All about professional flooring НС35

The article briefly describes everything about professional flooring НС35. The dimensions of the profiled sheets and their technical characteristics are described. The step of the lathing is indicated, the weight of 1 m2 of galvanized profiled sheet, recommendations are also given on the choice of a seal in a particular case.
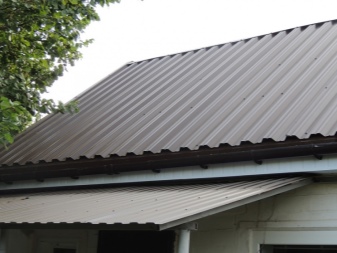

Composition
The popularity of professional flooring НС35 is largely due to exactly what it is made of. The basis for this material is steel with an outer zinc layer. Polymers of various types are necessarily applied on top of the base. For your information: when they talk about a professional sheet or a metal profile, then, in fact, they mean the same product. As in the case of metal tiles, it is possible to achieve a complete coverage.
There are no differences between corrugated board and metal tiles in terms of chemical composition. But there is a difference in how the wave is drawn. Its placement on the surface of the sheets is also different. It is also worth considering that metal tiles are more like traditional ceramic tiles. But the corrugated board is closer to the classic slate sheet.



Specifications
A modern galvanized profiled sheet is made according to the standards of GOST 1994 or 2004. Therefore, there can be no doubt about its high bearing capacity, as well as the long service life of the surface. Normative acts provide for the use of steel grade 220. However, in some cases, the use of steel 01 is also permitted. The wave height, as the name of the finished product grade implies, is 35 mm; they are all exactly the same and resemble a trapezoid.
Additional reinforcement with stiffeners is always provided. They are placed along the entire length of the structure. It is understood that such "edges" are placed both on the waves and in the intervals dividing them.
Correctly selected alloys guarantee high strength and long service life. In general, this product does not cause any complaints.

Dimensions and weight of sheets
Typical working width for a metal profile of the HC35 group is 1000 mm. Important: do not confuse it with the maximum overall width, which is 1120 mm. It should also be taken into account that in some sources the working width is 1080 mm. Apparently, this is due to the nuances of the products of different companies. The permissible working length (in length) is 14 m, which is quite acceptable even when covering large roofs. The thickness of the profiled sheet ranges from 0.5 to 0.8 mm. An increase in it predictably leads to an increase in the load on the base. However, this also increases strength, which forces us to seek an optimal balance.
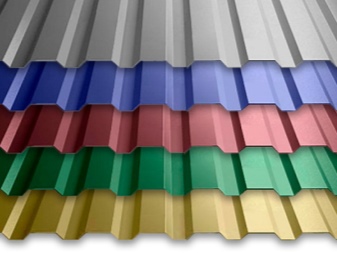
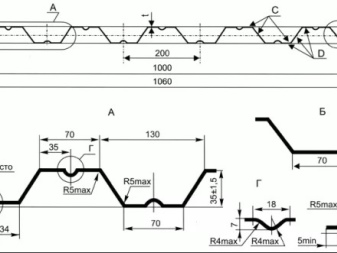
It is sometimes difficult to make the right choice without consulting specialists. It should be noted that only sheets no longer than 6 m are found in serial sale; products measuring 6.1-14 m are made only for individual orders. Looking at the thickness of the finished sheet, the mass of 1 m2 can be 4.5 kg, and it can reach 8.5 kg. This allows you to choose a product with good weight characteristics. By default, a trapezoidal profile is used. The distance between the reinforcement ribs is 215 mm.
Other technical properties are of interest mainly to professionals.

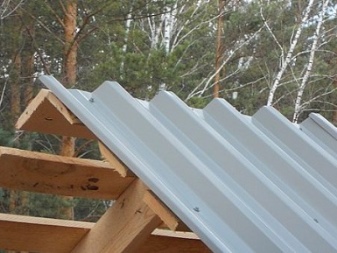
Applications
The professional sheet of the HC35 group is universal. It is not only a roofing material; it is also used to decorate fences and make partitions inside rooms. Some experts choose such a solution for floors in capital houses.Most often, the metal profile is placed on the roof with a slight slope. Too steep a bevel makes you abandon such an idea.
In some cases, HC35 is used to cover capital garages. The motivation is quite transparent: the material is inexpensive and at the same time quite reliable in terms of loads. It is worth noting that such a metal profile, in addition to work for the roof, can be used as a fence for construction sites. In some cases, it is also taken as a base for formwork. Finally, it is also possible to use it as a façade material.
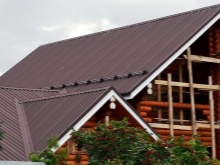


Styling tips
Normally, the leaf lock should look “down”. It is very important to arrange the frame, to which the sheet material on the roof is attached. Mostly such frames are formed from wood. To obtain them, a beam of 4x4 or 5x5 cm is used.In some cases, they prefer to take edged boards with a thickness of 3.2 and a width of 10 cm.
The stuffing is done strictly at an angle of 90 degrees in relation to the rafters. The arrangement of the counter-lattice is also necessary. This element allows for a ventilation gap. A well-made counter grill makes it possible to exclude the appearance of condensation. With a small slope angle, a solid frame should be used, but this is not very suitable for HC35.

The pitch of the lathing of the standard (not solid) type for the profile ranges from 20 to 50 cm. But in some cases, you can use a sparse crate, the distance between the nodes of which is 60-100 cm. Only professionals can accurately calculate these parameters. They can take into account the strength and main direction of the wind, key technical parameters. The higher the snow load, the steeper the roofing should be. The installation instructions assume that the battens must be treated with an antiseptic. Thanks to him, rotting of the tree is excluded, the period of operation is extended. Sometimes it is possible to fasten the corrugated board to a metal crate.
The metal layer should not exceed 0.2 cm. Otherwise, the rafters will be overloaded.
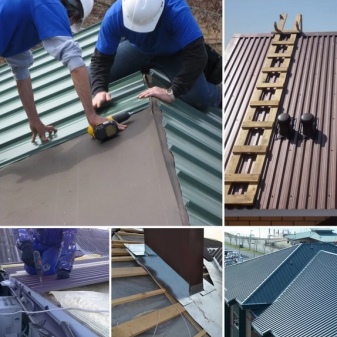

Joining sheets to thick beams is technically possible. However, this often turns into excessive labor intensity of work. Perhaps the most important stage is the direct joining of the flooring and the substrate. It is secured by fastening with self-tapping screws. Without understanding this procedure, there is nothing to take to work. Using simple self-tapping screws is hardly reasonable. Hardware of a special design is required. Their cross-section ranges from 0.48 to 0.63 cm, and the length varies from 2 to 25 cm. A special seal, obtained on the basis of neoprene rubber, turns out to be an obligatory feature of such fasteners. It ensures that there are no leaks at the connection points.
When using simple flat screws, the sealing elements are additionally placed under their heads. You cannot use fasteners devoid of branded brands of manufacturers - it will almost certainly let you down. Most often, 1 sq. m use 6, 7 or 8 hardware. The profiles must be fixed strictly in the lower waves in order to guarantee a tight fit and reduce the risk of leaks. The overlap within the strip is 1-2 waves, in the aisles a run of 10-20 cm is recommended.



At the top and in the lowest segment of the roof, you need to attach sheets on each wave. Mutual joining is made with standard rivets. They can be driven in with a standard hand pistol. Important: when working with self-tapping screws, you should look that they go strictly at 90 degrees to the sheet plane. The slightest deviation means the appearance of leaks, and after them - and serious leaks in wet weather.
Installation accuracy is especially critical at the time of fixing to a run; the screw is then taken the longest, and it bends extremely easily. Problems can also arise when attaching the ridge to the crate. It can be done only through the upper waves. Any other option means a loss of density.On a non-steep roof, under the undulating areas located below, a seal is placed, which guarantees protection even in heavy oblique rain.



However, problems can also arise when the sheet is cut incorrectly. Straight cuts are carried out neatly with scissors for metal. To cut the workpieces correctly with the formation of oblique cuts, electrified jigsaws are used. But it is not recommended to use a cutting disc tool with powerful revolutions. No matter how good the Bulgarian is in itself, but with such a job she does not cope well.
It is often forgotten that after some time after the installation of a corrugated roof, its revision will be required. When 8-12 weeks have passed, it is useful to stretch the screws again. This technique eliminates the loosening of the fasteners.
Possible shifts are often provoked by adjustments during the installation process, but appear later. They can also be caused by thermal deformations.

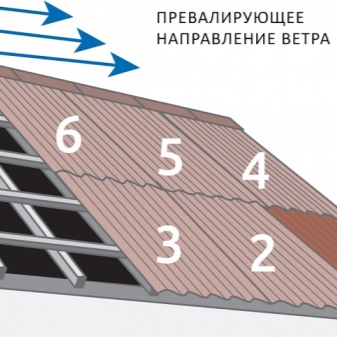
Whatever subtleties and nuances appear during work, it must be remembered that the profiled sheet is normally laid in a plane parallel to the cornice. The cornice itself is trimmed in advance, and when laying, the sheets are brought out behind it in the manner of an overhang. Before screwing in any additional self-tapping screw, you need to thoroughly think about whether this will violate the integrity of the coating. Important recommendations:
- use, whenever possible, self-tapping screws from foreign manufacturers with boring barbs;
- use a membrane that retains steam and liquid water (it is mounted from the eaves to the ridge, and not vice versa);
- nail this membrane onto nails with a large head (gap - 0.2 m);
- lay waterproofing with an overlap of 0.1-0.15 m (in addition, a sagging section of 0.02-0.03 m is left between the rafters);
- provide openings for ventilation closer to the ridge;
- mount the sheets so that there are depressions at the edges (there should not be peaks there!);
- exclude nailing the corrugated board with nails (often the wind tears them off);
- pre-mark the sheets and select their individual positions for them.

The comment was sent successfully.