What is hydrosandblasting and how to choose it?

What is hydrosandblasting, as well as how to choose it, is a rather important topic for novice craftsmen. This article describes the features of a water sandblaster and the nuances of its choice. A separate topic is the rules for working with equipment.

Peculiarities
Hydro-sandblasting, it is also water sandblasting, it is also a hydro-sandblasting machine - one of the types of devices for supplying an abrasive jet when cleaning various surfaces. The specificity of such equipment lies in the fact that the jet is formed here due to the supply of water.
This contributes to less dust formation than when working with airborne counterparts.


Therefore, we can say that sanitary and epidemiological standards are fully observed, which prohibit working with quartz sand without removing dust. Besides, surfaces treated in this way shrink less and are better cleaned.

For cleaning, a combination of quartz sand with water is mainly used. Other abrasive materials are in much less demand. An important condition for the normal operation of the system is the unhindered pushing of the mixture with water under pressure through the nozzle.

Another advantage of premixing the abrasive with water in the chamber is the ease of handling large parts and hard-to-reach areas. Sometimes it is possible to reduce the consumption of abrasive by 30-40% when compared with traditional dry processing methods.
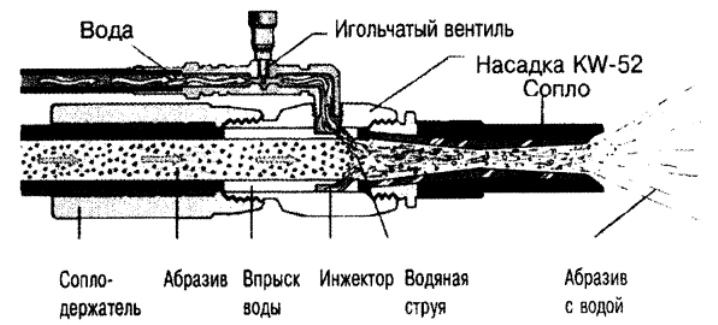
In addition, cleaning surfaces with a water jet is a rather gentle procedure for the material of parts. Heating of the treated areas is guaranteed, so they do not deform, and their appearance does not change.
Conclusion - this technique is excellent for processing softwood.

Also worth noting:
-
almost zero risk to operator health (due to the absence of dust);
-
obtaining a slightly rough coating (the adhesion of the surface improves, which is good, for example, for its subsequent painting);
-
effective work with brick, natural stone;
-
regulation of work intensity;
-
the ability to wash out caustic soda and other detergents;
-
guaranteed removal of dirt, rust, scale.

Small particles of sand knock out the dirt. The surface takes on a matte look. It is much better to apply a primer, varnish or paint on such a base. Additional polishing is greatly simplified. It is hydrosandblasting that makes it possible to obtain samples for studying the macrostructure of alloys. In the industrial sector, many parts cleaned in this way can be ground without long pre-etching.
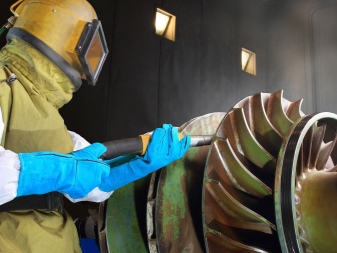

However, there are also disadvantages:
-
it is impossible to work with hygroscopic materials;
-
water will spray;
-
puddles will appear on the floor.
The water pressure in the jet can be from 2 to 7 kg / cm2, therefore it is unsafe to work without special suits. Even when using personal protective equipment, additional safety measures must be taken.

There are also such disadvantages:
-
adhesion of wet grains of sand makes it difficult to assess the degree of cleaning;
-
the appearance of rust (can be prevented by the introduction of phosphoric acid and some other additives, but this requires additional costs);
-
penetration of water into microscopic cracks allows it to remain under the paint and varnish layer and activate oxidation;
-
low productivity (dry sandblasting allows you to do much more work per unit of time).

Species overview
In addition to the difference in the form of nozzles with water (in shape, performance), there are several options for hydro-sandblasting machines for the method of handling abrasives.
-
Suction. The substance is captured and transferred to the nozzle. Basically, this technique is suitable for removing old paint.

-
Vacuum. There is a possibility of re-collection, which increases the cost and complicates the design.

- Pneumatic. They are used mainly in industrial conditions due to their great complexity and considerable dimensions. Such equipment develops high productivity, it will be able to process hard-to-reach areas of surfaces.

Nuances of choice
Water sandblasting machines are either stationary or mobile. The required size of the structure is determined by the dimensions of the workpieces and workpieces. Predictably, builders and repairmen, as well as organizations caring for pipelines and other linear objects, try to take mobile equipment. It is worth paying attention to the size of the nozzle cone, as it determines the performance. It is also helpful to take a close look at reviews and check the reputation of suppliers and sellers.

Application rules
When working with hydro-sandblasting, the pump takes liquid from the reservoir. Connecting it to the water supply is prohibited. This inevitably turns into a water hammer that destroys the entire plumbing. And also it is necessary to ensure that the pressure compensating air flow is stable. In box-type chambers, although small parts are processed, they are processed in rather huge batches.

In this case, operators are monitoring the progress of work through the control glass. When working with an open method, it is possible to turn on hydrosandblasting only when using special suits, safety shoes and goggles.
Waterjet processing is carried out using:
-
glass beads;
-
ordinary and quartz sand;
-
aluminum oxide;
-
soft blasting.

It is strictly forbidden to direct the waterjet jet at yourself and other workers, as well as at foreign objects, except for the workpiece being processed. The composition of the working fluid is selected in accordance with the task to be solved. To reduce the corrosiveness of water, sulfo compounds are used. The optimal amount of abrasive suspension in the liquid is selected experimentally, but in most cases it is from 20 to 30%.
The length of the nozzle should be chosen in such a way as to ensure the optimal acceleration rate of the mass and maintain the specified feed angle.
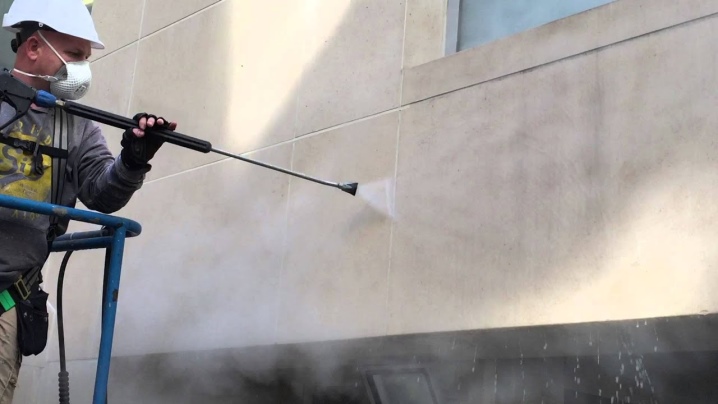
It is necessary to carefully select the processing mode. By varying the proportions of the components in the suspension, it is possible to carry out rough cleaning, and fine grinding, and preparation for staining.
Before starting work, it is required to carefully check the serviceability of all equipment, the tightness of the hoses and the accuracy of their connection. First of all, an idle start is carried out to make sure that the equipment is working properly. Only the next step can be a full-fledged processing of the parts or surfaces themselves.
The comment was sent successfully.