Varieties of fiberboard plates and areas of their use
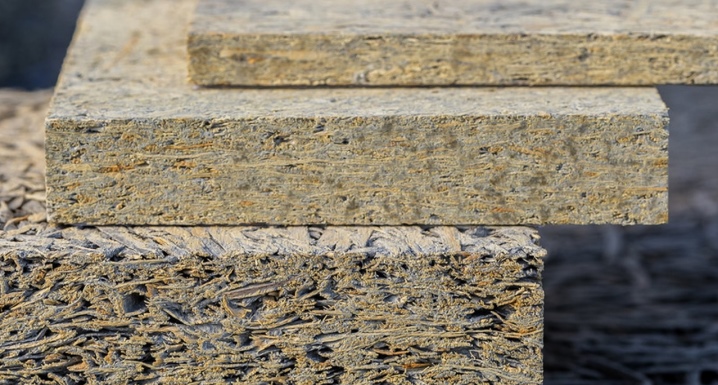
In the modern world, the construction industry is developing rapidly, the requirements for interior and exterior decoration of premises are growing. The use of high quality multifunctional materials is becoming a necessity. Home improvement with fiberboard plates will be a good solution.
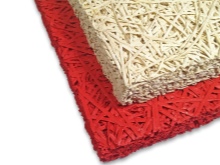
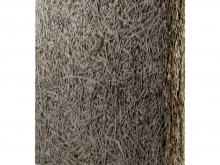
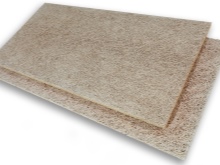
What it is?
Fibrolite cannot be called a very new material, it was created back in the 20s of the last century. It is based on special wood shavings (fibers), for which an inorganic binder is used... The wood fiber should look like thin, narrow ribbons; wood chips will not work. To get long, narrow chips, special machines are used. Portland cement usually acts as a binder, less often other substances are used. The production of a product requires a certain number of stages, the whole process takes about a month.
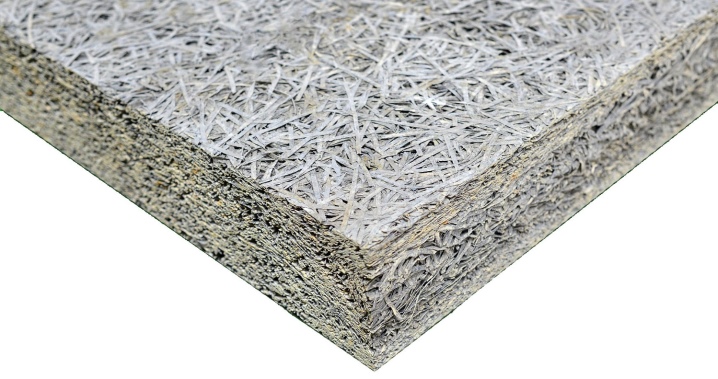
The first step in wood fiber processing is mineralization. For the procedure, use calcium chloride, water glass or sulphurous alumina. Then cement and water are added, after which the plates are formed under a pressure of 0.5 MPa. When molding is complete, the slabs are moved into special structures called steaming chambers. Plates harden in them, they dry until their moisture content is 20%.
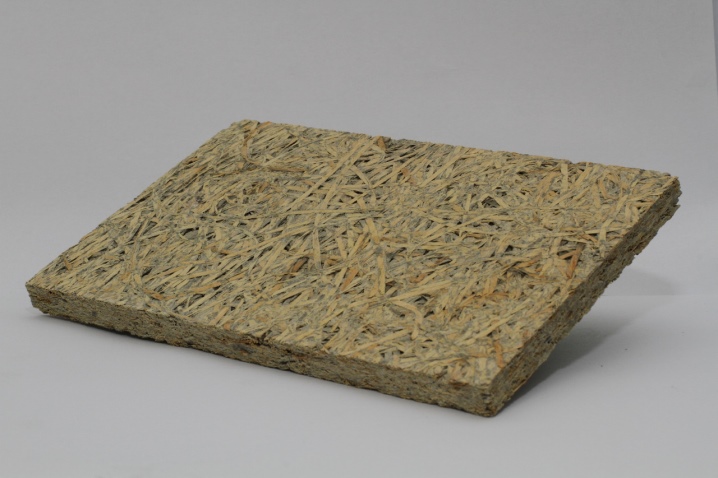
When cement is not used in production, no special mineralization is carried out. The binding of water-soluble substances contained in wood takes place with the help of caustic magnesite. During drying, magnesia salts crystallize in wood cells, excessive shrinkage of wood stops, magnesia stone adheres to the fibers.
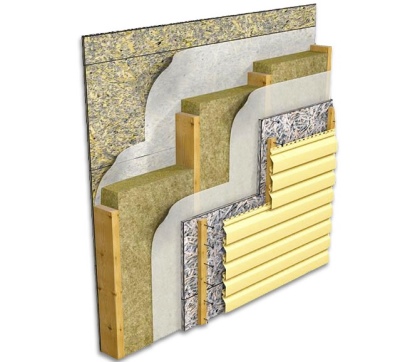
If we compare the properties of the fiberboard obtained in this way with cement, then it has less water resistance and greater hygroscopicity. Therefore, magnesia slabs have disadvantages: they strongly absorb moisture, and they can only be used in places where there is no high humidity.
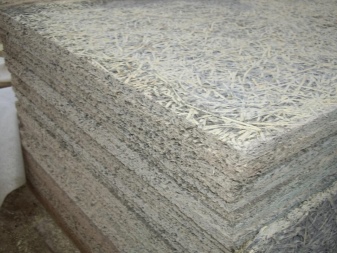
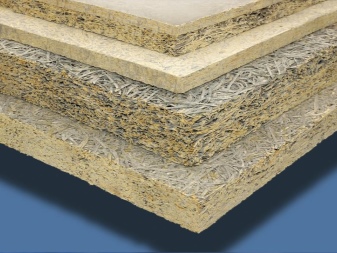
Cement fiberboard consists of 60% wood chips, which are called wood wool, up to 39.8% - from cement, the remaining fractions of a percent are mineralizing substances. Since the constituent elements are of natural origin, fiberboard is an environmentally friendly product. Due to its naturalness, it is called Green Board - "green board".
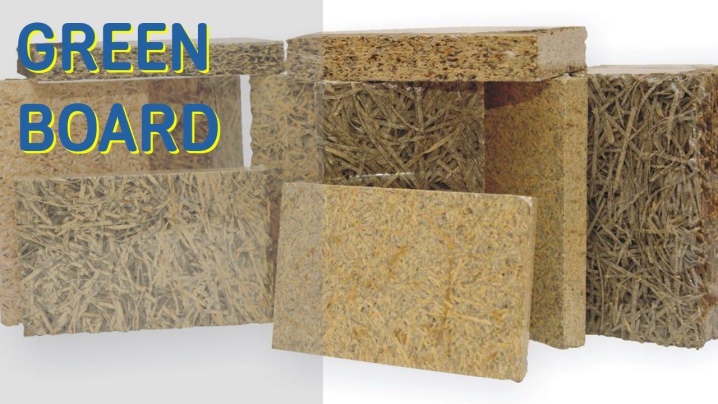
To create fibreboard, you need soft wood, which is possessed by conifers. The fact is that it contains minimal sugars, and water-soluble resins are present in large quantities. Resins are a good preservative.
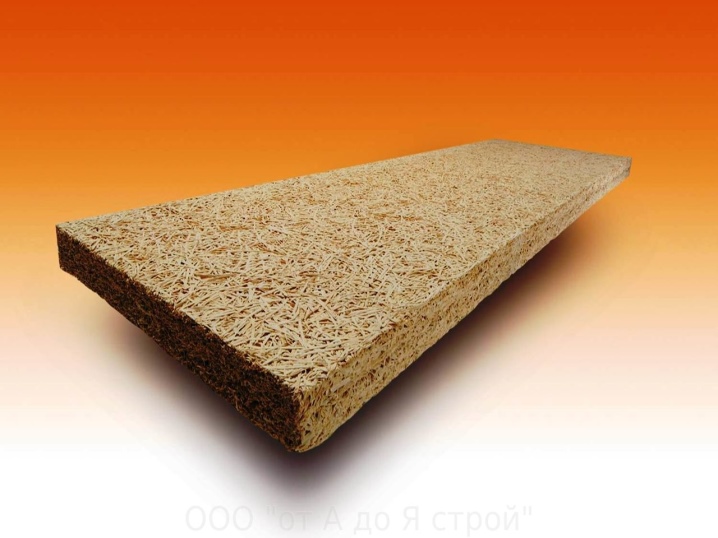
Fibrolite - an excellent building material, because it has an ideal rectangular shape. In addition, the panels almost always have a smooth front side, so the coating is constructed quickly - after installation, only the seams between the panels need to be repaired.
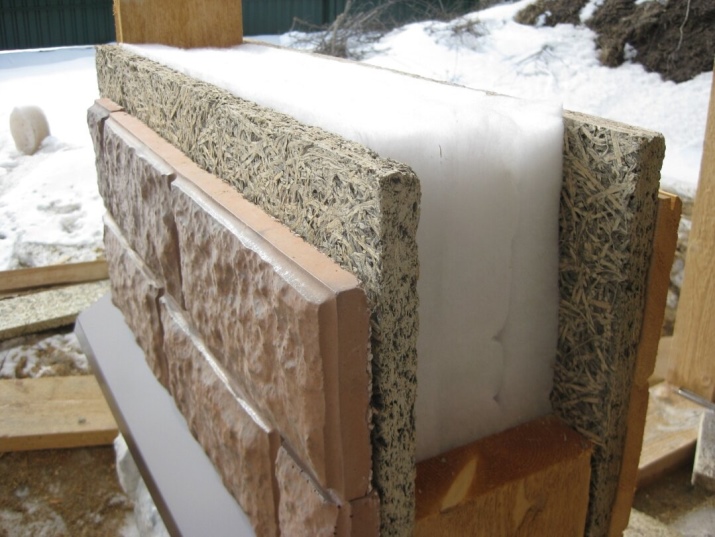
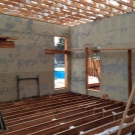

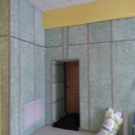
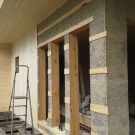
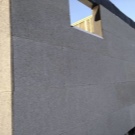
Specifications and properties
To understand the possible areas of application of the material and evaluate its advantages and disadvantages in comparison with other similar construction products, you need to know its technical characteristics. One of the most important is weight. Since the composition of fiberboard, in addition to wood shavings, includes cement, by this indicator it surpasses wood by 20–25%. But at the same time concrete turns out to be 4 times heavier than it, which affects the convenience and speed of fiberboard installation.
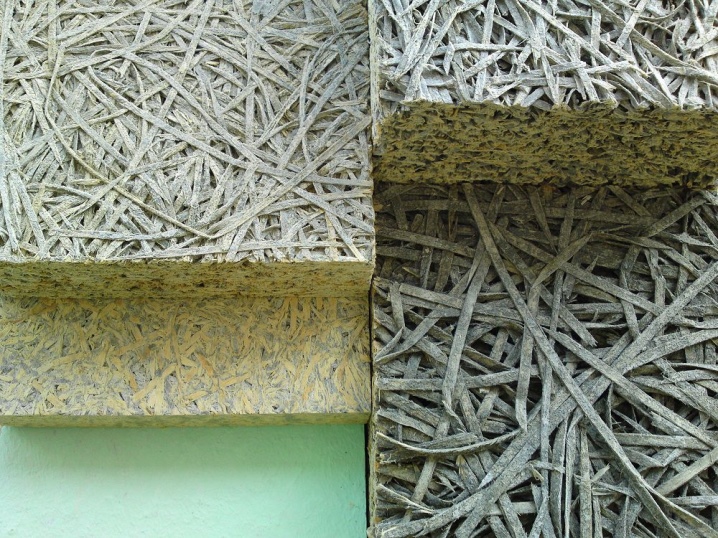
The weight of the slab depends on its size and density. Fiberboard plates have the dimensions established by GOST. The length of the slab is 240 or 300 cm, the width is 60 or 120 cm. The thickness ranges from 3 to 15 cm. Sometimes manufacturers do not make slabs, but blocks. By agreement with the consumer, it is permissible to produce samples with other sizes.
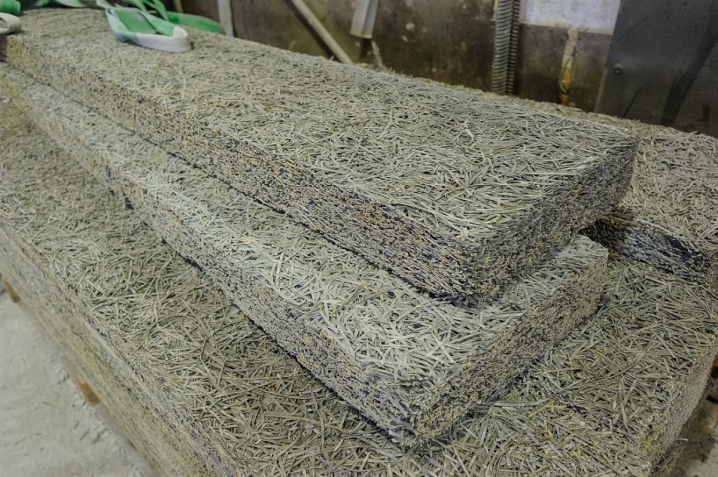
The material is produced in different densities, which determines its use for different purposes. The slab can be of low density with a value of 300 kg / m³. Such elements can be used for interior work. However, the density can be 450, 600 and more kg / m³. The highest value is 1400 kg / m³. Such slabs are suitable for the construction of frame walls and partitions.
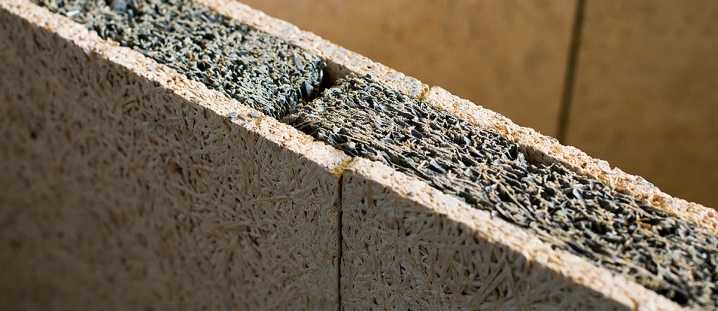
Thus, the weight of the slab can be from 15 to 50 kg. Plates with average density are often in demand, since they have an optimal combination of heat and sound insulation properties with high strength. However, structural elements are not made of such material, since it has insufficient compressive strength.
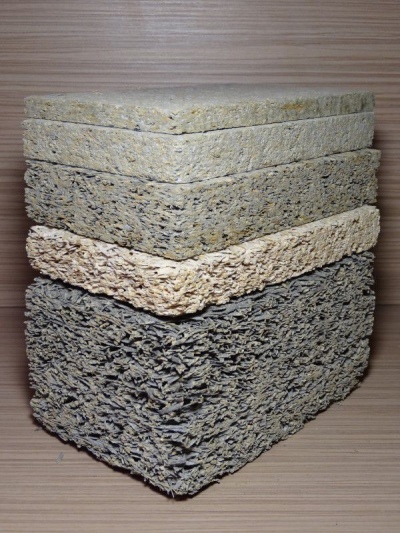
Fibrolite has many positive qualities.
- Due to its environmental friendliness, it can be used for decoration of residential premises. It does not emit any odors, does not emit harmful substances, therefore, it is safe for the health of people and animals.
- It has a very long service life, which is determined on average 60 years, that is, it has almost the same durability as metal or reinforced concrete. During this period, major repairs will not be required. The material can last longer. Maintains a stable shape and does not shrink. If repair is necessary, cement or a cement-based adhesive is applied to the damaged area.
- Fibrolite is not a biologically active material, therefore it does not rot. Insects and microorganisms do not start in it, it is not interesting for rodents. Resistant to various environmental substances.
- One of the remarkable properties is fire safety. The product tolerates high temperatures very well, is resistant to fire, like other materials that are not easily combustible.
- Plates are not afraid of temperature changes, withstand more than 50 cycles. Despite the fact that they are resistant to heat, the lower value for the operating temperature is -50 °.
- Differs in increased durability. Due to the wide range of characteristics, it is suitable for various types of work. If the mechanical impact fell on one point, the shock load is distributed over the entire panel, which results in minimizing the appearance of cracks, dents, and plate fractures.
- The material is relatively lightweight, so it is easy to move and install. It is easy to handle and cut, you can hammer nails into it, apply plaster on it.
- It has a low coefficient of thermal conductivity, therefore it has excellent heat-saving and sound-insulating properties. Maintains a constant microclimate indoors, while being breathable.
- Provides good adhesion to other materials.
- The product made using modern technologies is quite moisture resistant. After getting wet, the fibrolite dries quickly, while its structure is not disturbed, but its properties are preserved.
- An undeniable advantage for consumers will be the price, which is lower than for similar materials.

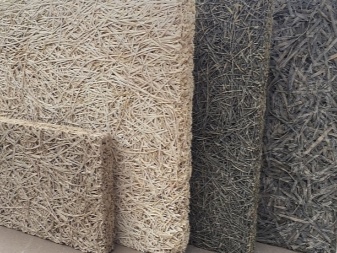
However, there are no perfect materials. Moreover, sometimes the positive side turns into a minus.
- High processing flexibility can mean that the material can be damaged by strong mechanical stress.
- Fiberboard has a fairly high water absorption. As a rule, it leads to a deterioration in quality indicators: there is an increase in thermal conductivity and average density, a decrease in strength.For fiberboard, prolonged exposure to high humidity in combination with low temperatures is detrimental. Therefore, there may be a decrease in the service life in regions where there are frequent temperature drops per year.
- In addition, material produced using old technologies or without observing technological standards can be affected by fungus. The product should not be used in rooms where high levels of humidity are constantly maintained. In order to increase the water resistance, it is recommended to cover the fibreboard with hydrophobic impregnations.
- In some cases, a rather high weight of a high-density slab is considered a disadvantage compared to wood or drywall.
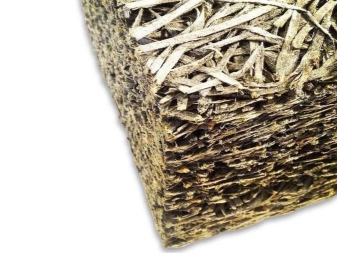
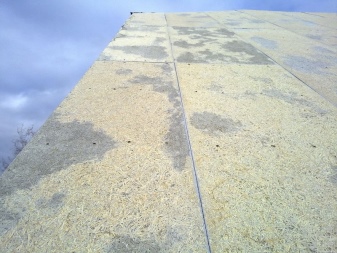
Applications
Due to their characteristics, fiberboard boards are very widely used. Their use is widespread as fixed formwork for monolithic housing construction. Fixed fiberboard formwork is the easiest, fastest and most economical way to build a house. In this way, both one-story private houses and several floors are erected. Plates are in demand when buildings and structures are being repaired or reconstructed.
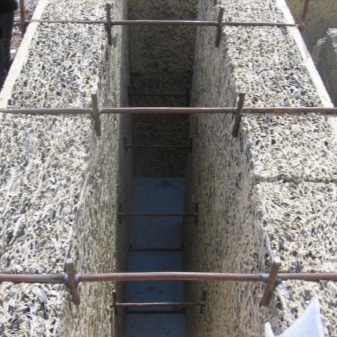
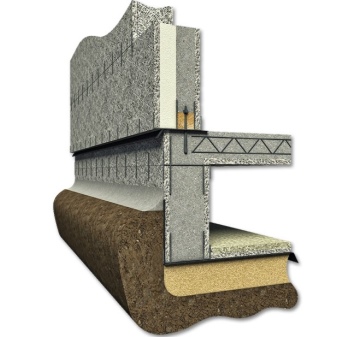
The construction is facilitated by the standard size of the slabs and the low weight of the material, and there is a reduction in work time and labor costs. If necessary, it is processed in the same way as wood. If the structure contains complex curvilinear shapes, the slabs can be easily cut. Fiberboard frame walls are a good solution for a modern home, as the material has excellent acoustic characteristics.
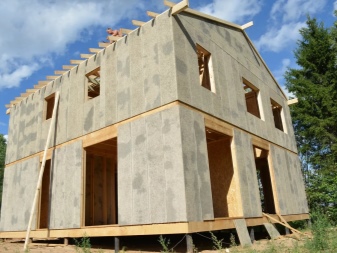

Fibrolite is an effective soundproofing product with a high level of noise absorption, which turns out to be very useful if the building is located near large routes.
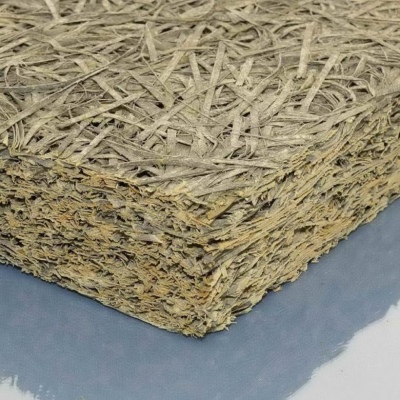
The material is no less widely used for interior decoration. For example, wall partitions are mounted from it. They will not only protect against noise, but also ensure the preservation of heat in the room. The product is suitable not only for homes, but also for offices, cinemas, sports venues, music studios, train stations and airports. And also fibrolite is used as insulation, which will be a wonderful additional tool for the heating system, will reduce heating costs.
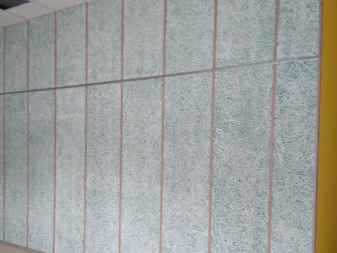
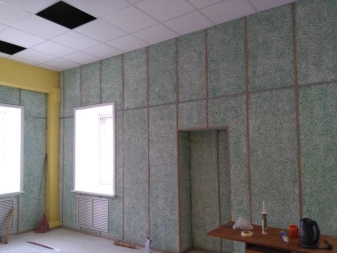
Plates can be fixed not only on walls, but also on other surfaces: floor, ceiling. On the floor, they will serve as an excellent base for linoleum, tiles and other floor coverings. Such a floor will not creak and collapse, since the base is not subject to decay.
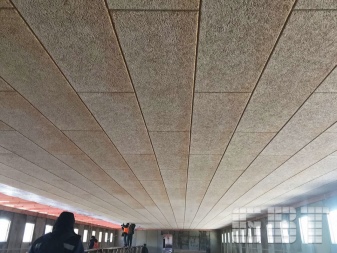
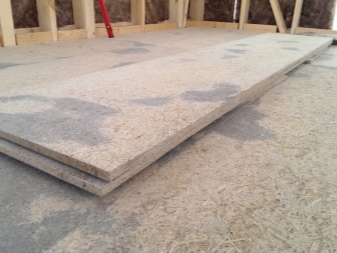
Fiberboard can be a structural element of the roof... It will provide the roof with heat and sound insulation, will serve to prepare the surface for the flooring of roofing materials. Since the product is fire resistant, roofers often take advantage of the open flame fusion method.
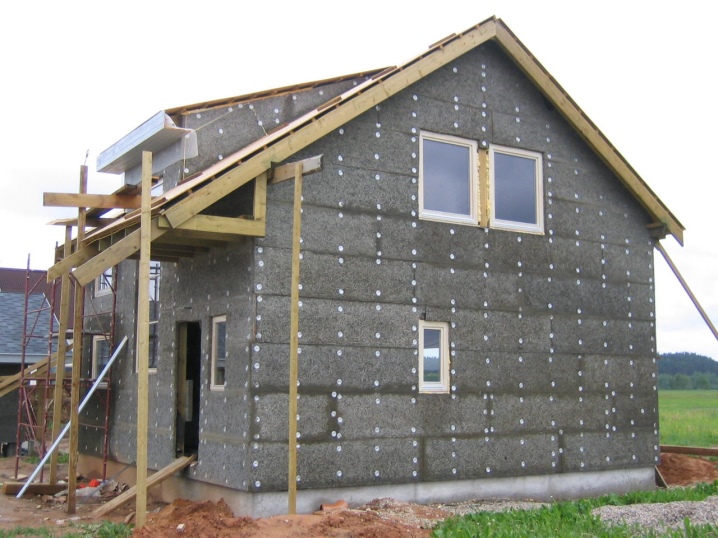
Today's construction market offers innovative products, which include fiberboard-based SIP sandwich panels. SIP panels consist of 3 layers:
- two fiberboard plates, which are located outside;
- insulation inner layer, which is made of polyurethane foam or expanded polystyrene.
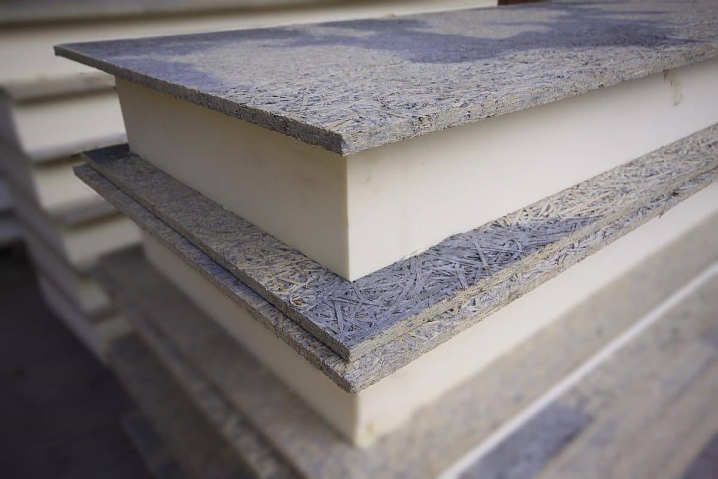
Thanks to several layers, a high level of noise and sound insulation is ensured, heat preservation in the room even in frosty weather. In addition, the inner layer can have different thicknesses. CIP panels are used to build cottages, baths, garages, as well as gazebos, outbuildings and attics to finished buildings, for the construction of which brick, wood, and concrete were used. And also from the panels are created internal and external walls, load-bearing structures, stairs and partitions.

SIP panels are safe products and are often referred to as "improved wood". They are durable, fireproof, and increase the biological resistance of the building. Fungi do not appear in them, pathogenic bacteria do not multiply, insects and rodents do not breed.
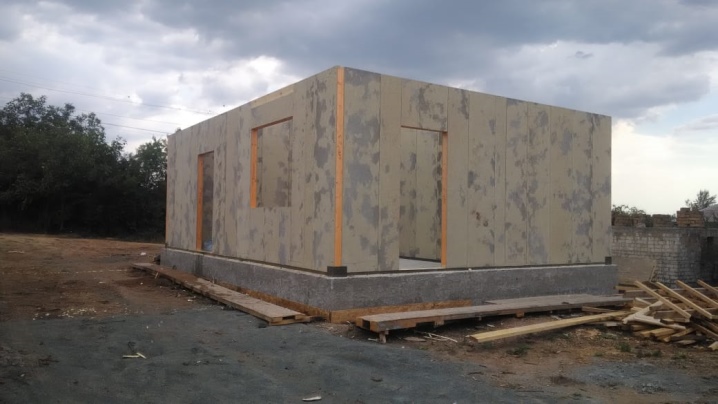
Species overview
There is no clear generally accepted division of material into varieties. But since the use of fiberboard depends on its density, classifications are applied taking into account this parameter. Today there are two types of classification. One of them is the current GOST 8928-81, issued by the USSR State Committee for Construction.
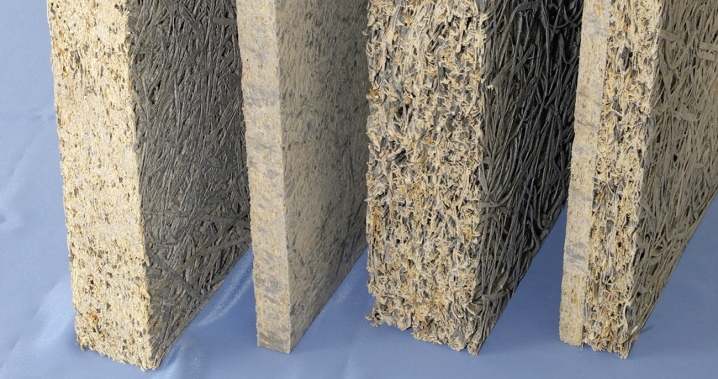
However, the more commonly used system is the one introduced by the Dutch firm. Eltomation... This system is used when marking ultralight slabs. Green Board, for the production of which Portland cement is used. It should be noted that the Green Board name applies only to slabs made with Portland cement. Although magnesia and cement blocks have identical characteristics other than moisture absorption, magnesia slabs are not termed Green Board.
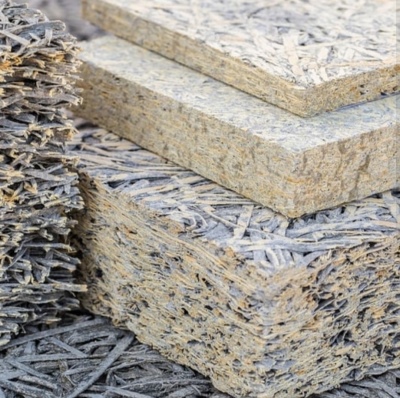
By brands
In accordance with GOST, there are 3 grades of slabs.
- F-300 with an average density of 250-350 kg / m³. These are heat-insulating materials.
- F-400. Density of products from 351 to 450 kg / m³. Structural properties are added to the thermal insulation. The F-400 can be used for soundproofing.
- F-500. Density - 451-500 kg / m³. This brand is called construction and insulation. Like F-400, it is suitable for sound insulation.
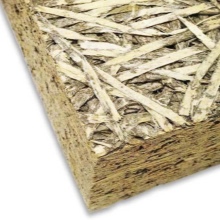
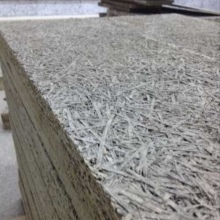
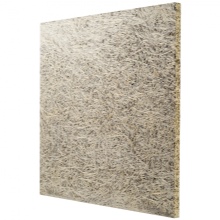
GOST also defines standards for dimensions, strength, water absorption and other characteristics.
By the degree of density
Since the modern market needs new, more advanced materials, manufacturers have expanded the boundaries of density and other indicators of fiberboard, the products do not fit into the above classification. Eltomation's classification system also offers 3 main brands.
- GB 1. Density - 250-450 kg / m³, which is considered low.
- GB 2. Density - 600-800 kg / m³.
- GB 3. Density - 1050 kg / m³. High density is combined with great strength.
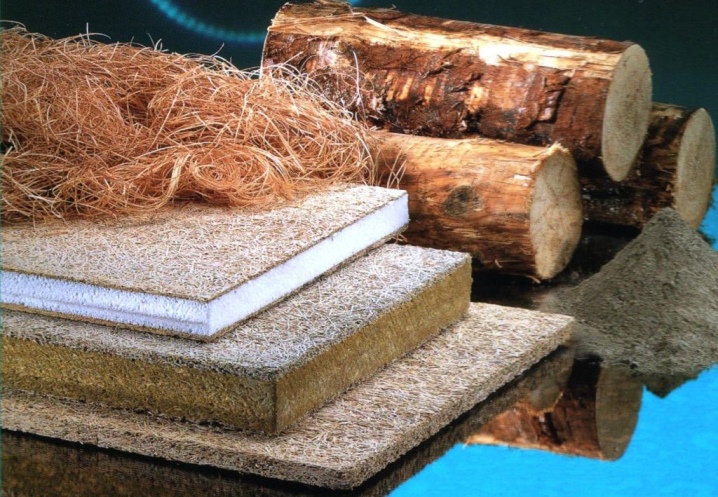
Plates with different densities can be of any size. It should be noted that this classification does not cover the entire variety of products. Therefore, other meanings can be found among manufacturers. For example, GB 4 denotes a combination board in which there is an alternation of loose and dense layers. GB 3 F are products with maximum density and decorative coating.
There are other designations that take into account not only strength, but also other characteristics. Manufacturers may have variations in designations. Therefore, when buying, you must carefully study all the parameters. As a rule, a detailed technical specification is given for products.
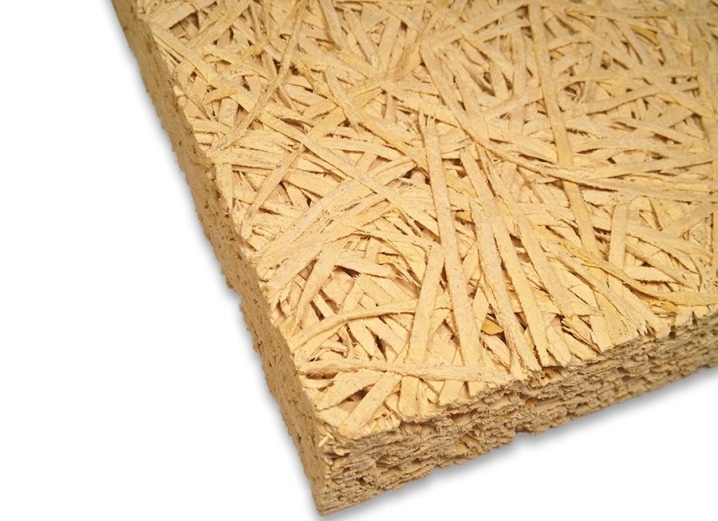
Installation rules
The variety of technical characteristics of the products makes it possible to use them at almost any stage of construction. Although the procedure for installing the plates is not particularly complicated, some rules and sequence of work must be followed.
- Slabs can be cut with the same tools as wood.
- Fasteners can be nails, but experienced builders recommend using self-tapping screws to ensure a more stable connection.
- It is imperative to use metal washers to protect the holes for the fasteners and prevent damage and destruction.
- The length of the self-tapping screws is determined using simple calculations: it is equal to the sum of the plate thickness and 4–5 cm. This is the depth to which the self-tapping screw must go inside the base where the plate is attached.
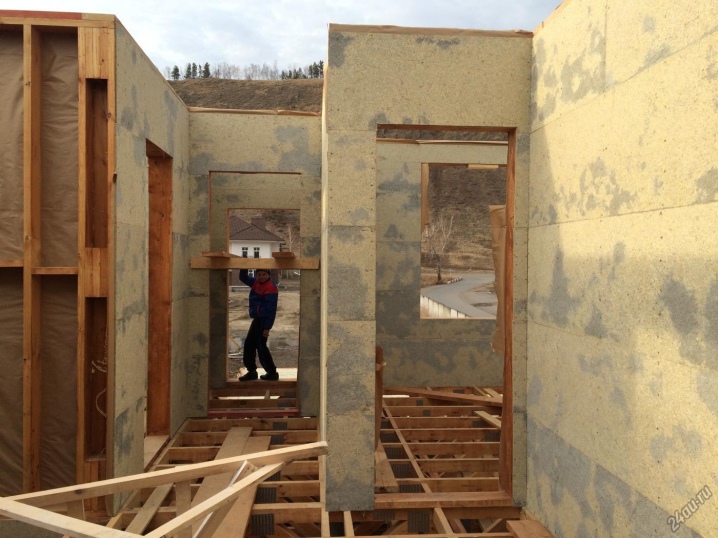
If a frame structure is sheathed with fiberboard plates, then it is necessary to make a crate. The step should not be less than 60 cm, if the thickness of the slab does not exceed 50 cm. If the slabs are thicker, then the step size can be increased, but not more than 100 cm. In frame construction, fiberboard can be installed both from the outside and from the inside. For greater insulation of the structure, a layer of insulation, for example, mineral wool, is often placed between the plates.
For the installation of fiberboard material, you will need glue. It is a dry mix. Before use, it is diluted with water.Care must be taken that the solution does not turn out to be very liquid, otherwise the plate may slide under its weight. The glue should be mixed in small portions, as the setting takes place rather quickly.
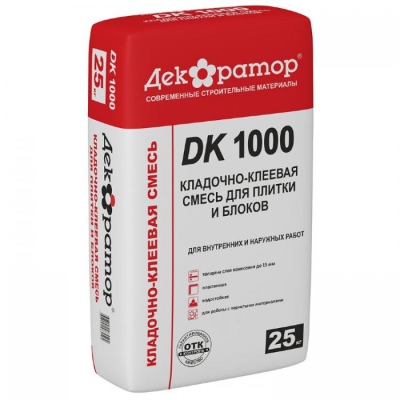
The building is insulated sequentially.
- First of all, the outer surface of the wall is cleaned. It should be free of plaster residues and dirt.
- Laying of external facade insulation starts from the bottom row. The next row is laid with overlap, that is, the joint of the slabs of the lower row should be in the middle of the element in the upper row. A continuous, even layer of glue is applied to the inner surface of the part. The same layer is applied to the wall. This is most conveniently done with a special notched trowel.
- The installed slab must be secured with suitable large umbrella-headed anchors. Such heads contribute to the fact that the dowels will securely hold the plate. You will need 5 fasteners: in the center and in the corners. Each fastener must enter the wall to a depth of at least 5 cm.
- Then a reinforcing mesh is applied. It is laid on a surface on which glue is applied with a spatula.
- When the glue is dry, the wall can be plastered. A layer of plaster will protect the fiberboard from the influence of ultraviolet rays and precipitation in adverse weather. For the facade wall, a solution containing moisture-resistant additives is added to the plaster.
- The plaster is trowelled and primed. After drying, the walls can be painted. In addition to staining, siding or tiles can be used for cladding.
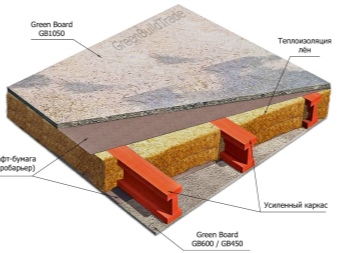
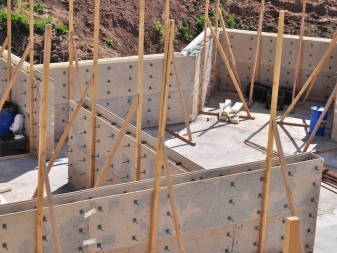
When insulating floors, the slabs are laid on a concrete base. It must be dry and clean. Cement is used to seal the joints. Then the screed is performed. It is a cement-sand mortar with a thickness of 30-50 cm. When the screed hardens, they make the floor covering from linoleum, laminate or tile.
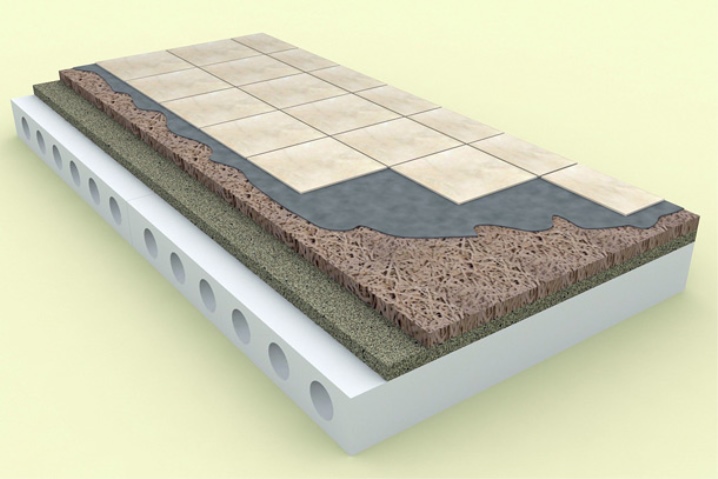
The pitched roof must be insulated from the inside. The work is performed step by step.
- First you need to sheathe the rafters with edged boards. This is necessary so that gaps do not form.
- For cladding, you will need plates with a thickness of 100 mm. Screws are used as fasteners. Cut the slabs with a saw.
- For finishing, you will need fiberboard sheets or other material.
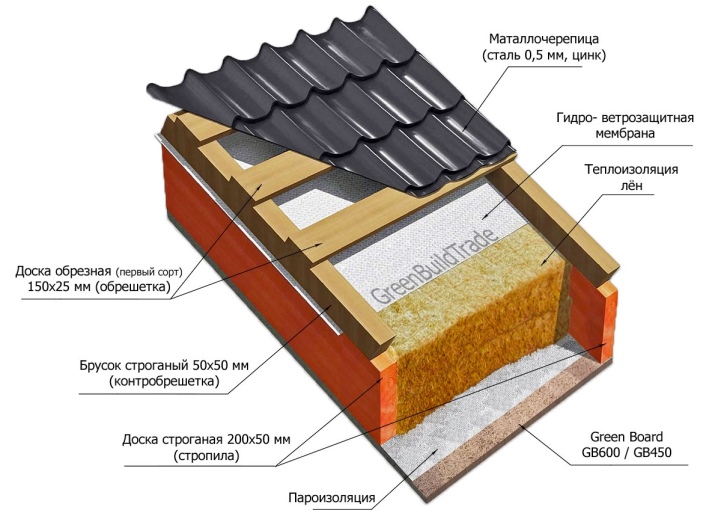
For the outer cladding of the roof, it is advisable to use reinforced slabs reinforced with wooden battens.
The comment was sent successfully.