Features of wood slabs and their application
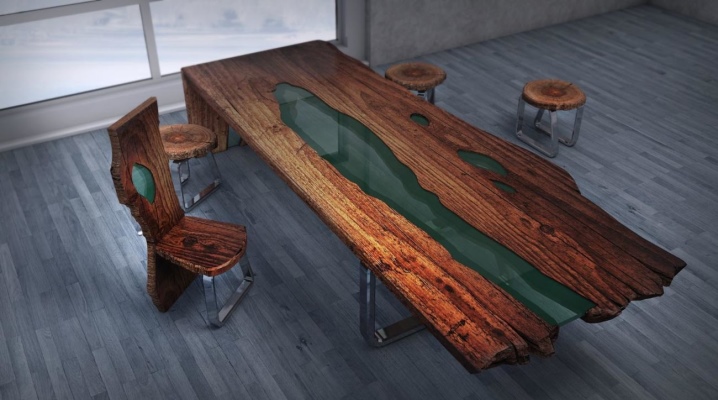
Slabs made of wood: what is it, how can you do it yourself - such questions are increasingly posed by people who are thinking about environmental friendliness of housing. Indeed, completely natural, natural material looks good in the interior, allows you to create frames for mirrors and shelves, countertops and decor items. It is worth talking in more detail about what else is made of wooden slabs, how to dry them correctly and prepare them for processing.






What it is?
The fashion for natural, unprocessed materials came from the USA, where they are known as woodslabs and are in great demand. A slab made of wood is not a transverse, but a longitudinal section of the trunk.
The resulting massive saw cut looks very impressive, depending on the species of the plant, only the pattern and colors of the annual rings change.
The non-standard section of the cut allows for a full disclosure of the natural beauty of the material. At the same time, the slab usually retains a debarked layer along the edge, which is especially appreciated by designers. Obtaining such materials is fundamentally different from other methods of cutting wood. A solid massive saw cut is valued higher than a regular board or timber.



The following characteristics can be attributed to the distinctive features of slabs.
- Complete absence of any unnatural inclusions. Solid wood has a solid structure without traces of gluing and joining.
- The thickness of the slab is in the range of 50-150 mm. This indicator is very important because it affects the strength characteristics of the material.
- Raw edges. They remain natural, with an uneven texture, and a unique pattern.
- Special cut point. Only those areas of wood that are as close to the roots as possible are suitable for slabs. They are more appreciated for their increased diameter, clarity of the pattern, and strength.
- Unique shape. The material is valued higher if the tree trunk itself has a heterogeneous structure, sagging and other unusual elements. Even in the same original slab, the outlines can change as you climb.



Large layers of natural wood are a unique, valuable material that differs from others in its original appearance, strength and durability.
Much in its characteristics depends on the breed that is used to make cuts. Not every option will meet the established requirements and standards.


What rocks are slabs made of?
Not all woods are suitable for making slabs. Most often, these are valuable, rare and expensive varieties. They look spectacular in the form of mahogany slabs with their rich shades of orange, scarlet, burgundy brown. They often have a significant cutting area, are durable, and are not afraid of moisture and decay.



The most expensive and valuable of the exotic species is the rain tree (suar). Its radial cuts are unmatched in durability. The trunks of the soir are distinguished by a spectacular pattern with a sinuous structure and a wide cross-section. Their diameter can reach 10 m, which leaves almost unlimited possibilities for decorative purposes. In addition, other rocks can be used as the basis for the slab.
Among the demanded options are:
- merbau;
- rosewood;
- ebony;
- teak;
- maple;
- oak;
- larch;
- nut;
- elm.



Depending on the choice of material, the craftsmen decide on the method of its further processing. For example, larch slabs are very beautiful, but they contain oils that complicate the subsequent finishing. Walnut is rarely used due to increased drying requirements - it can crack if the temperature is incorrect. Maple is more stable but less decorative.


Where are they used?
The use of cuts of a natural tree trunk is limited only by the imagination of designers. Large-format slabs are used in loft or country interiors, in Scandinavian and minimalist design of spaces. In the classic format, the edge is left untouched and retains its natural texture. When finishing in the style of Liveedge, other techniques are used - cracks and irregularities are emphasized, they are filled with transparent epoxy.


Among the options for using wood slabs, the following design solutions are most popular.
- Furniture. Wooden tables, bar counters, benches are most often made from oak and exotic wood species. Maple slabs are thinner, suitable for the creation of seats and backs of chairs, coffee tables, whatnots. Larch will make a beautiful shelf or window sill.



- Partitions and doors. They are often combined with glass or epoxy resin inserts.

- Decorative panels and consoles. They are placed at the head of the bed or as a stand-alone product serving as a work of art in the interior.
Beautiful cuts of a small diameter tree, attached to the wall, form beautiful and unusual panels that can be framed or left in their natural form.


- Foundations for products. The slab can be used as a stand for a sink in a bathroom, to provide stability to a floor lamp or a lamp. The mirror on the surface of the wooden saw cut is also easily fixed, it looks very impressive. From a small slab, you can make a watch with a dial by attaching hands and other elements to it.


Spectacular tree cuts do not always have the correct shape. Longitudinal elements fit well into the interior in the form of steps of stairs, fireplace shelves. They retain their natural decorative effect, but at the same time remain quite functional.
True, such design delights do not fit into all interior styles.


Manufacturing technology
You can make a slab from a tree trunk with your own hands, but only with proper preparation and accurate calculation. The material from which beautiful cuts are made is mined in the mountains or wild forests. The most valuable slabs, which can later be processed at home yourself, are obtained from trees over 50 years old, with a significant trunk diameter. They are made to order, sometimes you have to get a special permit for a saw cut.
The more knotty, inhomogeneous structure the trunk has, the more decorative the saw cut will be. Variants with diverging elements, forks, twisted sections are valued higher. The richness of the color gamut of the material also directly depends on the choice of the base. The most interesting palette is the cuts obtained in spring and summer. The bark from such trees falls off by itself, but it can be easily removed in advance.


Learn more about how to properly make a slab from a solid barrel by processing on site or in a workshop. The step-by-step instructions will help you navigate correctly in the sequence of actions, it will be useful for novice masters.
Transportation
The logs are rolled onto a special platform, the distance between the ramps is adjusted so that the load is located as securely as possible, without losing balance. Transportation is carried out using large-tonnage trucks and lifting equipment. Small pieces can be rolled onto the platform with a cable winch.The position of the log when being pulled onto the transport platform must be strictly parallel to it.
Secure the workpieces with wooden wedges and tie-down straps, preventing them from rolling or shifting.

Saw cut
This step is necessary if the cut or sawn-off workpiece is too large, weight. In this case, the material is divided into more compact sections at the place where the timber was mined.
The work is carried out using a mobile band sawmill. Subsequently, the material is transported to the place of further processing.

Dissolution
The round log is dissolved into separate slabs 5-15 cm thick. The fastest and easiest way to do this is on industrial equipment, but you can do without it. A mobile sawmill is easy to organize on the basis of a high-power chainsaw. At the same time, the breaking up of logs can be done directly at the place of harvesting, making the transportation of the material much easier and more convenient.
In order for the log to turn into slabs, it is sawn into pieces of equal thickness, making an exception for the core area. Here the standard size is doubled to reduce the risk of material warping. The individual slabs can be spliced together with epoxy glue to obtain blanks of the desired width.
The choice of the dissolution method depends on the subsequent processing of the wood.
- For ready-made slabs. At the log, the middle part with a width of 100 to 120 mm is separated. The rest is dissolved into layers of 5-10 cm. Finished layers can be sent to drying.
- For gluing. In this case, the debarked part is sawn off from 3 sides of the log. The rest of the workpiece is unfolded in the same way as in the first method. Then the layers are joined so that the smooth sides touch, and the debarked ones are located on the outside.

Materials prepared by any of these methods are sent to special chambers or dried naturally.
Drying and stabilization
Most natural wood is susceptible to warping when exposed to weather conditions. In addition, it contains natural moisture, which also affects the overall condition of lumber. Since the main period of timber harvesting is spring, the resulting layers turn out to be very damp, it is unlikely that it will be possible to dry them correctly without additional tweaks. The resulting stress leads to warping, cracking of the array.
Pre-treatment of the material with stabilizing compounds helps to reduce the risks of splitting of the workpieces. Very wide slabs are sometimes cut from the rear. This technique significantly reduces the tension in the wood fibers.
Drying of slabs can be carried out in the following ways.
- In vivo. In this case, the material is simply protected from contact with sunlight and other heat sources, placed in a dark room with good ventilation. Due to the air exchange, moisture from the wood gradually evaporates. Slabs are stored in stacks or on racks. The drying time can be quite significant, much depends on the type of wood, its initial moisture content.
- In the cells. Special drying equipment removes excess moisture from wood using IR-emitting lamps or closed booths that maintain a given temperature regime. During the drying process, the material may change color.


The method for removing moisture from wood is selected based on the size and characteristics of the workpieces. Large-format options are dried in an exclusively natural way. Correct stacking allows you to create conditions under which the boards will not change their geometric parameters.
The only drawback of this method is the length of the process: in 1 year the wood dries only 25 mm thick, a 50 mm slab will take at least 24 months to reach a moisture content of 10%.
Upon completion of the dehumidification process, the slabs are further processed. It is possible to exclude damage to the material by applying a protective coating to it. For wood subject to mechanical abrasion, oil-based impregnation is well suited. You can also use polyurethane varnish, epoxy as a coating. For surfaces that are not subject to significant wear, a protective wax is suitable.

The comment was sent successfully.