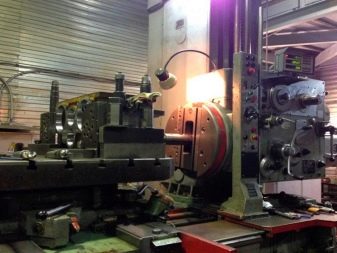
The last type of horizontal boring machines with the C classification is notable for being equipped with devices for mass production of products. This is made possible by the operation of automatic systems, safety functions and an overall increased resource.
Such equipment is used almost non-stop and does not require frequent maintenance, if all structural elements are correctly attached and assembled in accordance with standards.
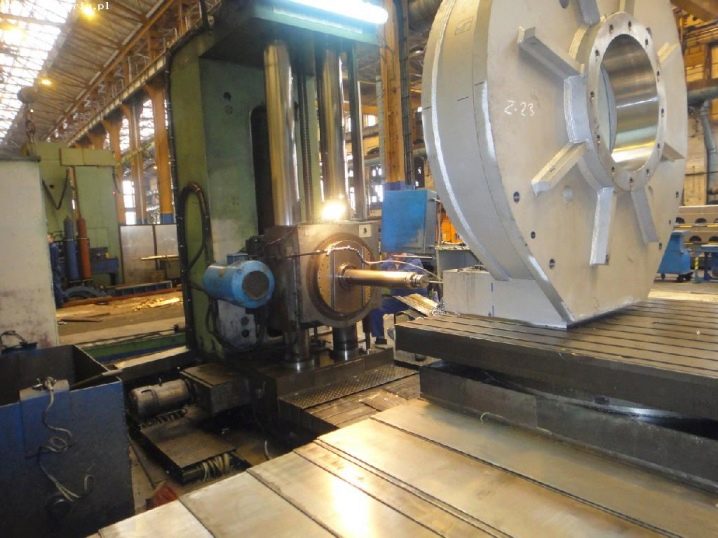
Popular manufacturers
One of the world famous manufacturers of this type of machine is Czech SKODA. Model FCW160 has good reviews from consumers due to its versatility and scopes. This unit is used to create parts and components in large-scale power engineering, transport engineering, shipbuilding, oil industry, and aircraft construction. It is this model that differs from its predecessors in that it has several options for upgrading. The manufacturer's models are most popular in different parts of Europe and are used in medium and large enterprises.
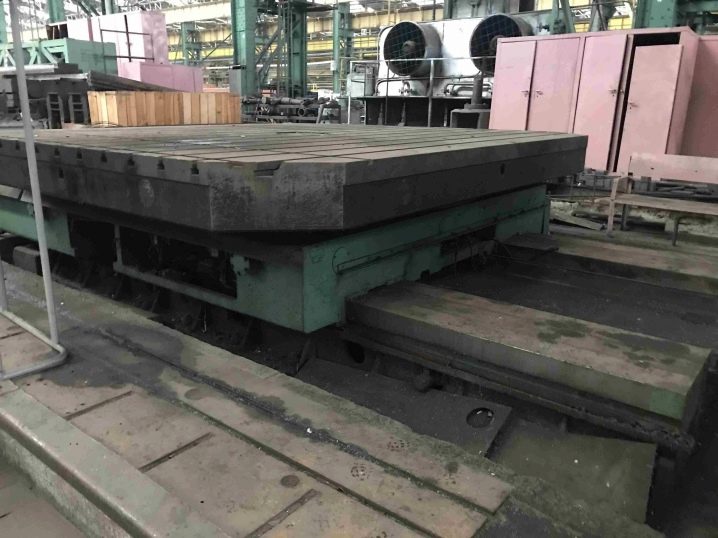
The spindle diameter is 160 mm and its rotation speed is 3000 rpm. The main motor power reaches 58 kW, bush extensions are provided for each of the axles. The headstock is made of gray cast iron, which is one of the best materials in the machine tool industry. It should be noted that in terms of its scope of application SKODA FCW series is used as equipment for mass production, and therefore the operational life of all parts of the structure is extremely long.
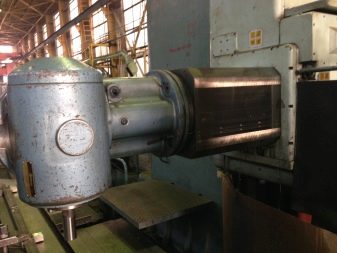

GMW Machines Is a German manufacturer known for its TB110-TB160 series machines. Each of the models has robust cast bases that meet the highest requirements. The working process is very varied, since the CNC system is used. The design of the products consists of individual modules that can be assembled in a fairly short time immediately at the production site. Also, one of the features is the ability to improve the configuration by integrating a variety of systems.
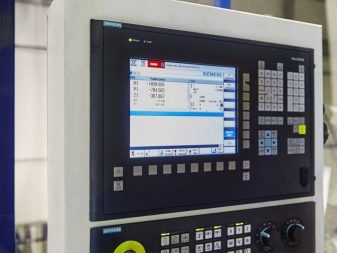
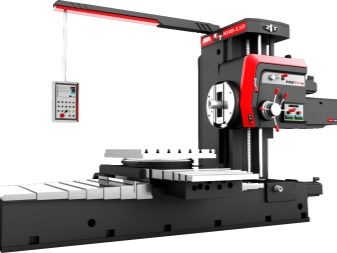
These include linear and prismatic guides, quick-change systems for working tools, the presence of a bearing spindle quill, as well as constructively new rotary tables with different load capacities. Before ordering, the client has the opportunity to independently choose the control system - Siemens, Heidenhain or Fanuc... The most versatile model is TB160CNC with a large table 2000x2500 mm. At the same time, the maximum workpiece weight can reach up to 20 tons. Spindle diameter 160 mm, router 260 mm, speed 2500 rpm.
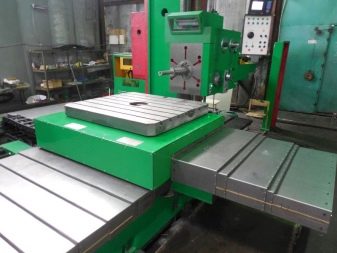
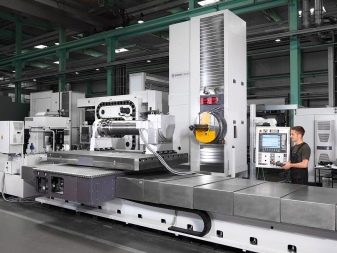
The angle of rotation of the table in all axes and 360 degrees, which guarantees complete processing of the product from all sides and angles. On TB160CNC up to 60 different tools can be accommodated, thanks to which the number of processes performed allows very complex operations with different materials. The power of the main engine is 37 kW, the installation area of the machine is 6.1x7.0x4.9 m, and the weight is about 40 tons. The popularity of the series of these products lies in the fact that they can be modified depending on the area in which they will be used.

Operating rules
Complex technology requires careful handling. This is especially true for machines, as they need to be kept in optimum condition to be as productive as possible. First of all, after assembly, it is necessary to connect to the power supply system. This component is very important, as there are many faults in this part, and all of them can lead to problems.
Do not forget that after some time of use, it is necessary to review and timely replace working tools and materials, the quality of which is gradually decreasing.
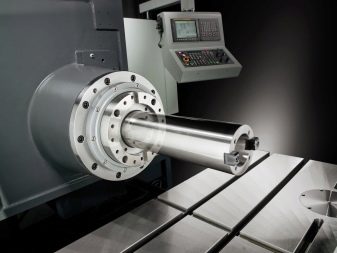
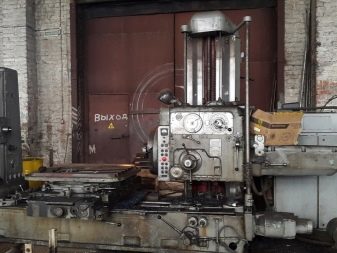
There must be special conditions in the room where the equipment is located. Naturally, work debris, shavings, dust, dirt and the like must be removed. This also applies to production units. They need to be cleaned and lubricated, as well as to monitor the general condition. Periodically, a complete diagnostics of the equipment should be carried out, which consists both in checking the software and control systems, and the design, reliability of fastening parts, assemblies to each other. It is important to understand that even with a small amount of play in any of the undercarriages, the final result may become less accurate. In the context of mass production, this will become a serious problem.
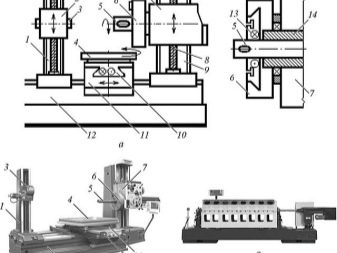
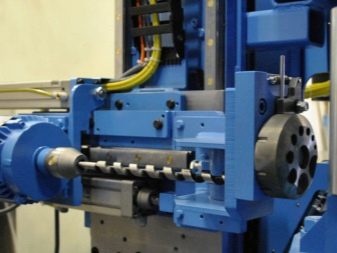
As far as service and repair is concerned, it should be carried out by trained people, whose responsibility is to maintain the optimum condition of the machine. The more complex the unit, the more difficult it is to create all the necessary conditions for its operation.
Safety precautions also consist in the fact that the user must wear protective clothing and other elements in order to use the machine more conveniently. Securing the workpiece, processing it, moving around the table, programming and any other stages must be carried out in accordance with the standards described in the technical documentation. It should be understood that deviation from the indicators negatively affects the result of the work. Do not be lazy to study the documentation, as there is a lot of useful information that will help in the operation of the equipment.
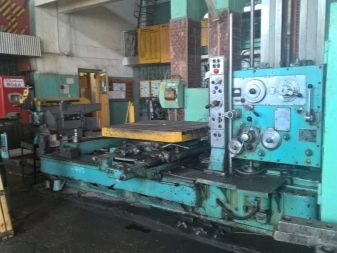
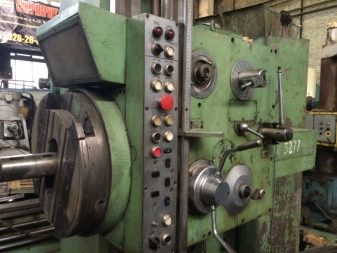
The comment was sent successfully.