Decking MP20: dimensions and characteristics
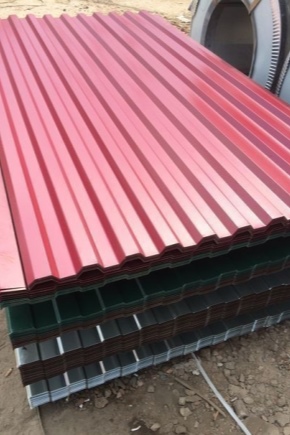
The use of MP20 corrugated board remains a very promising business. But that is why you should thoroughly study the information about the dimensions of the profiled sheets, the technical characteristics of galvanized sheets for the roof and fence. It is imperative to analyze the lathing step and other information required to install the sheets.

Description and scope
Decking MP20 has been a very popular solution for cladding various surfaces for many years. It is used for both the roof and the fence; naturally, this material is still used successfully for the design of facades. Such products are eagerly bought by:
-
private developers;
-
small construction and repair teams;
-
large construction and repair firms;
-
improvement services, management companies.

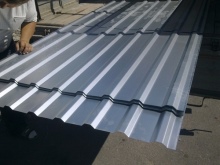

In the descriptions of manufacturers, the emphasis is on the harmony of valuable qualities, namely: lightness, pleasant appearance and a comfortable price for the consumer... There is a nuance in decoding the marking of the roofing profiled sheet: the number 20. The fact is that the actual wave height is 1.8 cm, and "20" is the result of rounding. The profile itself has a pronounced asymmetry, that is, a sequential change of relatively narrow and widened shelves.

The letters "MP" indicate that this is a metal-polymer type product. Various partitions can be made from it. A separate area of use is the construction of medium-sized buildings: temporary, as well as periodically used, for example, sheds or utility blocks. It is worth pointing out such a characteristic weakness as a high susceptibility to sunlight.
Because of it, it is impossible to use the professional sheet fully in the southern regions of the country.



How do they do it?
Metal profiling is carried out by deformation without heating... This approach guarantees the strengthening of the structure. Since the MP20 is always galvanized, corrosion problems usually do not arise. Galvanizing is done in a hot way, which has proven itself better than other options. Polyester is applied to the profiled sheet, which provides an increased decorative effect.
If the coating is made around the entire perimeter of the sheet, then it is marked as "AB". For one-sided application of a protective layer, use the index "A". For the production of a profiled sheet, only specialized equipment is used. The initial raw material is thin rolled coils, which usually already have a continuous layer of polymer coating by default.
Work begins with unwinding the roll: of course, most often not by hand, but using special machines.

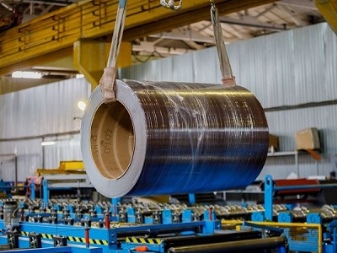
Further:
-
the material is driven through a bending profile machine (it is at this moment that the required wave geometry is formed);
-
the workpiece is cut to predetermined lengths;
-
the product is sent to the warehouse, where it is properly packed and stored (or immediately handed over to the customer).
Naturally, there are no more factories left where all production would not be as automated as possible. Any technological manipulations, including the transition from one roll to another, are carried out as part of a continuous cycle. This approach increases productivity and reduces costs. What is important, at the same time, a very high quality of the finished product is ensured. And no less important is the availability of a wide range of lengths with a small step, as a result of which losses for residues are minimized.


Specifications
Sheet sizes
The usual thickness of the profiled sheet starts from 0.4 mm.Serially produce products up to 0.8 mm. And you can also find products with a thickness:
-
0,45;
-
0,5;
-
0,55;
-
0,6;
-
0.7 mm (these are the most basic, widely used positions, and among them the material with a layer of 0.4 to 0.55 mm prevails).
The usable width is 1100 mm. Sometimes the term working width is used - this is the same indicator. The overall width is 1150 mm. This is the name of the total distance separating the edges; another 50 mm goes to the so-called lock, which is closed when the sheet overlaps. The length can range from 50 to 1200 cm; within this framework, you can order any size, but the most practical product is no longer than 400 cm.
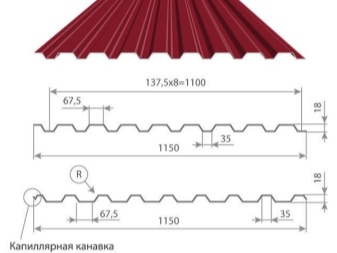
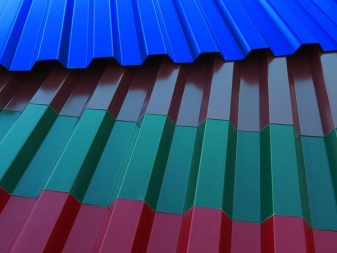
The weight
The weight of 1 m2 is predictably dependent on its thickness. In most cases, this figure varies. from 3.8 to 7.3 kg... An increase in the metal layer increases its protective properties. But at the same time, the load on the supporting structures increases. With a layer of 0.4 mm, the average weight will be 3.87 kg - more precisely, it can be said only taking into account the characteristics of the products of a certain manufacturer.
Other averages:
-
for 0.45 mm - 4 kg 210 g;
-
for 0.5 mm - 4 kg 720 g;
-
for 0.55 mm - 5 kg 150 g;
-
for 0.6 mm - 5 kg 570 g.


Other
Bearing capacity is a very important characteristic. - in other words, the level of load that this coating can tolerate. It makes no sense to give ready-made universal numbers. The main thing for the consumer is that The MP20 will withstand significantly more snow than products with a less pronounced relief. This brand is the minimum acceptable for use in the middle lane. But in especially snowy regions, even it may not withstand the created conditions. In this case, it is necessary to choose an even more durable and stable material.
Coating color can be flexibly varied... You can easily pick up both gray and black, and colored professional sheet. This product is subject to a special GOST 24045, approved in 2016. The standard prescribes the use of a color corresponding to the RAL catalog, or another approved catalog in accordance with the established procedure.
The standard indicates that by agreement between the supplier and the customer, protective and decorative means not specified by the standard may be used. Then it is required that they are no worse in their qualities than standardized ones (which is confirmed by the test report). The standard specifies indicators of deviations from geometry. An approximate basic configuration is also described there.
And also it is allowed to apply alternative technical conditions.


Types of coatings
It is the coatings applied to the metal that provide an exceptional level of resistance and durability. The basic point is always the application of zinc to ferrous metal. It is he who provides increased anti-corrosion characteristics. Zinc is additionally passivated. It is a coating with an oxide film that enhances the corrosion resistance.
The primer must be applied. It enhances the adhesion of other materials and improves the adhesion on top of additional polymers. The total thickness of the polymer layer is 25-200 microns. The decision is made in accordance with the type of use of the material and the category of the polymer mixture.
A special protective varnish is most often applied to the inner edge of the profiled sheet.


For cheapness, polyester coating is distinguished. This is the most common variant in the world. Polyester is UV resistant and will not fade as quickly as other options. Therefore, the original brightness of the color will be preserved for a long time. The advantage of such a coating is that it effectively prevents corrosion and perfectly tolerates strong temperature fluctuations.
But polyester also has a significant weakness - it is always applied in a thin layer. It will not be difficult to scratch it even with weak impact. Damage can occur during transportation and installation. That is why it is necessary to work with a professional sheet of this type as carefully as possible. It is categorically impossible to walk on it.
Matte polyester differs from the usual not only in appearance.It is always less even and therefore more applied than a glossy polymer. As a result, the overall service life is significantly increased. Extended decorative options are also useful.
Matt polyester can be used to reproduce the look of a wide variety of materials, even natural stone.



Also in demand professional sheet with pural... The time of its use reaches 50 years. The resistance to the application of mechanical force is beyond doubt. Such a coating will help out even when used on the sea or ocean coast, in the air saturated with salts. But it should be noted that the pural still becomes less bright over time, and its cost is pretty upsetting.
Plastisol is also noteworthy. This protection is supported by the fact that it is always applied with a layer of at least 200 microns. Therefore, the resistance to mechanical damage is at a very high level. But the resistance to heating in the bright sun is not too high, and this greatly interferes with the spread of such a coating.
Problems are also caused by rapid fading, due to which you even have to constantly use the lightest colors.


Mounting
But standard specifications and even coatings are only half the battle. It is much more important in practice to know exactly how to lay the MP20 profiled sheet, how exactly they need to cover the roof with their own hands. The typical pitch of the lathing is determined by setting:
-
bearing capacity of a particular material;
-
calculated loads on it;
-
gaps between rafters;
-
roof slope level.
An ordinary pitched roof may well be equipped from the same MP20. The installation instructions say that the sheathing boards should have dimensions of 3x10 cm. This material is suitable, however, only if the gap between the rafters is not more than 100 cm. Otherwise, the sheathing itself should be thicker and more massive.
You can attach the MP20 both to the left and to the right along the slope.


Sometimes they equip slopes with complex configuration... In this case, it is necessary to work on the basis of a preliminary calculation. It is even useful to lay out the sheets schematically on paper. For roofs with a drainage system, the overhang along the eaves should be 4-6 cm.
The passage of ventilation, and sometimes the chimney, requires the use of a passage element. The geometry of such products varies greatly as needed. It is not allowed to equip passages made of metal thinner than 0.1 cm.For chimneys, this figure should be at least twice or three times more. The initial sheets are leveled along the ends and cornices, then they are fixed with one self-tapping screw near the ridge.
Then you need to put the next element and level it. The sheets are also fixed between themselves with self-tapping screws. Having connected 3 or 4 panels, you need to immediately trim them along the cornice. Next, it is attached to the crate. You can continue to work by attaching the sheets first to the original sheets, and only then to the crate.


It is not essential to introduce fasteners at the top or at the bottom of the profile. It rather depends on how much the roof is sloped. Top mounting is carried out at an inclination of less than 25 degrees. The number of self-tapping screws is determined simply: near the cornice they are driven in every 30-40 cm, and the subsequent rows are screwed in according to a checkerboard pattern every 100-150 cm.On the pediment, the gap is 50-60 cm, on the longitudinal overlap, the fastening goes with a step of 30-50 cm; total for 1 sq. m is consumed from 7 to 10 hardware.
When screwing the self-tapping screw along the top of the profile, it is impossible to pull it over, otherwise dents may form. Correctly joining the corrugated sheet on the roof means maintaining a certain overlap. When the angle is less than 15 degrees, the surge is 2 waves. But on a relatively steep roof, the slope of which is 30 degrees or more, you will have to bring one sheet over the other by only 10-15 cm.


When arranging a cornice, several tasks are solved at once:
-
how to make everything as aesthetically pleasing as possible;
-
how to equip a drainage system;
-
how to maintain normal ventilation under the roof.
Always use the ridge seal. This element itself is nailed on both sides on additional sheathing boards. There must be a distance of at least 100 cm between the end of the waterproofing film and the top of the structure. We are talking about the film that lies on the legs of the rafters; the film along the crate should overlap the lower film layer by at least 15 cm. The overhang of the corrugated board along the gable is from 5 to 7 cm; it is recommended to cover the end of the roof with a wind bar.


The comment was sent successfully.