What is cold welding, where is it used and how does it work?
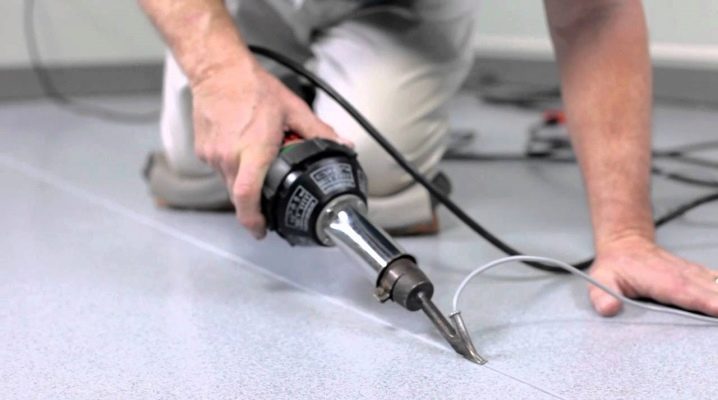
The joining of parts by cold welding has proved to be quite a popular solution in recent years. But to get a good result, you need to figure out how to apply this method correctly. You also need to understand the technical characteristics of these products and the peculiarities of their chemical composition.
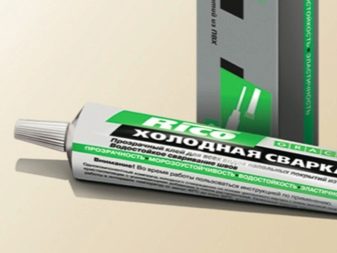
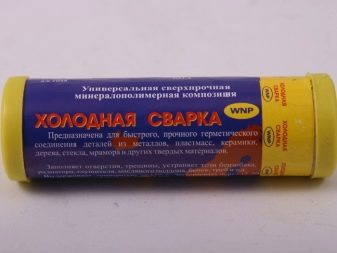
Description
Cold welding is known to quite a few, and some consumers recognize the merits of such a solution. But at the same time, there is a certain category of home craftsmen who have encountered negative results from using it. The reason in most cases is obvious - insufficient study of instructions and inattention to the details of this technology. With proper use, special glue effectively holds various parts together for a fairly long time.
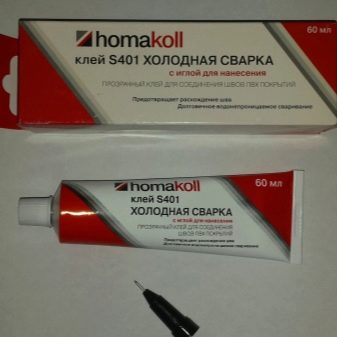
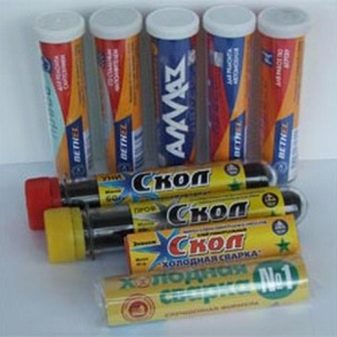
Cold welding works stably as a way to bond parts that do not undergo significant stress. It is in such cases that it is advisable to use it for fixing plumbing equipment and automotive equipment. But regardless of the degree of reliability, cold welding is needed to temporarily fix the problem. Later, as soon as the opportunity arises, a major overhaul is required. Cold welding is a means of joining parts that allows them to be connected without heating, practically “in the field”.
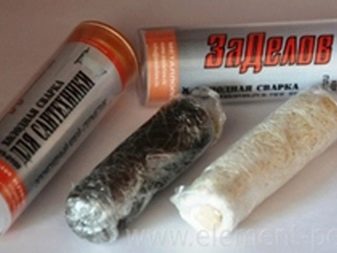
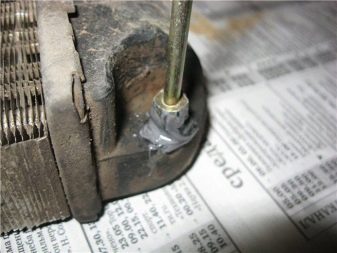
The chemical composition of the glue can include one or two components (in the first case, the material must be used as soon as possible, until it loses its qualities).
The advantages of cold welding over other options for joining materials are:
- elimination of deformations (mechanical or thermal);
- creating a consistently neat, outwardly even and reliable seam;
- the ability to connect aluminum with copper;
- the ability to close cracks and gaps in containers and pipes containing explosive substances;
- no waste;
- saving energy and fuel;
- environmental Safety;
- the ability to do all the work without specialized tools.
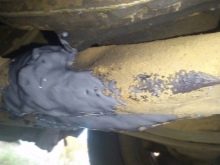
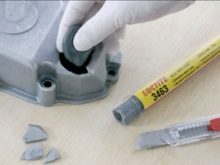
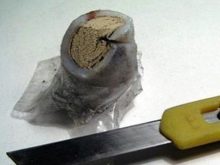
It should be borne in mind that cold welding is only suitable for minor repairs, since the seams formed are less durable than when using "hot" methods.
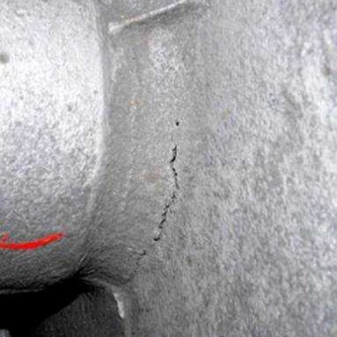
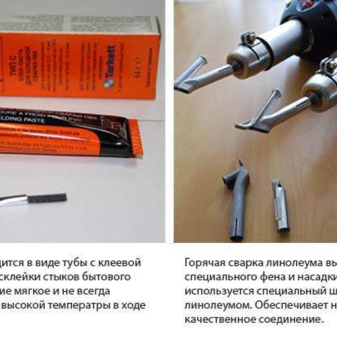
Types and purpose
Cold welding can be used for aluminum. After applying glue, the parts are pressed tightly and kept under pressure for about 40 minutes. The mixture will finally solidify in 120-150 minutes. This technique is capable of both tying flat parts and closing holes and cracks with minimal effort.
Plastic structures (including those based on PVC) can be cold-welded in industrial facilities and at home. Basically, such mixtures are designed to connect plastic pipes for heating, water supply, sewerage. Cold welding for linoleum can also be used to bond hard rubber products. It should be noted that the joints between parts of linoleum, if done in this way, are much better than when using other adhesives or double-sided tape.
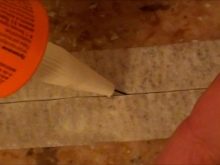
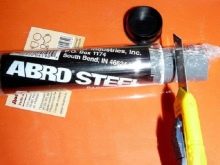
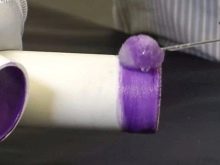
Cold welding for metal, including copper, allows you to close leaks in various pipelines and tanks.
Moreover, the capacity can be:
- 100% filled;
- completely empty;
- under limited pressure.
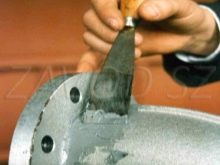
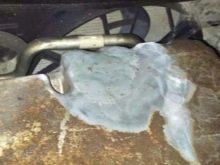

This means that the repair of leaky batteries, radiators, cans and barrels, and other containers can be carried out without draining the liquid. Even inexpensive glue options can be used to repair hot water pipelines; they easily tolerate heat up to 260 degrees. But it is imperative to find out whether this condition is actually met or the temperature will be higher. The high-temperature type of cold welding retains its working qualities when heated to 1316 degrees. It allows you to connect to each other surfaces exposed to heating, which are difficult or impossible to weld in the traditional way.
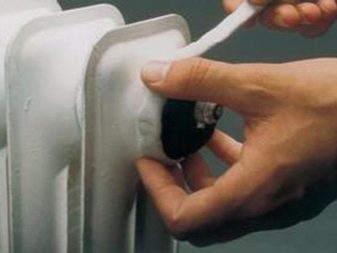
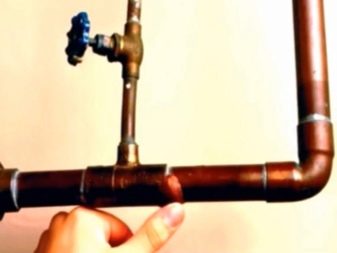
The two most common types of glue are, of course, for cast iron and for "stainless steel". You should not confuse them with each other, because each is suitable only for "its" metal.
The universal modification of cold welding allows:
- repair metal products;
- repair cars;
- connect parts even under water.
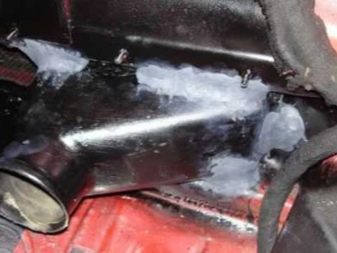
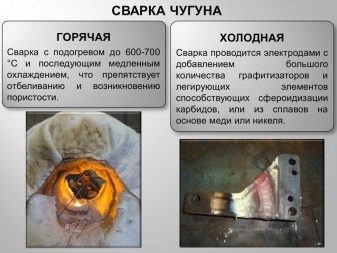
The most durable and stable are naturally those adhesives that are designed exclusively for working with metal, wood and polymers at the same time. The advantage of using such mixtures in the repair of plumbing is that even non-professionals who do not have sophisticated equipment can do the job. Universal compounds can also be used when gluing ceramics, polypropylene products. Regardless of the specific purpose, liquid welding is produced on a par with products that have the consistency of plasticine.
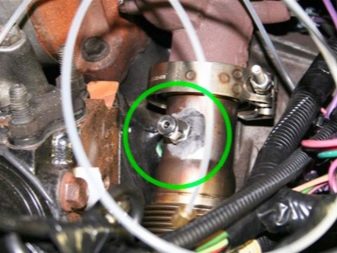
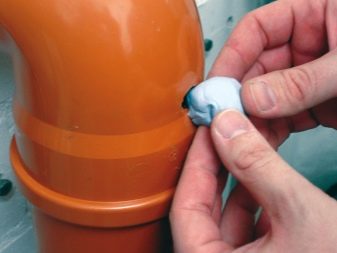
Composition
Two-component cold welding is located in a cylinder filled with a pair of layers: the outer layer is created by a hardening agent, and inside there is an epoxy resin core with the addition of metal dust. Such an additive helps to make the adhesion of parts stronger and more reliable. Special characteristics are given by slightly different additives, carefully hidden by each manufacturer. But it is known for sure that sulfur is always present among the main components.
Gas-resistant cold welding is formed by various resins. Its durability depends on the magnitude of the load and ranges from several hours to several days. It is recommended to take glue filled with metal to close the slots and holes in gasoline tanks, only then will it be possible to get to the nearest service.
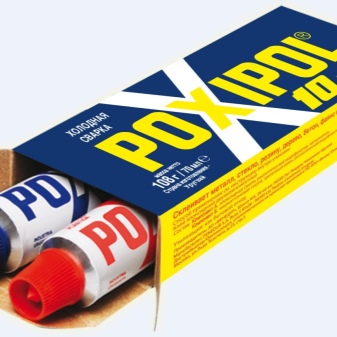
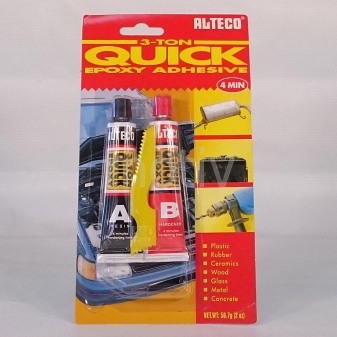
Specifications
How quickly a cold weld dries is determined by its chemical composition. In most cases, the resulting seam stops being sticky after 1-8 hours, although there are exceptions. It should not be forgotten that the special glue usually hardens more slowly, because it is necessary to wait for the completion of the reaction in the entire thickness of the coating. The setting time varies depending on the air temperature and most often it ranges from 12 to 24 hours. The seam formed by cold welding conducts current evenly along its entire length and thickness.
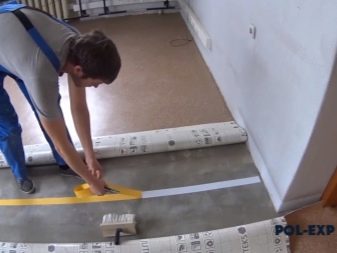
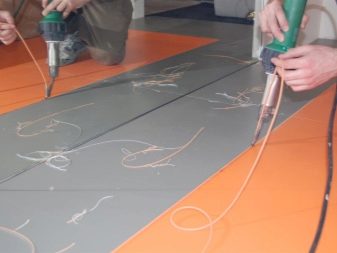
Based on the combination of properties, it can be concluded that a high-quality composition for cold welding can be used in almost all cases when a traditional electric welding machine cannot be used. But in order for the result to meet expectations, you must first choose a quality product.
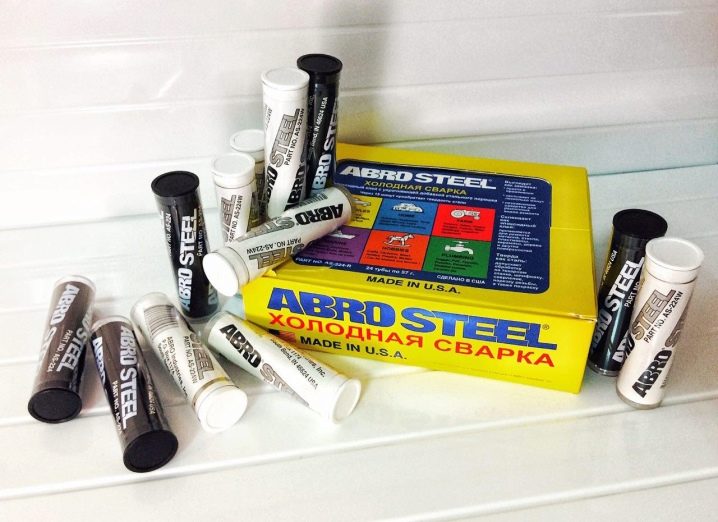
Review of popular manufacturers
It can be useful to be guided by reviews when buying cold welding, but it is equally important to know which manufacturers' products are in constant demand. Russian goods of this kind are relatively affordable, but their quality often does not meet the expectations of buyers. Judging by the assessments that are shared even by professional experts, among foreign brands the best Abro and Hi-Gear.
If you still look for mixtures of domestic production, then on the first lines of any rating they invariably turn out to be Almaz and Polymet... Branded products "Diamond" hardens in 1 hour, and the joint acquires full strength in 24 hours.Only then will it be possible to expose it to all the loads. The adhesive can be reused if it is sealed with plastic wrap and packed in a tube.
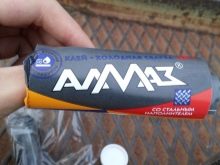
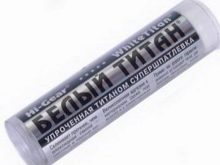
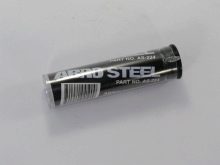
The manufacturer's manual states that "Diamond" can be applied even to damp surfaces. You only need to iron it until the adhesion is obvious. To make the glue harden, it is held with a tourniquet for 1/3 hour; this process can be accelerated by blowing the glued area with a home hairdryer. According to the manufacturer, he is not responsible for the consequences of cold welding in poorly ventilated rooms and / or without protective gloves.
Its chemical composition, in addition to epoxy resins, includes fillers of mineral origin, hardeners and iron-based fillers. The critical temperature is 150 degrees, the time for applying the mixture after preparation is 10 minutes. The minimum operating temperature is +5 degrees, but it must be borne in mind that with it the life cycle of the material is measured in minutes.
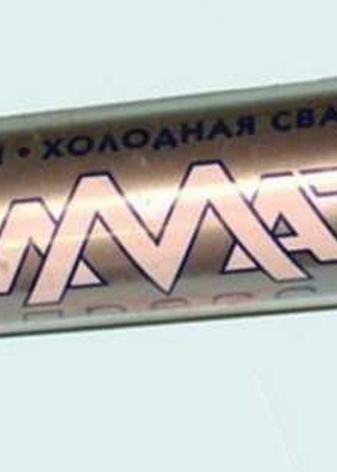
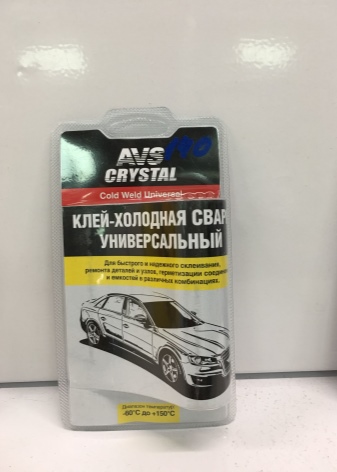
Cold welding for linoleum is supplied to the Russian market under the grades A, C and T (the latter is used less often). Modification A - liquid, contains a high concentration of solvent. The edges of the backing are glued just as effectively as the middle. It is impossible to use such a substance to seal large cracks due to its consistency. But it allows you to create an elegant, difficult to detect, even with close inspection of the seam.
With all the advantages of type A cold welding, it is suitable only for new linoleum, moreover, cut according to all the rules. If the material has already been stored for a long time or it has been cut ineptly, it would be more correct to use type C glue. It contains more polyvinyl chloride, and the concentration of the solvent, accordingly, decreases. Such material is thick, it can even cover up rather large cracks. There is no need for an accurate scrupulous adjustment of the edges, gaps of up to 0.4 cm are allowed between them, and this does not interfere with compliance with technological requirements.
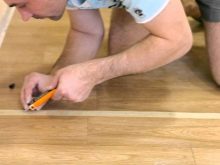
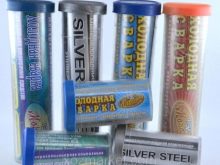
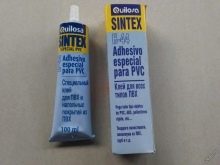
Cold welding of group T is intended for work with multicomponent linoleums, the main component of which is PVC or polyester. The resulting seam will be at the same time reliable, neat in appearance and flexible enough. With the help of such a mixture, even sheets and rolls of a semi-commercial class coating can be joined together.
Cold welding for metal under the brand "Thermo" Is a combination of metals and silicates with high viscosity. "Thermo" excellent for work with heat-resistant alloys, including titanium. If you need to repair burnt-out parts of the engine muffler, cracks formed in engine parts without dismantling, this is the best solution. The created seam not only can be operated in the temperature range from -60 to +900 degrees, it is very strong, tolerates well the ingress of water and exposure to strong vibrations. But the material will show its best qualities only after thorough processing of the parts, removing the slightest rusty areas and deposits from them.
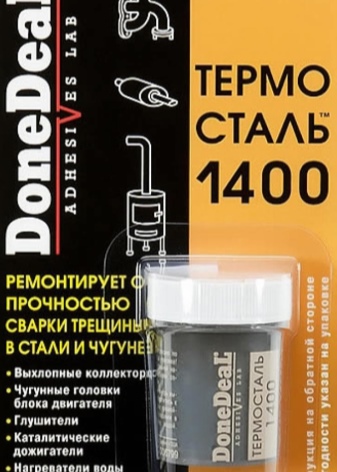
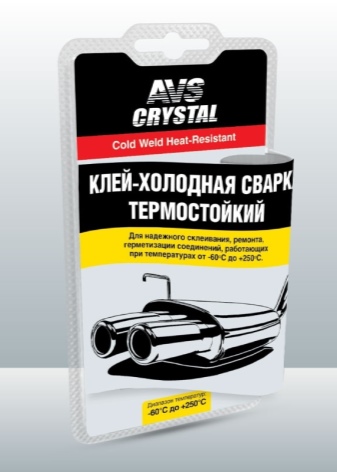
Instructions for use
Cold welding is not possible if the surface is not properly prepared. The best way to clean it is sandpaper, and you can judge the readiness of the surface by the exposed metal layer and scratches on it. The more such scratches in each area, the deeper they enter the material, the stronger the connection will be. The next step is drying the material, for which a simple household hair dryer is sufficient.
Claims may be encountered that cold welding successfully joins even wet parts., but no matter how impressive such a connection may look, it is unlikely to be reliable and sealed, resistant to the action of water and harmful factors. Drying alone is never enough, you still need to remove the fat layer from the surface.The most reliable means for degreasing was and remains acetone, it effectively removes even very small stains.
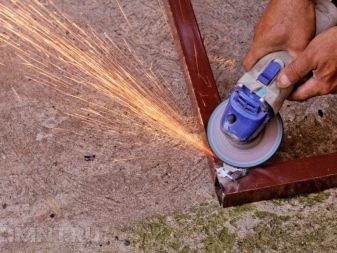
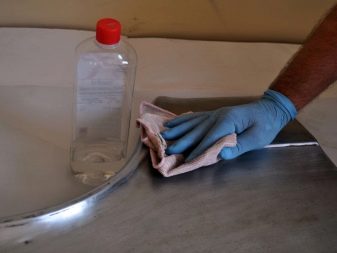
Then comes the turn of the preparation of the adhesive itself. The fragment of the desired size can be detached from the cylinder only with a sharp knife. They should only be cut across, otherwise the proportions of resin and hardener specified by the manufacturer when formulating the formulation will be violated. When a piece is cut off, it is crumpled until it is soft and completely uniform in color. It is easy to avoid the mixture from sticking to your hands, you just need to regularly dip your palms in water (prepared in advance, because it is much more convenient than constantly opening the tap, even if it is very close).
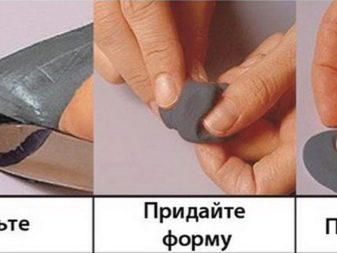
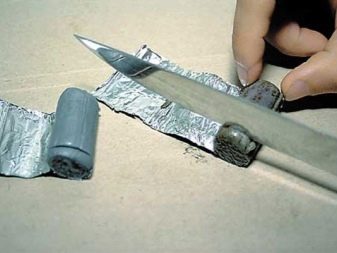
Working with your hands, it is important to accelerate when the glue reaches the desired consistency. It is enough to leave it unattended for a few minutes to detect the beginning of solidification. In this case, you still need to work carefully. The cold weld must partially penetrate the inside when closing the hole. But when the gap is too large, it is advisable to close it with a metal patch, which will already hold on to cold welding.
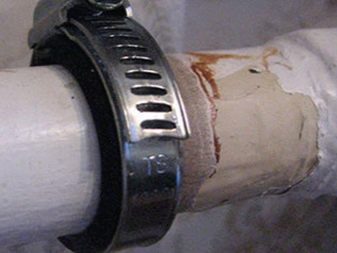
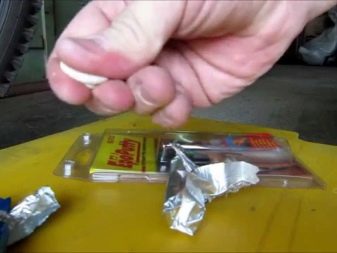
The glue will completely cure after 24 hours (although sometimes the recipe will speed up this process).
Before the expiration of the time specified by the manufacturer, it is impossible to finish the repaired area:
- clean it up;
- putty;
- primed;
- paint;
- treat with antiseptics;
- grind;
- using water pipes or heating radiators is also not worth it.
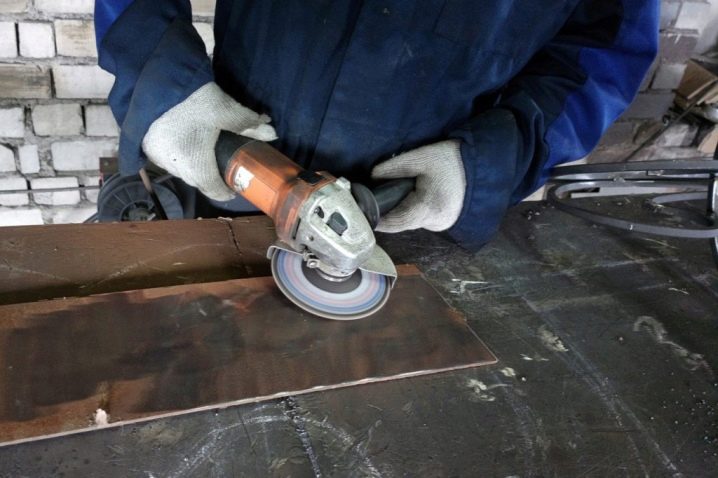
The fact that with the help of cold welding you can weld a variety of structures and their details, to achieve an impressive effect, does not mean that you can use it thoughtlessly. It is recommended not only to read the instructions from the manufacturer, but also to look at reviews, expert advice. We must not forget that acetone and other degreasing agents pose a great danger to the health of people and animals, in especially difficult cases they can even lead to disability or death. Therefore, it is necessary to wear protective clothing, work outdoors or with good ventilation in the room, preferably in the presence of someone who can help.
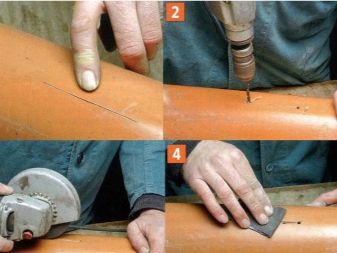
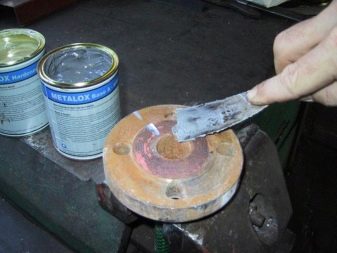
Helpful tips from the pros
Epoxy-based plasticine-based glue is recommended to be used when it is necessary to repair metals or their alloys. The mixture is impervious to water, solvents and even industrial oils. It can be used to glue products that will be used at temperatures from -40 to +150 degrees. Such a composition remains operational for no more than five minutes, and when an hour has passed, the glued metal can already be sharpened, drilled, polished, and so on.
Experts believe that the most reliable fixation of flat surfaces with clamps. In order to detect areas in the radiator of a car that allow liquid to pass through, it is blown through the water with a compressor from the inside; places where bubbles come out and need to be processed. Such repairs are short-term, when there is no possibility in the next few hours to seek help from a car service. It is categorically unacceptable, even for a short time, to use glue designed for a different material or for less intense heating.
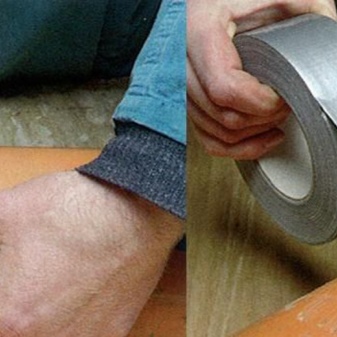
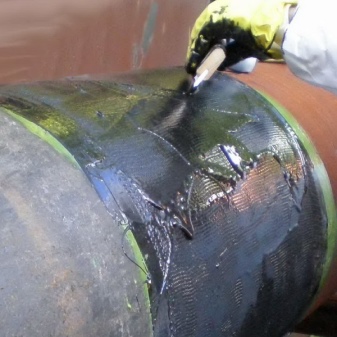
What is cold welding and what it is for, see the video below.
The comment was sent successfully.