Frame profiles made of MDF
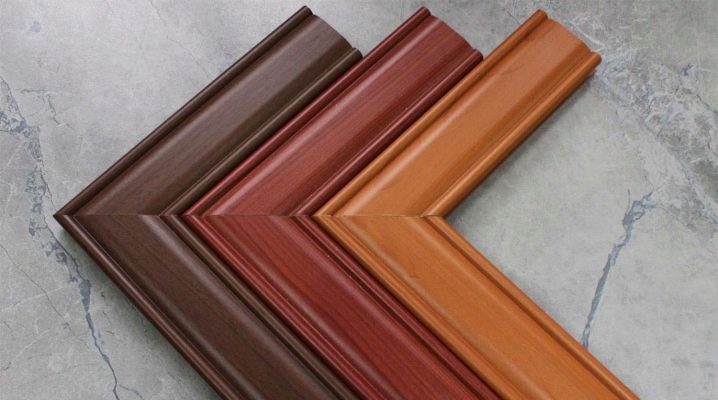
Frame profiles made of MDF are a very expressive option for furniture decor. There is a profile for dairy oak, wenge and other colors for facades. Additionally, one should take into account the dimensions of such structures and how they are produced.
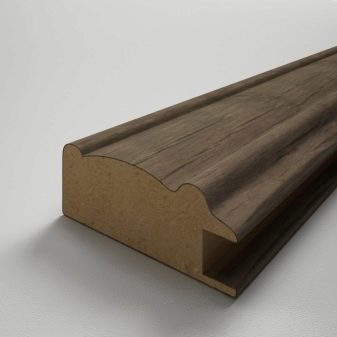
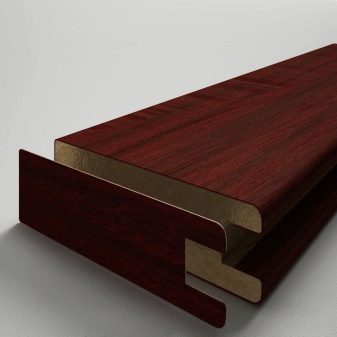
Advantages and disadvantages
The level of strength of such a material is only slightly less than that of a first-class natural solid wood. It is not serious to compare weak chipboard with it in this indicator. The strength advantage means a long service life and reliability of the resulting structures. There are no air pockets in MDF, and there is no danger of drying out. The dimensions given in production are maintained for a long time without any risk.
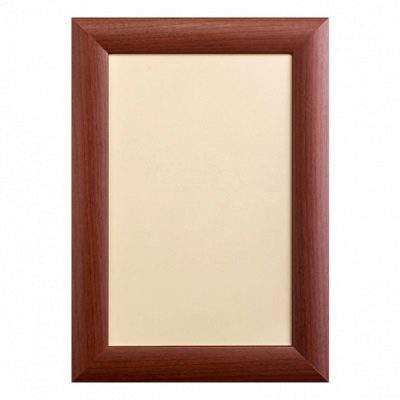
Finished products are relatively inexpensive. From the aesthetic point of view, they have no complaints. You can widely combine colors and textures, other performance details. Combination with other materials also has no limits. Products of non-standard dimensions are obtained without any problems.
However, even such a seemingly top-notch solution has objective flaws. First of all, MDF will have to be operated in strict compliance with the basic rules. The degree of reliability, especially in kitchens and other humid places, is determined not so much by the quality of the material itself and its assembly as by the additional applied coatings. In addition, when the protective layer is broken, the ingress of liquid quickly leads to material degradation.
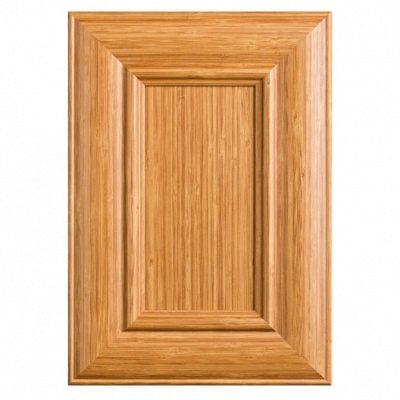
Another nuance - you need to carefully understand the resistance of a particular batch of MDF and its coating to dirt, dust and grease.
Profile types
The main part of the production is made:
-
with a “quarter” sample;
-
with 4 mm grooves;
-
with 8 mm grooves.
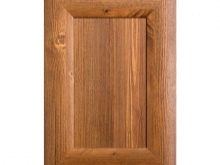
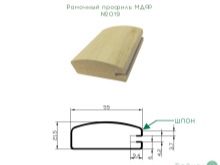
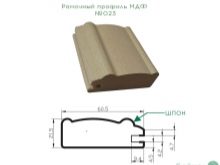
Additionally, panels are distinguished:
-
wall;
-
ceiling;
-
outdoor;
-
one-sided;
-
bilateral;
-
sheet;
-
wall types.
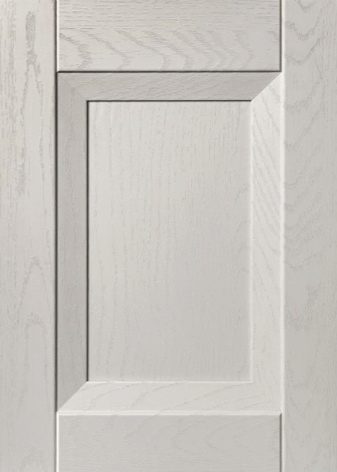
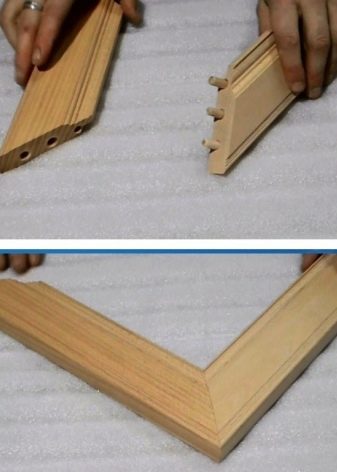
There is a difference in the technology of obtaining:
-
one-piece pressing (the product is perfectly smooth on either side);
-
treatment to increase moisture resistance;
-
lamination (additional film after normal pressing).
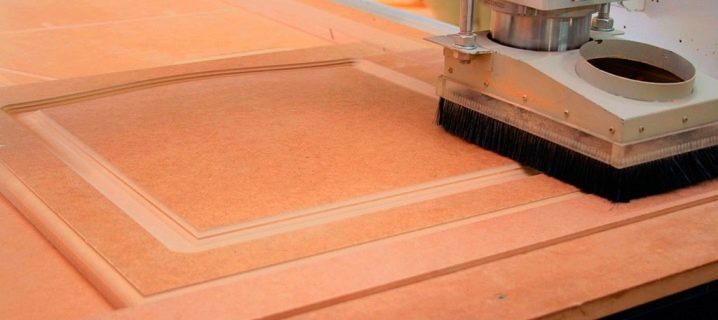
Coating options
MDF for framed facades can be covered with various facing materials. The finishing film is considered the most profitable. However, such a paper layer will not withstand rough mechanical stress. With long-term use, it will also show itself badly. Natural veneer looks just like natural wood.
But he loses to her in terms of resistance to deformation. The external environment can also easily damage the veneer. The cost of such structures is often overstated. The best choice is film polyvinyl chloride. In terms of quality and practical properties, this material is usually not satisfactory.
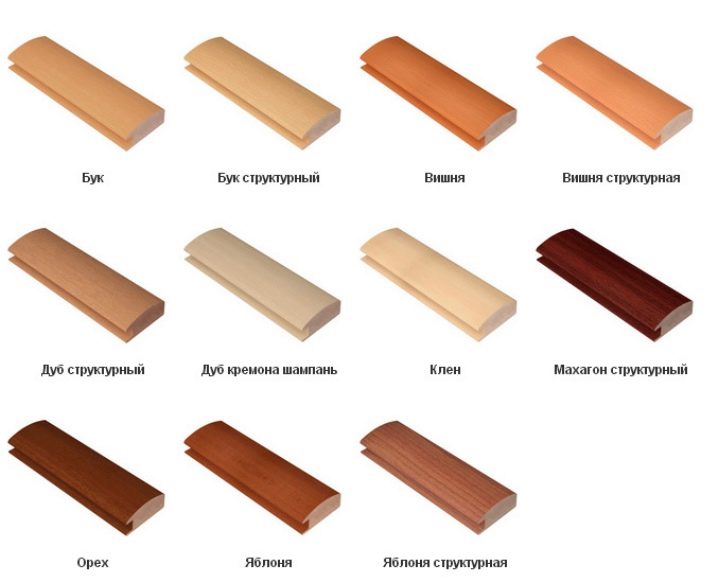
In its pure form, the profile is painted in a gray-brown tone. Along with it, the density and homogeneity of the entire mass are clearly visible on the cut. In addition to applying various coatings, MDF can also be painted. Since this material is very strong, it is bent and transformed into a variety of geometric shapes.
The radius profile is mainly needed for decorative applications, for decoration of facades.
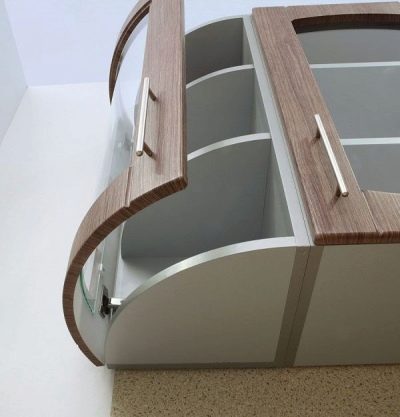
The U-shaped version is needed for door and window blocks. It is also used when installing panels on walls and ceilings. Such designs are used to create rectangular frames, where the filler is then inserted. Further, the filler can be painted, covered with veneer or foil. Overhead models are used for finishing furniture and its facades; the geometric shape of such profiles is quite different.
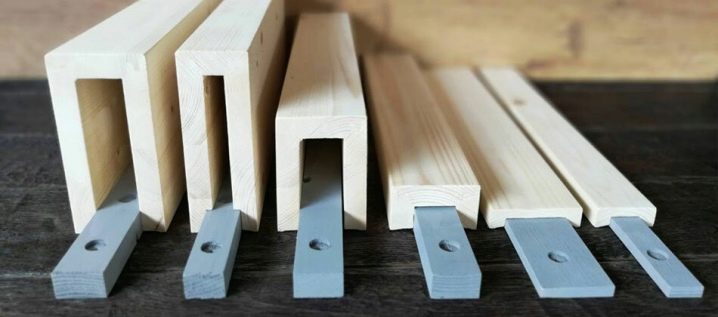
Overhead profiles are used to do:
-
dressers;
-
pedestals;
-
beds (it has both a decorative and a protective role).
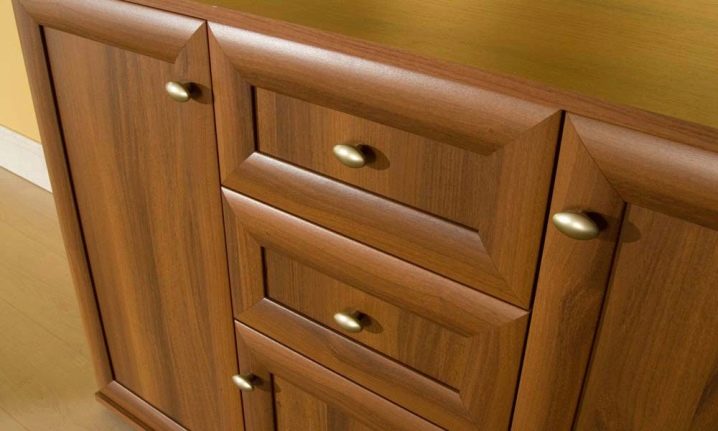
The appearance of the MDF profile can also be determined by its color. There are options such as:
-
milk oak;
-
beech;
-
white wood;
-
wenge;
-
sonoma oak;
-
dark cherry;
-
pear;
-
ash shimo (dark or light);
-
regular and dark walnut;
-
silver;
-
ash;
-
maple;
-
mahogany.
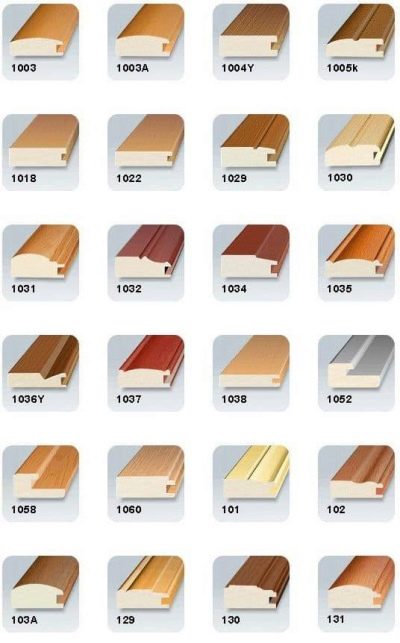
Dimensions (edit)
Dimensions of frame profiles can be:
-
70x2400;
-
55x2400;
-
66x2400;
-
30x2750;
-
54x2800;
-
50x2800;
-
70x2800;
-
60x2800;
-
35x2800;
-
47x2800;
-
102x2800;
-
84x2800 mm.
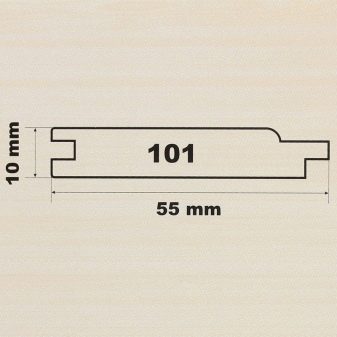
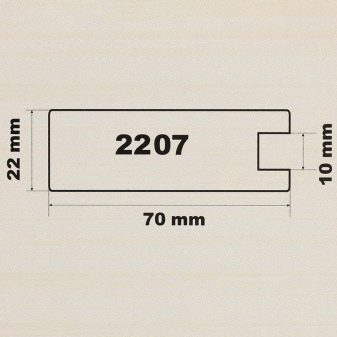
The 50mm and 70mm models are considered standard. There are also curved pieces at 66 mm. Profile height can be:
-
18;
-
22;
-
25;
-
30;
-
50 mm.
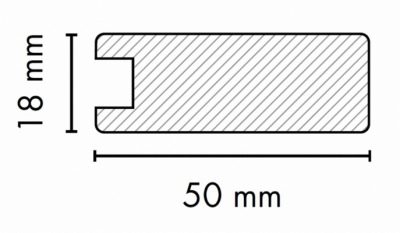
How is it made?
They begin work with a markup on a prepared profile. Then the material is cut out according to the size and marks. A very important step is dowel milling. Corner joints are glued straight, and a dowel is placed. The installation of the filler is also quite meaningful.
Frame profiles are assembled by cutting at an angle of 45 degrees. They should be docked as carefully as possible, without any visible gap. The profile is cut in a variety of ways. In a domestic environment, a manual technique is used, which involves the use of a miter box.
You can also cut the workpieces with an electric end plate or a professional sawmill.
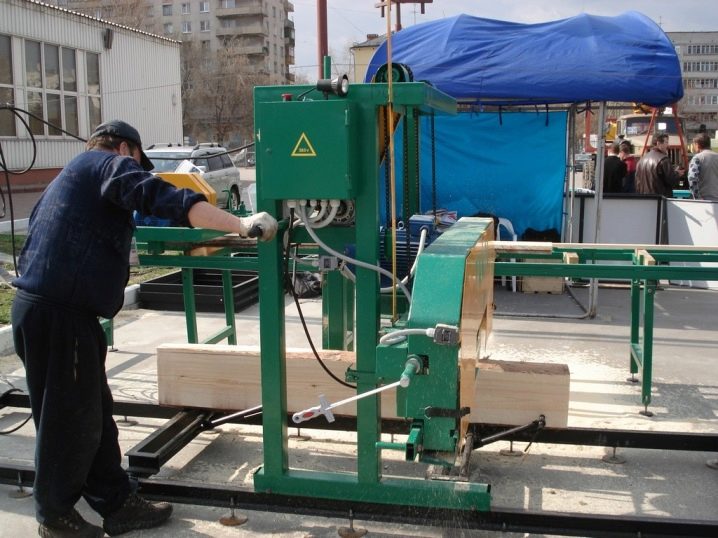
High-quality work using any of these techniques allows us to guarantee high accuracy of joining. Sawing is done with an ordinary hacksaw. Cut lines are cleaned with sandpaper. A metal miter box is better than wooden and plastic counterparts, since it allows you to work more accurately. The miter saw is the easiest to handle.
The sheet must be applied as tightly as possible to the stopper. Then the cutting disc is lowered to the workpiece. It is very important to correctly set the workpiece itself and its dimensions. Only after that the saw is turned on and the cut is made. The disc descends exclusively at the required angle with no lateral deviations.
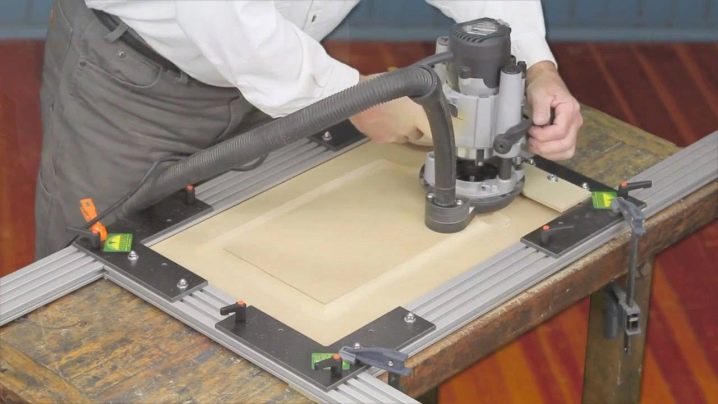
It is these properties that allow us to guarantee the accuracy of the cut, and eliminate gaps in the frame. A sawmill is used if it is impossible to use a miter saw. The MDF profile is rigidly fixed at an angle of 45˚ in relation to the disc and sawing it. When the material is cut, you can glue it.
The workpieces are attached to the milling machine. A figured cutter is used to work out the grooves. Then the ends are covered with fast-acting glue. All elements must be quickly docked. Then dowels are inserted into the grooves and hammered into them with a hammer. The excess glue is wiped off, after which the glue is applied to the inner edge of the frame, and the insert is placed. As soon as the structure is dry, the profile is completely ready for use.
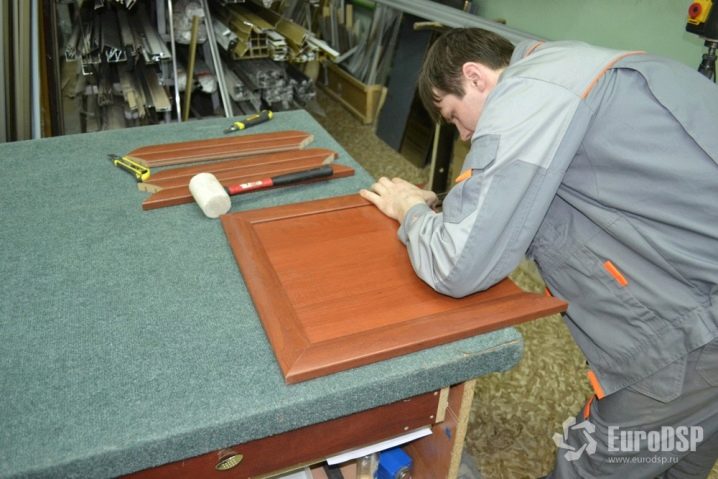
The comment was sent successfully.